摘要
采用微观形貌观察以及失重法研究了不同转速下循环泵叶轮材料高铬铸铁Cr30A在模拟湿法脱硫浆料环境中的腐蚀磨损行为,研究了转速对高铬铸铁腐蚀磨损行为的影响以及腐蚀-磨损交互作用。结果表明,腐蚀磨损中机械磨损占主导作用。腐蚀-磨损交互作用程度随转速不同而产生变化,当转速为400 r/min时,腐蚀磨损试样表面无氧化膜,腐蚀磨损交互作用量占总腐蚀磨损量的48.73%,表现为协同作用;当转速为1200 r/min时,腐蚀磨损试样表面存在致密氧化膜,腐蚀-磨损交互作用量为负,表现为对抗作用。腐蚀-磨损交互作用是影响材料耐磨蚀性能的重要因素。
关键词: 脱硫循环泵 ; 高铬铸铁Cr30A ; 腐蚀磨损 ; 交互作用 ; 湿法脱硫
脱硫浆液循环泵通常被称为火电厂脱硫过程中的动力心脏,是整个湿法脱硫工艺中至关重要的一部分。冲蚀磨损的腐蚀磨损模式是叶轮材料失效的主要原因。冲蚀磨损是指液体或固体颗粒对材料表面进行腐蚀和冲击而造成的材料损坏的现象,普遍存在于化工、矿山、水利、发电等行业[1]。在实际工况下,由于不仅仅是脱硫浆液的腐蚀和磨损简单相加,还存在二者之间的交互作用,这使得浆液循环泵过硫件尤其叶轮的工作寿命极短。现阶段火电厂维护处理方法主要是表面施加涂层和加装内衬,但是这两种措施受经济条件以及实际成效等因素的制约,很难取得理想效果。因此,研究材料本身腐蚀磨损失效规律对于延长循环泵使用寿命显得尤为重要。
高铬铸铁Cr30A作为循环泵的主要使用材料,相比于以前使用的高锰不锈钢和镍硬铸铁,具有高硬度、优异的韧性以及抗腐蚀磨损能力,在使用寿命方面更具优势。这些性质是因为其存在高硬度的硬质相碳化物,发挥了优越的抗磨削作用,同时保护了基体。Seetharamu等[2]研究了以抗磨损著称的铬铁,通过添加Mn,能够进一步改善其抗磨损性能。Anijdan等[3]研究了含W和不含W的高铬白口铸铁在冲蚀腐蚀条件下的耐磨性。浆液循环泵叶片的腐蚀磨损并非纯磨损和纯腐蚀的简单叠加,腐蚀磨损是一个非常复杂的过程,既有磨损又有腐蚀,还存在着二者的交互加速作用。Al-Bukhaiti等[4]使用浆料旋臂试验台研究了冲击角对AISI 1017钢和高铬白口铸铁冲蚀磨损的影响。Tian等[5]研究了一系列铸造高铬铸铁的微观结构及其相应的耐磨性和耐腐蚀性,认为这些高铬铸铁的耐腐蚀性在很大程度上取决于基体中的Cr含量和碳化物体积分数,而耐磨性主要由碳化物的体积分数决定。据报道,在阿尔伯塔油砂行业,高铬铸铁广泛用于泥浆泵输送系统以及其他加工和处理设备[6]。
现阶段对高铬铸铁Cr30A腐蚀磨损失效规律研究不多,且较集中在材料的纯腐蚀或纯磨损失效方面,而对于在实际工况中存在的浆料对材料腐蚀-磨损交互作用研究较少。本文对高铬铸铁Cr30A在模拟湿法脱硫浆料环境下的腐蚀磨损行为进行了研究,特别是探究了循环泵转速的影响以及腐蚀-磨损交互作用机制。
1 实验方法
1.1 实验装置
在腐蚀磨损试验机上进行高铬铸铁Cr30A的腐蚀磨损实验。图1是本实验所使用的腐蚀磨损试验机工作原理示意图。实验时,将立方体试样贴壁固定在容器内壁之上,整个浸泡于腐蚀浆液之中,主轴上有旋转叶片并随轴转动,浆液随叶片旋转冲击试样表面。实验结束后,测定样品的质量损失,以表征材料的腐蚀磨损程度。
图1 腐蚀磨损装置示意图
1.2 腐蚀、磨损及其交互作用程度的表征方法
金属材料腐蚀磨损时,材料的损失是力学因素、电化学因素和环境因素共同作用的结果。腐蚀和磨损对材料损失产生明显的互相促进作用[7]。根据下式,材料的总损失量V大于纯腐蚀量VC与纯磨损量VW之和,差值为腐蚀-磨损交互作用量ΔV:
ΔV=V−VC−VW(1)
在模拟湿法脱硫浆料中进行腐蚀磨损实验,测量实验前后高铬铸铁Cr30A的失重,得到V。在静态腐蚀的条件下测量纯腐蚀实验前后高铬铸铁Cr30A的失重,得到VC。在去离子水中进行纯磨损实验测量高铬铸铁Cr30A的失重,此时材料流失可以看作是由单纯机械磨损所致,得到纯机械作用下的损失量VW。
1.3 实验条件
实验材料为高铬铸铁Cr30A,其化学成分 (质量分数,%) 为:C 0.012,Si 0.36,Mn 0.48,Cr 29.05,Mo 1.79,Ni 1.2,N 0.012,Fe余量。将实验材料线切割成10 mm×10 mm×10 mm的立方体试样,依次用240#、400#、800#、1200#和2000#的砂纸打磨试样表面,然后进行抛光,最后在无水乙醇中超声清洗20 min,称重后备用。
配制3种实验浆液如下所示,分别用于纯磨损、纯腐蚀和腐蚀磨损实验。
