高温合金的发展为燃气涡轮发动机的性能提升做出了重要贡献。近年来,为满足发动机涡轮前温度不断提升的需求,在进一步发展更高服役温度和环境抗力的高温合金的同时,也相继开展了探索研发铁、钴、镍基以外的高温金属结构材料的研究工作,例如:高熵合金、金属间化合物基合金等。其中,关于Ti-Al、Ni-Al和Nb-Si系金属间化合物的研究历史较长、相对比较深入,一些合金也逐渐在航空航天等领域获得应用。本文主要对近年来Ti-Al、Ni-Al和Nb-Si系金属间化合物的研究进展和成果进行介绍。
1 Ti-Al系金属间化合物
近年来,我国Ti-Al系金属间化合物的基础研究与工程应用均取得重要进展,主要体现在:(1) 新一代高铌含量TiAl合金成分设计与组织-性能关系研究发现新的规律和机制;(2) 二代TiAl合金工程应用取得突破;(3) Ti3Al和Ti2AlNb合金工艺进步显着,应用范围不断扩大。
1.1 锻造高铌含量TiAl合金组织控制及力学性能优化
高铌TiAl合金是北京科技大学Chen等最早提出的,特点是高温蠕变和抗氧化性能好,使用温度比普通TiAl合金高约100 ℃,缺点是室温塑性更低,难以铸造成形。因此,高铌TiAl合金大多是由高温锻造、挤压等热机械变形的方法制备,之后再通过热处理优化组织提高其室温塑性。
在对该系合金进行广泛研究的基础上,提出了辩证地利用和控制B2相,即高温下细化组织、提高热变形能力,同时在热变形过程中逐步减少和消除室温非平衡的脆性B2相的产生。变形高铌合金Ti-45Al-8.5Nb-(W, B, Y, C) (原子分数,%,下同)的细小近片层组织比国外强度最大的TNB (Ti-45Al-8Nb-0.2C)和TNM (Ti-43.5Al-4Nb-1Mo-0.1B)合金[6,7]强度高约200~300 MPa,其塑性也与TNB和TNM相当。经多次等温锻造变形,形成均匀细小的双态组织,室温延伸率超过2%,900 ℃的强度为490 MPa。铸态直接轧制板材通过控制变形温度可以得到TiAl合金的双态和近全片组织(图1),这是首次通过控制高温变形温度直接得到的均匀细小的全片层组织,省去了繁琐的热处理工艺。
研究发现,8Nb和10Nb的添加对Ti-(40%~50%)Al成分区间的垂直截面图产生显着影响。如:β/β+α相转变点降低大约50~80 ℃,β相区扩大并扩展到高Al含量区,α单相区被压缩、移向高Al含量区,添加8Nb使α→α2+γ共析转变温度上升至1170 ℃。因而,高铌TiAl合金的Al含量上下限对于合金的相变、组织和性能影响很大,应控制Al含量(原子分数)偏差小于1%。
1.2 铸造高铌含量TiAl合金的成分设计与热处理
精密铸造具有近净成形、工艺流程短等优点,是TiAl合金工程应用重点考虑的成形工艺。在国家973项目支持下,针对铸造工艺特点开发了新型高铌含量TiAl合金及特殊的热处理制度。
由于铸造合金不需引入β相来增加高温变形能力,提出采用较高Al含量的成分设计,以避免高温无序β相对高温强度的不利影响,同时还可减小凝固区间、有利铸造充型。实验发现,选定Nb含量为7%,当Al含量由46%增至47.5%时,900 ℃抗拉强度可提高至594 MPa;当Al含量超过47.5%时,抗拉强度稍有降低。分析表明,高铝、高铌的TiAl合金中B2相很少,是其高温强度和持久性能(图2)具有明显优势的原因之一。但是,其室温拉伸塑性几乎为零,室温脆性问题突出。根据研究经验,采用多步热处理工艺可得到细小的双态或近全层片组织,使合金的室温延伸率提高到1.0%以上,但900 ℃下的强度优势却因此消失。然而实验[15]发现,700 ℃退火处理可使该合金的室温拉伸塑性从小于0.4%提高到1.0%以上,这种采用低温退火改善TiAl合金室温塑性的现象目前尚未见报道。
