摘要
采用可控的化学氧化法制备出功能化石墨烯,最终实现石墨烯与三乙烯四胺的接枝反应。结果表明:石墨烯经化学修饰后其片层结构更平滑舒展。添加改性石墨烯的涂层在致密性、附着力等方面的性能明显提高。化学改性通过提高石墨烯的分散性及其与环氧树脂基料的相容性,减少涂层的内部缺陷,涂层结构更加致密,有效阻挡了腐蚀介质的扩散。同时,与环氧树脂形成紧密结合的化学结合界面,延缓了交变压力对该界面的破坏作用,从而延长涂层在交变压力条件下的使役寿命。
关键词: 改性石墨烯 ; 有机涂层 ; 压力交变 ; 失效机制
深海资源的开发利用对深海设备腐蚀防护的需求与日俱增。作为金属材料的主要防护手段[1],有机防腐涂层在深海服役时面临严重的快速失效问题,影响深海设备的稳定性及安全性[2]。因此,针对复杂苛刻的深海环境研发新型防护涂料是亟待解决的难题。
传统的重防腐涂层在深海高压力、压力交变条件作用下,腐蚀性介质会快速向涂层内部渗透,到达涂层/金属界面后导致涂层附着力快速丧失,涂层从金属表面快速剥离;涂层中的无机屏蔽填料与有机树脂相容性差,导致填料/树脂界面成为涂层体系的薄弱环节,在压力作用下容易发生开裂,涂层致密性破坏从而引发提前失效[3,4,5,6,7]。可见,新型防护涂料应具有耐压及屏蔽性能优异的特点,以实现深海环境下长效服役的目的。
石墨烯自被发现以来,在各个领域的应用研究都受到了广泛关注[8,9]。石墨烯具有sp2杂化的C—C键,其理论本征强度比任何材料都要强,单片层的石墨烯拥有最大的比表面积,这些性质预计会在有机涂层应用中展现出优异的屏蔽和力学性能,理论上是作为涂层填料最理想的候选材料[10]。然而,由于石墨烯化学性质稳定,惰性的表面不亲水亲油,与有机树脂的相容性较差。较高的表面能导致其片层极易发生团聚,这些都使得石墨烯在实际应用时不仅不会增强涂层的机械性能与防护性能,反而会导致性能下降[11]。
为了解决上述问题,通常选择对石墨烯氧化物表面进行修饰。由于氧化石墨烯表面具有羟基 (—OH)、羧基 (—COOH)、环氧基 (—O—)、羰基 (C=O) 等活性官能团,可实现对其分散性及与有机树脂相容性的改善。Mo等[12]采用硅烷偶联剂对氧化石墨烯进行改性,硅烷分子水解生成活性的Si—OH,与氧化石墨烯边缘的活性基团,如羟基、羧基、环氧树脂等发生化学反应。硅烷分子上的官能团,如氨基、环氧树脂等,可为后续的偶联修饰提供活性位点,既提高了石墨烯的分散性,又增强了石墨烯与树脂的相容性。与羧基反应后成功将氨基接枝到氧化石墨烯表面,实现了填料分散性的提升。Yu等[13]通过将氧化石墨烯与Al2O3颗粒进行杂化,从而提高了环氧涂层的防护性能。Chang等[14]采用原位聚合法制备了聚苯胺/四氨基苯甲酸改性石墨烯,使涂层具有更好的阻水、阻氧性能和耐金属腐蚀性能。
然而,氧化石墨烯的制备过程通常会引入晶格缺陷,使其力学性能及阻隔性能远低于理论值。为使石墨烯从惰性材料变为有反应功能的活化材料,同时基本保持石墨烯的原始结构,降低生成缺陷的程度,本研究采用氨水作为还原剂调整反应体系的氧化能力,使过硫酸铵的自由基与石墨烯反应并在其片层上产生环氧官能团,接着采用多乙烯多胺与石墨烯上的环氧官能团反应,制备出具有活性且较低缺陷的改性石墨烯。针对深海交变压力环境下改性石墨烯涂层的防护性能及失效机制进行了分析,为涂层设计及研发提供一定的理论依据。
1 实验方法
实验采用可控的化学氧化法制备改性石墨烯填料。将0.1 g石墨烯分散至100 g水与50 g乙醇的混合溶液中,并将2 g氨水逐渐加入到上述溶液,混合并加热搅拌。待温度稳定后向混合物中加入2 g过硫酸铵以开始氧化反应,随后每小时加入1 g过硫酸铵,3次后取出样品。将获得的悬浮液采用去离子水反复洗涤并高速离心,当pH值约为7、电导率<100 μs/cm即时停止洗涤,干燥后获得稳定的功能化石墨烯粉末。
取0.1 g功能化石墨烯加入100 mL去离子水与10 g三乙烯四胺并搅拌均匀,超声5 h制备改性石墨烯。提纯、超声润洗后满足pH值约为7、电导率<100 μs/cm即得到改性石墨烯样品。
