摘要
利用XRD、SEM和TEM等测试方法研究了淬火-配分-回火 (Q-P-T) 钢热处理后的物相结构和显微组织形貌,并以相同成分的淬火-回火 (Q&T) 钢和不含碳化物的淬火-配分 (Q&P) 钢为参照,利用失重法、电化学测试等方法研究了Q-P-T钢在模拟海水环境3.5% (质量分数) NaCl溶液中的腐蚀行为。结果表明,Q&T钢内的残余奥氏体主要以薄膜状分布在马氏体板条间,其含量低于3% (体积分数),而Q&P钢和Q-P-T钢内的残余奥氏体则以薄片状分布在马氏体板条间,其平均含量分别为15.35% (体积分数) 和14.6% (体积分数);含碳化物的Q-P-T钢的耐蚀性优于不含碳化物的Q&P钢,且经配分的Q-P-T和Q&P钢的耐蚀性能稍优于Q&T钢。4种钢表面腐蚀产物的演变规律基本一致,即初期腐蚀产物以β-FeOOH和γ-FeOOH为主,随浸泡时间的延长,逐渐以α-FeOOH和Fe3O4为主;4种试样腐蚀表面初期均分布着尺寸不一的点蚀坑,随浸泡时间的延长,逐渐变为均匀腐蚀。
关键词: 淬火-配分-回火钢; 残余奥氏体; 碳化物; 海水腐蚀; 电化学
淬火-配分-回火 (Q-P-T) 工艺是徐祖耀院士[1]在淬火-配分 (Q&P) 工艺[2]的基础上提出的一种新型热处理工艺。Q&P热处理工艺将含有奥氏体相的Fe-Mn-Si-C系列钢淬火至马氏体相变开始温度 (Ms) 和马氏体相变结束温度 (Mf) 之间的某一淬火温度 (QT),以形成部分马氏体,同时保留部分未发生马氏体相变的残余奥氏体[3,4]。再在计算好的配分温度 (PT) 下保温一段时间,使碳从过饱和马氏体中配分至残余奥氏体中,从而提高了残余奥氏体在室温下的稳定性,最后获得贫碳马氏体基体和富碳残余奥氏体的复相组织[5]。Q-P-T工艺弥补了Q&P工艺在沉淀强化效应方面的缺陷,在其内可加入Nb、V和Ti等合金元素,使碳在配分的同时,碳化物能够在马氏体基体上析出,从而进一步提高钢的强度。由于合金碳化物的沉淀强化作用,使得Q-P-T钢的综合力学性能较Q&P钢更好。
长期在海洋环境中服役的金属材料,容易受到海水的腐蚀,从而使得服役寿命大大降低。Q-P-T钢作为新型的先进高强度钢,现研究大多集中在其力学性能、氢脆机制等方面,而对其耐蚀性能特别是海洋腐蚀方面的研究报道却很少,仅有寥寥文献涉及到Q&P钢腐蚀方面的研究。如Lu等[6]认为在3.5% (质量分数) NaCl溶液中经Q&P处理的马氏体不锈钢 (Fe-0.28C-0.60Mn-0.35Si-13.0Cr) 的耐蚀性要优于Q&T处理的试样。但是,该合金在配分时将析出大量含Cr碳化物,影响配分结果,特别是不能区分残余奥氏体和碳化物对试样腐蚀行为的影响。此外,该合金为典型马氏体不锈钢,本身的抗腐蚀能力与主要含Mn (1.5%~2.0%,质量分数) 和Si (>1.0%,质量分数) 为合金元素的Q&P钢不在一个档次,对各种环境的腐蚀敏感性也与Q&P钢存在差异,故获得的结果不能用于解释Q&P钢的腐蚀机制。故此,杨继兰等[7]采用传统Q&T热处理试样作为参照,研究了中碳 (Fe-1.5Mn-1.5Si-0.4C) Q&P钢在3.5% (质量分数) NaCl溶液中的腐蚀性能。深入研究发现,富碳残余奥氏体的存在不仅能降低试样表面的残余应力,使得应力腐蚀的风险降低,而且能提高马氏体基体的腐蚀电位,使其作为阳极优先发生腐蚀,进一步保护了马氏体基体。虽然Q&P试样表面也存在严重的点蚀行为,但腐蚀产物内更多致密的α-FeOOH和Fe3O4相能阻碍Cl-的渗透和对腐蚀产物膜的攻击,这些因素的共同作用使得Q&P试样具有优于Q&T试样的抗腐蚀能力。
本文根据徐祖耀院士提出的高强度Q-P-T钢的组织和成分设计思想,在廉价Fe-C-Mn-Si钢的基础上添加微量V元素,设计81#和82#两种钢,以不含残余奥氏体的Q&T钢和不含碳化物的Q&P钢作为参照,研究了Q-P-T钢在模拟海水环境3.5% (质量分数) NaCl溶液下的腐蚀行为,评估碳化物对其腐蚀性能的影响,为该类钢在海洋环境下的应用提供一定的理论指导。
