玉门炼化总厂常减压蒸馏装置于1995年设计,1997年建成投产。最初是为了炼制低密度,酸值、残炭、硫含量低的轻质原油所设计的,其设计参数以吐哈原油为依据。但是,随着近年来油田的深度开采及加工原油结构调整,原油性质不断趋于重质化、劣质化,玉门炼厂常减压装置加工的原油由设计的吐哈原油逐年变为目前的吐哈中质-塔指-玉门混合原油,加工原油的密度、硫含量和酸值逐年呈现上升的趋势,已接近于含硫含酸原油,给装置安全生产带来了重大隐患。
玉门炼化总厂定时对生产装置进行巡查和调测,发现设备故障等隐患及时处理
原油劣质化后常减压装置操作变化
1 塔顶腐蚀加剧
原油中的盐类在一定温度和水存在下发生强烈的水解反应生成HCl,而原油中的硫化物加热被分解为H2S。在蒸馏过程中产生的HCl和H2S随轻油挥发进入塔顶冷却系统,当冷凝区出现液体水时,HCl溶于水形成稀盐酸。此稀盐酸会对设备造成强烈的腐蚀作用,而H2S的存在又会加强这一影响。
HCl-H2S-H2O腐蚀破坏性很大,对碳钢表现为均匀腐蚀,对0Cr13钢为点腐蚀,对奥氏体不锈钢为应力腐蚀开裂,在玉门常减压装置中具体表现为塔顶管线和塔内顶层塔盘腐蚀加剧、空冷泄漏。
2012年以来玉门炼化常减压装置先后出现3次空冷管束泄漏,全部集中在塔顶低温部位,主要是原油中的氯化物和硫化物受热分解产生的HCl和H2S,在有冷凝水存在时形成酸性环境对设备造成腐蚀,属于典型的HCl-H2S-H2O腐蚀。
2 直馏柴油酸度超标
直馏柴油的酸度会随着所加工原油酸值的变化而变化,原油酸值越高,直馏组分油酸度也随之增高。这直接接影响到成品柴油的酸度。这是由于常压蒸馏是一个物理过程,并不能减少或脱除酸性物质,其中的酸性物质只会随着馏分的轻重进行重新富集与分配。
2012年起常减压装置因原油性质变化,加工出的直馏柴油酸度严重超标,平均达到了12.8mgKOH/100ml,不但具有较强的腐蚀性,而且当直馏柴油与催化裂化柴油调合时,环烷酸与催化裂化柴油中的硫醇及氮化物作用生成胶质和沉渣,使柴油的颜色变深,安定性变差,给总厂柴油调和带来很大难度。
3 加热炉出口泄漏点增多
2013年常减压装置常压炉第三路出口热偶焊缝出现渗油、减压炉第四路进口孔板流量计焊缝出现渗油。主要产生在高温液相和气相混合区域,属于典型的高温部位环烷酸腐蚀。
环烷酸腐蚀受温度、浓度及流速影响较大,主要发生在酸值大于0.5mgKOH/g、温度在220~400℃之间的高温流速介质中。且在H2S和环烷酸共存的环境中,环烷酸会和FeS反应,生成可溶性的Fe(RCOO)2和H2S,破坏FeS保护膜,而生成的H2S又进一步腐蚀金属基体,在350℃时两者相互影响,腐蚀最为严重,在我装置中表现为加热炉出口泄漏点增多,给装置平稳运行埋下了隐患。
4 减压塔高温部位均匀减薄加剧
2013年装置测厚工作中表现较为突出的一个特点就是,减压塔高温部位均匀减薄加剧,主要集中在减五线、清洗油、循环油、减压塔下部,温度基本在250℃~380℃之间,是由原油中所含的有机硫化物热分解生成硫化氢而引起的均匀腐蚀,属于典型的高温硫腐蚀。
典型的高温含硫化合物腐蚀环境存在于常减压蒸馏装置常压塔、减压塔的下部和塔底管道,常压渣油和减压渣油换热器等部位,当温度达到340℃~375℃时,H2S开始分解为H2和S,分解出来的单质硫,活性最强,可直接腐蚀设备,在我装置生产中表现为减压塔高温部位均匀减薄加剧。
5 空气预热器出现内漏
2013年度在加热炉热效率检测结果中出现预热器烟气出口氧含量为8.35%,高于加热炉对流室出口处氧含量4.2%的现象,表明空气预热器内部出现泄漏。
造成上述问题主要原因是,在加工含硫原油时,瓦斯燃烧过程产生大量的SO2和SO3,在换热冷凝时形成硫酸,产生了较严重的硫酸露点腐蚀。
具体应对措施
1 合理优化掺炼比例
常减压蒸馏装置掺炼的原油为混合原油,各种原油性质有较大的差异,因此装置根据自身的特点,选择合适的加工工艺路线,优化原油调和比例,避免含硫高的原油与含酸高的原油混炼,以防止原油中的硫和酸产生的共同效应加剧对设备的腐蚀。
