导读:非均质微结构设计已成为解决结构材料强度延性困境的一种普遍策略。然而,实现可定制的异质微结构仍然很困难。本文采用简单的粉末冶金方法,在软铝基体中引入硬质高熵合金颗粒,构建了铝基复合材料(AMC)的“双金属”非均相结构。利用相互扩散和自组织策略,原位合成具有特殊核壳结构的增强材料,在复合材料内部形成多层非均质结构。结果表明,在塑性变形过程中,微观组织的非均匀性对调节应变梯度和保持显著的应变硬化能力起着有效的作用。此外,核壳增强外壳的纳米颗粒层具有良好的韧性和承载能力,能够有效地容纳变形和抑制裂纹扩展。本研究为非均质结构的复合材料设计提供了一种可行的方法,并为强韧性金属基复合材料的设计提供了概念框架。
1.介绍
颗粒增强铝基复合材料(PRAMCs)因其易于批量生产和优异的力学和物理性能而受到广泛关注(Geng et al ., 2023;Ma et al ., 2023)。目前已成功应用于军事、电子封装、汽车等领域(Li et al ., 2024;Sun等,2022a;Yang et al, 2023)。然而,在PRAMCs的发展过程中,由于颗粒团聚和界面破坏,无法满足强度和延性之间的平衡。例如,在基体变形过程中,应力集中会在基体/颗粒界面附近积累,在界面处形成空洞并聚集成裂纹,导致体块复合材料过早失效(Guan et al ., 2020;Li et al ., 2018;Xing et al ., 2022)。特别是在高强度时,低塑性突出(Liu et al ., 2024b;马和朱,2017;Tang等,2024;Wei et al ., 2014),已成为制约PRAMCs发展和应用的关键因素。迄今为止,如何同时提高PRAMCs的强度和延展性仍然是一个挑战。
图1
(a)纯Al粉末的SEM图像和(b)尺寸分布。(c) CrMnFeCoNi HEA粉末的SEM图像和(d) HEA粉末的粒度分布。(c)所示为HEA粉末的EDS结果,表明HEA颗粒中Cr、Mn、Fe、Co、Ni元素的原子百分数均在20%左右。
近年来,非均质结构设计已成为平衡金属材料强度与延性的有效策略(Nie etal ., 2023;Wan等,2024a;Wang et al ., 2023;吴等,2022,2023a;朱和吴,2023)。基于这一策略,提出了一系列典型的非均质结构,包括梯度结构(Cheng et al ., 2018)、多模态结构(Chen et al ., 2023;钟等人,2022),异质片层结构(施等人,2019;Wu et al ., 2015b),层压板结构(Dan et al ., 2024;Savage等人,2020;夏等,2022),金属基复合材料(耿等,2024;Liu et al ., 2018;Wu et al ., 2022),双相结构(Gao et al ., 2020;Wan et al ., 2024b)等。基本上,非均质结构材料包含强度差异显著的区域,如粗晶粒和细晶粒(Mao et al, 2024)。软区和硬区的塑性变形不相容,导致界面处的应变梯度,有利于几何上必要的位错(GNDs)的形成(Liu et al, 2023b)。这导致了额外的异质变形诱导(HDI)应力强化和HDI应变硬化,这是非均质结构材料抗拉强度和延性提高的根本原因(Wu and Zhu, 2017)。例如,Wu等人通过不对称轧制和退火工艺在Ti中引入了双峰片层结构,在不牺牲高强度的情况下获得了高拉伸延展性。结果表明,双峰片状Ti的HDI应力高达600 MPa,应变硬化能力远高于粗晶(CG) Ti (Wu et al ., 2015b)。Nie等人制备了具有富含AlN纳米颗粒的细晶粒(FG)区域和嵌入在这些FG区域中的带状CG区域的多尺度非均质amc。独特的双级HDI强化硬化是强度-延性协同的主要原因(Nie et al, 2023)。因此,通过非均质结构工程提高碳纤维材料的力学性能具有重要意义。
然而,精确控制金属基体中粗细晶粒(包括尺寸、体积分数和分布)的共存并不是一件容易的事情,通常需要适当的塑性变形和精细的退火处理相结合。例如,近年来,通过使用各种创新的加工技术,包括剧烈塑性变形、脉冲电沉积(Shen et al ., 2021)、粉末触变成形(Zhang et al ., 2022b)和双峰铣削(Sharma et al ., 2022)等,制备了各种异质结构材料。这些相对复杂的加工方法限制了异质结构金属的大规模生产和应用。
