导读:固态异种双金属或多金属键合技术有望在汽车、核电和航空航天工业中实现轻量化或多功能组件,应用前景广阔。为了了解如何在不同种材料之间实现高质量的结合界面,对铝合金(Al) -钢(Fe)双金属齿轮进行了系统的热锻结合研究。在这项工作中,使用非原位实验和有限元建模对锻造结合力学、微观结构特征、结合界面行为和由此产生的力学性能进行了综合分析。结果表明:两种不同工件(AA6082和E355)的力学性能不匹配显著影响着粘接行为和微观组织演变。这种失配可以通过设置不同的锻造温度来有效调整。观察到在低温和高温下制造的AA6082和E355的界面结合强度分别受相互扩散和氧化物颗粒的控制。平衡相互扩散和氧化物破坏似乎是实现异种双金属锻造键合技术优化界面强度的关键。
固态异种双金属或多金属键合是在汽车、核电和航空航天工业中制造轻型或多功能部件的一种很有前途的方法。常用的固态结合工艺包括压力焊接、扩散结合和基于摩擦的焊接技术。在核工业和航空航天工业中已有应用。例如,扩散键合用于在面向等离子体的组件中实现WCu-CuCrZr键合。在汽车行业,本田雅阁在其前副车架上采用了铝合金-钢搅拌摩擦焊工艺,以实现轻量化。在这些固态异种键合方法中,键合机制大体相同,氧化物断裂、相互扩散和微观结构演变从根本上影响键合强度。这三个基础工艺主要由应力、应变和温度等键合工艺参数决定。然而,键合工艺参数、这三个基本工艺和键合质量之间的关系在很大程度上是难以捉摸的。
不同固态键合技术有其优点和局限性。例如,扩散键合可以在低键合温度和压力下进行;然而,通常需要较长的键合时间和真空键合条件。基于摩擦的焊接可以实现快速结合,并通过材料流动有效地打破氧化层。有研究者提出了一种摩擦螺柱铆接工艺,用于将铝合金与钢粘合。粘合质量已被证实与工艺参数(如旋转和进给运动)密切相关。材料流动和界面行为可以通过采用不同的工具形状来调整。然而,载荷的应用或摩擦焊接直工具的使用,使其无法用于具有复杂焊接界面的焊接目标。在例如压力焊接的固态键合过程中,需要高效的键合时间和低热输入,尽管需要严重的材料塑性流动相邻的界面,也可以最大限度地减少脆性金属间化合物 (IMC) 的产生和演变。通过广泛的研究,将压力焊接和金属成型技术相结合,以快速形成双金属部件;其中一些技术是轧制、挤压和锻造。然而,之前的研究主要集中在开发粘合工艺和优化材料的塑性流动。详细的键合界面强度和潜在的键合机制仍不甚清晰,这限制了行业对该技术的接受。
在先前的固态铝和钢粘合研究中已经观察到了微观结构特征。在铝-钢界面附近观察到等轴细晶粒。铝的平均晶粒尺寸明显小于母铝,动态再结晶发生在界面的铝侧。此外,在铝-钢界面附近观察到固溶区。这是由高温引起的相互扩散和快速冷却速率引起的。还观察到了IMC。根据 Fe-Al 图,Fe 在 Al 中的高溶解度促进了键合过程中各种形式的IMC的不同组成。有关此课题,伦敦帝国理工学院联合挪威科技大学的学者进行了深入研究,相关研究成果以题为Solid-state hot forge bonding of aluminium-steel bimetallic gears: Deformation mechanisms, microstructure and mechanical properties发表在International Journal of Machine Tools and Manufacture上。
