进行涂层设计时,首先要了解工件服役情况和工件表面应具备的性能,准确判定易引发工件失效的原因,例如工件工作的介质、温度、受力的性质和大小、工件的材质、组织、尺寸等,从而确定对涂层的要求,包括结合强度、硬度、厚度、孔隙的多少及大小、表面精度、耐磨、耐腐蚀、耐热或其他性能。
耐腐蚀涂层材料的选择比较复杂。零件的工作状态、工作温度、工作环境和各种腐蚀介质都增加了对涂层材料的要求。腐蚀环境可能是水溶液、气体或各种化学介质,还可能具有宽广的温度范围。在有燃气存在的条件下,燃烧的气体或未燃烧的燃料也可能在适当的温度下与其它物质发生反应,形成很复杂的腐蚀环境。
01
耐腐蚀涂层材料的选择
耐大气腐蚀
这类涂层耐下述条件的腐蚀:金属或合金暴露在户外或室内的大气中,涂层在大气中能抵抗风、雨、阳光和其他气候变化条件的腐蚀。在户外使用的涂层在室内也能很好地使用。这类涂层包括耐工业气氛的涂层、耐海洋气氛腐蚀的涂层和耐农村大气腐蚀的涂层。
耐工业大气腐蚀的涂层
耐工业大气腐蚀的涂层能承受具有烟尘或化学烟雾(如大城市和重工业区等)的恶劣气氛,可喷涂Al、Zn涂层。这类涂层必须进行封孔处理,封孔剂的选择非常重要。
这类涂层常用于所有类型的结构和构件钢、电的导线管、桥梁、输电线、金属构件、草坪和庭院设施等。
耐海洋气氛腐蚀的涂层
这种涂层能承受海洋附近或具有盐雾条件下的腐蚀。常用于桥梁-高于水线、船坞结构-高于水线、贮藏容器外壁、船的上层结构、栈桥、变压器表面等。
耐农村大气腐蚀的涂层
农村大气中虽然没有工业烟雾和海洋性气候的盐雾,但含有少许的污染物。
耐浸渍腐蚀
浸渍腐蚀是金属或其涂层暴露在液体中,并且是全部或部分、或二者交替地受到浸渍,防腐蚀涂层必须能够耐液面以上或液面以下环境的腐蚀。这类涂层有如下几种:耐食用淡水的涂层、耐非饮用淡水的涂层、耐热淡水的涂层、耐盐水腐蚀的涂层、化学和食品工业使用的涂层。
耐饮用淡水涂层
这种涂层耐淡水,并且不能改变水的化学成分。为了适合可饮用水的要求,不能使用含铬酸盐的密封剂。常喷涂Zn涂层。常用于淡水贮器;高架渠(高架水道、输水道、导水管)、过滤机水槽、水输送管等。
耐非饮用淡水涂层
这种涂层耐非饮用淡水,水温不超过52℃,pH值为5~10。常喷涂Al、Zn涂层。常用于发电厂引入线、浸渍在淡水中的结构装置、航行在淡水中的船身等。
耐热淡水涂层
这种水系非饮用水,水温在52~204℃,pH值为5~10,可喷涂Al涂层,但要封孔。常用于交换器、热水贮藏容器、蒸汽净化设备、暴露于蒸汽的零件。
耐盐水涂层
这种涂层可以全部或部分浸在静止的或运动的食盐水或海水中。对静止状态的结构,海水浸没的范围应从泥线之下一直延伸到潮线之上0.914米的部位;高出这一范围,应作为“盐类大气”考虑。常喷涂Al涂层。常用于船用发动机的集油盘、钢体河桩和桥墩、船体、鱼舵和鱼箱、在船体水线之下存有污垢问题的部位等。
化学和食品工业使用的涂层
这种涂层能耐诸如油、燃料和溶剂等的化学作用,并且能耐各种食品的腐蚀,但不能改变食品的化学成分和味道,可喷涂Al涂层,但要封孔。常用于汽油、原油、燃料油以及二甲苯、乙醇、丁醇、醋酸戊酯和甲苯等药剂的贮藏、啤酒厂的麦芽浆槽、软饮料设备、乳品及制酪业设备、食品油贮槽及糖蜜罐、甘油槽内衬、木屑洗涤机等。