1 实验方法
1.1 实验材料
本文所用钢的具体化学成分和相应的相变特征温度如下表1所示。Fe-0.41C-1.56Mn-1.54Si和Fe-0.42C-1.57Si-1.55Mn-0.16V分别定义为81#和82#钢。添加Si是为了有效抑制脆性渗碳体 (Fe3C) 的析出[8],Mn能有效提高材料的淬透性和降低Ms点[9],V不但可以细化原奥氏体晶粒,并且能在回火过程中析出弥散分布的碳化物,产生沉淀强化效果[1]。实验钢材的相变特征温度,如奥氏体转变开始温度 (Ac1)、奥氏体转变结束温度 (Ac3)、马氏体相变开始温度 (Ms)、马氏体相变结束温度 (Mf) 等利用Gleeble 3500热模拟试验机通过热膨胀法测得,也一并列入表1。
表1 实验钢材的化学成分和相应的相变特征温度
实验原材料由北京钢铁研究总院提供,在高温熔炼炉中熔炼后经1200 ℃热轧成20 mm的厚板后空冷,获得原始金相组织为铁素体和珠光体的组织。
依据上述表1中钢的特征温度分别进行Q&T、Q&P和Q-P-T热处理工艺,获得相应的试样:将81#和82#钢样品在空气炉中经880 ℃奥氏体化保温600 s后,水淬至室温,随后在420 ℃的盐浴炉中回火120 s,后再次水淬至室温,分别标记为81-Q&T、82-Q&T;将81#钢样品在空气炉中经880 ℃奥氏体化保温600 s后,在245 ℃的盐浴炉中淬火60 s,随后在420 ℃的盐浴炉中等温120 s,最后水淬至室温,标记为81-Q&P;将82#钢样品在空气炉中经880 ℃奥氏体化保温600 s后,在245 ℃的盐浴炉中淬火60 s,随后在420 ℃的盐浴炉中等温120 s,最后水淬至室温,标记为82-QPT。其中,淬火温度 (245 ℃) 和时间 (60 s) 的选取原则为:依据限制性碳配分 (CCE) 热力学模型计算,尽可能多地获得奥氏体含量,并保证实验用钢完全淬透。配分回火温度 (420 ℃) 和时间 (120 s) 选取原则为:保证碳能充分配分到奥氏体中且析出相能弥散析出,同时避免回火脆性。
1.2 显微组织观察
在不同热处理工艺的试样上截取10 mm×10 mm的样品,经机械研磨并抛光后,采用4% (体积分数) 的硝酸酒精溶液腐蚀,然后使用扫描电镜 (SEM,LYRA3 TESCAN) 观察试样的显微组织。从试样经线切割切取约0.3 mm厚的薄片,经金相砂纸磨至60~80 μm,用冲孔器将试样冲成直径为3 mm的圆片,继续用砂纸减薄至40~50 μm,然后在离子减薄仪 (Leica EM RES 102) 上用5% (体积分数) 高氯酸酒精溶液在-20 ℃环境下双喷减薄,将薄区合格的样品置于透射电镜 (TEM,JEOL JSM-2100F) 上进行观察,操作电压200 kV。
1.3 XRD分析
线切割切取10 mm×10 mm尺寸的样品,经不同道次的砂纸机械研磨并抛光制备后在X射线衍射仪 (XRD, D/Max-2550/PC) 上进行分析,采用旋转铜靶,设置管电压和管电流分别为35 kV和20 mA,扫描角度为35~105 °,扫描速度为2 °/min。采用直接对比法计算试样内残余奥氏体的含量。选取奥氏体的 (200)γ、(220)γ、(311)γ峰和马氏体的 (200)α、(211)α峰进行组合配对,取平均值后,利用下式计算获得残余奥氏体的体积分数[10]:
式中,fγ表示残余奥氏体的体积分数,Iγ和Iα分别为残余奥氏体峰和马氏体峰的衍射积分强度,Area%,Cγ和Cα分别为对应的强度因子。
另外,为了克服XRD方法测量物相含量的下限限制,并精确计算试样内残余奥氏体的含量,利用综合物性测量系统 (PPMS-9T) 测试待测样和标样饱和磁化强度的比值来计算fγ。切取2 mm×2 mm×2 mm尺寸的样品,设置外加磁场强度为0~5 T,步长为0.25 T。将待测试样的饱和磁化强度值和不含残余奥氏体标样 (本文以相同奥氏体化温度处理的退火试样作标准) 的饱和磁化强度值进行对比,根据下式计算出fγ[11]:
其中,Ms(c)为待测试样的饱和磁化强度值,A·m-1,Ms(f) 为不含残余奥氏体标样的饱和磁化强度值,A·m-1,β=0.987。
依照JB-T 7901-1999标准进行腐蚀性能测试,截取尺寸为30 mm×15 mm×2 mm的试样,依次经过180目、320目、800目、1200目砂纸打磨,待试样表面无明显刻痕和麻点后,用无水乙醇清洗并用冷风吹干,干燥24 h后称取样品的初始重量 (m0,g)。然后采用挂片法浸入到盛有3.5%NaCl的溶液中,设定实验时间为8个周期,每个周期为7 d且每个周期更换一次NaCl溶液。根据实验周期设定,将所浸泡试样从溶液中取出后立即进行SEM观察,参照GB/T 16545-1996对试样表面剩余的腐蚀产物进行进一步的清除[12]。所使用的除锈剂为500 mL盐酸、500 mL去离子水和6 g六次甲基四胺的混合溶液。除锈完成后,用无水乙醇对试样进行超声清洗,冷风吹干并将其放入真空干燥器中,保存24 h之后再次称量腐蚀后试样的重量 (m1,g),根据m0-m1计算相应的失重量 (Δm,g),并根据公式 (3) 计算出试样的腐蚀速率。另外,采用SEM再次观察清除腐蚀产物后试样的表面形貌。
式中,V为腐蚀速率,mm·a-1;K为常数87600;m0和m1分别为腐蚀前后清洗干燥的试样重量,g;S为试样表面积,cm2;T为实验时间,h;ρ为样品密度,取7.85 g·cm-3。
1.4 电化学实验
切取尺寸为10 mm×10 mm×2 mm的试样用于电化学测试,将一根有绝缘层的铜线用电烙铁锡焊在试样的非工作面 (宽面) 上,用环氧树脂将除工作面外的其余表面封装起来。对工作面依次经过360目、800目、1200目砂纸打磨,待样品表面呈现平整光滑的状态后,最后依次用去离子水和无水乙醇进行清洗脱水干燥。
电化学实验利用瑞士万通Autolab PGSTAT 302N电化学工作站进行。实验采用三电极体系,工作电极为试样,辅助电极为铂片,参比电极为饱和甘汞电极 (SCE)。在室温下3.5%NaCl溶液中进行测试。为确保测试电位的稳定,测试前需将试样在电解液中浸泡10 min,之后在自腐蚀电位下进行电化学阻抗测试。选用信号为10 mV幅值,测试频率范围为105~10-1 Hz的交流正弦波进行电化学阻抗谱的测量。极化扫描区间为-2.0~2.0 V,扫描速率为1 mV/s。依次进行开路电位测试、电化学阻抗谱测试和极化曲线测试。
2 结果及讨论
2.1 显微组织的分析
图1是4种试样原始显微组织的SEM形貌。可以看到,4种试样的显微组织几乎均由板条马氏体组成,但由于82#钢中存在V,使得其马氏体领域相对81#钢的有所细化。另外,还可发现81-Q&P和82-QPT试样的板条马氏体间夹杂着少量块状的残余奥氏体。
图1 腐蚀前81-Q&T, 81-Q&P, 82-Q&T和82-QPT试样的SEM形貌
由图2a中可以看到,81-Q&T和82-Q&T试样只有马氏体的衍射峰,而81-Q&P钢以及82-QPT钢中则存在明显的残余奥氏体的衍射峰,根据式 (1),可计算出81-Q&P钢中残余奥氏体的含量约为15.1% (体积分数),82-QPT钢中残余奥氏体含量约为14.4% (体积分数)。
图 2 4种试样的XRD分析和饱和磁化曲线图
将相同奥氏体化温度的退火试样作为无奥氏体的标样,通过对比图2b中的饱和磁化强度值,根据公式 (2) 可计算出,81-Q&P和82-QPT试样内残余奥氏体的含量分别约为15.6%和14.8%,这一结果与XRD计算得到的结果相近。