论文链接:https://doi.org/10.1016/j.ijmachtools.2022.103930
结合强度是铝合金和钢的固态焊接的主要关注点。据报道,不同的机制有助于各种焊接技术的结合强度。图 1总结了参考文献中报道的粘合强度。归一化结合强度定义为结合强度(拉伸或剪切)与基础铝合金强度之比。如图1所示,冷压焊接下的焊接强度只能达到基础铝合金的 67% 左右。摩擦焊接的强度远高于冷压焊接。摩擦焊接的高结合强度归因于四个主要因素。首先,在某些情况下采用后热处理,通过沉淀硬化来增强材料。第二个因素是氧化层的破碎,因为摩擦焊接可以有效地破坏界面处的氧化层,这允许暴露并与原始材料密切接触。这些因素有效地提高了最终的粘合强度。第三,当工具与界面一起撞击材料时,会产生机械锁定特征,从而提高粘合强度。最后,在固态焊接过程中控制低热输入会产生薄的IMC层。这可以防止IMC层失效,从而提高粘合强度。对于不同的键合,大量的热输入会产生厚的IMC层,这会导致键合失效位置从铝母材转移到界面。

图 1 铝合金与钢之间固态焊接的归一化结合强度
尽管有关于搅拌摩擦焊的结合强度、机理和微观结构演变的文献,但没有详细研究调查热锻结合过程中的这些因素。目前尚不清楚锻造键合界面的坚固程度、控制键合强度的机制以及如何优化它们。以前关于双金属齿轮热锻结合的工作只关注齿轮设计和材料塑性流动。与传统的钢齿轮相比,双金属齿轮的失效预计会发生在齿轮根部区域,主要是断裂和弯曲疲劳等。证明了根部区域的应力状态受到锻造过程中使用的外钢圈厚度的显著影响。与钢齿轮相比,双金属齿轮在根部区域的应力状态更为严重,这表明双金属齿轮界面的结合质量对于高可靠性应用至关重要。
因此,本研究的重点是热锻结合双金属齿轮的结合质量和界面行为。研究了铝芯不同锻造温度(300°C、400°C 和 500°C)的三种情况,重点关注互扩散区和氧化物颗粒,揭示界面处与温度相关的显微组织演变。有限元分析用于了解界面处局部应力、应变和热场分布的影响。通过探索作为锻造温度函数的工件界面氧化物和晶粒细化的分数来理解结合机制。原位拉伸试验在 SEM 中进行了研究以揭示结合强度和失效机制,发现它们受高温促进的相互扩散和低温促进的氧化物破坏的支配。
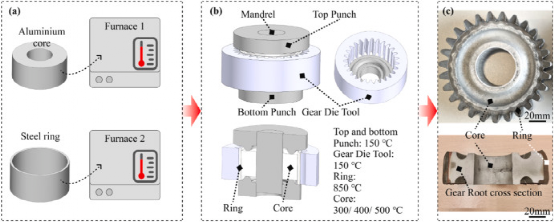
图 2 (a) 和 (b) 显示了双金属齿轮锻造实验的示意图,(c) 显示了热锻结合齿轮及其横截面。
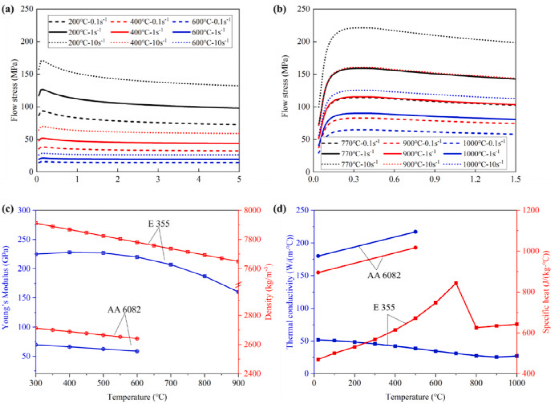
图 3 铝芯和钢环的材料特性:(a) 铝芯在不同温度和应变率下的应力-应变曲线;(b) 钢环在不同温度和应变率下的应力-应变曲线;(c)杨氏模量和密度,(d)芯和环的热导率和比热随温度的变化。
