截至2020年8月,全球可运行核电机组共441台。核电厂二回路系统是发电系统的核心部分,碳钢、不锈钢、耐蚀镍合金、铜镍合金、钛合金等是二回路常用的金属材料。二回路给水管线、凝结水管线、疏水管线等不可避免地会发生流动加速腐蚀(FAC)。 统计数据表明,FAC引起的管道失效量占管道失效总量的33%,在所有管道失效因素中位列第一名。为预防和减少FAC导致的事故,技术人员从1970年前后就开始对FAC进行了研究。这些研究主要集中在FAC的机理、影响因素、预防及缓解措施等三个方面。 FAC的机理与影响因素 碳钢、不锈钢以及Cr合金等材料表面的氧化膜能够有效降低材料基体直接与外界接触造成的腐蚀。但表面的氧化膜与溶液接触会发生溶解,若溶液是流动的,还会加速溶解过程,该现象称为FAC。 氧化膜溶解会导致金属基体暴露发生腐蚀,从而使材料厚度减薄,产生安全隐患。FAC现象在核电、石油和天然气行业都较为常见。 FAC过程是基体-氧化膜界面和氧化膜-溶液界面的微观溶解(传质)过程。以碳钢为例,FAC的机理如图1所示,在基体-氧化膜界面处,基体中的铁通过氧化反应转变为Fe3O4、Fe(OH)2;在氧化膜-溶液界面处,主要发生氧化膜溶解产生可溶性Fe2+这一过程,Fe2+通过流体边界层向主流区域扩散。因此,FAC的整个过程可以视为金属氧化膜和基体的溶解引起了金属的减薄。 图1 碳钢FAC机理示意 FAC的发生可以看作是两个相互影响过程,即化学溶解和传质过程。当这两个过程的影响因素发生变化时,FAC会随之产生偏移。这些影响因素可归结为流体动力学因素、化学环境因素、材料因素。 流体动力学因素 流体在管道中的流动状态受流体流速、管路几何形状、流体各相比等影响。二回路系统中的主要介质为化学处理过的碱性水,在不同管段以过热干蒸汽、湿蒸汽、饱和液等形态存在。流动状态与流体形态都会影响FAC的传质过程。 流速 流动边界层是金属氧化膜溶解产生的铁离子向主流区域扩散的通道,其扩散速率(传质速率)与边界层厚度成反比,流速越大,边界层厚度越小,则传质速率越快。 伊成龙测定了内径为2.0、2.2、2.4 mm的P11钢管在温度273 ℃下的FAC速率,结果发现内径为2.0 mm的钢管减薄最严重。 UTANOHARA等研究发现,90°弯头的FAC速率随着流速增加而增加,当流速为0.39~5.74 m/s时,对应的FAC速率为0.1~0.35 mm/a,流速与FAC速率之间的关系是非线性的。 SUBRAMANIAN等和YONEDA等的研究得到了相似的结论,即FAC的速率与流速的1.0~1.5次幂成正比。 SATOH等通过数据拟合得到FAC速率与流速的1.7次幂成正比的结论。试验条件不同是导致幂指数存在差异的原因。 管道几何形状 当流道(孔板、变径、弯头、三通等)的几何形状发生突变时,会产生涡流、回流等现象,内部的传质过程发生变化。 AHMED分析了弯头、孔板等部件上下游流场及FAC速率的变化,发现流体流经管道部件会产生邻近效应,导致下游临近管线FAC减薄率上升近70%;同时明确了受临近效应影响的下游管线长度约为管道直径的5倍。 马娜等将某核电厂由于减薄而更换下来的弯头进行了X射线衍射分析,结合弯头先前的工作参数,发现弯头曲率过小是导致其减薄的主要原因。 SINGH等通过试验研究发现流体流经管道连接焊缝时,会在焊缝下游产生涡流,导致焊缝处材料FAC加重。 流体各相比 二回路中的流体主要涉及气液两相流。