纯腐蚀溶液:3.5% (质量分数) NaCl水溶液,用98% (质量分数) H2SO4溶液将pH值调至约为3。
纯磨损浆液:石英砂 (粒度为40~70目)+去离子水,其质量配比为1∶4。
腐蚀磨损浆液:石英砂 (粒度为40~70目)+3.5%NaCl水溶液,其质量配比为1∶4,用98%H2SO4溶液将pH值调至约为3。
实验时间为24 h,实验之后洗净称重。为了尽可能模拟载荷较大的实际工况并了解不同阶段转速对Cr30A铸铁腐蚀-磨损交互作用的影响,选择400,800和1200 r/min 3种转速。实验后,试样在无水乙醇中超声波清洗处理20 min,采用电子天平测量质量损失,用单位面积上的质量损失来表征腐蚀磨损程度,最终数据采用3次实验的平均值。最后,利用扫描电镜 (SEM,SM-6700F) 及自带能谱仪 (EDS) 分析表面组织、形貌以及成分的变化。
2 结果与讨论
2.1 转速对材料腐蚀磨损失重的影响
图2为不同转速对Cr30A高铬铸铁腐蚀磨损失重的影响。可以看出,V及VW均随着转速的增加而增大,转速增加促进了材料的质量损失。当转速为400 r/min时,VW的失重占比 (VW/V) 为43.67%;转速为800 r/min时,VW的失重占比 (VW/V) 为85.46%;当转速为1200 r/min时,VW大于V。
图2 在不同转速条件下由磨损和腐蚀磨损引起的Cr30A铸铁质量损失
由表1中腐蚀磨损实验过程中材料损失各组成部分以及所占比例可以看出,虽然V及VW均随着转速的增加而增大,但是转速的增加对纯磨损促进作用更为明显。随着转速增加,纯磨损占总腐蚀磨损失重之比 (VW/V) 逐渐增大。腐蚀磨损交互作用ΔV则在转速增加的情况下逐渐减小,当转速从400 r/min增加到800 r/min时,腐蚀磨损交互作用量占总腐蚀磨损量之比ΔV/V由48.73%变为10.28%;当转速为1200 r/min时,腐蚀-磨损交互作用量为负数,这说明腐蚀-磨损交互作用抑制了材料的损失,即腐蚀与磨损两者之间是相互抑制的,表现为对抗作用。
2.2 浆液腐蚀与颗粒冲击磨损对材料损伤的交互作用
材料的冲蚀机理主要取决于材料的性质、冲蚀的角度和浆料。含有韧性第二相碳化物和脆性基体的材料具有两种类型的韧性和脆性的冲蚀行为模式[4]。
图3是在转速为400 r/min时Cr30A铸铁在不同介质中的侵蚀表面SEM像。从图3a可以看出,Cr30A铸铁在去离子水中发生纯磨损时,基体产生塑性变形所导致的疲劳磨损和石英砂的冲击导致的磨粒磨损是主要磨损机制。由于材料在受到磨粒冲击时的冲击角不是一成不变的,所以表面出现不同冲击角所造成的坑洞和切削犁沟 (图3a)。在具有腐蚀性石英砂浆液中磨损时,首先由于酸性浆液腐蚀试样表面,使得基体裸露在腐蚀性浆液中;同时由于受到石英砂冲击作用,出现微裂纹。在连续冲击后,微裂纹导致穿晶断裂。同时,碳化物在其周围基体被严重侵蚀后脱落。材料破坏以塑性变形导致的材料脱落和冲蚀磨损为主。冲击区表现为塑性变形区,存在疲劳韧性断裂,但脆性断裂占主导地位。碳化物的脱落主要取决于基体的变形程度,当基体经历大的变形时,存在于表面下方的碳化物将会析出且断裂脱落[8],导致在基体表面形成深坑 (图3b)。碳化物与奥氏体基体间的微裂纹和结合弱化是由于基体发生了明显的塑性变形[9]。当材料中存在高硬度碳化物时,它会赋予材料优异的耐磨性,从而使得材料在受到纯磨损时仅存在少量裂纹。但在腐蚀磨损作用下,材料基体中的奥氏体和珠光体由于较软,容易发生变形,从而导致碳化物析出和断裂,并最终导致材料发生大块脱落,使得材料质量损失明显[10]。
图3 Cr30A铸铁在转速为400 r/min下两种不同浆液中腐蚀磨损后表面的SEM像
图4是Cr30A高铬铸铁在转速为800 r/min时不同介质中的侵蚀表面的SEM像。在去离子水中纯磨损情况下,材料表面呈现整体断裂 (图4a),在高速冲击下,许多晶粒发生脱落导致基体发生大范围变形,从而使金属基质产生结合损失,最后发生大块断裂脱落。在纯磨损环境下,Cr30A铸铁失效机制是以疲劳脆性断裂为主伴随石英砂冲击导致的磨粒磨损。在腐蚀磨损浆料中,腐蚀磨损表面较平整且不存在明显断裂或脱落现象,存在少量凹坑和大量网状裂纹 (图4b)。由图5中EDS分析结果可以看出,表面存在Fe,O,Cr,推测FexOy和CrxOy在表面上形成。这说明当转速为800 r/min时,腐蚀磨损试样表面发生了氧化,从而表面生成了氧化膜。
