航空航天领域对轻质高模量构件的需求极为迫切,轻质高模量材料可使构件满足承载、高精度和高稳定性的要求,以大幅度减轻构件、提高飞行器的综合性能。现有的常规轻合金材料,难以同时满足低密度、高强度、高刚度和高韧性的需求。镁基复合材料保留了镁合金的优点,还有比强度高、比刚度高、尺寸稳定性好、耐高温性、耐冲击性优良等特点[1, 2]。同时,镁基复合材料还有电磁屏蔽和储氢等特性,有望成为当今高新技术航空航天、军工产品制造、汽车以及电子封装等领域不可或缺的理想结构与功能复合材料[3-6]。
1 镁基复合材料的组成
镁基复合材料具有极强的设计性,可根据需要设计由不同结构、种类和体积分数的增强体与不同基体生成的合金。增强体、镁合金基体以及连接增强体与基体之间的界面,都对镁基复合材料的力学性能有重要的影响。
先根据工作环境对性能的要求选择基体金属,既要考虑基体的各种性能,还要考虑其与增强体的相容性,使基体与增强体达到最佳的复合和性能的发挥。目前采用的基体合金多为AZ31、AZ61和AZ91等Mg-Al系合金,很少采用Mg-RE、Mg-RE-Zr等高强耐热稀土镁合金。如果能采用这类高强韧稀土镁合金作为基体,再辅以颗粒/纤维等复合强化手段,极有希望研发出性能更加优异的稀土耐热镁基复合材料。
增强体能使金属基体的强度、模量、耐热、耐磨等性能进一步提高。一般要求增强体有密度低,力学性能和功能特性优异、结构稳定、不易被镁熔体损伤、与镁基体界面结合良好等优点[7]。根据其形态,常用的增强体有颗粒、晶须和纤维。其中碳纤维(Cf)、碳纳米管(CNTs)、石墨烯纳米片(GNPs)、氧化石墨烯(GO)等碳纳米材料具有超高的强度和韧性,是目前较为理想的增强体。但是,石墨烯层片之间强烈的范德华力,使其在镁基体中极难均匀分散[8]。碳纳米管具有较高的高温稳定性,不易与金属基体反应[9]。提高增强体材料与基体的界面润湿性,一直是科研工作者研究的热点。
应力从基体转移到增强体的能力,是检测基体是否得到增强体强化的评判标准。因此,得到一个好的基体与增强体的结合界面至关重要。基体与增强体的相容性,包括物理相容性(润湿性、热膨胀匹配性)和化学相容性(能否形成合适的、稳定的界面,是否发生有害的化学反应)。在制备金属基复合材料的过程中,如果基体不润湿增强体或与增强体发生剧烈化学反应,则表明它们之间的相容性不好。选用适当的增强体实现与基体良好的润湿性和形成稳定的界面,是镁基复合材料具有良好性能的保障。
2 使增强体均匀分散在复合材料中的制备技术
对于复合材料,增强体的体积分数越高意味着其在某一方面具有更高的性能。但是在实际的制备过程中,增强体体积分数越高团聚或偏聚越明显。团聚的增强体不但没有强化效果,反而导致应力集中而成为裂纹的萌生源,严重影响复合材料的性能。碳纳米管、碳纤维等增强体与镁合金的润湿性差,在制备过程中极易缠结和团聚[10-12]。纳米SiC颗粒(SiCp)很高的表面能和表面张力,使其在镁基体中容易团聚。团聚后的纳米级增强体颗粒的“聚集体”尺寸大,不仅失去了纳米颗粒的增强效果,还使基体与增强体颗粒之间的润湿变差,降低界面结合力,最终使复合材料失效[13]。因此,实现细小含碳纳米增强体的均匀分散成为制备增强镁基复合材料领域一个极具挑战性的课题。目前主要采用以下技术提高镁基复合材料中增强体分布的均匀性。
(1) 粉末冶金技术
粉末冶金技术,是先将镁合金粉末与增强体粉混合,然后经机械搅拌/超声搅拌、烘干、压制、烧结等工艺过程制备复合材料,其工艺流程如图1所示[14]。粉末冶金技术对镁合金的种类和增强相的类型的限制较少,且可控制增强相与基体的配比,从而制备出用其他技术方法不能制备的高体分增强体镁基复合材料。
图1 用粉末冶金法制备镁基复合材料的示意图[14]
Fig.1 Schematic of the preparation of magnesium matrix composites by powder metallurgy
粉末冶金技术中最关键的过程,是制备增强体在基体中均匀分散的原料。一般用液态分散法促进增强相分散,例如用超声分散技术将纳米碳材料分散在无水乙醇溶液中,然后与镁合金粉/乙醇混合浆液混合,再进行机械搅拌混配成纳米碳材料/镁合金复合粉末混合浆料。将混合浆料进行过滤、真空干燥、烧结、热挤压和热处理,制备出纳米碳增强的镁基复合材料[15, 16]。此外,还可将溶剂分散与机械球磨相结合使原料均匀分散,然后进行粉末冶金+热挤压制备纳米SiCp增强镁基复合材料[17]。
对增强体界面进行改性,能更好的实现其在基体中的均匀分散。先对纳米SiCp进行800℃/2 h预氧化处理,再与Mg-8Al-Sn合金粉末均匀混合,然后进行真空烧结、热挤压处理制备出0.5 vol.% n-SiCp/AT81复合材料。结果表明,纳米SiCp经预氧化处理后在复合材料界面生成了1 nm厚的MgA12O4层,强化了载荷传递[18]。将在无水乙醇中搅拌1h得到的GNPs浑浊液倒入Mg、Al、Sn液中,再电磁搅拌1 h。将得到的悬浊液在700℃烘干后得到复合粉末,然后对粉体进行真空热压烧结+热挤压。用该方法很好的实现了均匀分散,制备出的纳米石墨烯增强镁基复合材料其屈服强度和抗拉强度比基体分别提高了29.2%和14.0%[19]。
(2) 搅拌铸造技术
搅拌铸造技术,包括液态搅拌铸造和半固态搅拌铸造,是一种制备颗粒增强镁基复合材料的典型技术。在改善润湿性的基础上,常利用超声振动的空化效应和声流效应打散团聚的增强体,实现其在基体中的均匀分散。Muley[20]向720℃的AZ91熔体中添加平均尺寸为4 μm的Si颗粒,随后对熔体施加超声处理,使原位生成的Mg2Si颗粒弥散分布在基体中。
王晓军采用半固态涡流搅拌技术制备出不同尺寸SiCp增强镁基复合材料,所制材料颗粒分布均匀,空隙率小且没有明显氧化的夹杂。但是SiCp呈“项链状”颗粒分布和在晶界上偏聚使界面成为弱结合,使铸态SiCp增强镁基复合材料的断裂强度降低,需要后续热变形以消除“项链状”颗粒分布和改善界面结合[21]。采用合理工艺参数成功制备出多尺寸SiCp颗粒增强镁基复合材料,与单一尺度SiCp相比,多尺寸复合材料中的小尺寸颗粒可延阻碍微裂纹的扩展,从而提高材料的抗拉强度[22]。但是在室温拉伸过程中,在大尺寸颗粒的尖端部位容易形成裂纹源。基于以上分析,使用亚微米级或纳米级的颗粒并对其进行钝化处理,有利于进一步提高材料的力学性能[23]。
(3) 液态压力浸渗技术
液态压力浸渗技术,是在压力作用下将熔融液态金属浸渗到预制体间隙中,是目前制备高体积分数增强复合材料最有效的技术之一。液态金属在较高的压力下凝固,可明显减少气孔、缩松等缺陷,使材料的组织比较致密。制备良好质量增强体均匀分布的预制块,是该方法的关键。
