近年来,随着石油资源的深度开采以及进口高硫、高酸原油的不断增加,原油劣质化趋势日趋明显,这对炼油厂的安全及长周期运行造成了严重威胁。常减压蒸馏装置是炼厂最为关键的装置之一,作为原油加工的第一道工序,典型的腐蚀问题是分馏塔顶冷凝冷却系统的HCl+H2S+H2O腐蚀,以及高温部位(温度大于220 ℃)的硫-环烷酸腐蚀,常常会造成设备、管线的腐蚀泄漏,甚至还会引起装置的非计划停工、安全环保等事故,并对后续加工装置的连续稳定运行、炼厂的生产平衡造成影响,严重影响炼厂的安全性和经济效益。
某350万吨/年常减压蒸馏装置为典型的燃料油型三段常减压装置,采取三塔两炉技术,即按照生产流程顺序设置电脱盐、初馏塔、常压炉、常压塔、减压炉、减压塔,装置设备、管线的主体材质均为碳钢。按照装置的原设计需求,主要加工大庆原油等低硫低酸原油,近年来逐渐掺炼苏丹达尔原油、俄罗斯原油等高酸、含硫原油。原油酸值、硫含量的增加会导致炼油装置设备腐蚀加剧,为了加强对常减压蒸馏装置的腐蚀监控与防护,减少由于腐蚀造成的生产波动,保障装置安全长周期运行,需对装置的腐蚀与控制状况进行系统分析,并在此基础上完善和优化腐蚀控制方案,确保装置的腐蚀受控。
装置的腐蚀风险分析
加工负荷情况
炼油装置的加工负荷是影响腐蚀的重要因素之一。装置的处理量过低,会造成装置各部位流速过低、腐蚀性介质滞留,从而加剧设备和管线的腐蚀;装置的处理量过高,会造成装置各部位的流速增大,加大对设备、管线的冲刷腐蚀,并引起塔顶低温部位露点后移造成的腐蚀问题。某常减压蒸馏装置的加工负荷情况见图1。
图1 某常减压蒸馏装置加工负荷变化情况
由图1可见:该装置的最低加工负荷均在80%以上,最高加工负荷每月均超过装置设计值的120%。一般来说,装置应尽可能控制加工量为设计值的60%~110%。因此,常减压蒸馏装置的高温、低温部位均存在较高的冲刷腐蚀风险,且塔顶低温部位可能存在由于负荷增加引起的露点后移等问题,这增大了塔顶低温部位的腐蚀风险。
加工原料的腐蚀性
1 原油酸值和硫含量的变化情况
常减压蒸馏装置加工混炼原油中的硫、酸含量是影响设备腐蚀的主要因素,硫含量、酸值的升高都会增大装置的腐蚀风险。某常减压蒸馏装置加工混炼原油的酸值、硫含量变化情况见图2。
图2 加工混炼原油的酸值、硫含量变化情况
从图2可见:加工原油的酸值在1~2月均低于0.05 mgKOH/g,硫含量在1~3月均约为0.1%;3月以后酸值、硫含量均有明显升高趋势,其中酸值最高达到0.46 mgKOH/g,硫的质量分数最高为0.22%。由于酸值和硫含量的升高,装置三顶低温系统的HCl+H2S+H2O腐蚀、高温部位的硫-环烷酸腐蚀风险均存在升高的趋势。
2 进装置原油的总氯变化情况
混炼原油经电脱盐后进入装置,其总氯含量变化情况见图3。
图3 原油的总氯含量变化情况
由图3可见:经电脱盐后进混炼原油的总氯含量呈逐渐升高的趋势,最高达到5.14 mg/kg,说明原料中存在一定量有机氯(无机氯在电脱盐过程中大部分会脱除),在后续加工过程中会产生氯离子,造成三顶低温系统HCl+H2S+H2O腐蚀加剧,需要考虑有机氯对后续装置的腐蚀影响。
电脱盐的控制情况
电脱盐是确保炼油厂后续加工装置安全长周期生产必不可少的措施。通过从原油中脱除盐、水和其他杂质,降低原油的水含量、盐含量,达到降低后续工序腐蚀的目的。
