随着油气资源需求量不断增加及高温高含硫酸油气田的勘探开发,油气田面临的服役环境日益苛刻。高温、高H2S/CO2分压、Cl-及S元素等多因素综合作用对油气工业用管材方案设计和现场生产安全提出挑战。
镍基耐蚀合金因具有良好的力学、加工及耐蚀性,被广泛应用于酸性油气田开发中。镍基合金中Cr、Ni元素含量较高,可以在材料表面形成钝化膜,有效保护金属基体。服役温度及H2S/CO2分压升高、S元素沉积及高盐环境Cl-侵蚀等因素均可能影响镍基合金表面钝化膜的完整性。钝化膜一旦遭到破坏且不能有效自修复,可能会形成点蚀,从而引发腐蚀失效问题。
镍基耐蚀合金在高温高酸性环境中存在的主要失效风险为点蚀和阳极溶解型应力腐蚀开裂。而阳极溶解型应力腐蚀开裂多萌生于钝化膜局部破损形成的点蚀坑位置。因此,点蚀的萌生与发展对镍基耐蚀合金在高含硫酸环境中的服役性能变化起着重要作用。
目前,对于镍基耐蚀合金在高温高含硫酸环境中的腐蚀行为研究多聚焦于其在服役环境中的腐蚀速率、点蚀敏感性和应力腐蚀开裂敏感性评估,针对其在高温高酸性工况下点蚀萌生与发展机制的系统分析讨论相对较少。为此,有必要开展试验评价及分析工作,探究镍基耐蚀合金在高温高酸性腐蚀环境中的钝化膜破钝机制。
中海油研究总院有限责任公司和北京科技大学的研究人员利用高温高压反应釜模拟高温高含H2S/CO2酸性腐蚀环境,开展不同周期下的腐蚀模拟评价试验,研究了G3合金在高温高酸性腐蚀环境中的点蚀敏感性,提出了G3合金的钝化膜破钝机制。
试验材料及溶液
试验材料为G3合金(UNS N06985),热处理状态为退火+固溶态。将材料加工成尺寸为20 mm×20 mm×3 mm的试样,用水磨砂纸逐级打磨试样表面后抛光,并依次进行丙酮除油、去离子水和无水乙醇清洗、冷风吹干后,放置在无氧器皿中备用。每组腐蚀模拟试验取6个平行试样。
试验溶液为30000 mg/L NaCl溶液,使用去离子水和分析纯级化学试剂配制而成。试验开始前,向试验溶液中通入99.999%高纯氮气进行除氧处理,每升溶液的通气时间约为12 h。
高温高压腐蚀模拟试验
在高温高压反应釜中模拟高温高含H2S/CO2腐蚀环境:150 ℃,3 MPa H2S分压,2 MPa CO2分压,30000 mg/L NaCl溶液。
将腐蚀试样安装在高温高压反应釜内的夹具上,采用高纯氮气吹扫釜体除氧1 h,然后导入试验溶液。釜体升温至150 ℃后,通入试验气体至设定压力,试验周期分别为168,336,504,672 h。
腐蚀形态观察
高温高压腐蚀模拟试验结束后取出试样,去离子水清洗,无水乙醇脱水后冷风吹干。利用SEM观察试样表面腐蚀形态,并结合EDS对试样表面钝化膜进行物相分析。
图1 试样经过不同时间腐蚀试验后的表面微观形貌
由图1可见:腐蚀168 h后的试样表面平整且具有肉眼可见的金属光泽,微观可见清晰完整的原始机械划痕,几乎没有腐蚀痕迹;腐蚀336 h后,试样表面出现少量颗粒状腐蚀产物凸起,原始机械划痕深度变浅,未见明显腐蚀产物生成。随着腐蚀时间的延长,试样表面的颗粒状腐蚀产物逐渐增多,腐蚀504 h后,基体表面依然完整,而腐蚀672 h后,试样表面完整性受到破坏,部分区域钝化膜出现破损并形成了大小不一的点蚀坑。其中,最大点蚀坑直径约为42.0 μm。进一步观察发现,点蚀坑呈闭合状态,蚀坑口仍覆盖有多孔钝化膜。
进一步分析腐蚀672 h后试样表面点蚀坑内外钝化膜的元素组成,可见蚀坑内钝化膜主要含有Fe、Ni、Cr、Mo、O和S元素,而点蚀坑外没有检测到S元素,说明经过腐蚀后点蚀坑内钝化膜中含有一定量的硫化物,H2S参与了G3合金在高酸性环境中的点蚀发展进程。
钝化膜性能测试
采用AXIS-UltraDLD型X射线光电子能谱在不同电位条件下进行测试,进一步分析钝化膜的组成,光源选用单色Al Kα(入射光子能量为1486.6 eV),15 kV靶电压,1.33×10-6 Pa真空度。对谱图进行谱线能量校正后,利用XPS peak41曲线拟合程序对谱图峰位进行拟合分析。
图2 试样经过不同时间腐蚀试验后表面钝化膜中Cr元素的高分辨XPS结果
图3 试样经过不同时间腐蚀试验后表面钝化膜中Ni元素的高分辨XPS结果
图4 试样经过不同时间腐蚀试验后表面钝化膜中Fe元素的高分辨XPS结果