制备预制块的方法,有湿法成型、缠绕法和编织法。吴昆教授等用湿法成型制备了体积分数50%、粒径分别为5 μm、20 μm和50 μm的SiCp/AZ91镁基复合材料。研究表明,5 μm SiCp增强的复合材料具有更高的力学性能、更低的阻尼性能和热膨胀系数[24]。采用碳纤维缠绕技术制备单向碳纤维均匀排布的预制体,再采用压力浸渗方法可制备T300、T700和M40碳纤维增强镁基复合材料。研究发现,M40的增强效果最明显,使复合材料的弹性模量达到300 GPa,弯曲强度接近1300 MPa[25]。Wu等采用压力浸渗法制备体积分数60%的Cf/Mg复合材料,发现碳纤维石墨化程度越高复合材料弹性模量越高,其热膨胀系数越低[26]。
制备高体分增强体的预制块,也是一种常见的预分散技术。先制备高体分的碳纳米材料增强镁基复合材料预制块,然后将其加入熔融镁中进行搅拌。在搅拌过程中预制块逐渐熔化并分散在镁基体中,从而制备出高体分且分散良好的碳纳米材料增强镁基复合材料 [27]。在此基础上王晓军等开发了一种预分散+搅拌铸造的制备工艺,主要用超声、磁力搅拌的方式制备黏附碳纳米材料的镁屑,然后将其加入半固态的熔融镁中,再进行超声和磁力搅拌进一步分散碳纳米材料[28],其过程示意图如图2所示。采用此工艺制备出的复合材料,增强体分散均匀、界面结合良好,其强塑性同时提高。
图2 石墨烯增强镁基复合材料过程的示意图[28]
Fig.2 Schematic diagram of graphene reinforced magnesium matrix composites
(4) 其它先进的制备技术
真空蒸发浓缩技术,在真空炉中使1%SiC/Mg-Zn铸锭蒸发出部分镁和锌,可将14 vol.%纳米SiCp均匀分布在基体中,其显微组织如图3所示。纳米SiCp与镁基体形成了半共格界面结合,提高了界面结合力和稳定性,经高压扭转后该复合材料的晶粒进一步细化。其室温屈服强度、弹性模量和塑性分别达到了710 MPa、86 GPa和30%,而且400℃屈服强度高达123 MPa[29]。
图3 SiC纳米颗粒增强镁基复合材料的显微组织[29]
Fig.3 Microstructure of SiC nanoparticles reinforced magnesium matrix composites (a) SEM images of the uniform distribution and dispersion of SiC nanoparticles in magnesium matrix, (b) HRTEM image showing a characteristic interface between a SiC nanoparticle and magnesium matrix
3 界面优化技术
镁基复合材料中的界面,是金属基体与增强体间的“桥梁”,承受载荷时界面起传递载荷的作用。界面的性能决定复合材料在服役过程中载荷能否有效传递,最终影响复合材料的力学性能。而界面性能的优劣除了取决于金属基体的成分、增强体的表面特性和复合材料的制造方法外,还取决于熔融镁合金与增强体的润湿状况[30]。界面结合强度、界面与基体的润湿程度以及界面的性能,都直接影响复合材料的性能。深入研究镁基复合材料的界面反应、优化界面组织结构,对提高镁基复合材料的性能至关重要[31]。
3.1 镁基复合材料的界面反应
界面反应程度,对合适界面结构的形成和性能有很大的影响。制备镁基复合材料时,一定要避免在界面生成大量反应产物、形成聚集的脆性相和脆性层。在Mg-Al合金中添加碳纳米管、碳纤维、石墨烯等碳纳米材料,复合材料中的C,Mg和A1三种元素可能根据碳纤维的石墨化程度、镁合金中Al元素的含量以及制备条件的差异而发生各种不同的化学反应,生成Al4C3相或Al2MgC2相[32, 33]。这两个相都对复合材料性能产生恶劣的影响,在设计材料时要避免或减少此类反应[34]。Bouix发现,在镁合金中加入少量的锆能明显改善基体与碳纤维的润湿性,使合金极易渗入到碳纤维束之间在其表面生成一层很薄的连续碳化物ZrCx;这种化合物的生成比含锰碳化物慢得多,可控制界面反应和界面结合强度[35],为含锆稀土镁基复合材料的研制提供了思路。
3.2 镁基复合材料的界面优化
可通过优化界面控制界面反应,从而改善界面结合。在973~1173 K温度区间SiCp与镁基体的润湿角为76~83°,润湿性较好[36]。而碳纤维在低于1273 K时与镁合金的润湿角仍然大于90°,润湿性能很差,给Cf/Mg复合材料的制备带来了很大的困难[37]。当金属液与纤维不润湿时纤维束之间的毛细作用阻力差增大了浸渗速度差,纤维束间金属液的横向流动对纤维束的挤压使纤维束内的空隙进一步减小,从而使充填更难进行,最终使液态金属的充填不完整[38]。提高熔体温度、添加合金元素、表面改性、表面涂覆或优化制备工艺,可改善增强体和基体界面润湿性[39, 40]。
对于Cf/Mg复合材料,为了最大限度地发挥Cf的性能,理想的界面结合状况使涂层材料与基体润湿性良好且有一定的反应,产生合适的界面结合强度。同时,反应层应该极薄且均匀,避免出现针状有害界面相,而内部的扩散阻挡层可避免碳纤维直接与基体反应而降低性能。
依据这个理论模型,采用溶胶-凝胶法制备了MgO、SiO2、TiO2等涂层。结果表明,TiO2涂层经熔融镁合金高温浸渗后仍然保存了剩余一定厚度的反应阻挡层,隔绝了镁合金中的合金元素与Cf的直接反应。同时,镁基体与TiO2涂层的接触区域非常干净,没有颗粒或针状的界面反应产物,如图4a所示。从图4b可以看出,在镁基体与TiO2涂层间有一层含有深色颗粒的完整过渡反应层,它们的界面反应产物是极薄的反应层。Cf表面的TiO2涂层,有扩散阻挡和弱界面反应的作用。
图4 涂层对Cf/Mg复合材料界面的影响[38]
Fig.4 The effect of coating on the interface of Cf/Mg composite. (a) TiO2 coating Cf/Mg-2% Al composite material, (b) TEM morphology of TiO2 coating Cf/Mg composite interface
袁等在CNTs表面引入纳米MgO,提高了CNTs与AZ91镁合金基体间的界面结合强度[42, 43]。研究发现,CNTs与MgO之间形成了“纳米级接触界面”(Nanoscale-contact bonds)和“扩散结合界面”(Diffused interfacial bonds),如图5a所示,通过“MgO”的桥接CNTs与镁基体形成了强界面结合。同时,MgO/α-Mg界面有如下的晶体取向关系:
