激光粉末床熔融(LPBF)产生的不规则大孔隙是一种固有缺陷,极大地限制了构件的力学性能。激光重熔是减少孔隙率和增加能量输入的有效方法,而过多的热量积累通常是以牺牲粉末飞溅为代价的。
Graphical abstract
近日,北京科技大学、上海交通大学研究团队将激光重熔和五种扫描策略(三种往返和两种棋盘策略)相结合, LPBF制备哈氏合金X合金,通过实验和模拟研究了扫描策略对相关组织和力学性能的影响。相关研究成果以题为 “Tailoring the microstructure and mechanical properties for Hastelloy X alloy by laser powder bed fusion via scanning strategy” 发表在Materials & Design期刊上。
图1(a)气雾化制备的 HX合金粉末形态(b)粉末粒度分布(c)LPBF制备的HX合金成分。
在增材制造之前,对直径在20-60μm范围内的粉末进行干燥,随后打印10×10×5mm的HX样品。保护气体为氮气,基板为预热80 ℃的45#钢。在打印过程中采用了基于初步测试确定的一系列优化参数,并总结在表1中。
表1 LPBF工艺参数
为了了解制造工艺对HX样品微观结构的影响,为HX块制备了五种扫描策略,如图2(a-e)。三种往返策略(分别为M0、M67和M90)对应于粉末层之间0°、67°和90°的旋转增量角。此外,还采用了两种棋盘策略(分别为CB1和CB2)来研究岛扫描的重熔效应。5×5mm的相邻岛区域的矢量彼此垂直,并且后续层的矢量与前一层保持正交关系。有趣的是,CB1策略的热历史更为复杂,它涉及到来自邻近区域的巨大热影响。与CB1相比,CB2策略每个单位面积简单,因为激光束在打印过程中优先扫描各向同性区域。在这项研究中,所有样本都是使用双扫描制作的,包括在初始熔化后立即开始第二次扫描。有人建议,在单个粉末层的熔化过程中实施这种双扫描方法可以提高冶金质量。制作室温拉伸试样,如图2(f),加载方向垂直于建筑方向。
图2(a-e)不同扫描策略的示意图,分别为M0、M67、M90、CB1和CB2,以及(f)实际样本的示意图。
对LPBF工艺进行了模拟,揭示了各种扫描方式的凝固状态和冷却条件。本文中,冷却速率(G×R)和热梯度(G)是熔池凝固的关键输出参数。此外,G/R的值代表组成过冷,并与晶体形成相关。为了模拟打印过程,使用Flow 3D软件建立了多物理场模型,其中包括熔融金属流动、相变、Marangoni效应、反冲压力、表面张力和激光与材料的相互作用。详细的计算方法和初始输入显示在补充信息中。
为了获得粉末在基板上的分布,应用离散元法(DEM),并铺下两层粉末来模拟打印过程。每层都进行了两次扫描,以检测重熔效果。在本研究中,模拟域设置为800×800×260μm,并切片为1312000个单元。往返策略,设置了两条轨道来了解整体凝固条件。棋盘策略,对四个岛屿的结合区域进行了建模,以获得额外的边界情况。与实际的增材制造工艺相对应,将单个激光束应用于熔融粉末,这导致岛扫描的时间成本更高。此外,在激光转向时关闭能量输入,以减少局部热量积聚对整体模拟的影响。HX的物理参数取自文献,激光参数也与实验数据一致。值得注意的是,密度和粘度随温度而变化,而不是固定值。
