沙钢联合东南大学研发海洋工程用铁素体贝氏体双相耐蚀钢筋
2023-10-19 15:52:14
作者:贾生晖 来源:腐蚀与防护
分享至:
港口码头、桥梁、临海建筑等海洋工程腐蚀失效日趋严峻。随着海洋强国战略的进一步实施,海洋工程朝着大型化、长寿命化方向发展,其腐蚀失效及防护问题亟待解决。
海洋工程腐蚀失效行为的影响因素众多,包含钢筋自身的抗腐蚀性能、混凝土的抗渗性以及服役环境中侵蚀性离子的浓度等。对于钢筋混凝土结构来说,已有数据表明,钢筋自身的抗腐蚀性能差是引发锈蚀的首要因素。钢筋在高盐、高温、高湿作用下,易发生锈蚀,锈蚀产物体积膨胀,引发混凝土胀裂,导致海洋工程腐蚀失效。双相不锈钢耐蚀性好,但价格很高;耐候钢成本低,但耐蚀性不足;涂层钢筋不易加工、焊接,且与混凝土的握裹力差、施工过程易破损,安全隐患大(表1)。可见,现有产品和防护技术尚无法完全解决海洋工程腐蚀失效问题。
表1 国内外海洋工程混凝土用钢筋现状
钢筋抗腐蚀性能不足,不仅造成巨大的经济损失,降低了建筑结构的安全性能,还加大了资源和能源的消耗,加剧了环境负担。研制和使用高耐蚀钢筋刻不容缓,是解决海洋工程腐蚀失效的有效方法,对确保海洋工程耐久性具有重要意义,已成为我国钢铁行业品种提档升级的标志性任务。基于上述背景,江苏沙钢集团有限公司联合东南大学开展海洋工程用长寿命高耐蚀钢筋研发,一方面通过超低碳多元素复合耐蚀设计,结合炼、轧工艺和现场施工条件,开发出海洋工程混凝土用高耐蚀钢筋和关键应用技术;另一方面研究耐蚀钢筋与混凝土之间的协同关系,建立耐蚀钢筋腐蚀评价体系和服役寿命预测平台,形成耐蚀钢筋混凝土应用技术规程,引领行业技术进步,为海洋工程混凝土结构耐久性不足问题的解决提供新思路。针对耐蚀钢筋产品在海洋环境下服役寿命不足的问题,系统研究了钢筋在混凝土结构中全寿命周期的腐蚀行为和耐蚀机理,阐明了合金元素、组织形态及钝化膜结构对钢筋耐蚀性的影响规律,突破了传统合金元素耐蚀机制,针对严酷海洋服役环境,率先提出了“超低碳铬钼多元复合耐蚀”成分设计体系,揭示了影响钢筋钝化行为的关键因素,开发了铁素体贝氏体双相组织调技术,攻克了超低碳高合金钢采用“转炉-LF-RH”工艺冶炼和焊接容易出现冷裂纹的关键技术瓶颈,解决了焊接接头与母材性能存在差异性难题,开展了实际服役环境下钢筋耐蚀性定量评价技术和服役寿命预测技术研究,形成了耐蚀钢筋混凝土关键应用技术。项目总体技术方案如下图所示:
图1 项目总体研究方案
(1) 钢筋高耐蚀高塑性低成本成分设计及组织调控技术针对严酷海洋环境,基于严酷环境下钢筋的钝化与腐蚀行为研究,发展了混凝土结构中钢筋全寿命周期连续耐蚀理论研究,形成了耐蚀钢筋腐蚀自抑制技术,构建了超低碳铬钼多元复合耐蚀成分体系。开发了新型耐蚀钢筋铁素体贝氏体双相组织调控技术及高塑性调控技术,获得了复合钝化膜+复相组织的耐蚀钢筋。新型耐蚀钢筋耐海水腐蚀性能比普通钢筋提高10倍以上,与马氏体不锈钢410相当,最大力总延伸率Agt≥11%,成本比马氏体不锈钢410低20%,兼顾了“高耐蚀”“高塑性”和“低成本”。
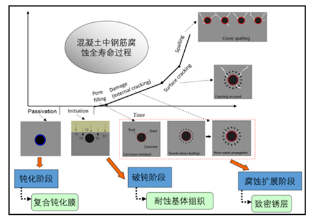
图3 新型耐蚀钢筋钝化膜Mott-Schottky曲线
图5 新型耐蚀钢筋过冷奥氏体连续冷却转变曲线
采用“转炉-LF-RH”工艺生产超低碳高铬合金钢全流程协同控制方法,基于合金烘烤、多点分散合金加料模型、钢温精准控制研究,开发了超低碳高铬合金钢转炉高效冶炼技术。明确真空度、冶炼时间和吹氧流量之间的关联,开发了超低碳高铬合金钢精炼深脱碳技术。铬收得率由70%以下提升至90%以上,精炼时间由130 min以上降低至100 min以下,解决了热量平衡、冶炼周期长等难题,实现了产业化制造。通过系列试验,获得焊接工艺参数如顶锻压力、焊后冷却速度等与焊接接头组织及力学性能的定量关系,开发了基于焊接接头组织控制的新型耐蚀钢筋专用固态焊接技术,突破了高合金钢熔化焊接易出现冷裂纹的技术瓶颈,解决了焊接接头与母材性能存在差异性难题,并实现了工程应用。针对耐蚀钢筋与普通钢筋以焊接、套筒连接、捆扎等不同方式连接时潜在的宏电池腐蚀倾向,基于腐蚀电化学测试的高强耐蚀钢筋宏电池腐蚀监测技术,形成钢筋/混凝土界面微化学环境调控和钢筋连接方式优化的高强耐蚀钢筋宏电池腐蚀的预防与抑制技术。