耐化学腐蚀
这类涂层能承受各种酸、碱、盐类的溶液、蒸汽和固体的腐蚀。这类涂层主要是各种铁基、镍基和钴基合金、自熔性合金、有色金属,氧化物陶瓷,碳化铬和碳化钨等金属陶瓷。由于热喷涂层都有一定的孔隙率,所以,各种涂层必须进行填充密封处理。密封剂本身也必须耐化学介质的腐蚀。
为了抗化学腐蚀的需要,在给定环境下采用的所有涂层,必须用推荐的密封剂进行处理。使用专门的密封剂,不会破坏涂层的力学性能。然而,在高温下涂层抗化学腐蚀的能力部分地取决于密封剂。
02
热喷涂涂层的耐腐蚀性能检测
涂层的耐腐蚀性是反映涂层保护基体金属和抵抗环境侵蚀能力的好坏,是直接影响金属构件使用寿命的重要指标。特别是对于防护性涂层及防护-装饰性涂层,对涂层的耐腐蚀性指标有其明确的要求,必须进行严格的检验。
腐蚀试验包括实验室腐蚀试验和现场腐蚀试验两类。实验室腐蚀试验,可分为室温或加热的液态浸渍腐蚀和气体腐蚀(含高温氧化)以及盐雾试验等。现场腐蚀试验也多种多样,如大气腐蚀、海水及淡水浸渍、土壤腐蚀、挂片试验等。按腐蚀介质的性质,又可分为酸性、碱性、中性盐腐蚀等类型。
腐蚀试验条件,需根据试验涂层材料的技术标准或涂层材料的使用条件来拟定。溶液的pH值、溶解气体量、溶解离子浓度、溶液温度与流速等,均会直接影响涂层的腐蚀反应。一般认为,溶液中的溶解气体,特别是中性溶液中的氧含量对腐蚀过程的阴极反应影响很大,而液体温度不仅影响反应速度,而且对反应类型也有一定的影响。
液态浸渍腐蚀试验
对喷涂层进行液态浸渍腐蚀,可带标样(一般为被喷涂的基体材料)同时进行,也可带入已知耐蚀性的其他材料试样,以期进行比较。由于喷涂层多有气孔存在,故应首先进行封孔处理后再做腐蚀试验。液态浸渍腐蚀又分为静态全浸式、部分浸渍式、交互浸渍式、气蚀等流液浸渍等。
静态全浸式
静态全浸式就是将试样完全浸入溶液浸泡的试验方法。此方法操作简便,重现性好,比较容易控制试验因素。国家标准GB 10124-1988《金属材料实验室均匀腐蚀全浸试验方法》中详细规定了试验方法和要求。试验时,不论是常温还是煮沸下的腐蚀试验,均应保持溶液的浓度始终一致。溶液的蒸发损失可采用恒定水平面装置控制或定时地添加溶液,使溶液体积的波动不超过±1%,有时也采用回流冷凝。为避免腐蚀产物积累影响腐蚀规律,一般将介质容量与试样表面积的比例控制在20~200mL/cm3。通常要求每个试验装置中只浸泡一种涂层,以避免一种涂层的腐蚀产物对另一种涂层腐蚀规律的干扰。
利用水浴或油浴控制试验溶液的温度。除非有特别规定,腐蚀试验过程不应对溶液充气。试验容器可密封,也可敞露。在沸点温度下进行的试验,应注意缓慢加热,并在容器底部铺一层玻璃(或陶瓷)碎片,以避免过度沸腾和气泡的冲击作用。试样的支架和容器在试验溶液中应是惰性的,从而保证自身不被腐蚀和破坏,也不污染试验溶液。
部分浸渍式
部分浸渍式是将试样部分浸入溶液,由于气/液相交界的水线长期保持在涂层表面的同一固定位置,从而造成严重的局部腐蚀破坏,部分浸渍试验也称为水线腐蚀试验。在贮存液体的容器内壁及部分浸入海水的涂层构件上,都会发生这种水线破坏。铝涂层和某些其他金属涂层往往在水线处发生浓差腐蚀,部分浸渍试验条件为其提供了非常适宜的加速试验方法。