使用图像分析软件计算相邻表面的平均孔隙率和每个试样的顶面粗糙度。CB2试样的相对密度最高(M0:98.13%、M67:97.28%、M90:97.34%、CB1:96.98%和CB2:99.60%)。与其他试样相比,CB2的粗糙度最低。图3(a,c)显示了对应于LPBF扫描策略M90和CB2的抛光X-Y横截面的光学显微照片。通过往返策略制造的样品获得了LPBF工艺的三个典型缺陷,包括气孔、未熔合和未熔化的粉末,如图3中红色箭头所示。相反,CB2中出现了罕见的小孔和缺乏聚变粒子。图右上角的高倍率SEM图像显示了不同样品的未熔化粉末形态。由于存在球化缺陷,图3(b)(对应于最高粗糙度为48.298μm的M90样品)描绘了显著的表面波动。从图3中可以看出,岛状扫描实现了更平滑的打印质量,表面粗糙度也可能与内部孔隙含量有关。
图3(a)(c)M90试样和CB2试样的OM图像(b)(d)M90标本和CB2标本的粗糙度照片,M90(e)和CB2(g)试样的缺陷分布图像,以及M90(f)和CB1(h)试样的孔隙放大率。
考虑到从横截面图像中获得的体积孔隙率的不可靠性,从M90和CB2试样中获得的孔隙率分布如图3(e,g)。球形直径小于0.03mm的缺陷被清除为噪点。值得注意的是,CB2试样的孔隙率小于M90试样(分别为0.67%和7.94%),并且CB2试样中的缺陷主要分布在岛内含量较低的连接区。从中还可以看出,M90中的缺陷尺寸比CB2中的大,前者大多是大的不规则孔隙,后者主要是小孔,如放大图像图3(f,h)。M90块中当量直径大于100?m的孔隙数量高达23个,而CB2中只有3个。先前的研究已经确立了基于球度值来区分LPBF合金中孔隙类型的可行性,球度值源自缺陷的体积和面积:
其中V和A分别表示体积和表面。通常,球度值大于0.7被认为倾向于球化。根据统计分析,M90试样缺陷中球形孔隙的比例(60.68%)远高于CB2试样的比例(26.28%),但几乎没有观察到大于0.9的气孔。用不同的扫描策略获得的各种缺陷百分比可能与LPBF工艺中的冷却条件密切相关。
通过不同扫描策略制造的蚀刻样品的横向光学显微照片如图4。与顶面图像类似,所有曲流样品中都存在不规则的大孔隙和未融合的颗粒。此外,M0和M90中捕获了一些凝固裂纹,这已被确定为LPBF制造的HX合金的固有缺陷。一些沿着晶界分裂形成晶间裂纹,一些裂纹从孔中出现。这种差异是显而易见的,因为棋盘样品中几乎没有制造缺陷。如图4(d,e)所示,两个XZ表面图像显示了相邻岛屿之间的良好组合。从这些照片中,岛屿策略获得了平滑均匀的熔池地形。然而,由于冶金缺陷的存在,往返策略获得了波动的熔池轨迹。
图4(a-e)分别为M0、M67、M90、CB1和CB2试样的OM图像(a1-e1)和(a2-e2)相关试样不同放大倍数的SEM形态。
蚀刻后试样XZ表面的SEM图像如图4(a1-e1)。可以发现,不同样本的边界间隔是不同的。因此,测量六个区域的线距离(D),然后计算平均值。随着激光轨迹旋转角度的增长,数值变得更加广泛(DM0:4.824μm,DM67:5.101μm,DM90:5.739μm)。至于岛状印刷,由于激光路径不垂直或平行于XZ平面,因此显示出交替的熔融路径图案。此外,还拍摄了局部区域的高放大率图像,如图4(a2-e2)。柱状晶粒是竣工样品的主要微观结构。柱状晶粒可以在多个熔池中连续生长,并且在晶界中没有发现碳化物分布,这与我们以前没有逐层重熔工艺的工作不同。这可以另外表明合金在重熔过程之后实现了更多的均匀化。晶粒偏转角是决定微观织构取向的关键因素。从黄色箭头可以看出,只有CB2试样的晶粒生长方向严重偏离池边界法线方向(20.04°),而其余晶粒的偏转角小于10°(分别为M0:5.71°、M67:2.79°、M90:7.07°、CB1:4.17°)。
