耐火材料的腐蚀是由于耐火材料与腐蚀性流体之间发生化学反应而导致耐火材料暴露面或热面厚度和质量损失的过程,在这个过程中,耐火材料和腐蚀性流体反应,在耐火材料和流体之间的接触区域趋向于化学平衡。一个重要的观点是,腐蚀反应是朝着局部化学平衡的方向进行的。这意味着可以使用相平衡图来分析腐蚀情况,并预测化学策略来最小化腐蚀和磨损速率。这给了对耐火材料腐蚀感兴趣的人两种选择。第一种是将腐蚀视为一个化学和物理过程,而不需要详细地应用相平衡图——称为“现象学方法”;第二种是使用现象学方法中的信息,并使用相平衡图。后者是对耐火材料腐蚀进行全面理解所必需的。下面将使用现象学方法和相平衡图来分析耐火材料的腐蚀。首先介绍两个基本的原则,它们可以帮助我们理解和控制耐火材料与渣之间的相容性。然后将讨论一些常见的耐火材料类型,它们在不同的腐蚀环境中的表现,以及如何利用相平衡图来优化耐火材料的选择和设计。耐火材料与渣之间的相容性是指耐火材料在高温下与渣反应产生的产物是否有利于保护耐火材料或降低腐蚀速率。相容性可以用酸度和碱度来描述,这两个概念在室温溶液化学和高温腐蚀化学中有不同的定义。
在室温溶液化学中,酸度和碱度是根据水溶液中氢离子(H+)和氢氧根离子(OH-)的浓度来定义的。水溶液中H+和OH-的浓度之积是一个常数,称为水解离常数(Kw),其值为1×10-14。因此,当H+浓度增加时,OH-浓度必须减少,反之亦然。水溶液中H+浓度的负对数称为pH值,其范围从0到14。
在高温腐蚀化学中,酸度和碱度是根据渣中硅酸盐(SiO2)和碱性氧化物(通常是CaO)的含量来定义的。渣中SiO2和CaO的摩尔比称为CaO/SiO2比,其范围从0到无穷大。CaO/SiO2比小于1的渣称为酸性渣,大于1的渣称为碱性渣,等于1的渣称为中性渣。酸性材料是含有过量SiO2的材料,碱性材料是含有过量CaO或MgO的材料。酸性材料在高温下与渣反应时会提供SiO2,碱性材料在高温下与渣反应时会提供CaO或MgO。例如,石英(SiO2)是一种酸性材料,它可以与碱性渣反应生成硅酸钙(CaSiO3);镁砖(MgO)是一种碱性材料,它可以与酸性渣反应生成硅酸镁(MgSiO3)。高温化学中酸度和碱度的定义比上面给出的更复杂。例如,在钢铁精炼中,常用“V”比这个术语,其中比值超过1.0表示碱性化学(通常是碱性渣化学),比值低于1.0表示酸性化学。在这种定义中,“V”比可以用如下的形式表示:V=(CaO+MgO+FeO+MnO+…) / (SiO2+P2O5+Al2O3+Fe2O3+Mn2O3+…)。在许多情况下,使用三元相平衡图来分析腐蚀情况是很方便的。主要的耐火材料组分可以视为三角形的一个顶点(角),而CaO和SiO2是另外两个组分(顶点)。在这些分析中,使用简单的CaO/SiO2比是很方便的。在使用先进的热力学软件进行更复杂的分析时,使用“V”比来定义“平衡”条件可能更准确。腐蚀反应应该被视为系统通过向平衡方向发展来实现相容性的尝试。耐火材料很少在微观尺度上达到化学平衡,因为它们通常是由不同矿物混合制成的。然而,在耐火材料和渣之间的直接腐蚀界面处,局部的体积元素可能处于或接近化学平衡。
