海底管道是海上油气田开发的大动脉,是海洋油气资源开发工程的重要组成部分。但是这些大规模的海底油气运输管道,必然会受到海洋环境的腐蚀侵害。
海底管道的腐蚀问题主要来自以下几个方面:管线内流体的腐蚀、海洋环境所引起的外腐蚀、交叉作业和自然灾害造成的机械损伤等。我国每年因腐蚀造成的经济损失至少有200亿元,尤其是在石油化工企业腐蚀损失量更大。
1 失效件概述
某油田管线所在海区水深约为30m,年平均气温为22.9℃,底层流速达1.08m/s。XX12-1B平台和XX12-1A平台之间采用立管(RISER)和输送管(PIPELINE)连接。XX12-1B平台高度31.4m,XX12-1A平台高度30.2m,输送管线总长度为2.3km。B平台下岸海底管道压力范围为1.5MPa~2.0MPa,A平台上岸海底管道压力基本维持在约1.6MPa。下岸海底管道与上岸海底管道内压力间存在0.5Mpa的压降。B平台至A平台间立管和输送管道均为双层管,双层管结构由外向内依次为:防腐蚀层、外管、聚氨酯保温层、内管。间隔一定距离安装隔离木,用于支撑外管与内管间距离。由B平台输送至油田A中心平台的流体包括:原油、油田产出水和天然气。B平台至A平台间海底管道外腐蚀采用牺牲阳极阴极保护。输送过程中,在流体中加注缓蚀剂和防垢剂用于管线防护。目前,B平台外输管线采用缓蚀剂HYH-80-N和阻垢剂HYZ-121,加注方式为连续加注,质量浓度均为30mg·L。
图1 B平台至A平台海底管道示意图
2 试样形貌
2.1宏观形貌
失效件取样位于弯管4处内管膨胀弯管一段,尺寸为Φ273.1*11.1mm,钢号为X65。
图2中样品放置方向为服役时的6点方向朝上,可观察到样品自弯管下游起6点方向存在成串的穿孔,从距下游焊缝0.57m处开始出现穿孔,成串的穿孔延伸至下游直管段。样品外壁6点方向存在局部腐蚀,直管段外壁有成片的腐蚀坑,弯管外壁6点方向存在腐蚀坑。将样品剖开,观察分析样品腐蚀情况,见图3。
图2样品宏观形貌
(a)内壁腐蚀穿孔
(b)内壁焊缝处腐蚀形貌
图3样品内壁腐蚀形貌
由图2、3可见,样品外壁腐蚀主要集中在6点方向,腐蚀区域从管端至焊缝,腐蚀方式为点蚀,最大腐蚀坑深度2.12mm直径27.24mm,部分腐蚀坑出现穿孔,参考海底管道服役工况,推断穿孔是由海底管道内壁腐蚀造成的,穿孔方向由内壁至外壁。
海底管道内壁附着有黑色油泥导致管体内壁呈黑色。为进一步观察样品内壁腐蚀产物形貌,用丙酮清洗除油后,观察内壁腐蚀产物形貌。样品管体内壁覆盖致密腐蚀产物层,厚度约为0.6~1.0mm。腐蚀产物表面凹凸不平,但凹凸处边缘圆滑,各方向腐蚀产物均无龟裂现象。腐蚀产物主要为黑灰色,部分区域呈红棕色,估计为样品腐蚀产物在大气中氧化所致。值得注意的是,样品焊缝处测量点壁厚与其他位置测量点壁厚相差不大,且腐蚀程度相似,因此焊缝并非海底管道的腐蚀薄弱环节,这与宏观分析结果吻合。
2.2微观形貌分析
为观察海底管道内壁腐蚀形貌,在样品弯管段12点方向、6点方向切取15×15mm块状试样,用丙酮清洗烘干后,并用SEM观察其横截面形貌并进行EDS分析。如图4.