有机涂层成膜物质选用现役防腐涂料中常用的E-44双酚A型环氧树脂,其固化剂为低分子TY-650聚酰胺,溶剂为二甲苯,三者质量配比为1∶0.8∶0.4。改性及未改性的石墨烯粉末作为填料各自加入成膜物质并制成涂层 (分别称作G-coating和MG-coating),其质量占比为0.1%。涂料配好后在25 ℃的环境中静置0.5 h,待充分熟化后进行涂装。
自由膜样品用于称重测量及拉伸实验。将涂料刷涂至硅胶板表面,经40 ℃固化4 h后进行裁剪。拉伸样品按照GB/T 528-92标准的尺寸进行裁剪。裁剪完成后,将自由膜继续在60 ℃固化20 h,而后取出在室温下 (25 ℃,RH30%) 固化24 h,以确保溶剂完全挥发。涂层/金属样品则是将涂料刷涂至Q235钢试样表面,经40 ℃固化4 h,60 ℃固化20 h后,再在室温下 (25 ℃,RH30%) 固化1 d。固化后干态涂层厚度的平均值为 (200±10) ?m。
交变压力实验均在深海模拟装置[7]中进行,交变压力加速条件设置为:常压0.1 MPa与高静水压6 MPa循环加载,以24 h为一个交变周期。前半个周期 (12 h) 在高静水压6 MPa下浸泡,后半个周期 (12 h) 在常压下浸泡,浸泡至少10个周期共240 h。实验温度通过恒温控温槽控制在 (25±1) ℃,溶解氧含量保持在空气饱和值 (约8 mg/L)。
实验通过重量法计算涂层的吸水率。将浸泡前自由膜的重量记为m0,在不同浸泡时间t条件下的重量称重并记为mt,则涂层的吸水率Qt按如下公式进行计算:
Qt=mt?m0m0×100% (1)
每组测量3个平行样品,最终结果为其算术平均值。附着力测试按照ASTM D4541-02进行。用快固AB胶黏剂将不同浸泡时间条件下的涂层样品表面与拉伸铝锭 (直径20 mm) 粘结起来,待粘结剂完全固化后,将涂层从基体上拉开时所需的临界附着强度,即为涂层与金属的附着力。每组实验选取5个平行样,最终结果为其平均值。涂层的强韧性测试按照ISO 37-2005进行,将浸泡后的拉伸试样采用万能拉伸试验机在室温下进行测试,加载速率为2 mm/min。为保证数据的重现性,每组实验采用6个平行样品。涂层微观形貌采用扫描电子显微镜 (SEM,ZEISS SUPRA 55) 进行直接观测。
电化学阻抗谱采用AutoLab PGSTAT302型电化学工作站进行测量,测量在开路电位下进行,测试频率范围为105~10-2 Hz,正弦扰动信号为20 mV。交变压力下三电极体系中的工作电极为涂层/金属电极,参比电极为固态高压参比电极 (ESCE=-0.157 V),辅助电极为铂电极。阻抗数据经计算机采集后,用ZSimpWin软件进行拟合。
2 结果与讨论
2.1 改性石墨烯的表征
为了分析对石墨烯功能化的效果,将过硫酸铵氧化的石墨烯进行红外光谱 (FTIR) 测试,其结果如图1所示。其中1220 cm-1波数处的振动特征应属于环氧特征峰,在1140 cm-1波数处的振动峰应属于环氧C—O—C的振动吸收峰。这些结果表明环氧官能团已经接枝到石墨烯的表面上,可实现与氨基的进一步反应。
图1 功能化后石墨烯的红外光谱图
为了对比改性前后石墨烯的分散性,进行了未改性及改性石墨烯的沉降实验,结果如图2所示。可以看出,初始时两种石墨烯分散液都呈现均一、黑色不透明的状态。本征态的石墨烯在8 h后全部沉淀,这是由于石墨烯本身没有官能团,与有机溶剂的结合力较差从而分散性不佳。而通过改性处理后,石墨烯在静置48 h后仍然可以在极性溶剂中保持良好的分散性,主要是由于氨基实现了与石墨烯表面官能团的接枝。
图2 不同时间条件下改性和未改性石墨烯粉末在有机溶剂中的分散稳定性
通过对两种状态下的石墨烯进行SEM观察,进一步分析本征态石墨烯的改性效果。从图3可以看出,本征态石墨烯片层堆叠较多,其延展性与分散性较差,而改性石墨烯的片层堆叠数较少,石墨烯片层之间的分散的更为彻底,片层延展性更好,说明采用本方法进行的石墨烯改性可以减少片层团聚,使其分散的更加均匀。
图3 改性及未改性石墨烯粉末的SEM像
2.2 交变压力条件下石墨烯涂层的性能测试
