大量SCC现场调查分析结果表明,SCC通常发生在防腐蚀涂层破损和阴极保护失效的管体位置,在管体上通常表现为垂直于主应力方向的多条平行裂纹。按照其发生的环境和开裂路径,SCC可分为两种类型:高pH SCC和近中性pH SCC。
SCC的孕育、萌生和前期扩展需要较长的时间,其风险随着管道运行年限的增加而增加,一般认为服役超过10年的非环氧类防腐蚀层管道具有发生SCC的风险,管道运行20年左右进入SCC高发期。国内长输管道经过近20年的快速建设和发展,在役管道里程接近14万公里,与SCC相关的管道防腐蚀层类型、管线运行参数、管道防腐蚀和检测管理方法都有了显著的变化、提高或改进。 埋地管道SCC历史调查及案例分析 在国外相继发生多起由SCC导致的埋地管道开裂事故,加拿大能源管道协会(CEPA)于1996年首次颁布了SCC管理推荐做法的背景下,2001年中国石油集团公司组织了由中国石油大学、四川石油勘探设计研究院和石油管材所等多家单位参与的长输埋地管道SCC调查和敏感性试验评价。 埋地管道SCC现状调查 自2002年SCC调查以后,经过近20年的发展,国内长输埋地管道里程数量、运行工况和日常管理维护方式都发生了巨大变化,长输油气管道总里程超过14万公里,大口径、高钢级和高压力的天然气管道投运越来越多,在役管道外防腐蚀层90%以上为三层聚乙烯(3PE),定期开展的管道内外检测成为管道完整性管理的重要依据。
部分管道的运行年限超过20年,进入了埋地管道SCC的高发时期。为明确在役管道SCC风险现状,依据埋地管道SCC发生特点和直接评价标准,一方面选择了不同服役时间的管道SCC高风险位置进行现场开挖,开展裂纹检测和应力腐蚀相关参数的测试,明确所选择管段的SCC风险,另一方面整理分析近年来的外腐蚀调查和环焊缝排查工作的调查结果,分析外腐蚀位置和管道补口位置的SCC风险。
埋地管道补口位置现场开挖检测 A管道 服役时间:22年 管材:X60螺旋焊管 壁厚:7.14mm 防腐蚀层和补口类型:3PE防腐蚀层,热收缩带 位置1 距离上游压气站7.3km 位置2 距离上游压缩机12.6km 位置3 距离上游压缩机14.6km 位置4 距离上游压缩机16.3km 位置5 距离上游压缩机40.0km,交流电压最大12.9V B管道 服役时间:8年 管材:X70螺旋焊管 壁厚:17.5mm 防腐蚀层和补口类型:3PE防腐蚀层,环氧底漆+热收缩带 位置6 石方区、补口浮锈 C管道 服役时间:8年 管材:X70直缝管 壁厚:26.2mm 防腐蚀层和补口类型:环氧底漆+聚丙烯冷缠带 位置7 压气站出站变壁厚焊接位置 D管道 服役时间:7年 管材:X60螺旋焊管 壁厚:7.1mm 防腐蚀层和补口类型:PE+聚氨酯保温层+FBE,环氧底漆+热收缩带+保温瓦+热收缩带 位置8 阴极保护屏蔽、微生物腐蚀 A管道:补口位置的典型防腐蚀层和补口腐蚀形貌如图1a所示,腐蚀以均匀腐蚀为主,腐蚀产物为棕褐色铁锈,主要成分为Fe3O4和α-FeOOH,与大气腐蚀产物类似,表明补口位置的腐蚀主要是由埋设位置沙土中的湿气进入补口导致。打磨除锈后的裂纹渗透检测结果如图2a所示,仅在个别位置有很小的点蚀坑,点蚀深度在0.2mm左右,没有发现裂纹类缺陷。 B管道:补口位置典型防腐蚀层和腐蚀形貌如图1b所示,腐蚀产物为黄褐色浮锈,管道没有发生明显的点蚀。腐蚀产物的主要成分为α-FeOOH,部分为SiO2杂质,这表明该位置的腐蚀也主要是湿气进入补口导致的。打磨除锈后的裂纹渗透检测结果如图2b所示,没有发现点蚀或者裂纹类缺陷。 C管道:焊缝位置防腐蚀层形貌和腐蚀形貌如图1c所示,在聚丙烯冷缠带防腐蚀层底部存在翘边和脆化的现象,但内部红色底漆基本良好,没有明显的腐蚀迹象。打磨后的裂纹渗透检测结果如图2c所示,没有发现点蚀或者裂纹类缺陷。 D管道:补口位置的腐蚀形貌如图1d所示,腐蚀产物为灰黑色黏稠物质,管道存在明显的点蚀,且点蚀坑深度较大,达管道壁厚的70%。腐蚀产物的主要成分为FeCO3和FeS,是典型的厌氧环境硫酸盐还原菌腐蚀产物,同时腐蚀产物中还含有部分β-FeOOH,该物质主要在富含氯离子的环境中产生。这表明该环境中的氯离子加速了细菌腐蚀。打磨除锈后的裂纹渗透检测结果如图2d所示,除了较大的点蚀坑外,补口局部位置还存在深度1mm左右的点蚀坑,没有发现明显的裂纹类缺陷。
图1 不同调查点管道的防腐蚀层和腐蚀形貌
上述现场调查结果表明,所调查管线的补口位置均未发生SCC现象。
管道外腐蚀开挖调查结果