(a)样品12点方向
(b)样品12点方向
(c)样品6点方向
(d)样品6点方向
图4样品内壁横截面形貌及腐蚀产物能谱分析
表1样品内壁腐蚀产物能谱分析结果(原子百分比atom%)
如图4所示,样品直管段内壁12点方向腐蚀产物较薄,内壁可见底大口小的葫芦状腐蚀坑,坑内填满由Fe、C、O和少量S组成的腐蚀产物。图2(c)为6点方向原有的较厚腐蚀产物脱落处,残留的腐蚀产物呈碎屑状。紧贴金属壁的腐蚀产物由Fe、C、O组成。在弯管内壁可观察到鳞片状晶体,该晶体以Fe、C、O元素比为1:1:3并含有少量的S元素,根据晶体形貌和能谱分析结果的原子百分比推断,管体内壁鳞片状晶体为FeCO3。
对现场取得的典型部位腐蚀产物清洗研磨后进行XRD分析,XRD测试环境真空度为10-8Torr,辐射光源为AlKα(1486.71eV)单色光源,光源强度为100W(10mA,10kV),采用中核电荷补偿表面电荷影响,键能标定采用C-H键(标准峰283.6eV,试验峰284.8eV,Δ=1.2eV)。
通过对XRD谱拟合可以发现,腐蚀产物主要以有少量Fe的氧化物、等沉积物,样品中还含一定量细砂。在油田生产中还是不可避免带入少量细砂,因此,在后续的高压阀模拟试验中加入少量的细砂进行模拟。通过腐蚀产物分析这表明海底管道内壁覆盖的硫酸锶钡盐结垢层,垢层表面存在较多裂纹,其在局部形成了垢下腐蚀环境,加速了海底管道内壁腐蚀。
图5内壁腐蚀产物XRD谱
3 模拟试验
根据现场提取的油水混合样,进行初步油水分离后与现场运回的硫酸盐还原菌(SRB)培养液混合,室内进行结垢预测,本实验参照《SY-T 0026-1999 水腐蚀性测试方法》,《SY-T5273-2000 油田采出水用缓蚀剂评价方法》,使用高温高压釜进行挂片实验,挂片条件如下:(A)有细菌环境+细砂;(B)无细菌环境+细砂;(C)无细菌环境+细砂+挂片上有碳酸钙和硫酸钡垢层;(D)有细菌+细砂+挂片上有碳酸钙和硫酸钡垢层;
试验中海底管道的实际出口温度为48℃,出口压力为1.6MPa,含水率21%,试验周期30d。试验环境有油水混合液环境1、2和高压釜环境,其中,油田混合液直接取自现场,高压釜底环境模拟油田采出水环境。试验结束后,观察局部腐蚀情况,并对挂片失重进行测量,计算腐蚀速率,对腐蚀后的挂片进行电镜扫描分析。
表2试片在不同试验条件下挂片试验30d后的腐蚀速率
表3试片在不同试验条件下挂片试验30d后的最大点蚀深度(mm)
由表2、3可见:釜底的挂片都要比同条件油水介质中的挂片腐蚀严重,根据水质分析和结垢预测并结合现场垢样分析结果,现场管内有钡盐、有结垢物质,所以试验工况中:有SRB、有细砂、有碳酸钙硫酸钡垢层最符合现场工况。
将试验后的挂片用石油醚清洗表面的油污后,进行SEM分析,如图6。很明显,在高压釜实验条件(a)、(b)中,SRB的存在导致腐蚀产物增多,在(c)、(d)中,碳酸钙硫酸钡垢层的存在,导致腐蚀更为严重。在实验条件D(有SRB,有细砂,有碳酸钙硫酸钡垢层)下,腐蚀最为严重,出现大量点蚀坑,而且蚀坑深度最深,说明SRB+碳酸钙硫酸钡垢层的存在对挂片腐蚀影响更为严重。
(a):有SRB,有细砂 (b):无SRB,有细砂 (c):无SRB,有细砂,有碳酸钙硫酸钡垢层(d):有SRB,有细砂,有碳酸钙硫酸钡垢层
图6高压釜底挂片SEM照片
4 结论与建议
根据海底管道腐蚀失效分析,实验室模拟试验结果,同时参考海底管道服役工况得出以下结论:
在深海管道材质满足API5L的要求,焊缝区没有表现出较管道本体更加严重的腐蚀趋势。
海底管道内部发生了结垢,垢样组成主要有CaCO3、BaSO4等组成,其在局部形成了“垢下”腐蚀环境,加速了海底管道内壁腐蚀,最终导致腐蚀由内至外穿孔。
实验室高压釜模拟实验表面:有SRB+有细砂+有碳酸钙硫酸钡垢层最符合现场工况。测试最深处约0.060mm,通过计算得到点蚀速率为0.6488mm/a。
针对海底管道失效,根据分析结果,提出以下建议:
在继续保持现有的电化学牺牲阳极保护措施外,评选适合B至A海底管道流体使用的防垢剂,该防垢剂既能抑制CaCO3,还能抑制BaSO4结垢,其加注于海底管道,可有效降低结垢物,防止结垢物质沉积管底,破坏“垢下”腐蚀的环境;
增加流速,降低流体在海底管道内的停留时间,避免油水分离;或者直接在B平台进行油水分离,降低海底管道油水混合物的含水量;
定期清管,为了有效破坏“垢下”腐蚀环境,建议可以考虑采用直板或者皮碗等除垢较好的清管器,并每次对清管产物进行分析,确定清管效果;
加强海底管道腐蚀检测,包括:防垢剂效果,清管效果,腐蚀速率变化趋势,水样中结垢离子变化等,做到及时发现问题,及时解决问题。
更多关于材料方面、材料腐蚀控制、材料科普等等方面的国内外最新动态,我们网站会不断更新。希望大家一直关注中国腐蚀与防护网http://www.ecorr.org 责任编辑:王元 《中国腐蚀与防护网电子期刊》征订启事
投稿联系:编辑部
电话:010-62313558-806
邮箱:ecorr_org@163.com
中国腐蚀与防护网官方 QQ群:140808414
免责声明:本网站所转载的文字、图片与视频资料版权归原创作者所有,如果涉及侵权,请第一时间联系本网删除。
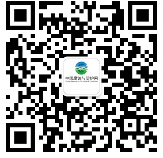
官方微信
《腐蚀与防护网电子期刊》征订启事
- 投稿联系:编辑部
- 电话:010-62316606-806
- 邮箱:fsfhzy666@163.com
- 腐蚀与防护网官方QQ群:140808414