摘要
采用激光重熔对高锰铝青铜进行表面处理,并通过显微组织观察、电化学测试和超声振动空蚀等实验,研究激光重熔对铸态高锰铝青铜微观组织、腐蚀和空蚀行为的影响。结果表明,重熔后合金组织明显细化,且晶粒分布均匀,硬度相对于铸态合金提高了约45%。电化学实验结果表明,重熔处理合金与铸态合金的电极反应过程相似,但铸态合金的腐蚀电位较低,腐蚀倾向较大。空蚀实验结果表明,在3.5%NaCl溶液中空蚀5 h后,重熔处理合金的失重率仅为铸态合金的3/5。空蚀形貌观察结果表明,重熔处理合金表面损伤较轻且分布较均匀,表面粗糙度明显小于铸态合金。铸态和激光重熔合金的纯空蚀作用引起的失重占空蚀总失重比例分别为71.1%和50.8%,即力学冲击是造成空蚀损伤的主导因素。
关键词: 高锰铝青铜 ; 激光重熔 ; 腐蚀 ; 空蚀 ; 交互作用
海洋中物质资源极其丰富,随着海洋经济的发展和对海洋资源的开发,越来越多的大型设备需要建设并应用在海洋环境中。螺旋桨是重要的船舶动力装置,船舶不断向着高速化大型化发展,对螺旋桨材料的性能要求也就越来越高。但是海洋环境是极为苛刻且较难控制的腐蚀环境[1],除了静态电化学腐蚀外,螺旋桨与海水高速的相对运动会使螺旋桨表面面临空泡腐蚀[2-4],而空蚀和腐蚀的交互作用也会使螺旋桨材料表面破坏越来越严重,使螺旋桨的效率大大降低。
高锰铝青铜 (MAB) 由于强度高,耐海水及大气腐蚀,铸造性能优良,被广泛用于制造大型船用螺旋桨,且用量仅次于常见的螺旋桨材料镍铝青铜。MAB是在Cu-Al合金中加入Mn、Fe、Ni等合金元素发展而来的[5]。铸态MAB合金在室温下的显微组织是复杂的,包含α相、β相和粗大的金属间化合物κ相。MAB铸件存在成分偏析、晶粒粗大、内部含有疏松和应力集中等诸多缺陷[6],在海洋环境中还要接触大量海生物[7],这些都使其耐海水腐蚀性能面临挑战,从而出现点蚀、空蚀、冲刷腐蚀、腐蚀疲劳等问题,而这些都会造成螺旋桨使用寿命大幅下降。对MAB铸件进行有效的表面改性处理是提高其腐蚀及空蚀性能的关键。
激光表面改性技术是通过高能激光束作用在金属表面以达到改善金属表面组织和性能的目的[8]。与传统工艺相比,激光表面改性技术可以在提高材料表面性能的同时保持基体金属原有的组织和性能。如激光表面重熔 (LSM) 可以在不添加任何金属元素的情况下达到减少或者消除铸件组织存在的铸造缺陷、改善材料成分偏析、细化晶粒等目的。这是因为能量集中的激光束可以使材料表面快速熔化形成熔池,同时又可快速冷却获得均匀致密的非平衡组织[9]。本文采用LSM对铸态MAB进行表面处理,并通过显微组织和形貌观察及硬度、电化学、空蚀失重测试等,分析LSM对铸态MAB在3.5% (质量分数) NaCl溶液的腐蚀和空蚀行为的影响机制。
1 实验方法
实验用材料为铸态MAB,其化学成分 (质量分数,%) 为:Al 7.28,Ni 2.10,Fe 3.62,Mn 12.35,其余为Cu。对尺寸为300 mm×100 mm×6 mm的试样进行LSM处理,激光功率5 kW,光斑直径为1 mm,扫描速度60 mm/min,氩气流量12 L/min。相邻两个激光焊道之间具有50%的搭接率。
采用5 g FeCl3+2 mL HCl+95 mL C2H5OH溶液对铸态MAB和LSM MAB试样进行蚀刻后,采用光学显微镜对显微组织进行观察。
采用维氏显微硬度计对原始铸态及LSM后试样的表面硬度进行测试,载荷为200 g,持续时间为10 s。测试点不少于10个,以保证准确性。
空蚀实验依据ASTM G32标准进行。本次实验的工作参数为振幅60 μm,振动频率20 kHz,超声振动探头置于试样正上方距离0.5 mm的位置。所用的腐蚀介质为蒸馏水和分析纯NaCl试剂配制的3.5%NaCl溶液。将试样浸入液体介质中,试样表面距液面15 mm。每种材料测试时应选择3个平行试样,确保实验结果的可重复性。采用JEOL ISM-6480扫描电镜 (SEM) 观察试样表面空蚀形貌。
