我国目前正在大力发展核电,其主要堆型为压水堆(PWR)。PWR核电站在运行过程中,由于停堆/启堆、热分层等,压力边界(如蒸汽发生器、压力容器、主管道)可能遭受腐蚀疲劳(CF)损伤[1~5]。美国电力研究院(EPRI)[1]统计表明,疲劳失效案例随核电站服役年限增长而逐步增加。核电站中很多部位可能发生疲劳失效,其中管道系统、阀门、小孔径管道是疲劳损伤最敏感部分。一旦CF裂纹穿透服役构件壁厚发生泄漏或瞬断,就会严重影响核电站运行的经济性和安全性。因此,环境疲劳是核电站关键设备设计、安全评审、延寿评估必须考虑的要素。美国核管会(NRC)于2007年颁布了RG1.207导则[6],要求新建核电站疲劳设计必须考虑轻水堆(LWR)环境的影响。基于此,世界上各核电大国最近几十年研究了LWR环境对核电结构材料(低合金钢、奥氏体不锈钢和镍基合金)疲劳性能的影响。实验结果[2~4,7,8]表明,抗腐蚀性能良好的奥氏体不锈钢(304、316不锈钢)在特定实验条件下,疲劳寿命可能下降10~100倍。亟需建立充分考虑LWR环境因素的疲劳设计模型,弥补美国机械工程师协会(ASME)疲劳设计曲线[9]未考虑LWR环境的影响而存在的安全裕度不足的缺陷。基于几十年的环境疲劳数据积累,美国阿贡实验室(ANL)建立了考虑LWR环境因素的核电结构材料ANL模型[2,3],日本核能安全组织(JNES)建立了JNES模型[4],法国建立了《压水堆核岛机械设备设计和建造规则》(RCC-M)亦给出了环境疲劳模型[10]。ASME也考虑在ASME设计曲线中植入LWR环境的影响,提出了Code Case N-761[11]和Code Case N-792[12]。然而,核电结构材料高温高压水环境疲劳数据主要基于标准圆棒状疲劳试样。在实际服役过程中,对疲劳损伤敏感的小孔径管道内部流通的高温高压水,使管道承受周向张力。很少有利用管状疲劳试样(内部流通高温高压水,外部与空气接触)研究核电结构材料高温高压水腐蚀疲劳性能的报道。基于此,本工作设计了一种管状疲劳试样,更真实地模拟核电站中小孔径管道服役状况,采用轴向应变控制模式,研究了316LN不锈钢的高温高压水腐蚀疲劳性能。
1 实验方法
实验材料为核电站一回路主管道用锻造316LN不锈钢,化学成分(质量分数,%)为:C 0.013,Cr 17.08,Ni 12.92,Mo 2.18,Mn 1.33,Si 0.27,N 0.12,P 0.021,S 0.005,Fe余量。将316LN不锈钢金相样品经过400~2000号砂纸水磨,用粒度为2.5 μm的研磨膏抛光至表面无划痕,利用酒精洗干净后在10% (质量分数)的草酸溶液中电解(6 V)蚀刻60~90 s。利用Observer.Z1m金相显微镜(OM)观察其微观组织。
设计并加工了一种管状疲劳试样,如图1所示。管状试样标距段长度为20 mm,外径为10 mm,内径为5 mm,标距段内外表面光洁度为0.2 μm。在疲劳试样两端设置V型密封口以及密封螺纹孔。图2为高温高压循环水腐蚀疲劳实验装置示意图,加载系统为EHF-EV051k1-020-1A疲劳试验机。利用比例积分微分控制(proportional integral differential,PID)方法,调节吹入储水罐中的高纯N2 (99.99%)和空气比例,控制溶液中的溶解氧值;利用高压泵以及背压阀控制系统中溶液的压力;利用PID方法控制系统中的温度,控温精度为± 2℃。系统中所有管道材质为304或316不锈钢。将管状试样与系统进水口与出水口连接,将热电偶粘贴在管状试样标距段表面,高温引伸计安装于管状试样标距段,安装示意图如图3所示。采用应变控制、三角波,实验参数如表1所示。疲劳寿命定义为峰值拉应力下降至最大峰值拉应力的88%对应的循环周次(或者疲劳裂纹穿透壁厚发生泄漏时对应的循环周次)。
图1 316LN不锈钢管状试样形状尺寸示意图
图2 高温高压循环水腐蚀疲劳装置示意图
图3 316LN不锈钢管状试样安装示意图
表1 腐蚀疲劳实验参数
腐蚀疲劳实验完成后,选取典型的疲劳试样,在空气中利用EHF-EV051k1-020-1A疲劳试验机将试样疲劳加载至断裂。利用Leica S6体视显微镜或INSPECT F50扫描电镜(SEM)观察腐蚀疲劳断口、疲劳裂纹以及腐蚀产物形貌。
2 实验结果
图4为316LN不锈钢的显微组织的OM像。为典型的奥氏体,基体上分布着孪晶。
图4 316LN不锈钢显微组织的OM像