事实上,金属基复合材料本质上是一种非均质结构,在软基体中嵌入了硬增强材料(Zhu etal, 2021)。然而,在传统的PRAMCs中,硬陶瓷颗粒不参与变形,导致基体/颗粒界面处应变梯度过大,界面过早脱落(Bao et al ., 2023;Liu et al ., 2024c),这阻止了材料表现出HDI强化和硬化(Zhu and Wu, 2023)。为了防止界面破坏,有必要采用具有塑性变形能力的金属颗粒作为加固材料。近年来,多主高熵合金(HEAs)引起了社会各界的广泛关注(Diao等,2024;Fan等,2020;刘等,2024a;Tung et al ., 2024)。与传统合金材料相比,HEAs具有高硬度、高强度、高热稳定性和优异的耐腐蚀性等诸多优点(George et al, 2019;Miracle and Senkov, 2017;Xing等人,2023)。此外,与陶瓷颗粒相比,高熵合金颗粒具有非常高的塑性变形能力。因此,HEA颗粒是铝基复合材料的潜在增强剂。此外,优化增强筋与基体之间的界面结构是缓解局部应力集中、实现强荷载传递能力和强延性协同的关键(Guo et al ., 2022;Han et al ., 2020;Luo等,2023;Ma等人,2023;Sun et al ., 2022b)。例如,Liu等人报道了CoZrB金属玻璃纳米颗粒增强的AMCs,其中在基体和颗粒之间存在无定形夹层,改善了应力传递和应变分配,进而改善了强度-塑性协同作用(Liu等人,2024c)。值得注意的是,与AMCs中传统的金属增强颗粒不同,HEAs通常含有至少5种主要元素,并表现出独特的缓慢扩散效应(Fan etal ., 2020;Shi等人,2019),这为界面结构的设计和调整开辟了许多可能性。
本文提出了一种通过在软铝基体中引入硬质高熵合金颗粒来制备具有“双金属”非均相结构的AMCs的新策略。通过控制烧结温度,合成了具有特殊核壳结构的增强材料,有效地克服了复合材料的强度-延性权衡问题。与没有核壳结构的HEA颗粒增强的碳纤维相比,核壳颗粒增强的碳纤维的抗拉强度和塑性分别提高了48%和24%以上。强度的提高主要是由于多个非均质界面产生的高HDI应力。独特的双层壳层的形成可以实现增强材料与基体的共变形,减少基体中的应力集中,延长裂纹扩展距离,从而使复合材料具有良好的延性。此外,多种非均相界面的引入赋予了AMCs优异的HDI强化/硬化能力。
2.实验程序
2.1原材料
原料为纯铝粉和CrMnFeCoNi HEA粉。采用气雾法制备了纯度为99.9%的CrMnFeCoNi HEA粉末。粉末颗粒形状接近球形,直径约为7.0 μm。纯铝粉纯度为99.95%,接近球形,直径约为20 μm。图1为纯Al和CrMnFeCoNi HEA粉末的形貌和尺寸分布。
2.2复合材料制造
首先,用行星球磨机将纯铝粉与CrMnFeCoNi HEA粉(HEA粉的体积分数为2%)均匀混合。磨球为3mm氧化锆球。氧化锆球与氧化锆粉的质量比为10:1。球磨时间为10 h,球磨速度为200 r/min。经球磨后,将复合粉末装入圆柱形石墨模具。采用火花等离子烧结系统(SPS, LABOX-650F)在真空环境下烧结复合粉末。烧结温度分别为560℃、580℃和600℃。保温时间为15min,压力为50mpa。最后,得到了块状的CrMnFeCoNi/Al复合材料。为方便起见,C-560、C-580和C-600分别用于560、580和600℃烧结的复合材料。
2.3描述
在SLFL-100 kN万能电子试验机上,以恒定应变速率室温下进行骨样单轴拉伸试验。骨形标本的标尺尺寸为长10 mm,宽2 mm,厚1.5 mm。至少进行了三次拉伸试验,以确保数据的可重复性。在AGS-X 10 kN试验机上进行了加载-卸载-再加载(LUR)拉伸试验,循环应变间隔为1%。加载和卸载速率均为0.4 mm/min,每次卸载的终止载荷为40 N。采用Bruker Hysitron TI980仪器,配上Berkovich压头,测试HEA芯、壳和Al基体的硬度。在连续刚度测量模式下,应变速率为0.05 每秒。
图2
(a) C -560, (b) C -580, (c) C -600复合材料的SEM图像,显示了复合材料的显微组织演变和增强分布。(d) HEA芯、壳和Al基体的荷载-深度曲线。
采用Cu Kα辐射能谱仪(EDS)和x射线衍射仪(XRD, MiniFlex600)对粉末和烧结体材料进行了物相和元素分析。利用扫描电子显微镜(SEM, Nova Nano 450)观察了原料的形貌、HEA/Al复合材料的微观组织、铝基体内HEA的分布以及拉伸试样的断裂形貌。在装有Oxford Symmetry S2 EBSD探测器的SEM (SEM 5000Pro)上进行了电子后向散射衍射(EBSD)表征。EBSD的电压、电流和光束步长分别为20 kV、3.2 nA和0.12 μm。采用聚焦离子束(FIB, 30kv, Thermo Scientific Scios 2)系统制备透射电镜样品。然后,利用0.5 nA ~ 10 pA的离子束电流将薄片厚度减小到70 nm。在200 kV加速电压下,采用高分辨率透射电镜(HRTEM, Tecnai G2 F30 S-TWIN)对复合材料的微观结构和界面结合进行了表征。
2.4计算方法
