摘要
对AZ31B镁合金进行超声滚压表面处理,利用电化学测试手段评价了改性后合金的耐蚀性能,通过SEM和白光干涉仪观察分析了合金处理层微观组织、表面形貌以及腐蚀后表面形貌。结果表明,经过表面处理后,镁合金表层晶粒发生明显细化且表面平整,表面腐蚀产物分布均匀且致密性高,去除腐蚀产物后表面点蚀坑细小密集。在浸泡前期,经表面处理试样的钝化膜层电阻Rf为9020 Ω,远大于未经表面处理试样的14.8 Ω。在浸泡中期,未经表面处理试样的阻抗谱图上出现扩散过程引起的阻抗特征,此时钝化膜层电阻Rf为22.9 Ω,远远小于经表面处理试样的19800 Ω。在浸泡后期,表面处理试样钝化膜层电阻Rf为31400 Ω,而未经表面处理试样的为11400 Ω。超声表面滚压处理降低了镁合金表面粗糙度及晶粒尺寸,进而增加了镁合金在溶液中钝化膜的均匀性和致密性,阻滞了镁合金表面的电化学反应过程,延缓了镁合金的腐蚀。
关键词: 镁合金; 超声滚压; 阻抗谱; 表面形貌; 电化学; 腐蚀机理
近年来,随着人口老龄化的增长,老年人数量迅速增长,因骨质疏松所导致的骨折数量大幅度增加[1]。许多外部治疗对骨折来说过于复杂,必须通过内部植入物固定。目前,常用的永久性承力骨骼植入物如不锈钢、Ti和钴铬合金存在力学性能不相容[2]、释放有毒金属离子[3]、不可自行降解等缺点。相比之下,Mg及其合金的力学性能如Young's弹性模量 (E=41~45 GPa) 与人骨的力学性能相似 (E=15~25 GPa),减少了应力遮挡效应。此外,Mg2+是人体中常见的代谢物,镁合金在人体内降解所产生的镁离子会促进骨细胞再生,因此镁合金具备良好的生物相容性[4]。然而过快的腐蚀速率使得镁合金作为骨植入材料在生物体内存在时间较短,难以满足骨骼生长对力学性能的要求。因此,提高镁合金耐蚀性有着十分重要的意义[5-10]。
表面处理能够在很大程度上影响镁合金的耐蚀性[11,12]。Denkena等[13]研究滚球抛光加工对镁钙合金在0.9% (质量分数) NaCl溶液中腐蚀行为的影响,通过抛光工艺使得在镁钙合金次表层产生高残余压应力,从而使腐蚀速率降低了约100倍。Salahshoor等[14]研究了抛光处理对生物医用钙镁合金在模拟体液中腐蚀行为的影响,认为经过抛光的镁合金表面展示出更加均匀的腐蚀以及更少的腐蚀产物。刘蒙恩等[15]研究了高能喷丸对AZ31镁合金在5% (质量分数) NaCl溶液中耐蚀性的影响,结果表明,经喷丸处理的表面形成厚度约150 μm的塑性变形区,极大地细化了表层晶粒,但是由于在喷丸过程中表面形成了大量的裂纹,使得腐蚀接触面增大,导致喷丸试样的腐蚀速率明显高于未喷丸试样的。超声表面滚压强化技术是在喷丸与抛光的基础上发展的一种金属表面改性方法[16]。相比较传统的滚压和喷丸处理,超声表面滚压处理 (USRP) 能够实现表面冲击和光整同时进行,近年来已经在疲劳延寿、表面改性等热门研究领域得到广泛关注和应用[17-20]。
综上所述,表面处理能够提高镁合金的耐蚀性,目前,应用超声滚压表面处理技术在提高40Cr钢和铝合金耐蚀性方面研究甚多[21-24],但是采用超声滚压表面处理技术来提高镁合金腐蚀性能的相关研究鲜有报道。因此,本文以医用镁合金AZ31B作为实验材料,首先采用USRP对镁合金表面进行改性处理,然后对改性前后镁合金的电化学腐蚀行为进行研究,最后通过对改性前后镁合金腐蚀形貌观察,分析超声表面滚压对镁合金腐蚀性能的影响机理,从而为选取合适的超声滚压工艺参数来提高镁合金在人体生理环境下的耐蚀性奠定基础。
1 实验方法
本实验所用材料为商用挤压态AZ31B镁合金棒料,直径D为30 mm,化学成分 (质量分数,%) 为:Zn 0.52,Al 2.96,Si 0.16,Cu 0.006,Mn 0.31,Fe 0.003,Ni 0.001,Mg余量。
1.1 实验步骤