图5为316LN不锈钢管状试样在不同应变幅、应变速率条件下的高温高压水腐蚀疲劳数据。所有数据点位于ASME平均曲线下方,高温高压水环境降低316LN不锈钢的疲劳寿命;所有数据点位于ASME设计曲线上方,说明在本实验条件下,316LN不锈钢有足够的安全裕度。图中亦给出了标准棒状试样(标距段长度为16 mm,直径为8 mm)的高温高压水腐蚀疲劳数据[13]。通过对比得出,管状试样高温高压水疲劳寿命与棒状试样结果一致。内部高压水(12 MPa)对管状试样附加的周向张力,对316LN不锈钢环境疲劳寿命几乎无影响。图6为应变速率对316LN不锈钢高温高压水腐蚀疲劳寿命的影响。实验结果表明,316LN不锈钢环境疲劳寿命随应变速率降低而降低。在应变速率为0.004 × 10-2 s-1时,与高温(325℃)空气中的疲劳寿命相比,其疲劳寿命下降约10倍,环境效应显著。图6中亦包含了文献[3]中报道的应变速率对316LN不锈钢(标准棒状试样)高温高压水环境疲劳寿命的影响数据。对比表明,应变速率对管状试样与棒状试样环境疲劳寿命的影响规律一致。因此,将基于标准棒状试样获得的环境疲劳数据,用来评价核电站小孔径管道的环境疲劳损伤是合理可行的。实验结果同时表明,利用管状试样替代标准棒状试样评价核电关键设备的高温高压水腐蚀疲劳性能是可行的。利用标准棒状试样开展高温高压水低周疲劳实验,需要将试样安装于高温高压釜内,试样完全浸泡在高温高压水环境中,导致控制/测量疲劳试样标距段应变难度极大。而利用管状试样开展高温高压水腐蚀疲劳实验,管状试样内部流经高温高压水,外部与空气接触,可利用高温引伸计控制/测量管状试样应变,提高实验精度。
图5 316LN不锈钢管状试样和标准棒状试样[13]高温高压水腐蚀疲劳数据
图6 应变速率对316LN不锈钢管状试样疲劳寿命的影响
图7为316LN不锈钢高温高压水腐蚀疲劳过程中峰值载荷与循环周次之间的关系。在疲劳开始时,表现为循环硬化,之后为循环软化直至开裂。在低应变速率条件下(0.004 × 10-2 s-1)的峰值拉应力高于高应变速率条件下(0.4 × 10-2 s-1)的。据文献[7,14~16]报道,316LN不锈钢在320℃会发生动态应变时效,且随应变速率降低而更加显著,表现出屈服强度、抗拉强度升高以及变形局域化等特征。因此,在低应变速率条件下,动态应变时效导致316LN不锈钢峰值拉应力升高,可能降低材料的低周疲劳性能。
图7 316LN不锈钢高温高压水腐蚀疲劳过程中峰值载荷与循环周次之间的关系
图8为不同应变速率条件下管状试样疲劳断口宏观形貌。图中深色部分为高温高压水环境中的断口,白色部分为高温高压水腐蚀疲劳实验完成后在空气中疲劳断裂的断口。疲劳裂纹萌生于管状试样内壁,向外壁扩展。图9为不同应变速率条件下管状试样疲劳裂纹源形貌。所有应变速率条件下,均为多裂纹源萌生特征。裂纹源均呈扇形花样,随应变速率降低,扇形花样越明显。随着应变速率下降至0.004 × 10-2 s-1,裂纹源呈现准解理断裂特征,表明随应变速率降低,环境效应对裂纹萌生促进作用更加显著。图10为不同应变速率条件下管状试样腐蚀疲劳断口疲劳辉纹特征。腐蚀疲劳裂纹萌生区域,断口形貌为扇形花样,有准解理开裂特征,无明显的疲劳辉纹特征;当裂纹扩展约200 μm,疲劳断口上开始呈现疲劳辉纹特征(图10a~c),随着疲劳裂纹继续扩展,疲劳辉纹间距增加(通常疲劳辉纹间距代表一个循环周期疲劳裂纹的扩展量),表明疲劳裂纹扩展速率随裂纹长度增加而增加。随着应变速率降低,疲劳辉纹间距增加,表明疲劳裂纹扩展速率增加,与随应变速率降低疲劳寿命降低一致(图6)。随着应变速率降低,疲劳断口准解理开裂更加显著,疲劳辉纹特征逐步弱化(图10)。
图8 不同应变速率条件下316LN不锈钢管状试样疲劳断口宏观形貌
图9 不同应变速率条件下316LN不锈钢管状试样疲劳裂纹源形貌
图10 不同应变速率条件下316LN不锈钢管状试样断口不同位置处(与裂纹源距离)的疲劳辉纹特征
图11为316LN不锈钢管状试样高温高压水腐蚀疲劳实验后(0.004 × 10-2 s-1)内表面二次裂纹以及氧化物形貌。试样内表面有较多二次裂纹,表明高温高压水环境促进疲劳裂纹萌生,316LN不锈钢在高温高压水环境中为多裂纹源起始特征。试样表面覆盖“疖状”氧化物,主要为Fe、Cr、Ni的氧化物。在静态或流速很小的高温高压水环境中,316LN不锈钢表面生成了内层致密的富Cr氧化物以及外层富Fe、Ni的尖晶石氧化物颗粒[2,17]。在本工作中,管状试样内部流速约为0.142 m/s,外层尖晶石氧化物颗粒可能被冲刷掉,难以在试样表面聚集。