,MgO与Mg基体则形成了半共格界面结合(图5b),其原子错配度为6.5%。与此同时,CNTs与α-Mg形成了半共格界面结构,如图5c所示。MgO@CNTs还具有更好的分散性,使分散在基体中的CNTs能更好地发挥应力细化强化、应力转移强化和位错强化等作用,提高复合材料的强度。

图5 CNTs包覆MgO和AZ91-MgO@CNTs复合材料界面结合的示意图[42]
Fig.5 Sketch diagrams of the interface bonding structures of AZ91-MgO@CNTs composite (a) CNTs/MgO, (b) MgO/α-Mg and (c) CNTs/α-Mg interface
MgO微观结构上的区别,是复合材料力学性能差别的主要原因。研究表明,具有织构化的界面反应层能更有效地提高复合材料的力学性能。这种界面反应层织构化导致材料性能提升的结论,也在碳纤维表面具有织构化的BN膜层发现[43]。
TiN也是一种有效的涂层,对比有无TiN涂层的C/Mg复合材料的弯曲强度可以发现,TiN涂层与基体的交互作用增大了Cf和镁基体之间的结合力,提高了有TiN涂层复合材料的横向拉伸性能[44]。但是TiN是一种又脆又硬的间隙化合物,涂层厚度必须严格控制在10~15 nm以避免涂层微裂纹引起的碳纤维凹槽效应。
此外,碳纳米材料常用的金属涂层有Ni、Zn、Ti等。在碳纳米管表面包覆Ni,在制备的镁基复合材料的界面处生成Mg2Ni金属间化合物,可改善CNTs与镁基体的界面结合,使复合材料的显微硬度、抗拉强度和屈服强度分别提高41%,39%和64%[45]。碳纤维表面的镀Ni层改善了基体与增强体的界面结合性,使复合材料的性能提高。使用体积分数为1%的镀Ni短碳纤维制备的复合材料,具有良好力学性能和导热性能。在碳纤维表面镀Zn能有效改善界面结合状态,提高复合材料的弯曲弹性模量,降低材料的热膨胀系数,20~200℃的平均热膨胀系数为2.82×10-6 K-1[46]。但是,金属涂层在纤维预热时容易氧化而失去润湿能力。同时,由于镁基体的化学性质活泼,很容易与金属涂层在复合材料界面处生成脆性的金属间化合物,大大降低复合材料的性能,工艺控制的难度也比较大。
4 镁基复合材料的力学性能
表1列出了目前常见含碳增强体增强镁基复合材料的力学性能。可以看出,镁基复合材料的强度随着增强体的体积分数增加而提高,而且颗粒分布越均匀、尺寸越细小性能的提高越显著。SiCp表面改性后界面的强化作用加之热错配强化、Orowan强化和细晶强化等的综合强化作用,使制备出的镁基复合材料的屈服强度和拉伸强度分别提高到255 MPa和393 MPa[18]。多相混杂增强的镁基复合材料也具有很高的抗拉强度,(1 vol.%纳米+4 vol.%亚微米+10 vol.%微米SiCp)/AZ91D的抗拉强度达到378 MPa,伸长率达到2.3%[48]。与SiCp相比,GNPs、GO和CNTs增强的镁基复合材料具有更加优异的综合力学性能,在提高强度的同时还保证了材料的塑性。但是这类增强体添加的体积分数或质量分数都比较低(3%),并未完全发挥出其提高复合材料力学性能的潜力。采用新工艺制备更高含量、更加均匀分布的碳纳米材料增强镁基复合材料,是今后的一个重要发展方向。使用金属粉末和碳纳米管混合球磨以及在碳纳米管上涂覆镀层,能更好地提高其性能[54]。在CNTs表面引入纳米MgO,MgO@CNTs含量为3.0wt.%的复合材料其抗拉强度、屈服强度和断后伸长率分别为331 MPa、274 MPa和8.6%,比基体分别提高了33.1%、61.2%、53.9%和22.8%,抗拉强度比CNTs表面未改性时提高了30 MPa[41]。
表1 常用含碳增强体增强镁基复合材料的力学性能
Table 1 Mechanical properties of carbon-containing reinforcements reinforced magnesium matrix composites
对于以Cf为增强体的复合材料,其拉伸破坏的主要形式为纤维断裂和界面脱粘。在Mg-Al系合金中,由于Al元素和Cf之间发生了化学反应,随着基体中Al含量的提高界面处的化学反应随之增加,生成的针状Al4C3相影响复合材料的力学性能。
研究表明,单向复合材料的横向拉伸强度,主要取决于纤维在基体中的分布[22]。若纤维分布不均匀则在基体内和界面上产生严重的局部应力和应变集中,使材料的内部损伤过早发生。在纤维分布密集区域的微观裂纹很容易通过自身的发展和相互间的连接而形成细观裂纹,导致材料的破坏。因此,从材料设计和制造的角度,应尽可能降低纤维分布的不均匀性和减小纤维密集区域。对于连续碳纤维增强金属基复合材料,纤维轴相与横向性能的巨大差异导致单向复合材料性能受纤维排列方式的严重影响,呈现出明显的各向异性特征[7]。
宋美慧等用压力浸渗法制备了不同高体分的连续碳纤维和石墨纤维增强镁基复合材料,发现碳纤维与镁合金基体复合良好,浸渗完全,没有气孔和分层等缺陷,碳纤维也没有折断,在镁基体中分布均匀;结果还发现,随着石墨化程度的提高纤维体积分数为60%的复合材料的强度不断提高,拉伸强度从381 MPa提高到了1267 MPa,弹性模量为219~241 GPa;实验进一步发现,对复合材料进行SiC颗粒混杂能有效改善碳纤维与镁合金的润湿,提高复合材料的力学性能,降低横向热膨胀系数和减少热膨胀各向异性[55, 56]。
镁基复合材料受制于镁基的hcp结构,往往塑性较差其强度提高而塑性急剧下降。未来镁基复合材料的设计和制备可模仿自然界中仿生构型,如贝壳的层状结构。对于仿生结构的镁基复合材料,有望同时提高强度、刚度和韧性[57]。模拟鱼皮结构在纤维层中间铺上钛网,从仿生学角度制备Ti/Mg/Cf层状复合材料,不仅强度提高了40 MPa,挠度也大幅度提高[58]。同时,添加的钛网在材料纤维层断裂后有连接和缓冲作用,使复合材料的延伸率提高(达到6%)[59]。在Mg与5.6%体积分数的Ti混合,在显著提高镁合金强度的同时还保留了良好的断后延伸率(约为8%)[60]。在镁合金中添加Cu、Ni等金属也能提高镁基复合材料的强韧性[61, 62],只是较小的添加量使强度的提高有限。添加体积分数较高又大幅度提高复合材料的密度,很难同时满足密度低、强度高、刚度高、韧性好的要求。由此可见,显著提高镁基复合材料的比强度、比刚度并保证其具有优异的韧性,是镁基复合材料亟待解决的一个难题。使用韧性金属材料和纳米增强体混杂作为增强体,可能是一个有效的解决办法。邓等将10 μm、15vol.%SiCp增强的AZ91镁基复合材料与韧性好的Mg-Zn-Y合金(ZW31)板材复合,用挤压、轧制,退火等工艺制备出厚度为1 mm的ZW31/+AZ91/SiCp层压板[63],其工艺流程如图6所示。ZW31合金层能吸收能量并减轻AZ91/SiCp层的应力集中,延缓了裂纹的扩展,退火后层压板的延伸率为3.1%,但是层压板的抗拉强度仅为312 MPa。尽管综合力学性能并没有明显改善,但是为复合材料薄板的制备提供了新方法,也为复合材料的增强增韧途径提供了很好的借鉴。
