目前,国内已铺设的石油天然气管道总里程数已达13万公里,其中天然气管道总里程数近8万公里。伴随着油气资源的大规模开发和利用,国内油气输送用钢管制造企业数量在2010年前后大幅增加。而酸性油气、深海油气、页岩气、可燃冰等资源的深度开发也促进了国内油气输送用钢管制造技术能力的提升。
油气输送用钢管制造的基础标准为API Spec 5L《管线管规范》、ISO 3183《石油天然气工业 管线输送系统用钢管》、GB/T 9711《石油天然气工业 管线输送系统用钢管》(该标准等同于ISO 3183)以及DNVOS-F101《海底管线系统》。国外陆上油气输送管制造标准多采用API Spec 5L 或ISO 3183、国内陆上油气输送管制造标准多采用GB/T 9711、海底油气输送管制造标准多采用DNV-OS-F101。另外,一些大型油气公司在输送管基础制造标准的基础上补充了一些技术要求,形成了自己的企业标准。如中国石油天然气集团公司的企业标准《油气输送管道用管材通用技术条件》、壳牌石油公司的DEP标准、道达尔公司的GS标准等。
油气输送过程中泄漏或断裂失效可造成无法估量的损失,尤其天然气管道的泄漏或断裂失效可造成毁灭性的灾难,所以各油气输送用钢管制造标准均要求应用无损检测技术对质量进行把控。从某天然气工程项目直缝焊接钢管制造工艺流程(见下图)中可以看出,无损检测工序数量约占总检测工序数量的70%。同时从工艺流程图中也可看到,在原材料复验、过程检验以及最终检验上均可用超声检测。
图1 某天然气工程项目直缝焊接钢管制造工艺流程
下面将对超声检测技术在油气输送用钢管制造行业的发展及应用现状进行介绍,并对其在行业中的应用前景提出展望。
1 超声检测技术在油气输送 用钢管制造行业的应用发展
油气输送用钢管制造过程属于流水线作业,为了满足生产节拍的需求,检测工序应具备较高的自动化程度,所以在钢管制造过程中的超声检测常采用多通道自动化超声检测系统。多通道自动化超声检测技术是伴随着计算机技术的发展而发展的,在2000年之前其成熟度落后于当时的X射线实时成像技术。因此API Spec 5L第42版(2000年发布)中对埋弧焊钢管焊缝的无损检测仍要求对全长焊缝进行X射线实时成像检测。而随着多通道自动化超声检测技术的进步,标准对于无损检测的要求也进行了相应调整,API Spec 5L从第43版(2004 年发布)到第46版(2018年发布)各版标准中对埋弧焊钢管焊缝的无损检测均优先采用超声检测,全长焊缝X射线检测仅作为协议条款,已不再作为硬性要求。油气输送用钢管有着钢级由低到高、壁厚由小到大的发展趋势,较之射线检测利用超声检测技术检测高钢级、大壁厚钢管更具优势,可见标准对检测方法进行调整具有其合理性。另外,自动化超声检测系统可以做到自动评定、自动记录,从而减少了过程中人的参与,目前这一优势也是射线检测技术所无法比及的,亦可见标准对检测方法进行调整具有合理性。
在很长一段时期内,在多通道自动化超声检测系统的检测设备制造水平方面,国内与国外存在较大差距,而高性能的全套进口多通道自动化超声检测系统动辄上千万,同时还需要高额的使用和维护费用,这些情况导致高性能的多通道自动化超声检测系统在国内油气输送用钢管制造行业得不到广泛配置。出于对行业水平的整体考量,国内油气管线项目虽要求对埋弧焊钢管焊缝进行超声检测,但截至目前仍未舍弃焊缝全长的X 射线检测。
