[摘要] 对碳纤维增强复合材料(CFRP)粘接接头在极限温度下的耐久性进行了研究。分析CFRP表面粗糙度对粘接性能的影响,并制作了AL-AL和CFRP-AL单搭接接头,分别测试80和-40℃环境下不同老化周期后的接头失效载荷。结果表明:砂纸打磨能有效提升CFRP粘接效果。但随着粗糙度进一步增加,CFRP-AL接头承载能力逐渐降低;在高温下,AL-Al接头性能由胶粘剂后固化决定,而CFRP-AL接头高温耐久性受到胶粘剂后固化和CFRP老化的共同影响;低温老化对AL-Al接头性能无明显影响,而CFRP-AL接头失效载荷在热应力的影响下出现下降。最后建立了CFRP-AL接头内聚力模型,定义了温度退化因子,实现极限温度持续作用下的接头失效预测。
关键词:碳纤维增强复合材料;粘接接头;极限温度;耐久性;内聚力模型
前言
轻量化技术是实现汽车节能减排的有效措施之一。汽车轻量化途径主要包括新材料应用、结构优化设计和新工艺,其中又以新材料应用最为有效[1]。碳纤维增强复合材料(carbon fiber reinforced polymer,CFRP)具有高比强度、高比模量、耐腐蚀和抗疲劳性能良好等优点,能够在保证整车性能的同时实现轻量化,在汽车产业中的应用日益广泛[2]。传统的连接技术如铆接、焊接等往往存在应力集中和材料损伤等问题,不能完全满足CFRP连接的需要,这严重制约了CFRP的进一步应用。粘接作为一种新型的结构连接技术,具有密封性好、应力分布均匀、抗疲劳和耐腐蚀等优点,能够在不破坏零件结构的同时保证一定粘接强度,实现异种材料连接,在CFRP连接中起到越来越重要的作用[3]。
汽车在实际服役过程中,往往须经受严寒和暴晒等恶劣条件,环境温度范围一般为-40~80℃。在持续极限温度作用下,胶粘剂属性会发生改变,从而影响粘接结构性能,同时由于胶粘剂和基材热膨胀系数不同而产生的热应力效应可能会导致结构损伤[4]。对于CFRP,碳纤维和树脂基底同样存在较大的热膨胀系数差异,且树脂基底在温度载荷下也会发生老化,造成粘接结构力学性能下降[5-6]。因此针对极限温度下的粘接接头耐久性进行研究,获得性能变化规律和内在机理,并在此基础上提出有效的失效预测方法具有十分重要的意义。