耐火材料通常含有一定的气孔率,这些气孔可能是开放的,也就是说,可以被流体介质渗透(称为“显气孔率”),也可能是封闭的,不易被流体介质渗透。如果耐火材料没有气孔(或砖缝、膨胀缝或施工缝),那么腐蚀反应只限于暴露于腐蚀介质的耐火材料表面(称为热面)。当存在气孔时,特别是当存在开放气孔时,腐蚀介质可以渗透到耐火材料内部,导致热面后面的破坏性反应。许多研究人员发现,渣对耐火材料的腐蚀速率与耐火材料的显气孔率成正比。这通常在一定范围内的显气孔率内成立——例如在12%~16%的显气孔率范围内——但在高显气孔率(>20%)时不一定成立。因此,人们致力于提高耐火材料的密度,即获得尽可能低的显气孔率。高密度的耐火材料通常具有较低的磨损速率。可以理解的是,非常高密度的耐火材料可能表现出较低的抗剥落性,导致另一种过程如热震造成的更高的磨损速率。这说明了腐蚀损失是炉衬总磨损速率中可能的多种因素之一。通常有一个磨损过程,如腐蚀,是主要的磨损过程。由于腐蚀介质可以渗透到耐火材料中,这种渗透通常会导致耐火材料“基质”的破坏甚至毁灭。“基质”是指将“粘结”砖和单质型耐火材料粘合在一起的“烧结细粒”的区域。通常,基质含有更多的杂质和更多的气孔,如骨料颗粒,因此腐蚀会以比密度更高或纯度更高的颗粒更快的速度影响耐火材料中最“弱”的组分。在基质攻击极端情况下,粗骨料颗粒会发生快速侵蚀。
耐火材料腐蚀是指高温炉中与反应性组分(如熔渣或玻璃)接触时,耐火材料发生的化学反应和物理变化,导致性能下降或损坏。
图1显示了熔渣或玻璃与耐火材料接触时的情况。耐火材料从热面到冷面有一个温度梯度,即热面温度最高,而冷面温度最低。熔渣或玻璃在高温下会发生化学反应,并且由于毛细作用和重力作用,会向内部渗透。当熔渣或玻璃达到一个足够低的温度时,会固化成为固体,在耐火材料中形成一个“固化面”。耐火材料的热面被熔渣或玻璃覆盖。在大多数冶金应用中,这种覆盖层相对较薄(2~5 mm厚)。在某些没有与金属熔池或熔渣池接触的垂直壁耐火材料结构中,熔渣会堆积在较厚的部分(0.25 mm)。
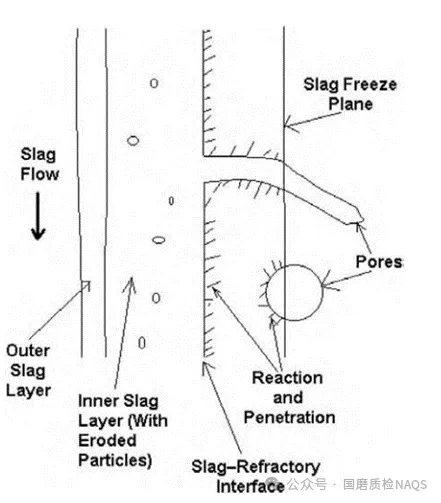
图1 熔渣-耐火材料界面区的横截面
在某些情况下,对使用过的材料进行切片后,可在耐火材料外部观察到两个不同的熔渣层。外层是流动性较好的液态层,内层是粘度较高的固态层,直接接触耐火材料的热面。内层是由于熔渣或玻璃溶解了耐火材料中的一些成分而形成的,其中可能含有耐火材料颗粒。在显微镜下可以观察到这些颗粒。这种双层结构通常出现在液态熔渣沿垂直耐火壁流下的地方。