图4 Cr30A铸铁在转速为800 r/min下两种不同浆液中腐蚀磨损后表面的SEM像
图5 Cr30A高铬铸铁在转速为800 r/min条件下腐蚀磨损后表面EDS分析结果
在腐蚀磨损实验过程中,石英砂随浆料冲击材料表面产生摩擦热,基体的温度由于摩擦热而升高。在低转速下,产生的摩擦热较少且容易散失。随着转速增加,摩擦热增多,促进了摩擦接触区表面的氧化反应,使氧化膜的形成速度增加[11]。而氧化膜的硬度和剪切强度比都比试样高,从而提高了试样承受冲击的能力。因此,冲击磨损成为失效次要因素,材料损失的主要原因是腐蚀磨损。
图6是在转速为1200 r/min时Cr30A铸铁在不同介质中侵蚀后表面的SEM像。在去离子水中纯磨损情况下,表面受侵蚀情况加剧,材料脱落现象更加明显。此外,表面出现小部分氧化层。由图7中EDS分析结果可以看出,表面存在Fe和O,推测转速为1200 r/min时在纯磨损试样表面上形成了Fe的氧化物。但在纯磨损试样表面形成的氧化层结构较为疏散,并且在冲击下出现脱落现象,导致仍有大部分基体裸露出来,因此难以起到保护基体的作用。而在腐蚀磨损情况下,试样表面裂纹明显增多,但氧化膜依然保持较致密稳定的形态,仍然起到了保护基体的作用。在腐蚀磨损过程中,表面上各个区域所受侵蚀效果并不一致,存在受侵蚀最为严重的几个部位,区域之间侵蚀效果不同影响了表面形貌。不同侵蚀区的形成与冲击角和速度直接相关。在腐蚀磨损过程中,由于浆料冲击,表面受侵蚀严重的区域会更容易损失其表面钝化膜。在这种情况下,原电池出现在磨损区域 (阳极) 和未磨损区域 (作为阴极) 之间,钝化膜重新形成。在腐蚀磨损实验中,原电池的形成可能是表面裂纹形成的原因[12]。
图6 Cr30A铸铁在转速为1200 r/min下两种不同浆料中腐蚀磨损实验后表面的SEM像
图7 Cr30A铸铁在转速为1200 r/min条件下纯磨损后表面EDS分析结果
2.3 腐蚀-磨损交互作用
材料同时受到磨损和腐蚀共同作用时,材料的损失不是磨损和腐蚀的简单叠加,还存在腐蚀和磨损之间的交互作用[13]。在腐蚀磨损实验中,当转速为400 r/min时,腐蚀-磨损交互作用占总腐蚀磨损失重比 (ΔV/V) 为48.73%,腐蚀-磨损交互作用明显。当材料受到腐蚀和磨损的协同作用时,腐蚀会加速磨损,反过来磨损也会同时加速腐蚀,导致材料质量损失更为明显[13]。磨损对腐蚀具有明显的促进作用,摩擦和冲击作用使得Cr30A铸铁表面产生严重的破坏塑性变形,裸露出新鲜的金属表面,遭受进一步腐蚀。并且变形区域晶体缺陷密度会急剧增大,由此造成受冲蚀的部位产生了较高的位错密度和腐蚀活性,形成原电池反应,同时浆液的转动作用促进了阴极反应过程,促进了材料的损失[7]。磨损加快了材料的腐蚀,而高铬铸铁韧性较低,材料表面的塑性变形是磨损产生的,导致材料被冲击破碎损耗或断裂失效 (图3b)。亚表层产生的裂纹会沿着碳化物与基体的相界面扩展,裂纹扩展到表面后,腐蚀介质随之渗入,加重了材料的腐蚀并最终导致碳化物剥落从而形成碎片状剥落,促进了磨损的进一步发生。随着转速的增大,腐蚀-磨损交互作用量反而减小,这说明腐蚀-磨损交互作用在较低载荷 (转速) 下尤其明显[7,14]。
在腐蚀磨损系统中,不仅存在腐蚀和磨损之间的协同效应 (腐蚀与磨损相互促进) ,而且在某些情况下也存在对抗效应 (腐蚀和磨损在腐蚀磨损中相互抑制)[15]。在腐蚀磨损实验中,当转速达到400 r/min时,腐蚀-磨损交互作用占总腐蚀磨损失重比 (ΔV/V) 为48.73%;当转速达到800 r/min时,腐蚀磨损试样表面上出现氧化膜 (图4b),腐蚀-磨损交互作用占总腐蚀磨损失重比 (ΔV/V) 降到10.28%[16];当转速为1200 r/min时,V相较于VW更小,腐蚀-磨损交互作用抑制了材料的损失。这说明,在高转速下,腐蚀和磨损在腐蚀磨损过程中存在相互抑制,呈现对抗作用。当转速为800和1200 r/min时,腐蚀磨损试样表面都出现了致密氧化膜 (图4b和6b),为金属基体提供了保护,使得材料损失随保护膜的出现而下降[17]。由于氧化膜的耐腐蚀性,以及良好抗冲击能力,保护膜不易分层,同时具有承载能力,对基体产生了优异的保护而削弱了基体的塑性变形,这可以用来解释为什么磨损与腐蚀之间呈对抗作用[18]。
3 结论
(1) 高铬铸铁Cr30A纯磨损失重和腐蚀磨损失重都随转速增加而增大,腐蚀-磨损交互作用在转速增加的情况下逐渐减小,磨损在侵蚀过程中占主导地位。
