导读:构建异质结构对于调整铝基复合材料(AMC)的机械性能至关重要。在这项工作中,通过操纵初始复合材料粉末的冷焊接和原位固态反应,在 AMC 中实现了多级异质结构。由此产生的微观结构具有带状粗晶粒(CG)区域嵌入细晶粒(FG)区域的特点,展示了一种异质薄片(HL)晶粒结构。此外,Al、Mg 和 CuO 之间的原位固态反应产生了粒内纳米级氧化镁颗粒,这些颗粒主要分布在 FG 中。这种独特的微观结构加剧了不同结构域之间的机械性能不匹配,从而激活了异质变形诱导(HDI)强化。值得注意的是,FG 区域需要高应力来激活位错,从而导致大块复合材料出现 “屈服下降”。研究还阐明,与 FG 结构域相比,CG 结构域在变形的早期阶段会承受更高的应力,从而导致位错壁的形成。这些位错的聚集和恢复促进了 CG 在随后的塑性变形过程中转变为原生等轴晶粒或亚结构,从而有助于复合材料的超常应变硬化。此外,氧化镁增强体在晶粒内的分布促进了位错的显著扩散,实现了应力的重新分布,从而使复合材料具有相当大的延展性。这项研究为通过协同调节晶粒结构和增强体分布配置来实现具有优异机械性能的多层次异质复合材料提供了启示。
长期以来,铝基复合材料(AMC)一直面临着强度-电导率权衡的难题。这一问题主要源于强化层在晶界(GB)处的聚集,这限制了塑性变形过程中的局部塑性流动,并导致应力集中。最近,旨在实现异质晶粒的概念已成为提高综合机械性能的一种有前途的方法。这一概念包括在细晶粒(FG)区域中加入粗晶粒(CG),从而在软域和硬域之间形成致密界面。在塑性变形过程中,由于粗晶粒具有显著的位错存储能力和裂纹容限能力,因此这种策略可大大提高样品的延展性和韧性。一旦 CG 区域出现裂纹,FG 区域的致密 GB 将有效阻止裂纹的进一步扩展 。此外,这些区域之间变形阻力的差异会导致几何必要位错(GND)的积累,从而提高流动应力。此外,FG 区域对 CG 施加的刚性约束可通过大量的异变形诱导(HDI)强化/硬化有效提高强度。上述机制的结合产生了具有异质晶粒的金属,与传统的同质晶粒金属相比,这种金属具有更优异的机械性能。
就 AMC 而言,机械性能不仅受到基体晶粒结构特性的显著影响,还受到包括几何参数、分布配置和增强体界面等因素的影响。有观点认为,加入与移动位错强烈相互作用的粒内纳米尺寸增强体可为复合材料提供卓越的加工硬化能力。值得注意的是,由 "富增强区/贫增强区 "交替组成的复合材料断裂模式从增强体-基体界面破坏转变为裂纹沿富增强区和基体之间的界面扩展,从而显著延迟了复合材料的过早断裂。然而,有效调节强化剂分布和基体晶粒结构是一项巨大的挑战。对于通过铸造或粉末冶金工艺制造的 AMC,增强材料通常分布在 GB 上。具体来说,在铸造过程中,与强化剂/液体界面相比,强化剂/固体界面具有更高的界面能,从而导致强化剂向 GB 偏移和偏析。
该研究由天津大学材料科学与工程学院赵乃勤教授、张翔、赵冬冬教授等人联合创作。
相关研究成果以“Towards understanding the microstructure-mechanical property correlations of multi-level heterogeneous-structured Al matrix composites”发表在Journal of Materials Science & Technology上
链接:https://www.sciencedirect.com/science/article/pii/S1005030224005796
图 1. Al-Mg-CuO 复合材料的形成机理和结构特征。
(a)MH 和 NH 复合材料的形成机理;(b) 和 (c) 分别为 MH 和 NH 复合材料晶粒结构的 EBSD-IPF 表征;(d) 显示 MH 复合材料整体形态的 STEM 图像;(e) MH 和 NH 复合材料晶粒尺寸的统计;(f) MH 复合材料中 FG 的代表性 STEM 图像;(f1)-(f4) (f) 的相应 EDS 图谱;(g) MgO 的 HRTEM 表征;(h) MgO 粒径统计,(i) θ 沉淀的 HRTEM 表征;(j) θ 沉淀粒径统计。
图 1(a)说明了 MH 和 NH Al-4Mg-5CuO 复合材料的形成机理。如图 S2(a,b)所示,调节硬脂酸的含量可促进铝镁复合粉末的粘附和冷焊接。冷焊后的粉末与研磨球之间的碰撞会导致粉末表面产生严重的塑性变形,产生大量位错或其他缺陷。与此同时,冷焊粉末的核心部分则表现出轻微的塑性变形,缺陷密度相对较低。复合粉末的这种独特形态造就了 MH 复合材料独特的晶粒结构。具体来说,在 MH 复合材料中,CG 嵌入 FG 区,形成了 HL 晶粒结构(图 1(b))。相反,适量的硬脂酸会延迟冷焊的开始,从而促进片状复合材料粉末的均匀混合(图 S2(c,d))。这一过程的结果是形成了 NH 复合材料,其上缀有均匀分布的等轴晶粒(图 1(c))。
