导读:当纳米晶和纳米孪晶金属的晶粒尺寸或孪晶厚度低于临界尺寸时,纳米晶和纳米孪晶金属的强度停止增加甚至开始下降——这种现象被称为霍尔-佩奇击穿,阻碍了超高强度的实现。本文报告了纳米孪晶纯 Ni 的连续强化,孪晶厚度范围从 81.0 到 2.9 nm。在 2.9 nm 的极细孪晶厚度下实现了前所未有的 4.0 GPa 强度,比传统的粗粒镍强度高约 12 倍。这种超高强度源于孪晶界的出色稳定性及其对位错运动的强大阻抗。特别是,我们发现二级纳米孪晶被激活以维持塑性变形,这也有助于高强度。
Hall-Petch 强化源于晶界或孪晶界(GBs 或 TBs)阻碍位错运动,是一种经典但最有效的提高材料强度和硬度的方法。在此理论的基础上,材料的理想理论强度可以在其极细的晶粒尺寸或孪晶厚度下达到。不幸的是,先前的研究表明,当晶粒尺寸或孪晶厚度低于临界尺寸(通常约为 10 到 15 nm)时,屈服强度要么保持不变,要么随着晶粒尺寸或孪晶厚度的减小而降低;这种现象被称为 Hall-Petch 击穿或软化。现有理论表明纳米晶粒 (NG) 和纳米孪晶 (NT) 金属的软化机制不同;前者的软化是由 GB 滑动或晶粒旋转引起的 ,而后者是由软模式位错(孪晶部分位错沿 TB 滑动)或解孪晶引起的 。在抑制这些软化机制和实现低于临界尺寸的持续强化方面仍然存在巨大挑战。
将溶质原子分离成 GBs 和 TBs 可以有效降低迁移驱动力,从而抑制 NG/NT 合金(如 NG-Ni-Mo 合金和 Cu 微合金化 NT-Ag)的软化效应 . 结果,即使晶粒尺寸或孪晶厚度低于 10 nm,也能实现连续强化。然而,由于在这个长度尺度上边界的不稳定性(强烈的解离和迁移趋势),很少获得显示低于 ~10 nm 晶粒尺寸或孪晶厚度的连续强化的纯金属。除了边界处的偏析影响 GB 和 TB 行为外,TBs 的稳定性还与具有柱状晶粒的 NT 金属中的加载方向密切相关。在正常负载条件下,TBS已经报道表现出优异的稳定性,无明显去孪晶化,并且可以阻碍位错运动。因此,我们预计具有极细孪晶厚度的NT-金属可能会发生连续强化,从而实现超高强度。然而,由于难以可控地合成孪晶厚度低于 10 nm 的 NT 金属,因此对该假设的实验验证仍然是一个巨大的挑战。
在这里,金属研究所沈阳材料科学国家研究中心材料动力学研究部李毅研究员(通讯作者),潘杰副研究员(通讯作者)联合上海交通大学材料与工程学院研究员郭强通过直流(DC)电沉积成功制造了孪晶厚度范围为 2.9 至 81.0 nm 的柱状晶 NT-Ni,并证明了其持续强化。强化可以扩展到 2.9 nm 的孪晶厚度,导致 4.0 GPa 的超高强度。透射电子显微镜 (TEM) 表明,这种强化归因于细间距 TBs 的优异稳定性,阻碍了解孪晶并导致二次孪晶的形成,这些孪晶是阻碍位错运动的强大屏障。相关研究成果以题“Ultrastrong nanotwinned pure nickel with extremely fine twin thickness”发表在国际著名期刊Science Advances上。
论文链接:
https://advances.sciencemag.org/content/7/27/eabg5113
图 1A显示了沉积态 NT-2.9 试样的典型三维显微结构。平面图 TEM 图像显示等轴纳米尺寸晶粒,而横截面图像显示细长柱状晶粒嵌入纳米级生长孪晶(图 S3)。柱状晶粒宽度在14-48nm之间,平均值为28nm(图1B)。孪晶厚度显示范围从 0.5 到 15 nm 的窄分布(图 1C)。放大的 TEM 显微照片(图 1,D和 E) 表明大多数双平面具有相干的 TBs (CTBs)。除了这些 CTB 之外,还观察到一小部分(小于 2%)的非相干 TB 和堆垛层错 (SF)。NT-2.9 样品的 X 射线衍射 (XRD) 图案表明 (111) 面外晶体结构和微弱 (200) 峰的存在(图 1F);这与TEM结果一致,表明柱状晶粒的长轴和(111)孪晶面的法线方向平行于生长方向。
图 1 具有极细孪晶厚度的沉积态 NT-Ni 的典型微观结构。
( A ) NT-Ni 的三维结构,由平面图和横截面明场 TEM 图像组成。(B)从沉积的 NT-2.9 样品的 TEM 和 HRTEM 图像测量的双厚度和(C)柱宽分布。( D ) NT-2.9 样品的更高放大截面 TEM 图像。( E ) 沿 [011] 区轴拍摄的 HRTEM 图像。(E) 中的插图显示了相应的选区电子衍射图。( F ) XRD 图案显示NT-2.9 样品中存在的主要(111) 取向。au,任意单位。