近年来,随着多通道自动化超声检测技术的进步,钢管制造标准对超声检测系统提出了更高的要求,一些技术要求已经突破习惯做法。比如,DEP标准对检测系统的稳定性提出了更高要求,在系统稳定性测试过程中,要求满屏高度80%(±5%)的测试回波信号进行连续8次试验,8次试验测试信号波动不应超过信号幅度均值的25%。通常认为检测系统不漏检即可,如果回波信号波动较大,可适当提高整体增益水平以保证不漏检。但是,回波信号波动较大的检测系统如果按照DEP标准验收,很可能就会归于不合格检测设备。再比如,澳大利亚天然气管道公司APA集团的油气钢管技术规范对自动化超声检测结果的准确性提出了更高的要求,其要求最终检测结果应以自动化超声检测的结果为准,不允许采用手工超声检测对自动化超声检测报警信号进行放行。通常认为自动检测系统如果灵敏度设置偏高一些,可以在一定程度上保证不漏检,但检测过程中部分未超标的缺欠可能会因此发生报警标识。习惯做法是在自动检测之后采用手工检测进行进一步确认,但若按照APA的技术规范,存在被自动检测系统报警标识的钢管将不能被直接验收。
2 超声检测技术在油气输送 用钢管制造行业的应用现状
油气输送用钢管分为焊接钢管和无缝钢管,其中焊接钢管分为直缝埋弧焊钢管、直缝高频焊钢管、螺旋埋弧焊钢管。钢管制造过程中的超声检测采用自动超声检测辅以手工超声检测。其中手工超声检测广泛采用数字便携A型脉冲反射式超声检测仪,目前该类仪器已较为成熟,其性能满足检测要求。而自动化超声检测的应用现状较为复杂,下面从焊接钢管用钢板(或钢卷)的超声检测、焊接钢管焊缝的超声检测、无缝钢管管体的超声检测等3个方面对其应用分别进行介绍。
No.1焊接钢管用钢板(或钢卷)的自动化超声检测
焊接钢管用钢板(或钢卷)超声检测主要用以检测分层缺欠,特殊情况下才用以检测裂纹缺陷。以钢板(或钢卷)作为检测面较为平整,易形成良好的耦合效果,通常情况会优先选择成型前在钢板(或钢卷)上进行均布的平行带扫查(即列线扫查),其常用的检测机构形式如下图所示。
图2 钢板(或钢卷)的超声检测常用检测机构形式
直缝埋弧焊钢管进行管体超声检测将会受到焊缝余高的影响,检测不易实现,通常选择在钢板上进行,如下图所示。
图3 直缝埋弧焊钢管用钢板的自动化超声检测
直缝高频焊钢管的管径较小,在管体上进行超声检测如采用直接接触法,则耦合效果较差;如采用液浸式耦合,检测机构较为复杂,故通常选择在钢卷上进行,如下图所示。
图4 直缝高频焊钢管用钢卷的 自动化超声检测
螺旋缝埋弧焊钢管的管径较大,而且在管体上采用螺旋方式检测可以有效避开焊缝余高的影响,可以在成型和焊接后在管体上进行检测,如下图所示。
图5 螺旋缝埋弧焊钢管的管体 自动化超声检测
标准中对钢板(或钢卷)超声检测扫查覆盖率的要求一般因钢管服役环境不同而不同,海洋服役环境、酸性服役环境以及地质状况复杂的服役环境通常要求较高的扫查覆盖率。另外,钢板(或钢卷)的不同部位的超声检测扫查覆盖率也有所不同,边部以及端部如存在分层,易对质量造成不良影响(这一点笔者在《钢板边部分层对双面埋弧焊钢管的质量影响》一文中曾进行过专题论述,见《理化检验-物理分册》2016年第52卷第3期),通常这些部位的扫查覆盖率要求较高。高扫查覆盖率可以通过多次扫查实现,也可以一次扫查实现。如果一次扫查实现高扫查覆盖率就需要较多数量的检测通道,比如一款国产新型的钢板电磁超声检测系统配有800个检测通道,可以同时检测分层、裂纹以及进行厚度测量,如下图所示。
图6 800通道钢板电磁超声自动化 检测系统
虽然钢板(或钢卷)自动化超声检测机构较为庞大,但实际结构较为简单,因此国内油气输送用钢管制造企业对该设备的配置较复杂,其中有进口设备、国产设备,也有自制设备。这也导致行业内设备性能参差不齐,高性能的设备系统稳定、检测盲区小、检测效率高、可以实现缺欠自动评定,而性能较低的设备则无法做到这些。
No.2 焊接钢管焊缝的自动化超声检测
焊接钢管焊缝的自动化超声检测按照耦合方式可以分为水膜法和射流法两种,如下图所示。
图7 水膜法和射流法耦合示意