采用Gamry 1000E电化学工作站进行电化学测试,采用三电极体系,工作电极为铸态MAB及LSM MAB,辅助电极为铂片,参比电极为饱和甘汞电极。在静态或者空蚀条件下,首先将试样浸泡在腐蚀介质中30 min以获得稳定的开路电位,然后进行极化曲线测试。极化曲线测试时,起始电位为相对于开路电位-0.25 V,电位扫描速率是0.5 mV/s。每次测试至少要有3个平行试样,确保试验结果的可靠性。采用Cview软件对极化曲线结果进行拟合。
2 结果和讨论
2.1 显微组织及硬度分析
铸态及LSM MAB的微观组织如图1所示。图1a为整体截面图,在激光功率5 kW,扫描速度60 mm/min的参数下进行LSM处理后,得到的重熔层深度近190 μm。从LSM MAB表面到基体的区域包括激光重熔区和过渡区。图1b所示为基体微观组织,由α相、β相和κ相组成,各相尺寸都相对较粗大。重熔区晶粒为均匀细小的单相β,如图1c所示,铸造过程引起的成分不均匀现象消失。高能量激光使材料表面重熔区快速熔化,由于保护气体的冷却以及铜合金基体的优良导热作用,使得熔池的冷却速度很快,原铸态组织中的α和κ相来不及析出,因此可获得单一细小的β相组织。图1d所示的过渡区组织中包含晶粒较粗大α相和κ相,该区域内受到激光加热的作用较弱,使该区域熔化不完全,一些粗大的κ相保留下来,一些重熔后的组织由于没有保护气体的冷却作用,在冷却的过程中冷速较慢,析出了α相。
图1 铸态及LSM MAB的显微组织
对LSM MAB和铸态MAB进行维氏硬度测试,结果表明,基体的显微硬度平均值约为176 HV,LSM处理后重熔区的显微硬度平均值为256 HV,较基体提高了约45%。与铸态MAB相比,LSM处理使得晶粒细化。根据Hall-Petch公式,晶粒尺寸变小,显微硬度变大。
2.2 空蚀失重结果与分析
铸态及LSM MAB在蒸馏水及3.5%NaCl溶液中的空蚀失重量-时间曲线及失重率-时间曲线如图2所示。在蒸馏水中空蚀5 h后,LSM MAB的失重率约0.6300 mg·cm-2·h-1,孕育期大约为2 h;而铸态MAB的失重率则达到了1.4500 mg·cm-2·h-1,约为LSM MAB的2.3倍,孕育期约为1 h。在3.5%NaCl溶液中,铸态MAB的孕育期较短,约为0.5 h,失重率在短时间内快速增长;而LSM MAB的失重率呈缓慢增长趋势,孕育期约1 h。空蚀5 h后,铸态MAB的失重率为2.0389 mg·cm-2·h-1,而LSM MAB的失重率仅有1.2400 mg·cm-2·h-1,为铸态试样的3/5。可见,LSM处理使铸态MAB的抗空蚀性能提高了约1.64倍,这得益了LSM后MAB表面硬度的提高和组织的均匀化。此外,铸态和LSM MAB在3.5%NaCl溶液中的失重率均高于在蒸馏水中的结果,这是由于腐蚀和空蚀之间存在交互作用。
图2 铸态和LSM MAB在蒸馏水和3.5%NaCl溶液中的空蚀失重量-时间曲线及空蚀失重率-时间曲线
2.3 空蚀-腐蚀交互作用分析
在腐蚀介质中,空蚀与腐蚀之间存在交互作用,且两者交互作用所带来的破坏比单独作用的加和要大得多。材料的空蚀损伤包含纯空蚀损伤、纯腐蚀损伤和腐蚀-空蚀交互作用损伤。腐蚀和空蚀的交互作用可用以下公式表示[10]:
式中,T为累积质量损失,即在3.5%NaCl溶液中的空蚀累积质量损失;E为静态条件下,即蒸馏水中的纯空蚀质量损失;C为静态条件下的纯腐蚀质量损失;S为空蚀和腐蚀交互作用引起的质量损失,包括由腐蚀增强的空蚀损伤?E和由空蚀增强的腐蚀损伤?C。两者可以通过以下公式计算得到:
式中,C‘为空蚀条件下的腐蚀质量损失。C和C’可由下式确定:
其中,A是金属的原子量,这里主要考虑Cu基体,因此A=64 g·mol-1;n为金属的原子价,即阳极反应方程式中的电子数,取+1价;F为Faraday常数,取值为96500 C·mol-1;Icorr和I'corr分别为静态和空蚀条件下的腐蚀电流密度 (A·cm-2),可通过电化学测试得到。
图3为铸态及LSM MAB在3.5%NaCl溶液中静态和空蚀条件下测得的极化曲线。铸态和LSM MAB在3.5%NaCl溶液中静态和空蚀条件下的腐蚀电位、腐蚀电流密度和腐蚀速率结果如表1所示。在静态条件下,两种试样的阴极和阳极过程都是类似的,阴极反应均为氧还原过程:O2+2H2O+4e-→4OH-[11,12]。LSM并没有改变材料的化学成分,因此阳极过程没有被改变,主要是Cu的溶解:Cu+2Cl-→CuCl2-+e-[11,12]。