图 4显示了收到的材料的微观结构。热锻样品的坐标系定义为径向(RD)、锻造方向(FD)和环向(HD),如图4a所示。在固溶热处理条件下,收到的芯材是AA6082 。大的细长晶粒与 FD 一起被识别(图 4?b)。根据EBSD图,几乎看不到亚晶界。图4c 显示了收到的 E355 钢的反极图 (IPF) 图,表明不均匀分布的铁素体晶粒主导了显微组织。图中所示的极图 (PF)图 4 d 表明 FD-HD 平面中钢的纹理很少。
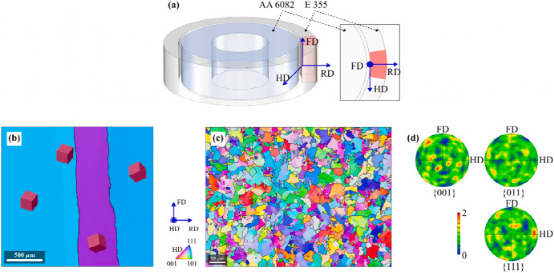
图 4 (a) 示意图显示了用户定义的轴和从收到的材料中获取的样本位置;(b) 接收到的 AA6082 沿 HD 轴的反极图 (IPF);(c) 收到的 E355 沿 HD 轴的 IPF 和 (d) 收到的 E355 的极图 (PF)。
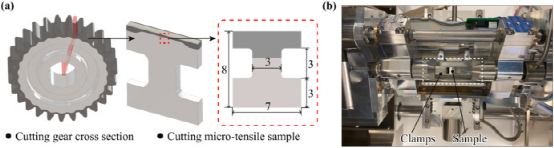
图 5 (a) 微拉伸样品的切割过程和 (b) 原位拉伸试验台和夹具。
有限元模型首先通过比较实验的齿轮几何形状与案例 A 锻造条件下的模拟齿轮几何形状进行验证。如图6所示,齿轮根部截面的界面轮廓在有限元之间匹配良好。结果和锻造实验。
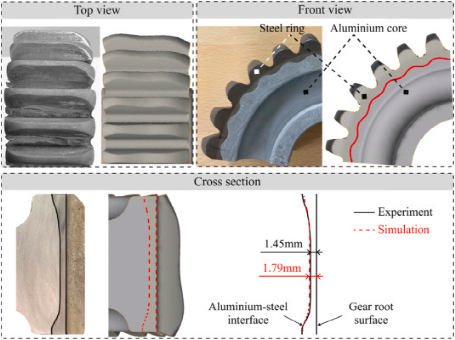
图 6 通过从顶视图、正视图和齿轮根部横截面比较齿轮几何形状来验证有限元模型。

图 7 案例 A 在双金属热锻焊接过程中的变形和热历史 (a)有效塑性应变和 (b) 温度。

图 8 (a)不同锻造温度下齿轮根部横截面的变形过程和由此产生的界面轮廓示意图;(b) 环材料和 (c) 芯材三种情况下有效塑性应变和温度的比较。
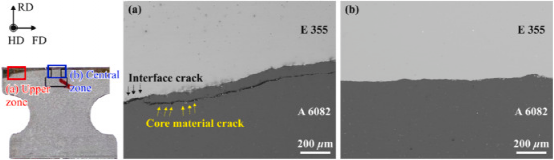
图 9 (a) 上部区域和 (b) 中心区域的情况 B 的芯和环材料之间的界面。

图 10 案例 B 界面处的氧化物行为。(a)BSE 图像显示破裂的氧化物颗粒;(b) EDS 图显示元素分布和 (c) SE 图像显示迁移的氧化物颗粒。

图 11 物质流动和氧化物迁移。(a) 核心和环中心区的 RD 速度;(b)、(c) 和 (d) RD 速度的反图;(e) 锻造过程中材料流动示意图和 (f) 氧化物迁移示意图。
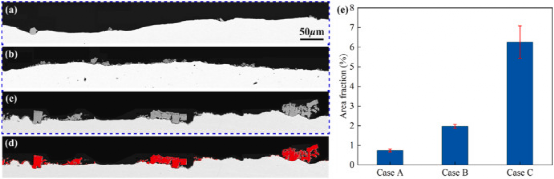
图 12 (a)~(c) 案例 A、B、C 中界面处的 BSE 图像;(d) 案例 C 中已识别的氧化物颗粒的示例和 (e) 对应于图 12 a-c 的氧化物颗粒的面积分数。
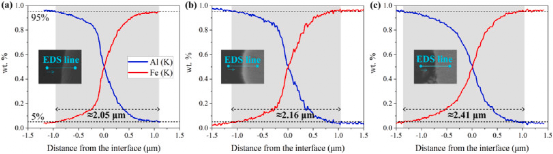
图 13 具有定义的相互扩散距离的 EDS 线扫描。(a) 案例 A,(b) 案例 B 和 (c) 案例 C。
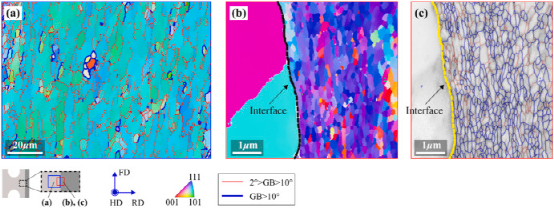
图 14 中心区域的界面晶粒结构细节。(a) 晶界图重叠的铝芯的 IPF 图;(b) 钢环的 IPF 图和 (c) 钢环的晶界图与图像质量 (IQ) 图叠加。蓝线表示高角度晶界(HAGB,取向错误>10°),红线表示低角度晶界(LAGB,2°<取向错误<10°)。
