摘要: 以自行设计开发的新型3Cr2Al低合金钢为研究对象,采用高温高压磁力驱动反应釜进行饱和CO2模拟油田采出液环境下的腐蚀模拟实验,通过失重法获取腐蚀速率评价其耐蚀性能,并结合扫描电子显微镜、能谱分析、电化学测试等表征手段,研究腐蚀产物膜结构及成分特征,探讨耐蚀机理。相比3Cr钢,3Cr2Al钢中少量Al的添加提高了材料的抗CO2腐蚀性能,在短周期(20 h)和长周期(144 h)条件下,其腐蚀速率分别下降15%和69%,这种耐蚀性能的提升主要是由于3Cr2Al钢表面产物膜中不仅有Cr的富集,同时还有Al的富集,提高了产物膜对基体的保护性。溶液中的氯离子对产物膜中Al的富集存在一定影响,在低氯溶液环境中,3Cr2Al钢表面腐蚀产物膜中Al/Fe原子比明显高于其Cr/Fe原子比,Al的富集更明显;当提高溶液氯离子浓度,腐蚀产物膜中Al/Fe原子比相比低氯溶液明显降低,Al的富集程度减弱,阳极极化曲线半钝化现象消失。
关键词: 材料失效与保护 ; 低Cr合金钢 ; CO2腐蚀 ; 元素富集 ; 半钝化
近年来,油气矿藏资源被大规模开采,其储量已出现明显下降,高效开采深层油气资源越来越被人们所重视。但与此同时,这也带来了一系列的腐蚀问题。碳钢作为油气工业应用最为广泛的管道材料,其经济性好,但耐蚀性较差,已不能应对目前日益苛刻的CO2腐蚀问题[1,2]。耐蚀合金虽具有较高耐蚀性,但经济性较差。对此,近年来相关研究学者开展了大量抗CO2腐蚀低Cr材料的开发及其腐蚀行为、耐蚀机理等方面的深入研究[3,4,5,6,7,8,9,10,11]。含Cr低合金钢(简称“低Cr钢”)的成功开发填补了碳钢和不锈钢之间的空白,兼具经济性和耐蚀性。阿根廷SDT公司对含CO2油田使用不同材料的经济性进行了评价[12],包括普通油套管钢+缓蚀剂防腐、低Cr油套管钢以及耐蚀合金钢。对比结果表明,在腐蚀性不是很苛刻的环境下,低Cr钢表现最佳。国内方面,宝山钢铁股份有限公司“抗CO2、H2S腐蚀用3Cr系列油套管研制”项目获得2009年度国家技术发明二等奖,低Cr钢的开发和应用已成为抗CO2腐蚀油井管材的发展趋势,也为长期以来严重的油气田CO2腐蚀问题的解决提供了一个有效的新途径。目前,Cr含量为3%的3Cr钢在国内外油气田获得了一定范围的应用,如宝钢开发的BG80-3Cr、BG110-3Cr、BG80S-3Cr、BG95S-3Cr等系列油套管,己成功应用于中石化江汉油田、中石油大庆油田、塔里木油田等含CO2、微量H2S腐蚀环境的油气井。兼具良好耐蚀性和经济性的3Cr钢有望在中等苛刻环境下代替普通碳钢和不锈钢在油气田的现场应用。
低Cr钢的抗腐蚀性能与钢中Cr元素的添加密切相关,其表面可以形成具有保护性的腐蚀产物膜,从而提高了基材对CO2腐蚀的耐受能力。当Cr含量增加到3%左右时,腐蚀产物表现为Cr元素的高度富集,主要为非晶态的Cr(OH)3或富Cr的FeCO3层[13]。Cr含量在3%~4%时,可以有效预防局部腐蚀的发生[14]。但在实际应用中,由于腐蚀环境的复杂多变,如管线内部O2的混入等,导致了低Cr钢在实际应用中仍然面临一定的腐蚀风险。因此,通过合金化方式进一步提升其耐蚀性能十分必要。Al作为一种重要的合金化元素,其在常用金属材料中电位较低。从热力学上看,它极不稳定,易发生腐蚀。但这也促进了其表面致密、牢固氧化膜的快速生成,从而使铝表面钝化。Al和Cr在钢中的同时添加,将会明显提高材料的抗腐蚀能力[15,16]。例如,在含9%Cr的P91钢中添加约2%的Al可以极大的提高P91钢的抗腐蚀能力[17]。针对含铝钢耐蚀性能的研究已有较多报道,但针对含Al钢在油气工业CO2环境下的腐蚀行为研究较少,尤其针对含Al低Cr钢的相关研究更鲜有报道。
本文通过自行设计和炼制了一种Al含量为2%的新型低Cr钢,采用腐蚀模拟、微观表征和电化学测试,研究了其在CO2环境中的腐蚀行为及氯离子浓度对其腐蚀产物膜和电化学特性的影响,探讨了Cr、Al等元素在提高其抗CO2腐蚀性能方面所起的作用。