二维截面图或显微图无法显示截面区域的三维结构。因此,有些孔洞看起来是孤立的,但实际上可能通过截面下方的通道与热面相连。熔渣与耐火材料发生化学反应,在热面附近形成新相。化学反应也发生在热面后方,熔渣与耐火材料颗粒在孔洞壁上接触。在冶金应用中,有时可以看到金属与熔渣一起渗入耐火材料中。温度梯度会影响熔渣腐蚀现象的程度。当温度梯度很大时,熔渣的渗透很少,腐蚀反应主要局限于熔渣和耐火材料的直接界面。在这种情况下,熔渣在熔渣-耐火材料界面的流动性可能受到限制,反应产物从熔渣-耐火材料界面运走的速度可能很慢。而当耐火材料较厚时,由于温度梯度相对较小,熔渣可以深入到耐火材料内部。这种情况下,耐火材料会经历不同的腐蚀阶段。在传统的耐火材料设计中,耐火材料的厚度至少为一块砖(0.225 mm),而且还有一层背衬,总厚度至少为450 mm。熔渣固化面可位于热面后40~75 mm的区域内。在某些情况下,熔渣可渗透至热面后150 mm处。
薄壁耐火衬的腐蚀情况如图2所示。这里,耐火材料与熔渣的反应主要发生在热面,熔渣几乎没有渗透到耐火材料内部。显微镜检查通常显示,熔渣只渗透到热面后方不到0.1 mm的深度。这种情况可以称为“第一阶段”的熔渣侵蚀,即反应仅限于热面附近。
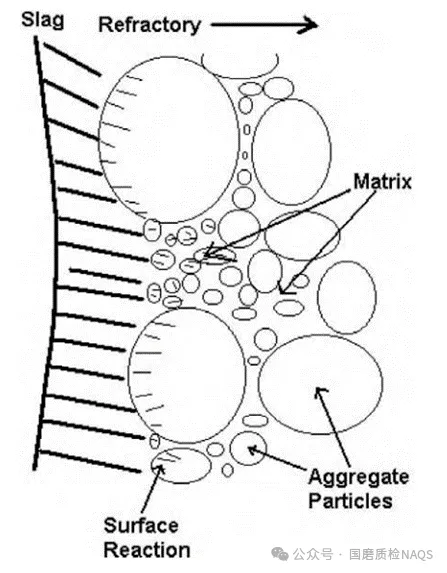
图2 熔渣侵蚀的第一阶段(结合耐火材料)
影响这种反应速度的主要因素是热面温度。如果热面温度低于耐火材料和熔渣反应产物的最低熔点,那么反应就会非常缓慢或者不发生。大多数专家认为,如果热面温度高于最低熔点208 ℃,就会出现较快的腐蚀速度。在一些应用中,比如公用事业锅炉,可以通过“按钮熔化试验”来确定熔渣的熔化温度。更准确的方法是通过热分析来确定耐火材料和熔渣之间的最低共晶温度或固相线温度。固相线温度是指在加热过程中出现内吸热反应(即熔化)的温度。耐火材料和熔渣之间的反应温度可以通过对粉碎的耐火材料和粉碎的熔渣混合物进行热分析测试来确定。薄壁耐火衬设计很少出现比“第一阶段”更严重的腐蚀现象。因此,影响腐蚀的主要工艺变量是热面温度,次要工艺变量包括熔渣撞击速度和化学成分。在化学成分方面,耐火材料在一定程度上会溶解在熔渣中。如果耐火材料和熔渣之间达到了化学平衡,那么腐蚀就会减少。所谓化学平衡,就是指熔渣中已经溶解了足够多的耐火材料成分,达到了溶解度极限。通常情况下,耐火材料和熔渣之间没有达到化学平衡,也就是说,熔渣对耐火材料有腐蚀作用。
有些厚壁设计中,耐火材料对熔渣有很强的抵抗力,所以反应也仅限于热面区域。这些耐火材料通常是用于长期保持高温的冶金或玻璃窑中的电熔型耐火材料。