利用维也纳从头算模拟软件包(Kresse和furthmller, 1996),利用基于密度泛函理论(DFT)的第一性原理计算,研究了壳组分相(型相)本征增厚的潜力。选择Perdew- burke - ernzerhof (PBE)形式来表示交换相关能(Perdew et al ., 1996)。离子-电子相互作用用投影增强波(PAW)方法描述(Blochl, 1994)。基于收敛性检验,采用基于Monkhorst-Pack格式的2 × 4 × 3 k点网格,平面波截止能量设为500 eV。离子力和电子能的收敛准则分别为0.01 eV/Å和eV。本文根据应力-应变函数,根据Hooke定律计算型相的弹性常数(Wang et al ., 2021)。型相对应的体积模量(B)、剪切模量(G)和杨氏模量(E)可以通过Voigt-Reuss-Hill近似得到(Colmenero et al ., 2017)。有关DFT计算的更详细信息可在补充材料中找到。
为了说明壳的形成对复合材料局部应力集中和裂纹扩展行为的影响,采用代表性体积元(RVE)方法进行了有限元模拟。采用弹塑性von Mises本构模型。对于C-560和C-580复合材料,RVE由Digimat/FE软件生成。RVE模型如图补充图S3a和b所示。球形HEA颗粒和球形核壳增强颗粒随机嵌入Al基体中。模型面积为200×200 μm,颗粒体积分数为2%,粒径为8 μm,岩心直径为2 μm。对于两种RVE模型,网格尺寸约为0.5µm。总元素数约为105。利用Abaqus/Explicit软件对RVE模型进行仿真,在RVE模型上施加对称边界条件(SBC)作为单轴拉伸。在RVE上边缘,所有节点沿y方向进行位移,如图S4所示。采用平面应变单元(CPS4R + CPS3)。在壳体上应用了最大主应力准则。元件达到某一阶段相应的损伤判据后将被删除。有限元模拟的更多信息可在补充资料中找到。
图3
C-580复合材料的TEM表征:(a) BF-TEM图像显示HEA核心和内壳。(b-g)对应(a)的Al、Fe、Co、Ni、Cr、Mn元素映射,HEA核包含Fe、Co、Ni、Cr、Mn元素,内壳层包含Al、Fe、Co、Ni、Cr、Mn元素。(h) HEA核心HRTEM图像。(i) FFT后(h)区衍射斑,HEA核心为FCC结构。(j)内壳能谱分析结果。
3.结果
3.1. CrMnFeCoNi /Al复合材料的显微组织特征
图2为C-560、C-580和C-600复合材料的SEM图像。可以看出,复合材料的界面结构随烧结温度的变化而变化。如图2a所示,当烧结温度为560℃时,CrMnFeCoNi颗粒与Al基体之间没有明显的反应层,这是由于低烧结温度下产生新相的能量不足。当烧结温度升高到580℃时,可以观察到Al基体与CrMnFeCoNi颗粒之间存在明显的界面层(图2b)。HEA增强颗粒呈三层核壳结构,由HEA核、HEA核表面的厚壳(内壳)和外围连接Al基体的锯齿状结构(外壳)组成。这表明,当烧结温度升高时,由热引起的原子扩散导致了元素在Al基体和CrMnFeCoNi颗粒之间的定向传递。当烧结温度达到600℃时,CrMnFeCoNi颗粒与Al基体之间的扩散变得更加明显,导致HEA核心消失。强化颗粒形成双层核壳结构(图2c)。此外,复合材料的低倍扫描电镜图像显示,近球形的CrMnFeCoNi颗粒均匀分布在Al基体中(图S1)。采用纳米压痕法测量不同层的硬度。如图2所示,结果表明HEA核心的硬度为~10.4 GPa,而内壳和外壳的硬度分别为~6.7和~6.1 GPa。Al基体的硬度最低,为~1.18 GPa。
图4
C-580复合材料的TEM表征:(a) BF-TEM图像显示了增强层的内壳层和外壳层,以及增强层/Al界面。增强材料的内壳、外壳和周围的Al基均呈现纳米颗粒结构。(b-g)对应(a)的Al、Fe、Co、Ni、Cr、Mn元素映射,外层主要含有Al、Fe、Co、Ni元素,以及少量Cr、Mn元素。(h) (a)中虚线矩形区域的高倍透射电镜图像,虚线圆圈表示不同成分的颗粒。(h)中标记的颗粒对应的HRTEM图像(i-k)和SAED图案(l-n)。
图5
纯Al和CrMnFeCoNi/Al复合材料的EBSD结果。IPF图显示了(a)纯Al、(b) C -560、(c) C -580和(d) C -600的基体晶粒结构,相应的晶粒尺寸分布统计显示了平均晶粒尺寸。纯Al和C-600的(e)晶粒类型、(f)施密德因子和(g) GB取向偏差角统计。
图6
(a)纯Al和CrMnFeCoNi /Al复合材料在不同温度下烧结的工程应力-应变曲线,插图显示相应的真应变-应力曲线。(b)对应的应变硬化率-真应变曲线。
为了清晰地揭示壳体的微观结构,对其进行了透射电镜分析。HEA核和内壳的微观结构如图3a所示,对应的EDS元素映射如图3b-g所示。结果表明,HEA核心不含Al元素,并保持了其原始成分。经过快速傅里叶变换(FFT)得到的HEA磁芯[001]带轴的衍射斑表明HEA磁芯具有FCC结构(图3i)。图3j为内壳的EDS结果。Al元素在内壳层中的原子百分率为79.26 at.%。Cr、Mn、Fe、Co、Ni元素的单体含量均在4%左右。