图6 ZW31/+AZ91/SiCp层压板的制备工艺流程[63]
Fig.6 Process flow diagram of ZW31+AZ91/SiCp laminate fabricated by co-extrusion and hot rolling
5 展望
镁基复合材料的综合性能优异,在各领域有巨大的应用潜力。但是,针对镁基复合材料的研究目前还处于起步阶段。为了进一步提高镁基复合材料的力学性能、促进其应用,需要从以下几个方面着手。
(1) 高性能镁基体合金的优化
基体金属对复合材料的性能有决定性的作用。大量的研究多集中在AZ91、AZ61、AZ31等Mg-Al系合金,这些合金中的Al元素使高性能的碳纳米材料难以加入,不能大幅度提高镁基复合材料的性能。含锆稀土镁合金优异的室温和高温强韧性,正受到极大的关注。如果能将含锆稀土镁合金作为基体合金并添加碳纳米增强相,有望进一步提高镁基复合材料的性能。
(2) 制备多相混杂增强的镁基复合材料
除了多尺度SiCp、CNTs@SiC混杂增强体,还应该开发多相或三维尺度的新型增强体。例如,将一维结构的CNTs与石墨烯适当搭配,制备具有三维尺度结构的新型纳米碳材料增强体(图7a)、具有三维柱状石墨烯/碳纳米管纳米结构增强体(图7b)以及包裹石墨烯的纳米SiC颗粒增强体。使用这类增强体制备的镁基复合材料能发挥各增强体的独特优势,具有更优异的性能。目前有关多相混杂增强镁基复合材料的研究还处于起步阶段,有许多科学问题须要解决。
图7 多相混杂增强示意图
Fig.7 Schematic diagram of multiphase hybrid enhancement (a) Schematic diagram of self-assembly of CNTs and graphene[64], (b) Three-dimensional columnar graphene / carbon nanotube reinforced structure[65]
(3) 用新工艺提高增强体在镁基体中的分散性
增强体的分散性一直是制约复合材料性能的主要因素之一。现阶段常用的手段,有超声分散和机械搅拌。急需探索新分散工艺,如CNTs表面改性等。与传统的外加增强体制备工艺相比,原位合成法避免了增强体表面的污染,与基体的相容性较好,界面结合好。
(4) 新型结构仿生材料
天然生物材料的宏观力学性能显著优于其基本结构单元的简单加和,诸如贝壳、骨骼等在微观上呈现三维相互贯穿式结构。各组成相连通且相互穿插,可实现各组成相在性能与功能上的优势互补,使材料同步强韧化。借鉴天然生物材料的三维互穿微观结构,将镁熔融浸渗至增材制造的镍钛合金骨架,可制备出轻质、高强、高阻尼、高吸能镁-镍钛仿生复合材料。具体的制备工艺及结构,如图8所示[66]。理解自然界神奇“结构-性能关系”,可为今后设计综合性能优异的镁基复合材料提供思路。
图8 新型镁-镍钛仿生复合材料的制备工艺及其三维互穿仿生结构[66]
Fig.8 Formation and 3D architecture of Mg-NiTi interpenetrating-phase composite
参考文献
[1]Song J F, She J, Chen D L, et al.Review latest research advances on magnesium and magnesium alloys worldwide[J]. J. Magn. Alloys., 2020, 8(1): 1[本文引用: 1]
[2]Xu T C, Yang Y, Peng X D, et al.Overview of advancement and development trend on magnesium alloy[J]. J. Magn. Alloys., 2019, 7(3): 536[本文引用: 1]
[3]Alaneme K K, Okotete E A.Enhancing plastic deformability of Mg and its alloys-A review of traditional and nascent developments[J]. J. Magn. Alloys., 2017, 5(4): 460[本文引用: 1]
[4]Wang X J, Hu X S, Liu W Q, et al.Ageing behavior of as-cast SiCp/AZ91 Mg matrix composites[J]. Mater. Sci. Eng. A., 2017, 682: 491
[5]Haghshenas M.Mechanical characteristics of biodegradable magnesium matrix composites: A review[J]. J. Magn. Alloys., 2017, 5(2): 189
[6]You S H, Huang Y D, Ulrich K K, et al.Recent research and developments on wrought magnesium alloys[J]. J. Magn. Alloys., 2017, 5(3): 239[本文引用: 1]
[7]Feng Y, Chen C, Peng C Q, et al.Research progress of magnesium-based composites[J]. Chin. J. Nonferrous. Met., 2017, 27(12): 2385[本文引用: 2]冯艳, 陈超, 彭超群等。镁基复合材料的研究进展[J]. 中国有色金属学报, 2017, 27(12): 2385[本文引用: 2]
[8]He Y, Yuan Q H, Luo L, et al.Current Study and Novel Ideas on Magnesium Matrix Composites[J]. J. aeronaut. Mater., 2018, 38(4): 26[本文引用: 1]何阳, 袁秋红, 罗岚等。镁基复合材料研究进展及新思路[J]. 航空材料学报, 2018, 38(4): 26[本文引用: 1]
