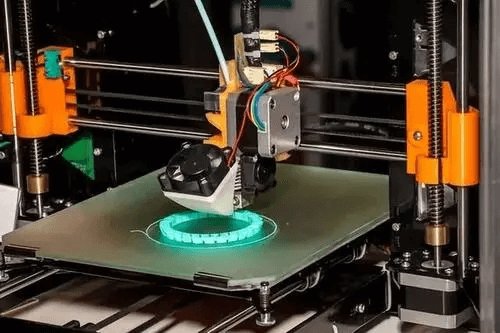
增材制造是基于分层制造原理发展而来的先进制造技术,是信息技术、新材料技术与制造技术多学科融合发展的产物,被视为支撑制造业转型升级与创新发展的关键技术。增材制造,作为全球范围内新一轮科技与产业革命中至关重要的一部分,被认为是现代科技发展中一项核心及颠覆性技术,已逐渐成为当今世界各国对未来产业发展的新增长点。本次全国科普日活动,将对增材制造如何推动航空航天制造技术变革进行全面解读。
增材制造及其优势
增材制造的国际发展态势
-
增材制造目前的国际发展态势主要表现在四个方面。第一,得到了世界上主要工业国家的普遍关注与高度认可。面对增材制造的种种优势与巨大发展前景,世界主要工业国家纷纷将其视为战略性新兴产业,把推动本国增材制造发展上升到了国家战略层面。美国拜登政府2022 年10 月发布《先进制造国家战略》,强调要发展和运用先进制造技术,其中就包括增材制造。2019 年2月,德国发布的《国家工业战略2030:对于德国和欧洲产业政策的战略指导方针》将增材制造列为十大关键工业部门之一。早在2014 年6月,日本内阁出台的《制造业白皮书》就将增材制造作为今后本国制造业的重点发展领域。是年8月,日本经济产业省出台《制造业革命技术》,将增材制造作为优先扶持对象。
增材制造在航空航天领域的应用 更多
-
增材制造在航空发动机构件领域的应用
先进航空发动机朝着高推质比、高可靠性、长寿命和经济可承受性的方向发展,苛刻且相互矛盾的指标要求航空发动机关重件构型复杂、轻质高效。传统的“减材”制造技术面临生产周期长、成品率低、制造成本高等挑战,成为制约先进航空发动机研发的瓶颈。变革性的“近净成形”增材制造技术,因具有一体化成形、无需模具、制造成本低等优点,最早被美国联合技术研究中心(UTRC)尝试用于涡轮叶盘一体化制造,随后通用电气(GE)、罗尔斯-罗伊斯(RR)等航空发动机企业也开始应用增材制造技术加工或修复零部件。
-
增材制造镍基高温合金在航天构件领域的典型应用
相较于航空领域,航天领域对于高温合金部件的制造要求更加苛刻,呈现出更加复杂化、薄壁化、复合化、一体化等趋势。以高性能液体火箭发动机燃烧室为例,其部件往往暴露在高热、负荷等工作环境中,因此需要进行高效率的冷却。传统的减材或等材加工技术无法胜任此类独特且巧妙的冷却系统的制备。
-
金属增材制造在直升机中的应用前景
结构拓扑优化设计技术,又称创成式设计技术,经过几十年的发展,已经被证实是一种高效的结构设计方法,在航空航天结构轻量化、高性能设计领域具有广阔应用前景,但受限于现有加工技术,其实际应用面临巨大挑战。郭文杰等对某型无人机翼梁结构开展刚度拓扑优化设计,优化后的结构满足强度、刚度设计要求,同时减重达到6%。胡添翼等对飞机典型双耳结构连接件进行拓扑优化设计,如图4所示,优化后的双耳结构连接件满足强度设计要求,且可减重26.8%。
总结
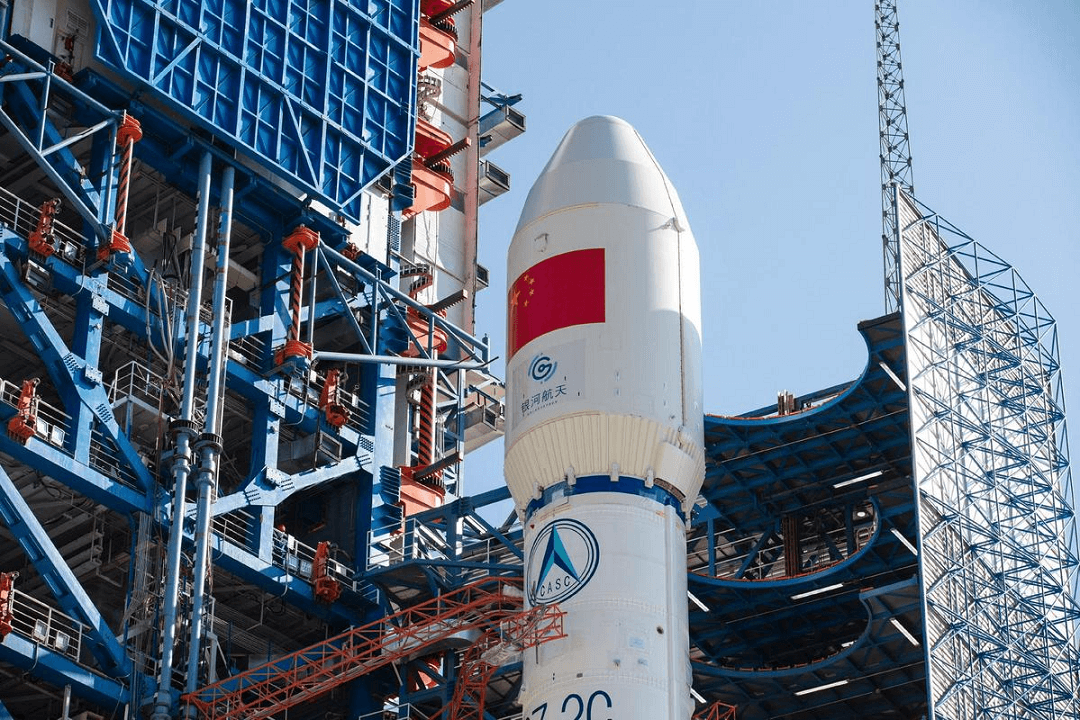
在航空航天应用方面,增材制造技术具有单件小批量复杂结构快速制造的优势,当前多型重点装备的关键零部件(例如铰链、支架、内部组件、发动机部件等)均已实现增材制造技术的工艺替代及应用,其应用正加速向终端零件制造、产品修复再制造、商业化应用等方面深化发展,在太空制造、新型空天装备等研究中也将提供重要支撑作用。
随着增材制造在更多领域应用场景的普及与推广,增材制造的成本在不断降低,加之增材制造本身的技术优势带来的不可替代性越来越强,基于增材制造技术的新应用、新产品越来越多,增材制造将获得更广阔的增量市场。预计,2023年航空航天批量化生产将持续增加,铸造、消费电子将成为新的增长点。