由图2~4可见:腐蚀336 h后,G3合金表面钝化膜依旧保持完整,由Cr2O3、Cr(OH)3、NiO、Ni(OH)2和FeO、Fe3O4等组成;腐蚀504 h后,钝化膜逐渐受到侵蚀,出现了少量NiS;腐蚀672 h后,Cr、Ni的氢氧化物和氧化物及Fe氧化物的信号均明显减弱,钝化膜中出现了Cr、Ni的硫化物Cr2S3、NiS2及铁硫化物FeS,且信号均较强。材料表面钝化膜稳定性被破坏,诱发点蚀。金属硫化物的出现可能是导致G3合金表面钝化膜发生不可逆损伤的原因。
破钝机制分析
根据MACDONALD等提出的点缺陷模型(PDM模型),钝化膜具有双层结构且存在高含量的点缺陷。钝化膜中电子及空穴传输处于动态平衡状态。对于电子来说,在金属/膜或膜/溶液界面进行的电化学反应是一个速度控制步骤,而金属离子或氧离子缺陷在钝化膜中的传输也是一个速度控制步骤。
在钝化膜的生长过程中,施主缺陷(氧空位)主要存在于金属/钝化膜界面,并消耗于钝化膜/溶液界面,而受主缺陷(金属间隙离子)主要存在于钝化膜/溶液界面,并消耗于金属/钝化膜界面。氧空位的迁移会导致钝化膜的生长,而金属间隙离子的迁移使得钝化膜发生溶解。
图5 G3合金在高温高酸性环境中的钝化膜破钝机制
如图5所示,腐蚀初期,G3合金钝化膜表层主要由Cr、Ni的氢氧化物组成,钝化膜内层主要由Cr、Ni、Fe的氧化物组成。钝化膜结构具有双极性n-p型半导体特性,能够很好地阻碍阴离子向钝化膜内层扩散及阳离子向钝化膜外层扩散,有效保护基体表面。
根据PDM模型,随着腐蚀的进行,钝化膜中的氧空位不断迁移至钝化膜/溶液界面处,发生Schottky空位对反应,导致钝化膜表面金属阳离子溶解并与OH-形成金属氧化物沉淀。由于溶液中S2-、HS-大量存在,且其极性高于Cl-和OH-,与Cl-及OH-发生竞争吸附,在钝化膜表层形成金属硫化物,这与上述试验及XPS分析结果相符。同时,钝化膜中的S2-可以借助氧空位向基体一侧扩散迁移。
钝化膜中空位迁移速率可能改变钝化膜的保护性能。当S2-空位迁移速率小于金属氧化物氧空位迁移速率时,迁移到钝化膜中的S2-不足以破坏钝化膜的完整性,钝化膜内层的金属氧化物仍然维持在动态平衡的稳定状态。而当钝化膜表层金属硫化物中S2-空位迁移速率大于氧空位迁移速率时,S2-借助空位不断向钝化膜内部迁移扩散,最终使金属氧化物完整性遭到破坏。
由于耐蚀元素Cr和Ni化学活性较高,在材料晶界处容易以碳化物形式析出,并在析出相中富积,造成晶界处贫Cr、贫Ni,因此容易在晶界处形成点蚀源。
点蚀源位置的金属大量溶解将促进溶液中的阴离子向点蚀源迁移。一方面,S2-、HS-与Cl-竞争吸附,导致点蚀源位置富集高浓度的S2-和HS-,加速氧化物膜的分解;另一方面,由于歧化反应,钝化膜局部大量H+电离,局部酸化也将加速钝化膜中氧化物层溶解。
S2-、HS-与金属基体发生反应生成的硫化物膜质地疏松,且易于吸附溶液中的Cl-。Cl-进入钝化膜后能够占据膜中的氧空位,并通过Mott-Schottky Pair反应产生氧空位/金属离子空位对,新生成的氧空位再次被Cl-占据,氧空位数量减少,金属离子空位增加。多余的金属离子空位会在基体/膜界面局部堆积,并阻止钝化膜继续生长,破坏钝化膜结构的动态平衡。最终,由于钝化膜局部完全溶解或破裂,点蚀萌生并发展,进而形成稳定的点蚀坑。
结论
1 在高温、高H2S/CO2分压腐蚀环境中,腐蚀初期,G3合金表面钝化膜主要由Cr、Ni的氢氧化物、氧化物 [Cr2O3、Cr(OH)3、NiO、Ni(OH)2] 及Fe的氧化物(Fe3O4和FeO)组成。随着腐蚀时间的延长,钝化膜中出现了Cr、Ni的硫化物Cr2S3、NiS2及铁硫化物FeS。
2 G3合金在高温高酸性环境中具有较高的点蚀敏感性。在模拟高温、高H2S/CO2分压腐蚀环境中腐蚀672 h后,G3合金表面钝化膜破损并形成了大小不一的点蚀坑,其在高温高酸性环境中的钝化膜破钝及点蚀萌生与S2-对钝化膜的硫化作用有关。
免责声明:本网站所转载的文字、图片与视频资料版权归原创作者所有,如果涉及侵权,请第一时间联系本网删除。
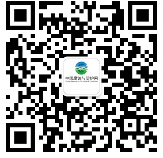
官方微信
《腐蚀与防护网电子期刊》征订启事
- 投稿联系:编辑部
- 电话:010-62316606
- 邮箱:fsfhzy666@163.com
- 腐蚀与防护网官方QQ群:140808414