导读:激光冲击喷丸等严重塑性变形技术已被广泛应用于材料的微观结构改造。了解SPD过程中的塑性变形机理将有助于优化SPD过程以获得所需的微观组织。本文利用LSP技术,对含有马氏体板条和碳化物的aisi420马氏体不锈钢表面组织进行了改性,经过LSP处理后,AISI 420马氏体不锈钢的抗拉强度和延伸率分别提高了24.3%和47.8%,并从组织演变的角度研究了其变形机理。高分辨透射电子显微镜和x射线衍射分析结果表明,激光冲击波对AISI 420马氏体不锈钢中原始亚微米碳化物产生严重变形,导致碳化物破碎。这些lsp诱导的碳化物碎片和原始碳化物促进了马氏体板条的纳米晶化,因为碳化物/基体界面是位错的有效形核位点,并阻碍了位错的运动。
提高结构材料的力学性能和性能是非常理想的,可以通过优化材料的微观结构和/或成分来实现。晶体材料的微观结构操纵主要通过剧烈塑性变形(SPD)技术加上热处理来实现。例如,超声纳米晶表面改性,激光冲击喷丸(LSP),喷丸强化,表面机械磨损处理(SMAT)和高压扭转(HPT) 技术已被普遍采用以细化晶粒,实现超细晶粒/纳米晶(UFG/NC)材料。塑性变形机制、织构演化、再结晶甚至纳米结晶机制都与SPD技术在不同应变速率和温度下的工作密切相关。位错滑移和/或变形孪晶是SPD技术处理的粗晶材料的两种主要变形模式,随着应变和/或应变速率的增加,位错结构和/或变形孪晶的趋势增加,lsp诱导的晶粒细化机理(从亚微米到纳米尺度)越来越受到关注。因为与喷丸处理相比,LSP导致了更深层的表面纳米晶化和压缩残余应力层。在具有面心立方(FCC)和六方密排(HCP)结构的单相金属材料中,lsp诱导的晶粒细化主要归因于位错活动,机械孪晶和再结晶。与单相材料相比,多相材料由于不同的变形机理和相互作用,变形诱发的微观组织演化非常复杂,而且可能会发生化学成分和相结构的变化。例如,当含有渗碳体颗粒的钢通过SMAT进行塑性变形时,渗碳体中会发生溶解/分解。在HPT处理的马氏体轴承钢中也报道了类似的现象,渗碳体的分解过程被解释为基体流动和渗碳体塑性变形产生的界面磨损的协同过程。
马氏体不锈钢是一种碳元素含量低、铬元素含量高、具有体心立方晶体结构的铬不锈钢。马氏体不锈钢的低碳高铬在热处理过程中可能诱发富Cr析出碳化物。近年来,人们对SPD后马氏体不锈钢的塑性变形机理和强化机理进行了大量的研究。SPD期间,马氏体钢中马氏体板条的细化是通过各种位错运动获得的,随着应变和应变速率的增加,位错壁和纠缠发展为亚边界,细化马氏体板条。表面机械轧制处理后的AISI 52,100钢表层获得了梯度纳米结构,使其表面显微硬度提高了约20%。随着变形量的增加,经冷轧和电塑轧制处理的低碳马氏体钢的强度增加,伸长率呈下降趋势。有效晶界强化和弥散强化提高了冷镦9Cr2WVTa钢的强度。特别是,硬质合金还可以通过位错滑动进行细化、碎片化和纳米晶化。与此相对应,在LSP诱导的马氏体不锈钢显微组织演变研究领域,还存在几个有待解决的问题,包括:(i) LSP如何生成具有球状碳化物的BCC钢的梯度纳米结构?(ii)碳化物对马氏体基体纳米化过程的影响机理是什么?(3)激光冲击压缩下碳化物纳米化的机理是什么?(4)富Cr碳化物在塑性变形和碳化物破碎过程中如何分解?(v) LSP处理后提高aisi420马氏体不锈钢强度和塑性的根本机制是什么?目前的工作旨在解决这些问题。研究了LSP处理对含两相(马氏体板条和碳化物)aisi420马氏体不锈钢的梯度纳米结构和拉伸性能的影响。
在此,江苏大学重点研究了激光冲击波产生的碳化物碎片的微观组织特征、两相的纳米化机理以及富Cr碳化物的分解机理。最后,系统地揭示了LSP诱发的潜在强度和延性增强机理。经过LSP处理后,AISI 420马氏体不锈钢的抗拉强度和延伸率分别提高了24.3%和47.8%,其抗拉性能的提高可归因于晶粒细化强化、沉淀强化和位错强化。LSP生成的马氏体板条纳米晶化是通过两种同时细分模式来实现的:纵向和横向亚边界的相交由位错密集壁发展而来,横向亚边界由位错缠结转化而来。碳化物的分解与严重的塑性变形同时发生,表现为变形碳化物中Cr浓度连续下降,Fe浓度随变形程度的增加而增加。相关研究内容以题为《Carbide-facilitated nanocrystallization of martensitic laths and carbide deformation in AISI 420 stainless steel during laser shock peening》发表在《Inter. Jour. Plasticity》上。
原文链接:https://www.sciencedirect.com/science/article/pii/S0749641921002576
(1)发现分散的碳化物极大地促进了马氏体板条细化,因为碳化物/基体界面是位错的有效形核位点,也是位错运动的障碍。LSP诱导的深度马氏体板条纳米化过程包括两种类型的同时细分模式:从致密位错壁(具有初级滑移系统)和横向子边界转变的纵向和横向子边界之间的交叉来自位错缠结(具有两个滑移系统)。