图11 316LN不锈钢管状试样(0.004 × 10-2 s-1)内表面二次裂纹以及氧化物
3 分析讨论
核级奥氏体不锈钢在高温高压水环境中,疲劳寿命分为疲劳裂纹萌生寿命与扩展寿命。疲劳裂纹萌生阶段对应微观小裂纹扩展,微观小裂纹长度一般为150~250 μm[2,3],该裂纹对材料的微观组织特征(如晶界以及夹杂物)比较敏感[2,18,19],以裂纹扩展速率随裂纹长度增加而降低为特征。如载荷低于临界值,微观小裂纹停止扩展。316LN不锈钢管状试样高温高压水腐蚀疲劳裂纹扩展至200 μm左右时,疲劳断口开始出现疲劳辉纹特征。因此,在本实验中微观小裂纹长度约为200 μm。对于核级奥氏体不锈钢,高温高压水腐蚀疲劳微观小裂纹主要萌生于驻留滑移带[7,19~22],裂纹源区域呈扇形花样,尤其在低应变速率条件下,为准解理开裂特征(图9)。力学因素与高温高压水环境因素交互作用促进微观小裂纹萌生与扩展。在高温高压水环境中,316LN不锈钢表面生成致密的富Cr氧化膜以及富Fe尖晶石颗粒[2,17],在疲劳过程中,产生驻留滑移带,在表面形成侵入和挤出,导致氧化膜发生破裂,基体金属暴露于高温高压水环境中。由于驻留滑移带内部位错密度高,电化学活性高,优先发生溶解。金属(Fe、Cr、Ni)的溶解和金属离子的水解以及H+与O2的还原,会产生氢[23,24]。Dumerval等[25]和Jambon等[26]的实验结果表明奥氏体合金浸泡于高温高压水环境中,表面氧化膜和基体中会聚集一定量的氢,而吸附的氢来源于金属离子的水解。在疲劳过程中,滑移带为氢优先吸附位置。氢会促进位错运动,促进微观小裂纹萌生。因此,滑移溶解与氢共同作用,促进316LN不锈钢在高温高压水环境中微观小裂纹萌生与扩展。316LN不锈钢在320℃会发生动态应变时效[7,14~16],且随应变速率降低,动态应变时效更加显著(图7)。动态应变时效会导致变形局域化,进一步促进氢吸附于滑移带中,加速疲劳裂纹萌生[14]。因此,在低应变速率条件下(0.004 × 10-2 s-1),裂纹源区域准解理开裂特征更加明显,表明氢致开裂起重要作用。晶界以及夹杂物会阻碍微观小裂纹扩展[18,19],然而,316LN不锈钢在高温高压水环境中,晶界以及夹杂物周围金属电化学活性相比于基体金属更高,同时为氢优先吸附位置,导致对微观小裂纹的阻碍作用大大减小。因此,316LN不锈钢在高温高压水中的环境疲劳效应,高温高压水环境对微观小裂纹萌生与扩展的促进作用是主要原因之一。
疲劳裂纹扩展阶段对应机械小裂纹[2],对材料的微观组织特征不敏感。机械小裂纹一般垂直于加载轴扩展,以疲劳辉纹为特征。在本实验中,当裂纹长度大于200 μm时,316LN不锈钢疲劳断口上呈现疲劳辉纹特征。疲劳辉纹是裂纹尖端在循环加载过程中反复锐化和钝化而形成的[27],一般疲劳辉纹间距为一个循环周期裂纹扩展的长度。图12为316LN不锈钢在高温高压水环境中距离裂纹源不同位置处的疲劳裂纹扩展速率。在距离裂纹源200 μm处,低应变速率条件下(0.004 × 10-2 s-1)的裂纹扩展速率是高应变速率条件下(0.4 × 10-2 s-1)的3.72倍;在距离裂纹源500 μm处,低应变速率条件下(0.004 × 10-2 s-1)的裂纹扩展速率是高应变速率条件下(0.4 × 10-2 s-1)的3.35倍;在距离裂纹源1000 μm处,低应变速率条件下(0.004 × 10-2 s-1)的裂纹扩展速率是高应变速率条件下(0.4 × 10-2 s-1)的2.58倍。随着疲劳裂纹长度增加,高温高压水环境效应弱化。在低应变速率条件下,机械小裂纹扩展速率更高,与随应变速率降低疲劳寿命降低一致(图6)。同时,在低应变速率条件下(0.004 × 10-2 s-1),疲劳辉纹特征弱化(图10)。在机械小裂纹扩展过程中,裂纹尖端形成滑移带,基体金属暴露于高温高压水环境中,发生金属溶解和金属离子水解以及H+与O2的还原[23,24]。在低应变速率条件下,裂纹尖端与高温高压水的接触时间更加充分,同时发生的动态应变时效导致裂纹尖端变形局域化,更加有利于氢吸附于滑移带中[28]。Kanezaki等[29]报道,氢诱导的裂纹尖端塑性变形局域化,可能抑制疲劳辉纹形成,导致充氢的SUS304不锈钢疲劳断口表面疲劳辉纹区域远少于未充氢试样。因此,氢致开裂促进机械小裂纹扩展,导致在低应变速率条件下疲劳辉纹特征弱化,呈现解理开裂特征(图10)。值得注意的是,高应变速率条件下的疲劳寿命(2833 cyc)是低应变速率条件下的疲劳寿命(692 cyc)的4.09倍,高于应变速率降低对316LN不锈钢裂纹扩展速率的增加值(图10和12)。说明对于316LN不锈钢,高温高压水环境在微观小裂纹阶段,对疲劳损伤的促进作用更加显著。