针对环境温度作用下的粘接接头耐久性能,国内外学者展开了相关研究。韩啸等[7]基于响应面法研究了经历不同极限温度环境后,采用不同属性胶粘剂制作的钢-铝单搭接胶接接头的强度退化现象。在此基础上进一步对循环温度场作用下的接头剩余强度进行了试验测试和仿真预测[8]。Zhang等[9]选用电镀钢、铝合金为粘接基材,研究了同种、异种材料单搭接接头在80℃持续作用下的耐久性能,发现在高温老化作用下接头强度均出现下降,且异种材料粘接接头耐久性由相对较弱的胶粘剂-基材界面所决定。Wu等[10]对80℃环境下作用14天后的铝合金单搭接接头静态、疲劳性能进行测试,结果表明,高温老化后接头准静态强度和低周疲劳强度明显下降而高周疲劳强度几乎没有变化。Akderya等[11]采用环氧树脂基底复合材料制作单搭接接头,并在-18和70℃环境下暴露一周进行拉伸试验,发现高低温持续作用均造成接头失效载荷的下降。
现有的粘接接头高低温耐久性研究通常针对传统金属材料粘接基材,而CFRP与金属材料之间存在明显的差异,而且CFRP自身的老化也会对接头性能产生影响。本文中研究CFRP表面粗糙度对接头失效载荷的影响,并确定了最佳粘接方案。在此基础上,对铝合金-铝合金/CFRP-铝合金(AL-AL/CFRP-AL)单搭接接头进行-40和80℃环境下0(未老化)、5、10、15、20和 25天的老化试验,研究失效载荷随老化周期的变化规律,并通过宏观观察与扫描电子显微镜(SEM)微观观察分析接头失效形式。基于双线性内聚力单元建立接头仿真模型,并引入温度退化因子,结合试验测试获得初始失效准则,对持续极限温度作用下的接头失效载荷进行预测。
试验过程
1.1 材料选择
粘接基材为车体结构中常见的6061铝合金和CFRP板材。CFRP板材由斜纹、单向预浸料加工而成,其整体厚度为2 mm,铺层顺序为[(0/90)/0/90/0/90/0/90/(0/90)];选用双组份环氧树脂胶粘剂Araldite?2015(亨斯迈先进材料有限公司),它具有较高的粘接强度并适用于复合材料粘接,广泛应用于汽车工业。胶粘剂和CFRP主要材料参数如表1和表2所示。依据标准GB/T 228—2002《金属材料室温拉伸试验方法》制作铝合金拉伸试样,并进行准静态拉伸试验,获得铝合金真实应力-应变曲线如图1所示,铝合金材料参数如表3所示。
表1 Araldite2015材料参数
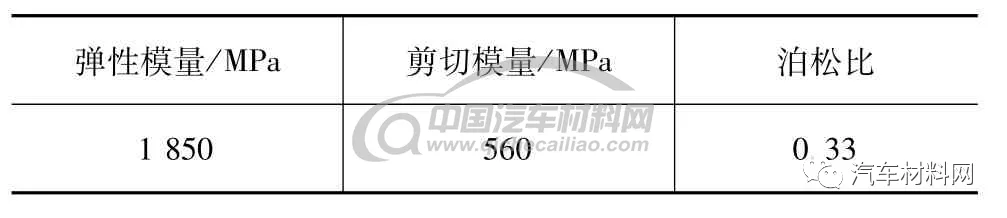
表2 CFRP材料参数
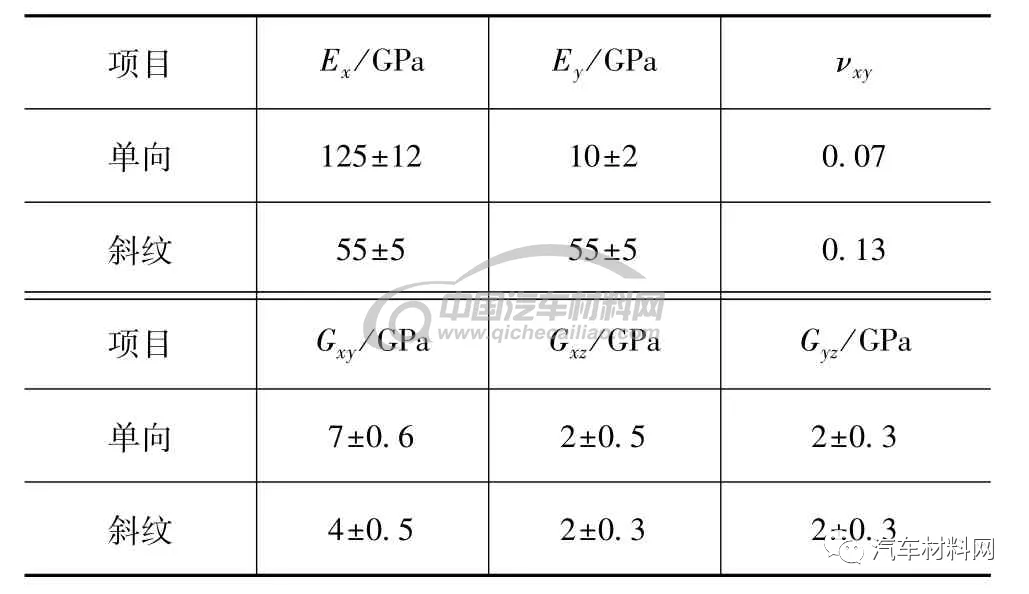
注:E为弹性模量;G为剪切模量;ν为泊松比。
表3 铝合金材料参数

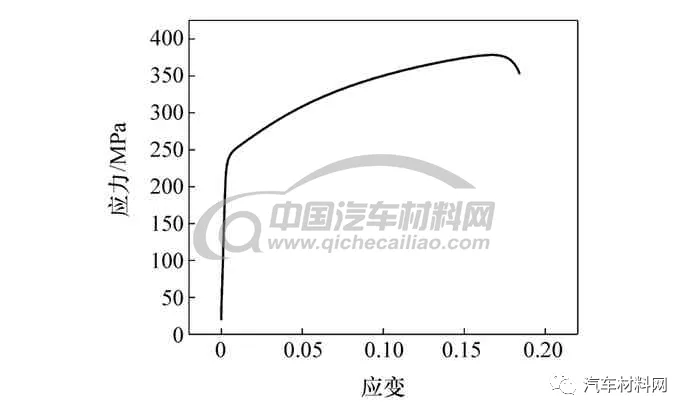
图1铝合金应力 应变曲线