应用英国ISIS的EngX设备对铸态和低温退火2种状态试样残余应力进行中子衍射测试,以退火态试样基体中(001)和(110)晶面的面间距为d0,计算拉伸试样标距内横截面外缘到中心位置应变和残余应力的相对值。结果表明,相对退火态,铸态试样中的确存在较高的残余张应力,最大差值出现在近表面层0.5 mm处,该位置铸态试样中残余应力为49.7 MPa,而退火态残余应力平均值仅为4.1 MPa。
可见,导致材料脆性的因素除化学成分、晶体结构、冶金缺陷和组织之外,还有残余应力状态。塑性较低的TiAl合金中存在的残余拉应力会阻碍塑性变形,导致拉伸试样的脆断。
1.3 二代TiAl合金工程应用取得突破
国际上二代TiAl合金已在航空和汽车发动机上取得商业应用。国内研制的Ti-47.5%Al-2.5%V-1.0%Cr-0.2%Zr合金增压器涡轮应用取得重要进展。某型高功率密度增压发动机对比实验表明,装配该零件的发动机全负荷瞬态加速响应性提高49%,比油耗降低3 g/(kW·h),稳态烟度降低0.2波许,总机械效率提高1.5%。在车辆实验中,整车的加速响应时间缩短了近30%,结构减重效果十分显着。该TiAl涡轮已通过增压器超温超转和发动机整机耐久性考核,现正在车辆上进行全路况考核,首阶段1000 km行驶后拆解检验涡轮本体完好,涡轮叶片与涡轮壳体配合间隙未见变化。
1.4 Ti3Al和Ti2AlNb合金制备工艺与应用的研究进展
Ti3Al基合金和Ti2AlNb基合金同属Ti-Al系金属间化合物材料,但工艺性能优于TiAl合金,已成为新一代航空发动机中高温部件最有潜力的备选轻质合金材料。
美国GE公司研制的Ti3Al基合金高压涡轮定子支撑环在GE-29发动机上成功地经受了试车考验[20],Ti3Al基合金高压压气机匣和燃烧室扩张型喷管封口也进行了试车。
国内研制的Ti3Al基合金[21]零件已装神舟号飞行,Ti2AlNb基合金完成了从实验室向工程化生产的转化。通过对电极制备、低熔速熔炼、末次氦冷熔炼过程控制,冶炼出直径540 mm的吨级铸锭。利用两类合金在高温单相区的热变形能力,多次镦拔锻造破碎铸态组织;在α2+O+B2三相区采用循环换向锻造使α2+O相充分变形,获得均匀细晶等轴组织。图3显示了制备的Ti-22Al-25Nb合金直径300 mm棒材超声波探伤达到GB/T 5193-2007标准A级(直径2.0 mm平底孔-6 dB)。
2 Ni3Al金属间化合物基合金
Ni3Al为具有长程有序的L12结构的金属间化合物,与镍基高温合金相比,Ni3Al基合金由于具有较高的比强度和较低的密度而受到关注。近年来,我国Ni3Al基合金研究取得了长足的进展,已逐渐开始在航空航天等领域获得应用。
2.1 Ni3Al基合金强韧化研究
Ni3Al金属间化合物的熔点为1390 ℃,密度7.5 g/cm3,Young's模量180 GPa,具有高的高温比强度,是一种潜在的高温结构材料。自科研人员通过在Ni3Al中添加微量B元素,显着改善了多晶Ni3Al的室温塑性之后,国内外对Ni3Al作为高温结构材料开展了大量研究,但未能在兼顾室温塑性和高温强度等综合性能方面取得实用性突破。
近年来,为了满足我国航空航天等领域对高承温、低密度高温结构材料的需求,我国科研人员借鉴镍基高温合金的强韧化经验,针对偏离金属间化合物化学计量比(富Ni侧)的Ni3Al基合金开展了强韧化和抗氧化的应用基础研究,成功研制了几种Ni3Al金属间化合物基合金。这类合金在性能上保持了Ni3Al金属间化合物高比强、低密度的优点,又兼具镍基高温合金良好的塑性和抗疲劳优势,并且在铸造工艺上基本与镍基高温合金相同。