部分浸渍式试验方法、要求、条件的控制及试验装置与静态全浸式试验基本相同。关键是如何提供合适的试样支撑方法,使水线部位保持在固定的位置上,保证液面上、下的试样面积比恒定不变。采用自动恒定液面装置,可以显著提高试验结果的重现性。
交互浸渍式
交互浸渍试验又称间浸试验,是指将带有金属涂层的试样交替地浸入液态腐蚀介质和暴露在空气中。交互浸渍试验是一种模拟试验,也是一种加速试验。这种交互浸渍状态为水溶液作用提供了加速腐蚀的条件,因为在大部分暴露时间中试样表面可以保持频繁更新,几乎为氧所饱和的溶液薄膜,而且在干湿交替过程中,由于水分蒸发使得溶液中的腐蚀性组分浓缩。另外,试样表面完全干燥常常使腐蚀速度下降,但是腐蚀产物膜破裂则起相反的作用。
交互浸渍试验结果与干湿变化的频率、环境的温度和湿度密切相关,所以必须合理设计干湿变化周期,并在连续试验中保持不变。同样,应合理控制环境温度和湿度,以保证试样在大气暴露期间有恒定的干燥速度。根据不同的试验要求,有时在湿度相当高的密闭装置中进行间浸试验,使试样离开溶液后始终保持湿润状态;有时在空气中暴露时用干燥热风吹拂(或辐照加热),以加速干燥。
交互浸渍试验条件的选择与所用试验装置的工作原理有关。为了实现干湿交替,可以交替地将试样浸入和提出溶液;也可使试样固定不动,而让溶液相对试样升降。通常使试样运动比移动腐蚀介质更容易实现。溶液和空气中的暴露时间比应视试验的具体要求而定,一般为1:1~1:10,一次循环的总时间常为1~60min不等,有时也可达24h。
中性盐雾试验
中性盐雾试验是一种常用的人工加速腐蚀试验,它是模拟沿海大气环境中,温暖的海面向寒冷的空气蒸发和海浪冲击下泼向空间的含氯离子微小液滴,形成细雾状介质对金属的腐蚀条件,采用一定浓度的氯化钠溶液,在加压下以细雾状喷射,由于雾粒均匀地落在试样表面,并不断维持液膜更新,因而对涂层的腐蚀符合大气腐蚀基本原理,实现测定涂层的加速腐蚀作用。
中性盐雾试验毕竟不能完善地模拟大气条件对金属涂层的腐蚀,加之影响腐蚀的因素较多,造成测试条件不易控制等等,往往重现性较差,所以只能作为同一类型涂层在该条件下相对耐蚀性的比较。实践表明,它对阳极性涂层(如钢铁基体上的锌层和镉层等)耐蚀性效果较好,而对阴极性涂层,则只能揭示涂层的孔隙和缺陷程度,间接地反映涂层的抗腐蚀能力。
国家标准GB 6458-1986《金属覆盖层 中性盐雾试验》中规定了中性盐雾试验所使用的设备、试剂和方法。
试样的数量按测试具体规定,一般情况下每批取3件。试验时,试样放置在盐雾试验箱内,试验溶液为5%NaCl(质量分数)溶液,pH值为6.5~7.2,喷雾箱内温度为35±2℃,相对湿度大于95%。试验面朝上,让盐雾自由沉降在被试验面上,经24h喷雾后,每个收集器所收集的溶液,就80cm2而言应为1~2mL,被试面与垂直方向成15°~30°,不能直接喷射被试面。试样不能接触箱体,也不能相互接触。试样之间的距离应不影响盐雾自由降落在被试面上,试样上的液滴不得落在其他试样上。试验时间应按被试覆盖层或产品标准的要求而定,若无标准,推荐时间为2、6、16、24、48、96、240、480、720h。停喷时不加热,试样密封在箱内自然冷却。试样在试验结束后,取出试样。为减少腐蚀产物的脱落,试样在清洗前,放在室内自然干燥0.5~1h。然后用不高于40℃的清洁流动水轻轻清洗,除去试样表面盐雾溶液的残留物,经干燥后作外观检查和评级。按我国热带电工产品JB/Z 88-66评定标准,经盐雾试验后的腐蚀程度分为4级:1级为良好,2级为合格,3~4级为不合格。在每一级中,只要满足一项,就按该级评定。