FERNG等使用台湾核电站低压汽轮机进行了气液两相流FAC试验,并指出气液两相流系统中的腐蚀主要由液滴撞击氧化膜产生,重力、离心力、两相分离等是影响腐蚀的关键因素。 AHMED等研究发现,在雷诺数相同情况下,当入口流体中气相质量分数由0.001%增加至0.003%时,孔板下游管段的FAC速率峰值下降约34.2%。 李鹏通过计算流体力学(CFD)软件模拟得到流速为0.58 m/s条件下,入口流体含气率在0.1%~1.0%范围逐渐增加时,弯头FAC速率从0.37 mm/a逐渐减小至0.13 mm/a。 环境因素 环境因素是影响FAC的众多因素中不可忽视的因素,包括流体温度、pH、溶解氧含量等。 温度 REMY等认为温度对FAC产生的影响是间接的,且具体表现在两个方面。一方面,随着温度的升高,溶液中亚铁离子含量降低;另一方面,温度对流体黏度和控制传质过程的亚铁离子扩散速率的影响非常大。 对于单相流,最大腐蚀速率出现在温度为130~150 ℃时;对于两相流,最大腐蚀速率则出现在100~250 ℃时。在温度为125、180、225 ℃时,碳钢表面氧化膜的厚度稳定在1 μm左右,125 ℃时氧化膜比较疏松,180、225 ℃时氧化膜变得比较致密,在温度超过130 ℃时,碳钢表面氧化膜的孔隙率随温度升高而变小。 pH Fe3O4的溶解与FAC速率有直接关系,当pH<9.8时,Fe3O4的溶解度随温度升高而增大,当pH为9.8~10.3时,Fe3O4的溶解度随着温度升高而降低。这是因为温度影响了Fe(OH)2与Fe3O4转换的反应平衡常数。 王柱等研究发现,在气液两相条件下,当某电厂二回路的给水pH由9.0提高至9.6,给水中铁离子质量分数由2.2 μg/kg降至1.0 μg/kg时,管壁减薄速率下降约100倍。 溶解氧含量 JIANG等发现对蒸汽发电回路进行微氧处理后,管道内亚铁离子质量分数下降约80%。这是由于加氧处理后,氧化膜表面的FeOOH和Fe2O3更易转化为Fe3O4。 WOOLSEY等分别在115 ℃、pH 9.1和150 ℃、pH 7.8条件下对碳钢进行了腐蚀减薄试验。结果发现:当二回路中氧气质量分数为2.1~3.0 μg/kg时,碳钢的减薄速率保持在0.99 mm/a,氧气质量分数达到3.8 μg/kg后,减薄速率迅速下降;在两种试验条件下,碳钢减薄速率的变化趋势相同,但在后一种试验条件下,减薄速率整体更大。 SATOH等通过试验发现:当溶解氧质量分数大于100 μg/kg时,碳钢几乎不发生FAC,在氧气质量分数小于1 μg/kg的环境中,其FAC减薄速率约为2.7 mm/a;表面已形成良好氧化膜的碳钢,在氧气质量分数小于1 μg/kg、流速为6.3 m/s的环境中腐蚀约10天后,氧化膜会完全溶解。 腐蚀电位 由于氧含量对电极反应有很大影响,因此腐蚀电位对FAC的影响多与氧含量相关。SATOH等在试验回路中先通入氮气除氧(0~30天),使溶液中氧气质量分数小于1 μg/kg,再通入N2和O2的混合物(30~70天),使溶液中氧气质量分数大于100 μg/kg,最后通入氩气除氧(70~90天),使氧气质量分数小于1 μg/kg。在此过程中,腐蚀电位、内径的变化如图2所示。 图2 腐蚀电位、内径随时间的变化 材料因素 材料因素主要指钢的化学成分。这是由于氧化膜的稳定性和溶解度受材料化学成分的控制。铬元素具有抑制钢材腐蚀的作用。