由图3a,d和g可以看出3种试样主要由板条马氏体组成,采用g=111γ操作矢量得到残余奥氏体的中心暗场像 (图3b和e),采用g=200VC操作矢量得到82-QPT试样中碳化钒颗粒的中心暗场像 (图3h)。可以看出,81-Q&T钢中残余奥氏体的含量很少,呈薄膜状,大约只有几个纳米的厚度 (图3b);而81-Q&P钢中的残余奥氏体则以薄片状的形式存在,厚度大约为几十个纳米 (图3e)。从82-QPT钢中则可以看出,在马氏体基体上弥散分布着很多纳米碳化钒颗粒 (图3h)。另外,从选区电子衍射图 (图3c和f) 可以看出,81-Q&T和81-Q&P试样中的马氏体基体和残余奥氏体之间具有Nishiyama-Wassermann ([011]γ∥[001]α,(111)γ∥(110)α) 位向关系;图3i则显示马氏体基体和碳化钒颗粒之间存在Baker-Nutting ([001]VC//[001]α,(110)VC//(010)α) 的位向关系。
图 3 81-Q&T,81-Q&P和82-QPT试样的TEM像及相应的选区电子衍射花样
2.2 失重曲线的分析
图4为4种试样在3.5%NaCl溶液中浸泡不同时间的腐蚀失重情况。从失重变化图4a可以看出,4种试样腐蚀失重量的变化趋势基本相同,在腐蚀最初的100 h内,失重量上升比较明显,在400 h后,失重量上升逐渐趋向平稳。从腐蚀速率变化图4b可以看出,腐蚀速率在腐蚀前期上升很快,在200 h附近达到峰值,之后腐蚀速率在一定范围内波动直至趋向平稳。从腐蚀失重曲线的形状上大致可以判断腐蚀的机制:首先在浸泡初期,试样表面天然存在的保护膜可以有效阻止试样被腐蚀,但是一旦保护膜被破坏,失重量则会迅速上升;腐蚀一段时间后,试样表面堆积了很多腐蚀产物,溶液中的Cl-向试样表面的渗透一定程度上被减缓,从而抑制了腐蚀的进行,故试样失重量的增长速度减缓,腐蚀速率逐渐降低直至稳定。另外,还可观察到4种钢在800 h附近时出现腐蚀速率先降低后又增加到某一极大值的现象,此腐蚀行为被称为“逆现象”,常见于服役环境为海水的碳钢,是样品表面腐蚀产物的保护作用和溶液中Cl-对表面的侵蚀作用相竞争造成的结果[13]。整体来看,81#钢种的耐腐蚀性要低于82#钢种;从热处理的工艺上看,经碳配分处理的钢耐腐蚀性要优于Q&T处理的钢,即81-Q&P钢的耐腐蚀性能明显优于81-Q&T钢,但82-QPT钢相较于82-Q&T钢则领先的不是特别明显。
图4 4种试样在3.5%NaCl溶液中的腐蚀失重和腐蚀速率随浸泡时间的变化
2.3 电化学曲线
图5是4种试样在3.5%NaCl溶液下测得的极化曲线,可以看出,4种试样的极化曲线基本符合典型金属电极在中性溶液中的极化曲线。图中81-Q&T钢试样的极化曲线,阴极极化曲线和阳极极化曲线相交于a点,a点横坐标则对应于试样的自腐蚀电位Ecorr。阴极极化曲线位于a点左侧,对应电化学反应为O2+2H2O+4e→4OH-。阳极极化曲线位于a点右侧,对应的电化学反应为Fe-2e→Fe2+,即以Fe的阳极溶解为主。可以看出,4种试样的阳极极化曲线均由三部分组成,分别为Fe的活性阳极溶解区间 (ab)、钝化区间 (bc) 和过钝化区间 (cd)。
图5 4种试样在3.5%NaCl溶液中的极化曲线
为了获取相关腐蚀动力学信息,如自腐蚀电位Ecorr(V)、自腐蚀电流密度Icorr (μA·cm-2)、阴极/阳极Tafel斜率βc/βa (mV·dec-1)、击穿电位Ed(mV)、致钝电位Eb(mV)、维钝电流密度Ip (μA·cm-2) 等,选取极化曲线的Tafel区间进行数据拟合,将拟合结果列于表2中。可以看出,相对于81-Q&T (82-Q&T) 钢,81-Q&P (82-QPT) 钢的自腐蚀电位稍负,较易发生腐蚀,但其自腐蚀电流密度Icorr却较低,说明发生腐蚀后的腐蚀速率较低。除82-Q&T外,其他3种试样的维钝区间接近。另外还可看出,81-Q&P (82-QPT) 试样的维钝电流密度远低于81-Q&T (82-Q&T) 试样,试样表面的钝化膜更稳定,其耐腐蚀性能更好。