铜盐加速醋酸盐雾试验
铜盐加速醋酸盐雾试验(CASS法)是中性盐水喷雾试验的改进方法。由于它在氯化钠溶液中用醋酸酸化,并加入氯化铜提高对某些金属涂层的腐蚀速率和效果,取得了钢铁基体上阴极性涂层腐蚀方式接近于实际环境的良好结果。CASS法与中性盐雾法相比,不仅腐蚀速度加快,而且重现性较好,所以正逐步取代中性盐雾法对阴极性涂层的耐蚀性检验。该法适用于钢铁基体上阴极性涂层(铜、镍、铬涂层等)和铝或铝合金上阳极氧化膜的耐腐蚀性检验。
铜盐加速醋酸盐雾试验的溶液成分为:氯化钠(NaCl)50±5g/L、氯化铜(CuCl2·H2O)0.26±0.02g/L,pH(用醋酸调整)为3.2±0.1。测试设备与盐雾试验设备大致相同,只是对箱体耐高温性要求更高(50±1℃)。目前除了专门用于CASS试验的设备外,也有与盐雾试验通用的设备。除测试温度为50±1℃外,其他条件与盐雾试验条件相同。
大气暴露腐蚀试验
大气暴露腐蚀试验是在天然大气条件下,对喷涂层试样在试样架上(室外或室内)进行实际的腐蚀试验,通过定期观察及测定其腐蚀过程特征和腐蚀速度确定其防护寿命。大气暴露试验是正确判断涂层耐蚀性能的一个重要方法,其评定结果通常作为制定涂层厚度标准的依据。具体试验方法可参照国家标准GB 6464-1986《金属和其它无机覆盖层 静置户外暴晒腐蚀试验一般规则》进行。
大气暴露腐蚀试验条件的选择应与工件使用的实际条件相同或相似。一般按暴露场地所处地区的环境条件,将大气条件分为四类(包括室内和室外):工业性大气、海洋性大气、农村大气和城郊大气。暴露场应设在完全敞开的地方,能充分受到大气(空气、日光、雨、露、雾、霜、雪等)的侵袭。周围的建筑物、树木和试样架应有一定间隔距离,保证周围建筑物和树木等的阴影在任何时刻不会投射到被测试样上。
试样大气暴晒的方式有三种:
1)露天暴晒,即将试样直接放在室外的框架上。框架采用能够经受腐蚀的材料制成,试样在框架上面向南方。框架附近的植物高度不应大于0.2m;
2)半封闭暴晒,把试样放在有顶棚遮盖下进行暴晒,以防止直接受太阳辐射和大气降水的作用,或试样暴晒在部分封闭的空间,例如百叶箱中;
3)“全封闭”暴晒,此时外界因素对试样的影响是非常有限的。
大气暴露试验用的试样,不得小于50cm2(5cm×10cm),专门制备的试样应为平板形状,一边的长度最好为50mm的整数倍,厚度为1~3mm。同一种试样的数量不得少于三件。在暴晒前应彻底清洗试样,以除去涂层表面的污染物。每件试样应有不易消失的编号,如打上钢印或挂有刻字的塑料牌等。试验开始前,试样应采用专用测试记录卡分别记录试样编号、涂层结构、厚度、外观光泽等情况,并编写试验纲要(包括测试目的、试验要求、检查周期等)。每种试样需留1~3件保存在干燥器内,供试验中比较观察。