[9]Shen K, Zhang Q, Huang ZH, et al.Interface enhancement of carbon nanotube/mesocarbon microbead isotropic composites[J]. Compos. Part A., 2014, 56(1): 44[本文引用: 1]
[10]Xiang SL, Wang XJ, Gupta M, et al.Graphene nanoplatelets induced heterogeneous bimodal structural magnesium matrix composites with enhanced mechanical properties[J]. Sci. Rep., 2016, 6: 38824[本文引用: 1]
[11]Xiang SL, Gupta M, Wang XJ, et al.Enhanced overall strength and ductility of magnesium matrix composites by low content of graphene nanoplatelets[J]. Compos. Part. A., 2017, 100: 183
[12]Wang M, Zhao Y, Wang L D, et al.Achieving high strength and ductility in graphene/magnesium composite via an in-situ reaction wetting process[J]. Carbon., 2018, 139: 954[本文引用: 1]
[13]Ferkel H, Mordike B L.Magnesium strengthened by SiC nanoparticles[J]. Mater. Sci. Eng. A., 2001, 298: 193[本文引用: 1]
[14]Saberi A, Bakhsheshi-Rad H R, Karamian E, et al.Magnesium-graphene nano-platelet composites: Corrosion behavior, mechanical and biological properties[J]. J. Alloys Compd., 2020, 821: 153379[本文引用: 2]
[15]Rashad M, Pan F S, Zhang J Y, et al.Use of high energy ball milling to study the role of graphene nanoplatelets and carbon nanotubes reinforced magnesium alloy[J]. J. Alloys Compd., 2015, 646: 223[本文引用: 1]
[16]Rashad M, Pan F S, Lin D, et al.High temperature mechanical behavior of AZ61 magnesium alloy reinforced with graphene nanoplatelets[J]. Mater. Des., 2016, 89: 1242[本文引用: 2]
[17]Li C P, Wang Z G, Wang H Y, et al.Fabrication of nano-SiC particulate reinforced Mg-8Al-1Sn composites by powder metallurgy combined with hot extrusion[J]. J. Mater. Eng. Perform., 2016, 25: 5049[本文引用: 1]
[18]Li C P, Wang Z G, Zha M, et al.Effect of pre-oxidation treatment of nano-SiC particulates on microstructure and mechanical properties of SiC/Mg-8Al-1Sn composites fabricated by powder metallurgy combined with hot extrusion[J]. Materials., 2016, 9: 964[本文引用: 3]
[19]Rashad M, Pan F S, Asif M, et al.Powder metallurgy of Mg-1Al-1Sn alloy reinforced with low content of graphene nanoplatelets (GNPs)[J]. J. Ind. Eng. Chem., 2014, 20: 4250[本文引用: 1]
[20]Muley S V, Singh S P, Sinha P, et al.Microstructural evolution in ultrasonically processed in situ AZ91 matrix composites and their mechanical and wear behavior[J]. Mater. Des., 2014, 53: 475[本文引用: 1]
[21]Wang X J, Wu K, Huang W X, et al.Study on fracture behavior of particulate reinforced magnesium matrix composite using in situ SEM[J]. Compos. Sci. Technol., 2007, 67: 2253[本文引用: 1]
[22]Shen M J, Wang X J, Zhang M F, et al.Fabrication of bimodal size SiCp reinforced AZ31B magnesium matrix composites[J]. Mater. Sci. Eng. A., 2014, 601: 58[本文引用: 2]