图5给出了不同试样沿构建方向的反极图(IPF)图和极图(PF)图,因此可以从EBSD数据中讨论晶体取向和晶粒尺寸。与水平方向相比,垂直方向的晶粒尺寸相当大,尤其是M0和M67样品。IPF图的颜色显示M90的〈1.0〉取向更为明显。有趣的是,从图5(e2)中可以看出,CB2试样表现出更明显的〈111〉微观织构,晶粒形态趋于等轴类晶体。图中的白色虚线表示每层的划分区域,相邻晶粒以不同的方向发展,晶粒的高度与粉末层的厚度相似。如图5(a1-e1)所示,CB2制造显示出最高的微观结构分布,最大指数为6.842,CB1样品的最大极性密度略降至6.814左右。然而,所有往返构建的微观结构都被削弱了,如下最大微观结构指数所示(分别为M0的5.326、M67的4.091和M90的4.976)。
图5(a-e)、(a1-e1)、(a2-e2)和(a3-e3)重建的EBSD、PF、IPF以及M0、M67、M90、CB1和CB2的KAM映射分别作为构建样本。
图5(a3-e3)描述了XZ纵向横截面局部区域中往返策略试样的更显著的取向差关系(M0、M67和M90分别为1.375°、1.645°和1.437°)。与纹理密度的趋势相反,岛状扫描获得了较低的KAM值(CB1样品:1.429°),CB2样品的平均KAM角显著降低到0.872°。由于KAM值可以表示残余应力的水平,因此有理由证明,竣工CB2块体中存在最低的内应力。几何必要位错(GNDs)可以反映镍基合金的塑性变形能力。通过设置5°的最大方位角来计算五个试样的平均GND密度(ρGNG),并对其进行计数以进行后续比较。CB2样品获得了最稀疏的位错密度(1.370×1013 m?2),这意味着通过这种岛扫描策略制造的金属块体的室温变形能力可能比其他构建方法更好。
此外,棋盘制造的平均晶粒尺寸略低于往返策略(分别为M0:10.84μm、M67:11.16μm、M90:11.06μm,CB1:10.68μm、CB2:10.40μm)。不同样品的纵横比(晶粒的短轴与长轴的比率)也从SEM图像中捕获。由于CB2样品中的优先晶粒生长趋势被抑制,它表现出最高的纵横比(0.46),而其余四个样品更倾向于外延生长(分别为M0:0.43、M67:0.44、M90:0.44、CB1:0.39)。相似的晶粒长度和宽度表明,CB2策略可以降低LPBF合金的各向异性,少量等轴晶体的存在也可以削弱非均匀性趋势,改善性能。
此外,凝固金属的恢复或再结晶可能发生在多次熔融过程中,因为在CB2样品中发现了一些等轴颗粒。因此,使用晶粒重建软件测量了晶粒的内部再结晶分数,具体数据如图所示。6。通过将2°设置为内部平均取向差角(IAMA)的临界阈值,变形晶粒的值高于2°。亚结构区域被定义为IAMA<2°,但亚晶粒的取向差是大于2°的IAMA。除此之外,其他晶粒被标记为再结晶晶粒。CB2试样的变形晶粒百分比最低(12.72%),回收晶粒百分比为69.46%。
图6 不同样品的再结晶图,分别包括M0、M67、M90、CB1和CB2。
图7(a)显示了五个竣工试样的代表性工程应力-应变曲线和断裂试样的宏观形貌。不同程度的颈缩现象发生在断裂区附近。通过CB2策略形成的样品实现了拉伸强度和伸长率的最佳平衡,其中屈服强度(YS)、极限拉伸强度(UTS)和断裂伸长率(El)分别达到579±38MPa、816±17MPa和29.2±4.8%。对于CB1样品,三种力学性能的值都有所下降(YS:454±57 MPa,UTS:814±17 MPa,El:24.3±3.2%)。与之前的研究一致,M67试样的结果优于M90(YS值分别为568± 54MPa和546±57MPa,UTS值分别为762± 44MPa和721±35MPa,El值分别为16.0± 3.3%和13.2± 4.9%)。