试样投放最好选择每年的潮湿、阴雨季节前,建议在每年的4~5月或9~10月。由于大气腐蚀速度很慢,试验时间最好为1~20年。试样开始暴露后,头3个月内检查次数应频繁,一般每月2~3次。检查时应注意开始出现腐蚀点的时间,做好详细记录。3个月后每月检查一次,一年后每3个月检查一次。冬季室外暴露的试样如遇下雪时(指冬季有下雪的地区),应定期拭去表面的积雪。取试样时不可用手直接与主要表面接触。不允许将两片试样接触或摩擦以防止人为机械损伤或电化学腐蚀,造成试验结果误差。
测试结果的评定,除参照盐雾试验方法外,还可按试样表面腐蚀率进行腐蚀等级评定。
海水腐蚀试验
热喷涂防腐蚀技术目前已广泛用于大量海洋工程设施,如海上采油钻探平台、舰船及港口设施等,因此海水腐蚀试验是热喷涂涂层进行较多的试验内容之一。
海洋的腐蚀环境大致可以分为海洋大气区、飞溅区、潮差区、全浸区和海底泥浆区,由于所处环境的不同,使金属的腐蚀速度有很大差异。金属构件在飞溅区,处于干、湿交替,氧供应充足具有相当高的腐蚀性。高潮位区在涨潮时与含氧的海水接触,腐蚀也较严重。另外,潮差区相对低潮线以下的全浸区部分,形成明显的氧浓差电池作用,潮差区供氧充分为阴极,而恰好位于低潮线下的全浸区,因供氧相对较少而成为阳极,使腐蚀加速。按海洋环境区域特点,金属防护涂层的海水腐蚀试验可分为6类。
海洋大气腐蚀试验
可以表征船上、船舱内的金属防护涂层腐蚀,以及不会直接受到海水或浪花作用的海岸设施的金属防护涂层腐蚀。
浪花飞溅带腐蚀试验
表征海上和沿岸结构件在海平面之上经常遭受浪花飞溅作用,但不会受到海水浸润的金属防护涂层腐蚀。通常试样被放置在乎均高潮位上方0.2~2m的位置。
海水间浸试验
又称交替浸泡试验。表征港口结构和船体外部结构间或受到海水浸润的金属防护涂层腐蚀。
海水半浸试验
即海水水线腐蚀试验,表征任何海洋飘浮结构外部的气/液/固三相交界处的金属防护涂层腐蚀。
海水全浸试验
表征各种水下设施的金属防护涂层腐蚀,通常试样被放置在最低潮位以下0.2~2m的位置。
海洋土壤腐蚀试验
海洋土壤腐蚀试验。这是模拟埋在海底土壤部分的管道、电缆及水下设施的金属防护涂层腐蚀试验。
具体试验方法可参照国家标准GB 6384-1986《船舶及海洋工程用金属材料在天然环境的海水腐蚀试验方法》。海水腐蚀试验通常在专门的试验站进行。
03
腐蚀试验结果评定
涂层经腐蚀试验后,试验结果的评定方法有目测法、称重法、深度法和电流密度法。
目测法
热喷涂涂层在遭受某种类型的腐蚀之后,必然会导致涂层表面状态或性能等发生改变,腐蚀的产物也具有颜色、状态等特征,从这些特征及其变化情况,可以定性地判别涂层或基体金属的腐蚀程度,从而确定其防护性能。
目测法是用肉眼或放大镜(3~5倍)对涂层表面进行观察,有时也适当地使用一些简单的工具和设备。腐蚀后涂层的定性检查和记录,主要有以下五个方面:
(1)涂层和基体腐蚀产物的颜色和状态。
(2)腐蚀率:腐蚀率(涂层被穿透、直达基体金属的腐蚀点比率)是评定阴极性涂层防护性能的主要内容,可按下列方式观察计算:
评定时以5mm×5mm方格面积为单位,计算出现锈点的方格数占被测面积总方格数的百分比表示腐蚀程度。即:
腐蚀率(%)=n/N×100%
式中:n为出现锈点的5mm×5mm面积的方格数;N为试样表面的5mmX5mm面积总方格数。