使用数控车床对毛坯件外圆进行粗加工处理,然后使用超声表面滚压设备对预处理工件外圆进行超声表面滚压处理,滚压进给量为0.01 mm/r,主轴转速为600 r/min,静压力为30 N,振幅为10 μm,滚压长度为10 mm。超声表面滚压加工简图如图1所示。将未经和经过超声滚压处理试样均切割成如图2和3所示大小,分别用于表面形貌观察和腐蚀性能测试,以及金相组织观察。电化学测试时,所有试样除测试面外,其余面使用环氧树脂密封。将未经超声滚压处理的试样记为试样1,经超声滚压处理的试样记为试样2,贴标签密封保存备用。
图1 超声表面滚压加工示意图
图2 用于形貌观察和腐蚀性能测试的试样
1.2 表面形貌及微观组织表征
使用白光干涉ZeGage? Plus光学轮廓仪对试样1及试样2表面3D形貌沿轴向取样420 μm进行测量。
利用光学显微镜 (OM) 和场发射扫描电子显微镜 (FE-SEM,Quanta 600FEG) 观察试样1和2沿截面方向的微观结构。试样的预处理为:(1) 使用800#水磨砂纸沿一方向将取样时的切痕磨掉,然后依次使用1000#,2000#,3000#和5000#水磨砂纸打磨表面;(2) 使用金相抛光机去除5000#砂纸所带来的划痕,抛光布使用植绒布,使用W2.5金刚石抛光膏抛光至镜面;(3) 最后使用金相浸蚀液腐蚀25 s,清水冲洗后酒精清洗,冷风吹干。浸蚀液成分为:10 mL硝酸+30 mL乙酸+40 mL蒸馏水+120 mL无水乙醇。
图3 用于微观组织观察的试样
1.3 腐蚀性能测试与腐蚀形貌表征
实验介质为PBS磷酸盐缓冲液,由1.15 g/L Na2HPO4,0.2 g/L KH2PO4,8 g/L NaCl和0.2 g/L KCl组成。电化学实验在Zennium X化学工作站上进行。辅助电极为10 mm×10 mm×0.1 mm的铂片电极,参比电极为R232饱和甘汞电极,工作电极为镁合金试样。
腐蚀电化学性能测试时,试样在浸蚀液中浸泡3,24,48,96,144和360 h后进行腐蚀电化学测试,并使用恒温水浴锅将温度设置为37 ℃来模拟人体体温,每24 h更新55%的溶液来模拟人体体液更新[25]。在自腐蚀电位下进行阻抗测试,测试频率范围为105~10-2 Hz,正弦扰动电压为10 mV。低频 (小于66 Hz) 每十位区间取5个点,每个取样点测试5次;高频 (大于66 Hz) 每十位区间取10个点,每个取样点测试10次。所有的电化学测试均在室温下进行。
使用SEM观察浸泡360 h后的镁合金试样表面腐蚀形貌和去除腐蚀产物后的表面形貌,其中,表面腐蚀形貌观察之前使用无水乙醇进行超声清洗;观察去除腐蚀产物后的表面形貌之前将试样放入铬酸溶液 (200 g/L CrO3+10 g/L AgNO3) 中浸泡5 min以去除试样表面所覆盖的腐蚀产物,腐蚀产物去除后立即使用无水乙醇进行超声清洗15 min,冷风吹干。
2 实验结果
2.1 加工表面形貌
图4a~c分别为AZ31B镁合金在车削和USRP加工后的表面三维形貌及轮廓曲线。表面轮廓曲线测试位置位于三维形貌图中虚线AB处。从图4a和c可以看出,车削后试样表面上沿切削方向存在呈近似周期性凹凸分布,轮廓波峰与波谷处尖锐过渡,其中最低谷与最高峰的最大高度差Sz为6.107 μm,均方根Sq为1.008 μm。而从图4b和c可以看出,USRP处理对车削表面起到削峰填谷的作用,车削表面走刀痕迹被消除,表面轮廓曲线更加平缓,最大峰值与最大谷值之间的距离显著降低,其中Sz为2.953 μm,Sq为0.219 μm。试样1的轮廓算术平均高度Sa为802 nm,而试样2的Sa为158 nm,仅为试样1的1/5。
图4 镁合金AZ31B在车削和USRP加工后的表面三维形貌及表面轮廓
2.2 晶粒尺寸分布
图5a为试样1的显微组织,镁合金母材由大小不均的等轴晶组成,表层晶粒大小和基体晶粒大小几乎看不出差别。而对于经USRP处理后的镁合金变形层试样2 (图5b),显然由于高频超声滚压的影响,材料表层的显微组织尺寸显著减小,晶粒压扁拉长,晶粒内部存在大量孪晶,晶界增多且更致密,与基体存在显著区别。