依托上述研究成果,制定T/CECS 1202-2022《耐蚀钢筋混凝土应用技术规程》,已应用于施工现场,且连接效率可提升20%以上。

图7 焊接接头低倍形貌

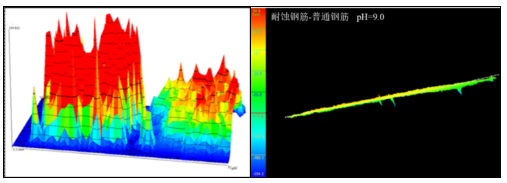
图 8 耐蚀钢筋与普通钢筋接头的SVET及DHM形貌
(4) 新型超低碳铬钼系耐蚀钢筋服役寿命预测技术开发融合电化学、盐雾、现场挂片等试验数据、借助多尺度腐蚀形态学分析,开发了钢筋混凝土结构耐蚀性定量评价技术,评价效率及精度提升50%以上。依据混凝土结构中钢筋锈蚀破坏模型,基于混凝土中氯离子的扩散传输行为及规律,构建了混凝土结构服役寿命预测平台,可接受实时监测数据、实现自动更新和预报,为重大工程应用、腐蚀行为研究及服役寿命预测奠定了基础。
图9 混凝土结构服役寿命预测平台
项目以重大需求为导向,对海洋工程用耐蚀钢筋制造及应用关键技术进行了系统研究,成功开发出具有自主知识产权的高耐蚀、高塑性、可焊接且成本低的耐蚀钢筋,并在重大工程实现应用。项目主要创新有:(1) 发明了铁素体贝氏体双相耐蚀钢筋。针对严酷海洋环境,率先构建了超低碳铬钼多元复合耐蚀成分体系,开发了铁素体贝氏体双相组织调控技术,获得了复合钝化膜+复相组织的耐蚀钢筋,其耐海水腐蚀性能比普通钢筋提高10倍以上,与马氏体不锈钢410相当,最大力总延伸率Agt≥11%,成本比马氏体不锈钢410低20%,兼顾了“高耐蚀”“高塑性”和“低成本”。(2) 开发了“转炉-LF-RH”冶炼超低碳高铬钢工艺。开发了转炉高效冶炼和精炼深脱碳技术,铬收得率由70%以下提升至90%以上,精炼时间由130 min以上降低至100 min以下,解决了热量平衡、冶炼周期长等难题,实现了产业化制造。(3) 开发了专用固态连接技术。开发了闪光对焊技术,突破了高合金钢熔化焊接易出现冷裂纹的技术瓶颈,形成了工程应用技术规程,已应用于施工现场,且连接效率可提升20%以上。(4) 构建了耐蚀性评价、服役寿命预测平台。融合电化学、盐雾、现场挂片等试验数据、借助多尺度腐蚀形态学分析,开发了钢筋混凝土结构耐蚀性定量评价技术,评价效率及精度提升50%以上。构建了混凝土结构服役寿命预测平台,可接受实时监测数据、实现自动更新和预报,为重大工程应用、腐蚀行为研究及服役寿命预测奠定了基础。本项目研究成果是高端棒材领域首个横跨防腐、冶金和轧制多学科的海洋工程用耐蚀钢筋制造及关键应用技术。采用该关键技术,成功开发出海洋工程铁素体贝氏体双相耐蚀长寿命钢筋,并实现了批量、稳定供货。近三年利用该技术开发的相关产品累计达到万吨级别,累计新增产值近1亿万元。2017年2月,规格ф10~ф25 mm耐蚀钢筋在沿海高铁通道青岛-连云港段重大节点工程胶州湾跨海大桥实现应用,主要用于桥墩和梁柱关键位置,累计使用量1000吨。2020年2月,规格ф10~ф25 mm 耐蚀钢筋在京沪高铁二线-京津冀城际铁路石横沧港段使用,主要用于桥墩和梁柱关键位置,累计使用量6000余吨。2022年2月,规格ф10~ф25 mm 耐蚀钢筋在南海岛礁某军事工程实现示范,主要用于量、板、柱等关节结构的钢筋混凝土工程中,保证了工程的顺利实施和完成。经专家评价,本项目发明的超低碳铁素体贝氏体双相耐蚀钢筋,其钢筋耐蚀设计及焊接工艺技术达到国际领先水平,这对引领行业技术进步、促进钢筋产品的升级换代具有重要示范意义。项目已获授权专利18项,发表论文25篇,软件著作权2件,主持制定国家标准1项。项目的成功实施引领了国际耐蚀钢筋的技术发展,是循环经济、智能制造和绿色发展的杰出代表,经济和社会效益巨大,应用前景广泛。
海洋强国等政策的实施,推动了海洋工程的快速发展,促进了海洋工程混凝土用耐蚀钢筋的推广应用。已实施的国家标准GB/T 34206-2017《海洋工程混凝土用高耐蚀性合金带肋钢筋》对耐蚀钢筋的具体性能指标做了明确说明与规定;已发布的T/CECS 1202-2022《耐蚀钢筋混凝土应用技术规程》对耐蚀钢筋的应用指标作了明确的规定,并将于2023年4月1日起正式实施。依托本项目技术开发的海洋工程混凝土用高耐蚀钢筋及相关成果,正在申报ISO国际标准。国家标准或技术规程的起草、实施为耐蚀钢筋的工程应用提供了保障。
免责声明:本网站所转载的文字、图片与视频资料版权归原创作者所有,如果涉及侵权,请第一时间联系本网删除。