通常1%的铬就能使钢材的FAC速率降至很低。铬元素可以提高钢材抗FAC能力的主要原因是铬在碳钢表面形成了Fe3XCrO4尖晶石氧化膜,该物质在高温时的溶解度比Fe3O4低很多;另外,铬元素的添加使氧化膜不会形成大颗粒的晶体,从而降低了氧化膜的孔隙率,提高了其对基体的保护作用。 王亮亮在模拟二回路工况下对A335P11合金钢、20碳钢、A106B碳钢等管材制作的弯头、三通、变径管进行了1200小时的FAC模拟试验,结果表明铬含量最高的A335P11合金钢的抗FAC效果最好。 伊成龙则在相似的条件下对SA335-P11(1.09% Cr)、SA106B-0.2Cr(0.2% Cr)、SA106B-0Cr(0.066% Cr)进行了1500小时的FAC模拟试验,结果发现SA335-P11的点蚀较严重。其原因可能是试样中硫离子和氯离子含量以及流速影响了SA335-P11材料表面氧化膜的形成。 FAC的研究方法 目前,国内外研究FAC的方法主要包括试验测试和数值模拟两大类。试验测试需要搭载试验平台,尽可能还原二回路的运行工况,并通过观察材料表面的变化测得FAC速率。数值模拟相对于试验测试效率更高,但其结果较理想化,多用于辅助试验结果分析以及现场管路减薄预测。 试验测试 实验室多采用搭载流动回路的方法对FAC进行研究,常用的FAC试验装置有旋转式、管流式和冲击式。旋转式和冲击式装置多用于固液两相冲刷腐蚀试验。管流式装置更适用于核电厂二回路流动加速腐蚀的研究。 田钰和王力等搭载管流式试验台,测试了不同材料的FAC速率。管流式试验装置主要包括蒸汽发生器、热交换器、稳压罐、背压阀、流量计、温度计、循环泵、高压釜、储液罐,相当于建立了核电厂二回路的等效模型。 MADASAMY等使用γ射线对钢制管道内壁的氧化膜进行辐照,利用放射性同位素捕捉方法研究了管道的FAC,并取得了不错效果。试验结果对核电厂二回路FAC的研究具很好的参考价值。FAC试验所需周期长(大部分单次试验的时间在7天以上),装置长期无间歇运行,因此对阀门、管件以及密封的可靠性要求较高。 测试结束后,常使用扫描电镜、光学显微镜、立体显微镜等观察FAC后试样的表面形貌,包括氧化膜溶解情况、钙质层沉积,使用X射线衍射和等离子体-原子光谱法分析试样表面物质的化学成分,推算其物相。 失重法是常用的FAC速率评价方法。该方法较为简单,但在连续试验过程中无法进行称量,因此只能得到整个试验周期的FAC速率。 直流电压法是借助材料壁厚减薄引起的电阻变化来反映FAC速率,能够实现对FAC速率的连续监测;超声波壁厚测量方法多用于电厂在役管道及设备减薄测量。 YUN等综述了电厂使用的现役壁厚减薄估算方法(总分法、连续变量均匀性试验方差分析法)和局部减薄估算方法(位置偏差法、二项变量一致性检验法、连续变量均匀性试验法)。 数值模拟 用于FAC模拟的软件可分为两大类。一类是根据核电厂长期运行积累的数据与经验开发的用于评价核电厂FAC的软件如CHECWORK,这类软件能够预测部件的壁厚减薄率及使用寿命,为核电厂的检修方案制定提供一定参考,指导修改FAC老化管理大纲,实现零部件寿命最大化。另一类是商业化的计算流体力学(CFD)软件,如Fluent、CFX、Comsol等。这些模拟软件都离不开腐蚀数学模型的建立。 