1 实验方法
1.1 实验材料
以普通3Cr钢为基础,通过添加少量的Al(约2%,质量分数),设计开发了一种新型的含Al低Cr钢(简称3Cr2Al钢),由钢铁研究总院完成炼制,具体材质成分如表1所示。
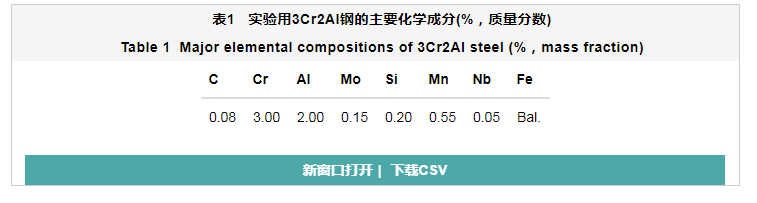
1.2 腐蚀模拟实验
为了模拟现场实际运行工况,采用高温高压磁力驱动反应釜进行油田采出液环境下的CO2腐蚀模拟实验,温度80oC,CO2压力0.8 MPa,实验周期20、144 h。同时,为了研究氯离子浓度对3Cr2Al钢腐蚀行为的影响,采用两种不同氯离子浓度的模拟某油田采出液作为腐蚀介质,溶液成分配比见表2。
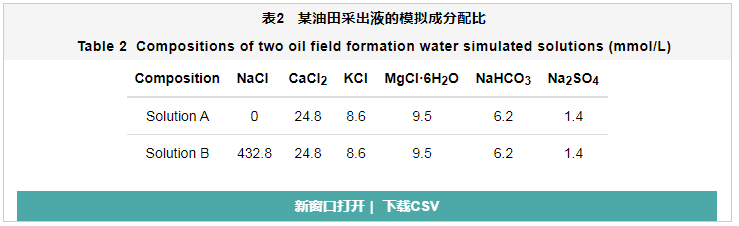
实验采用弧形试样。每组实验需制备4个用于表面分析试样和1个截面样(弧长约为表面试样的1/3)。实验前,将试样表面用砂纸逐级打磨至1500#,依次丙酮除油、去离子水清洗以及吹风干燥。电子分析天平称量试样初始重量,游标卡尺测量试样尺寸。试样安装于特制的聚四氟乙烯夹具侧面卡槽内,硅胶密封,使需要腐蚀的表面单独暴露。待实验结束后,取下试样快速清洗并干燥。其中,截面试样通过冷镶制成扫描电镜观测试样,用于腐蚀产物膜截面的形貌观察和成分分析;1个表面试样进行喷碳处理用于腐蚀产物膜表面微观形貌和成分的分析;3个表面试样(平行试样)按照式(1)通过失重法获取平均腐蚀速率。腐蚀产物的去除参考ASTM G1-03[18]标准进行,即用蒸馏水将500 mL浓盐酸和3.5 g六次甲基四胺稀释至1000 mL,在20~25℃的温度下将试样在溶液中浸泡10 min。
式中,Ci 为均匀腐蚀速率,mm?y-1;W0i 为试样腐蚀前原始重量,g;W1i 为试样酸洗后重量,g;t为腐蚀模拟实验周期,h;ρ为金属材料密度,g?cm-3;S为试样暴露面积,cm2。
1.3 电化学测试
采用传统三电极体系对试样在上述表2中的两种溶液中进行电化学测试,辅助电极为铂片,参比电极为Ag/AgCl,工作电极为3Cr2Al方形试样。实验温度80oC,饱和CO2溶液环境。在极化曲线测试前,稳定开路电位约1 h,动电位扫描起始和终止电位分别为相对开路电位-200 mV和500 mV,扫描速度0.1 mV/s。
1.4 微观表征
采用LEO-1450型扫描电镜(SEM)对试样表面和截面腐蚀产物膜进行微观形貌的观察和分析,并结合Kevex SuperDry型能谱分析系统(EDS),采用点扫和面扫的方式分析腐蚀产物膜的成分特征和元素分布。并采用微区拉曼测试方法对截面腐蚀产物进行进一步的成分表征。
2 结果及分析
2.1 微观组织
图1为3Cr2Al钢的金相组织SEM形貌图。由图可以看出,3Cr2Al钢主要是由铁素体和贝氏体组成。相较于传统的3Cr钢,其铁素体含量较高,这是由于Al是铁素体形成元素,Al的添加诱发了更多铁素体组织的形成。

2.2 宏观腐蚀形貌和腐蚀速率
图2给出了在80℃、0.8 MPa的饱和CO2模拟油田采出液中3Cr2Al钢不同周期下的腐蚀形貌图。腐蚀20 h后(图2a),材料表面整体较为平整,腐蚀产物较少;144 h后腐蚀产物明显增多,且外层明显有不连续物质覆盖,呈点状凸起分布。酸洗后,如图2c和d所示,材料基体表面较为平整,未见明显的局部腐蚀发生。
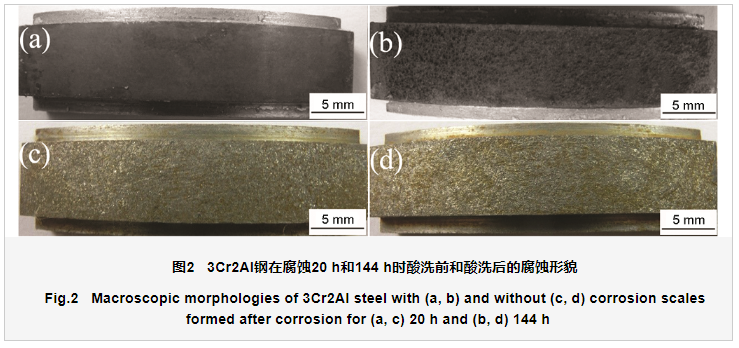
通过失重法计算获得3Cr2Al钢在不同周期下的平均腐蚀速率,如图3所示。同时测量了不含Al的普通3Cr钢在相同条件下的腐蚀速率,作为参照。可以看出,相比3Cr钢,3Cr2Al钢的腐蚀速率明显下降。在较短周期条件下(20 h左右),3Cr2Al钢腐蚀速率相比3Cr钢下降了约15%;而在较长周期条件下(144 h左右),其下降幅度达到69%。也就是说,在较长腐蚀周期下,3Cr2Al钢腐蚀速率的下降更为明显,这说明3Cr2Al钢表面腐蚀产物膜相比3Cr钢具有更好的保护性。