在高温条件下,厚壁耐火衬开始在初始熔渣涂层处发生腐蚀。最初的腐蚀过程是第一阶段(图2)。由于温度梯度较大,熔渣会渗透到耐火材料内部。耐火材料中最细小的孔隙(直径小于10微米)会通过毛细管作用将液态熔渣吸入热面后方。随着时间的推移,耐火材料会发生大面积腐蚀,进入第二阶段(图3)。
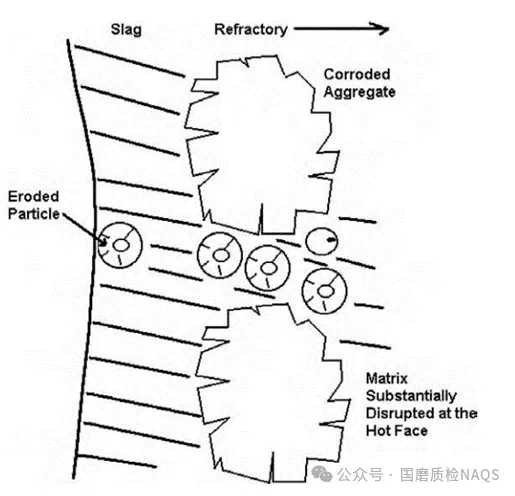
第二阶段的特点是:(1)耐火材料被熔渣完全渗透;(2)热面区域因腐蚀而严重破坏。只有当温度梯度足够宽,才能发生熔渣的渗透,第二阶段才会在第一阶段之后出现。
在第二阶段,粘结型耐火材料中的粗骨料会沿着晶界被熔渣渗透(晶界是构成多晶骨料颗粒的晶体之间的边界)。基质和骨料颗粒之间的直接结合被破坏,但仍然存在。
第二阶段的熔渣渗透可能导致致密化剥落。这种剥落是因为熔渣渗透区域和未渗透冷面区域的热膨胀系数不同。在持续的热循环(冷却和加热)中,剥落可能发生在渗透区域和未渗透区域的分界线上。剥落后的残余内衬重新开始腐蚀过程,从第一阶段再次进入第二阶段。
在耐火衬寿命即将结束时,或者在腐蚀速度相对较慢且没有发生致密化剥落的情况下,耐火材料热面区可能进入最后一个腐蚀阶段,即第三阶段(图4)。在这种情况下,热面区域以及其后方2~4 mm处的结合力极弱。看起来是炉渣将残留的骨料颗粒固定在一起。这可能是由于耐火材料溶解在熔渣中,使得热面区域的熔渣粘度增加。
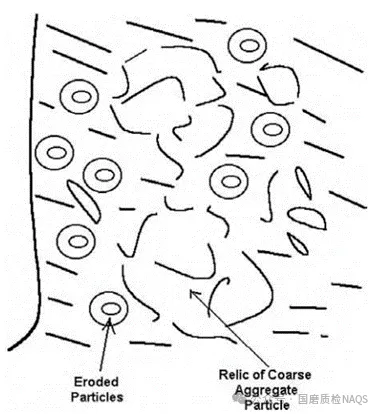
由于炉渣粘度的影响,在厚壁设计中,第二阶段和第三阶段的热面区域保持一定的连贯性。因此,影响腐蚀速率的一个关键工艺变量是热面温度。许多专家建议,热面温度不应超过耐火材料和熔渣之间固相线温度以上20 ℃。但是,在许多厚壁耐火材料设计中,这种温度限制是不切实际的。相图是一种图表,用于表示不同成分和温度下存在的平衡相,反映了特定化学体系中的熔化关系。即使不完全了解相图,也可以利用“简化方法”来分析腐蚀。这种方法可以提供系统腐蚀电位的“初步估计”。
下面将以Na2O–Al2O3–SiO2体系(图5)为例,说明这种方法的原理和步骤。Al2O3–SiO2砖接触Na2O时可能出现的两种后果,即“上釉”(形成熔融相而导致的腐蚀)和膨胀。本节只讨论耐火材料在腐蚀过程中形成液相的情况。
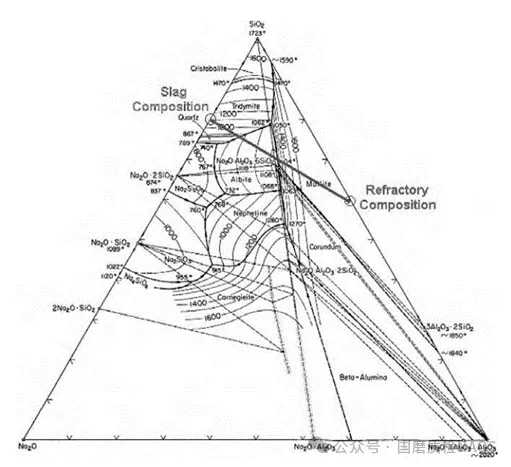
图5 腐蚀实例中使用的Na2O-Al2O3-SiO2相图第一步是在相图上找到代表耐火材料主要成分的点。本例中,我们使用一种含有40% Al2O3的超级砖,与一种含有20% Na2O和80% SiO2的炉渣接触。图5中用圆圈标出了这两种成分,其中一个圆圈表示炉渣的大致成分,另一个圆圈表示砖的大致成分(位于Al2O3–SiO2组分线或“连接线”上)。第二步是在炉渣成分和砖的成分之间画一条直线(如图5所示)。