钨铜复合材料是由不互溶的钨和铜构成的一种独特的双金属复合材料,在高压电触头、电加工电极、电子封装、核聚变、电磁推进等领域具有广泛的应用。随着科技发展和新应用领域的拓展,钨铜部件的服役环境越来越严苛,对其综合性能提出了更高的要求。而通过熔渗法等制备的传统钨铜复合材料,其粗大的组织结构和较低的力学性能严重限制了其高端应用。近年来,研究者主要利用细晶强化、第二相强化或合金化等方法提高钨铜复合材料的强度。然而,溶质原子、第二相以及晶界、相界等内界面的引入,不仅导致钨铜复合材料塑性严重恶化,还大大增强了电子散射,降低了钨铜复合材料的传导性能。因此,如何使钨铜复合材料同时具有高的强度、塑性和电导率,是领域多年来共同关注和亟待解决的关键问题。
针对这一挑战,北京工业大学韩铁龙副教授和宋晓艳教授等提出了一种创新的钨铜复合材料跨尺度多层级设计理念:在细观尺度上利用独特的自组装超细层片构型提高钨相在复合材料中的应力配分能力;在微观尺度上利用先期预处理形成的高密度位错和超细晶组织提高钨相自身的强度,并利用铜相内位错增殖和可动位错提供大的塑性变形能力;同时,借助跨尺度多层级设计产生的长程取向组织结构,保证了钨铜复合材料较高的电导和热导特性。研究团队巧妙地结合液相球磨和化学镀覆等技术实现了设计的自组装层状钨铜复合材料(SAL W-Cu)的成功制备。进一步,作者利用基于同步辐射的原位高能X射线衍射技术、扫描电镜下原位压缩技术和基于真实材料结构的有限元模拟等,对SAL W-Cu的承载形变行为、强韧化机制和传导机理进行了深入分析。该研究为获得兼具高的力学性能和物理性能等优异综合性能的双金属类复合材料提供了崭新的设计思路和实现技术。相关成果以“Simultaneous enhancement of strength and conductivity via self-assembled lamellar architecture”为题发表在国际顶刊Nature Communications上。论文通讯作者为北京工业大学宋晓艳教授,第一作者兼共同通讯作者为韩铁龙副教授。该研究得到了聂祚仁院士的指导和其带领的国家自然科学基金创新研究群体的支持。
论文链接: https://www.nature.com/articles/s41467-024-46029-w
首先,作者构建了有限元模型针对不同构型特点的钨铜复合材料的力学、电学和热学响应特性进行了定量化研究。发现钨铜复合材料的强度不仅受钨相自身的强度影响,还强烈地受钨铜两相构型特征的影响。如果某一构型中钨相的载荷配分比例较低,则钨相自身的高强度优势不能充分发挥,复合材料的强度水平有限。只有在实现钨相自身高强度的同时保证钨相在复合材料构型中具有高的载荷配分能力,才能充分发挥钨相高强度的优势,最终获得钨铜复合材料的整体高强度。同时,为了兼具高的导电导热性能,还需要独特的降低电子散射、利于电子快速输运的结构设计。为此,研究团队提出创新的自组装层片结构多层级设计理念,形成SAL结构(“self-assembled lamellar architecture”)的钨铜复合材料,记为SAL W-Cu。作者通过预处理制备了产生有高密度位错的超细晶高强度钨片,随后利用化学镀方法对钨片表面进行了均匀的铜层包覆,再利用自组装效应和短时快速烧结技术实现了致密SAL W-Cu的制备。研制的SAL W-30Cu复合材料表现出高达1.13 GPa的压缩屈服强度(约为同等测试条件下常规粗晶钨铜合金的两倍)和56 %IACS的电导率(高于导电性最好的商用粗晶钨铜合金),同时,SAL W-30Cu复合材料具有高达14%的塑性变形能力。
图1具有不同构型特征的钨铜复合材料的力学和物性的有限元模拟:a,钨颗粒增强的钨铜(a1)、钨骨架增强的钨铜(a2)和本研究的SAL W-Cu (a3)的三维周期性有限元模型;b-e,各种构型特征的复合材料中的应力分布(b)、钨相的应力分布(c)、电流密度分布(d)和热流密度分布(e)。
图2 a,SAL W-Cu复合材料的制备策略示意图;b-d,制备的SAL W-Cu复合材料的微观组织形貌及对应的元素分布。
图3 a-c,预处理获得的钨片形貌;d-h,镀铜钨片的形貌及元素分布。
图4 SAL W-Cu复合材料及镀铜钨片的内部微观结构:a-b,复合材料中钨相和铜相朝向VD方向的晶粒取向分布;c,界面结构;d,镀铜钨片中的铜纳米晶;e,复合材料内部的微结构;f,预制钨片内部的高密度位错;g,复合材料中钨相内部的高密度位错;h,SAL W-Cu复合材料内部微观结构示意图。
图5 SAL W-Cu复合材料的力学、电学性能及与其他钨铜复合材料的性能比较。