水、氧气等腐蚀性介质在到达金属基体前会逐渐向有机涂层内部渗透,涂层的高聚物网络结构与形态上的多孔性决定了吸水过程是不可避免的,而有机涂层中填料/基料树脂界面的致密性是涂层耐渗透能力的关键[15]。通过测试未改性石墨烯环氧涂层与改性石墨烯环氧涂层的吸水随浸泡时间的质量变化,计算涂层的吸水动力学,得到两种涂层吸水率与浸泡时间关系的对比曲线,研究石墨烯的化学改性对涂层致密性的影响以及有机涂层中的水传输过程。从图4中可以看出,两种涂层在整个浸泡周期内吸水率的变化大致可以分为两个阶段:吸收阶段和饱和阶段,在吸收阶段过程中,石墨烯涂层和改性石墨烯涂层的吸水率在浸泡初期明显增加,此时水会快速渗透到涂层的孔隙中。浸泡48 h后,未改性石墨烯和改性石墨烯涂层吸水率分别为2.23%和1.99%。另外,相同浸泡时间下改性石墨烯涂层的吸水率要小于未改性石墨烯涂层,在浸泡后期两种涂层吸水率均出现平台,即均达到饱和状态。浸泡周期480 h后,未改性石墨烯和改性石墨烯涂层吸水率分别为3.63%和2.71%,可见,采用三乙烯四胺改性的石墨烯不仅能延缓涂层饱和吸水时间而且明显降低了涂层的吸水量。
图4 交变压力条件下未改性石墨烯和改性石墨烯涂层的吸水动力学曲线
由于涂层/金属界面基体腐蚀、起泡等界面反应的发生,涂层湿态附着力将会显著下降。因而涂层的湿态附着力是评价涂层防护性能的关键参数之一。改性与未改性石墨烯有机涂层的湿态附着力随浸泡时间变化曲线如图5所示。两种涂层的干态附着力较高,为10.88 MPa。当浸泡时间为24 h时,改性石墨烯涂层和未改性涂层的湿态附着力分别下降至6.94和3.74 MPa。此时通过对涂层表面宏观形貌的观察,未有肉眼可见的腐蚀点,表明在形成宏观腐蚀产物之前,附着力即发生明显下降。随着浸泡时间的延长,两种涂层的湿态附着力均呈下降趋势,表明涂层附着力都在逐渐丧失。当浸泡20个周期后,涂层的湿态附着力分别下降到1.99和1.32 MPa,此时涂层已不能很好地附在基体上。以上分析可以得出,交变压力会导致涂层附着力的快速下降丧失,而改性石墨烯能够延缓附着力下降的速度。
图5 不同压力条件下石墨烯有机涂层的湿态附着力随浸泡时间的变化
2.3 涂层的失效历程分析
涂层失效历程的研究是全面准确分析涂层失效机制的基础。电化学阻抗谱 (EIS) 是目前最成熟的涂层失效电化学评价手段之一,通过等效电路拟合可分别得到涂层电容、微孔电阻等与涂层破坏过程有关的信息。图6和7分别为实验所测的未改性和改性石墨烯涂层Nyquist图。未改性涂层在最初的96 h内,只有一个容抗弧特征。从96 h到约120 h,阻抗曲线随着浸泡时间的变化而变化,且阻抗弧的半径随着浸泡时间的增加而逐渐减小。随后阻抗谱出现扩散特征。涂层在整个浸泡时期 (240 h) 内显示了经历了3个阶段。另一方面,改性石墨烯涂层初始阶段的阻抗数据也呈现单容抗弧,在120 h后阻抗谱图呈现两容抗弧特征。半径随着浸泡时间增加而减少,整个浸泡时期分为两个阶段。
图7 改性石墨烯有机涂层在交变压力下浸泡不同时间的Nyquist图
图6 未改性石墨烯有机涂层在交变压力下浸泡不同时间的Nyquist图
通过对两种有机涂层EIS结果的拟合,可以确定表征涂层防护性能的涂层孔隙电阻Rc随浸泡时间变化的曲线 (如图8所示)。对于改性涂层和未改性涂层,240 h实验周期内Rc值分别从1.25×1010 Ω·cm2降低到9.02×108 Ω·cm2和约9.92×109 Ω·cm2降低到6.73×107 Ω·cm2。两种涂层的防护作用皆因吸水逐渐恶化,而交变压力的“推-拉”作用导致涂层防护性能的快速下降。根据以上分析可以发现,改性石墨烯涂层能通过延缓水在涂层内部的传输而显著地降低交变压力带来的破坏作用。
图8 两种有机涂层的涂层电阻Rc随浸泡时间的变化
