海洋及近海区的大气中多存在腐蚀性气流,加上昼夜温差大,湿度又高,这些因素对钢结构,特别是承重钢结构桥梁的影响是致命的,轻则影响桥梁的外观,重则造成桥梁损毁,因此必须对此环境下服役的钢结构桥梁采取相应的涂装措施。
位于浙江杭州湾新区(该地区为典型的海洋大气环境,腐蚀环境类别为C5-M)的某大桥为三跨连续钢桁梁桥,长227.7 m,宽41.5 m,其桥型总体布置立面图如图1所示。横断面采用两片主桁布置,主桁中心间距25.8 m。主体结构采用Q345D钢,栓焊结合。
1 防腐涂装体系的选择
根据桥梁所处环境、设计要求和桥梁的结构部位,结合相关理论JT/T 722–2008《公路桥梁钢结构防腐涂装技术条件》及GB 50205–2017《钢结构工程施工质量验收规范》的要求来为主体钢结构选定表1所示的长效型涂装方案,其中耐候性面漆的颜色按全桥景观设计要求来确定。
1.1 内表面(即箱型杆件内部空间)的涂装
考虑到钢结构加工期间焊接及涂装交叉施工等不利因素,参考南京大胜关长江大桥、贵州鸭池河桁架桥的施工经验,上、下弦杆及腹杆等封闭型杆件的内部仅做预处理涂装,取消中间漆和面漆,表面除锈达到GB/T 8923–1988《涂装前钢材表面锈蚀等级和除锈等级》规定的St3级,仅设1道厚度≥60 μm的环氧富锌底漆。
施工完成后用航空密封胶对所有隅角部位以及拼接板的缝隙进行填塞。
1.2 涂层体系的性能特点
(1)醇溶性无机富锌底漆用于打底及调平,其阴极保护作用可使钢材不易发生锈蚀;环氧磷酸锌底漆可满足钢结构临时防锈的要求。
(2)环氧封闭漆能够杜绝空气侵入底漆,同时起到隔离作用,降低底漆与中间漆发生化学反应而导致中间漆起泡的风险;环氧云铁中间漆含云母,起到封闭、保护涂层的作用。
(3)第一道面漆在厂内完成可以节省工地的涂装工作量,保证涂装质量,并能保护中间漆;第二道面漆则是防止第一道面漆在运输、安装过程中出现破损之后的重涂,统一色调。
该体系在15 ~ 25 a内能最大限度地保护钢结构不受有害气体、干湿变化等侵害,具有优异的装饰性能,抗紫外线、防老化(氟碳面漆和聚氨酯面漆的耐人工加速老化时间分别为3 000 h和1 000 h),以及承受构件变形能力强的优点。
1.3 涂装工艺试验
选取涂有车间底漆(醇溶性无机硅酸锌)的试板(厚度为14 mm),漆膜厚度选用上限,即25 μm。施工前,通过试验确认表面处理及喷涂的工艺参数,为后续施工及批量涂装生产提供有效的技术依据。
在满足表面处理要求的情况下,确定并记录空气压力、喷射角度、喷射速率等工艺参数。采用的阶梯试件1、2的规格均为300 mm × 200 mm × 12 mm,评定项目为涂层厚度(采用干膜测厚仪检测),施工方法为高压无气喷涂法及电弧喷铝法,试验结果见表2 ~ 5。
1.4 施工准备
1.4.1 钢材预处理
在钢材预处理流水线上完成钢板和各种型材的预处理,表面除锈达到GB 8923规定的Sa2.5级,Rz 30 ~ 70 μm,并喷涂一道车间底漆以防止钢材在加工过程中锈蚀。
要注意优化钢结构加工,对零件边角部位进行倒角、打磨处理。钢结构加工完成后要进行二次喷砂,清除车间底漆以便于喷涂底漆。
1.4.2 涂装车间设施
涂装厂房按“喷涂合一”配置,执行“一喷一涂”工艺方案,即需要具备保温除湿功能的喷砂车间和涂装车间。
喷砂是为了防止灰尘,清除钢材上的污点及油渍,在光滑的钢材表面做出粗糙度。涂装有手工及机械喷涂。
2 涂装施工
2.1 总体安排