1.2 接头制作
参考标准ISO4587—2003设计制作了AL-AL和CFRP-AL单搭接接头,接头尺寸示意图如图2所示。其中搭接长度和宽度均为25 mm,胶层厚度为0.2 mm。

图2 单搭接粘接接头尺寸示意图(mm)
在试验环境(温度保持在25±3℃,相对湿度保持在50±5%)条件下,完成所有试件的粘接。参考标准GB/T 7124—2008对粘接基材进行表面预处理,其中铝合金表面采用#80氧化铝喷砂处理(空气压力0.5 MPa,喷砂时间10 s)。考虑到喷砂容易造成CFRP损伤,因此使用砂纸对其进行轻微打磨。采用丙酮对喷砂后铝合金和打磨后CFRP板进行去脂和清洁。待试件干燥后进行施胶,并利用设计的专用夹具完成粘接。粘接夹具如图3所示,夹具表面粘贴特氟龙胶带以防止残留胶粘剂固化后难以清理。胶层厚度由垫片进行控制。粘接完成后接头在常温下放置24 h,然后进行2 h的80℃高温固化,并在试验环境中保持24 h。为提高试验数据一致性,在完全固化之前切除粘接区域附近余胶。
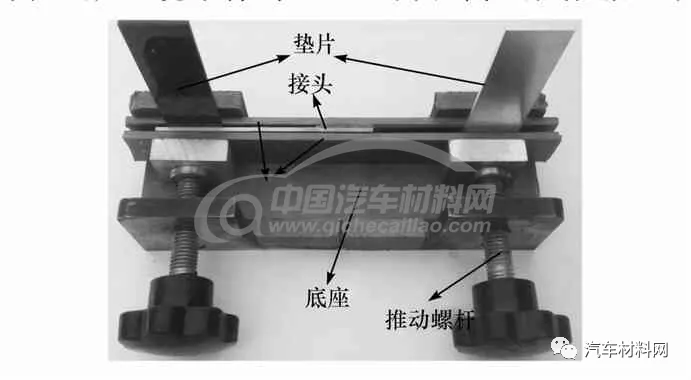
图3 粘接夹具
1.3 试验方案
为研究CFRP表面粗糙度对粘接性能的影响,获得较好的 CFRP-AL粘接效果,分别采用#80、#240、#360、#600和#800砂纸对 CFRP表面进行打磨,然后采用OLS3000型激光共聚焦显微镜测试表面粗糙度。针对每个测试表面,选取5个位置进行重复测试,获得平均表面粗糙度R a。按照接头制作流程完成试件粘接和固化,通过准静态拉伸试验测试失效载荷,每种粗糙度测试5个试件。
根据粗糙度测试结果,选取失效载荷最大的前处理方案制作粘接接头。将固化好的粘接接头均匀放置于高低温湿热环境箱(WEISS实验设备有限公司)中,分别设置环境温度为80和-40℃,进行0、5、10、15、20和25天的老化试验。老化试验结束后将试件再置于试验环境中,直到恢复常温,然后进行准静态拉伸试验,每组试验至少重复3次。
使用WDW3100微机控制电子万能试验机(长春科新试验仪器有限公司)对AL-AL和CFRP-AL单搭接粘接接头进行准静态拉伸,试验机拉伸速度为1 mm/min。试件夹持端放置2 mm厚的垫片,以消除拉伸试验过程中弯曲应力的影响。拉伸过程试验载荷由万能试验机记录。考虑到试验过程中拉伸机夹持机构的变形对试件位移采集存在一定影响,采用基于三维数字图像相关技术的非接触全场应变测量系统测取接头粘接区域真实变形。准静态拉伸试验现场如图4所示。
