12Cr1MoVG钢是一种具有良好抗高温蠕变性能、耐高温腐蚀和抗氧化性能的合金钢,广泛应用于电厂锅炉主蒸汽管、过热器管和再热器管,其供货状态为正火+ 回火态,组织为铁素体+ 贝氏体。由于该材料长期服役于高温环境中易发生珠光体球化、碳化物沿铁素体晶界析出和粗化,导致材料使用性能下降,严重时会危害锅炉部件的安全。张彦文等研究了火电厂用12Cr1MoVG钢管在使用过程中发生早期爆管失效的原因,研究表明:钢管受腐蚀介质影响,内壁发生减薄,出现蠕变孔洞,进而发生爆管。杨滨等研究了火电厂用12Cr1MoV钢主蒸汽管道长期服役后的组织性能变化,结果表明:材料组织发生了明显的珠光体球化,碳化物和晶粒长大,高温屈服强度和抗拉强度也明显下降。YAN等采用扫描电镜原位拉伸试验,研究了服役20000h和200000h后的12Cr1MoVG钢的组织性能,结果表明:材料均发生了珠光体球化,碳化物沿晶界析出,材料断裂性能下降。
来自河南农业大学、武汉大学、中国大唐集团科学技术研究院有限公司华中电力试验研究院的刘泰然、张一可等研究人员以某发电厂300MW火电机组锅炉末级再热器12Cr1MoVG钢管为研究对象,该设备已累计运行超过1×105h,在运行期间的几次维修中,经检测发现12Cr1MoVG钢的显微组织已发生珠光体球化,为了评估机组的安全状态,对该末级再热器钢管进行组织观察、性能分析以及寿命评估,以期为12Cr1MoVG钢的应用提供更多参考。
01 试验材料与方法
试验材料取自服役时间超过1×105h的锅炉末级再热器管道,材料为12Cr1MoVG钢。在第22排最外圈(编号为A22)、第39排最外圈(编号为A39)和最内圈(编号为B39)、第55排最外圈(编号为A55)管道截取试样,分别在管道向火侧和背火侧取金相试样和室温拉伸试样,取样部位如图1所示,拉伸试样尺寸如图2所示。
图1 拉伸试样取样部位
图2 拉伸试样尺寸
宏观观察管道内外壁的表面状态,测量管道内外壁氧化膜厚度和有效壁厚,采用合金分析仪测定管道的化学成分。采用维氏硬度计测量管道向火侧和背火侧内外壁的维氏硬度。采用电子万能试验机测定试样的室温拉伸性能,并进行强度校核。采用金相显微镜和场发射扫描电镜(SEM)分析材料的珠光体组织形态、蠕变孔洞,评估珠光体球化级别和蠕变状态,结合能谱仪(EDS)的分析结果,分析组织的老化状态。
02 结果与讨论
2.1 氧化层厚度检测
再热器管道的实测尺寸结果如表1所示。
表1 再热器管道的实测尺寸
由表1可知:只有A39管道的全壁厚度是负偏差,其余管道均为正偏差;只有B39管道的金属壁厚未发生减薄,A55管道的内外壁氧化膜总厚度超过450μm,这表明再热器管道在工作时出现超温现象,管道在超温环境中,氧化剧烈,导致氧化膜厚度过厚。
2.2 化学成分分析
根据再热器管道的化学成分分析结果可知,服役超过1×105h后,各管道的化学成分符合GB/T 5310—2017《高压锅炉用无缝钢管》对12Cr1MoVG钢的技术要求,表明材料未发生显著的元素贫化。
2.3 力学性能试验及强度校核
2.3.1 力学性能试验
为评估材料的性能,从每个管道的背火侧和向火侧各取两个试样,在试验机上进行室温拉伸试验,试验温度为24℃,取两个试样实测结果的平均值。根据DL/T 438—2016《火力发电厂金属技术监督规程》,对试样进行硬度试验,室温拉伸试验和维氏硬度测试结果见表2。
表2 再热器管道的室温拉伸性能和维氏硬度
由表2可见,末级再热器管道服役超过1×105h后,各管道硬度值均符合DL/T 438—2016的技术要求,其抗拉强度、屈服强度和延伸率仍满足GB/T 5310—2017对12Cr1MoV钢的技术要求。
2.3.2 强度校核
为评估材料的运行状态,参照DL/T 654—2009《火电机组寿命评估技术导则》的推荐公式,计算材料的运行当量温度和环向应力。材料环向应力计算公式如式(1)所示。
管壁运行当量温度和内壁氧化膜厚度满足式(2)。