FAC模拟的理论依据 碳钢直管段常用的FAC速率计算公式如下: 式中:vFAC为FAC速率,mm/a;ceq为可溶性含铁组分的溶解度,mol/L;cb为主流区域中可溶性含铁组分的浓度,mol/L;K*为生成Fe(OH)2反应速率常数,m/s;k为传质系数,m/s;θ为氧化膜的孔隙率;D为可溶性含铁组分的扩散系数,m2/s;δ为氧化膜厚度,m。 直角弯头、孔板下游FAC速率的计算公式如下: 式中:cw为氧化膜-水界面可溶性含铁组分的溶解度,mol/L;τ为壁面剪切力,N;ρ为介质密度,kg/m3;U为主流区域流速,m/s;Sc为施密特数。 两相流液滴冲击引起的FAC减薄速率计算公式如下: 式中:mFAC为FAC减薄速率,kg/s;Cs为由管道制造和安装决定的系统常数;N为频率,Hz;Fθ(θ)为特征函数;H为壁面硬度,HB。 模拟研究 刘忠等建立了碳钢在单相流中的FAC数学模型,并用模型计算了直管的FAC情况,结果与前人的研究结果吻合较好。 刘景军等详细介绍了固液两相流动的数值模拟模型与方程,通过比较数值计算结果与实测结果,说明了模型的正确性。 KESHTKAR和RANI等用Fluent软件模拟了双弯头管路的FAC传质系数,结果发现沿流动方向第二个弯头内侧的FAC速率最大,且随着雷诺数的增大,FAC速率也随之增加。 LIN等使用CFD软件模拟了不同角度碳钢弯管在不同雷诺数下的FAC。结果发现,流体沿管壁流动产生的二次流和流动分离会导致弯头内壁边界层厚度发生变化,传质系数与边界层厚度成反比。 PRASAD等以随机Hougaard为原理,结合58°弯管的FAC试验数据对核电站高温高流量管道的壁厚减薄进行了预测,其预测值的绝对误差在8%左右。 SANAMA等对前人提出的孔板下游FAC速率预测模型进行了修正,当孔板比为0.25和0.5时修改后模型预测的最大FAC磨损位置误差分别由30%和11%降低至3%和2%。 JYRKAMA等使用Kriging曲面拟合方法获得了核电金属管道部件的预测寿命,该方法克服了传统网格点到点值方法的不确定性和局限性。 相较于试验测试,数值模拟的周期更短,成本更低,能实现变量的稳定控制(温度,流速,pH等),但由于数值模拟过程中对几何模型、流体物性等进行了简化,因此模拟结果为理想状况,与实际情况存在差异。数值模拟结果可以为已有管路的改进提供一定的参考依据。 - FAC的防护措施 - 碱化剂 使用碱化剂提高二回路的pH从而降低FAC的速率是一种较为常用且有效预防FAC的方法。国内压水堆核电厂多用氨和联氨的全挥发处理法。在使用该方法处理时,由于氨的挥发性极强,其在气相中的分压远大于凝水中的,导致凝水的pH下降,下部管段产生腐蚀。 试验证实,乙醇胺(ETA)在150 ℃和300 ℃下的气水分配系数分别为0.26和0.66,更倾向溶解于水,故可以用ETA替代氨和联氨进行二回路水化学处理。 王琳等使用Mathcad软件模拟了ETA在二回路系统中的分布,模拟结果表明,若要使主给水pH达到9.5~10.0,ETA质量分数需达到3.5~25.1 mg/kg。 蔡金平和曹松彦等通过试验验证了ETA在高温下的稳定性,以及它与二回路常用碳钢材料的良好相容性。 近几年来,对复合碱化剂的研究也逐渐深入。赵永福等就乙醇胺和氨的复合应用可行性提出了依据,并通过模拟和试验的方法优选出复合碱化剂中ETA 和氨气的最佳比例。 曹林园等通过高温高压腐蚀试验考察了压水堆二回路工况下A106Gr.B和A508Ⅲ钢分别在NH3·H2O、NETA+DMA和ETA碱化剂中的均匀腐蚀和电化学腐蚀性能。