钛合金具有密度小、耐高温、耐海水腐蚀性好等特点,是一种理想的海洋装备材料,被誉为“海洋金属”。钛合金材料在海洋装备中的应用范围极其广泛,如耐压装备的壳体,各种类型的管接头,换热器、燃气轮机部件和特种装置等。舰船用钛合金的服役工况较为复杂,局部腐蚀、轻微划痕等表面缺陷在服役过程中不可避免,在深海高压环境下,表面结构不连续导致的应力集中都是裂纹易于形核并扩展的部位。研究表明,钛合金的力学性能对其表面状态十分敏感,表面划痕和缺口等缺陷会大大降低其服役性能。目前,国内外学者研究了钛合金部件的表面缺陷对其力学性能的影响。曾玉金等研究了缺口对TC21钛合金拉伸性能的影响,并发现缺口半径增大会导致抗拉强度下降,缺口对断裂机制的影响并不明显。王春雨等对不同缺口深度的TC18钛合金进行了冲击试验,结果表明缺口会导致冲击韧性显著降低,并且冲击韧性随缺口深度的减小而增大。张思倩等研究了不同缺口半径对Ti-24Nb-4Zr-8Sn合金室温高周疲劳性能的影响,发现缺口会明显降低钛合金的疲劳强度,缺口半径对钛合金的缺口敏感性影响不大。目前,不同表面状态对钛合金强度、局部塑性变形行为的影响机制尚不明确,钛合金打磨态的板材表面本身存在大量的微划痕,轻微的外物撞击可能会使其表面出现局部损伤,大量的试验结果表明,钛合金弯曲试样经表面磨削处理后,开裂倾向就会大大减小;表面抛光态试样与非抛光态试样的疲劳寿命相差数倍。因此,表面缺陷带来的应力集中会给装备的安全服役带来极大的安全隐患,探究钛合金表面状态对其力学性能的影响规律,并分析该类表面缺陷在局部塑性变形过程中的作用机制,对其在深海环境下的安全应用具有重要意义。 研究人员对Ti80合金板材的打磨划痕、缺口、裂纹等表面缺陷进行研究,分析了Ti80合金表面状态对拉伸性能、冲击性能、疲劳性能等的影响规律,并利用数字图像相关方法(DIC)分析拉伸过程中的局部变形行为,结果可为Ti80合金的工程应用提供数据支撑。
试验材料为Ti80合金板材,其组织主要为等轴α和板条α的双态组织(见图1)。为了研究不同表面质量和缺口尺寸对Ti80合金动态和静态力学性能的影响,对Ti80合金试样进行静态拉伸试验、动态冲击试验和疲劳试验,设计了6种试样形式,分别为:1号表面抛光试样;2号原始表面试样;3,4,5号缺口试样,缺口尺寸如表1所示;6号预制2mm裂纹试样。2号试样表面经过百叶轮打磨,取样保留了原始表面状态,其宏观形貌如图2所示。拉伸及疲劳试样尺寸如图3所示,冲击试样尺寸及缺口尺寸如图4,5所示。 使用电子材料试验机进行拉伸试验,试验前在试样的表面喷涂随机分布的散斑标点,通过视频引伸计对试样表面应变进行实时测量,试验速率为2mm/min。使用摆锤式冲击试验机进行冲击试验,试验过程可以采集力与位移信息,试样断裂后,利用双束扫描电子显微镜(SEM)观察试样断口形貌。使用电液伺服疲劳试验机进行疲劳试验,试验过程中使用载荷控制的模式进行加载,应力比为0.1,最大疲劳应力为680MPa,加载频率为6Hz。
2.1 不同表面状态试样的拉伸试验 6种类型试样的拉伸试验结果如表2所示,应力-应变曲线如图6所示。 由表2和图6可知:1~6号试样的应力-应变曲线在弹性段范围内差异较小;缺口试样应力-应变曲线的斜率略有增大;1,2,3号试样的抗拉强度比较接近,断后伸长率依次减小;4,5号缺口试样的抗拉强度明显增大,表现出缺口强化效应,但是断后伸长率显著减小,约为光滑试样的20%;6号预制裂纹试样的抗拉强度最低,且断后伸长率也较低。 2号原始表面试样的抗拉强度升高是由表面硬化层导致,断后伸长率降低的原因是表面硬化层与划痕两种效果叠加使材料塑性减小。3号试样微小缺口产生的应力集中较小,对抗拉强度的影响并不明显,而该微小缺口可视为表面缺陷,影响其拉伸塑性变形能力,导致断后伸长率明显减小。4,5号试样缺口改变了缺口尖端的应力分布,呈现三轴应力状态,缺口试样的等效应力要小于光滑试样的等效应力,材料需承受更大的载荷才能断裂,因此展现出了更高的强度,又因为截面积变小会导致塑性变形集中,对于深缺口来说,其塑性变形能力显著降低。6号试样受裂纹尖端的束缚作用,塑性区域非常小,在试验过程中,试样提前断裂导致其抗拉强度及断后伸长率均显著减小。 2.2 拉伸试验过程中的应变分布 利用DIC观察整个拉伸试验过程中试样的全场应变情况,图7为1~6号试样断裂前的应变云图。