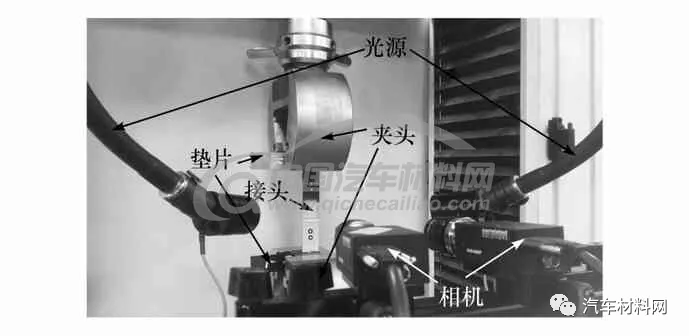
图4 准静态拉伸试验现场
试验结果与分析
2.1 CFRP表面粗糙度对失效载荷的影响
CFRP板材表面光滑且有可能附着脱模剂,因此采用砂纸对其表面进行打磨处理,然后再粘接。未经表面处理和采用不同目数砂纸打磨后的CFRP-AL粘接接头表面粗糙度Ra如表4所示。
表4 CFRP表面粗糙度
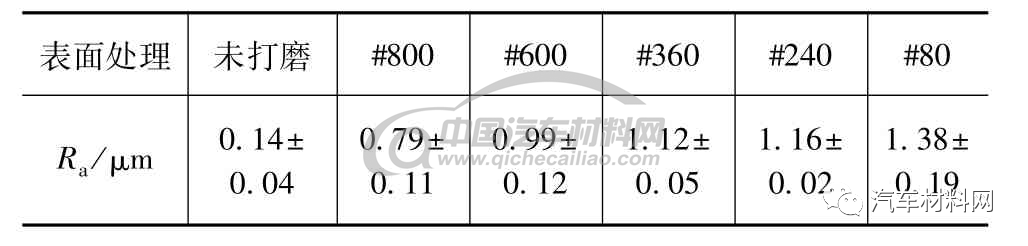
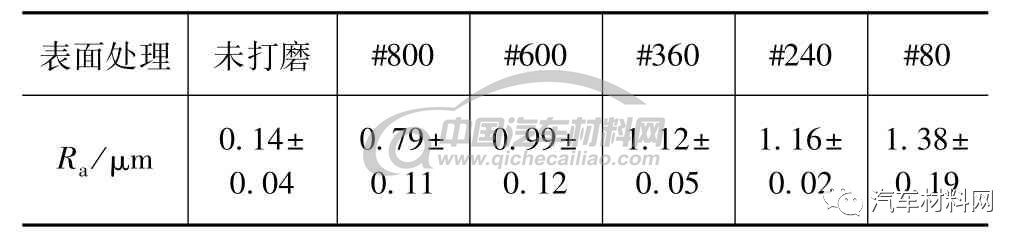
由表4可知,未打磨的CFRP表面粗糙度最小,打磨后随着砂纸目数的减少,CFRP表面粗糙度逐渐增加。采用不同粗糙度CFRP制作的粘接接头的失效载荷如图5所示。由图可知,未打磨的CFRP,表面十分光滑,不利于胶粘剂粘附,因而粘接失效载荷相对较低(3 597 N),且其破坏断面呈现明显的界面失效,如图6(a)所示,未能实现有效粘接;而打磨后的接头,即使用#800砂纸打磨,其表面粗糙度也骤然得到显著提升而得以和胶粘剂有效粘附,不再产生界面失效,而断面的失效则呈现为胶粘剂内聚破坏,打磨后失效断面如图6(b)所示。
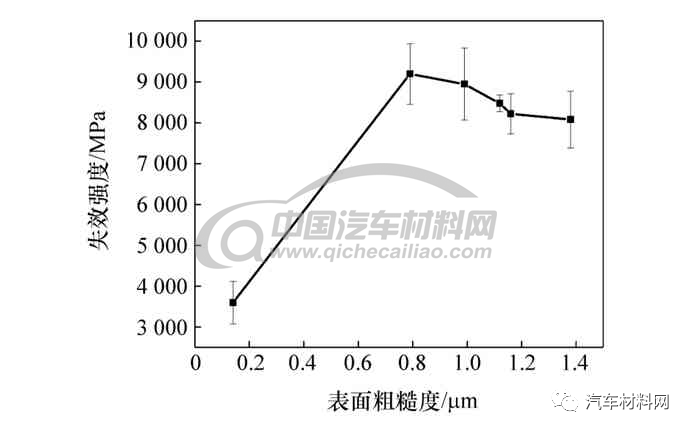
图5 不同粗糙度CFRP-AL接头失效载荷
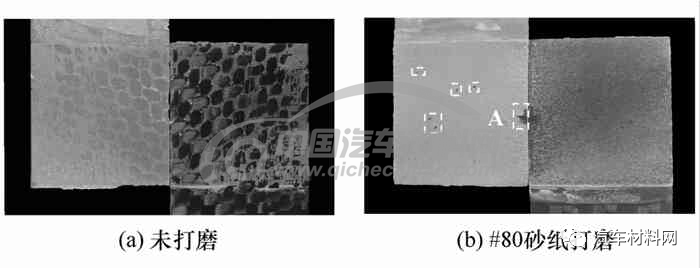
图6 未打磨和#80砂纸打磨接头失效断面
对于CFRP打磨后的粘接接头,随着表面粗糙度的增加,其失效载荷逐渐下降,即在测试范围内(0.79-1.38μm),CFRP表面越粗糙,接头承载能力越低。当采用#800砂纸打磨时,获得最大失效载荷,为9 198.5 N。采用#600砂纸时,失效载荷相比最大值减少了2.71%,下降幅度相对较小。而采用#360砂纸时接头失效载荷出现明显下降,为7.83%,采用#240和#80砂纸打磨时接头失效载荷分别下降了10.62%和12.16%,下降速度有所减缓。随着粗糙度的增加,胶粘剂不能有效地浸润粘接表面,容易造成粘接胶层不连续,从而降低接头承载能力[12]。