图3 静态和空蚀条件下铸态及LSM MAB在3.5%NaCl溶液中的极化曲线
表1 铸态和LSM MAB在3.5%NaCl溶液中静态和空蚀条件下的电化学参数
铸态和LSM MAB的静态腐蚀电位分别为-446和-318 mV,可见铸态试样的腐蚀倾向较大。在空蚀条件下,铸态和LSM MAB的腐蚀电位分别为-348和-293 mV。可见,空蚀会使腐蚀电位正移。空蚀作用一方面破坏材料表面腐蚀产物膜;另一方面会加速传质过程,前者使电位降低,后者使电位升高,如果材料表面没有形成保护性的腐蚀产物膜,那么后者占主导作用,就会出现空蚀使电位正移的结果[13-15]。铸态和LSM MAB的腐蚀电流密度在静态时分别为2.9472×10-6和3.2265×10-6 A·cm-2。与静态相比,空蚀状态下的电流密度更大,铸态和LSM MAB的腐蚀电流密度分别是3.5123×10-5和5.9900×10-5 A·cm-2。可以看出,在静态和空蚀条件下,铸态和LSM MAB的腐蚀电流都比较接近,这是由于在3.5%NaCl溶液中,阴极过程主要是氧还原反应,材料的腐蚀速率受氧扩散控制。在空蚀条件下,氧的扩散被加速,因此腐蚀电流密度高于静态下的结果。
结合公式 (1~4),可计算得到不同分量造成的空蚀失重,见表2所示。图4为铸态及LSM MAB在3.5%NaCl溶液中空蚀5 h后各分量引起的失重占总失重的比例结果。铸态和LSM MAB的空蚀总失重T比纯空蚀E和纯腐蚀C失重的加和要大,即空蚀与腐蚀之间存在正的交互作用,共同促进材料表面损伤。在铸态MAB的空蚀失重中,纯空蚀损伤所占比例最大,达71.1%,在LSM MAB的空蚀总失重中,纯空蚀损伤所占比例也达到了50.8%,这一结果说明空蚀过程中产生的力学冲击是使铸态和LSM MAB发生空蚀破坏的主导因素。在铸态和LSM MAB的交互作用导致的失重中,?E占比均大于?C,即腐蚀促进空蚀的占比大些。这是由于腐蚀可以粗化材料表面,恶化力学性能,加速空蚀破坏。
表2 铸态及LSM MAB的空蚀-腐蚀交互作用分析
图4 铸态及LSM MAB的腐蚀-空蚀交互作用各分量占空蚀总失重的比例
2.4 空蚀损伤形貌分析
铸态和LSM MAB在3.5%NaCl溶液中空蚀不同时间后的表面形貌如图5所示。空蚀1 h后,在铸态MAB的α/β相界处以及κ相周围出现裂纹,这是由于各相成分结构不同[16],对空蚀应力的响应不同,因此优先在相界处萌生裂纹,裂纹扩展后引起κ相脱落,形成空蚀坑,如图5a所示。另外,较软的α相上已经有较小尺寸的空蚀坑出现,硬度较高的β相损伤较轻。空蚀3 h后,铸态MAB的α相发生严重塑性变形,原始组织已不能辨认,β相发生解理断裂,表面粗糙度明显增加,空蚀坑呈现蜂窝状形貌,见图5c所示。空蚀5 h后,空蚀坑尺寸变大,空蚀损伤程度加重,见图5e所示。由于LSM MAB内是单一的β相组织,且硬度相对于铸态MAB明显提高,因此,在空蚀应力下,无大颗粒相的脱落和铸态组织中粗大β相的解理断裂,其表面空蚀损伤程度较轻且均匀,见图5b,d和f所示,空蚀5 h后,表面才出现尺寸较小的空蚀坑 (图5f)。从空蚀形貌上来看,LSM MAB表现出明显优异的耐空蚀性能。
图5 铸态及LSM MAB在3.5%NaCl溶液中空蚀不同时间后的表面形貌图
3 结论
(1) 经LSM处理后的MAB重熔区组织明显得到细化,且为单一的β相组织。与铸态MAB相比,LSM处理使基体硬度提高了约45%。
(2) 空蚀相同时间后,LSM MAB的空蚀损伤较小。在3.5%NaCl溶液中空蚀5 h后,LSM MAB的失重率仅为铸态的3/5,即LSM处理使铸态MAB的抗空蚀性能提高了约1.64倍。
(3) 在3.5%NaCl溶液中,铸态和LSM MAB的阴极和阳极过程都是类似的,但铸态MAB的电位较低,腐蚀倾向较大。在静态和空蚀条件下,铸态和LSM MAB的电流密度都比较接近,这是由于静态和空蚀条件下的阴极过程都是氧还原反应。在空蚀条件下,氧的扩散被加速,因此腐蚀电流密度高于静态条件下的结果。