某常减压蒸馏装置1~10月电脱盐脱后原油盐含量合格率分别为97.24%(按≤3 mg/L计)和30.34%(按≤2 mg/L计),脱后盐含量与指标要求还存在一定差距;电脱盐后水含量合格率为100%,脱后水含量控制较好。电脱盐后原油盐含量超标,加上装置加工负荷较高,会造成塔顶冲刷腐蚀、露点后移等问题,导致三顶低温系统H2S-HCl-H2O腐蚀风险加大。
塔顶低温系统的腐蚀风险
1 塔顶露点温度
(1) 塔顶露点温度计算:
根据常减压蒸馏装置的温度、压力等工艺数据以及物料平衡数据,对初馏塔顶、常压塔顶、减压塔顶的露点温度进行了模拟计算,结果见表1。
表1 塔顶的露点温度计算结果
根据炼油装置工艺防腐蚀的控制要求,为防止和减缓塔顶低温系统结垢、结盐和腐蚀,应控制塔顶操作温度超过露点温度14 ℃。根据露点温度计算结果,即初馏塔、常压塔顶和减压塔顶的温度应分别超过78,106,38 ℃。
(2) 塔顶温度控制情况:
装置初馏塔、常压塔、减压塔的塔顶的实际操作温度变化情况见图4。
图4 装置初馏塔、常压塔、减压塔塔顶的实际操作温度变化情况
由图4可见:1~9月,常减压蒸馏装置初馏塔顶操作温度为123~135 ℃,常压塔顶操作温度为104~117 ℃,减压塔顶操作温度在42~54 ℃。按照三顶露点温度计算结果,以及工艺防腐控制要求,应控制初馏塔顶温度>78 ℃,常压塔顶温度>106 ℃,减压塔顶温度>38 ℃。
从温度控制情况来看,初馏塔顶温度虽然控制在露点控制温度以上,但温度偏高,会造成塔顶馏出量增大、负荷偏高,对设备和管线的冲刷腐蚀及露点后移的腐蚀风险将增大;常压塔顶温度控制基本符合要求;减压塔顶温度控制在合理范围。
2 塔顶含硫污水控制情况
为了控制和减缓塔顶低温系统的腐蚀,常减压蒸馏装置在初馏塔顶、常压塔顶、减压塔顶馏出线中注缓蚀剂+水,并对塔顶含硫污水的pH、铁离子、氯离子含量等进行分析,掌握腐蚀控制状况并对注水量和注剂量进行调整。
(a) pH变化情况
(b) 铁离子含量变化情况
(c) 氯离子含量变化情况
图5 装置塔顶含硫污水的水质变化情况
由图5可见:初馏塔顶部分pH在3~4月低于6,常压塔顶pH在2月、5月、7月、9月均低于6,减压塔顶部分pH在3月~4月低于6;初馏塔顶铁离子含量在7月、10月存在部分超过3 mg/L的情况,常压塔顶铁离子含量在2月、4月、9月存在超过3 mg/L的情况,减压塔顶铁离子含量控制较好,均低于3 mg/L;三顶含硫污水的氯离子含量变化趋势基本一致,均存在大部分时间超过30 mg/L情况。
按照炼油装置工艺防腐控制要求(表2),装置初馏塔顶、常压塔顶、减压塔顶含硫污水的pH、铁离子、氯离子含量存在较多超标情况,说明塔顶的腐蚀风险均未得到有效控制,需要进一步加强工艺操作,并适当加大注水量、注剂量,合理控制塔顶的腐蚀风险。
表2 塔顶的水质控制情况
高温部位的腐蚀风险分析
针对常减压蒸馏装置服役温度220 ℃以上的高温管线,根据高温管线内介质硫含量、酸值分析数据,初步测算了腐蚀速率;同时根据NACE RP0775—2005标准规定的腐蚀速率等级(腐蚀速率>0.13 mm/a为严重腐蚀),将各部位腐蚀速率进行了对比分析,结果见图6。
图6 高温管线的腐蚀速率