从交变压力条件下两种涂层的性能变化以及失效历程分析中可知,有机涂层中的石墨烯经改性而与环氧树脂化学结合后,涂层的防护性能有了显著的提升。如图9a所示,未改性石墨烯涂层添加了具有较高表面能的本征态石墨烯颗粒,为降低表面自由能,石墨烯粒子会相互聚集以减少表面积,发生团聚现象。石墨烯填料加入有机涂层体系中,在界面处就会产生一定的缺陷,难以形成结合较好的界面。涂层服役时,水等腐蚀介质在交变压力作用下,快速渗透到涂层内部,同时涂层孔隙以及缺陷会进一步扩展,增大水的扩散速率,在填料/树脂结合较差的位置还会出现一些相对宽松的扩散通道,使水较快地到达金属界面。水分子在该界面存积,涂层的屏障作用减弱。涂层结构破坏达到一定程度后导致提前失效。改性的石墨烯涂层 (图9b) 中石墨烯片层的分散性较好,填料与有机树脂之间的结合更加紧密,因此产生的缺陷较少。在交变压力的推拉作用下,相容性较好的界面能够更好地延缓水的渗透及传输过程,结合力较好的界面不易被破坏,因此涂层的防护性能得到了改善,使用寿命大大延长。通过以上分析可以得出,颜填料的化学改性可以减少涂层内部的缺陷,使涂层的防护性能提高,并且可以在涂层服役的过程中有效地减缓腐蚀介质的传输渗透过程。
图9 交变压力下两种涂层失效过程示意图
3 结论
(1) 采用过硫酸铵和氨水制备出的改性石墨烯可实现石墨烯与三乙烯四胺的接枝反应。添加改性石墨烯的涂层在致密性、附着力等方面的性能明显提高。
(2) 石墨烯经化学修饰后其片层结构更平滑舒展。化学改性提高了石墨烯的分散性及其与环氧树脂基料的相容性,减少了涂层的内部缺陷,涂层结构更加致密,有效阻挡了腐蚀介质的扩散。
(3) 三乙烯四胺改性将氨基接枝到石墨烯表面,与环氧树脂形成紧密结合的化学结合界面,延缓了交变压力对该界面的破坏作用,从而延长涂层在交变压力环境下的使役寿命。
参考文献
[1] Liu B. Study on the evaluation technique for the performance of anticorrosion coatings under deep sea environment [J]. Shanghai Coat., 2011, 49(5): 34
[1] (刘斌. 深海环境下防腐蚀涂料性能评价技术研究 [J]. 上海涂料, 2011, 49(5): 34)
[2] Liu B, Fang Z G, Wang H B, et al. Effect of cross linking degree and adhesion force on the anti-corrosion performance of epoxy coatings under simulated deep sea environment [J]. Prog. Org. Coat., 2013, 76: 1814
[3] Liu J, Li X B, Wang J. Effect of hydrostatic pressure on the corrosion behaviors of two low alloy steels [J]. Acta Metall. Sin., 2011, 47: 697
[3] (刘杰, 李相波, 王佳. 模拟深海压力对2种低合金钢腐蚀行为的影响 [J]. 金属学报, 2011, 47: 697)
[4] Tian W L, Liu L, Meng F D, et al. The failure behaviour of an epoxy glass flake coating/steel system under marine alternating hydrostatic pressure [J]. Corros. Sci., 2014, 86: 81
[5] Tian W L, Meng F D, Liu L, et al. The failure behaviour of a commercial highly pigmented epoxy coating under marine alternating hydrostatic pressure [J]. Prog. Org. Coat., 2015, 82: 101
[6] Meng F D, Liu L, Tian W L, et al. The influence of the chemically bonded interface between fillers and binder on the failure behaviour of an epoxy coating under marine alternating hydrostatic pressure [J]. Corros. Sci., 2015, 101: 139
