案例1:核电疏水阀蒸汽管线泄漏原因分析与预防(服役环境考虑不周)
1. 事故背景
某核电站近几年接连发生常规岛X机组疏水阀蒸汽管线泄漏事故,泄漏发生于相同机组的不同管线,出现泄漏的时间有长有短,泄漏位置均与焊缝有关,有焊缝与直管交界处,有焊缝与弯管交界处,也有焊缝区域,在靠近焊缝弯管内表面的气蚀坑中也发现了裂纹。
2. 失效部位
管线开裂泄漏情况见图1a)。宏观分析时发现焊接部位钢管内壁的颜色不同,焊缝一边颜色较亮,呈银灰色,而另一边覆盖着褐色氧化腐蚀产物,见图1b);焊接下塌比较明显,焊缝上存在蜂窝状孔洞,而另一侧焊缝未见此特征,见图1c);焊缝与母材交界处存在孔洞以及起源于孔洞的微裂纹,见图1d)。
图1 泄漏管线宏微观形貌
3. 失效分析
采用有限元对管线的实际工况进行数字模拟,并经过现场勘查、事故调查、现场取样和全面的理化分析及综合分析,最后得出管线发生泄漏失效的原因如下:管线内高温水流经弯管或焊接下塌处时,产生了局部负压区,高温水流经过这些区域时因压力突然下降,瞬间气化变为气泡,气泡爆炸时产生巨大的爆破应力,发生空泡腐蚀,同时也引起管线振动,当其频率与管线固有频率成整数倍时,管线还发生共振,振动幅度加大,导致管线在焊缝这个“薄弱环节”部位发生了腐蚀疲劳开裂,裂纹穿透整个管壁后,管线发生泄漏。
4. 改进措施
针对该次失效分析的结论,提出了三个预防措施:
① 提高焊接质量,控制焊接下塌尺寸,减少空泡腐蚀发生的可能;
② 增加管线支撑架或改变管线规格,以改变管线固有频率,防止发生共振;
③ 在管线上安装减震设施实时监测,依据监测结果及时采取纠正措施,避免管线产生共振。
5. 整改后
核电机组根据该失效分析报告的结论和提出的预防措施,结合机组的实际情况,加强了焊接质量控制,并将管线的壁厚由3mm改为5mm,改变了系统的固有频率。经过一年多的实际运行,未再发生管线泄漏事故。
案例2:装卸料机料仓Ferguson齿轮随动滚轮顶丝断裂失效分析与预防(安装不合理)
1. 事故背景
断裂的顶丝服役于核电燃料装卸料机料仓Ferguson齿轮随动滚轮,该顶丝表面采取了“发黑”处理,安装使用不到两年,在设备维护和保养时发现断裂,见图2a)。
图2 断裂顶丝宏观形貌及有限元模拟结果
2. 事故调查与分析
经事故调查,在不同的设备上共发现有10多个顶丝断裂,其装配情况和断裂位置基本相同。该顶丝在设备上的安装服役示意图见图2b),正常情况下,顶丝依靠其头部的圆锥体顶住滚轮螺纹部分的键槽部位,起定位和预防滚轮转动的作用。顶丝拧进去的深度大约为16mm,露在外面大约为8mm,顶丝总长度为25.4mm。顶丝拧紧后再在露出部分紧固一个螺母,其目的是防止顶丝松动脱落。
经调查,安装螺母时没有对扭矩作要求,原则上拧紧即可。在使用过程中,顶丝和滚轮会一起反复浸入齿轮箱中的润滑油中。
按照实际顶丝的形状、尺寸,以及装配情况进行几何建模和网格划分,然后采用Ansys软件对顶丝的受力情况进行模拟分析,分析结果如下:
①假设安装时没有螺母,最大拉应力出现在锥部第一扣螺纹处,见图2c);
②实际装配情况下,即顶丝外部有螺母时,最大拉应力出现在螺母与滚轮架接合处,见图2d),该最大受力位置与实际断裂位置相吻合。
3. 失效分析
根据顶丝的理化检验结果和断口形貌分析结果判断,该顶丝断裂性质为氢致延迟断裂。
该顶丝的实际使用特点类似于螺栓,其硬度测试结果为476~482HV0.5,参考GB/T 3098.1-2010《紧固件机械性能螺栓、螺钉和螺柱》,该硬度已经超出了12.9级螺栓的维氏硬度范围385~435HV10。螺栓的强度等级越高,其对氢脆型断裂就越敏感。
由受力分析结果可知,顶丝未加装螺母时,服役过程中靠近锥部第一扣螺纹侧面承受最大拉应力,但该部位顶丝的中心部位承受压应力,见图2c);若安装扭矩较大时,靠近锥部的螺牙可能会发生断裂,但顶丝整体不会发生断裂。
加装螺母后,顶丝受力特点与螺栓相似,服役过程中承受恒定拉应力,有限元分析结果表明最大拉应力出现在螺母与滚轮架接合处,见图2d),该最大受力位置与顶丝实际断裂位置相吻合。