图4清晰地显示了内外壳的微观结构。内壳和外壳中纳米颗粒的平均尺寸约为360 nm。强化颗粒周围的Al基体也呈现纳米颗粒结构。在图4 (a-g)中,亮场TEM (BF-TEM)图像和相应的EDS元素映射表明,Al, Cr, Mn, Fe, Co和Ni元素在内壳中均匀分布。外层主要包括铁、钴和镍元素,在某些区域偶尔存在Cr和Mn(用黄色虚线表示)。结合图3j内壳的EDS结果和图4 (b-g)的EDS元素映射结果,内壳中富FeCoNiCrMn的相可以识别为Al13(FeCoNiCrMn)4。这是因为Al在HEA颗粒中的扩散导致型相的形成,其中Fe位同样被Co、Ni、Cr和Mn原子共占,在以前的研究中也报道过类似的现象(He et Al, 2022;Li et al ., 2021b)。外壳由两个不同的次级相组成。一种富含Fe、Co、Ni元素,且含量显著;另一种富含Cr、Mn元素,含量较少。图4 (j, k)和(m, n)显示了两种第二相的HRTEM图像以及多区轴(z =[112]和[123])上相应的选择区域电子衍射(SAED)图。从图4m可以看出,富FeCoNi相为型相,具有单斜晶结构。结合图4 (b-g)的EDS元素映射结果,可以识别出外层富FeCoNi相为
。同样,由图4n可以看出,富CrMn相为型相。结合图4 (b-g)的EDS结果,确定富CrMn相为
3.2. CrMnFeCoNi /Al复合材料的晶粒结构表征
为了研究CrMnFeCoNi/Al复合材料的非均质晶粒结构(HGS)特征,我们检测了纯Al、C-560、C-580和C-600复合材料的EBSD反极性图(IPF)和相应的晶粒尺寸分布,如图5 - d所示。纯Al的晶粒结构以等轴粗晶为主,少量细晶(图5a)。然而,具有HGS的复合材料由细粒度和粗粒度区组成。细粒区主要分布在增强颗粒周围(如图5b-d所示)。这可以归因于球磨过程中晶粒的细化和SPS过程中HEA颗粒的粒子激发形核(PSN)效应。晶粒尺寸统计结果如图5 - d所示,纯Al的平均晶粒尺寸为1.84 μm。C-560、C-580和C-600复合材料的平均晶粒尺寸略小于纯Al,分别为1.46、1.42和1.41 μm。为了更深入地了解晶粒结构特征,选择纯Al和C-600样品进行对比分析。计算晶粒类型、施密德因子分布和晶界取向角分布,如图5e-g所示。纯Al和C-600复合材料中各类晶粒的百分比如图5e所示。C-600复合材料的再结晶率为56.6%,高于纯Al的34.9%。C-600复合材料中再结晶晶粒增多的原因是HEA颗粒通过PSN效应促进再结晶,形成细小的再结晶晶粒。纯Al和C-600复合材料的施密特因子分布特征相似,如图5f所示。纯Al的平均施密特系数略高于C-600样品。纯Al和C-600样品中大部分晶粒的施密德因子值均在0.4以上,表明滑移体系容易被激活,因此样品具有良好的延展性。与纯Al相比,C- 600复合材料中高角度晶界的比例更大(图5),这反映了HGS的形成和再结晶面积的增加。
3.3. 力学性能和断口形貌
不同温度下纯Al和CrMnFeCoNi /Al复合材料的工程应力-应变曲线如图6a所示。表1给出了不同试样的屈服强度(YS)、极限抗拉强度(UTS)和断裂伸长率(EL)的具体数值。从图6a可以看出,HEA颗粒的加入具有显著的强化效果。C-600复合材料具有最高的YS和UTS,分别为130 MPa和202 MPa,分别比纯Al高118%和106%。此外,C-600复合材料的EL也高达18.5%,仅略低于纯Al在600℃烧结时的EL。
值得注意的是,随着烧结温度从560℃升高到600℃,复合材料的极限拉伸强度和极限拉伸强度同时增加,这表明当前颗粒增强金属基复合材料的强度和延性权衡困境正在被打破。图6b为纯Al和CrMnFeCoNi /Al复合材料在不同温度下的应变硬化速率。在初始应变阶段(ε < 3%), C-580和C-600复合材料的应变硬化率明显高于C-560复合材料和纯Al,当应变小于1%和大于3%时,C-600复合材料的应变硬化率略高于C-580复合材料。在大应变下,纯Al和复合材料的应变硬化率差异逐渐减小,但C-580和C-600的应变硬化率仍大于纯Al和C-560复合材料。在6%应变下,C-600复合材料的应变硬化率是纯Al的2倍。CrMnFeCoNi/Al复合材料的高应变硬化率可能是由于其独特的非均相结构。
4.讨论
4.1. 配筋结构对力学性能的影响
为研究壳体结构对力学性能的影响,对试件拉伸变形至断裂后的壳体进行了TEM分析。图7a为内壳的BF-TEM图像,可以发现,内壳中超细/纳米颗粒的GBs非常尖锐、笔直、清晰。图7b中SAED图案的分散衍射斑点和图7c中的HRTEM图像进一步证实了超细/纳米颗粒结构和高角度GBs (Zhang et al ., 2021;Zhao et al ., 2008b)。从图7a-c可以看出,内壳中含有很大比例的大角GBs。一方面,高角度GBs可以有效防止位错滑移(Zhao et al ., 2008a)。另一方面,在内壳的纳米颗粒中,Frank-Read源的位错倍增受到明显抑制(图7a),晶界密度和面积的增加会刺激晶界滑动作为塑性变形的重要载体参与变形(Meyers et al ., 2006)。