常压储罐,一般是指钢制立式圆筒形焊接储罐,是国家能源保障、战略储备、商业储备以及石油石化行业生产必不可少的重要储存设备。据统计,至2017年,我国已建成九大国家石油储备基地,原油储备能力达3770万吨/4400万立方米。按照《国家石油储备中长期规划》的要求,到2020年我国的石油储备能力将达到8500万吨/10000万立方米,折合10万立方米储罐1000台。加上商业储备公司、社会仓储公司以及石油石化等行业生产用各类储罐,在役常压储罐数量非常可观。
在役储罐一旦发生破坏,不仅会造成物料损失,还可能引发燃烧、爆炸、中毒等事故。2014年1月,美国自由工业公司一台175立方米的常压储罐发生事故,造成了严重的生命和财产损失。事故的直接原因是,储罐投用后至少10年没有进行过检验和维修,致使罐底板腐蚀穿孔,近40吨4-甲基-1-环己烷甲醇(MCHM)和聚乙二醇醚(PPH)混合物渗流进入储罐周围的碎石和土壤中,最终进入河流和居民的饮用水系统。
因此,加强常压储罐的在役检验具有非常重要的意义,而无损检测技术在其中发挥着至关重要的作用。
1 常压储罐的主要损伤机理和失效模式
常压储罐的设置方式、操作条件和受力状态决定了其损伤机理和失效模式与压力容器不同,标准API 575-2014《常压和低压储罐的检测》指出:腐蚀是钢制储罐及其辅助设备失效、破坏的主要损伤机理,储罐检测的主要目的是查找腐蚀位置,确定腐蚀程度。罐体腐蚀减薄导致的失稳和穿孔渗漏是常压储罐的主要损伤模式。此外,材料劣化、焊缝裂纹、机械接触损伤、疲劳裂纹等也是大型储罐失效的常见原因,储罐的检测方法应针对其失效机理进行选择。
2 无损检测技术的选择及应用
1 目视检测
目视检测,指用人的眼睛对被检件进行检查,是最为古老、用途最为广泛的无损检测方法,必要时也可借用简单的辅助工具,比如检测锤、放大镜、焊缝尺等。从广义上来说,只要用视觉进行的检查都可以称为目视检测。2012年国内以标准的形式将目视检测明确为承压设备行业的一种专业无损检测方法,标准代号为NB/T 47013.7-2012《承压设备无损检测 第7部分:目视检测》。
目视检测同样适用于常压储罐的在役检验,目视检测不但可以发现缺陷,而且在某些方面比采用仪器检测更为直观,例如在结构完整性、罐体腐蚀、变形、泄漏、表面裂纹、罐体保温层、防腐层的损坏等方面。目视检测是宏观检查的主要手段,通过目视检测还可以明确需要做进一步检验的部位或部件及其检验重点。
2 超声波测厚
超声波测厚是厚度测定最常用的方法,是检查设备腐蚀减薄最为直接有效、经济可靠的办法,通过厚度测定可以找出设备相应部位的腐蚀规律,及时发现隐患。对于常压储罐而言,壁板的重点检测区域一般为底板向上1 m的范围,拱顶的检测重点为腐蚀严重部位,浮顶的检测重点为明显腐蚀部位。
为了解决手工测厚需要搭设脚手架的问题,国内外仪器厂商已开发出了多款自动爬壁检测机器人,通过遥控操作,可使机器人到达罐壁任意指定位置,采用水耦合或者空气耦合,不需要对罐壁进行处理,即可进行厚度检测或者超声波A/B/C扫描检测,有的产品检测速度可达10m/min,还可以顺利通过厚度25mm以上的焊缝,从而大大提高检测效率。
超声波测厚方法适用于罐壁板、顶板均匀腐蚀的检测,但一般不宜将其作为主要腐蚀状态为非均匀腐蚀的底板腐蚀的检测手段。由超声波测厚的原理(见图1)可以知道,超声波传感器发出的脉冲穿过被检物体到达材料的分界面时,脉冲被垂直反射回传感器,通过测定超声波在材料中传播的时间即可确定材料的厚度,而罐底板腐蚀形貌主要是溃疡状的坑腐蚀,腐蚀部位上下表面不平行,超声波不能被反射回发出脉冲的传感器,因而很难检测出腐蚀部位的实际厚度。
图1 超声波测厚原理示意
3 底板漏磁检测
漏磁检测是一种高效的无损检测方法,广泛应用于各种铁磁性材料的缺陷检测与评估。20世纪70年代英国天然气公司将该技术应用于在役管道的检验并开展定量分析,漏磁检测技术取得了长足的进展,我国在2007年即推出了JB/T 10765-2007《无损检测金属常压储罐漏磁检测方法》。漏磁检测是目前检测有效性、准确性和检测效率最高的储罐底板腐蚀检测方法。采用漏磁检测仪能够准确地检测出腐蚀位置,水平较高的仪器位置准确度可以达到毫米级。