由图7可知:1~3号试样的应变分布比较均匀,4~6号试样的应变则集中在缺口尖端位置,随着表面质量的下降及缺口深度的增大,试样破坏前的最大应变逐渐减小。钛合金具有良好的塑性变形能力,缺口试样能够通过塑性变形减小其缺口尖端应力集中的影响,抗拉强度则因为束缚导致的剪应力向正应力变化而增大。在试样的拉伸断裂过程中,三轴应力的作用方式使其最大力存在于试样心部,表面承受的正拉力小于内部的拉力峰值,当缺口尖端受塑性变形影响,应力集中系数降低到一定阈值以下时,该应力集中不会导致材料的抗拉强度降低。但当缺口应力集中系数过高,且束缚足够大时,其应变强化能力弱,使塑性变形对缺口尖端应力集中的缓解程度不足,导致试样提前断裂,抗拉强度降低。6号预制裂纹试样的应变比4,5号试样更加集中。 2.3 不同表面状态试样的冲击试验 6种类型试样的冲击试验结果如表3所示,冲击过程中的力-位移曲线如图8所示。 冲击试验过程中试样的受力类似于三点弯曲过程,最大力和最大塑性变形均产生在试样的表面,可以很好地反映表面状态对材料性能的影响。由图8可知:起裂后裂纹扩展速率较慢,以韧性断裂为主。1号光滑试样的冲击吸收能量最高,平均冲击吸收能量为382J,当试样表面存在打磨划痕时,冲击吸收能量会显著降低;2号试样的冲击吸收能量约为160J,下降幅度可达58%,对于缺口试样,随着缺口深度的增加,冲击吸收能量会进一步降低,当缺口深度相同时,随着缺口根部曲率半径的增大,5号试样的冲击吸收能量大于4号试样,表明钛合金材料的冲击吸收能量受其缺口尖端应力集中的影响。由于钛合金应变强化能力弱以及塑性扩展速率慢,在动态加载过程中,其应力集中几乎无法释放,导致材料的断裂扩展阻力非常小,相较于静态拉伸试验,冲击试验对试样的表面状态更为敏感。 1~6号冲击试样断口起裂位置SEM形貌如图9所示,所有试样断口表面均存在大量韧窝,表现为韧性断裂,即裂纹在整个断裂过程中都呈塑性扩展特征。1号试样的韧窝小而浅,断口较为平整,具有良好的塑性,而在2~6号试样断口表面发现了一些孔洞及二次裂纹,具有明显的撕裂脊,表明其断裂前承受了更大的变形,冲击性能相应较差。 2.4 疲劳试验 3种类型试样的疲劳试验结果如表4所示。 由表4可知:当施加的疲劳载荷相同时,光滑表面试样的寿命约为原始表面试样寿命的3倍,2号原始表面试样的寿命约为3号缺口试样寿命的8倍。随着试样表面质量的下降,其疲劳寿命会显著缩短,这是因为疲劳是一种动态损伤过程,其对应力集中效应非常敏感。当试样的表面存在加工划痕或缺口时,可以视为试样本身存在缺陷,疲劳试验过程中,应力会在试样表面的缺陷处集中,导致该区域的局部应力大大增加,并且钛合金自身塑性变形速率较慢,因此材料在疲劳加载最初的过程就开始快速损伤,当损伤累积到材料的最大使用阈值时,试样会被破坏。 采用不同表面状态试样的力学性能指标除以表面抛光试样的力学性能指标作为表面敏感性系数,以此评价不同表面状态对Ti80合金力学性能的影响。不同表面状态试样的表面敏感性系数如图10所示,不同表面状态试样静态拉伸试验的表面敏感性系数为0.9~1.1,浮动范围较小,而对于动态冲击试验和疲劳试验,即使是表面打磨态及微小缺口,也会使表面敏感性系数显著下降,6号冲击试样的表面敏感性系数仅为0.1,3号疲劳试样的表面敏感性系数仅为0.08。对比拉伸、冲击、疲劳试验可以看出,不同表面状态试样的力学性能对动态加载过程更为敏感。
(1)Ti80合金表面打磨态和深缺口试样的抗拉强度呈增加趋势,预制裂纹试样的抗拉强度下降较为明显,断后伸长率随着表面质量的下降及缺口深度的增加而减小。 (2)Ti80合金不同表面状态试样的冲击吸收能量随着表面质量的下降及缺口深度的增加显著减小,表面打磨划痕及微小缺口均会使材料的疲劳寿命显著缩短。 (3)不同表面状态试样静态拉伸试验的表面敏感性系数浮动较小,不同表面状态试样的力学性能对于动态加载过程更敏感。
免责声明:本网站所转载的文字、图片与视频资料版权归原创作者所有,如果涉及侵权,请第一时间联系本网删除。
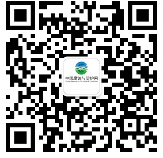
官方微信
《腐蚀与防护网电子期刊》征订启事
- 投稿联系:编辑部
- 电话:010-62316606
- 邮箱:fsfhzy666@163.com
- 腐蚀与防护网官方QQ群:140808414