研究团队结合同步辐射技术对SAL W-Cu复合材料的变形机理和强韧化机制进行了深入研究。结果表明,钨相的屈服导致了复合材料的宏观屈服,而在SAL W-Cu发生宏观屈服时,钨相承受的载荷高达1700 MPa,是铜相承受载荷的3.8倍(450 MPa)。因此,钨相的高强度及高的载荷配分能力得到了验证。此外,同步辐射结果还表明,铜相屈服在复合材料宏观屈服之前发生,其应变会受到仍是弹性变形状态的钨相的强烈限制,进而诱发异质形变强化(HDI)效应。尽管这一效应也存在于其他构型的钨铜复合材料中,但是SAL W-Cu复合材料中的明显高的界面密度显著增强了这种强化效应。这一点由SAL W-Cu复合材料LUR曲线中出现更加明显的滞后环得到了证实。
SAL W-Cu复合材料高塑性的来源,一方面归因于自组装多级层状结构诱发的可持续的位错增殖能力,另一方面归因于该独特结构诱发的微裂纹缓冲效应。开展的原位压缩测试研究表明,在塑性变形的后期SAL W-Cu中产生了大量的微小裂纹,这些微裂纹沿着钨铜相界面扩展,与最大剪切应力方向大约呈45度,并不发生快速扩展形成主裂纹而导致复合材料断裂失效。恰恰相反,这些微裂纹的形成有效释放了局部的应力集中,促进了复合材料在整体范围内均匀的塑性变形,从而促进了复合材料整体塑性的提高。此外,这种独特的层状结构和钨相的高强度也增大了主裂纹产生所需的临界应力,进一步延缓了复合材料的断裂。
最后,自组装多级层状结构中连续的铜导电通路的存在,是SAL W-Cu复合材料具有高电导和高热导的本质原因。实测值较设计理论值还有一定的差距,其原因在于钨相和铜相中的微观缺陷(孔隙、内界面、位错等)、钨层的弯曲角和界面阻抗对SAL W-Cu电导率的影响。为评估这些影响因素的作用大小,团队开展了有限元模拟计算研究,结果表明,铜相中的缺陷是导致复合材料电导率降低的主要原因,其次是钨相中的缺陷和钨片的弯曲,而单纯的界面阻抗引起的电导率降低效应影响较小。由此提出,进一步调控铜相中的缺陷密度并减小钨片层的弯曲角度,可促进SAL W-Cu复合材料的电导率向结构设计对应的理论值提升。
图6 a,同步辐射研究原位压缩过程的示意图;b,原位压缩过程中{200}Cu和{200}W的晶面间距随应力的变化;c,原位压缩过程中钨相和铜相不同晶面的晶格应变随应力的变化;d,基于同步辐射结果计算的原位压缩过程中钨相和铜相实际承受的载荷;e,SAL W-Cu复合材料的加载卸载循环曲线。
图7 a,SAL W-Cu复合材料在不同应变下铜相和钨相中的位错密度观察;b,SAL W-Cu在制备态和断裂后的铜相和钨相中的KAM分布;c1-c2,准原位压缩过程中沿相界面的微裂纹;c3,SAL W-Cu断裂后主裂纹切过多个钨层片;d,SAL W-Cu沿PD方向压缩在应力下降发生后的微观组织特征:钨片层的屈曲和裂纹偏转、钝化、缓冲效应。
图8 SEM下的准原位压缩过程中裂纹特征及演变。
图9考虑钨相和铜相中的缺陷(孔隙、内界面、位错等)、钨层的弯曲角和界面阻抗对SAL W-Cu电导率影响的有限元模型及计算结果。
本研究得到了国家自然科学基金重点项目、国家自然科学基金创新研究群体项目、国家自然科学基金面上项目和青年项目的资助。
韩铁龙,北京工业大学材料科学与工程学院副教授、博士生导师,2020年获得天津大学材料学专业工学博士学位,2022年入选北京工业大学高层次人才计划“优秀人才”,主要研究方向为基于构型设计的金属基复合材料及综合高性能化。作为项目负责人主持了国家自然科学基金、中国博士后面上项目,同时作为骨干参与了多项国家自然科学基金项目。在Nat. Commun.、Compos. Part B: Eng.、Engineering、Carbon、J. Mater. Sci. Technol.等期刊发表SCI论文15篇,授权/公开国家发明专利7项,兼任《Tungsten》、《粉末冶金工业》等期刊青年编委。
北京工业大学宋晓艳教授研究团队多年来致力于具有稳定高性能的合金微结构设计与制备调控,形成了“合金纳米组织结构稳定性基础研究”与“工程应用”紧密结合的发展主线和学术特色。团队主持国家重点研发计划、国家自然科学基金重点、德国研究联合会基金(DFG)、北京市自然科学基金重点等项目以及多项企业委托攻关项目,成果获得省部级科技进步奖一等奖 1 项、自然科学奖二等奖 3 项、技术发明奖二等奖1项;授权和公开国际、国内发明专利100余项,高性能硬质合金规模化制备技术落地企业实现重大成果转化;于Sci. Adv.、Nat. Commun.、Adv. Mater.、Acta Mater.等期刊发表SCI论文350余篇,在国际国内学术会议上作大会/主旨/邀请报告80余次
免责声明:本网站所转载的文字、图片与视频资料版权归原创作者所有,如果涉及侵权,请第一时间联系本网删除。
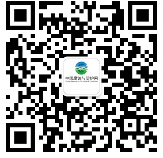
官方微信
《腐蚀与防护网电子期刊》征订启事
- 投稿联系:编辑部
- 电话:010-62316606
- 邮箱:fsfhzy666@163.com
- 腐蚀与防护网官方QQ群:140808414