基于SEM对打磨后CFRP表面进行微观观察,如图7所示。#80砂纸打磨后CFRP表面存在明显的划痕,造成较为严重的局部纤维断裂,如图7(a)中矩形虚线框所示,#240和#360砂纸打磨后也出现了一定程度的纤维损伤,而使用#600和#800砂纸打磨后CFRP表面相对平整,没有较大的划痕,其中#600砂纸打磨后观察到轻微纤维损伤,而#800砂纸打磨表面基本上没有纤维受损。对采用#80砂纸打磨后的CFRP-AL接头失效断面宏观观察可以发现,虽然失效形式为内聚破坏,但断面上存在局部纤维撕裂,如图6(b)中矩形虚线框所示,即采用粗糙砂纸打磨容易损伤纤维,破坏CFRP表面完整性,导致接头失效载荷下降[13]。由于以上原因,本文中高低温耐久性试验CFRP均采用#800砂纸打磨。

图7 打磨后CFRP表面典型SEM形貌
2.2 持续高温下接头耐久性分析
对高温老化后接头失效载荷进行统计分析,获得接头耐久性规律,如图8所示。在80℃环境持续作用下,CFRP-AL和AL-AL粘接接头平均失效载荷发生了较为明显的改变。随着老化周期的增加,CFRP-AL接头失效载荷总体呈现上升趋势,相比于初始失效载荷,5、10、15和20天高温老化后CFRPAL接头失效载荷分别上升了6.11%、10.61%、14.24%和15.62%,上升速度逐渐变慢,而在25天时出现了轻微下降(相比20天下降0.98%)。在高温老化环境下,AL-AL粘接接头失效载荷持续上升,相比初始载荷,5、10、15、20和25天后上升幅度分别为4.64%、7.69%、10.31%、12.73%和13.74%,初始老化5天时上升速度最快,之后逐渐减慢。
为进一步揭示接头失效机理,对高温老化前后AL-AL/CFRP-AL接头失效断面进行分析。老化前后AL-AL粘接接头断面没有发生明显变化,均表现为内聚失效。考虑到本文中选取的胶粘剂玻璃转化温度T g为67℃[14],在80℃条件下处于高弹态,缓解了由于胶粘剂和基材热膨胀系数不同所导致的热应力作用,因此老化后AL-AL接头性能变化由胶粘剂性质决定。在持续高温条件下,胶粘剂发生后固化,使粘接接头承载能力提升,而随着老化周期的增加,胶粘剂逐渐接近完全固化,反应速度降低,接头失效载荷增加速度相应减缓[15]。
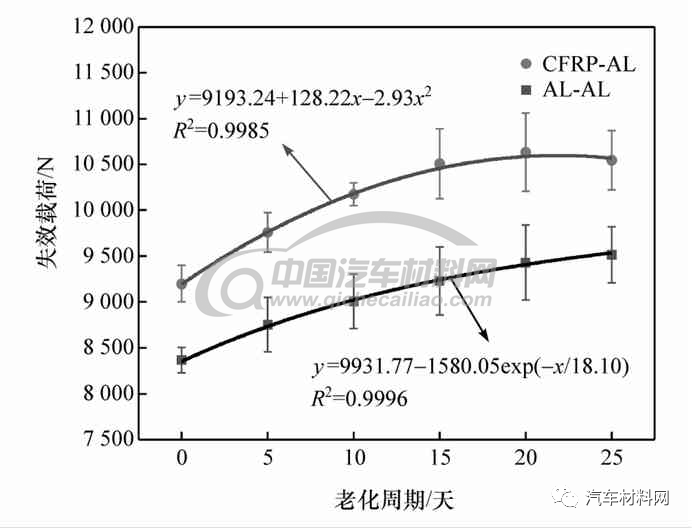
图8 高温下粘接接头失效载荷随老化周期的变化规律

图9 高温老化CFRP-AL接头失效表面典型宏观形貌
对于CFRP-AL接头,其典型失效断面如图9所示。未老化和老化5天后CFRP-AL接头发生内聚失效,而10天后出现CFRP局部纤维撕裂(如图9中矩形框所示),且随着老化时间的增加,撕裂面积有所增大。对图6中A区域和图9中B区域进行SEM微观观察,结果如图10所示。由图可见,在高温环境下,由于纤维与树脂基体热膨胀系数的差异而导致的热应力会引起CFRP老化。与未老化CFRP相比,高温老化25天后碳纤维更加光滑,附着的树脂基体明显减少,纤维 基体界面出现损伤[16]。因此,CFRP-AL粘接接头高温耐久性受到胶粘剂后固化与CFRP老化的共同影响。