图5 滚压前后镁合金试样的微观组织形貌
2.3 电化学阻抗谱测试结果
为获得两种AZ31B镁合金试样在浸泡不同时间后的阻抗特性,进行了电化学阻抗谱测试,测得的Nyquist图如图6a和b所示。从图6a可以看出,在浸泡2,24,48,144,240及360 h后,高频区和低频区各有一个容抗弧,且随着时间的推移,高频弧径逐渐减小,而低频弧径出现增加-减少-增加的交替变化,且在240 h时达到最大。而当浸泡时间为96 h时,试样1的Nyquist图上除高频和中频的两个容抗弧之外,低频还出现了Warburg阻抗。从图6b可以看出,试样2的阻抗谱图在所有的浸泡时间下均出现两个容抗弧,且随着时间的推移,高频弧径逐渐减小,而低频弧径同样出现增加-减少-增加的交替变化,且在360 h时达到最大。可以看出,在经过360 h的浸泡之后,试样2的弧径远大于试样1的。
图6 两种镁合金试样在37 ℃浸泡不同时间后的Nyquist图
2.4 腐蚀表面形貌
经过360 h浸泡之后,试样1和2表面腐蚀形貌分别如图7a和b所示。可以清晰看到,试样1的腐蚀产物均匀性差,随处可见较大的孔洞存在。相比之下,试样2的腐蚀产物较均匀致密,且未见到较大孔洞的存在,表面被花瓣状的腐蚀产物完全覆盖。清除腐蚀产物后的表面形貌如图8a和b所示。可以看出两者的表面均以点蚀为主,其中试样1表面存在着大小不一的点蚀坑,体积相差甚大,点蚀坑沿纵向发展。而试样2中点蚀坑细小密集,且沿横向发展。
图7 两种试样在PBS中浸泡360 h后的表面腐蚀形貌
图8 两种试样在PBS中浸泡360 h并去除腐蚀产物后的表面腐蚀形貌
3 讨论
3.1 阻抗行为
Nyquist图上高频容抗弧一般体现电荷转移过程所引起的溶液与电极表面的阻抗特性,而低频容抗弧体现电极表面多孔膜层的阻抗特性[26,27]。在PBS溶液中浸泡2 h后,从图9a可以看出试样1和试样2在高频和低频各有一个容抗弧;从图9b中可以看出在高频段,试样2的阻抗值略大于试样1的,而在低频区,试样2的阻抗值远大于试样1的,这表明此时试样2表面膜层对基体的保护作用远远大于试样1的。这主要是因为在浸泡初期,试样1表面凹凸不平,致使表面存在不连续的多孔钝化膜,在没有钝化膜覆盖的镁合金表面与溶液直接接触;而对于试样2来说,由于表面粗糙度低且晶粒细化,致使表面快速的形成连续且均匀致密的钝化膜[28],使得带电粒子穿越钝化膜的阻抗远远大于试样1的。在没有钝化膜覆盖的镁合金表面和溶液界面有双电层的存在,其性质可由一个电阻和一个电容并联来表征。考虑到电极表面的实际物理特征,钝化膜电阻应与双电层串联成一个单元后再与氧化膜电容并联[29],见图10a所示的溶解模型,其等效电路如图10c所示。而对于试样2来说,由于表面均匀且晶粒细化,致使表面快速且完全的形成致密的钝化膜[30],因此溶液中的阴离子几乎均匀地穿越钝化膜来到达镁合金基体表面,其溶解模型可由图10b来表示,其性质可由钝化膜层的阻抗和溶液与镁合金表面之间的阻抗串联来表征,见图10d所示的等效电路。其中,Rs代表溶液电阻,Rct表示镁合金阳极和PBS溶液之间界面的电荷转移电阻,Rf表示镁合金阳极表面所覆盖的多孔钝化膜层电阻,Qdl表示镁合金阳极和电解液之间的双电层电容,Qf表示镁合金阳极表面多孔钝化膜与溶液之间的双电层电容。由等效电路所得拟合曲线如图11实线所示,其中各元器件值列于表1中。可知,在浸泡2 h之后,试样1的Rf为14.8 Ω;而试样2的Rf为9020 Ω,远远大于试样1的。
图9 浸泡2 h后试样1和试样2的Bode图
图10 滚压前后镁合金试样在PBS溶液中的溶解模型及等效电路
图11 浸泡24,48,和96 h后两种镁合金试样的Bode图
表1 两种镁合金试样浸泡不同时间后的阻抗拟合结果