为满足航空发动机高涡轮前温度(≥1850 K)的要求,利用镍基高温合金现有数据库、蠕变抗力计算、电子平衡理论和d电子理论,对Ni3Al金属间化合物合金进行了模拟计算,结合实验验证,研制出1100 ℃导向叶片用定向凝固金属间化合物基合金JG4010 (IC10)。该合金不含贵金属Re,初熔温度≥1320 ℃,密度约8.29 g/cm3,高温持久性能高,1100 ℃、100 h下的纵向持久性能大于80 MPa,高温下组织稳定,经950 ℃、3000 h长期时效后无TCP相析出,1100 ℃达到完全抗氧化级,同时具备优良的抗热腐蚀和铸造工艺性能,可进行大缘板、薄壁(0.6 mm)、复杂内腔结构导向叶片的整体定向凝固成型。
为了进一步提高Ni3Al基合金的服役温度,满足更高涡轮前温度(>1950 K)的新一代航空发动机研制需求,在对镍基单晶高温合金的γ‘-Ni3Al强化相回溶温度研究分析的基础上,开展了可进一步发挥Ni3Al金属间化合物高温稳定性和低密度优势、目标服役温度≥1150 ℃的新型Ni3Al基单晶合金的合金化研究。结果表明,通过适当地增加Al和Ta的含量,并结合固溶热处理消除初生大块Ni3Al相,可有效提高Ni3Al相的回溶温度(提高有序度)。如图4c所示,1200 ℃热暴露后Ni3Al相体积分数大于55%。从图4b还可以看出,热处理后Ni3Al相的体积分数大于80%,但室温组织仍是由γ-Ni基固溶体相与γ'-Ni3Al相构成,与镍基高温合金极其相似。借鉴镍基高温合金的合金化元素作用机制,采用第一原理计算和实验研究确定固溶强化元素和加入量,通过添加Mo和Re元素(<1.6%,质量分数)有效提高了Ni-Ni、Ni-Al对间的键合强度,起到了Mo-Re合金协同强化作用,两相界面为负错配,1200 ℃的错配度绝对值约为0.47%。在此基础上,研究了添加微量活性元素Ce、Dy等对合金抗高温氧化性能的影响。图5a为添加不同含量Ce元素后合金1100 ℃循环氧化增重曲线(强制风冷,每小时循环1次),Ce含量约为0.005% (质量分数)时,合金达到完全抗氧化级。
经过成分优化后的新型低铼Ni3Al基单晶合金(暂定牌号:IC21)的初熔温度≥1340 ℃,密度约为8.20 g/cm3,[001]取向1150 ℃、80 MPa的持久寿命>1000 h (未断),[111]取向1150 ℃、137 MPa的持久寿命>150 h,1100 ℃达到完全抗氧化级,同时具备优良的铸造工艺性能。值得指出的是,该合金[111]取向1100 ℃、137 MPa的蠕变寿命>1400 h。研究发现,IC21合金[111]取向在1100 ℃、137 MPa蠕变实验初期(<10 h)即发生所谓的“拓扑反转”现象。如图5b中插图所示,热处理后呈网状连续的γ-Ni基固溶体相被分割成“孤岛”,γ'-Ni3Al相成为连续的基体相。透射电镜观察到有<110>位错对切入γ'-Ni3Al相,此组织结构一直保持到蠕变断裂。该组织结构演变特征难以用镍基单晶高温合金的机理解释,尚有待于进一步研究。
2.2 Ni3Al基合金的应用