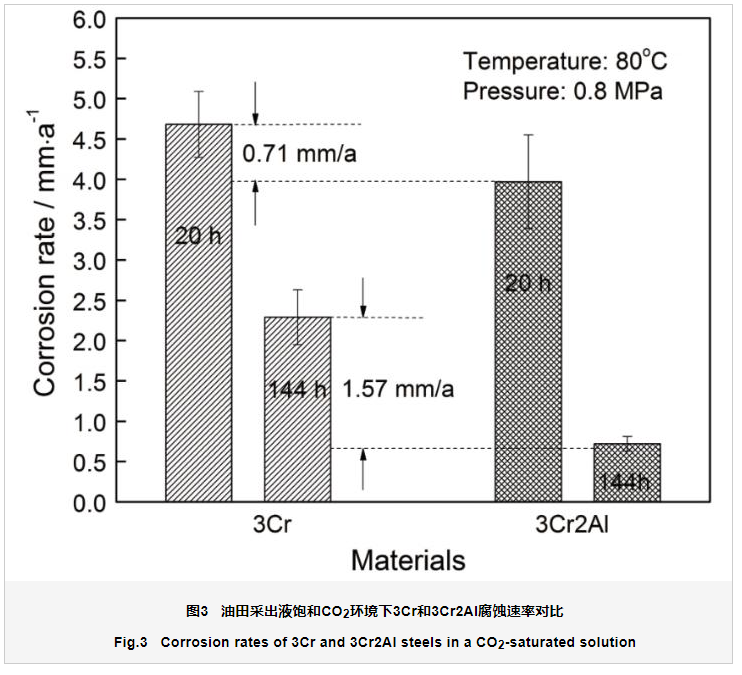
2.3 表面微观腐蚀形貌和腐蚀产物膜成分分析
图4给出了3Cr2Al钢在饱和CO2模拟油田采出液(A溶液)环境中腐蚀20 h后的表面形貌和元素成分分析。可以看出,3Cr2Al钢表面腐蚀产物膜呈明显的龟裂状,这很可能是由于Cr元素在腐蚀产物膜中以Cr(OH)3的形式富集,致密的富Cr产物膜从高压釜中取出后发生脱水开裂导致[10]。EDS能谱分析结果表明,腐蚀产物膜中除了Cr的富集,同时出现了明显的Al元素富集。与Cr(OH)3类似,Al很可能是以Al(OH)3的形式存在。
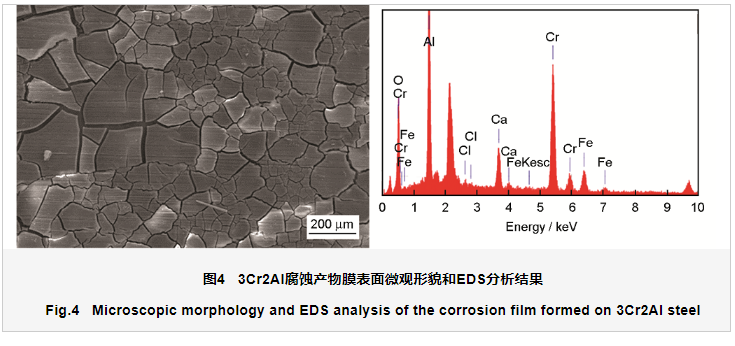
2.4 腐蚀产物膜截面形貌和元素分布
3Cr2Al钢在溶液A中腐蚀后的截面形貌如图5所示。左侧深色区域为环氧树脂,右侧浅色区域为金属基体,中间部分为生成的腐蚀产物层。从图中可以看出,3Cr2Al钢在腐蚀20 h后,已经生成完整覆盖的腐蚀产物膜,其厚度约为21.8 μm。Zhu等人曾对3Cr钢在CO2环境中的腐蚀作过系统研究[19],发现3Cr钢在腐蚀初期(8 h)生成的产物膜极薄且覆盖度较低,基体表面仍存在大量裸钢区域,24 h后则形成具有一定厚度且完整覆盖的产物层,厚度约为5.5 μm。与3Cr钢对比,类似条件下3Cr2Al钢在较短的时间里即可生成更厚更完整的产物层(21.8 μm),推测这可能与产物膜中不仅有Cr的富集,还有Al的富集有关。
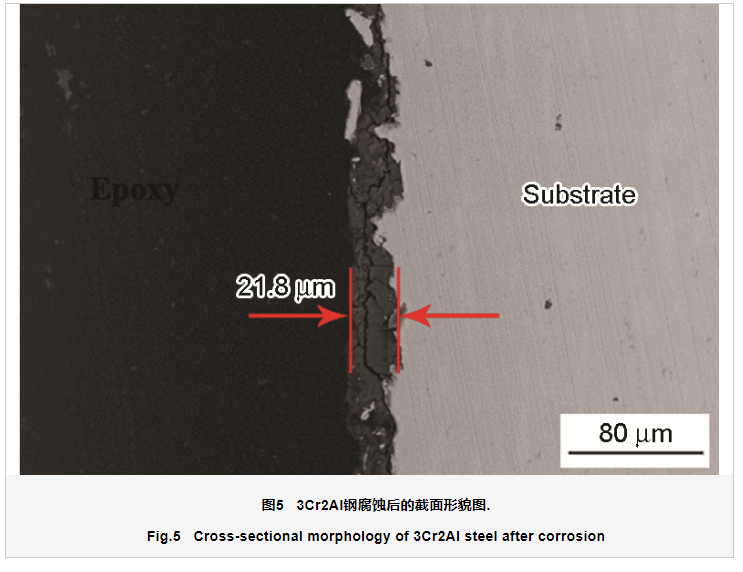
为了进一步验证腐蚀产物膜的成分,对图5中的截面试样进行了选区拉曼谱分析,结果如图6所示。拉曼频移在3000 cm-1左右的吸收峰主要源于OH伸缩振动[20]。另外,含OH的金属化合物在700~1200 cm-1左右会出现面内弯曲振动谱带[20],798 cm-1和715 cm-1两处的吸收峰对应含OH金属化合物的面内弯曲振动。451 cm-1和614 cm-1处的特征峰分别对应Al-O和Cr-O的伸缩振动峰[20,21]。综上,结合EDS测试结果及前期研究结果,认为3Cr2Al钢表面腐蚀产物膜中Al和Cr分别主要以Al(OH)3和Cr(OH)3的形式存在。

3Cr2Al钢在溶液A中腐蚀产物膜截面区域EDS面扫结果如图7所示。由图可知,与基体相比,腐蚀产物层中出现了明显的Cr和Al的富集,尤其Al的富集程度更高;从分布上看两种元素在腐蚀产物膜中为均匀分布,无分层现象。图8给出了产物膜中关键元素的含量对比。结果表明,腐蚀产物膜中Cr、Fe、Al元素的含量(原子百分比)依次约为38.2%,17.3%,6.8%,对应Al/Fe原子比约为5.65,远高于Cr/Fe原子比(约为2.56)。这进一步证明了3Cr2Al钢表面腐蚀产物膜中Al的富集更明显,这对材料耐蚀性能的提升有利,这也是3Cr2Al钢耐蚀性能优于普通3Cr钢的主要原因。
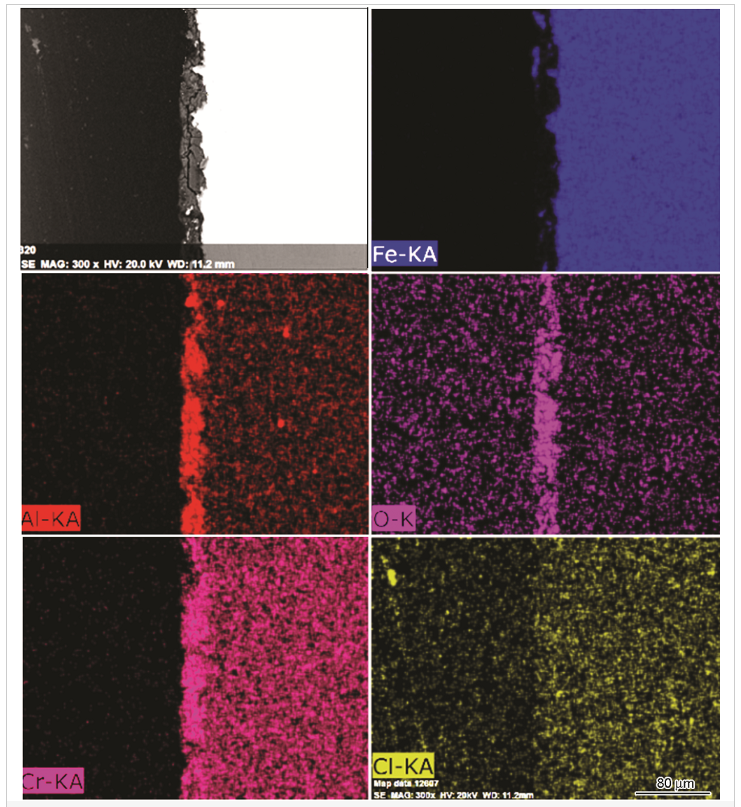
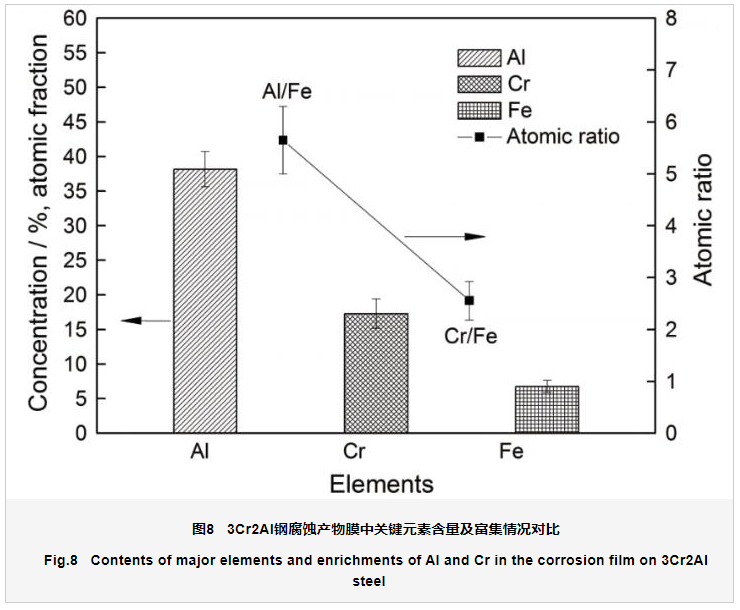
2.5 溶液中氯离子对产物膜特性的影响