计算方格数时,用一透明的带有5mm×5mm方格的有机玻璃板或塑料薄膜、覆盖在被测涂层试样表面,读出有腐蚀点的方格数(n)和被测涂层的总方格数(N),进行计算。
(3)光泽:经大气暴露后涂层的光泽,是指涂层呈膜状腐蚀时被氧化的程度。
(4)开裂:涂层开裂是指涂层经腐蚀后,表面出现肉眼能见的裂纹。计算方法与计算腐蚀率面积百分比相同。
(5)以定性评定结果确定涂层腐蚀等级。
称重法
称重法是对涂层腐蚀进行定量评定的主要方法,即测量单位时间内的涂层腐蚀失重,并得出其腐蚀速度。
定量评定的试样,在试验前应按要求称出准确重量,经一段时间腐蚀试验后取出试样,用规定溶液浸渍除去腐蚀产物,再干燥称重。将两次称重结果按下式计算腐蚀速度:
V = (W0-W1-W2)/(S×t)
式中:V为腐蚀速度,g·m2·h-1;W0为试样原始重量,g;W1为试样除去腐蚀产物后的重量,g;W2为清除腐蚀产物时同样尺寸同种材料空白试样的校正失重;S为试样表面积,m2;t为腐蚀时间,h。
深度法
腐蚀深度法是把涂层的厚度因腐蚀而减小的量,以线量单位表示,并换算成为相当于单位时间(年)内腐蚀掉的厚度(毫米)。该种指标常用腐蚀的失质指标与该涂层的密度比值表示,可按下列公式:

式中:KL为腐蚀的深度指标,mm/a;K-为腐蚀的失质指标,g/(m2.h);ρ为涂层密度,g/cm3;8.76为换算系数。
显然,知道了涂层的密度,即可将腐蚀的失质指标和深度指标进行换算。腐蚀的质量指标和深度指标,对于均匀的化学或电化学腐蚀均可采用。
电流密度法
电流密度法是以电化学腐蚀过程的阳极电流密度(A/cm2)的大小来衡量涂层腐蚀速度的程度。lmol物质发生电化学反应时所需的电量为1个法拉第,即96484≈96500C/mol。假如电流强度为I,通电时间为t,则通过的电量为It。从而可得出涂层阳极溶解的质量ΔW为:

式中:A为涂层的相对原子质量;n为价数;F为法拉第常数(1F=96500C/mol=26.8A·h)
对全面腐蚀而言,涂层表面积可看作是阳极面积S,从而得出腐蚀电流密度icorr=I/S(A/cm2)。所以腐蚀速度v-与腐蚀电流密度icorr之间存在如下关系:
v-=ΔW/St= A·icorr/nF
若icorr的单位取μA/cm2,涂层密度ρ的单位取g/cm3时:

或 

因此,可用腐蚀电流密度icorr表示涂层的电化学腐蚀速度。可见,腐蚀速度与腐蚀电流密度成正比关系。
值得指出的是,涂层的腐蚀速度一般随时间而变化。因此,在实验时应确定腐蚀速度与时间的关系,尽可能选择测定稳定腐蚀速率的时间。关于局部腐蚀的速度比较复杂,通常不能用上述方法表示。
免责声明:本网站所转载的文字、图片与视频资料版权归原创作者所有,如果涉及侵权,请第一时间联系本网删除。
相关文章
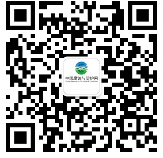
官方微信
《中国腐蚀与防护网电子期刊》征订启事
- 投稿联系:编辑部
- 电话:010-62316606-806
- 邮箱:fsfhzy666@163.com
- 中国腐蚀与防护网官方QQ群:140808414
点击排行
PPT新闻
“海洋金属”——钛合金在舰船的
点击数:7130
腐蚀与“海上丝绸之路”
点击数:5741