近年来,通过添加Hf、Zr、Cr、Mo、Re、B等合金化元素形成的Ni3Al基合金已逐步获得应用。美国橡树岭国家实验室研发的Ni3Al基合金用于在1000 ℃以下使用的民用材料。俄罗斯研发的Ni3Al基合金BKHA-1B用于直升机燃烧室喷嘴和导向叶片、BKHA-2M合金在20~1300 ℃强度和塑性基本达到使用要求,并具有优良的抗氧化和耐磨性。国内研制的铸造多晶Ni3Al基合金具有优异的抗氧化、耐烧蚀性能,已被多型先进航空发动机选为喷口调节片和机匣材料。“十三五”期间将重点进行多晶Ni3Al铸造合金成分与铸造工艺优化,形成制备Ni3Al基合金复杂大型薄壁铸件的成套技术,满足航空发动机发展的需求。采用定向凝固金属间化合物基合金JG4010,突破了大缘板导向叶片整体定向凝固、整体铸造大缘板导向叶片尺寸控制和真空热处理等关键技术,研制的高、低压导向叶片随我国某型发动机验证机在高空台顺利完成了超声速巡航状态实验,达到设计要求;完成了我国某型在研航空发动机高压涡轮导向叶片1650 cyc的专项热疲劳实验、试车考核和装机首飞。
目前,新型低铼Ni3Al基单晶合金IC21被选用为我国某型在研航空发动机的高压涡轮导向单晶叶片用材料,突破了单晶薄壁铸件尺寸和生长取向控制以及叶片热处理等关键技术,现阶段IC21合金已成功研制出单晶叶片。
3 Nb-Si基合金研究进展
3.1 Nb-Si基合金的发展
Nb-Si基高温合金的合金化研究起步于20世纪80年代,采用实验研究、相图计算及热力学模拟,以Nb-Si二元合金为基础,逐步发展到Nb-Si-X (X:Ti、Cr、Al、Hf、Zr、Sn、Mo、W、V、Ta、Fe、Zr、B、稀土元素)和Nb-Ti-Si-Cr-Al-Hf-Zr及Nb-Ti-Si-Cr-Al-Hf-B等多元体系,部分合金化元素对Nb-Si基高温合金相组成和性能的影响如表1所示,为Nb-Si基高温合金的成分优化提供了指导。目前,以实用化为目标的合金体系中,合金化元素高达5种以上,元素交互作用复杂,为加快该合金的研发进度,高通量研究方法开始被用于研究合金化元素对Nb-Si基高温合金组织及性能的影响,如采用高通量方法研究了Ti、Al元素的合金化作用,发现在多元合金体系中加入9.5%的Ti使α-Nb5Si3开始转变为γ-Nb5Si3,当Ti含量为22.6%时,组织中硅化物全部转变为γ-Nb5Si3;当Al含量达到4.5%时,组织中α-Nb5Si3完全转变为γ-Nb5Si3相。高通量研究方法将有助于该类合金的进一步合金化研究。
3.2 Nb-Si基合金的制备研究
Nb-Si基合金的力学性能与其相尺寸、形貌、各相分布等密切相关。研究表明,定向凝固可有效改善合金室温断裂韧性及高温拉伸持久性能。但由于Nb-Si基合金熔点高,定向凝固需在高达2000 ℃的温度下进行,且活泼组元多,成分与组织控制难度较大。因此,需要发展适用于Nb-Si合金的定向凝固技术。Czochralski法(晶体提拉法)、悬浮区熔法(电子束悬浮区熔、激光悬浮区熔和感应悬浮区熔)等制备方法被用于Nb-Si基合金定向凝固制备研究,基本上实现了Nb-Si合金试棒的定向凝固生长。相较于上述无坩埚的悬浮区熔法及水冷铜坩埚内的Czochralski法,有坩埚整体定向凝固技术是将合金棒放入坩埚中,通过电阻加热将试样整体熔化,再将试样拉入装有Ga-In-Sn液态金属的结晶器中。该方法的加热温度可达到2150 ℃以上,温度梯度高,可以获得稳定的定向凝固组织,其最大优点是可以实现工业化的变截面的复杂形状零件如叶片等的定向凝固。但此方法需要坩埚与Nb-Si基合金液在高达2050 ℃的温度下长时间接触,因此要求坩埚耐温能力高,与合金熔体基本不反应,研究发现,添加La2O3+ZrO2的Y2O3陶瓷坩埚基本适合Nb-Si基合金的定向凝固。