为了进一步研究溶液中氯离子对腐蚀产物膜特性的影响,尤其对Al、Cr元素富集的影响,本节针对高氯采出液(B溶液)环境中3Cr2Al钢表面腐蚀产物膜进行了截面形貌和元素分布的分析,结果如图9所示。对比图9和图7可以看出,在产物膜厚度方面,在高氯溶液环境下,3Cr2Al钢表面产物膜厚度明显小于低氯溶液(A溶液)下的产物膜厚度。在元素富集方面,与低氯溶液下的产物膜类似,在高氯溶液环境下3Cr2Al钢表面的腐蚀产物膜中也有Cr和Al的富集,并且也呈均匀分布,无分层现象。低氯和高氯溶液下腐蚀产物膜中各元素含量的对比如图10所示。可以看出,当提高溶液中氯离子含量,材料表面腐蚀产物膜中Al含量和Al/Fe原子比相比低氯溶液条件下的均明显降低,Al的富集程度减弱,而Cr、Fe的含量变化不明显。也就是说,在饱和CO2溶液环境中Al和Cr均具有在材料表面富集的能力,但在较高氯离子含量的溶液中,Al元素的富集程度会减弱,而Cr的富集则基本不受影响,二者的富集行为存在差异。
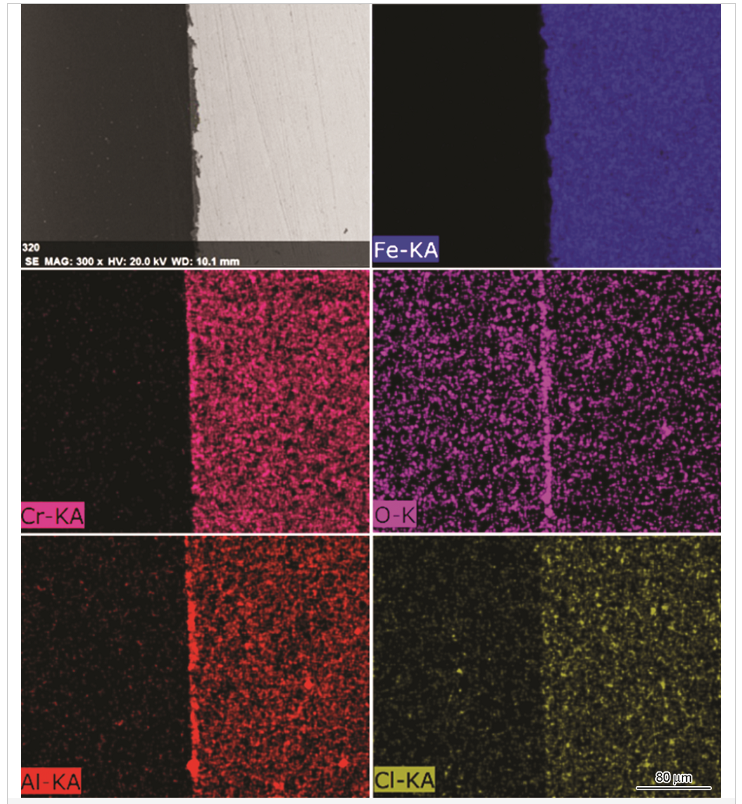
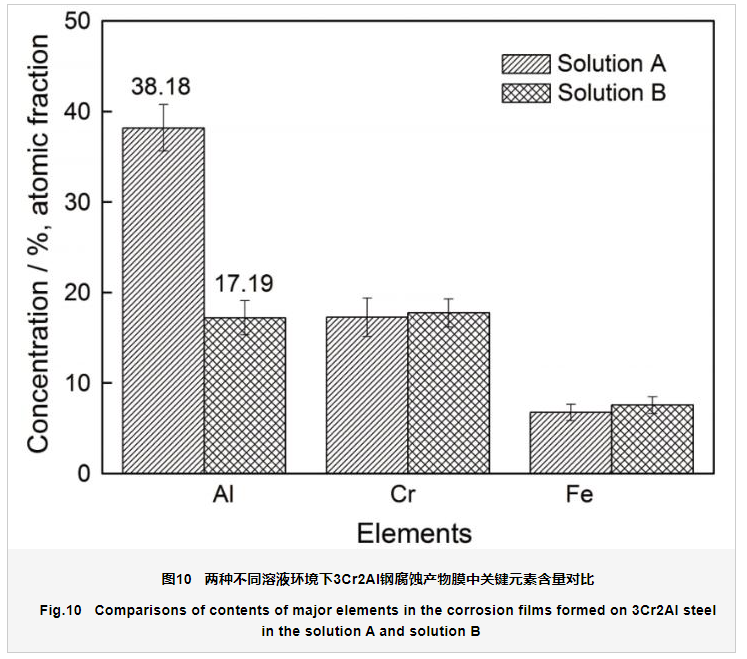
另一方面,对高氯和低氯两种溶液条件下3Cr2Al钢进行了动电位极化曲线的测试,如图11所示。整体来看,在高氯溶液中,3Cr2Al钢的阴、阳极极化曲线均右移,腐蚀电流密度增大。对于阳极极化曲线,在低氯溶液条件下,出现了一个明显的电流回头峰,文献中把这种现象称为“半钝化”[10]。而在高氯溶液条件下,这种电流的下降现象消失,试样表现为活化态。这说明,随着氯离子浓度的升高,3Cr2Al钢腐蚀电流密度升高,钝化特性减弱,腐蚀速率增大。这与图9和图10中高氯溶液中腐蚀产物膜中Al的富集程度减弱导致腐蚀产物膜保护性下降的结果是相符的。
显然,上述产物膜厚度以及Al、Cr在不同氯离子含量溶液中形成的腐蚀产物膜中富集程度变化是一个很有趣的现象,对此本文开展如下讨论。首先,我们测试了Cl-的添加对溶液pH的影响,结果表明,随着Cl-浓度的升高,溶液的pH值逐渐降低。在高氯离子含量的B溶液中,其pH约为5.43,相比低氯离子含量的A溶液(pH约为5.68)下降约0.25。相关研究已经证实,当溶液pH值低于6时,Cr(OH)3的溶解度随着pH的降低而升高[22,23]。当pH为5.43时,Cr(OH)3的溶解度大约是pH为5.68时的4倍[24]。因此,对于高氯含量的B溶液,其Cl-浓度较高,溶液pH较低,对应Cr(OH)3的溶解度较高,这就导致Cr(OH)3在3Cr2Al表面的沉积更加困难。对于Al元素[25],当溶液pH低于5.8时,Al(OH)3的溶解度随着pH的降低而升高。当溶液的pH为5.43时,Al(OH)3的溶解度大约是溶液pH为5.68时的5倍。因此,当溶液的Cl-浓度较高时,Cr(OH)3和Al(OH)3的沉积均会受到抑制,最终导致在高氯含量的B溶液中所形成的腐蚀产物膜厚度较小。3Cr2Al钢耐蚀性能的好坏主要取决于产物膜的保护性,当产物膜致密性接近时,腐蚀产物膜越厚,保护性越好,腐蚀速率越低。也就是说,Cl-通过改变溶液的pH值,从而影响了腐蚀产物膜的厚度,最终影响了腐蚀速率。
另一方面,如图10所示,在高氯含量的B溶液下腐蚀产物膜中Al的含量明显低于A溶液下的。这说明,通过改变溶液的pH值,Cl-不但显著影响了产物膜的厚度,同时也影响了Al的富集。Al在溶液中有强烈的水解倾向,当溶液pH大于3.5时,Al与氢氧根形成多种化合物[26]。在本文中,如式(2)和式(3)所示,3Cr2Al钢的主要阳极反应是Al的水解[27]。
随着Al的水解,氢氧化铝在3Cr2Al钢表面形成。当溶液中含有氯离子时,则会同时发生式4,5,6的反应[28,29,30]。
当提高溶液中Cl-含量,更多的Al会形成Al(OH)2Cl,Al(OH)3的沉积量变低。因此,Cl-除了对Al有间接影响外,也通过直接的方式影响Al(OH)3的沉积,从而降低Al元素的富集程度。而对于Cr元素,Cr不与Cl-形成可溶性的物质。因此Cl-对Cr(OH)3的沉积并没有直接影响。如图11所示,在高Cl-含量的B溶液中,腐蚀产物膜中的Cr含量仅比A溶液下的Cr含量略高一些。这可能是由于产物膜中Al含量的减少,从而导致Cr含量相对略微升高。