(2) Cr30A铸铁在纯磨损状态下,基体塑性变形所导致的断裂、脱落和石英砂的冲击导致的磨粒磨损是主要磨损机制。在存在腐蚀情况下,低转速400 r/min下侵蚀原因是塑性变形导致的疲劳脱落和冲蚀磨损;转速升高达到800和1200 r/min时,材料的损失以腐蚀磨损为主。
(3) 当转速为400 r/min时,腐蚀-磨损交互作用表现为协同作用;当转速为1200 r/min时,腐蚀磨损试样生成致密氧化层,起到了保护基体的作用,腐蚀-磨损交互作用表现为对抗作用。Cr30A铸铁在酸性腐蚀浆料的腐蚀磨损中,腐蚀和磨损的协同和对抗作用共同存在。
参考文献
[1] JingY W, LiuS G. A study on erosion and protective methods of water wall tubes of CFB boilers [J]. J. Power Eng., 2006, 25: 747
[1] (景永伟, 刘少光. 流化床锅炉水冷壁管冲蚀磨损特性及防磨措施 [J]. 动力工程, 2006, 25: 747)
[2] SampathkumaranP, SeetharamuS. Erosion and abrasion characteristics of high manganese chromium irons [J]. Wear, 2005, 259: 70
[3] AnijdanS H M, BahramiA, VarahramN, et al. Effects of tungsten on erosion-corrosion behavior of high chromium white cast iron [J]. Mater. Sci. Eng., 2007, A454/455: 623
[4] Al-BukhaitiM A, AhmedS M, BadranF M F, et al. Effect of impingement angle on slurry erosion behaviour and mechanisms of 1017 steel and high-chromium white cast iron [J]. Wear, 2007, 262: 1187
[5] TianH H, AddieG R, VisintainerR J. Erosion-corrosion performance of high-Cr cast iron alloys in flowing liquid-solid slurries [J]. Wear, 2009, 267: 2039
[6] TangX H, ChungR, PangC J, et al. Microstructure of high (45wt%) chromium cast irons and their resistances to wear and corrosion [J]. Wear, 2011, 271: 1426
[7] ChenJ, ZhangQ A, ZhangQ, et al. Sliding wear-corrosion performance of AISI 316 stainless steel against alumina in artificial seawater [J]. J. Chin. Soc. Corros. Prot., 2014, 34: 433
[7] (陈君, 李全安, 张清等. AISI 316不锈钢腐蚀磨损交互作用的研究 [J]. 中国腐蚀与防护学报, 2014, 34: 433)
[8] YoganandhJ, NatarajanS, Kumaresh BabuS P. Erosive wear behavior of high-alloy cast iron and duplex stainless steel under mining conditions [J]. J. Mater. Eng. Perform., 2015, 24: 3588
[9] CoronadoJ J, SinatoraA. Abrasive wear study of white cast iron with different solidification rates [J]. Wear, 2009, 267: 2116