结果发现在复合碱化剂条件下,两种材料腐蚀速率分别下降42%和29.01%。 我国秦山二期核电厂采用NH3H2O+ETA的联合控制法,秦山三期采用吗啉和联氨的全挥发处理方法在设备运行期间,这些复合碱化剂均表现出不错的防腐蚀效果。 合金材料 铬可以在合金表面形成钝化膜,且腐蚀介质pH越小,铬在钝化膜中富集就越多,因此含铬合金多表现出良好的耐蚀性。含铬金属管道内锈层中的铬含量要高于外锈层中的铬含量,使内锈层具有更好的韧性及致密性。由于贫铬效应,镍铬合金中的铬质量分数通常要在10%以上才能确保合金表面有效且准确地形成Cr2O3氧化膜,但提高铬元素含量会使合金在高温下的强度降低。 涂层 核电站中易发生FAC的部位多使用碳钢管,所以提升碳钢管的电化学性能可有效抑制FAC的发生。 刘云平在碳钢表面制得了以硅烷为主体、硝酸铈和正硅酸乙酯为添加物的杂化膜。结果表明,相对于单一的硅烷膜,杂化膜对碳钢具有更好的保护作用。 董会等在Q235钢表面沉积了NiCrAl涂层,结果发现:在3.5% NaCl溶液中NiCrAl涂层具有较好的耐蚀性,其腐蚀电流密度约为Q235钢的三分之一,但在高温高压试验中,NiCrAl涂层对基体的保护作用较小。 表面热处理 WANG等对碳钢进行了电镀铬,并在200 ℃温度下对其进行热处理。结果表明表面热处理后,碳钢表面的Cr(OH)3含量降低,Cr2O3和铬的含量上升;相较于未进行热处理的镀铬碳钢,其耐FAC性能更好;相比于同条件下的裸碳钢,FAC质量损失下降88%以上。 GHAZIOF等研究了金属表面Cr-C合金涂层经不同退火温度处理后的性能变化,发现经300 ℃退火处理后,涂层的硬度提升,但耐蚀性下降;经600 ℃退火后,涂层中部分碳会析出,使得涂层硬度上升,耐蚀性提升。 - 结束语 - 对于核电厂二回路FAC研究多为实验室或理论研究,这些研究虽然不能代替实际情况,但其研究方法及结论为核电厂实际运行维护提供了很大的帮助。 FAC受温度、流速、pH、管路几何形状等影响,其中温度和pH对FAC的影响研究较为成熟。数值模拟是FAC最常用的研究方法,模拟结果十分明确,且周期短,可以根据需求自由设置试验工况。数值模拟的结果需要结合实际工况进行合理性判断。 但由于实际工况的复杂性,在机组的日常运行中,碳钢管不单会出现FAC,而且常伴随出现应力腐蚀和液滴冲击腐蚀等,当多种腐蚀同时发生时,用于单一腐蚀的预测手段不能有效预测管件的剩余寿命及安全性。使用合金材料和水化学处理是预防FAC常用和较为有效的方法,秦山二期与三期工程是我国使用复合碱化剂技术较为成熟的核电站。 在设计模拟FAC搭载的试验平台时,为了测试温度对FAC的影响,除了满足工况及基本的安全、密封性等要求外,还应考虑管路中液体的流动状态以及模型的缩放问题。 核电厂对于二回路中介质化学性质的监测技术已较为成熟,管道在使用过程中不断损耗,也应逐步加大对管道的保护,如碱化剂使用可在一个运行周期内参照介质参数的变化进行动态调整。
免责声明:本网站所转载的文字、图片与视频资料版权归原创作者所有,如果涉及侵权,请第一时间联系本网删除。
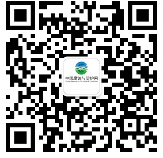
官方微信
《腐蚀与防护网电子期刊》征订启事
- 投稿联系:编辑部
- 电话:010-62316606
- 邮箱:fsfhzy666@163.com
- 腐蚀与防护网官方QQ群:140808414