此外,从图7d、e中可以看出,在内壳的一些超细/纳米颗粒中存在不同的条纹对比和超晶格衍射(插入图7e中),这证实了在一些超细/纳米颗粒(图7e)中存在层错(SFs),而在其他超细/纳米颗粒中没有(如黄色箭头所示)。SFs的形成往往有助于提高塑性变形能力和加工硬化能力,从而提高力学性能(Guo et al ., 2021)。在这里,内壳中形成的SFs类似于纳米孪晶,有利于强化和增韧(Zhang et al, 2021)。此外,由于某些纳米颗粒中存在高密度的SFs,内壳中的纳米结构在微观结构上实际上是异质的,这使得壳纳米结构内部产生多轴应力状态,导致应变硬化增加,塑性变形过程中应变局部化延迟(Li et al ., 2017;陆,2014;Ma and Zhu, 2017;Wu et al ., 2014)。因此,由于内壳的特殊结构,它可以获得良好的韧性,然后参与塑性变形过程。
图7
C -600复合材料的TEM表征:(a)内壳的BF-TEM图像显示纳米晶结构,(b) (a)对应的SAED模式。(c)内壳高角度GBs的HRTEM图像。(d)内壳的BF-TEM图像,不含SFs的颗粒用黄色箭头标记,插图为不含SFs的颗粒对应的SAED图案。(e) (d)中SF区域的TEM图像,带有SF的晶粒用红色箭头标记,插图为带有SF的晶粒对应的SAED模式。(f)在g =(221)衍射条件下,外层的BF-TEM图像显示了位错的存在。
图8
C-600复合材料的TEM表征:(a)在外壳/Al界面附近观察到高密度的SFs, SFs用白色箭头标记。(b) (a)中Al基体区域的放大HRTEM图像,Al中原子面失配处用黄线标记,表明存在SF,插图为SF区域相应的SAED模式。(c) SFs附近区域的IFFT,显示大量的位错。
图9
复合材料在5%应变、10%应变和断裂状态下的KAM分布图:(a-c) C-560, (d-f) C-580, (g-i) C-600。复合材料内部GNDs的密度随应变的增大而增大。GNDs的增殖主要发生在增强颗粒附近和基体内部的细晶区域内。
图10
C-600的TEM图像显示了位错分布:(a) TEM图像显示,在CG区和UFG区交界面附近有高密度的GNDs。(b) CG中的高密度GNDs。(c, d)核壳增强颗粒附近的GNDs。(e)非均质界面位错积累示意图
除了在内壳中形成单孔位错外,在外壳中还观察到全位错的积累和滑动(图7f),说明外壳具有一定的塑性变形能力。此外,外壳中大量的gb也会阻碍位错的滑移,从而导致晶界强化(Zhang et al, 2021)。应考虑到壳体具有较高的承载能力,这也可以防止壳体在低应力水平下过早开裂。综上所述,与HEA核相比,两层纳米结构壳具有更好的变形能力和更高的应力承载能力。
此外,如图8(a)所示,在外壳周围的Al基体内部观察到大量的SF,这在大多数粗晶铝合金中是相对不常见的现象,因为Al具有非常高的SF能量(Yamakov et Al, 2001;Zhang et al ., 2022a)。在制备过程中,增强材料与基体之间的热膨胀系数不匹配导致界面附近产生高应力。通常,这种应力是通过在非均质界面附近形成位错来进行塑性调节的(Hou et al, 2021)。然而,在本研究中,增强层周围Al基体的晶粒尺寸过小(图4a),完美位错难以扩散,导致晶界处发射SFs,以缓解壳/Al界面处的应力集中。此外,最近的研究表明,在铝合金或AMCs中加入大量界面可以有效地降低层错能,从而降低SFs形成的阈值(Guo等,2021;Wu等,2023b;Zhou et al ., 2022)。因此,纳米晶Al基体中较大的界面体积也为SFs的形成提供了空间。图8b为SFs区域的放大图像,SFs的长度约为11nm。图8b中的插图显示了SFs的SAED模式。与晶界对位错运动的阻碍作用类似,SFs的存在降低了位错的平均自由程,从而提高了强度。此外,SFs作为位错的交汇和储存场所,促进了位错在界面附近的积累(图8c),提高了Al基体的应变硬化能力(Su et Al, 2021;Wei et al ., 2020)。综上所述,增强体内壳层和增强体周围Al基体中产生的固结力均有利于复合材料的强化增韧。
4.2. 拉伸变形下的位错分布与应变硬化
图9为不同拉伸应变下C-560、C-580和C-600复合材料的核平均错取向(KAM)分布。KAM值可以用来估计GNDs的密度,KAM值越高的地区表明GNDs密度越大(Hartel et al, 2019, 2022;Liu et al ., 2023a)。由图9可知,各复合材料内部GNDs密度随应变的增加而增加。GNDs的增殖主要发生在增强颗粒附近和基体内部的细晶区域,凸显了复合材料的结构不均匀性。此外,变形后的C-600复合材料的微应变在Al基体中的分布要比C-560复合材料均匀得多。显然,在同一应变阶段,C-600复合材料的GNDs密度更高,如图9g - 1所示。采用应变梯度理论计算了C-560、C-580和C-600复合材料的GND密度(Gao et al ., 1999;库宾和莫滕森,2003):