图12 316LN不锈钢在高温高压水环境中距离裂纹源不同位置处的疲劳裂纹扩展速率
4 结论
(1) 高温高压水环境降低316LN不锈钢管状试样疲劳寿命,且疲劳寿命随应变速率降低而降低。
(2) 316LN不锈钢管状试样疲劳寿命与棒状试样疲劳寿命相当,管状试样可用来研究核电结构材料高温高压水腐蚀疲劳性能。
(3) 疲劳裂纹源区域为典型的扇形花样,随应变速率降低,呈准解理开裂特征;滑移溶解与氢致开裂共同作用,促进疲劳裂纹萌生。
(4) 疲劳裂纹扩展区域为典型的疲劳辉纹特征,随应变速率降低,疲劳辉纹特征弱化;氢致开裂在疲劳裂纹扩展过程中起重要作用。
(5) 相比于机械小裂纹扩展阶段,在微观小裂纹萌生与扩展阶段,316LN不锈钢在高温高压水中的环境疲劳效应更加显著。
参考文献
1 Carey J. Materials reliability program, fatigue issues assessment (MRP-138) [R]. Electric Power Research Institute, 2005
2 Chopra O K, Shack W J. Effect of LWR coolant environments on the fatigue life of reactor materials [R]. NUREG/CR-6909, ANL-06/08, 2007
3 Chopra O K, Stevens G. Effect of LWR coolant environments on the fatigue life of reactor materials [R]. NUREG/CR-6909, 2018
4 Japan Nuclear Energy Safety Organization. Environmental fatigue evaluation method for nuclear power plants [R]. JNES-SS-1005, 2011
5 Kondo T, Nakajima H, Nagasaki R. Metallographic investigation on the cladding failure in the pressure vessel of a BWR [J]. Nucl. Eng. Des., 1971, 16: 205
6 US Nuclear Regulatory Commission (NRC). Regulatory Guide 1.207, Guidelines for evaluating fatigue analyses incorporating the life reduction of metal components due to the effects of the light-water reactor environment for new reactors [Z]. Washington DC, USA: Nuclear Regulatory Commission, 2007
7 Tan J B, Wu X Q, Han E H, et al. Strain-rate dependent fatigue behavior of 316LN stainless steel in high-temperature water [J]. J. Nucl. Mater., 2017, 489: 33
8 Wu X Q, Xu S, Han E H, et al. Corrosion fatigue of nuclear-grade stainless steel in high temperature water and its environmental fatigue design model [J]. Acta Metall. Sin., 2011, 47: 790
8 吴欣强, 徐 松, 韩恩厚等. 核级不锈钢高温水腐蚀疲劳机制及环境疲劳设计模型 [J]. 金属学报, 2011, 47: 790
