硫化物腐蚀大部分情况下表现为全面腐蚀或均匀腐蚀,在一定环境中也可发生局部腐蚀。目前,普遍认为硫化物腐蚀的腐蚀机理主要有两种形式,分别是无氢环境中的硫化物腐蚀和有氢气存在的硫化物腐蚀。 01
无氢环境中的硫化物腐蚀机理通常认为有四个不同的步骤:
一般硫化物腐蚀的腐蚀速率受到以上四个步骤的影响,第一步和第二步是限速步,有研究表明某些硫化合物甚至比HS更容易被吸收(化学吸附)到硫化物膜中,因此表现出比H2S更高的腐蚀速率。对于普通碳钢,形成的锈蚀物是贫金属型的硫化铁(Fe1-xS)膜,而含Cr的合金形成的是双层膜:内层是Fe1-xS和尖晶石结构的磺基FeCr2S4的混合膜,外层是Fe1-xS6,当合金中的Cr含量增加时,内层膜倾向于单一相的尖晶石结构的磺基FeCr2S4膜,通常认为这种尖晶石结构的磺基膜比Fe1-xS更稳定,因此更具有保护性。当金属中含有Cr时,阳离子空位和电子空穴通过尖晶石相(FeCr2S4)的扩散量要比Fe1-xS少,于是第三步得到减缓,进而腐蚀速率得到限制。在无氢存在时,一般使用修正的McConomy曲线预测腐蚀速率。
02 有氢环境
在H2-H2S环境中,硫化物的腐蚀机理与无氢环境中的硫化物腐蚀相类似,硫化铁膜的成分和形貌在本质上同无H2环境中的相同。但是,一些合金在无氯硫化物环境和H2-H2S环境中却表现出了截然不同的性能,如在某些情况下,铬钼钢(Cr-Mo)和碳钢的腐蚀率相同,其原因可能与H2能够促进各类吸附性硫合物的扩散进而抵消了Cr的影响有关。有文献报道在轻组分馏出物的H2-H2S环境中之所以有更高的腐蚀速率,是因为没有结焦的发生,从而不会形成保护性膜。
针对硫化物腐蚀,现有装置可采取以下措施避免硫化物的腐蚀失效:制定和实施检测、材质鉴别、低硅钢检测、定义操作界限、在线监测、注缓蚀剂以及材质更换等。
01 制定和实施检测
其他用于检测硫化物腐蚀的新技术主要有:
02 材质鉴别
中国石化目前要求各企业对所有设备管线材质进行100%材质检验,确保所用材料符合使用要求。但是由于很多装置已经使用很多年、中间更换及改造等原因,再加上设备、管线数量多,很难保证在用材质100%符合要求。因此,针对重点部位及有问题部位进行材质鉴别检验很有必要。
03 加强低硅碳钢检测
根据已有的使用经验,低硅(<0.10%)碳钢当暴露在硫化腐蚀条件下时,会发生加速腐蚀。一般零件硅含量较高,而管道最有可能含有较低的硅。因此,对于低硅碳钢的检测是有必要的,企业应根据使用材质情况,编制出装置的低硅钢分布图,并加强对这些管道的检测,可使用超声波测厚检测厚度情况,确定是否需要更换及何时进行更换。
04 调整工艺,优化操作参数
对装置腐蚀部位进行分析,确定可能发生硫化物腐蚀的部位,并优化操作参数,一般工艺参数应考虑温度和硫含量,分别规定出其操作界限,禁止超温、超临界值操作,并提出采样和监测的具体要求。另外,由于在弯头、大小头、三通、设备进出口接管等处易产生湍流、涡流,导致腐蚀速率提高。因此,在设计上应保证流体的路径呈流线形,减少拐弯、变径和变向,设备结构及管线布置应合理,以便对流速和流态进行控制。
05 在线监测
腐蚀在线监测系统因其实时高效而成为目前国内外炼油企业普遍采用的腐蚀监测方法之一。该系统利用电阻、电感、电化学等监测技术,将多个腐蚀探针的监测信号通过模数转换、远程传输、数据处理、软件集中控制等实现多路在线自动腐蚀监测。
腐蚀探针能更好地反映原油或原料的硫化物腐蚀行为,对于硫化物腐蚀,电阻探针更适合,现在应用的探针有固定型和收缩型两种,固定型探针更常见于高温环境,收缩型探针需要更多精细配件,而且在探针收起或插入过程中要考虑安全性。
为获得可靠的监测数据,一般需要很多天重复采集数据,较好的做法是将监控数据与原油或物料组成以及硫化物含量和种类相结合,从而得到这些因素同腐蚀速率之间的关系。
06 注缓蚀剂
为抑制硫化物腐蚀,可考虑使用一些缓蚀剂,目前用于抑制高温硫化物腐蚀的缓蚀剂并不多,对于一些用于控制环烷酸腐蚀的磷酸类缓蚀剂,其对硫化物腐蚀的抑制效果也在实验室里进行了测试,但是效果并不很理想,因此可考虑加快对抑制硫化物腐蚀的缓蚀剂的研发。
07 材料更换或升级
免责声明:本网站所转载的文字、图片与视频资料版权归原创作者所有,如果涉及侵权,请第一时间联系本网删除。
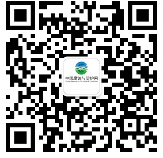
官方微信
《腐蚀与防护网电子期刊》征订启事
- 投稿联系:编辑部
- 电话:010-62316606-806
- 邮箱:fsfhzy666@163.com
- 腐蚀与防护网官方QQ群:140808414