漏磁检测原理如图2所示。当一个含缺陷的铁磁性工件被施加磁场时,由于铁磁材料的磁导率与缺陷处的不同,磁通在缺陷处发生畸变,一部分磁通(图中第3部分)会逸出工件表面,穿过空气后再回到S极,这一部分就是所谓的漏磁,漏磁场的强度与缺陷的大小和深度成一定的比例关系,用霍尔元件检测到这部分磁通的大小,通过计算即可知晓缺陷的大小和深度。
图2 漏磁检测原理示意
由于漏磁扬的强度与缺陷的大小和深度都有关系,检测结果显示的腐蚀深度为当量深度,而非实际腐蚀深度。因此,漏磁检测结果需要采用超声波直探头或超声波C扫描等方式复查确认。图3为某储罐底板的漏磁检测结果。
图3 某储罐底板漏磁检测结果
漏磁检测的局限性在于只能在开罐状态下实施,必须事先进行清罐处理,不但会产生高额的辅助工作费用而且还会造成停产损失。另外,由于检验条件和仪器自身限制,检测范围不能达到100%,边角部位、盘管覆盖等部位无法覆盖到。为了保证检测覆盖率,需要用小型的手动边角扫查器进行补充检测。
4 底板声发射检测
声发射检测在承压设备检测中的应用已非常成熟,对裂纹类或蠕变类损伤的声发射机理已经比较清楚,在管道和容器的检测和监测中,均有很多实际应用成功案例。对于储罐腐蚀检测,虽尚未完全搞清腐蚀产生声发射的机理,但声发射技术在常压储罐检测上的应用也越来越多,其主要用来探测底板的腐蚀状态或渗漏位置。研究人员常用的做法是,通过安装在罐壁下部的声发射传感器阵列采集腐蚀或泄漏产生的声发射信号,根据检测结果划分综合等级。按照现行标准,可将底板腐蚀状态分为5个等级,如表1所示。
承压设备与常压储罐声发射检测的比对如表2所示。
5 高频导波检测
导波检测是一种以点代面的快速母材超声波检测技术,可以通过一个很小的检测区域对周围一定范围进行100%面积的覆盖检测,检测效率高,检测结果直观,具有一定的检测灵敏度和定位精度,是目前对各种板材或者复合板材比较有效的缺陷检测方法,可以准确地发现板材中毫米级以上的腐蚀坑或线性缺陷。导波检测一般可以与声发射技术相结合,在线检测储罐边缘底板的腐蚀状况,验证声发射检测结果,也可以在开罐状态下,作为漏磁检测的补充。高频导波检测的缺点是衰减快,传播距离短,一般检测范围只有1~2 m。
6 三维激光扫描检测
罐体变形是大型常压储罐主要的失效模式。储罐在服役过程中,受风载、地基沉降、液位静压等因素的影响,罐体可能发生变形、倾斜、沉降等损害,不仅影响储罐的计量精度,严重时会造成卡盘、沉顶、泄漏、破裂等事故,因此对罐体的变形检测和监测非常重要。传统的罐体测量方法主要有围尺法、光学参比线法、光电测距法、全站仪法等,这些检测方法普遍存在测量时间长、工作强度大、检测成本高、结果精度低等缺点。此外,由于油罐所处地形及周围环境复杂、罐体较大、罐间距较小,传统检测方法实施起来也会遇到各种各样的困难。
三维激光扫描技术是近年来出现的新的测量技术,也被称为“实景复制技术”,其利用激光测距的原理,通过记录被测物体表面密集点云的三维坐标、反射率和纹理等信息,可快速复制出被测目标的三维模型及线、面、体等数据,从而获取精准的测量数据和结果。从扫描图上可以直观地看出各部位的变形情况,一般将可接受区域以绿色表示,外凸超标区域以红色表示,内凹超标区域以蓝色表示,并且可以读出指定部位的检测值。图4~7为某常压储罐的扫描检测结果。
图4 罐壁扫描结果
图5 罐底扫描结果
图6 罐体某平面圆度扫描结果
图7 罐体某母线垂直度扫描结果
7 焊缝表面检测
磁粉检测和渗透检测是两大常规表面检测方法。磁粉检测适用于铁磁性材料表面和近表面缺陷的检测,其灵敏度高、检测速度快,能直观地显示缺陷的长度和形状,但难以确定其深度。渗透检测适用于表面开口缺陷的检测,对于钢制储罐而言,其检测有效性、准确性、灵敏度均劣于磁粉检测,而且探伤剂一般都具有毒性,因而常压储罐的表面检测应优选磁粉检测,在不能实施磁粉检测时,可选用渗透检测。
从罐体受力状况分析,立式常压储罐是典型的薄壳结构,壳体在自重和液体静压的共同作用下,承受环向薄膜内力和弯曲内力,按第四强度理论计算,其等效应力最大值位于罐壁下部。根据经验公式,最大应力位置距底板的高度H为:
H=2
式中:R为罐体半径;T为罐体厚度。
对于容积为100000立方米的储罐,H≈2.3m;对于容积为2000立方米的储罐,H≈0.8m;可见储罐最大应力的位置一般位于第一层壁板或第二层壁板靠近一、二层壁板间环焊缝的位置,对于底板而言,中幅板主要受液体的静压作用,应力值很小,而边缘板由于受到向外扩张的壁板的作用,承受很大的径向弯曲应力,边缘部位受力较大,向里则迅速衰减。表面裂纹的产生主要与承受的应力大小有关,因而应对第一、二层壁板间的丁字缝、第一层壁板纵焊缝、大角焊缝、边缘底板对接焊缝、接管与壁板连接的角焊缝以及宏观检查发现有渗漏痕迹的部位实施表面检测。
8 焊缝内部检测
射线检测和超声检测是应用最广泛的焊缝内部缺陷检测方法, 超声波衍射时差法(TOFD)技术也可用于焊缝内部缺陷的检测。对于常压储罐而言,射线检测体积型缺陷的检出率很高,缺陷定量准确,有胶片作为检测记录;而超声检测面积型缺陷的检出率较高,检测成本低、速度快,对缺陷在工件厚度方向上的定位较准确,但没有直观的缺陷记录;TOFD适用于板厚12mm以上的板材,检测效率高,可靠性好,定量精度高,能全程记录信号,长久保存数据。
焊缝内部缺陷一般都是在建造施工过程中产生的,诸如夹渣、气孔、未熔合、未焊透等。由于常压储罐在运行过程中的受力状态较为简单,应力较小,焊缝中原始制造缺陷扩张的可能性较低,焊缝中即使保留某些超标缺陷也不会导致焊缝开裂或罐体失效。笔者在检验实践中曾多次遇到过壁板焊缝,甚至整圈焊缝存在发现大面积超标缺陷的情况,参照GB/T 19624-2019《在用含缺陷压力容器安全评定》进行评定后,发现这些缺陷的存在不影响储罐的安全运行。因而一般情况下,不必进行焊缝埋藏缺陷的检测。
3 无损检测技术综合比较
目视检测
适用缺陷:腐蚀、变形、泄漏、开裂
主要优点:简单、直观、经济
主要局限性:检测环境和主观因素对检测结果影响较大
超声波测厚
适用缺陷:罐体腐蚀
主要优点:快速、方便、经济
主要局限性:不适用于非均匀腐蚀检测
漏磁检测
适用缺陷:底板腐蚀
主要优点:定位定量准确、检测有效性高、准确性高
主要局限性:辅助费用高
声发射检测
适用缺陷:底板腐蚀/渗漏
主要优点:快速、经济、全覆盖
主要局限性:不能定量,检测结果受环境影响较大
导波检测
适用缺陷:罐体腐蚀
主要优点:快速、准确,可在线检测
主要局限性:衰减过快,覆盖范围小
3D扫描
适用缺陷:罐体变形/沉降
主要优点:快速、准确、直观
主要局限性:精度低于全站仪
磁粉检测
适用缺陷:表面/近表面缺陷
主要优点:灵敏度高、微小缺陷检出率高
主要局限性:仅适用于铁磁性材料
渗透检测
适用缺陷:表面开口缺陷
主要优点:结果直观
主要局限性:仅适用于开口缺陷
超声检测
适用缺陷:内部缺陷
主要优点:面积型缺陷检出率高、高度方向定量准确
主要局限性:没有直观记录
射线检测
适用缺陷:内部缺陷
主要优点:体积型缺陷检出率高、有直观的胶片记录
主要局限性:检测成本高,厚度方向位置、尺寸确定困难
TOFD检测
适用缺陷:内部缺陷
主要优点:定量精度高、可靠性好
主要局限性:适用于12mm以上板材,工件表面存在盲区
结 论
无损检测技术在常压储罐在役检验中应用非常广泛,不同检测方法有其不同的应用范围,储罐检测的重点是腐蚀检测。开罐检验中应首选漏磁检测;在线检验中应首选声发射和超声导波检测;表面检测和3D扫描检测也是常用的检测方法。随着储罐的大型化、复杂化、高参数化,对新的无损检测技术的需求也会日益增长, 希望能有更加智能化、自动化的无损检测仪器应用于常压储罐的在役检验中。
免责声明:本网站所转载的文字、图片与视频资料版权归原创作者所有,如果涉及侵权,请第一时间联系本网删除。
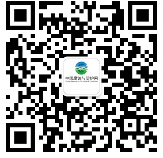
官方微信
《中国腐蚀与防护网电子期刊》征订启事
- 投稿联系:编辑部
- 电话:010-62316606-806
- 邮箱:fsfhzy666@163.com
- 中国腐蚀与防护网官方QQ群:140808414