射流法检测的优点较多,但对耦合水的控制要求较高、声束入射角的控制要求较高、耦合状态自监控较难实现,目前行业内仍以水膜法检测为主。直缝埋弧焊钢管焊缝自动化超声检测系统和螺旋缝埋弧焊钢管焊缝自动化超声检测系统如下图所示。
图8 直缝埋弧焊钢管焊缝的自动化超声检测
(a)探头机架的结构
(b)检测系统实物
图9 螺旋缝埋弧焊钢管焊缝的自动化 超声检测
焊接钢管焊缝的自动化超声检测设备较为复杂,目前行业内多由专业设备厂家制作。近年来国内专业设备厂家也从单纯模拟国外设备发展到能够对检测设备自主研发,设备的整体性能也得到了大幅度提升,进一步拉近了国内外的技术差距。同时,行业对自动化超声检测系统的要求也越来越高,比如焊缝自动跟踪以及横波斜探头耦合监控已成为检测系统的必备功能。另外,超声检测新技术也逐渐步入检测系统,如一款带PAUT功能的自动化超声检测系统在螺旋缝埋弧焊钢管焊缝检测上得以应用(见下图),这将在很大程度上减小机械结构的复杂程度,也进一步提高了检测的可靠性。
图10 螺旋缝埋弧焊钢管焊缝 带有PAUT功能的自动化超声检测
焊接钢管焊缝的自动化超声检测需要科学和严谨的检测工艺作为技术支持,目前在行业内还存在一定程度的不足。比如检测探头的布置,很多人认为能够按照标准要求发现人工缺陷即可,那么仅仅满足标准的要求是否就可以了呢?从下图可以看出,两种探头布置均能够满足标准的灵敏度校验要求(即发现焊缝中心竖通孔以及焊缝边缘人工刻槽),但两种布置的有效声束覆盖状况迥异,按图11(b)布置将会导致严重的漏检。
(a)一种检测探头布置
(b)另一种检测探头布置
图11 自动化超声检测探头的两种不同 布置方式
No.3 无缝钢管管体的自动化超声检测
油气输送用无缝钢管管体自动化超声检测多采用局部液浸形式。探头与钢管之间的运动形式有两种,一种是钢管原地旋转加探头直线运动,另一种是钢管直线运动加探头高速旋转,见下图。
图12 钢管原地旋转加探头直线运动的无缝钢管管体自动化超声检测
图13 钢管直线运动加探头高速旋转的无缝钢管管体自动化超声检测(结合以无线通讯技术)
无缝钢管如用于海洋服役环境、酸性服役环境或地质状况复杂的服役环境,对其质量要求就较高。通常要求检测纵向缺欠和分层缺欠,同时还有壁厚测量的要求,特殊情况下还会有横向缺欠的检测要求。
无缝钢管管体自动化超声检测的机构较为简单,检测效果较好,目前应用较为成熟。随着无线通讯的发展,结合以无线通讯技术的无缝钢管管体自动化超声检测系统已得以应用(见图13)。该检测系统以数字信号替代了模拟信号,既提高了信噪比,也解决了模拟信号耦合困难的问题。
超声检测技术在油气输送用钢管制造行业的应用前景展望
随着科技的高速发展,超声检测技术本身将会向着超声成像的方向发展,检测系统中辅助技术将会变革升级,这些将使得超声检测系统不断更新迭代。
自动化超声检测系统也将向着智能化超声检测系统发展。首先是超声检测技术本身的智能化,工艺的选择、制定和执行等工作将不再过多地依赖于人。另外,超声检测技术将与其他检测技术之间、与制造工序之间建立良好的智能互联互通。
超声检测技术在油气输送用钢管制造行业的应用将随着工业体系的进步而进步,先进的超声检测技术也将为国家能源事业提供更加有力的保障。
免责声明:本网站所转载的文字、图片与视频资料版权归原创作者所有,如果涉及侵权,请第一时间联系本网删除。
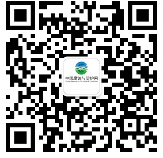
官方微信
《中国腐蚀与防护网电子期刊》征订启事
- 投稿联系:编辑部
- 电话:010-62316606-806
- 邮箱:fsfhzy666@163.com
- 中国腐蚀与防护网官方QQ群:140808414