导读:本文研究了流变挤压 5087 合金的微观结构演变引起的力学性能和强化机制。经过3道次后,对合金有明显的晶粒细化作用,平均晶粒尺寸由45.6 μm下降到2.5 μm;合金的极限抗拉强度(UTS)和屈服强度(YS)分别增加到362.8 MPa和234.6 MPa。变形过程中产生的位错壁促进了低角度晶界 (LAGB) 的形成。累积应变加速了低角度晶界 向高角度晶界 (HAGB) 的转变。位错强化和晶界强化主导了合金屈服的增强。
纯铝 (Al) 及其合金被认为是用于减轻结构重量和能耗的钢替代材料。Al-Mg 合金是一种商业变形铝合金,由于其具有竞争力的强度重量比、良好的耐腐蚀性和优异的可焊性,已广泛应用于航空航天、航海、汽车和电子领域。为满足上述领域的需要,对Al-Mg合金的力学性能提出了很高的要求。提高Al-Mg合金中的Mg含量被认为是提高力学性能的有效途径。然而,由粗晶粒和次生相引起的延展性差和高加工硬化率(WHR)仍然是高镁含量的铝镁合金后续工艺面临的挑战。因此,有必要开发一些新的策略来获得具有高机械性能的Al-Mg合金。
基于此,东北大学、大连交通大学管仁国教授团队研究了通过 累积连续挤压成型流变挤压 5087 合金的微观结构演变和力学行为。讨论了CDRX生成的α- Al基体的晶粒细化效果。揭示了微观结构诱导的强化机制。研究了显微组织的变化导致合金力学性能的变化。讨论了CDRX和二次相引起的α- Al细化。揭示了由显微组织引起的强化机制。这项工作的目的是提供一种策略来生产兼具强度和延展性的 Al-Mg 合金。在 ACEF 之后,发现流变挤压 5087 合金具有显着的晶粒细化效果。对于 ACEFed 合金的 3 道次,平均晶粒尺寸从 45.6 μm 减小到 2.5 μm,UTS 和 YS 从 293.5 MPa 增加到 362.8 MPa,分别形成 128.9 MPa 到 234.6 MPa。相关研究成果以题“Microstructural evolution and strengthening mechanism of Al–Mg alloys with fine grains processed by accumulative continuous extrusion forming”发表在国际著名期刊Journal of Materials Science & Technology上。
链接:https://www.sciencedirect.com/science/article/pii/S1005030222004182
图 1。示意图显示了通过连续流变挤压和 ACEF 制备 5087 合金丝的过程。从位置 I、II 和 III 采集的试样用于显微组织观察。
冷却水系统的流量为 20 L/min。通过红外温度计测量的 ACEF 屏障和末端的温度分别约为 300°C 和 285°C。为了研究合金在 ACEF 过程中的微观组织演变,在轮靴间隙的不同位置(位置Ⅰ-Ⅲ)沿剪切方向(SD)采集试样,如图 1 所示。此外,从与挤压方向(ED)平行的中心区域取出淬火后经受不同 ACEF 道次的试样。
图 2。(ac) 流变挤压 5087 合金在 ACEF 过程中不同位置的晶粒取向分布的 IPF 图、(df) 晶粒尺寸统计和 (gi) 相邻晶界的取向角:(a, d, g) 位置Ⅰ;(b, e, h) 位置 II;(c, f, i) 位置 III。(ac) 中的黑线和白线分别代表 HAGB 和 LAGB。