表2 4种试样在3.5%NaCl溶液中的极化曲线拟合参数
图6a为4种试样在3.5%NaCl溶液中的Nyquist图。可以看出,4种试样的EIS特征非常相似,都为不完整的半圆弧。一般来说,圆弧半径越大,试样的电子交换阻抗值越大,其抵抗腐蚀反应的阻力越大,耐腐蚀性能力就越好。从图6b和c可以看出,相同浸泡时间内81-Q&P (82-QPT) 相对于81-Q&T (82-Q&T) 试样具有较大的峰值,表明其具有较好的耐腐蚀性。
图6 4种试样在3.5%NaCl溶液中的电化学阻抗谱
利用电化学分析软件ZView 2中的Equivalent Circuits模块对4种试样的EIS图进行等效电路拟合,采用几种电路模型拟合后,发现最适合实验结果的等效电路图如图7所示,拟合结果列于表3。其中ZCPE为伪双层电容器,代表外部多孔膜,RS为电解液电阻,RP为电子交换电阻。考虑到电容元件的非理想状态,引入了常相位角元件CPE,并采用Q和n两个参数来表征CPE元件的阻抗值ZCPE:
式中,ZCPE为相位角元件的阻抗;Q为与尺寸相关的电容常数,Ω-1cm-2sn;s=2α/π,α是元件CPE相位角;n在0~1范围内取值,当n=0时,CPE为理想电阻,当n=1时,CPE为理想电容;j代表虚数 (j2=-1),w为角频率。
图7 4种试样在3.5%NaCl溶液中的等效拟合电路图
表3 浸泡在3.5%NaCl溶液中的4种试样阻抗谱拟合电路的各项参数值
由表3可知,误差函数Chi-squared (x2) 的数值范围在 (3.0~7.0)×10-5之间,较低的误差函数值表明实验结果与所用等效电路图具有很高的契合程度[14]。一般来说,线性极化电阻值的倒数即1/RP,它的数值的大小,反应了试样的腐蚀速率的大小。根据表3的结果,可以发现,82-QPT试样具有最低的1/RP数值,即它在3.5%NaCl溶液中的耐腐蚀性能最好。另外,CPE的n可以作为表征试样表面不均匀性的参数,金属表面越粗糙,n的值越小[15,16]。从表3可看出,81-Q&T和82-Q&T试样的n值低于81-Q&P和82-QPT,说明两试样表面的粗糙度较大,试样被腐蚀得更严重。
2.4 腐蚀形貌的分析
2.4.1 腐蚀产物的形貌
如图8所示,浸泡初期 (32 h) 81-Q&T试样表面腐蚀产物刚开始从基体上产生,主要为花状的γ-FeOOH和少量针状的α-FeOOH;腐蚀中期 (43 d),腐蚀产物出现片状的β-FeOOH,细晶状的α-FeOOH数量逐渐增多,尺寸逐渐变大;腐蚀后期 (89 d),腐蚀产物则主要为球状的Fe3O4和少量的α-FeOOH[17,18]。
图8 81-Q&T试样腐蚀后的表面腐蚀产物形貌
81-Q&P试样腐蚀不同时间后的表面腐蚀产物形貌如图9所示。可以看到,腐蚀初期 (32 h) 试样表面堆积的腐蚀产物较少,主要为花状的γ-FeOOH;腐蚀中期 (43 d),腐蚀产物明显增多且出现球状Fe3O4;腐蚀后期 (89 d),腐蚀产物则主要为Fe3O4。
图9 81-Q&P试样腐蚀后的表面腐蚀产物形貌
82-Q&T试样腐蚀不同时间后的表面腐蚀产物形貌如图10所示。可以看到,与81-Q&T腐蚀产物形貌的发展规律类似,腐蚀初期 (32 h) 试样表面腐蚀产物为花状的γ-FeOOH和针状的α-FeOOH,随着腐蚀的进行,腐蚀产物逐渐向稳定的α-FeOOH以及Fe3O4演变[18]。
图 10 82-Q&T试样腐蚀后的表面腐蚀产物形貌
82-QPT试样腐蚀不同时间后的表面腐蚀产物形貌如图11所示。可以发现,与81-Q&P钢类似,腐蚀初期 (32 h) 试样表面产物较少且主要为β-FeOOH夹杂少量花状的γ-FeOOH,随后腐蚀产物逐渐向稳定的α-FeOOH和Fe3O4演变[18]。
图11 82-QPT试样腐蚀后的表面腐蚀产物形貌