[23]Shen M J, Wang X J, Li C D, et al.Effect of bimodal size SiC particulates on microstructure and mechanical properties of AZ31B magnesium matrix composites[J]. Mater. Des., 2013, 52: 1011[本文引用: 1]
[24]Qiu X.Microstructure and Mechannical Properties of SiCp/AZ91 Magnesium Matrix Composites Fabricated By Squeeze Casting[D]. Harbin: Harbin Institute of Technology, 2006[本文引用: 1]邱鑫。挤压铸造SiCp/AZ91镁基复合材料的显微结构与性能[D]. 哈尔滨: 哈尔滨工业大学, 2006[本文引用: 1]
[25]Zhang C L.Study on fabrication, microstructure and properties of Cf/Mg composites[D]. Harbin: Harbin Institute of Technology, 2017[本文引用: 1]张春雷。Cf/Mg复合材料的制备与组织性能研究[D]. 哈尔滨: 哈尔滨工业大学, 2017[本文引用: 1]
[26]Wu G H, Song M H, Xiu Z Y, et al.Microstructure and Properties of M40 Carbon Fibre Reinforced Mg-Re-Zr Alloy Composites. J. Mater. Sci. Technol[J]. J. Mater. Sci. Technol., 2009, 25 (03): 423426[本文引用: 1]
[27]Du X, Du W B, Wang Z H, et al.Ultra-high strengthening efficiency of graphene nanoplatelets reinforced magnesium matrix composites[J]. Mater. Sci. Eng. A., 2018, A711: 633[本文引用: 1]
[28]Li C D, Wang X J, Liu W Q, et al.Microstructure and strengthening mechanism of carbon nanotubes reinforced magnesium matrix composite[J]. Mater. Sci. Eng. A., 2014, A597: 264[本文引用: 2]
[29]Chen L Y, Xu J Q, Choi H, et al.Processing and properties of magnesium containing a dense uniform dispersion of nanoparticles[J]. Nature., 2015, 528(7583): 539[本文引用: 2]
[30]Liu G J, Li W F, Du J.Investigation on wettability of Al-Mg metal matrix composites[J]. Foundry., 2006, 55(9): 911[本文引用: 1]刘贯军, 李文芳, 杜军。铝、镁基复合材料的润湿性探究[J]. 铸造, 2006, 55(9): 911[本文引用: 1]
[31]Wang T, Huang X F, Liang Y, et al.New ideas of compound reinforcement of particulate reinforced magnesium matrix composite[J]. Hot. Work. Technol., 2008, 37(20): 98[本文引用: 1]王韬, 黄晓锋, 梁艳等。颗粒增强镁基复合材料的增强复合新思路[J]. 热加工工艺, 2008, 37(20): 98[本文引用: 1]
[32]Russell-Stevens M, Todd R, Papakyriacou M.Microstructural analysis of a carbon fibre reinforced AZ91D magnesium alloy composite[J]. Surf. Interface Anal., 2005, 37(3): 336[本文引用: 1]
[33]Viaia J C, Claveyrolas G, Bosselet F.The chemical behaviour of carbon fibres in magnesium base Mg-Al alloys[J]. J. Mater. Sci., 2000, 35(7): 1813[本文引用: 1]
[34]Feldhoff A, Pippel E, Woltersdorf J. et al.Interface engineering of carbon-fiber reinforced Mg-Al alloys[J]. Adv. Eng. Mater, 2000, 2(8): 471[本文引用: 1]
[35]Bouix J, Berthet M P, Bosselet F, et al.Physico-chemistry of interfaces in inorganic-matrix composites[J]. Compos. Sci. Technol., 2001, 61(3): 355[本文引用: 1]
[36]Dan Z, Ping S, Shi L, et al.Wetting and evaporation behaviors of molten Mg on partially oxidized SiC substrates[J]. Appl. Surf. Sci., 2010, 256(23): 7043[本文引用: 1]
[37]Wu F, Zhu J, Chen Y, et al.The effects of processing on the microstrues and properties of Gr/Mg composites[J]. Mater. Sci. Eng. A., 2000, 277(1-2): 143[本文引用: 1]