这条直线表示耐火材料和炉渣之间可能发生的反应方向。必须认识到,在平衡状态下,耐火材料和炉渣之间所有可能形成的反应产物都必须位于图5中连接耐火材料和炉渣成分的直线上。(1) 在渣-耐火材料界面处,组分必须从耐火材料向炉渣方向移动,即局部组分向“西北”方向移动。(2) 在平衡状态下,耐火材料和炉渣之间可能形成的反应产物是“白云石”,即Na2O·Al2O3·6SiO2,其熔点为1104 ℃。因此,在平衡状态下,耐火材料表面处反应产物的局部熔点为1104 ℃。注意,白云石位于SiO2、莫来石(3Al2O3·2SiO2)和白云石之间的“相容性三角形”内。相容性三角形确定了平衡时可能存在的相。莫来石和SiO2(作为玻璃相或玻化相)是耐火材料固有的相。白云石是由于耐火材料和炉渣之间的反应而形成的。(3) 连接耐火材料和炉渣成分的直线穿过低至约1000 ℃的温度。这意味着,在非平衡条件下,可能在这样低的温度下形成液相。在腐蚀过程的第一阶段,预计会出现这种非平衡液相。只有在腐蚀过程的第二阶段,炉渣中才会溶解足够的耐火材料,从而观察到平衡反应产物。(4) 连接耐火材料和炉渣成分的直线穿过Na2O·2SiO2–SiO2–Na2O·Al2O3·6SiO2相容性三角形靠近三元(3组分)共晶或最低熔点740 ℃处。这意味着,在非平衡条件下,可能形成熔点低至740 ℃的液相。在进行这种分析时,需要考虑一些限制和注意事项。一是耐火材料中除了Al2O3和SiO2外还含有其他成分,如K2O和Fe2O3等熔剂。这些成分会影响耐火材料和炉渣之间的反应方程式和平衡相图,从而降低预测的熔点。另外,炉渣中也可能含有其他成分,改变熔化关系。因此,这种方法只能提供一个初步的估计,不能作为最终的判断依据。
Konig在1971年提出了一个模型,将耐火材料在高炉墙壁区域的腐蚀速率与墙壁中的温度梯度相关联。这种分析包括一个假设,即温度梯度控制了渣-耐火材料接触面的温度。由于高炉壳体在炉缸区域内是水冷却的,因此Konig的分析适用于具有陡峭温度梯度的薄壁耐火材料。
Konig通过假设进入耐火材料表面的热流量必须等于通过炉壳的热流量来建立热平衡。如果进入耐火材料表面的热流量超过了通过炉壳的热流量,那么接触面温度必须增加,导致腐蚀速率增加,直到再次维持热平衡。
在尝试将Konig的分析应用于高炉时,Herron和Beechan发现,如果耐火材料的导热系数随着温度的升高而发生显著变化,则需要进行修正。该模型被发现能够描述旋风燃烧器和锅炉应用中耐火材料的行为,其中初始墙壁厚度的耐火材料约为25 mm。