收集分析了2015-2020期间开展的总共98处管道外腐蚀调查结果。现场调查检测均未发现管道表面有裂纹类缺陷,具体调查信息和结果如表1所示。其中管道防腐蚀层主要为3PE,防腐蚀层类型中的其他是指聚丙烯冷缠带或沥青。调查结果表明,在发生外腐蚀的管道中,阴保屏蔽或者保护不足的有62处,存在机械损伤的有33处,发生明显点蚀的有43处。阴保不足或屏蔽导致管道发生腐蚀是管道发生SCC的必要条件,机械损伤导致的应力集中可明显增大管道发生SCC的风险。而调查结果表明,在上述易发生SCC的管道位置均未发现SCC现象,这表明目前国内埋地长输管道SCC的风险较低。
表1 2015-2020管道外腐蚀调查结果
环焊缝排查检测结果
针对事故风险高的环焊缝补口位置,中石油自2018年起开展了环焊缝排查工作,将需要排查的环焊缝定位、开挖、去除补口防腐蚀层并打磨后,采用超声相控阵、超声衍射时差法、磁粉、渗透和X射线等无损检测技术,对焊缝位置的缺陷进行详细的检测,并对检测出的缺陷定性、定量、分级和评价。
目前,总共已完成3万多处环焊缝开挖检测工作,截至2019年底共发现了180多处裂纹类缺陷,但通过渗透或者磁粉检测发现的表面开口裂纹仅3处,且都是单一裂纹。其中,两处焊缝表面裂纹沿管道轴向扩展,焊缝位置没有腐蚀迹象:裂纹1位于管道的1点钟位置,长度7mm,裂纹2位于11点半位置,长度8 mm,裂纹形貌如图3所示。
(a) 裂纹1
由于焊缝表面没有腐蚀迹象,所以这两处裂纹主要由焊接和应力集中导致。另一处存在表面裂纹的补口位置有浮锈,射线检测时发现了3mm左右的裂纹,去除浮锈后再次进行渗透检测时,裂纹消失,这表明该处裂纹很浅。该处补口位置土壤较为干燥,补口热收缩套黏结力合格(大于80N/cm),腐蚀产物仅为一层浮锈,不存在明显的点蚀,发生腐蚀的风险低。且该位置管线运行压力为6.7MPa,壁厚17.5mm,管径1016mm,管道环向受力仅为194MPa,为管道屈服强度(485MPa)的40%,受力较低,因此该位置出现SCC的风险较低,该裂纹由焊接导致的可能性较大。
以上分析表明,环焊缝排查发现的裂纹多数为内部裂纹而非表面开口裂纹,仅有3处表面开口裂纹,其中两处裂纹位置不存在腐蚀,1处裂纹位置发生腐蚀和SCC的可能性很小,因此可判定这3处裂纹不是SCC导致的裂纹。环焊缝排查结果表明,现阶段国内管道补口位置发生SCC的风险较低。
原因分析 上述国内管道SCC相关调查结果表明,目前国内尚未发现典型的管道高pH或者近中性pH的SCC,SCC风险较低。国内外大量的现场调查和试验研究数据表明,管道SCC只有在应力、环境和材质3个因素的协同作用下才会发生,风险随着管道运行年限延长而增加,且SCC只可能在因涂层破损而发生腐蚀的位置发生。目前,国内管SCC风险较低的原因主要有以下几点: 01 国内在役管道外腐蚀风险低 02 管道服役时间较短 03 管道运行压力相对较低 表2 国内主要输气管道运行压力
结合国内管道服役现状,建议现阶段采取以下措施降低3PE防腐蚀层管道发生SCC的风险:
(1)继续加强外腐蚀控制,通过定期开展外检测和内检测,修复破损涂层,防止出现3PE防腐蚀层发生大面积剥离腐蚀的情况; (2)根据埋设土壤环境,对在役的X70和X80钢级管道设定合适的阴极保护电位范围,避免发生析氢; (3)在日常外腐蚀开挖检测工作中,重点关注防腐蚀补口、划伤、硌伤、凹陷、环境干湿交替和石方区等SCC高风险位置,并开展裂纹检测工作; (4)对运行20年以上的管线开展SCC直接评价,建立SCC位置识别模型,积累SCC高风险位置识别经验; (5)管道运行和启停输过程中,尽量减少压力波动范围、升降压速度和次数。 结束语 国内现有SCC案例分析和管道补口、环焊缝和外腐蚀开挖调查结果分析表明,国内尚未发现典型的埋地管道SCC案例,已发生的管道SCC主要与材料制造缺陷、焊接缺陷和机械损伤有关。目前,国内3PE防腐蚀层埋地管道外腐蚀控制较好,服役时间较短和服役压力较低,因此管道发生SCC的风险较低。但国内3PE防腐蚀层管道存在较多的剥离和补口失效问题,易产生阴极保护屏蔽导致管道腐蚀,随着服役时间的延长,管道存在发生近中性pH SCC的风险。建议通过加强外腐蚀控制,防止高强钢阴极析氢导致的氢脆,减少运行压力波动,开展针对性SCC调查和直接评价工作,降低SCC风险,保障管道的安全运行。
免责声明:本网站所转载的文字、图片与视频资料版权归原创作者所有,如果涉及侵权,请第一时间联系本网删除。
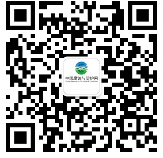
官方微信
《腐蚀与防护网电子期刊》征订启事
- 投稿联系:编辑部
- 电话:010-62316606
- 邮箱:fsfhzy666@163.com
- 腐蚀与防护网官方QQ群:140808414