[38]Xia C J.Interface tailoring in coated carbon fiber reinforced magnesium alloy composites[D]. Shanghai: Shanghai Jiao Tong University, 2013[本文引用: 2]夏存娟。涂层碳纤维镁基复合材料的界面控制[D]. 上海: 上海交通大学, 2013[本文引用: 2]
[39]Contreras A, Leonb C A, Drew R A L, et al.Wettability and spreading kinetics of Al and Mg on TiC[J]. Scr. Mater., 2003, 48(12): 1625[本文引用: 1]
[40]Uozumi H, Kobayashi K, Nakanishi K, et al.Fabrication process of carbon nanotube/light metal matrix composites by squeeze casting[J]. Mater. Sci. Eng. A., 2008, 495(1-2): 282[本文引用: 1]
[41]Yuan Q H, Zeng X S, Liu Y, et al.Microstructure and mechanical properties of AZ91 alloy reinforced by carbon nanotubes coated with MgO[J]. Carbon., 2016, 96: 843[本文引用: 1]
[42]Yuan Q H, Zhou G H, Liao L, et al.Interfacial structure in AZ91 alloy composites reinforced by graphene nanosheets[J]. Carbon, 2018, 127: 177[本文引用: 4]
[43]Reischer E, Pippel J, Woltersdorf G, et al.Carbon fibre-reinforced magnesium: Improvement of bending strength by nanodesign of boron nitride interlayers[J]. Mater. Chem. Phys., 2007, 104(1): 83-87[本文引用: 2]
[44]Korner C, Schaff W, Ottmuller M, et al.Carbon long fiber reinforced magnesium alloys[J]. Adv. Eng. Mater., 2000, 2 (6): 327[本文引用: 1]
[45]Nai M H, Wei J, Gupta M.Interface tailoring to enhance mechanical properties of carbon nanotube reinforced magnesium composites[J]. Mater. Des., 2014, 60(8): 490[本文引用: 1]
[46]Lu P, Xia C J, Wang H W, et al.Study on zinc-coated Cf /Mg composite[J]. Hot. Work. Technol., 2009, 38(10): 122[本文引用: 1]鲁鹏, 夏存娟, 王浩伟等。Zn涂层碳纤维增强镁基复合材料的研[J]. 热加工工艺, 2009, 38(10): 122[本文引用: 1]
[47]Wang X, Liu W, Hu X, et al.Microstructural modification and strength enhancement by SiC nanoparticles in AZ31 magnesium alloy during hot rolling[J]. Mater. Sci. Eng. A., 2018, 715: 49[本文引用: 1]
[48]Shen M J, Wang X J.Ying T,et al. Characteristics and mechanical properties of magnesium matrix composites reinforced with micron/submicron/nano SiC particles[J]. J. Alloys. Compd., 2016, 686: 831[本文引用: 3]
[49]Rashad M, Pan F, Liu Y, et al.High temperature formability of graphene nanoplatelets-AZ31 composites fabricated by stir-casting method[J]. J. Magn. Alloys., 2016, 4(4): 270[本文引用: 1]
[50]Du X, Du W B, Wang Z H, et al.Ultra-high strengthening efficiency of graphene nanoplatelets reinforced magnesium matrix composties[J]. Mater. Sci. Eng. A., 2018, 711: 633[本文引用: 2]
[51]Yuan Q H, Qiu Z Q, Zhou G H, et al.Interfacial design and strengthening mechanisms of AZ91 alloy reinforced with in-situ reduced graphene oxide[J]. Mater. Charact., 2018, 138: 215[本文引用: 2]
[52]Han G, Wang Z, Liu K, et al.Synthesis of CNT-reinforced AZ31 magnesium alloy composites with uniformly distributed CNTs[J]. Mater. Sci. Eng. A., 2015, 628: 350
[53]Liang J, Li H, Qi L, et al.Fabrication and mechanical properties of CNTs/Mg composites prepared by combining friction stir processing and ultrasonic assisted extrusion[J]. J. Alloys Compd., 2017, 728[本文引用: 1]