其中,是使用EBSD测量的局部取向偏差,u = 0.12 μm是EBSD采集中使用的步长,b = 0.286 nm是Al的Burgers向量。C-560、C-580和C-600复合材料的平均GND密度分别为。因此,在拉伸过程中,C-580和C-600复合材料比C-560复合材料积累了更多的GNDs。
C-600复合材料的位错分布表明,在拉伸变形过程中,在粗/细晶粒界面的粗晶侧和增强/细Al晶粒界面的基体侧产生了高密度的GNDs,如图10所示。具体来说,当受到施加载荷时,软粗粒区(CG)首先发生塑性变形。然而,由于周围硬超细晶(UFG)区域的限制,这些粗晶中的GNDs在粗晶和细晶之间的边界处积累,如图10a, b所示。GNDs的积累在软Al基体上产生背应力,从而阻止位错源发射更多的位错(Zhu和Wu, 2023)。这种背应力抵消了部分施加的剪应力,加强了软铝区域以承受更高水平的外部应力(Peng et Al, 2024)。也就是说,受硬UFG区域约束的软CG区域比不受约束时显得更强。此外,与CG/UFG界面类似,由于硬壳与软Al基体的硬度差异,变形过程中GNDs也会在壳/Al基体界面处积累,如图10c、d所示。不同应变下的KAM分布也证明了GNDs在壳/Al界面处的积累(图9)。使得位错难以在靠近增强的软Al基体中移动,直到外壳在更大的总应变下开始屈服(Wu et Al ., 2015b;夏等人,2022)。也就是说,当整个试样屈服时,背应力显著增加软铝的流变应力,最终提高整体屈服强度。随着塑性应变的增加,GNDs在非均质界面处不断积累(见图9),导致高应变硬化,从而保持了复合材料的延性。因此,C-580和C-600复合材料中大量的shell/Al和CG/UFG界面会导致显著的HDI强化和硬化。此外,背应力可以有效缓解壳体、UFG和CG区域之间显著的强度和塑性差异,从而激活共变形。
图11
纯Al和CrMnFeCoNi /Al复合材料的包辛格效应和HDI应力。(a) LUR应力-应变曲线。(b)放大后的LUR曲线清晰地显示了迟滞回线。(c)测定和的C-600磁滞回线示意图。(d-f)随真应变的变化。
为了评估HDI强化的贡献和高应变硬化的来源,进行了加载-卸载-再加载(LUR)拉伸试验。如图11a、b所示,复合材料的LUR曲线均存在明显的滞回,这是由Bauschinger效应引起的(Xiang and Vlassak, 2005)。其中,C-600和C-580复合材料的滞回线面积较大,而C-560复合材料的滞回线较小,说明C-600和C-580复合材料的包辛格效应更强。纯Al样品的磁滞回线可以忽略不计,说明HDI应力沿其GBs难以激活。图11c显示了C-600复合材料的典型磁滞回线。一般认为流变应力包括GND相关的HDI应力()和有效位错滑移应力(
) (Yang et al ., 2016)。和可确定为:
式中和分别为卸载屈服点和再加载屈服点对应的应力值。摩擦应力()为常数,表示为:
必须克服外加应力和摩擦应力才能使GNDs向后滑动,即:
纯Al和CrMnFeCoNi/Al复合材料的值如图11d-f所示。不同烧结温度下复合材料的
随应变的增大而增大,当真应变为5%左右时,增加趋势变缓,此时位错积累趋于饱和。当真应变为1%左右时,C-560、C- 580和C-600复合材料的
分别为56.3 MPa、83.8 MPa和87.9 MPa,当真应变为6.8%时,其
分别增加到72.5 MPa、118.1 MPa和122.5 MPa。在不同应变阶段,复合材料的
均大于
,说明HDI强化对C-580和C-600复合材料的强度起主导作用。其中,C-600的HDI应力最大,C-580次之,C-560最小,说明形成更多的壳和双峰型晶粒结构可以产生更显著的HDI强化硬化。
4.3. 加强机制
与纯Al相比,CrMnFeCoNi /Al复合材料的抗拉强度有了很大的提高。分析强化机理有助于理解微观组织与力学性能之间的关系。金属基复合材料的强化机制主要有Hall-Petch ()、载荷传递(
)、Orowan (
)和GNDs (
)强化四种。在本研究中,微米级HEA增强颗粒主要分布在晶界处,Orowan的增强作用可以忽略不计。因此,CrMnFeCoNi/Al复合材料的屈服强度(
)可由下式估算:
式中为Al基体的屈服强度,为56 MPa。可由Hall-Petch方程(Hansen, 2004)计算得出:
其中K为Hall-Petch常数,在这种情况下(对于人工智能)的值为0.04 MPa· (Hansen, 2004)。和分别代表纯Al和复合材料的平均晶粒直径。各样品的粒度如图5所示。C-560、C-580和C-600的温度分别为3.32 MPa、4.08 MPa和4.20 MPa。可以计算如下(Nardone and Prewo, 1986):
式中为Al基体的屈服强度,为53 MPa。 = 2%为增强材料的体积分数。S = 1为钢筋长径比。C-560、C-580和C-600复合材料的均为0.56 MPa。GNDs的强化源于增强材与Al基体热膨胀系数和杨氏模量的不相容(Suh et Al, 2009)。的贡献可以用下式计算(Sun et al, 2024):