由图6可见:由于装置主体材质为碳钢(仅常压、减压转油线材质为0Cr18Ni10Ti),1号加热炉进料、常二线、常三线、常四线、二中出、常压塔底、2号加热炉进料、减二线、减三线、减四线、减压塔底等管线的腐蚀速率全部超过0.13 mm/a,部分管线的腐蚀速率甚至超过1 mm/a,均存在较高的硫-环烷酸腐蚀风险。
腐蚀损伤测厚排查情况
根据装置塔顶低温部位以及高温部位的腐蚀风险分析结果,为了进一步掌握装置的真实腐蚀损伤情况,对装置重点部位进行了全面的测厚排查,其中部分典型部位的测厚结果见表3。
表3 装置典型部位的测厚结果
从表3可见:装置常压塔顶馏出线、常三线、各减压侧线、减压渣油线的腐蚀减薄非常严重,部位典型部位管线的减薄率超过20%。对于这些腐蚀严重的部位,应立即采取相应的防护措施并加强监控。
结论与建议
腐蚀风险分析结论
1 装置的加工负荷偏高,装置的高温、低温部位均存在较高的冲刷腐蚀风险,同时塔顶低温部位由于可能存在露点后移等问题,增大了塔顶低温部位的腐蚀风险。
2 装置加工混炼原油的酸值、硫含量、氯含量均呈明显升高趋势,因此装置的三顶低温系统HCl+H2S+H2O腐蚀、高温部位的硫-环烷酸腐蚀风险均存在升高的趋势。
3 装置电脱盐脱后原油盐含量合格率与指标要求还存在一定差距,加上加工负荷较高,因此装置三顶低温系统存在较高的H2S-HCl-H2O腐蚀风险。
4 装置初馏塔顶操作温度偏高,存在塔顶负荷大、冲刷腐蚀和露点后移的风险;装置初馏塔顶、常压塔顶、减压塔顶含硫污水的pH、铁离子、氯离子含量存在较多超标的情况,说明塔顶的腐蚀风险均未得到有效控制。
5 1号加热炉进料、常二线、常三线、常四线、二中出、常压塔底、2号加热炉进料、减二线、减三线、减四线、减压塔底等管线均存在较高的硫-环烷酸腐蚀风险。
6 常压塔顶馏出线、常三线、各减压侧线、减压渣油线的腐蚀减薄非常严重,部位典型部位管线的减薄率全部超过20%,腐蚀减薄非常严重,应立即采取相应的防护措施并加强监控。
腐蚀控制措施与建议
1 装置的加工量应尽可能控制在设计值60%~110%内,降低装置高负荷运行造成的腐蚀风险。
2 通过合理调整原油混炼比例等措施,进一步降低近装置原料的硫含量、酸值、氯含量。
3 建议装置增加原油罐区静置沉降脱水等措施,降低进电脱盐原油的盐含量、水含量(将脱前水含量控制在0.5%以下),优化电脱盐操作,合理增加注水量,确保脱后盐含量、水含量达标。
4 优化塔顶工艺操作温度,控制塔顶注水水质符合工艺防腐注水指标要求,适当加大注水量、注剂量,保证塔顶含硫污水pH、铁离子、氯离子含量达标,合理控制塔顶的腐蚀风险。
5 对减薄严重部位,应立即采取相应的防护措施,进行加固处理并密切监控,同时加强高风险部位的测厚频次,并利用合适的时机进行更换处理,确保装置安全。
6 装置的加工原油变化后,原有设备和管线的材质已经难以适应腐蚀防护要求;建议装置进一步开展系统的材质适应性评估,并对装置的设备和管线进行必要的材质升级。
免责声明:本网站所转载的文字、图片与视频资料版权归原创作者所有,如果涉及侵权,请第一时间联系本网删除。
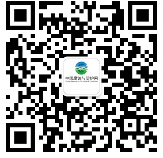
官方微信
《腐蚀与防护网电子期刊》征订启事
- 投稿联系:编辑部
- 电话:010-62316606
- 邮箱:fsfhzy666@163.com
- 腐蚀与防护网官方QQ群:140808414