[54]Yuan Q H, Qiu Z Q, Zhou G H, et al.Interfacial design and strengthening mechanisms of AZ91 alloy reinforced with in-situ reduced graphene oxide[J]. Mater. Charact., 2018, 138: 215[本文引用: 3]
[55]Song M H, Wu G H, Chen G Q, et al.Thermal expansion and dimensional stability of unidirectional and orthogonal fabric M40/AZ91D composites[J]. Trans. Nonferrous Met. Soc. China., 2010, 20(1): 47[本文引用: 1]
[56]Song M H, Wu G H, Yang W S, et al.Mechanical Properties of Cf/Mg Composites Fabricated by Pressure Infiltration Method[J]. J. Mater. Sci. Technol., 2010, 26(10): 931[本文引用: 1]
[57]Wang X J, Xiang Y Y, Hu X S. et al.Recent progress on magnesium matrix composites reinforced by carbonaceous nanomaterials[J]. Acta. Metall. Sin., 2019, 55(1): 73[本文引用: 1]王晓军, 向烨阳, 胡小石等。碳纳米材料增强镁基复合材料研究进展[J]. 金属学报, 2019, 55(1): 73[本文引用: 1]
[58]Jiang B.Study on fabrication, microstructure and properties of Cf/Mg composites[D]. Harbin: Harbin Institute of Technology, 2016[本文引用: 1]蒋博。Cf/Mg复合材料制备与组织性能研究[D]. 哈尔滨: 哈尔滨工业大学, 2016[本文引用: 1]
[59]Zhang C L.Study on fabrication, microstructure and properties of Cf/Mg composites[D]. Harbin: Harbin Institute of Technology, 2016[本文引用: 1]张春雷。Cf/Mg复合材料的制备与组织性能研究[D]. 哈尔滨: 哈尔滨工业大学, 2016[本文引用: 1]
[60]Sankaranarayanan S, Jayalakshmi S, Gupta M.Hybridizing micro-Ti with nano-B4C particulates to improve the microstructural and mechanical characteristics of Mg-Ti composite[J]. J. Magn. Alloys., 2014, 2(1): 13[本文引用: 1]
[61]Hassan S F, Gupta M.Development of high strength magnesium based composites using elemental nickel particulates as reinforcement[J]. J. Mater. Sci., 2002, 37(12): 2467[本文引用: 1]
[62]Wang W L, Gupta M.Development of Mg/Cu nanocomposites using microwave assisted rapid sintering[J]. Compos. Sci. Technol., 2007, 67(7/8): 1541[本文引用: 1]
[63]Zhang X C, Wang C J, Deng K K, et al.Fabrication, microstructure and mechanical properties of the as-rolled ZW31/PMMCs laminate[J]. Mater. Sci. Eng. A., 2019, 761: 138043[本文引用: 2]
[64]Yuan Q H.Preparation and mechanical properties of AZ91 alloy composite reinforced with nano-carbon materials[D]. Nanchang: Nanchang University, 2016[本文引用: 1]袁秋红。纳米碳材料增强AZ91镁基复合材料制备与性能研究[D]. 南昌: 南昌大学, 2016[本文引用: 1]
[65]Du F, Yu D, Dai L, et al.Preparation of tunable 3D pillared carbon nanotube-graphene networks for high performance capacitance[J]. Chem. Mater., 2011, 23(21): 4810[本文引用: 1]
[66]Zhang M Y, Yu Q, Liu Z Q, et al.3D printed Mg-NiTi interpenetrating-phase composites with high strength, damping capacity, and energy absorption efficiency[J]. Sci. Adv. 2020, 6: 1[本文引用: 2]
免责声明:本网站所转载的文字、图片与视频资料版权归原创作者所有,如果涉及侵权,请第一时间联系本网删除。
相关文章
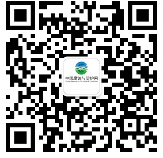
官方微信
《中国腐蚀与防护网电子期刊》征订启事
- 投稿联系:编辑部
- 电话:010-62316606-806
- 邮箱:fsfhzy666@163.com
- 中国腐蚀与防护网官方QQ群:140808414
点击排行
PPT新闻
“海洋金属”——钛合金在舰船的
点击数:7426
腐蚀与“海上丝绸之路”
点击数:5955