导读:本文利用激光增材制造技术(LAM)制备了一种多层Zr基非晶合金复合材料。通过控制每一层材料在激光增材制造过程中的冷却速率,对其微观组织进行调控,进而成功地获得了枝晶相体积分数呈梯度变化的非晶合金复合材料。该梯度非晶合金复合材料表现出高屈服强度(>1.3 GPa)和高拉伸延展性(~13%)的完美结合。这种强韧性的同时提高源于相邻层间相互作用引起的协同强化和非均质微观结构导致的异步形变方式。该研究利用激光增材制造技术来设计和制备大尺寸梯度金属结构,不但为高性能非晶合金复合材料的开发和大规模结构应用打开了一扇新的窗口,也对许多其他金属材料的增材制造具有普适意义。
由于没有晶体缺陷(如位错和晶界),大块非晶合金(BMG)表现出极高的强度和弹性,并具有类似塑料的加工性能。然而,在室温下,特别是在受拉条件下,大块非晶合金通常缺乏塑性。非晶合金的塑性应变高度局域于剪切带内,该剪切带会迅速扩展并导致非晶合金的灾难性破坏,这严重阻碍了大块非晶合金的广泛应用。为了克服这一问题,人们通常会原位引入塑性较好的第二相来增韧非晶合金基体,从而形成非晶合金复合材料(BMGC)。这些分散的韧性枝晶相促进了多重剪切带的形核,并阻碍了剪切带向裂纹的快速发展,从而极大地提高了非晶合金的室温延展性。
除此之外,迄今为止大多数非晶合金复合材料的制备加工都是基于液态熔铸工艺,其力学性能强烈依赖于凝固组织特征(如枝晶的尺寸、体积分数和枝晶间距),而这些都对制备加工条件高度敏感。以Cu48Zr48Al4非晶合金复合材料为例,当铸造直径从3 mm增加到5 mm时,同一合金发生了韧脆性转变。又比如在非晶合金复合材料的铸锭中,组织控制是相当困难的,由于从表面到内部的冷却速率不同,树枝晶的分布往往不均匀且不受控制。尽管通过适当的合金成分设计,结合半固态加工或Bridgeman定向凝固,可以获得微观组织更加均匀的非晶合金复合材料,但是其作为结构材料来应用仍然面临巨大挑战,这主要由于受铸造时玻璃形成所需的高冷却速度的内在要求,其尺寸通常都限制在厘米尺度。此外,为了最有效地增韧非晶合金基体,通常需要引入较高的枝晶相体积分数(40%~50%),这导致了非晶材料整体强度的显著下降。这种强度-延展性的“此消彼长”是材料科学中一个长期存在的挑战,要求采用新的策略来设计和制造强度-延展性同时提高的新型非晶合金复合材料。
近年来,人们一直在努力克服金属强度和延展性之间的“此消彼长”问题。在这些方法中,非均质梯度结构设计是特别有效的方法,并因此成为克服强度和延性冲突的主要机制,即使在脆性材料(如纳米晶金属和非晶合金)中同样适用。在具有梯度结构的金属材料中,软区和硬区被巧妙地设计成连续变化的特征尺寸(即粗晶、超细晶、纳米晶和非晶)。在形变时,软硬区域之间会出现塑性不相容,在此区域会产生塑性形变梯度,并激发几何必需位错(GND),致使强度-延性协同提高。
激光增材制造技术是一种以金属粉末为原料的快速制造技术。由于激光增材制造金属材料是一个逐层堆积的过程,它可以通过实时调节粉末成分、激光加工参数等工艺来实现每一层材料的成分和微观组织的精准控制,这为设计和制备梯度金属材料提供了绝佳的机会。另外,在激光增材制造过程中高达103~104 K/s的熔池冷却速率也使许多金属发生玻璃化成为可能。