对比81-Q&T和81-Q&P试样,可以看到,81-Q&P试样腐蚀产物初期产生较少并且腐蚀进行到中期时产物主要为α-FeOOH以及Fe3O4,而此时81-Q&T试样的腐蚀产物中还存在较多的β-FeOOH;对比82-Q&T以及82-QPT试样也可以发现相同的规律。但是与81#钢不同的是,在腐蚀初期,82#钢腐蚀产物已出现细晶状的α-FeOOH,由于α-FeOOH以及Fe3O4比较致密,可以在一定程度上阻止Cl-渗透到试样表面,因此81-Q&P (或82-QPT) 钢能够表现出更好的耐腐蚀性[15]。
2.4.2 腐蚀产物的XRD分析
对4种样品在浸泡不同时间后的表面腐蚀产物进行XRD分析,可见其在相同浸泡时间内表面的腐蚀产物的相组成一样,仅各相的比例不同,因此仅分析82-QPT试样的结果。图12为82-QPT试样在3.5%NaCl溶液中分别浸泡32 h、43 d和89 d后表面腐蚀产物的XRD图谱。经PDF卡片标定可识别出可能的腐蚀产物种类主要包括β-FeOOH、γ-FeOOH、α-FeOOH和Fe3O4,可以看出,随浸泡时间的延长,β-FeOOH和γ-FeOOH的比例逐渐减少,α-FeOOH和Fe3O4的比例逐渐增加,与图11 SEM结果基本一致。
图12 82-QPT试样在3.5%NaCl溶液中浸泡32 h、43 d和89 d后表面腐蚀产物的XRD图谱
2.4.3 清洗腐蚀产物后试样的形貌
图13为试样浸泡不同时间后将腐蚀产物清洗干净后的表面SEM形貌图。可以看到,腐蚀初期 (32 h),4种试样表面都分布着大小不一的点蚀坑,点蚀坑主要来源于Cl-对表面钝化膜的侵蚀。对比不同钢种来看,点蚀坑的发展规律基本一致,但相对来说82#钢的点蚀坑尺寸更小,表明其具有更好的耐腐蚀性;对比不同热处理工艺可以看出相比于81-Q&P (82-QPT) 试样,81-Q&T (82-Q&T) 的点蚀坑数目更多、尺寸更大且分布更加密集,说明Cl-对Q&T试样表面钝化膜的侵蚀作用更大,腐蚀更加严重。随着时间的延长,当腐蚀进行到后期 (89 d),点蚀坑发生堆叠增加,由最初的点蚀发展到后期的均匀腐蚀,并且这一现象在Q&T试样上表现的更为明显。
图 13 不同浸泡时间下4种试样清洗腐蚀产物后的形貌
3 结论
(1) Q&T钢主要组织为马氏体,且马氏体板条间有极少量薄膜状的残余奥氏体,Q&P (或Q-P-T) 钢主要由板条马氏体和板条马氏体条间夹杂着的薄片状的残余奥氏体组成,另外82-QPT的马氏体基体上还弥散分布着碳化钒颗粒;经XRD计算,81-Q&P钢中残余奥氏体含量约为15.1%,82-QPT钢中残余奥氏体含量约为14.4%,这一结果与PPMS所计算的数值 (81-Q&P~15.6%和82-QPT~14.8%) 基本一致。
(2) 4种试样在3.5%NaCl溶液中的腐蚀产物主要由β-FeOOH、γ-FeOOH、α-FeOOH和Fe3O4组成,不同浸泡时间下,各腐蚀产物的比例不同,随浸泡时间的延长,腐蚀产物由β-FeOOH和γ-FeOOH逐渐过渡为α-FeOOH和Fe3O4。
(3) 4种试样在3.5%NaCl溶液中发生的腐蚀主要为吸氧腐蚀,由于Cl-对表面钝化膜的侵蚀作用,腐蚀初期4种试样表面主要发生点蚀,随着腐蚀时间的延长,点蚀坑连接成片,由最初的点蚀逐渐发展为均匀腐蚀。
(4) 失重法和电化学测试均表明,82-QPT (81-Q&P) 试样的耐腐蚀性能较82-Q&T (81-Q&T) 试样的好,且含V的82#钢的耐腐蚀性能较81#钢的更好,这主要是由于82-QPT (81-Q&P) 钢内存在部分残余奥氏体,残余奥氏体的存在提高了马氏体基体的腐蚀电位,其作为阳极优先发生腐蚀,从而保护了马氏体基体[7],加之碳化物的弥散分布,使得试样表面存在更多致密的有利的α-FeOOH和Fe3O4相,能有效阻碍Cl-的渗透,这些因素的共同作用使得82-QPT试样具有最好的耐腐蚀能力。
参考文献