9 American Society of Mechanical Engineers. ASME boiler and pressure vessel code section III (Z), New York, 2015
10 Faidy C. Status of French road map to improve environmental fatigue rules [A]. Proceedings of the ASME 2012 Pressure Vessels and Piping Conference [C]. Toronto, Ontario, Canada: ASME, 2012
11 American Society Mechanical Engineers. Fatigue design curves for light water reactor environments [Z]. ASME Code-Case N-761, 2010
12 American Society Mechanical Engineers. Fatigue evaluations including environmental effects [Z]. ASME Code-Case N-792, 2010
13 Tan J B, Zhang Z Y, Zheng H, et.al. Corrosion fatigue model of austenitic stainless steels used in pressurized water reactor nuclear power plants [J]. J. Nucl. Mater., 2020, 541, 152407
14 Cho H, Kim B K, Kim I S, et al. Low cycle fatigue behaviors of type 316LN austenitic stainless steel in 310℃ deaerated water-fatigue life and dislocation structure development [J]. Mater. Sci. Eng., 2008, A476: 248
15 Hong S G, Lee S B. Mechanism of dynamic strain aging and characterization of its effect on the low-cycle fatigue behavior in type 316L stainless steel [J]. J. Nucl. Mater., 2005, 340: 307
16 Hong S G, Lee S B. Dynamic strain aging under tensile and LCF loading conditions, and their comparison in cold worked 316L stainless steel [J]. J. Nucl. Mater., 2004, 328: 232
17 Kuang W J, Wu X Q, Han E H. Influence of dissolved oxygen concentration on the oxide film formed on 304 stainless steel in high temperature water [J]. Corros. Sci., 2012, 63: 259
18 Gavenda D J, Luebbers P R, Chopra O K. Crack initiation and crack growth behavior of carbon and low-alloy steels [R]. Orlando, FL: ASME, 1997: 243
19 Gao J, Tan J B, Wu X Q, et al. Effect of grain boundary engineering on corrosion fatigue behavior of 316LN stainless steel in borated and lithiated high-temperature water [J]. Corro. Sci., 2019, 152: 190