2 改进工艺防腐
造成塔顶冷凝冷却系统低温部位腐蚀主要是原油中的氯化物和硫化物受热分解产生的HCl和H2S,在有冷凝水存在时形成酸性环境对设备造成腐蚀,为了解决上述问题,2011年起,玉门炼化采用超声波破乳——电脱盐技术代替原有的破乳剂脱盐,有效降低了脱后原油盐含量;同时根据原油性质优化了HY8110中和剂缓蚀剂配方来减缓腐蚀,即改进“一脱二注”防腐工艺。
玉门炼化优化传统的“一脱二注”法后原油盐含量降低到2.5mgNaCl/L以下;2013年在改进中和缓蚀剂配方后,常压塔顶冷凝水中的铁离子、氯离子质量浓度分别控制在0.5 mg/L和20 mg/L以下,达到了技术指标。通过监测发现2013年同期常压塔顶的点腐蚀速率平均为0.070 mm/年,属于轻度腐蚀,较2012年有所降低。
3 设备材质升级
选材是防腐的关键,提高材质等级是减缓常减压装置腐蚀最有效的方法。为了能够有效防止腐蚀,在选用设备的材料时,应该根据所处的不同腐蚀部位来选择不同的材料。玉门炼化根据SH/T3096-1999《加工高酸原油重点装置主要设备设计选材导则》以及中石化的《加工高硫原油部分装置在用设备及管道选材指导意见》在2013年大检修中对腐蚀较严重部位进行材质升级;空冷材质升级为09Cr2AlMoRe;对腐蚀严重的部分空冷升级为双相不锈钢2205。对于环烷酸腐蚀严重的炉出口转油线升级为316L,解决常压炉炉管出口高流速下环烷酸的影响。对于减压高温渣油管线升级为Cr5Mo,以应对高温硫腐蚀。
4 直馏柴油加注柴油脱酸剂
针对直馏柴油酸度超标这一情况,2012年9月常减压车间制定了常二线柴油加注复合脱酸剂方案,在柴油管线增加管道静态混合器,增加混合强度,解决常压直馏柴油酸度高的问题。改造后常二线柴油酸度明显降低,达到国家规定的不大于7 mgKOH/100ml的指标。
5 建议减压高温部位加注缓蚀剂
目前中石化已研制出了缓蚀性能优于美国同类产品的高效高温缓蚀剂。经实验证明:该缓蚀剂不仅可用于解决高温环烷酸酸腐蚀问题,而且对高温硫腐蚀也有很好的缓蚀作用。乌石化二套常减压装置在减四线抽出部位注入GX-195高温缓蚀剂,铁离子浓度由197mg/l,下降到11.4mg/l。乌石化一套常减压装置试用LX-213高温缓蚀剂后,蜡油中铁离子含量下降明显,说明减压高温部位加注缓蚀剂是应对高硫、高酸原油设备管道腐蚀的有效手段。
效果监测
针对装置存在的腐蚀类型和存在部位,2013年大检修时选取塔顶中间罐、冷却器、空冷器露点腐蚀区,常压侧线、加热炉出口环烷酸腐蚀区,减压侧线高温硫腐蚀区等18个点进行腐蚀在线监测改造,使用15个精密电阻探针和3个PH计系统涵盖了常减压装置几种腐蚀的典型部位,提供的数据能直观的反应出某段时间及某段管线的腐蚀速率和腐蚀裕量,能客观地反应温度和PH值大小对腐蚀的影响。
通过技术改造,目前常减压装置重点部位腐蚀率均满足HG/T20580-2011上给出的化工设备腐蚀速率范围(0.13~0.25mm/a)腐蚀裕量充足,表明装置在2013年大检修中材质升级合理、防腐措施到位,现阶段玉炼常减压装置具备加工含酸、含硫原料的条件。
责任编辑:田双
《中国腐蚀与防护网电子期刊》征订启事
投稿联系:编辑部
电话:010-62313558-801
邮箱:ecorr_org@163.com
中国腐蚀与防护网官方 QQ群:140808414
免责声明:本网站所转载的文字、图片与视频资料版权归原创作者所有,如果涉及侵权,请第一时间联系本网删除。
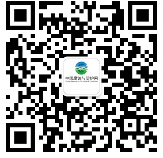
官方微信
《腐蚀与防护网电子期刊》征订启事
- 投稿联系:编辑部
- 电话:010-62316606-806
- 邮箱:fsfhzy666@163.com
- 腐蚀与防护网官方QQ群:140808414