[1] Hsu T Y. Quenching-partitioning-tempering process for ultra-high strength steel [J]. Int. Heat Treat. Surf. Eng., 2008, 2: 64
[2] Speer J G, Streicher A M, Matlock D K, et al. Quenching and partitioning: A fundamentally new process to create high strength trip sheet microstructures [A]. Austenite Formation and Decomposition [C]. Chicago, 2003: 505
[3] Speer J G, Assuno F C R, Matlock D K, et al. The “quenching and partitioning” process: Background and recent progress [J]. Mater. Res., 2005, 8: 417
[4] Speer J, Matlock D K, De Cooman B C, et al. Carbon partitioning into austenite after martensite transformation [J]. Acta Mater., 2003, 51: 2611
[5] HajyAkbary F, Sietsma J, Miyamoto G, et al. Interaction of carbon partitioning, carbide precipitation and bainite formation during the Q&P process in a low C steel [J]. Acta Mater., 2016, 104: 72
[6] Lu S Y, Yao K F, Chen Y B, et al. Effect of quenching and partitioning on the microstructure evolution and electrochemical properties of a martensitic stainless steel [J]. Corros. Sci., 2016, 103: 95 DOI:10.1016/j.corsci.2015.11.010 URL
[7] Yang J L, Lu Y F, Guo Z H, et al. Corrosion behaviour of a quenched and partitioned medium carbon steel in 3.5wt.%NaCl solution[J]. Corros. Sci., 2018, 130: 64DOI:10.1016/j.corsci.2017.10.027 URL
[8] Edmonds D V, He K, Rizzo F C, et al. Quenching and partitioning martensite—A novel steel heat treatment [J]. Mater. Sci. Eng., 2006, A438-440: 25
[9] De Moor E, Speer J G, Matlock D K, et al. Quenching and partitioning of CMnSi steels containing elevated manganese levels [J]. Steel Res. Int., 2012, 83: 322 DOI:10.1002/srin.v83.4 URL