20 Chopra O K, Park H B. Mechanism of fatigue crack initiation in light water reactor coolant environments [R]. ANL/ET/CP-101178, 2000
21 Huin N, Tsutusmi K, Legras L, et al. Fatigue crack initiation of 304L stainless steel in simulated PWR primary environment: Relative effect of strain rate [A]. Proceedings of the ASME 2012 Pressure Vessels and Piping Conference [C]. Toronto, Ontario, Canada: ASME, 2012
22 Xu S, Wu X Q, Han E H, et al. Crack initiation mechanisms for low cycle fatigue of type 316Ti stainless steel in high temperature water [J]. Mater. Sci. Eng., 2008, A490: 16
23 Turnbull A. Modelling of crack chemistry in sensitized stainless steel in boiling water reactor environments [J]. Corros. Sci., 1997, 39: 789
24 Turnbull A. Modeling of the chemistry and electrochemistry in cracks—A review [J]. Corrosion, 2001, 57: 175
25 Dumerval M, Perrin S, Marchetti L, et al. Hydrogen absorption associated with the corrosion mechanism of 316L stainless steels in primary medium of pressurized water reactor (PWR) [J]. Corros. Sci., 2014, 85: 251
26 Jambon F, Marchetti L, Jomard F, et al. Mechanism of hydrogen absorption during the exposure of alloy 600-like single-crystals to PWR primary simulated media [J]. J. Nucl. Mater., 2011, 414: 386
27 Laird C, Smith G C. Crack propagation in high stress fatigue [J]. Philo. Mag., 1962, 7: 847
28 Zhang Z Y, Tan J B, Wu X Q, et al. Corrosion fatigue behavior and crack-tip characteristic of 316LN stainless steel in high-temperature pressurized water [J]. J. Nucl. Mater., 2019, 518: 21
29 Kanezaki T, Narazaki C, Mine Y, et al. Effects of hydrogen on fatigue crack growth behavior of austenitic stainless steels [J]. Int. J. Hydrogen Energy, 2008, 33: 2604
免责声明:本网站所转载的文字、图片与视频资料版权归原创作者所有,如果涉及侵权,请第一时间联系本网删除。
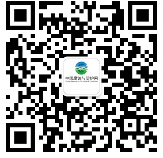
官方微信
《腐蚀与防护网电子期刊》征订启事
- 投稿联系:编辑部
- 电话:010-62316606-806
- 邮箱:fsfhzy666@163.com
- 腐蚀与防护网官方QQ群:140808414