综上表明,溶液中Cl-影响产物膜中Al元素富集的机理与影响Cr元素的机理不同。对于Al,Cl-有两种影响方式:一是直接地参与Al的水解过程,减少不溶性Al(OH)3的形成和沉积;另一种是降低溶液pH值,从而阻碍Al(OH)3的沉积。而对于Cr元素,Cl-只有一种间接的影响方式,即通过降低溶液pH值,从而间接的阻碍Cr(OH)3的沉积。从实验结果来看,这种间接的影响效果较弱,而Cl-直接参与水解过程抑制Al(OH)3的形成和沉积为主要的影响方式。
3 结论
(1) 3Cr2Al钢中Al的添加可以提高材料自身的抗CO2腐蚀性能,这主要与Al的富集有关。相比无Al的普通3Cr钢,3Cr2Al钢表面腐蚀产物膜具有更好的保护性。
(2) Al与Cr相同,均可以在腐蚀产物膜中富集,并且都是均匀富集,Al的富集能力略强于Cr的。
(3) 溶液中Cl-的存在会降低Al在腐蚀产物膜中的富集能力,这主要是由以下两个方面导致,一方面是Cl-直接参与Al的水解过程,减少了不溶性Al(OH)3的形成;另一方面是Cl-通过改变溶液的pH值,Al(OH)3的溶解度升高,从而抑制了Al(OH)3在金属基体表面的沉积。
参考文献
[1] Ingham B, Ko M, Kear G, et al. In situ synchrotron X-ray diffraction study of surface scale formation during CO2 corrosion of carbon steel at temperatures up to 90 ℃ [J]. Corros. Sci., 2010, 52: 3052
doi: 10.1016/j.corsci.2010.05.025
[2] Zhang G A, Cheng Y F. Localized corrosion of carbon steel in a CO2-saturated oilfield formation water [J]. Electrochim. Acta, 2011, 56: 1676
doi: 10.1016/j.electacta.2010.10.059
[3] Sun J B, Su X, Zhang Y. Effect of H2S/CO2 corrosion scales on the hydrogen permeation behavior of low chromium steels [J]. Surf. Technol., 2018, 47(6): 17
[3] (孙建波, 苏鑫, 张勇. 高温高压H2S/CO2腐蚀产物膜对低铬钢氢渗透行为的影响 [J]. 表面技术, 2018, 47(6): 17)
[4] Nice P I, Buene A M, Takabe H, et al. Corrosion problem and its countermeasure of 3Cr110 production tubing in NaCl completion brine on the statfjord field [A]. Corrosion 2006 [C]. Houston: NACE International, 2006
[5] Nice P I, Takabe H, Nice P I. The development and implementation of a new alloyed steel for oil and gas production wells [A]. Corrosion 2000 [C]. Houston: NACE International, 2000