(4) 在3.5%NaCl溶液中,腐蚀和空蚀交互作用使材料破坏更加严重。对铸态和LSM MAB,力学损伤是空蚀破坏的主导因素。在交互作用导致的失重中,?E占空蚀总失重的比例要大于?C,即腐蚀促进空蚀所引起的损伤更显著。
(5) 空蚀损伤形貌观察结果表明,铸态MAB在空蚀应力下出现κ相的脱落和β相的解理断裂;与铸态相比,LSM MAB的表面损伤较轻且分布较均匀。LSM处理提高了铸态MAB的表面硬度,并使组织明显细化,因此耐空蚀性能显著提高。
参考文献
1 Li K, Zhai X F, Guan F, et al. Progress on materials and protection technologies for marine propeller [J]. J. Chin. Soc. Corros. Prot., 2017, 37: 495
1 李科, 翟晓凡, 管方等. 船用螺旋桨防护技术及其材料研究进展 [J]. 中国腐蚀与防护学报, 2017, 37: 495
2 Lin C, Yang Y, Zhao X B. Research methods and research progress for cavitation corrosion of passive metals [J]. Corros. Prot., 2018, 39: 369
2 林翠, 杨颖, 赵晓斌. 钝态金属的空蚀研究方法和研究进展 [J]. 腐蚀与防护, 2018, 39: 369
3 Tomlinson W J, Talks M G. Erosion and corrosion of cast iron under cavitation conditions [J]. Tribol. Int., 1991, 24: 67
4 Sakamoto A, Funaki H, Matsumura M. Influence of galvanic macro-cell corrosion on the cavitation erosion durability assessment of metallic materials—International cavitation erosion test of Gdańsk [J]. Wear, 1995, 186-187: 542
5 Zhu Y Y. Factors affecting the mechanical properties of marine propeller materials [J]. Spec. Cast. Nonferrous Alloys, 1989, (1): 31
5 朱友元. 影响船用螺旋桨材料机械性能的因素 [J]. 特种铸造及有色合金, 1989, (1): 31
6 He C L, Fu X Y, Chen H Z, et al. Corrosion resistance of laser-clad copper-based alloy on high manganese aluminum bronze surface [J]. J. Shenyang Univ. (Nat. Sci.), 2019, 31: 87
6 贺春林, 付馨莹, 陈宏志等. 高锰铝青铜表面激光熔覆铜基合金的耐蚀性能 [J]. 沈阳大学学报 (自然科学版), 2019, 31: 87
7 Wang Y, Wu J J, Zhang D. Research progress on corrosion of metal materials caused by dissimilatory iron-reducing bacteria in seawater [J]. J. Chin. Soc. Corros. Prot., 2020, 40: 389
7 王玉, 吴佳佳, 张盾. 海水环境中异化铁还原菌所致金属材料腐蚀的研究进展 [J]. 中国腐蚀与防护学报, 2020, 40: 389
8 Chen X M, Wang H J, Zhou X L, et al. Laser surface modification technology and its research progress [J]. Mater. Rev., 2018, 32(S1): 341
