高温合金又称“超合金”,主要成分为Fe-Ni基、Ni基及Co基等,具有优异的高温强度及良好的耐热腐蚀性、疲劳性能和断裂韧性等,往往被加工成各种各样复杂的零部件,并在具有严苛环境的领域使用,如宇航工业、核电和石油化工等。因此,高温合金的质量对其加工使用至关重要。低倍组织检验作为评价高温合金质量的重要方法之一,往往能反映出生产工艺参数和设备运行状况,并对产品质量的控制和提升起着关键性作用。来自陕钢集团产业创新研究院有限公司和中航上大高温合金材料股份有限公司的田伟、孙信阳、王仲凯等研究人员对高温合金的低倍组织检验进行了概述,结合腐蚀检测标准、常见低倍组织缺陷和腐蚀影响因素,说明了低倍组织腐蚀的方法要点,为进一步提升高温合金低倍组织的腐蚀质量提供指导性参考。
01 腐蚀方法与检验标准
1.1 腐蚀方法
高温合金低倍组织的浸蚀方法有电解腐蚀和化学腐蚀两种。电解腐蚀是在外加电源下进行,无须加热,酸洗液循环使用周期长,节省时间,同时检验面相对干净、均匀,适用于大批量和大尺寸试样的酸洗。化学腐蚀是将试样直接浸泡在溶液中,在25℃或特定的温度下进行,酸洗液循环使用时间较短,腐蚀效率较低,一般适用于小批量和小尺寸试样。高温合金含有大量Ni,Cr等耐腐蚀元素,低倍组织腐蚀往往很难进行。目前国内所使用的酸洗液组分及配制比例主要参考GB/T 14999.1—2012 《高温合金试验方法:第1部分:横向低倍组织及缺陷酸浸检验》和GB/T 14999.2—2012 《高温合金试验方法:第2部分:横向低倍组织及缺陷酸浸检验》,国外主要参考ASTM E340—2015 Standard Practice for Macroetching Metals and Alloys和ASTM A604/A604M—2007 Standard Practice for Macroetch Testing of Consumable Electrode Remelted Steel Bars and Billets。
在实际生产中,低倍腐蚀多数情况以化学浸蚀方式为主,温度通常在25℃下。形状简单的小试样以浸蚀为主,对形状复杂且体积较大试样,往往切割成若干块浸泡或者进行整体刷洗。选用酸洗液为硫酸铜(150g)+硫酸(35mL)+盐酸(500mL)溶液或者王水(盐酸∶硝酸的摩尔比为3∶1)。整个过程涵盖的主要步骤为:①试样制备,以棒材为例,试样通常在相当于铸锭的头部和尾部直接截取,厚度为15~30mm,以精车或者磨光的方式进行加工,检验面粗糙度一般不大于3.2 μm;② 腐蚀,首先按照要求配置好溶液,用乙醇和水将粗糙度满足要求的试样检验面进行清洗,去掉油污,然后放入溶液中,检验面朝上,浸泡至检验面呈深灰色、无金属光泽,以能够清晰显示宏观组织形貌为准,另外,为了尽可能避免试样组织状态对处于临界条件缺陷腐蚀的影响,推荐延长腐蚀时间至20~60min,在浸泡过程中,可以采用毛刷间断式擦拭检验面,防止覆盖的腐蚀产物影响腐蚀进度和均匀性;③ 清洗和检验,用质量分数为10%的过硫酸铵水溶液刷洗掉表面附着的腐蚀产物,用风机吹干后进行检验,必要时可以采用不大于10倍的放大镜进行观察。图1为采用不同溶液腐蚀后高温合金低倍组织的宏观形貌。
1.2 检验标准