基于此,大连交通大学的吕云卓老师、研究生苏爽、哈尔滨工业大学的黄永江老师和美国马萨诸塞大学的陈文老师等研究人员合作,以Zr39.6Ti33.9Nb7.6Cu6.4Be12.5(DH3)非晶合金复合材料为模型材料,利用同轴送粉式激光增材制造技术(LAM)制备出具有较高屈服强度(>1.3 GPa)和较好拉伸延展性(~13%)的多层梯度非晶合金复合材料。相关研究成果以题“Controllable Additive Manufacturing of Gradient Bulk Metallic Glass Composite with High Strength and Tensile Ductility”发表于金属顶刊Acta Materialia。
论文链接:https://www.sciencedirect.com/science/article/abs/pii/S1359645421000124
通过精确调节熔池的冷却速率,成功地制备出由多层枝晶含量梯度变化的DH3组成的梯度非晶合金复合材料,枝晶体积分数逐渐从~20%变化为~65%。基于连续的“双向”塑性形变和断裂过程,以及位错运动引起的枝晶形变强化和剪切带引起的非晶基体形变软化之间的竞争,解释了这种新型多层梯度非晶合金复合材料的优异力学性能。该研究为开发同时具有高强度和高延展性的梯度非晶合金复合材料开辟了一条全新的途径,而采用的激光增材制造技术也使得非晶合金复合材料作为结构材料的大规模应用成为可能。
图1 梯度DH3非晶合金复合材料的可控制备。(a)Zr39.6Ti33.9Nb7.6Cu6.4Be12.5(DH3)雾化粉末的SEM微观形貌图。(b)激光增材制造实验装置示意图,BD:材料堆积方向,LD:拉伸加载方向,TD:横向方向。(c)预先设计的DH3非晶合金复合材料的梯度结构示意图。设计了包含10层的层状结构,其枝晶体积分数逐渐从20%过渡到65%。为了给拉伸试样的后续切割和抛光留有余量,额外设计了两层附加层,即底层有20%的枝晶和顶层有65%的枝晶。(d)利用激光增材制造技术制备的10层梯度DH3非晶合金复合材料。(e)枝晶体积分数F与激光加工工艺参数组合P/v的关系。(P为激光功率,v为激光扫描速率。)
图2 梯度DH3非晶合金复合材料的微观结构。(a-j)复合材料不同层的扫描电镜(SEM)微观形貌图,对比度较亮的区域为枝晶相,对比度较暗的区域为非晶基体。(k)枝晶和非晶两相界面的高分辨透射电镜(TEM)图,插图为相应的选区电子衍射图。
图3 梯度DH3非晶合金复合材料的拉伸形变行为。(a)梯度DH3非晶合金复合材料的拉伸工程应力-应变曲线。梯度DH3非晶合金复合材料的拉伸形变呈现线性弹性、形变强化和形变软化三个阶段。为了对比,铸态非晶合金Vit1、铸态含有67%枝晶的非梯度DH3非晶合金复合材料以及利用激光增材制造技术制备的含有20%和65%枝晶的非梯度DH3非晶合金复合材料的拉伸应力-应变曲线也同样列在图中。(b)梯度DH3非晶合金复合材料的断口形貌。枝晶含量大于45%的顶部5层的断裂角度与加载方向夹角约为90°,枝晶含量小于45%的底部5层的断裂角度接近45°。(c)第5层和第6层界面处的典型放大形貌图,与断裂面相似,剪切带在第5和第6层的界面处发生了方向变化,剪切带也在向界面的扩展过程中产生大量的分叉。
图4 梯度DH3非晶合金复合材料的异步形变。(a)梯度DH3非晶合金复合材料的不同层在不同形变阶段的显微硬度演变。如图中箭头所示,数字1到10对应于梯度DH3非晶合金复合材料的第1到第10层。a-k形变阶段与图3(a)所示的拉伸应力-应变曲线上的形变阶段一一对应。(b)拉伸应变3%后梯度非晶合金复合材料的侧面高度。(c)拉伸应变3%后沿材料堆积方向的侧面平均高度。