8 陈小明, 王海金, 周夏凉等. 激光表面改性技术及其研究进展 [J]. 材料导报, 2018, 32(S1): 341
9 Fu A Q, Zhao M F, Li C Z, et al. Effect of laser surface melting on microstructure and performance of super 13Cr stainless steel [J]. J. Chin. Soc. Corros. Prot., 2019, 39: 446
9 付安庆, 赵密锋, 李成政等. 激光表面熔凝对超级13Cr不锈钢组织与性能的影响研究 [J]. 中国腐蚀与防护学报, 2019, 39: 446
10 Wood R J K. Marine wear and tribocorrosion [J]. Wear, 2017, 376-377: 893
11 Wharton J A, Stokes K R. The influence of nickel-aluminium bronze microstructure and crevice solution on the initiation of crevice corrosion [J]. Electrochim. Acta, 2008, 53: 2463
12 Kear G, Barker B D, Walsh F C. Electrochemical corrosion of unalloyed copper in chloride media-a critical review [J]. Corros. Sci., 2004, 46: 109
13 Dong L F. Cavitation erosion behavior of ZQMn12-8-3-2 manganese aliuminium bronze in 2.4%NaCl solution [J]. Corros. Sci. Prot. Technol., 2011, 23: 485
13 (董立峰. ZQMn12-8-3-2高锰铝青铜在2.4%NaCl溶液中的空蚀行为 [J]. 腐蚀科学与防护技术, 2011, 23: 485
14 Ding G Q, Li X Y, Zhang B, et al. Variation of free corrosion potential of several metallic materials in natural seawater [J]. J. Chin. Soc. Corros. Prot., 2019, 39: 543
14 丁国清, 李向阳, 张波等. 金属材料在天然海水中的腐蚀电位及其变化规律 [J]. 中国腐蚀与防护学报, 2019, 39: 543
15 Zheng Y G, Luo S Z, Ke W. Effect of passivity on electrochemical corrosion behavior of alloys during cavitation in aqueous solutions [J]. Wear, 2007, 262: 1308
16 Iqbal J, Hasan F, Ahmad F. Characterization of phases in an as-cast copper-manganese-aluminum alloy [J]. J. Mater. Sci. Technol., 2006, 22: 779
免责声明:本网站所转载的文字、图片与视频资料版权归原创作者所有,如果涉及侵权,请第一时间联系本网删除。
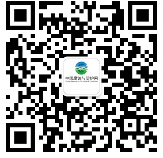
官方微信
《中国腐蚀与防护网电子期刊》征订启事
- 投稿联系:编辑部
- 电话:010-62316606-806
- 邮箱:fsfhzy666@163.com
- 中国腐蚀与防护网官方QQ群:140808414