4. 改进措施
针对该次失效分析的结论,提出了以下两个预防措施:
① 不加装螺母,改用其他方法来预防顶丝滑脱;
② 降低顶丝的硬度(相当于降低螺栓的强度等级),安装时增加扭矩要求。
对于使用方来说,建议①比较容易实施,可从根本上解决问题;建议②涉及的实际硬度和扭矩都是未知数,需要进一步验证,实施起来相对比较困难。
5. 整改后
后来用户从实际设备的整体考虑,将该顶丝材料改为304不锈钢(实际上是降低了螺栓强度等级),经过两年多的实际运行,未再出现类似的断裂事故。
案例3:地铁列车减震总成中心销失效分析与预防(优化设计)
1. 事故背景与失效件宏观形貌
地铁列车减震总成上的中心销在列车运行21a(年)后发生了断裂,断裂位置见图3a),断口形貌见图3b)。中心销材料为34CrNiMo6钢,图纸技术要求抗拉强度为800~1080MPa,已断裂部分的螺母高度经测量为57mm,断裂的螺纹端长度为90mm。
图3 断裂中心销宏观形貌及示意图
经实际称重,断裂部分的总质量为2.965kg,见图3c);断裂位于螺纹根部的过渡圆角处,该部位外圆尺寸为?46mm,过渡圆角半径为R2.5mm,见图3d),螺纹部分公称直径为56mm。
图3e)为中心销实际装配情况,可以看到正常服役时,断裂的螺纹部分位于列车底部,处于悬空状态,见椭圆形标识。列车静止时,断裂部位只受到螺纹部分和螺帽的重力作用。
2. 理化检验
由理化检验结果可知:断裂中心销的化学成分和拉伸性能符合技术要求;实际晶粒度等级为9.5~10级,夹杂物评定结果为A2.0,A1.0e,B0,C0,D0.5,横向低倍和纵向低倍检验均未见明显异常,断裂源处、断口处的显微组织与远离断口处基体的一致,均为回火索氏体+少量铁素体,断口上可观察到少量夹杂物;断口宏观分析和扫描电镜(SEM)微观分析均表明该中心销断裂性质为疲劳断裂,疲劳源位于螺纹端与销杆的过渡圆角处,该部位存在周向分布的机械加工刀痕,过渡圆角半径经测量符合技术要求,疲劳断裂源相对分布,为双向弯曲疲劳断裂。
3. 现场勘查
现场勘查时发现,正常装配情况下,螺纹部分处于悬空状态,但列车在启动或刹车时会产生加速度,悬空的螺纹部分会受到惯性力的作用,力的大小遵循牛顿第二定律,即F=ma(F为作用力,m为质量,a为加速度),该力的大小与断裂部分的质量以及加速度均成正比。悬空的螺纹部分类似于一个悬臂梁结构,螺纹端与销杆过渡圆角处承受最大的弯矩和弯曲应力。过渡圆角处外圆直径为46mm,螺纹外径为56mm,可见断裂处尺寸相对较小,R2.5mm处会产生应力集中,该部位的周向加工刀痕还会增加应力集中的程度,因而该部位容易萌生疲劳裂纹,成为疲劳裂纹源。
4. 失效原因
该中心销断裂失效分析的结论为:
① 断裂的中心销材料质量检验结果符合相关技术要求;
② 中心销断裂性质为双向弯曲疲劳断裂,列车在启动或刹车时产生的加速度导致悬空的螺纹部分产生惯性力,该力的大小遵循牛顿第二定律,过渡圆角处较小的尺寸以及该部位的周向加工刀痕均会增加该处应力集中的程度,使该处容易萌生疲劳裂纹。
5. 改进措施
根据该失效分析结论和现场勘查情况,提出的预防措施如下:
①增大过渡圆角处的外圆尺寸?值和过渡圆角半径R值;
③ 提高过渡圆角位置的表面加工质量,减轻螺母的质量。
6. 整改后
由于中心销的原设计寿命为30a,断裂时已经服役了21a,考虑到减震总成的整体设计和结构,设计方同意将原来的R2.5mm提高到R5mm,用垫片解决了螺纹根部的紧固问题。各种理论计算结果表明:改进后的中心销其疲劳寿命有了较大幅度的提高,完全可以达到30a的使用寿命。
免责声明:本网站所转载的文字、图片与视频资料版权归原创作者所有,如果涉及侵权,请第一时间联系本网删除。
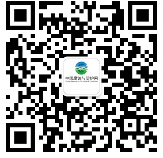
官方微信
《腐蚀与防护网电子期刊》征订启事
- 投稿联系:编辑部
- 电话:010-62316606-806
- 邮箱:fsfhzy666@163.com
- 腐蚀与防护网官方QQ群:140808414