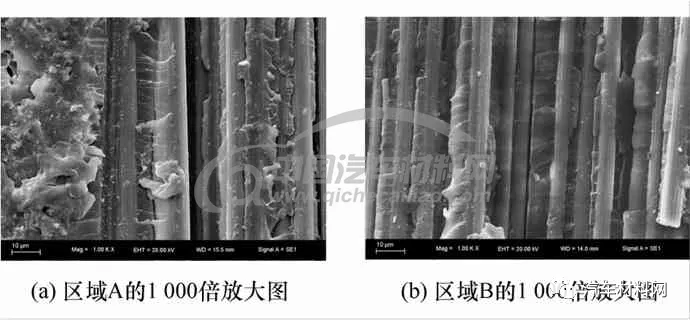
图10 高温老化CFRP-AL接头失效表面典型SEM形貌
根据接头失效载荷随老化周期的变化规律,分别选取二次多项式和指数函数对试验数据进行拟合,并选取拟合优度R2相对较高的作为理想函数。拟合曲线和拟合优度R2如图8所示。
2.3 持续低温下接头耐久性分析
在低温环境下,CFRP-AL和AL-AL粘接接头耐久性呈现不同的变化规律,如图11所示。由图可见,低温老化对AL-AL接头影响不明显,接头失效载荷几乎没有发生改变(变化幅度不超过4%)。而CFRP-AL粘接接头失效载荷则随老化周期的延长而持续降低,相比于未老化接头失效载荷,5、10、15、20和25天后分别下降5.47%、6.30%、8.26%、8.87%和9.57%,但下降幅度逐渐减小。
分别采用指数函数和二次多项式对失效载荷数据进行拟合,并对比拟合精度。AL-AL接头更符合二次多项式而CFRP-AL接头更符合指数函数,拟合曲线和拟合优度R2如图11所示。
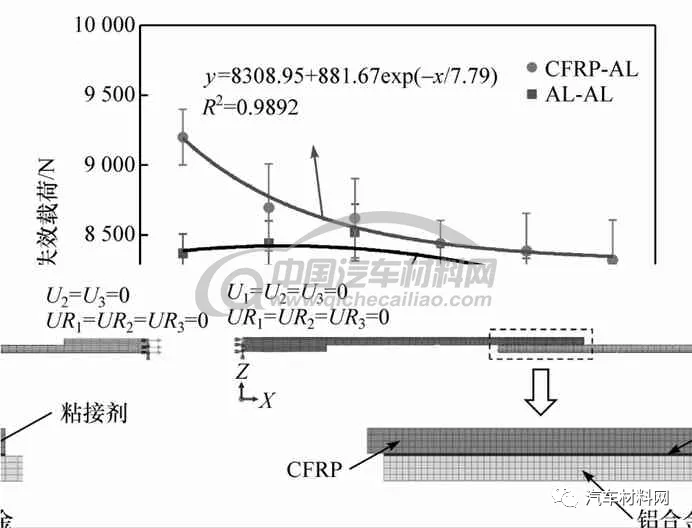
图11 低温下粘接接头失效载荷随老化周期的变化规律
与高温老化类似,低温老化后AL-AL接头失效形式未发生改变,仍表现为内聚破坏。在低温环境下,胶粘剂后固化反应不明显。同时对于同种材料粘接,由于胶粘剂和粘接基材热膨胀系数不同所导致的热应力对接头性能影响有限[17],因此AL-AL接头失效载荷也未发生明显改变,相比于初始载荷,25天后下降3.58%。
CFRP-AL接头在低温老化后失效形式没有发生改变,仍为内聚失效,而接头承载能力持续下降。在长期低温作用下CFRP也会发生老化,但考虑到并未发生纤维撕裂,失效形式主要为内聚破坏,说明由基体、胶粘剂热膨胀系数不同所产生的热应力造成的粘接剂性能下降影响更加显著。因此低温环境下CFRP-AL接头性能退化主要由粘接接头热应力引起的粘接胶层退化导致。
数值模拟
3.1 数值模拟方法
为模拟粘接接头在极限温度环境下发生老化后的失效过程,实现接头失效载荷预测,采用ABAQUS?软件建立CFRP-AL粘接接头三维有限元模型,进行数值模拟分析。