(2)当马氏体板条被细化到小于碳化物的尺寸时,碳化物发生塑性变形,其特征是沿{111}和{311}面的多向位错滑移,并积累多次滑移,逐渐将碳化物细化为纳米级上表面有一定尺寸的碳化物。激光冲击波在原始亚微米碳化物中产生了严重变形、轻微变形和不变形三种塑性变形区域。
图1所示。AR样品的典型TEM显微照片。(a)在板条马氏体金属丝网和微米/纳米碳化物边界,(b) (a)的相应SAED模式共存的马氏体金属丝网和M23C6碳化物(c和e)的高放大TEM图像微米和纳米碳化物(d和f) Cr的EDS分析谱线轮廓,c和铁碳化物在c和e,(g) AR试样的x射线衍射图,(h和i)放大的(110)和(211)XRD峰显示马氏体板条与第二相共存。
图2所示。(a1-a4) LSP-1和(b1-b4) LSP-2样品在不同深度下的典型TEM图像分别显示了(b1)、(a3)和(a4)的梯度纳米晶结构和(ce)高倍率SAED图案。
图3所示。(a) AR、LSP-1和LSP-2样品的x射线衍射图;(b和c)放大后的(110)和(211)XRD峰显示了LSP发生后的峰移和第二相溶解;(d)放大后的(110)XRD峰显示了LSP发生后的峰宽。
图4所示。(a) LSP-1样品在~30μm深度处碳化物周围位错线(DLs)的TEM典型图像,(b)位错线的高倍放大图像,(c)对应的SAED图形,(b)(d、e) LSP-2样品在~30μm深度处碳化物周围致密位错壁(DDWs)和超细晶粒(UFGs)的典型透射电镜图像。
图5所示。在LSP-1样品最上层的TEM图像中,可以看到弥散碳化物周围的变形基体剪切流形态,如黄色点状箭头所示。
图6所示。(a和b)典型高放大率亮场(BF)显像在最顶层表面LSP-1和LSP-2标本显示纳米结构,(c)相应的暗场(DF) (b)的形象,和(d1-d3) EDS映射结果c Cr和Fe对应于矩形D (c)。
图7所示。(a)高分辨率透射电镜(HRTEM)的纳米结构在图6 b,(中)逆快速傅里叶变换(传输线)数字的矩形(a)在nano矩阵和M23C6显示混乱,分别介绍(f)图像显示无定形结构和纳米矩阵,和(g和h)传输线图像的矩形g和h (f)。
图8所示。(a1-a4, b1-b4,) LSP-1和LSP-2样品在不同深度下的典型透射电镜图像显示了纳米碳化物的梯度结构,(c-f)对应的特定区域的SAED图形用c-f圆标记。
图9所示。(a)图8(a3)中碳化物变形的高倍图像,(b) (a)中矩形b的HRTEM图像,(C- e) (b)中矩形C- e的IFFT图像,(f) (a)中碳化物中Cr、C和Fe的线轮廓分析。
图10所示。(a)典型HRTEM等轴纳米碳化物的形象,(b和c)传输线矩形b和c的(一个)显示不同的晶格取向两个纳米碳化物,(d)矩形的传输线形象d (a)展示了非晶态结构,(e1)矩形的传输线形象E (a)显示点阵有序纳米硬质合金和非晶结构,(a)中矩形E的(e2-e3)一维IFFT图像。
图11所示。LSP-1和LSP-2样品在~15μm和~5μm深度的TEM图像显示碳化物碎片。(a) ~15μm深度的LSP-1样品,(b) ~15μm深度的LSP-2样品,(c) ~5μm深度的LSP-1样品,(d) ~5μm深度的LSP-2样品,(e和f)分别为(c)和(d)中e和f方块的高分辨率图像。
图12所示。典型(a)和(b)男朋友DF TEM图像最顶层LSP-1标本表面碳化显示碎片和分解,(b1b3)的EDS映射结果C Cr和相应有限元(b),和(C)的谱线轮廓分析Cr、C和Fe沿着方向的黄色虚线箭头(b)。
图13所示。(a) AR、LSP-1和LSP-2试样的工程应力-应变曲线和(b)微观硬度深度曲线。
图14所示。马氏体板条纳米晶化过程的示意图。(绿色的亮度表示碳化物中Cr的含量。)
图15所示。M23C6纳米晶化示意图,M23C6在lsps表面的破碎和分解过程随深度的降低呈现不同阶段。(绿色的亮度表示碳化物中Cr的含量。)
图16所示。lsp诱导aisi420马氏体钢的梯度纳米结构示意图。(绿色的亮度表示碳化物中Cr的含量。)
(3)LSP产生的超高应变率导致基体和碳化物的表层结晶顺序丧失和最上表面非晶化,这可能是绝热剪切变形过程中快速熔化和淬火产生的。
(4)碳化物分解与碳化物塑性变形同时发生,分解过程被解释为基体流动产生的界面磨损与碳化物细化/碎裂的协同过程。随着塑性变形程度的增加,变形碳化物中的Cr浓度不断降低,这是由于碳化物的连续分解和碳化物与马氏体基体的机械混合所致。
免责声明:本网站所转载的文字、图片与视频资料版权归原创作者所有,如果涉及侵权,请第一时间联系本网删除。
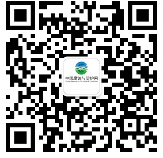
官方微信
《中国腐蚀与防护网电子期刊》征订启事
- 投稿联系:编辑部
- 电话:010-62316606-806
- 邮箱:fsfhzy666@163.com
- 中国腐蚀与防护网官方QQ群:140808414