由于打印缺陷的数量最大,M0样品获得了最差的强度(分别为YS:473±64MPa和UTS:580 ±65MPa)和伸长率(3.5±2.0%)。
图7(a)工程应力-应变曲线和五个拉伸样品的宏观照片,(b)五个拉伸样本的真实应力-应力曲线和应变硬化率曲线,(c)不同扫描策略的拉伸性能,分别代表M0、M67、M90、CB1和CB2,(d)激光重熔HX合金的UTS与伸长率和以前的文献值。
真实应力-应变曲线和应变硬化率也绘制在图7(b)。真实应力的分布趋势与工程应力值相似,棋盘策略的应变硬化率优于往返策略。与拉伸强度相对应,CB2试样的位错硬化也略高于CB1试样。选择并分析先前的文献,然后提取UTS和伸长率,得到图7(d)。绿色点是从制造的HX中获得的,而蓝色数据是从这些铸态合金中提取的,作为基准。在目前的研究中,使用红球突出显示了不同拉伸样品的数据。与之前的研究相比,在不进行后热处理的情况下,CB2样品的重熔工艺可以获得更好的效果。
为了进一步讨论增强性能的性质,通过SEM观察研究了五个拉伸部件的断裂表面形貌,如图7(a)。根据图8(a-e)的形态信息,每个样品的断裂表面都存在裂纹和孔隙。M0、M67、M90和CB1的SEM图像中明显出现了许多残留的未熔融颗粒,这与先前的OM结果相似。至于CB2本体,图8(e)中捕捉到几乎不存在球形粉末。图8(a1-e1)和图8(a2-e2)分别是拉伸断裂的较高放大率。值得注意的是,凹坑是主要的微观结构特征,这是这些建成块中发生韧性断裂的证据。此外,在M0样品中,在孔附近也很少产生类似解理的区域。解理面的存在意味着准解理断裂的开始。毫无疑问,M0的伸长率正在下降到CB2试样的约12%。然而,解理状表面可能不仅仅是解释极弱延展性的原因,而且凹坑的大小也可以在解释两种制造之间的性能差距方面发挥作用。CB2样品内部凹坑的平均尺寸略大于M0样品(M0:0.410μm和CB2:0.646μm)。由于CB2断裂中出现了韧窝和解理面的混合物(图8(e1,e2)),韧性-脆性协同断裂机制值得更多关注。此外,在补充信息中提供了与颈缩区域相邻的拉伸样品的详细分析。更重要的是,CB2试样的位错密度升高率相对高于M0试样,这也符合CB2拉伸试验中更好的伸长率(分别为M0:16.7%和CB2:159.2%)。
图8(a-e)M0、M67、M90、CB1和CB2样品的SEM断裂照片,分别为(a1-e1)和(a2-e2)局部区域的高放大率照片。
在不同的熔融区上进行了纳米压痕实验,以评估显微硬度。熔池被分为两部分,一部分是非重熔区(NRZ),它是仅在单个粉末层中的两条熔池线的中间区域,而另一个区域被命名为重熔区(RZ)。如图9(a)所示,RZ通常比NRZ更硬,CB2样品比其他样品更硬(NRZ:4.946GPa和RZ:5.679GPa)。对于M0样品的最高孔隙比,块体表现出相对最差的硬度(分别为NRZ:4.350GPa和RZ:5.099GPa)。此外,还对棋盘扫描的过渡区域进行了测试。与其他区域相比,这些弱点获得了较低的显微硬度(分别为CB1:3.894GPa和CB2:3.970GPa)。CB2试样的硬度明显高于其他试样。人工测量一次枝晶臂间距(PDAS)以区分微观结构变化。测量每个区域的枝晶距离5次,并获得平均值。图9(b)描述了CB2试样的PDAS值仍然处于最低水平,而与RZ(0.40μm)或NRZ(0.60μm)无关。此外,通过比较这两个区域,RZ的值通常低于NRZ的值,显示出与显微硬度一致的趋势。