在钢结构件加工场地完成单元节(上、下弦杆,腹杆,桥门架等)的涂装,流程如图2所示,即单节钢桁外表面完成喷砂除锈、电弧喷铝及油漆涂装;杆件内部表面完成喷砂除锈预处理及涂装,喷涂或刷涂耐热环氧富锌底漆,并适当加厚涂膜,对密封区域进行密闭封堵。
桥面板顶面的临时防腐是在厂内喷砂除锈至Sa2.5级后喷涂60 μm厚的环氧磷酸锌底漆。
钢结构各单元节在厂内防腐涂装完后,运到桥址现场拼装成桥,并完成焊缝处理、破损处修补及桥面焊缝涂装。
最后对整桥外表面(含桥面系)总体涂装第二道面漆,以及做好护栏等附属工程。
2.2 表面清理工艺
表面清理包括对表面缺陷进行修补、打磨,以及清除钢板表面的氧化皮、油污、可溶盐等。工艺流程为:焊接缺陷补焊→打磨→用清洗剂清洗油污→吹净→干燥。
为增强漆膜与钢材的力,应对二次除锈后的钢材表面进行清洁处理:先用压缩空气吹净表面的粉粒,再用无油污的干净棉纱或碎布抹净。
2.3 喷漆的技术要求
采用刷涂法及高压无气喷涂法,其中刷涂属手工操作,只在预涂和小面积补涂时采用。表面喷砂处理经检验合格后应保护好清洁的表面,并在4 h内喷涂底漆。
喷底漆前,还应预涂所有焊缝、边角以及所有不易喷涂的部位。所有预涂均采用刷涂。用搅拌机将涂料的各组分搅拌均匀,必要时进行过滤,再按要求进行调配。
底漆与中间漆的最长暴露时间不超过7 d。两道面漆间隔若超过7 d,需用细砂纸打磨拉毛。
2.4 金属喷涂的技术要求
采用十字喷涂法进行电弧喷铝,通过调节施工参数来做到铝层颗粒细小,以降低铝层的孔隙率。摩擦面涂装范围从孔群最外侧螺栓孔壁外延80 mm,要做到摩擦面、喷涂面规整,无波浪边。
2.5 工地涂装
2.5.1 涂层损坏处的修补涂装
最后一道面漆在钢桥合拢后涂装。在此之前应对运输、安装过程中破损的涂层进行修补,先打磨破口,再逐层补涂油漆,从补涂底漆开始,底漆固化后再涂中间漆。
小面积涂层的修补可采用机械除锈,根据涂层配套进行修补,可手涂至设计厚度。
2.5.2 面漆的涂装
涂装最后一道面漆之前,对全桥整体拉毛及修补涂层,确保表面没有油污、灰尘。拉毛后的油漆表面应尽快涂装第二道面漆。
工地连接焊缝经检验合格后,其表面应喷砂除锈至St3。清洁已喷涂涂层表面的污染处,修复损坏的涂层,然后涂装整桥的面漆。
表面清洁的方法与步骤:
(1)可用环氧稀释剂擦洗掉钢结构件外表面较明显的油污;
(2)用洁净的清水高压冲洗表面,除去钢结构件外表面的盐分、灰尘等;
(3)用环氧稀释剂擦试钢结构件外表面一遍,除去表面残留的不易观察到的油污;
(4)待钢结构件外表面环氧稀释剂挥发后用1号砂纸打毛油漆表面,再用抹布擦净表面灰尘。
对于已涂装完毕的节段,应避免涂层损伤,严禁碰撞和擦伤涂层,尽量减少重新电焊等作业。
2.6 焊缝的处理
涂装前清除焊缝表面缺陷、焊渣和污染物,然后进行相应的表面处理,及时进行后续涂装。
在保证焊缝区域底漆厚度的基础上,可适当增加中间层的厚度,一般为原厚度的1.2倍,如一道中间漆厚度可由75 μm最大增至90 μm。
杆件拼装完成后,所有隅角部位和拼接板间的缝隙都必须用弹性腻子填补封闭,干燥后适当打磨,再涂装。
3 经验与教训
3.1 高强螺栓连接处生锈报废
初期由于工期紧张,未及时封堵局部外露的高栓群孔,两处共4块摩擦面的抗滑移系数现场检测小于0.45,使它们全部报废。
这是由于高强螺栓和栓接面在高强螺栓拧完报验合格后未及时进行涂装,结果遭遇下雨,雨水渗进摩擦面留下红色锈水,给摩擦面带来较大的质量隐患。