所建立的接头模型如图12所示,其中胶层采用内聚单元(COH3D8),CFRP采用连续壳单元(SC8R),铝合金采用3D应力单元(C3D8R)。各部分建模所采用的单元均为六面体网格。对粘接区域局部网格进行了细化,如图12中放大图所示。在分析过程中考虑了几何非线性,接头的左侧截面采用固定约束,右侧截面施加水平位移,并约束其他方向的自由度。
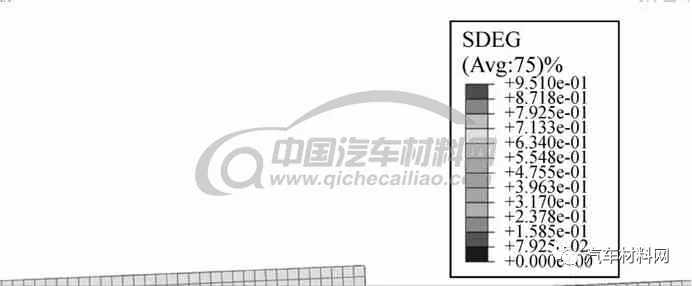
图12 CFRP-AL单搭接接头有限元模型
本文中胶层内聚力模型基于双线性牵引力 位移法则,包含的关键参数有初始刚度、临界牵引力和断裂能[18]。在进行有限元仿真时,须提供合适的初始失效准则。选取初始失效准则为二次应力准则,其广泛应用于粘接结构的失效预测[19],即

式中:tn、ts、tt分别为材料法向和两个切向应力图片图片分别代表法向和切向临界牵引力。
为获得更加准确的临界牵引力参数值,采用文献[20]中的方法测试CFRP-AL粘接接头拉伸和剪切失效强度(对应法向、剪切临界牵引力),结果如表5所示。
表5 胶层内聚力模型参数
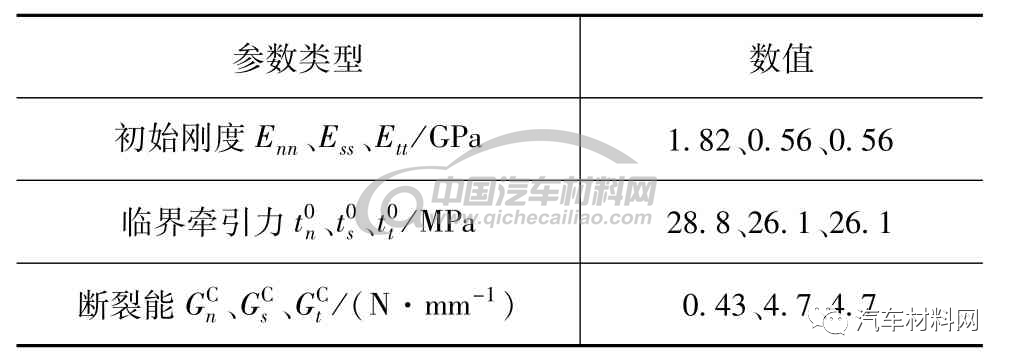
破坏扩展阶段采用能量法则控制,即

式中:Gn、Gs、Gt分别表示由法向和两个切向牵引力做功所释放的能量;图片表示对应方向的断裂能。
为预测极限温度老化后CFRP-AL单搭接接头失效行为,分别定义高温、低温退化因子D80和D-40,其计算公式为

式中:S D为不同老化周期后的接头平均失效载荷;S F为未老化接头平均失效载荷。
将图8和图11中接头失效载荷拟合公式代入式(3),获得任意周期后的高、低温退化因子函数为

假设持续极限温度作用后胶粘剂内聚力模型各参数随退化因子等幅度变化[8,18]。通过将原始参数与退化因子相乘,获得退化后参数,并重新进行数值模拟,实现极限温度老化后的接头失效预测。
3.2 仿真结果分析
未老化CFRP-AL单搭接接头失效过程如图13所示,图中采用ABAQUS软件中所提供的内聚力单元刚度退化标量(scalar stiffness degradation variable,SDEG)来表示材料的失效程度。SDEG为0时表示胶层没有失效,发生初始失效后SDEG逐渐增大,等于1时胶层完全失效。由图可知,胶层首先在铝合金端部发生失效,然后由两端向胶层内部扩展,直至完全断裂。

图13 CFRP-AL单搭接接头失效过程仿真结果