目前国内对于高温合金的低倍组织,所有产品技术协议都要求试样上不允许有目视可见的外来夹杂、残余缩孔、疏松、孔洞、偏析、裂纹、针孔及其他对材料使用有害的缺陷。高温合金低倍组织检验的标准GB/T 14999.1—2012 和GB/T 14999.2—2012中对高温合金的斑点状偏析、黑斑及白斑等缺陷进行了说明。在实际生产中,高温合金主要以真空感应+真空自耗和真空感应+电渣重熔两联工艺或者真空感应+电渣重熔+真空自耗重熔三联工艺进行冶炼,后期采用锻压、冷拔、热轧等各种冷热加工方式成形,在整个环节中都可能出现各种各样的缺陷。为了能较全面地囊括所有低倍缺陷,试样检验时也参考结构钢低倍组织缺陷评级标准GB/T 1979—2001 《结构钢低倍组织缺陷评级图》。国外依据合金冶炼工艺的特点,起草修订了关于自耗电极重熔钢棒及钢坯宏观浸蚀试验标准ASTM A604/A604M—2007,该标准列举了斑点、白斑、径向偏析和环形偏析4类缺陷组织,每类组织按照严重级别分为A,B,C,D和E5个级别,其中A级表示用肉眼观察浸蚀表面时,只能发现最少的上述各种缺陷组织,而B,C,D,E级表示可发现的缺陷组织依次增多。为了全面评判生产环节出现的各种产品状况,在进行低倍组织检验时,也采用了钢棒、钢坯、初轧坯及锻件的宏观浸蚀标准ASTM E381—2020 Standard Method of Macroetch Testing Steel Bars, Billets, Blooms, and Forgings,显示各种缺陷的非等级系列图谱。
对比国外的高温合金,国内一般不允许材料存在黑斑、斑点、白斑等低倍组织缺陷,因此高温合金低倍组织检验标准里也只对这些偏析类缺陷进行了描述及附图说明,但并没有划分级别。另外,对于自耗重熔冶金方式生产高温合金过程中形成的主要缺陷,即环形花样,高温合金低倍组织检验标准并未提及。参考ASTM A604/A604M—2007划分高温合金使用范围内接受缺陷的级别,可以确保材料质量和使用环境相匹配,降低生产成本,节约资源。
02 常见缺陷及影响因素
2.1 常见的低倍组织缺陷
高温合金在前期冶炼、后期冷热成形及热处理环节中,往往会因为工艺、生产操作及设备等因素产生各种低倍组织缺陷,使得产品降级使用或者直接判废,造成很大的损失。为了更好地了解缺陷产生机理,控制缺陷的发生,必须对缺陷进行准确定性。图2为高温合金常见低倍组织缺陷的宏观形貌,可以通过对比形貌的方法对部分缺陷予以甄别。
2.2 腐蚀影响因素
高温合金含有高含量的Ni,Cr等耐腐蚀元素,且受检验面粗糙度、腐蚀时间以及酸洗液浓度和温度等因素的影响,在进行低倍组织腐蚀时,试样检验面出现腐蚀深度浅、腐蚀不均匀等现象,甚至出现低倍组织缺陷没有被腐蚀出来的状况,无法保证材料的质量。现结合生产实践应用,就上述因素对腐蚀的影响进行分析,以提升低倍腐蚀的质量和效率。
2.2.1 粗糙度
粗糙度作为低倍酸洗试样制备环节的一项要求,对腐蚀时间、缺陷观察等都有显著影响,通常要求检验面粗糙度不大于3.2μm。在高温合金酸洗过程中,检验面粗糙度越小,试样越容易被腐蚀,缺陷越容易显现出来。同时在腐蚀结束后,可以观察到试样整个面腐蚀比较均匀,局部组织的粗细界限清楚,针孔、非金属夹杂、疏松等缺陷较容易显现。当粗糙度较大时,会影响试样宏观形貌及细小缺陷的显现和观察,对低倍组织的评定造成干扰。因此,在试样制备时,检验面在标准要求的粗糙度范围内尽可能精车加工,尤其对于低倍组织质量要求较高的材料,粗糙度越小越好。图3是试样检验面粗糙度为0.01μm和3μm时低倍组织的宏观形貌。