因此,对于外露积水的高强螺栓,建议用聚硫弹性密封胶封堵拼接板四周缝隙,以防止雨水从丝口处渗入,并在报验合格后12 h以内完成摩擦面涂装。
3.2 外表面涂装中面漆与中间漆之间结合力不良
在部分钢桁外表面涂装施工中,出现聚氨酯面漆与环氧云铁中间漆之间结合力不良,致面漆脱落的质量事故。
通过分析结合力与环境因素(包括稀释剂、昼夜温差和通风)之间的关系,认为如果涂装通用的环氧云铁中间漆的目标膜厚为150 μm,实际所需要的换气量在封闭的厂房内很难达到。
因此改进了车间的通风条件以加速溶剂释放,从而避免涂膜内溶剂残留。
另外,采用快干型环氧中间漆,并在环境温度较低的时间段施工来保证中间漆的干燥速率。经复检,该问题得到很好的解决。
3.3 氟碳面漆局部出现针孔
1月份在进行部分钢结构单元节的氟碳面漆施工时,由于气温骤降,涂料施工性能与环境不匹配,且中间漆干膜表面吸附了小分子水,致使面漆有密集针孔、鱼眼和流挂缺陷。
根据现场情况,通过调整喷涂工序及进行局部面漆试验,发现喷涂速率为1.2 m/s或0.2 m2/s,搭幅为33%时,所得漆膜平整,无异常,针孔问题也未再发生。
4 现场施工的要点
(1)在低温高湿的条件下,常规环氧中间漆受封闭环境的影响,涂膜内部的稀释剂挥发缓慢甚至不挥发,氟碳面漆又较致密,以至于中间漆内溶剂滞留,影响层间结合力。此时需要适当延长环氧涂料的干燥时间,干透后方可上面漆。
(2) 由于环氧中间漆具有较好的抗流挂性,因此要根据温度、湿度、喷涂膜厚和喷漆工的技术来控制稀释剂的添加量,一般在5% ~ 20%之间。但在气温低时,按上限加入稀释剂容易造成环氧中间漆干燥缓慢,短时间内再喷涂氟碳面漆会造成底层溶剂滞留,从而导致层间结合力差。因此气温低时要相应减少环氧中间漆中稀释剂的添加量。
(3) 施工现场根据气温和湿度的不同分别采用慢干稀释剂和快干稀释剂。由于工艺上没有严格区分稀释剂的使用温度和湿度,因此部分杆件在中涂时误用了慢干稀释剂,造成施工时间过长,受湿度影响较大,且与面漆间结合力不良。中间漆采用快干产品,涂层反应活性更高,硬度更好,因此要注意选用快干稀释剂,提高涂膜的干燥速率,缩短涂层间的涂装间隔。
(4) 密切关注现场施工动态,加强施工时的记录,认真控制产品搅拌、活化等环节,通过监控温度、湿度等条件,及时测试分段中间漆和面漆的干燥情况,以确定下一道施工与否,控制涂装间隔。如昼夜温差很大,涂膜难以均匀干燥,会造成不同部位的结合力不均。此时应尽可能减少施工,原则上中间漆不用拉毛处理便可涂面漆。
(5) 高压无气喷枪与喷涂表面应保持30 cm左右的距离,而喷枪角度接近90°,距离太远容易雾喷。为防止漆雾影响,可先对下部结构进行预喷。至于高强螺栓涂装,要先做清洁处理,并从多个方向喷涂,才能保证均匀覆盖。
5 结语
本项目的钢结构涂装严格按照涂装技术要求进行,通过控制相关质量及关键工序,成功地完成了防腐涂装工程,涂层的防腐性能及外观效果良好,可供类似工程参考。
免责声明:本网站所转载的文字、图片与视频资料版权归原创作者所有,如果涉及侵权,请第一时间联系本网删除。
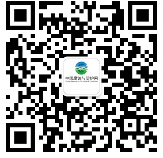
官方微信
《中国腐蚀与防护网电子期刊》征订启事
- 投稿联系:编辑部
- 电话:010-62316606-806
- 邮箱:fsfhzy666@163.com
- 中国腐蚀与防护网官方QQ群:140808414