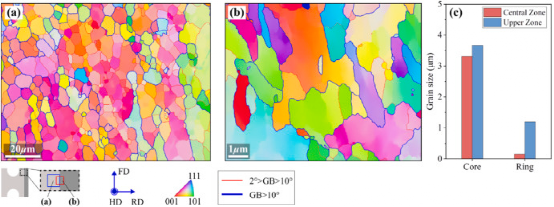
图 15 上部区域的界面微观结构细节和热机械历史。(a) 晶界图重叠的铝芯的 IPF 图;(b) 晶界图重叠的钢环的 IPF 图和 (c) 上部和中心区域的晶粒尺寸比较。
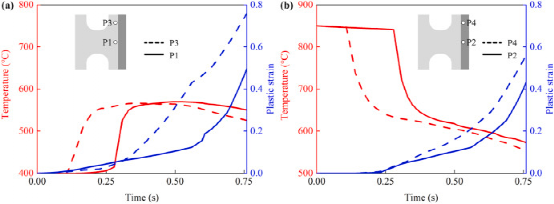
图 16 (a) 铝芯和 (b) 钢环的有效塑性应变和温度历史。P1 和 P2 位于中央区域,P3 和 P4 位于上部区域。
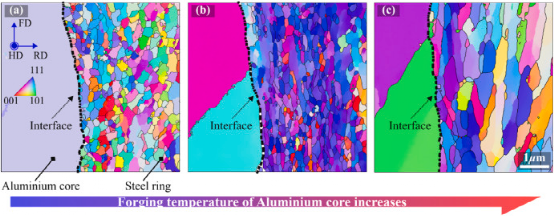
图 17 三种锻造条件下环材料的 IPFs。(a) 案例 A,(b) 案例 B 和 (c) 案例 C。
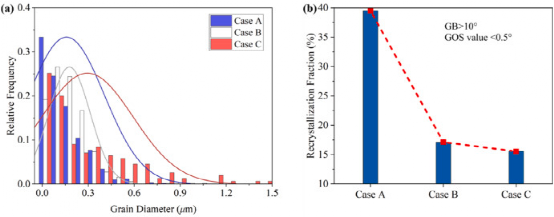
图 18 三种锻造条件下钢环显微组织特征的统计结果,(a)晶粒尺寸分布和(b)HAGBs分数。

图 19 三种锻造条件下铝芯的 IPFs。(a) 案例 A,(b) 案例 B 和 (c) 案例 C。
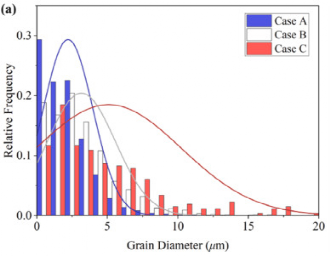
图 20 三种锻造条件下铝芯晶粒度的统计结果。
从双金属齿轮获得的拉伸样品在三种条件下进行锻造。通过重复拉伸试验获得的三种情况的界面拉伸强度和标准偏差如图21a所示。与其他两种情况相比,情况 A 表现出最高的抗拉强度,即抗拉强度随着锻造温度的升高而降低。如图 21b 所示,在案例 C 中获得了相对较低的延性力-位移行为,因为断裂发生在界面处。断裂行为的更多细节如图22所示。

图 21 铝-钢界面的机械性能 (a)抗拉强度和 (b) 力-位移曲线。
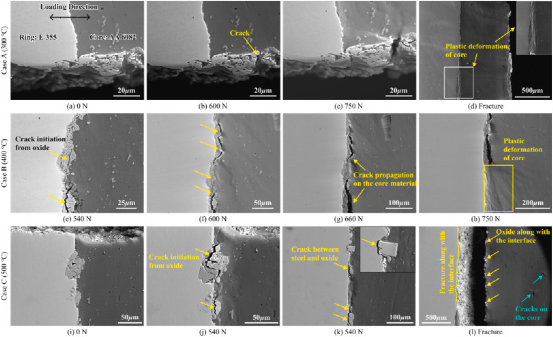
图 22 案例 A (a)~(d)、案例 B (e)~(h) 和案例 C (i)~(l) 的原位拉伸试验。
图 22显示了三种情况的原位拉伸结果。图 22 a-d 显示了案例 A 的结果,其中铝芯的锻造温度为 300 °C。从结果中,我们可以观察到裂纹被确定为在铝芯本身中开始。这表明与芯材相比,界面强度足够高。虽然在试样断裂后界面附近观察到严重的塑性变形(图22d),但没有观察到界面裂纹,最终断裂发生在铝芯侧。至于情况 B(图 22e和f),观察到裂纹是从界面氧化物开始的。裂纹扩展至铝芯中,当负载增加时没有观察到氧化物颗粒。在测试的后期阶段,观察到更多的裂纹从界面氧化物开始。然而,与案例 A 一样,尽管发生了严重的塑性变形,但在无氧化物界面区域上没有观察到裂纹(图 22 h)。图 22 i-l 说明了案例 C 的失效过程。如图 22 i 和 j所示,观察到裂纹从氧化物或氧化物环界面开始。如第3.2节所述,沿案例 C 的界面观察到大尺寸和高比例的氧化物。这导致与案例 A 和 B 不同的断裂机制。当载荷增加时,由氧化物引发的裂纹相互作用(图 22 k),导致最后的断裂和界面。此外,在测试的后期,铝芯出现了小裂缝(海蓝宝石箭头),而案例A和B的铝芯没有发现。这很可能是由于芯强度低造成的。由大晶粒尺寸和较低比例的HAGBs(图19,图20)。