图 2. MH、NH 复合材料和 HG 合金的机械性能。
工程应力链曲线;(b) MH 和 NH 复合材料的应变硬化率刻度;(c) 本 MH 复合材料与其他相关复合材料体系的力学性能比较;(d) MH 和 NH 复合材料的 LUR 曲线;(e) MH 复合材料的完整卸载-重载滞后环;(f) MH 和 NH 复合材料在不同应变下的 HDI 应力和有效应力的统计结果。
图 2(a) 绘制了样品的应力-应变曲线。MH 复合材料的极限拉伸强度 (UTS) 为 696 兆帕,断裂伸长率 (FE) 为 9.4%。值得注意的是,该复合材料在断裂前表现出均匀变形,没有明显的应变软化,横截面积减少了 1.1%(图 S3(a))。应力-应变曲线表现出一种被称为 “非连续屈服 ”的突出特征,即在达到屈服强度后出现瞬时应力降低,随后在塑性变形阶段应力逐渐增加[20]。HG 合金表现出与 MH 复合材料类似的变化特征,尽管 UTS 较低,仅为 145 兆帕。相比之下,NH 复合材料的 UTS 为 633 兆帕,而 FE 仅为 MH 复合材料的 58.3%,显示出连续屈服。这表明 MH 复合材料的 “非连续屈服 ”主要源于 HL 晶粒结构。
图 3. MH 复合材料的变形微观结构。
(a)-(e) 第一阶段屈服前:(a) CG 和 FG 的 STEM 图像;(b) CG 的代表性微观结构;(c) CG 中氧化镁颗粒的 HRTEM 图像;(d) (c) 中标记帧 D 的 IFFT 表征;(e) FG 区域的代表性微观结构。(f)-(j) 与第二阶段相对应的不连续屈服:(f) CG 带和 FG 区域的整体形态;(g) (f) 中记录的放大标记框 G;(h) FG 区域的整体形态;(i) (h) 中记录的放大标记框 I;(j) (f) 中记录的放大标记框 J。(k)-(m) 第三阶段的断裂:(k) 整体形态,插入的图像为相应的 DF-STEM 图像;(l) 位错微观结构;(m) 位错单元形态。
图 3 显示了 MH 复合材料的变形微观结构。在屈服之前(图 3(a-e)),即图 2(a,c)中的第一阶段,主要在 CG 区观察到位错(图 3(a,b))。这表明与 FG 区域相比,CG 区域承受的微应力水平相对较高。图 3(b) 显示了 CG 中的位错累积。除了 GB 与位错之间的相互作用外,作为有效屏障的氧化镁颗粒也促进了位错的扩散。通过反快速傅立叶变换(IFFT)图像分析(图 3(c,d)),在氧化镁周围的铝基体中观察到的位错进一步证实了这一点。FG 的晶粒尺寸较小,而且 FG 区域内的氧化镁密度较高,这加剧了 CG 与 FG 之间的强度不匹配[7]。因此,来自 FG 区域的约束迫使 CG 带产生更多的 GND,从而导致高背应力[29]。这最终增强了对宏观塑性的抵抗力,提高了复合材料的屈服强度。
图 4. MH 复合材料的 EBSD 表征。
分别为(a)未变形和(b)断裂 MH 复合材料的再结晶图;(c)断裂 MH 复合材料的局部错向图;未变形和断裂 MH 复合材料的(d)晶粒类型和(e)GB 错向角的统计结果;(f)MH 和 NH 复合材料的 Schmid 因子。(g) MH 复合材料在应变变形过程中的微观结构演变示意图。
总之,通过对复合材料粉末的初始冷焊和原位固态反应的操作,成功制备了一种 MH Al-4Mg-5CuO 复合材料,其 UTS 为 696 MPa,FE 为 9.4 %。复合材料的微观结构呈现出多层次的异质性,带状 CG 区嵌入 FG 区,在晶粒层形成异质薄片结构。此外,原位生成的纳米级氧化镁主要分布在 FG 的晶粒内部,形成了独特的分布结构。这种错综复杂的微观结构加剧了不同晶域之间的机械性能不匹配,从而导致了高密度互连的高度强化。由于 FG 区域没有移动位错,因此需要更高的应力来实现屈服,这也是块状复合材料 “屈服下降 ”的原因。此外,CG 在初始变形过程中积累了高应变,导致位错壁的形成,从而促进了位错的聚集和恢复。这一过程有利于 CG 转变为原生等轴晶或亚结构,从而极大地促进了复合材料的加工硬化。氧化镁颗粒与位错之间的相互作用有助于位错在晶粒内部的扩散。晶粒内位错的积累缓解了异质晶粒界面的应力集中,从而实现了微观应力的重新分布。这项工作为通过设计多层次异质结构实现复合材料的优异机械性能提供了全面的理解。
免责声明:本网站所转载的文字、图片与视频资料版权归原创作者所有,如果涉及侵权,请第一时间联系本网删除。
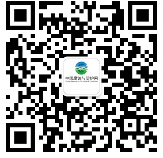
官方微信
《腐蚀与防护网电子期刊》征订启事
- 投稿联系:编辑部
- 电话:010-62316606
- 邮箱:fsfhzy666@163.com
- 腐蚀与防护网官方QQ群:140808414