胶层完全失效后,提取仿真失效载荷和粘接区域铝合金端部X和Z向变形,并与试验测试结果进行对比,结果如表6所示。试验与仿真X向位移误差相对较大,但模型具有一定有效性。
表6 试验与仿真结果对比
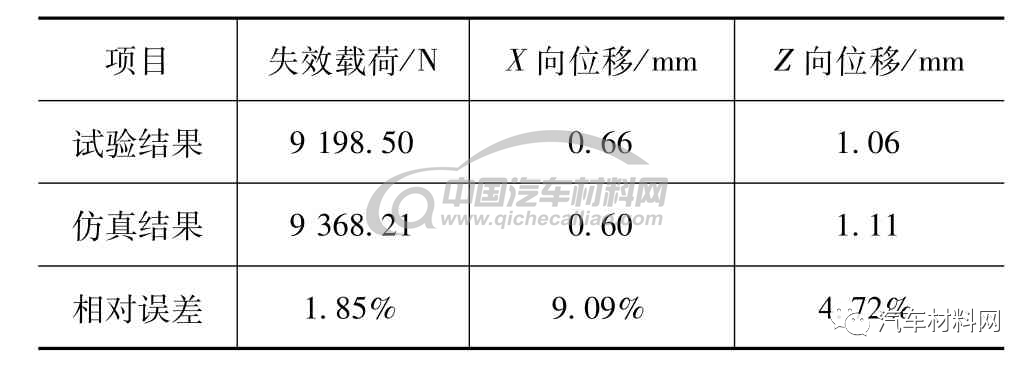
高低温环境下不同老化时间后的试验和仿真失效载荷如图14所示。仿真结果与试验数据相比最大误差为6.9%,这表明本文中采用的数值预测模型具有一定精度,能够实现持续极限温度作用下的接头失效预测。

图14 CFRP-AL接头试验与仿真失效载荷对比
结论
(1)采用砂纸打磨CFRP粘接表面能够有效提高CFRP-AL单搭接接头失效载荷。针对所试验砂纸型号,随着砂纸目数的增加,CFRP表面粗糙度减小,纤维损伤减少,粘接失效载荷逐渐增大。
(2)在持续高温环境下,随着老化时间的增加,接头失效载荷基本上呈上升趋势,其中AL-AL接头性能变化由胶粘剂后固化导致,而CFRP-AL接头高温耐久性能受到胶粘剂后固化和CFRP老化的共同影响。老化前后AL-AL接头均为内聚失效,未老化和老化5天后CFRP-AL接头表现为内聚失效,老化10天后出现局部纤维撕裂,且随着老化时间的增加,撕裂面积有所增大。两种接头失效载荷变化规律分别符合指数函数和二次多项式函数。
(3)在低温环境下,AL-AL接头失效载荷与失效形式均未发生变化。而在热应力作用下,胶层性能退化,CFRP-AL接头失效载荷随着老化周期的增加逐渐下降,不同老化周期后均为内聚失效。ALAL/CFRP-AL接头失效载荷变化规律分别符合二次多项式函数和指数函数。
(4)基于内聚力模型建立CFRP-AL单搭接接头有限元仿真模型,并通过拉伸、剪切试验测取初始失效准则参数。引入环境退化因子,对持续极限温度作用下的接头失效行为进行模拟。通过与试验结果进行对比,证明数值模型能够有效预测高低温老化后的CFRP-AL单搭接接头失效载荷。
免责声明:本网站所转载的文字、图片与视频资料版权归原创作者所有,如果涉及侵权,请第一时间联系本网删除。
相关文章
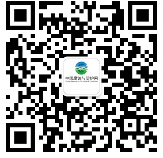
官方微信
《中国腐蚀与防护网电子期刊》征订启事
- 投稿联系:编辑部
- 电话:010-62316606-806
- 邮箱:fsfhzy666@163.com
- 中国腐蚀与防护网官方QQ群:140808414
点击排行
PPT新闻
“海洋金属”——钛合金在舰船的
点击数:7130
腐蚀与“海上丝绸之路”
点击数:5741