图9(a)竣工样品的纳米硬度值(b)不同样品的PDAS,分别代表M0、M67、M90、CB1和CB2(c)CB2试样NRZ的PDAS测量图(d)CB2试样RZ的PDAS测量图。
在本研究中,主要的制造缺陷被确定为大的不规则孔隙和气孔。激光能量密度不足是形成不规则孔隙的主要原因。由于熔体蒸发引起的反冲压力,气孔可以容易地以更高的能量密度形成。在这种情况下,较低的激光辐射不能充分熔化金属粉末,导致大尺寸孔隙内残留颗粒。在LR加工过程中,第二能量输入导致熔体飞溅,导致出现不规则的大开孔。除了能量密度外,屏蔽氮流入活性熔融金属也可能是形成这些缺陷的一种可能解释。气孔主要归因于施工室内的保护性气体或粉末表面未干燥的水分。值得注意的是,原始颗粒干燥时间的延长导致HX制造中微孔含量较浅。这些发现有助于理解使用LR加工的金属材料中缺陷形成的机制,并为开发改进的加工技术以实现无缺陷制造提供信息。
第一次扫描后的重熔过程在熔池中引发了严重的Marangoni对流和蒸汽羽流,导致一定程度的金属飞溅。这种方法还加速了熔池内焊剂的蒸发,导致在下一次粉末堆积之前,球形颗粒聚集在熔化轨道周围。此外,由于图3(a)中残余颗粒的存在支持了激光能量密度不足,以及某些区域的粉末层厚度相对较高,因此激光无法完全熔化金属颗粒。这削弱了层间结合效应,并导致形成许多不规则的大孔,在顶面上产生明显的波浪。此外,孔隙率可能与激光扫描路径长度呈正相关。弯曲策略制造的较长激光轨迹允许由于延长的冻结间隔而在熔池中生长空穴。岛策略的路径长度几乎是往返扫描的一半,这可能是第二次扫描期间较低余热效应的原因。这些发现有助于更好地理解重熔和激光扫描策略对使用激光技术制造的金属材料的质量和缺陷的影响。
与传统的制造技术相比,LPBF方法由于更高的冷却速率和温度梯度而产生柱状晶粒。图中的显微照片4(a-e)表明在第二次扫描过程中形成了重熔轨迹,与粉末相比,由于固体金属具有优异的导热性,因此其冷却速度自然更高。LPBF的逐层熔化方法使熔池的顶部晶粒能够重复熔化并沿着优选的方向生长,这进一步受到扫描策略的影响,导致不同的微观结构,如图5(e)。CB2样品重熔过程中的热发射导致晶粒倾斜,而不是向上生长,改变了柱状晶粒的优先取向,转变为〈111〉微观织构分布。
CB2策略中相对较细的晶粒可归因于第二次熔化期间较高的冷却速率和较快的成核。据观察,在第二次熔化过程中,积累的热量会使少数变形晶粒重新熔化,这可能导致无序的形核和生长。此外,CB2具有最低的PDAS,这意味着它具有最小的亚晶粒尺寸。围绕这些亚晶粒的位错网络限制了位错的滑动,从而提高了机械强度。Hall-Petch方程表明,对于CB2试样,更细的亚晶粒也产生更高的强度。此外,较高百分比的亚结构表现出较低的内部位错密度和残余应力,这也可以导致更好的伸长率效果。
在LPBF-ed HX合金中,位错硬化是除晶界强化外的主要强化机制。在棋盘样品中观察到的较高应变硬化率表明,在拉伸试验过程中,多个滑移系统同时运行,导致位错在应力集中(如晶界、孔隙和微裂纹)中增殖和积累。图8(a)可以作为支持这一观点的确凿证据。
Masahiro Kusano观察到的PDAS的减少反映了LPBF过程中冷却速率的快速增加。在第二次扫描期间,未完全冷却到环境温度的固体金属被重新注入激光能量。热扩散系数的差异将导致垂直熔体线方向上的点的不同冷却速率和热梯度,最终影响材料的硬度。除了残余应力和位错密度外,内部孔隙率在决定材料显微硬度方面也起着重要作用。较低的硬度值表示较差的结合效果,如图7(a)所示的锯齿状断裂形态所示。XCT三维图像显示,岛屿边界几乎没有孔隙,进一步支持了该地区较软的特征。