[6] Cheng L, Yu W, Cai Q W. Influence of microbands refined microstructure and two phase microstructure on high temperature fracture behaviors of a low Cr alloy steel [J]. Chin. J. Mater. Res., 2020, 34 (1): 21
[6] (程磊, 余伟, 蔡庆伍. 显微带细化组织和两相组织对低Cr合金钢高温断裂行为的影响 [J]. 材料研究学报, 2020, 34 (1): 21)
[7] Ueda M, Takabe H. The formation behavior of corrosion protective films of low Cr bearing steels in CO2 environments [A]. Corrosion 2001 [C]. Houston: NACE International, 2001
[8] Linter B R, Burstein G T. Reactions of pipeline steels in carbon dioxide solutions [J]. Corros. Sci., 1999, 41: 117
doi: 10.1016/S0010-938X(98)00104-8
[9] Chen C F, Liu M X, Zhao G X, et al. The ion passing selectivity of CO2 corrosion scale on N80 tube steel [A].Corrosion 2003 [C]. Houston: NACE International, 2003
[10] Zhu J Y, Xu L N, Lu M X, et al. Essential criterion for evaluating the corrosion resistance of 3Cr steel in CO2 environments: prepassivation [J]. Corros. Sci., 2015, 93: 336
doi: 10.1016/j.corsci.2015.01.030
[11] Zhu J Y, Xu L N, Feng Z C, et al. Galvanic corrosion of a welded joint in 3Cr low alloy pipeline steel [J]. Corros. Sci., 2016, 111: 391
doi: 10.1016/j.corsci.2016.05.032
[12] Kermani M B, Gonzales J C, Linne C, et al. Development of low carbon Cr-Mo steels with exceptional corrosion resistance for oilfield applications [A]. Corrosion 2001 [C]. Houston: NACE International, 2001
[13] Xu L N, Wang B, Zhu J Y, et al. Effect of Cr content on the corrosion performance of low-Cr alloy steel in a CO2 environment [J]. Appl. Surf. Sci., 2016, 379: 39
doi: 10.1016/j.apsusc.2016.04.049
[14] Ueda M, Takabe H, Nice P I. The development and implementation of a new alloyed steel for oil and gas production wells [A]. Corrosion 2000 [C]. Orlando: NACE International, 2000