在第一次 ACEF 道次的位置Ⅰ-Ⅲ的试样被收集在轮蹄间隙中,研究流变挤压 5087 合金在 ACEF 过程中的显微组织演变。图 2显示了 ACEF 期间流变挤压 5087 合金在不同位置的晶粒取向分布、晶粒尺寸统计和相邻晶界取向角的反极图 (IPF) 图。流变挤压合金显示出均匀的微观结构,在中心和边缘区域具有类似的细小和等轴晶粒,如补充图 S2 所示。在 ACEF 之前,在合金的 IPF 图(位置Ⅰ)中观察到平均晶粒尺寸为 45.6 μm 的细等轴晶粒。随着挤压轮的转动,轮靴间隙中的合金进一步变形。在位置 III 的阻挡块处,合金的流动方向发生变化,开始等通道角挤压。如图2(c,f)所示,与位置II相比,细长晶粒和LAGB的比例降低。同时,平均晶粒尺寸从 34.9 μm 减小到 24.0 μm。HAGB 的比例和平均取向角分别增加了 27.1% 和 19.0%,如图 2 (i) 所示。
图 3。(a, d) 显示晶粒取向分布的 IPF 图;(b, e) 粒度统计;(c, f) 流变挤压 5087 合金经过不同 ACEF 道次加工后的取向误差角:(ac) 1 道次;(df) 3 次传球。
图 3 (a) 显示了流变挤压 5087 合金在 1 道次后经受 ACEF 的 IPF 图。与流变挤压 5087 合金相比,晶粒细化并观察到少量 LAGB。同时,平均晶粒尺寸减小到 20.1 μm,如图3(b)所示。此外,如图 3(c)所示,HAGB 的比例和平均取向角分别增加到 56.6% 和 23.9° 。为了进一步研究经过多道次 ACEF 工艺的合金的晶粒细化,将合金再次送入轮靴间隙 3 道次。如图3(d, e),观察到显着的晶粒细化效果,平均晶粒尺寸减小到 2.5 μm。此外,根据EBSD数据统计,得到65.4%的HAGBs分数和27.7°的平均取向角,如图3(f)所示。流变挤压 5087 合金在 ACEF 期间不同位置和道次的平均晶粒尺寸、HAGB 分数和平均取向差总结在表 2中。
图 4。ACEF前后流变挤压5087合金的DRX分布及统计结果:(a)位置Ⅰ;(b) 位置二;(c) 立场三;(d) 1 次通行证;(e) 3 次通行证;(f) 不同职位的统计结果。
图 4显示了流变挤压 5087 合金在 ACEF 期间不同位置和道次的 DRX 分布和统计结果。在流变挤压 5087 合金中观察到一些亚结构和变形的微观结构,如图 4(a)所示。从Ⅰ位到Ⅲ位,再结晶晶粒的比例从59.7%先下降到11.4%,然后增加到30.9%,而变形组织的比例则呈现相反的变化趋势。
图 5。ACEF前后流变挤压5087合金的SEM显微照片和XRD分析:(a)流变挤压合金;(b) 通过 ACEF 1 次后;(c) ACEF 3 次通过后;(dg) (a)中红色方块区域对应的EDS图扫描结果;(h) (a)中红色箭头标记的白色相的相应EDS结果;(i) ACEF前后合金的XRD分析。
图 5显示了流变挤压 5087 合金在 ACEF 之前和不同 ACEF 通道之后的 SEM 显微照片、EDS 结果和 XRD 分析。在流变挤压合金中观察到具有块状或近球形形态的小尺寸白色二次相,如图5(a)所示。不同形貌的两相的平均尺寸分别为4.5 μm和1.5 μm。同时,一些体相在连续流变挤压过程中破裂(见图5(a)中的插图)。经过 1 次 ACEF 后,体相不断破碎和细化,而近球形相变成球形相,如图5(b)所示。
图 6。TEM 显微照片显示了ACEF 前后流变挤压 5087 合金中的 Al 6 (Mn, Fe) 相、位错和(亚)晶界:(a,d)流变挤压合金;(b, e) ACEF 1 次通过后;(c, f) 经过 3 次 ACEF 后。Al 6 (Mn, Fe) 相、位错和(亚)晶界分别由蓝色、红色和黄色箭头表示。(ac) 和 (df) 分别代表变形区和再结晶区。(a) 中的插图是 Al 6 (Mn, Fe) 相的 SAED 图案。