图5 梯度DH3非晶合金复合材料在不同形变阶段的微观形貌。(a-i)-(a-xii)第1、第6和第10层在b、g、i、j形变阶段的SEM微观形貌。(b-i)-(b-iv)为枝晶与非晶基体界面处的TEM图。(b-i)图显示的是在b形变阶段第1层内部形貌,没有看到位错或剪切带。(b-ii)图显示的是在c阶段第1层内部形貌。(b-iii)图显示的是在c阶段的第1层和第2层之间的界面区域形貌,在相邻层界面处,枝晶内部的位错密度高于第1层内部的位错密度。(b-iv)显示的是在d阶段第1层内部形貌,可以发现剪切带从非晶和枝晶的界面处萌生。
图6 梯度DH3非晶合金复合材料枝晶体积分数与激光增材制造加工工艺参数的关系。(a)-(c)激光增材制造单道DH3非晶合金复合材料的凝固过程有限元模拟。(d)熔池和热影响区温度分布示意图,熔池中心的黄点是采集图(f)中时间-温度曲线的位置。(e)非晶合金凝固的时间-温度-转变(TTT)示意图。(f)5组典型的不同P和v组合下的激光增材制造DH3非晶合金复合材料的时间-温度曲线。(g)熔池冷却速率R与激光加工工艺参数组合P/v和枝晶体积分数F之间的关系曲线。
图7梯度DH3非晶合金复合材料的形变和断裂过程示意图。(a)在宏观弹性形变阶段,软的枝晶和硬的非晶基体均发生弹性形变。(b)随着梯度非晶合金复合材料进一步加载至宏观塑性阶段,梯度非晶合金复合材料中不同层间的塑性形变不同步,枝晶较多的第1层首先发生塑性形变。在第1层中,枝晶与非晶基体之间也发生了异步形变。当外加应力达到屈服强度时,枝晶首先通过位错滑移发生塑性形变,而较硬的基体仍然保持弹性。(c)在进一步加载时,枝晶的塑性形变受到较硬的非晶基体的限制。在第1层非晶-枝晶界面处堆积大量位错,导致局部应力集中。当局部应力超过非晶基体的屈服强度时,剪切带作为非晶基体塑性的载体开始产生。同时,第二层的枝晶在此阶段开始塑性形变。(d)-(g)随着应变的增加,异步塑性形变过程从第1层逐渐扩展到第10层。在第1至第5层,枝晶间平均间距相对较小。应力集中在相邻枝晶间重叠,形成复杂的应力场,并使剪切带从最大剪应力方向向相邻枝晶扩展。因此,大量的剪切带启动并垂直于加载方向(90°)传播。在枝晶较少的第6至第10层,枝晶间平均间距较大,相邻枝晶之间的应力集中都发生在界面附近的小区域。因此,剪切带启动并沿着最大剪应力(向拉伸轴方向45°)传播,剪切带密度也逐渐减小。(h)当塑性形变转移到第10层时,由于该层的枝晶最少,对剪切带扩展的阻力最小,剪切带迅速演化为微裂纹。(i)和(j)微裂纹通过梯度非晶合金复合材料从第10层反向延伸至第1层,梯度结构实现了双向“往返”形变路径,即塑性形变从第1层发展到第10层,然后断裂从第10层开始裂纹萌生并扩展到第1层。
免责声明:本网站所转载的文字、图片与视频资料版权归原创作者所有,如果涉及侵权,请第一时间联系本网删除。
-
标签: 晶体缺陷, Acta Materialia, 增材制造, 复合材料
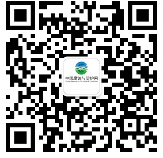
官方微信
《中国腐蚀与防护网电子期刊》征订启事
- 投稿联系:编辑部
- 电话:010-62316606-806
- 邮箱:fsfhzy666@163.com
- 中国腐蚀与防护网官方QQ群:140808414