案例 C 表现出三种案例中最低的拉伸强度。这可能与界面附近氧化物的行为有关。由于铝芯的锻造温度较高(500 °C),许多氧化物留在界面处,图 23中的 BSE 图像与这一观察结果一致。如图 23所示,在断口表面观察到高面积的氧化物。a-c。观察到铝芯是包围氧化物颗粒的单元型。这意味着在锻造过程中,只有少量的芯材可以突破氧化物并与钢圈接触。这并不奇怪,因为铝芯在 500 °C 时更软。

图 23 案例 C (a)–(d) 和案例 A (e)–(f) 的环(E 355 钢)侧断裂面的BSE 图像。(e) 和 (f) 是断裂表面的局部 EDS 图,用于识别氧化物、芯材和环形材料。
图 24 (a) 锻造结合产生的界面特征和 (b)断裂行为的示意图。
这项工作对铝合金-钢 (AA6082-E355) 双金属齿轮界面接合进行了系统研究,以了解如何实现高质量接合。使用原位/非原位实验和有限元模拟建立了制造过程和产生的机械性能之间的相关性。详细讨论了界面氧化物迁移、相互扩散和微观结构演变的潜在机制。
两个工件(AA6082 和 E355)之间的机械性能不匹配会影响粘合行为和微观结构演变。通过为工件设置不同的锻造温度,可以有效地调整这种失配。E355工件的氧化层在双金属锻造下因接触和塑性变形而断裂。由于界面材料流动,一些氧化物颗粒迁移到AA6082的基体中,留下无氧化物的界面区域。在 AA6082 的较低锻造温度 (300 °C) 下,在界面处观察到最少的氧化物。在三种情况下的无氧化物界面区域,EDS结果表明较高的锻造温度可以有效地促进两个工件之间的相互扩散。
初始锻焊温度影响两种不同工件(AA6082 和 E355)的微观结构;在较低的锻造温度(300 °C)下观察到更细的晶粒。来自 EBSD 和有限元建模的有力证据证实,两种不同工件之间的传热和机械性能不匹配是不同锻造温度下显微组织不同的主要原因。低温促进的氧化物断裂和高温促进的相互扩散是实现高双金属键合质量的关键。存在一个最佳锻造温度,在该温度下,铝合金足够硬以破坏钢零件上存在的氧化膜,而该温度允许铝合金和钢具有高扩散速率,以实现足够的相互扩散以增强结合质量。
对键合机制的深入理解不仅限于铝合金-钢系统,还可以扩展到各种不同的双金属或多金属固态键合材料。
免责声明:本网站所转载的文字、图片与视频资料版权归原创作者所有,如果涉及侵权,请第一时间联系本网删除。
相关文章
无相关信息
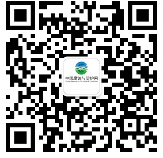
官方微信
《腐蚀与防护网电子期刊》征订启事
- 投稿联系:编辑部
- 电话:010-62316606-806
- 邮箱:fsfhzy666@163.com
- 腐蚀与防护网官方QQ群:140808414
点击排行
PPT新闻
“海洋金属”——钛合金在舰船的
点击数:8168
腐蚀与“海上丝绸之路”
点击数:6492