图10显示了两个粉末层的两次扫描的温度-速度场分布。熔融金属的蒸发在一定程度上发生在与粉末的激光接触区的前部,这是由于在小区域内积累了大量的热量,导致温度高于蒸发点。尽管如此,较厚的光斑直径和中等的激光能量密度导致了气泡的不存在。如黑色轮廓线所示,由于熔池尾部的流速较弱,激光束的移动和蒸发产生的反冲压力在熔池内部引起了显著的逆时针Marangoni对流。此外,由于固体的传热系数大于氮气的传热系数,由重熔扫描产生的熔池体积小于由第一次扫描产生的熔融池体积,通过比较图10(b,d)和图10(a,c)可以明显看出。
图10 同一截面在不同状态下的温度场和速度场(a)第一层和第一次扫描,(b)第一层与第二次扫描。
图11(a)显示了五种不同策略下粉末床中心点温度随时间变化的各种曲线,包括单层粉末的第二次扫描。除M67样品外,第一次扫描导致熔池温度高于重熔样品。此外,由于激光扫描速度均匀,构建相同尺寸的岛状样品所需的时间更长,这从图11(a)中也很明显。由于激光移动路径的差异,与长线扫描相比,岛状策略经历了多次热循环,CB1样品多次达到峰值温度,并且CB1的CB2峰值温度略低。此外,图11(b)展示了粉末层模型的平均温度曲线。值得注意的是,棋盘策略的最终平均温度远高于曲流策略,其中CB2达到880.88 K。这表明扫描后熔体的流动时间更长,可能会填充一部分孔隙,这可能是密度更高的原因。
图11 不同扫描时间和不同样品的温度-时间曲线分别表示M0、M67、M90、CB1和CB2(a)模型中心点的瞬态温度曲线(b)模型的平均温度曲线和(c)模型的每单位体积的累积蒸发质量。
根据liu的研究,打印引起的缺陷受到熔池蒸发的影响。具体而言,当温度超过材料的熔点时,金属颗粒蒸发并离开熔池,产生向下的反冲压力,促进熔池内的内部流动和孔隙成核。此外,强烈的蒸发会导致蒸发羽流,周围粉末的无序流动可能会加速大的不规则孔隙的形成。为了进一步解释密度差异,研究人员计算了每单位体积的累积蒸发质量,如图11(c)。虽然由于路径长度不同,最终蒸发值不同,但讨论的重点是不同模型在同一时期的蒸发。局部放大显示棋盘策略的蒸发比往返策略的蒸发弱得多。因此,可以假设CB2在制造相同尺寸的块时将损失最低的质量。质量损失越大,蒸发越剧烈,进一步破坏熔池的稳定状态。因此,棋盘制造的高密度可归因于较低的蒸发质量损失。
图12显示了各种型号的冷却速率图,所有这些都是从扫描轨迹的中心拍摄的。由于在这些模拟中激光束运动的轨迹不同,只选择了四个部分来检查横截面附近的冷却速率变化。熔池内部的冷却速率明显高于边缘,如图12(b4,c2)。此外,在相邻轨道扫描之后的热效应导致更深的区域经历冷却。此外,图12(d1,d4)和(e1,e4)表明,岛状扫描的冷却速率高于往返扫描。除M67外,在其他策略中,未重熔区的冻结率显著低于重熔区。这归因于第一次扫描后固化流的传热系数更显著,这导致更快的热扩散、相对较小的熔池体积以及重熔过程中更高的冷却速率。由于重熔区的凝固速度更快,最终结果将是局部区域的硬度相对较高,与纳米压痕测试结果一致。然而,应该注意的是,由于两个轨道的中心被选择在固液界面,所获得的数据将略高于LPBF实验中测量的冷却速率(105–106 K/s)。此外,除了冷却速率外,本研究还检查了温度梯度和温度梯度与生长速率的比率(G/R),如补充信息所示。观察到,与其他模型相比,CB2策略具有更高的平均G/R值(图S3),这意味着成分过冷不太明显,随机晶粒形成的可能性较小,从而导致更明显的微观织构。