2.2.2 酸洗液浓度
为了使试样呈现出均匀的低倍组织,在试样检验面的粗糙度达到要求后,要根据钢种选择合适的酸洗液,否则会出现不腐蚀或钝化现象。针对高温合金耐腐蚀的特性,目前较多采用的酸洗液为硫酸铜+硫酸+盐酸溶液和王水,都是在25℃环境下进行腐蚀。在实际生产应用中,硫酸铜+硫酸+盐酸溶液基本可以解决各种牌号的Fe-Ni基、Ni基及Co基等高温合金的低倍腐蚀;而用王水腐蚀某些牌号的高温合金时有低倍组织钝化的现象(见图4)。
同时两种溶液的循环使用周期较短,随着使用频次的增多,酸洗液的有效浓度降低,腐蚀时间相对延长,甚至有缺陷未被腐蚀出来的现象。向硫酸铜+硫酸+盐酸溶液中加入少量的浓硝酸,可以使腐蚀时间缩短,酸洗液的循环使用次数提高,低倍组织腐蚀均匀。图5为采用硫酸铜+硫酸+盐酸溶液加入少量浓硝酸腐蚀后低倍组织的宏观形貌。在腐蚀时要隔一段时间对检验面进行刷洗,防止腐蚀产物沉积。同时要根据酸洗液的使用频次、腐蚀时间及低倍组织腐蚀情况,及时更换酸洗液,提高腐蚀效率,防止酸洗液有效浓度降低,避免组织缺陷未能显现,或因溶液中杂质较多而产生腐蚀缺陷假象的情况发生。在试样发现有争议的缺陷时,必须重新精车、腐蚀或者补充进行高倍金相检验。
2.2.3 酸洗液温度
当酸洗液温度较低时,低倍组织极易出现不均匀和部分缺陷未能显现的情况;适当提高酸洗液的温度,会使腐蚀的时间缩短,缺陷显现较完全。对于25℃下试样腐蚀效果不佳的溶液,在较高温度下酸洗就可以得到较均匀的低倍组织。将盐酸+硝酸+水溶液(盐酸∶水∶硝酸的体积比为10∶10∶1)和硫酸铜+硫酸+盐酸溶液按照15∶1(摩尔比)混合,加热到70℃,酸洗30~60min,可见试样腐蚀均匀且组织清晰(见图6)。在酸洗过程中,斑点状偏析、黑斑等偏析类缺陷可以首先显现,避免了因溶液浓度低、腐蚀时间短而使缺陷不易显现的问题。对于使用刷洗方式进行低倍组织检验的大尺寸试样,采用40℃含有少量浓硝酸的硫酸铜+硫酸+盐酸溶液,腐蚀时间会相对较短,腐蚀均匀且低倍组织清晰。另一方面,相较于腐蚀时间的延长,提高酸洗液的温度更为关键,这样能够使得低倍组织和缺陷完全显现,检验面干净、清晰。
03 结论
(1) 国内高温合金低倍组织检验标准应参考ASTM A604/A604M—2007,补充环形花样,并划分黑斑、白斑、环形花样等缺陷级别,使材料质量和使用环境相匹配。
(2) 高温合金检验面的粗糙度在标准要求范围内应尽可能小,尤其是对低倍组织质量要求较高的材料,同时采用酸洗液浓度较高的热酸腐蚀,低倍组织显现完全、均匀且清晰,对针孔类细小缺陷易辨识;采用王水可以对部分牌号高温合金进行腐蚀,尤其是Co基高温合金。
(3) 酸洗液要根据使用的频次、腐蚀时间及低倍组织显现效果,及时进行更换,以提高腐蚀效率,防止缺陷未能显现及缺陷假象。对于存在异议的缺陷,必须重新精车、腐蚀或者进行高倍金相检验。
免责声明:本网站所转载的文字、图片与视频资料版权归原创作者所有,如果涉及侵权,请第一时间联系本网删除。
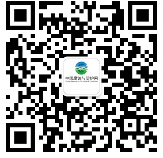
官方微信
《腐蚀与防护网电子期刊》征订启事
- 投稿联系:编辑部
- 电话:010-62316606-806
- 邮箱:fsfhzy666@163.com
- 腐蚀与防护网官方QQ群:140808414