在浸泡中期,如图11所示,试样2仍出现两个容抗弧,分别位于低频和高频区,这表明试样2的溶解模型并没有发生改变,改变的仅仅是元器件值,所以其等效电路可由图10d表示。相反,在浸泡96 h后,从图11e和f可以看出,此时在试样1的Nyquist图中 (图6a) ,紧接着中高频的容抗弧后,在低频出现倾斜角约为π/4的Warburg扩散阻抗直线[27];从图11e可以看出,此时试样1出现了3个时间常数,分别是代表着电荷传递过程的高频弧、表示膜层阻抗的中频弧以及表示扩散所引起的低频弧径。从图11f可以看出,试样1的中频段阻抗值远远小于试样2的。这是由于溶液中的攻击性离子破坏了表面钝化膜薄弱位置,造成钝化膜破裂,基体直接与溶液接触,使得反应离子可顺利通过宏观孔到达膜层/基体金属界面,从而在电极表面附近引起浓度差,相对于电迁移来说,扩散起到了主导作用,因此阻抗谱上出现Warburg阻抗。此时等效电路可由图12来进行表征[27],其中,ZW表示电极表面由扩散所引起的阻抗值,各元器件值如表1中所列。可以明显看到,在浸泡96 h之后,试样1的膜层电阻仅为22.9 Ω,而由电迁移所引起的电荷转移电阻却高达5440 Ω,这说明此时电迁移过程受到极大抑制。
图12 浸泡96 h后试样1的等效电路
在浸泡后期,从图13可以看到,试样1和试样2均存在两个容抗弧,分别位于低频和高频。试样1的Warburg扩散阻抗消失是由于钝化膜的自我修复功能,使得局部破坏位置自行修复,重新对基体提供保护。从表1可以明显看到,经过360 h的浸泡之后,试样2表面膜层电阻达到了31400 Ω,而试样1的表面膜层电阻仅为11400 Ω。同时,从图7和8的表面腐蚀形貌可以看出,试样1的表面钝化膜呈不均匀性,局部呈多孔特征;而试样2表面腐蚀形貌则呈均匀分布特征。
图13 浸泡144,240,和360 h后两种镁合金试样的Bode图
3.2 腐蚀机理
USRP处理显著降低了镁合金表面粗糙度,溶液与合金的接触面积减小,因此降低了局部腐蚀的几率。由于USRP处理后晶界增多且均匀分布,从而导致镁基体与晶界处的第二相形成大量微小电偶腐蚀,从而加速了钝化膜的均匀生长。
由于超声滚压使得镁合金表层发生严重压缩变形,变形层存在较大残余压应力,缩短了原子之间的距离,在单位体积内的原子数增多,从而使钝化膜易于形成且更加致密[31],最终导致溶液中的攻击性离子 (Cl-) 穿过膜层的阻力增大,从而在后期的腐蚀过程中钝化膜不会破裂而暴露基体。进而腐蚀后的表面点蚀体积小且分布更加均匀,使得膜层与基体的界面缓慢且平滑的移动,因此其界面移动模型可由图14a来表示。相反,晶粒粗大,表面粗糙的未处理试样会导致在溶液中所形成的钝化膜致密性差且不均匀,使得溶液中大量攻击离子进入膜层孔隙中[32],造成电极表面附近反应物浓度与PBS溶液本体浓度存在明显差别,因此就会出现反应物从溶液本体向电极表面的扩散过程,从而使得此处电极表面的孔蚀坑不断的沿纵向发展,其界面移动模型可由图14b来表示。
图14 镁合金试样1和2在PBS溶液中的界面移动模型
4 结论
(1) 经USRP冲击与光整加工后,镁合金表面粗糙度明显降低,加工表面形貌更加均匀,表层晶粒压扁拉长,晶粒细化。
(2) 经USRP工艺处理后,AZ31B镁合金耐蚀性显著提高。其钝化膜层阻抗值随时间变化幅度小且远远大于未经USRP处理试样的膜层阻抗值;腐蚀表面产物分布均匀且致密,去除腐蚀产物表面点蚀细小密集且分布均匀。
(3) 镁合金耐蚀性改善的主要原因是USRP处理后晶粒细化、晶界增多,显著提高镁合金钝化膜层的致密性及均匀性。此外,表面粗糙度降低,极大降低了浸泡样品与溶液的接触面积,从而导致合金耐蚀性的提高。
免责声明:本网站所转载的文字、图片与视频资料版权归原创作者所有,如果涉及侵权,请第一时间联系本网删除。
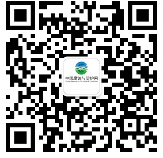
官方微信
《中国腐蚀与防护网电子期刊》征订启事
- 投稿联系:编辑部
- 电话:010-62316606-806
- 邮箱:fsfhzy666@163.com
- 中国腐蚀与防护网官方QQ群:140808414