其中η = 1.25为常数(Suh et al, 2009), G = 25.4 GPa为Al的剪切模量(Gubicza et al, 2007), b = 0.286 nm为Al的Burgers矢量,ρ为GNDs密度。C-560、C-580和C-600复合材料的值分别为22.7 MPa、27.3 MPa和29.5 MPa。
图12
根据式(5),计算出C-560、C-580和C-600复合材料的屈服强度分别为82.58 MPa、87.94 MPa和90.26 MPa。计算得到的C-560复合材料的屈服强度与试验结果(83 MPa)吻合较好。但C-580和C-600复合材料的屈服强度计算值明显低于实验值。这与许多研究的结果相似,因为非均质结构材料的强度和延性的良好结合不能仅仅用传统的混合规则或传统的强化机制来解释(Jiang et al ., 2016;Lai et al ., 2022;Li et al ., 2020, 2021a;Nie et al ., 2023)。C-580和C-600复合材料的额外强化贡献来自于壳体/Al界面和CG/UFG界面产生的背应力对Al基体的强化。C-580和C-600复合材料的高HDI应力也证明了这一点(图11)。由于HDI增强机制的定量解耦比较复杂,目前还缺乏量化HDI增强的理论方法。在这里,我们通过以下公式估计额外的人类发展指数加强贡献:
式中,
为HDI强化的贡献,
为每种复合材料强度的实验值
为每种复合材料强度的预测值。C-560、C-580和C-600复合材料的σHDI值分别约为0.42 MPa、34.06 MPa和39.74 MPa。因此,在C-580和C-600复合材料中,HDI强化对屈服强度的贡献占主导地位。
4.4. 管道化机制
首先,增强颗粒壳对软化或延性都有有利的影响。通常,将纯金属颗粒如Fe(Wang等人,2014;Xue等人,2015)和Ni(Wu等人,2015a)引入al基体中会导致形成金属间化合物(IMC)相,如、、等。这些IMC固有的硬脆性能往往导致复合材料的延展性低。然而,在这项研究中,添加CrMnFeCoNi多组分合金颗粒并没有产生复杂的IMC,而是主要产生了一个单一的Al13Fe4型相,其中Fe位点被Fe、Co、Ni、Cr和Mn均匀占据。我们使用基于DFT的第一性原理计算,通过在铁位点掺杂多主元素来研究Al13Fe4。图12a-c显示了和
、的优化晶体结构。
此外,利用VASPKIT工具箱计算型相的弹性常数,如表S6所示。根据弹性常数,相应的体模量(B)、剪切模量(G)和杨氏模量(E)可以通过Voigt-Reuss-Hill近似得到(Colmenero et al ., 2017)。此外,它们的理论硬度采用经验表达式推导(Chen et al, 2011),相应数据列于表2。由表2的数据可以看出,计算得到的的硬度为6.75 GPa, 的硬度为7.46 GPa,与实测硬度值的硬度为6.1 GPa, 的硬度为6.7 GPa)吻合较好,证明了预测的准确性。的硬度为12.25 GPa。通过五元掺杂,
的硬度降至~ 7.5 GPa,比
的硬度降低了近39%。更令人着迷的现象是通过三元掺杂实现的硬度降低,达到令人印象深刻的45%。此外,Pugh提出B/G的比值(B/G)也能反映金属材料的韧性/延性或脆性,B/G值越高,金属材料的韧性/延性越好(Pugh, 1954)。根据Pugh韧性/脆性标准,的B/G值小于1.75,反映了其脆性。相比之下,
的B/G值均有显著提高,其中
的G/B值提高到1.96,表明其固有韧性得到了显著提高。综上所述,与传统的硬脆IMCs不同,由硬度较低、固有韧性较好的
型相组成的壳体具有较低的塑性变形抗力。这有利于壳/Al界面的应变/应力传递,防止界面在低应力水平下脱粘,并有利于界面GNDs的持续积累。
在拉伸过程中,随着应变的增大,增强材料与Al基体界面处的应力集中更加严重。高界面应力通过界面剪切激活了钢筋壳的多种变形模式,包括外壳的位错滑移和内壳的SFs等,如图7所示。当壳/Al界面处的应力集中通过激活增强壳的变形而得到释放时,它有助于复合材料的总塑性变形。此外,如图8所示,高界面应力诱导基体在靠近壳体处形成SFs,进一步促进了基体的延性(Liu et al ., 2024c)。C-560样品中HEA颗粒周围未发现SF的存在(图S2)。因此,增强壳与Al基体的共变形有助于提高C-580和C-600复合材料的塑性,尤其是壳体积最大的C-600复合材料。
此外,复合材料的延展性与裂纹成核/扩展过程中释放的能量相关(Jiang等,2016)。不同结构钢筋的断裂形貌如图13所示。可以发现,在C-560复合材料中,HEA颗粒与Al基体发生界面脱粘(图13a)。这是因为HEA颗粒的刚度使得这种界面不适合应变/应力传递,不像壳/Al界面。因此,随着应变的增大,HEA/Al界面处的应力集中急剧增大,导致界面过早破坏。随着配筋壳的出现,其断裂模式由HEA/Al界面处的界面脱粘转变为壳体的断裂(图13b、c),也证明了壳体具有良好的应力承载能力,能够参与变形和承受拉伸载荷。与C-560复合材料相比,C-580和C-600复合材料外壳裂纹的形成和波状传播路径耗散更多能量,可以延缓裂纹的发展(Pu et al ., 2022)。这是由于壳中有丰富的纳米颗粒(~300 nm),见图4a。