图12 激光轨迹(a1-a4)M0、(b1-b4)M67、(c1-c4)M90、(d1-d4)CB1和(e1-e4)CB2样品之间XZ截面的冷却速率分布的比较。
总之,棋盘扫描策略的独特热流方向和重熔的第二次能量输入导致CB2试样内的晶粒偏转角更加突出,从而产生更加突出的〈111〉微观织构。棋盘策略中,蒸发引起的粉末飞溅不太可能发生,增强的流动性可以关闭一些不规则的孔隙。此外,在流动过程中,金属与未熔化的粉末结合,这提高了随后激光扫描的烧结效率。相反,对于弯曲样品,在两次焊道中使用相同的激光能量密度会增强熔池中的Marangoni对流,导致飞溅和羽流,从而降低密度。尽管对于相同数量的印刷层,岛状策略可能需要更多的时间,但由于较高的冷却速率可能导致合金在第二次扫描激活之前固化,因此它可能导致类似于传统工艺的后处理效果。因此,重熔允许合金内部恢复,甚至再次熔化凝固的金属以产生新的晶粒。最终,通过重熔和棋盘扫描制备的HX合金的强度和延展性得到了协同增强,超过了LPBF ed HX合金既定的性能。此外,重熔(一次和四次)和扫描策略(层间旋转角度的90°和67°)的组合可以产生更致密的合金。应进行进一步的研究,重点关注熔化时间和旋转角度的组合,以获得较低缺陷密度的较窄窗口。
本文设计了五种LPBF扫描策略,并分析了不同HX合金重熔后的密度、微观结构和室温力学性能。CFD模型用于模拟熔体流动,并进一步解释了凝固机理。具体研究结果总结如下:
1)与往返扫描相比,棋盘扫描重熔HX的表面更光滑。棋盘2策略的内部密度(99.33%)明显优于往返90°策略(92.06%),这是由于其优异的流动性和较轻的熔融金属蒸发。通过弯曲策略获得的合金内部的大量孔隙缺陷严重削弱了力学性能。
2)所有试样的微观结构主要由柱状晶粒结构组成。最短的平均树枝壁间距证明棋盘2试样具有最快的冷却速率。棋盘2试样的主要特征也是微观织构强度最强和位错密度最低,由于晶粒偏转角最大(20.04°),表现出明显的〈111〉取向。
3)在室温拉伸试验中,棋盘2试样获得了最佳的力学性能,其断裂机制主要为韧性-脆性协同断裂。根据GND的较高百分比上升,棋盘2样本在拉伸过程中驱动了大量的滑移系统。由于晶界强化和位错硬化,具有较小亚晶粒的棋盘2试样比其他试样更硬,尽管弱点大多分布在岛状连接处。
4)通过流体模拟分析,短线性棋盘策略导致了优越的冷却速率,粉末模型的平均温度更高,从而使扫描后的熔体流动性更好。重熔处理可以产生部分恢复的晶粒,进一步提高伸长率。较高G/R值的较宽区域也表明棋盘2试样晶粒不再倾向于垂直于熔池底部生长,但重熔可以形成一定量的等轴晶体。
对于棋盘扫描,第一次熔化可以产生更快的冷却速度和更好的熔体流动性,进一步填充孔隙缺陷。与重熔工艺相结合,凝固晶粒内发生回复,从而释放残余应力、稀疏位错和优异的机械性能。棋盘2策略与激光重熔相结合,实现了其他策略的最佳性能。重熔工艺与棋盘策略相结合,产生了良好的结合效果和力学性能,可为工程应用提供指导。
论文链接: https://doi.org/10.1016/j.matdes.2023.112386
免责声明:本网站所转载的文字、图片与视频资料版权归原创作者所有,如果涉及侵权,请第一时间联系本网删除。
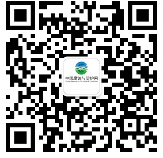
官方微信
《腐蚀与防护网电子期刊》征订启事
- 投稿联系:编辑部
- 电话:010-62316606
- 邮箱:fsfhzy666@163.com
- 腐蚀与防护网官方QQ群:140808414