[7] Liu Y, Wang J W, Liu L, et al. Study of the failure mechanism of an epoxy coating system under high hydrostatic pressure [J]. Corros. Sci., 2013, 74: 59
[8] Schriver M, Regan W, Gannett W J, et al. Graphene as a long-term metal oxidation barrier: Worse than nothing [J]. ACS Nano, 2013, 7: 5763
[9] Fauzi F, Suhendar H, Kusumaatmaja A, et al. A simple method to examine room-temperature corrosion of graphene-coated copper foil after stored for 2.5 years [J]. Mater. Res. Express, 2018, 5: 105016
[10] Xu X Z, Yi D, Wang Z C, et al. Greatly enhanced anticorrosion of Cu by commensurate graphene coating [J]. Adv. Mater., 2018, 30: 1702944.
[11] Ding R, Li W H, Wang X, et al. A brief review of corrosion protective films and coatings based on graphene and graphene oxide [J]. J. Alloy. Compd., 2018, 764: 1039
[12] Mo M T, Zhao W J, Chen Z F, et al. Excellent tribological and anti-corrosion performance of polyurethane composite coatings reinforced with functionalized graphene and graphene oxide nanosheets [J]. RSC Adv., 2015, 5: 56486
[13] Yu Z X, Di H H, Ma Y, et al. Fabrication of graphene oxide-alumina hybrids to reinforce the anti-corrosion performance of composite epoxy coatings [J]. Appl. Surf. Sci., 2015, 351: 986
[14] Chang C H, Huang T C, Peng C W, et al. Novel anticorrosion coatings prepared from polyaniline/graphene composites [J]. Carbon, 2012, 50: 5044
[15] Lin H C, Li M C. Corrosion process for metals beneath coating [J]. Corros. Sci. Prot. Technol., 2002, 14: 180
[15] (林海潮, 李谋成. 涂层下金属的腐蚀过程 [J]. 腐蚀科学与防护技术, 2002, 14: 180)
免责声明:本网站所转载的文字、图片与视频资料版权归原创作者所有,如果涉及侵权,请第一时间联系本网删除。
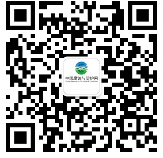
官方微信
《中国腐蚀与防护网电子期刊》征订启事
- 投稿联系:编辑部
- 电话:010-62316606-806
- 邮箱:fsfhzy666@163.com
- 中国腐蚀与防护网官方QQ群:140808414