拉伸试验后C-580复合材料断口侧形貌如图14所示。在断头附近区域的放大视图中,微裂纹起源于增强壳与Al基体之间的界面(如图14b中黄色箭头所示)。图14c-e显示了壳内微裂纹的挠度,它延长了裂纹的扩展路径,从而提高了复合材料的延性。此外,如图14c和e所示,由于界面影响区沿壳/Al界面和FG/CG界面形成(参见图10a-d),壳内微裂纹总是终止于壳与Al的交界面。界面影响带主要由GNDs聚集形成(Liu et al ., 2023a)。在这些区域,裂纹尖端位错的发射降低了裂纹尖端的应力集中(Liu et al ., 2020),这种钝化效应将延迟微裂纹的扩展,从而避免过早破坏。因此,裂纹的挠曲和钝化提高了复合材料的伸长率。
为了进一步了解核壳增强颗粒对复合材料延性的影响,通过有限元模拟比较了C-560和C-580复合材料在拉伸试验中应力场分布的差异。两种复合材料的RVE模型如图S3所示。图15为C-560和C-580复合材料在相同应变下的Mises应力分布图可以发现,C-580基体中最大应力的面积分数小于C-560基体中最大应力的面积分数,这表明与HEA颗粒相比,壳能有效地缓解基体中的应力集中。即在拉伸试验中,核壳增强颗粒承担了大量的外部应力,导致C-580复合材料基体的应力水平较低(图15)。因此,激活位错滑移机制所需的临界应力在C-560复合材料的更大范围内首先得到满足,而在C-580复合材料中,同样的情况被推迟了。这表明C-580复合材料在相同应变下具有较低的应变/应力集中程度。因此,该复合材料具有较好的延展性。
图13
复合材料的断裂形态和断裂模式图。(a) C-560复合材料中HEA颗粒与Al基体界面的脱粘。(b) C-580复合材料中HEA核心仍然完好无损,但外壳断裂。(c)在c -600复合材料中,增强材料HEA核心消失,裂纹贯穿整个壳体。
图14
C-580复合材料断裂侧面。(a)断头附近的表面形貌。(b)放大后的断头附近表面形貌显示微裂纹的分布,用黄色箭头表示。(c, d)放大后的图像显示了壳内微裂纹的偏转和钝化。
图15
(a) C-560和(b) C-580复合材料在4%拉伸应变下的Mises应力分布。
图16
(a)C-580 RVE模型在不同阶段的Mises应力分布和损伤演化。(b)核壳粒子在不同阶段的特写图像。LD表示拉伸加载方向
图17
C-560 RVE模型在不同阶段的Mises应力分布和损伤演化。LD表示拉伸加载方向。
图16为C-580复合材料拉伸过程中的损伤演化及Mises应力分布。在拉伸变形初期,应力主要集中在靠近钢筋的基体区域。随着拉伸过程的继续,应力集中逐渐增大,壳内开始形成裂纹(见图16b的放大细节),这与观察结果(图14c、d)一致。随着裂纹的成核扩展,裂纹附近的局部应力释放,基体应力减小(图16a)。而对于C-560复合材料,裂纹起裂发生在HEA颗粒与Al基体的界面处,如图17所示。随着拉伸应变的增大,裂纹向基体延伸,HEA颗粒与基体发生脱粘,这与断裂面观察结果一致(图13a)。最终,多个裂纹合并,复合材料完全破裂。结果表明,C-580复合材料的裂纹扩展路径比C-560复合材料的裂纹扩展路径更曲折,这有利于复合材料的延展性。
综上所述,核壳增强外壳的纳米颗粒层具有良好的韧性和承载能力,能够有效地容纳变形和抑制裂纹扩展,从而使复合材料具有良好的延性。还需要指出的是,根据前面的讨论,变形协调过程中,在非均质界面处产生了GNDs,导致额外的HDI硬化,有效地提高了复合材料的延性。
5结论
本文采用粉末冶金技术制备了一种具有特殊核壳增强和异质晶粒结构的新型“双金属”异质结构碳纤维。通过控制烧结温度,原位合成了均匀、致密、厚实的增强颗粒壳。增强材料的内壳由具有纳米晶粒结构的纳米颗粒组成。外壳由和少量组成,也具有纳米晶粒结构。与没有核壳结构的HEA颗粒增强的碳纤维相比,核壳颗粒增强的碳纤维的抗拉强度和塑性分别提高了48%和24%以上。强度的提高主要是由于多个非均质界面产生的高HDI应力。独特的双层壳层的形成可以实现增强材料与基体的共变形,减少基体中的应力集中,延长裂纹扩展距离,从而使复合材料具有良好的延性。此外,非均相界面的引入提高了复合材料的位错存储能力,并产生了显著的HDI强化/硬化效果,最终实现了强度和塑性的良好协同。该研究为强韧性金属基复合材料的设计提供了新的思路。
免责声明:本网站所转载的文字、图片与视频资料版权归原创作者所有,如果涉及侵权,请第一时间联系本网删除。
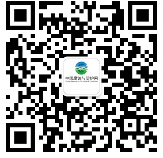
官方微信
《腐蚀与防护网电子期刊》征订启事
- 投稿联系:编辑部
- 电话:010-62316606
- 邮箱:fsfhzy666@163.com
- 腐蚀与防护网官方QQ群:140808414