为了评估具有极细孪晶厚度的 NT-Ni 的机械性能,我们对直径约 1.3 μm 的微柱进行了单轴压缩测试。加载方向与 TB 垂直。图 2显示了 NT-2.9 和 NT-6.4 试样的真实应力-应变曲线,以及从 ( 22 ) 中获得的 NG-Ni 和粗晶粒 (CG) Ni 的应力-应变曲线,晶粒尺寸为 20 nm 和 80 μm,以进行比较。 NT-6.4 试样在 2% 塑性应变下表现出 2.9 GPa 的流变应力(这里,我们将 2% 塑性应变下的流变应力指定为被测支柱的σ y),以及约 12% 塑性时的加工硬化行为屈服后的应变,这可能是由于 Lomer-Cottrell 锁和 TB 之间的更多相互作用引起的。NT-2.9 试样的流动应力 (σ y )更高,为 4.0 GPa,但塑性有限(~2.5%;)。NT-2.9的强度是晶粒尺寸为20 nm(σ y = 1.9 GPa)的NG-Ni的两倍以上,是晶粒尺寸为80 μm的CG-Ni(σ y = 0.3 GPa )的12倍)
图2 NT-Ni柱的机械性能。
柱子的单轴真实应力-应变曲线显示 NT-2.9 和 NT-6.4 试样在 2% 塑性应变下的流变应力分别为 4.0 和 2.9 GPa。还提供了(22)中NG-和 CG-Ni 的真实应力-应变曲线以供比较。红色正方形、橙色圆圈以及蓝色和黑色三角形表示四个样品在 2% 塑性应变下的流动应力。插图显示了对直径为 1.3 微米的 NT-Ni 试样进行的压缩试验的示意图。
图 3 NT-Ni 的连续强化。
Ni 和 Mo 微合金化 NT-Ni (1.3 at. %) 的屈服强度随平均晶粒尺寸或孪晶厚度的变化,以及通过电沉积 (ED) Ni、Ni 柱、ED 的拉伸和压缩试验直接获得的文献数据NT-Ni ( 22 , 24 – 33 , 53 , 54 ) 和 NT-Cu ( 2)。分别在沉积态 NT-Ni 和钼微合金化 NT-Ni 试样中观察到连续强化行为延伸至 2.9 和 1.9 nm 的孪晶厚度。相反,当平均孪晶厚度低于 10 至 15 nm 时,在沉积态 NT-Cu 中观察到软化行为,即屈服强度随着晶粒尺寸或孪晶厚度的减小而降低。此处用于数据拟合的霍尔-佩奇关系是 σ y = 0.267 GPa + 6.233 GPa·nm –1/2 d (λ) –1/2 ( 39 , 55 )。
图 4 NT-Ni 的变形机制,λ = 2.9 nm。
(A)验尸明场图像,显示样品中的剪切带和柱状晶粒。插图显示了在~3% 塑性应变下单轴压缩后支柱的形态。(B)来自(A)中框 R1 的更高放大倍数的 TEM 图像,显示变形区域中保留的纳米孪晶结构。( C ) 一个典型的 HRTEM 图像和 ( D ) 其相应的 GPA 应变图(面内刚体旋转,ω xy)在变形区域,显示部分位错向双平面倾斜的方向滑动,留下一个堆垛错误。
在结束之前,我们注意到观察到的连续强化可以进一步扩展到 1.9 nm 的孪晶厚度。这种更细的孪晶厚度是通过在 Ni 中微合金化 Mo 实现的,这会略微降低 SFE 并促进纳米孪晶的形成。在这种 Mo 微合金化 NT-Ni [1.3 原子百分比 (at %) Mo; 见图。S11] λ = 1.9 nm 时,其 σ y(在正常负载条件下)为 4.4 GPa(图 S12),比 NT-2.9 试样高 0.4 GPa,并且也位于外推的 Hall-Petch 线上(图3)。我们的 Mo 微合金化 NT-Ni 的强度比 NT-Ni 83.6 Mo 14 W 2.4膜的强度高 1.0 GPa,具有几乎相同的 λ (1.8 nm) 。结果(将强化扩展到 1.9 nm 的孪晶厚度)表明,在埃级孪晶厚度下可以实现更高的强度,甚至达到理想的理论极限。
图 5 变形 NT-2.9 样品中二次纳米孪晶的形成。
(A)来自图 4A中框 R2 的 HRTEM 图像显示二次纳米孪晶(用黄色箭头标记)穿过变形过程中在 NT-Ni 柱状晶粒内部形成的初始 TB。(B和C)来自( A )中框 B 和 C 的更高放大率的 HRTEM 图像,分别显示了次级纳米孪晶的成核和终止。( D ) HRTEM 图像 (C) 的相应 GPA 应变图(平面内刚体旋转,ω xy)。
总之,作者通过直流电沉积获得的具有极细孪晶厚度的 NT-Ni 的强度为 4.0 GPa,高于已知的纯 Ni。这种强度源自延伸至最细孪晶厚度 (2.9 nm) 的持续强化。持续强化行为源于TBs的优异稳定性及其对位错成核和运动的有效屏障,再加上二次纳米孪晶作为进一步阻碍位错运动的新障碍。本研究不仅为在高 SFE 金属中合成具有极细孪晶厚度的 NT 结构提供了机会,而且还阐明了霍尔-佩奇强化可以通过纳米结构金属中的结构构建扩展到极细的结构尺寸。
免责声明:本网站所转载的文字、图片与视频资料版权归原创作者所有,如果涉及侵权,请第一时间联系本网删除。
相关文章
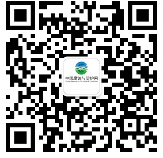
官方微信
《中国腐蚀与防护网电子期刊》征订启事
- 投稿联系:编辑部
- 电话:010-62316606-806
- 邮箱:fsfhzy666@163.com
- 中国腐蚀与防护网官方QQ群:140808414
点击排行
PPT新闻
“海洋金属”——钛合金在舰船的
点击数:7130
腐蚀与“海上丝绸之路”
点击数:5741