图 6显示了 TEM 图像,显示了ACEF 前后流变挤压 5087 合金中 Al 6 (Mn, Fe) 相和位错的形态。选区电子衍射 (SAED) 图案表明该相被确认为 Al 6 (Mn, Fe) 相[23]。在图6 (a)中观察到具有被缠结位错包围的多边形形态的破裂Al 6(Mn,Fe)相,并且相的平均长度小于1μm。在流变挤压的 5087 合金中经过 1 次 ACEF 后观察到平均直径约为 50 nm 的Al 6 (Mn, Fe) 相,如图 6所示(b)。
图 7。(a) ACEF 前后流变挤压合金的机械性能变化和 (b) 真应力与真应变。
图 7显示了 ACEF 前后流变挤压合金的机械性能和真实应力与真实应变的变化。在拉伸变形过程中观察到与溶质镁原子和合金中移动位错之间的相互作用有关的代表性 Portevin Le Chatelier (PLC) 效应[24]。在 ACEF 之前,流变挤压合金的 UTS、YS 和 EL 分别为 293.5 MPa、128.9 MPa 和 44.4%。ACEF后合金中UTS和YS持续增加,EL部分下降。对于经过 3 次 ACEF 后的合金,获得了显着的抗拉强度提高和适度的延展性(UTS 为 362.8 MPa,YS 为 234.6 MPa,EL 为 32.5%)。表3列出了流变挤压 5087 合金在不同 ACEF 道次前后的力学性能。此外,还测量了 2 次 ACEF 后合金的拉伸性能,如补充图 S4 所示。
图 8。显示 ACEF 前后流变挤压合金在室温下的断口形貌的 SEM 图像:(a) 流变挤压合金;(b) 通过 ACEF 1 次后;(c) ACEF 3 次通过后。
图 8展示了流变挤压合金在室温下 ACEF 前后的断裂形态。在断裂表面上发现了典型的凹坑断裂特征。因此,所有合金的拉伸断裂模式都被确定为延性断裂。同时,观察到一些Al 6 (Mn, Fe) 相分布在凹坑底部。具有深而均匀的等轴凹坑的断口如图 8(a)所示,表明流变挤压 5087 合金具有良好的延展性。ACEF之后,凹坑有变浅的趋势,如图8(b,c)所示。这意味着ACEF后合金的延展性下降,这与上述拉伸试验结果一致。
图 9。流变挤压合金在 3 次 ACEF 前后计算和测量的 YS 增量值的比较。
测量和计算的 YS 增量的比较显示在图 9中。计算得到的 YS 强度增量为 119.0 MPa,这与实验测量的 YS 增量(105.7 MPa)非常吻合。测量结果和计算结果之间的差异可能是由于强化机制之间的相互作用造成的。同时,位错强化和晶界强化在 ACEFed 合金中的 YS 增强中占主导地位。图 10显示了多道次 ACEF 过程中合金的微观结构演变和强化机制的示意图。
图 10。流变挤压合金在多道次 ACEF 过程中的显微组织演变和强化机制示意图。
图 11。(a) ACEF前后流变挤压合金的WHR变化;(b) 基于真应力-真应变曲线的双对数曲线。
总之,ACEF 3 次通过后,HAGBs 的比例和平均取向差分别增加到 65.4% 和 27.7°。这与变形过程中位错壁的形成有关。同时,纳米尺寸的Al 6 (Mn,Fe)相由于钉扎效应抑制了晶粒的生长。位错强化和晶界强化主要是 ACEFed 合金中 YS 增强的原因。ACEF后获得的细化晶粒和二次相有利于延展性保持。ACEF 策略有助于生产兼具强度和延展性的 Al-Mg 合金。
免责声明:本网站所转载的文字、图片与视频资料版权归原创作者所有,如果涉及侵权,请第一时间联系本网删除。
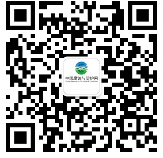
官方微信
《腐蚀与防护网电子期刊》征订启事
- 投稿联系:编辑部
- 电话:010-62316606-806
- 邮箱:fsfhzy666@163.com
- 腐蚀与防护网官方QQ群:140808414