[15] Melchers R E. Effect of small compositional changes on marine immersion corrosion of low alloy steels [J]. Corros. Sci., 2004, 46: 1669
doi: 10.1016/j.corsci.2003.10.004
[16] Wang R, Luo S J, Liu M, et al. Electrochemical corrosion performance of Cr and Al alloy steels using a J55 carbon steel as base alloy [J]. Corros. Sci., 2014, 85: 270
doi: 10.1016/j.corsci.2014.04.023
[17] Li Y S, Spiegel M, Shimada S. Effect of Al/Si addition on KCl induced corrosion of 9% Cr steel [J]. Mater. Lett., 2004, 58: 3787
doi: 10.1016/j.matlet.2004.06.068
[18] ASTM G1-03 Standard practice for preparing, cleaning, and evaluating corrosion test specimens [S]. West Conshohocken, PA: ASTM International, 2011
[19] Zhu J Y, Xu L N, Lu M X. Electrochemical impedance spectroscopy study of the corrosion of 3Cr pipeline steel in simulated CO2-saturated oilfield formation waters [J]. Corrosion, 2015, 71: 854
doi: 10.5006/1494
[20] Nakamoto K. Infrared and Raman Spectra of Inorganic and Coordination Compounds [M]. New York: Wiley, 1991
[21] Zhu J Y, Xu L N, Lu M X, et al. Interaction effect between Cr(OH)3 passive layer formation and inhibitor adsorption on 3Cr steel surface [J]. RSC Adv., 2015, 5: 18518
doi: 10.1039/C4RA15519J
[22] Rai D, Moore D A, Hess N J, et al. Chromium (III) hydroxide solubility in the aqueous Na+-OH--H2PO-4-HPO2-4-PO3-4-H2O system: A thermodynamic model [J]. J. Solut. Chem., 2004, 33: 1213
doi: 10.1007/s10953-004-7137-z
[23] Udea M, Ikeda A. Effect of microstructure and Cr content in steel on CO2 corrosion [A]. Corrosion 1996 [C]. Houston: NACE International, 1996