[10] Jatczak C F. Retained austenite and its measurement by X-ray diffraction [J]. SAE Trans., 1980, 89: 1657 [11] Zhao L, Van Dijk N H, Brück E, et al. Magnetic and X-ray diffraction measurements for the determination of retained austenite in TRIP steels [J]. Mater. Sci. Eng., 2001, A313: 145
[12] Peng X. Research on electrochemical corrosion behaviors and parameters of rusted carbon steel in marine environment [D]. Qingdao: Ocean University of China, 2013 (彭欣。海水环境中带锈碳钢腐蚀电化学行为及相关参数的研究 [D]. 青岛: 中国海洋大学, 2013)
[13] Rui J Q.Corrosion and passivation properties of 15Cr supermartensitic stainless steels [D]. Kunming: Kunming University of Science and Technology, 2013 (芮家群。15Cr超级马氏体不锈钢的腐蚀及钝化行为的研究 [D]. 昆明: 昆明理工大学, 2013)
[14] Osório W R, Peixoto L C, Garcia L R, et al. Electrochemical corrosion response of a low carbon heat treated steel in a NaCl solution [J]. Mater. Corros., 2009, 60: 804
[15] Chen Y Y, Tzeng H J, Wei L I, et al. Corrosion resistance and mechanical properties of low-alloy steels under atmospheric conditions[J]. Corros. Sci., 2005, 47: 1001 DOI:10.1016/j.corsci.2004.04.009 URL
[16] Ma Y T, Li Y, Wang F H.The atmospheric corrosion kinetics of low carbon steel in a tropical marine environment [J]. Corros. Sci., 2010, 52: 1796
[17] De la Fuente D, Díaz I, Simancas J, et al.Long-term atmospheric corrosion of mild steel[J]. Corros. Sci., 2011, 53: 604
[18] Ma Y T, Li Y, Wang F H.Corrosion of low carbon steel in atmospheric environments of different chloride content [J]. Corros. Sci., 2009, 51: 997
免责声明:本网站所转载的文字、图片与视频资料版权归原创作者所有,如果涉及侵权,请第一时间联系本网删除。
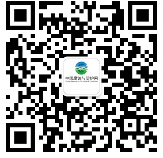
官方微信
《中国腐蚀与防护网电子期刊》征订启事
- 投稿联系:编辑部
- 电话:010-62316606-806
- 邮箱:fsfhzy666@163.com
- 中国腐蚀与防护网官方QQ群:140808414