12Cr1MoV 钢管的额定蒸汽工作压力为17.47MPa,在进行强度校核时,对实测金属壁厚进行环向应力计算,计算结果如表3所示。
表3 再热器管道的管壁运行当量温度和运行应力
由表3可见,各再热器管道的环向应力均低于GB/T 16507.2—2013《水管锅炉》标准中规定的12Cr1MoVG钢管的许用应力,强度校核合格,管道处于应力安全状态。
2.4 显微组织观察及珠光体球化评级
根据DL/T 773—2016 《火电厂用12Cr1MoV钢球化评级标准》,对各管道的向火面和背火面的显微组织进行观察,结果如图3所示,并对各管道的显微组织进行珠光体球化评定。
图3 再热器各管道不同位置处的显微组织
由图3可知:A55管道的珠光体球化程度最为严重,珠光体球化程度达到4级及以上,一些区域珠光体形态已完全消失,晶内碳化物显著减少;其余管道的珠光体球化程度为3~4级,片层状珠光体区域已显著分散,仍保留原有的形态。
2.5 扫描电镜及能谱分析
图4 再热器各管道不同位置处的SEM形貌
由图4可知:A55管道珠光体球化程度达到4级及以上,仅有少许片层状珠光体,晶内碳化物较少,呈点状分布,晶界碳化物较多,颗粒较大,沿晶界呈不连续链状、条状分布,说明珠光体中的碳化物已经向晶界大量转移,珠光体球化基本完成;其余管道的珠光体球化程度为3~4级,仍可见保留原珠光体特征的晶粒,片状碳化物已经聚集长大呈现短条状、点状特征,导致珠光体层片状特征消失,晶界析出较多碳化物。SEM 分析结果表明,各管道晶界均有碳化物析出,未见蠕变孔洞,无需进行蠕变评级,因此管道不会形成蠕变破坏,能够继续安全运行。
表4 再热器各管道晶界析出相和基体的EDS分析结果
由表4可知:晶界析出相中均含有铬,其质量分数最高达到14.73%,而基体内的铬含量均较低,说明基体中的铬已向晶界大量转移形成碳化物;部分管道晶界析出相中含钼,基体中钼含量较低,说明基体中的大部分钼都已转移到晶界,由于钼含量较低,部分晶界析出相中未能检测到钼,说明钼元素已产生了显著的再分配;晶界碳化物含有较多锰,说明锰元素也从基体向晶界处转移;钒含量在晶界和晶内均较为稳定,晶界处检测出的钒是热处理过程中析出的。基体中的钼、铬、锰都是可提高材料热强性的合金元素,大量的合金元素从基体向晶界碳化物中的再分配,致使材料的热强性显著下降。
2.6 剩余寿命评估
为分析材料的剩余使用寿命,采用参数外推法进行评估。当已知管壁的运行当量温度、应力,即可通过公式(3)估算管道的剩余使用寿命(即断裂时间)。
管壁运行当量温度由公式(3)计算得出,结果如表5所示。由表5可知,再热器管道的剩余使用寿命均超过100000h,材料整体处于较为安全的状态。
表5 再热器管道的剩余使用寿命
03 结论
(1) 再热器管道的化学成分均符合技术要求,力学性能均满足国家标准要求,强度校核合格,管道处于应力安全状态。
(2) 再热器管道珠光体球化级别处于3~4级,合金元素产生了明显的再分配现象,固溶合金元素贫化明显。未观察到蠕变孔洞,蠕变处于稳定的第二阶段。根据氧化膜厚度计算得到的管壁运行当量温度超过额定蒸汽温度(541℃),存在超温现象,但是未超过12Cr1MoV钢的最高使用温度(580℃),处于安全温度范围。根据氧化膜厚度估算的再热器管道的剩余使用寿命均超过100000h。
免责声明:本网站所转载的文字、图片与视频资料版权归原创作者所有,如果涉及侵权,请第一时间联系本网删除。
相关文章
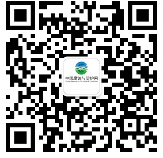
官方微信
《中国腐蚀与防护网电子期刊》征订启事
- 投稿联系:编辑部
- 电话:010-62316606-806
- 邮箱:fsfhzy666@163.com
- 中国腐蚀与防护网官方QQ群:140808414
点击排行
PPT新闻
“海洋金属”——钛合金在舰船的
点击数:7317
腐蚀与“海上丝绸之路”
点击数:5894