[10] AlbertinE, SinatoraA. Effect of carbide fraction and matrix microstructure on the wear of cast iron balls tested in a laboratory ball mill [J]. Wear, 2001, 250: 492
[11] QiuM, ZhangY Z, YangJ H, et al. Effects of friction heat on tribological properties of Ti6Al4V alloy sliding against GCr15 steel [J]. Tribology, 2006, 26: 203
[11] (邱明, 张永振, 杨建恒等. 摩擦热对Ti6Al4V合金摩擦磨损性能的影响 [J]. 摩擦学学报, 2006, 26: 203)
[12] BateniM R, SzpunarJ A, WangX, et al. Wear and corrosion wear of medium carbon steel and 304 stainless steel [J]. Wear, 2006, 260: 116
[13] ChenJ, ZhangQ, LiQ A, et al. Corrosion and tribocorrosion behaviors of AISI 316 Stainless steel and Ti6Al4V alloys in artificial seawater [J]. Trans. Nonferrous Met. Soc. China, 2014, 24: 1022
[14] BiH Y, LiS Z, JiangX X. The Effect of deformation strengthening on wear resistance of stainless steel in dry sliding and corrosive environment [J]. Tribology, 1998, 18: 327
[14] (毕红运, 李诗卓, 姜晓霞. 不锈钢腐蚀磨损过程中形变强化能力的研究 [J]. 摩擦学学报, 1998, 18: 327)
[15] ZhangL M, DongM C, LvJ J. Tribo-corrosion map of K4169 alloy in artificial seawater [J]. Tribology, 2016, 36: 636
[15] (张丽敏, 董沫辰, 吕晋军. K4169合金在人工海水中的腐蚀磨损图 [J]. 摩擦学学报, 2016, 36: 636)
[16] TaoY Q, LiuG, LiY S, et al. Corrosion wear properties of 2024 Al-alloy in artificial seawater [J]. J. Chin. Soc. Corros. Prot., 2016, 36: 587
[16] (陶永奇, 刘刚, 黎业生等. 海水环境下2024铝合金腐蚀磨损性能研究 [J]. 中国腐蚀与防护学报, 2016, 36: 587)
[17] ZhaoX P, ZhuC W, YeG L, et al. Experimental study on fly ash erosive wear of carbon steel 20# in corrosive gas environment [J]. J. Chin. Soc. Power Eng., 2015, 35: 944
[17] (赵宪萍, 朱崇武, 叶桂林等. 20碳钢在腐蚀性气流环境中飞灰冲蚀磨损试验研究 [J]. 动力工程学报, 2015, 35: 944)
[18] LiX X, ZhouY, CaoH, et al. Wear behavior and mechanism of H13 steel in different environmental media [J]. J. Mater. Eng. Perform., 2016, 25: 4134
免责声明:本网站所转载的文字、图片与视频资料版权归原创作者所有,如果涉及侵权,请第一时间联系本网删除。
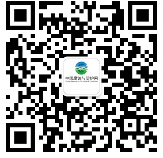
官方微信
《中国腐蚀与防护网电子期刊》征订启事
- 投稿联系:编辑部
- 电话:010-62316606-806
- 邮箱:fsfhzy666@163.com
- 中国腐蚀与防护网官方QQ群:140808414