[24] Papassiopi N, Vaxevanidou K, Christou C, et al. Synthesis, characterization and stability of Cr(III) and Fe(III) hydroxides [J]. J. Hazard. Mater., 2014, 264: 490
doi: 10.1016/j.jhazmat.2013.09.058
[25] Roberson C E, Hem J D. Solubility of aluminum in the presence of hydroxide, fluoride, and sulfate [P]. U S Geol Surv Water-Supply Paper, 1969
[26] Hem J D, Roberson C E. Form and stability of aluminum hydroxide complexes in dilute solution [P]. US Geol. Survey Water Supply Paper. Washington DC: US Government Printing Office, 1967
[27] Sun Z, Zhang D H, Yan B X, et al. Effects of laser remelting on microstructures and immersion corrosion performance of arc sprayed Al coating in 3.5% NaCl solution [J]. Opt. Laser Technol., 2018, 99: 282
doi: 10.1016/j.optlastec.2017.09.013
[28] Da Silva F S, Bedoya J, Dosta S, et al. Corrosion characteristics of cold gas spray coatings of reinforced aluminum deposited onto carbon steel [J]. Corros. Sci., 2017, 114: 57
doi: 10.1016/j.corsci.2016.10.019
[29] Li S X, Khan H A, Hihara L H, et al. Corrosion behavior of friction stir blind riveted Al/CFRP and Mg/CFRP joints exposed to a marine environment [J]. Corros. Sci., 2018, 132: 300
doi: 10.1016/j.corsci.2018.01.005
[30] Sherif E S M, Almajid A A, Latif F H, et al. Effects of graphite on the corrosion behavior of Aluminum-graphite composite in sodium chloride solutions [J]. Int. J. Electrochem. Sci., 2011, 6: 1085
免责声明:本网站所转载的文字、图片与视频资料版权归原创作者所有,如果涉及侵权,请第一时间联系本网删除。
相关文章
无相关信息
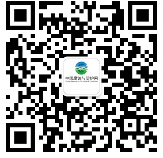
官方微信
《中国腐蚀与防护网电子期刊》征订启事
- 投稿联系:编辑部
- 电话:010-62316606-806
- 邮箱:fsfhzy666@163.com
- 中国腐蚀与防护网官方QQ群:140808414
点击排行
PPT新闻
“海洋金属”——钛合金在舰船的
点击数:7204
腐蚀与“海上丝绸之路”
点击数:5800