图6为Nb-15Si-22Ti-5Cr-3Al-3Hf合金在200 μm/s抽拉速率下有坩埚整体定向凝固的微观组织形貌。组织由沿着试棒轴向排列、并排耦合生长的花瓣状或层片状Nbss/Nb5Si3共晶胞组成。研究表明,采用该技术制备的定向凝固Nb-Si基高温合金的室温断裂韧性及高温拉伸持久性能得到了显着的提高。进一步研究表明,合金的力学性能随抽拉速率的变化与成分也具有关联性,随着抽拉速率从2.5 μm/s提高到100 μm/s,Nb-22Ti-16Si-6Cr-4Hf-3Al合金的共晶胞生长耦合度明显提高,其室温断裂韧性(KQ)也明显提高,可达22 MPa·m1/2。在Nb-29Ti-11Cr-8Si-5Hf-3Al亚共晶合金中,当抽拉速率达到50 μm/s时,共晶胞中的铌硅化物出现不连续生长,共晶耦合度下降,其室温断裂韧性随着抽拉速率提高而下降。
总之,Nb-Si基高温合金室温断裂韧性受到合金成分、定向凝固技术及其抽拉速率等因素的影响。整体来看,有坩埚整体定向凝固技术可明显提高Nb-Si基高合金的室温断裂韧性,而且在1200 ℃、70 MPa下的持久寿命达到108 h。
3.3 Nb-Si基合金抗氧化涂层研究
合金化可在一定程度上改善Nb-Si基合金的抗氧化性能,但难以满足1200 ℃以上应用的要求,必须采用涂层防护。一般而言,传统铝化物涂层和MCrAlY (M:Ni、Co或Ni+Co)包覆涂层的抗氧化防护温度低于1150 ℃;致密的贵金属Ir涂层可实现高温防护,但其成本限制了工程化应用。硅化物(主要为NbSi2和MoSi2)因具有热稳定性好、使用温度高、氧化后形成的SiO2不仅氧渗透率低且其自愈性能优良等特点而被用于Nb-Si基合金的防护涂层,其制备方法多采用多元共渗法。
纯NbSi2和MoSi2涂层在中温区易发生pesting氧化,形成的SiO2氧化膜保护性较差,因此需要对其进行改性。稀土元素Y可细化涂层组织,提高氧化膜的生长速率、致密性以及抑制金属离子外扩散,从而提高涂层的抗氧化性能;Al氧化后形成的Al2O3可与SiO2形成Al2O3·SiO2,能长时间保持完整致密;B和Ge氧化后生成的B2O3和GeO2可以溶入SiO2并降低其黏度,使其在低温下具有较好流动性,能够快速愈合氧化膜中的裂纹和孔洞,从而抑制pesting氧化。活性元素Zr可以促进致密氧化膜的形成并提高涂层的抗氧化性能。例如,采用多元共渗法制备的Si-Al-Y涂层经1250和1350 ℃氧化100 h后试样表面完整致密,氧化膜无脱落,氧化增重分别为2.3和24 mg/cm2 。
此外,高温下MoSi2涂层与Nb-Si基合金的界面稳定性差,涂层中的Si元素向基体扩散会导致涂层退化从而影响其服役寿命,需要在界面处制备阻扩散层。运用电化学沉积法结合包埋渗法可在Nb-Si基合金表面制备MoSi2/ReSi2/NbSi2复合涂层,对于界面互扩散具有一定的抑制作用。
4 结束语
近年来,我国在金属间化合物基高温结构材料的基础研究与工程应用方面取得了重要的进展,以TiAl、Ti3Al、Ti2AlNb、Ni3Al基合金为代表,在性能和工艺方面进步显著,研发出一些具有自主知识产权的新型高温结构材料,为我国高性能航空发动机的研制作出了重要的贡献。Nb-Si基合金在凝固工艺和抗氧化涂层的基础研究方面也取得了显着的进展,逐渐向实用化接近。但金属间化合物固有的共价键和金属键共存的特点导致其室温塑性偏低的问题仍在一定程度上制约其应用。因此,需要进一步开展金属间化合物基高温结构材料强韧化与抗氧化的基础与应用研究,使其固有的优异高温强度与较低密度的优势得到充分发挥,在航空航天等领域发挥出更加重要的作用。
免责声明:本网站所转载的文字、图片与视频资料版权归原创作者所有,如果涉及侵权,请第一时间联系本网删除。
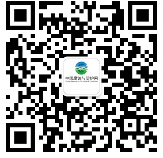
官方微信
《中国腐蚀与防护网电子期刊》征订启事
- 投稿联系:编辑部
- 电话:010-62313558-806
- 邮箱:fsfhzy666@163.com
- 中国腐蚀与防护网官方QQ群:140808414