在1939年,Endell、Fehling和Kley开发了一个经验关系式,用于描述厚壁耐火材料衬里容器中渣沿垂直耐火材料墙流动时的腐蚀情况。尽管这项工作是在1939年完成的,但它仍然是关于渣腐蚀的经典参考文献,尽管它具有经验性质。在腐蚀研究中,作者使用了一种安排,其中固体燃料在反应室内燃烧(释放热量),产生的灰分(渣)冲击墙壁。耐火材料腐蚀速率对热面温度有很强的依赖性。事实上,温度是在炉子设计或过程控制中可以考虑的最重要的过程变量。渣腐蚀速率随着耐火材料在渣中的溶解度线性增加。本质上,腐蚀速率与渣粘度成反比。这可能就是为什么耐火材料在第三阶段攻击时仍然表现出一些连贯性,因为耐火材料溶解于渣增加了渣-耐火材料接触面处的粘度。
铁铸造用炉渣主要含有CaO、SiO2、FeO等氧化物。作为初步分析,可以将炉渣视为Al2O3和SiO2的二元混合物,因为它们通常是炉渣的主要组分。耐火砖的主要组分可以用Al2O3-SiO2二元相图来表示,这样就可以利用CaO-Al2O3-SiO2三元相图来分析腐蚀情况(图6)。
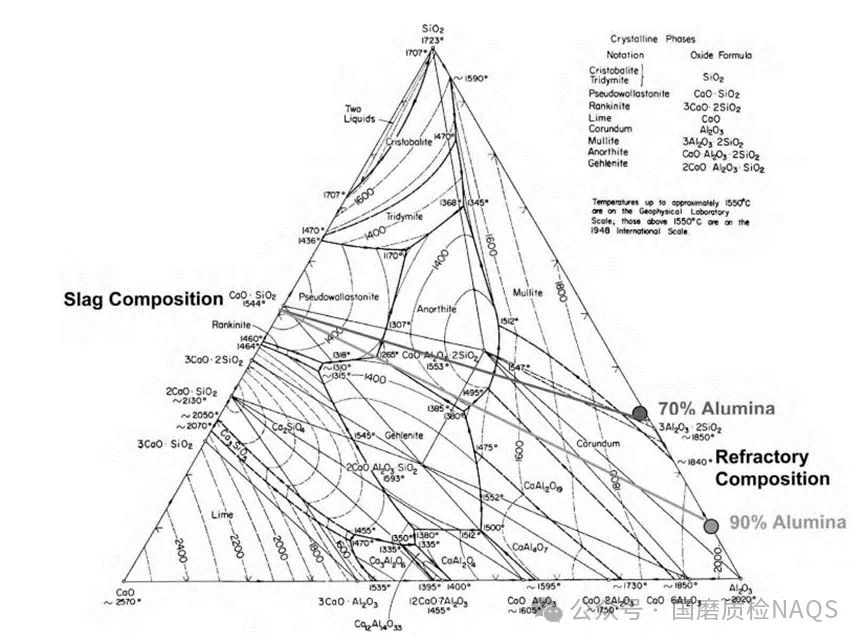
图6 氧化铝硅砖在铸造/炼钢炉渣中的腐蚀表示法
利用图6分析70% Al2O3和90% Al2O3耐火砖的腐蚀情况时,先在图中Al2O3-SiO2二元(双组分)一侧绘制耐火砖的成分点。然后,根据炉渣的平均CaO/SiO2比,从耐火砖的成分点画一条直线连接到预期的炉渣成分点。假定炉渣的CaO/SiO2比为1.0。观察图6中耐火砖成分点和炉渣成分点之间的连接线,可以发现以下几点:
(1) 两条连接线都非常靠近1265 ℃的三元共晶点,这意味着当炉渣和耐火材料接触并达到这个温度时,会产生液相,即发生腐蚀。其他助熔氧化物通常会使这个温度降低约50 ℃。
(2) 富含CaO的相渗入耐火砖后,会使耐火材料中的莫来石“粘结剂”成为非平衡相,即莫来石溶解到渗入的炉渣相和腐蚀产物中。在70%Al2O3耐火砖中,当局部CaO含量达到约20%时,莫来石就会消失;而在90%Al2O3耐火砖中,当局部CaO含量达到约8%时,莫来石就会消失。
相图提供了一个初步的判断标准,即当液相作为腐蚀反应产物出现时,即为腐蚀开始时的反应温度。这类似于Konig分析中的临界温度或Endell、Fehling和Kley分析中的“基准”温度。如果将图6中耐火材料成分点和炉渣成分点之间的连接线改为分析更高碱度的炉渣,即CaO/SiO2为1.5或2.0,那么这些连接线将在1380 ℃附近与三元共晶相交。这种由阳起石和海泡石组成的共晶混合物被称为“美利来石”。
图7显示了阳起石和海泡石之间的二元连接,在图中更容易看到固相线,即超过这个温度就会开始腐蚀。因此,CaO-SiO2比越高,液相形成和腐蚀开始的初始反应温度就越高。
图7 阳起石(2CaO·Al2O3·SiO2)和海泡石(CaO·Al2O3·2SiO2)两种钙铝硅酸盐在不同温度和成分下的相平衡关系
为了找出电弧炉顶部使用的70%氧化铝砖过早失效的原因,对砖的显微结构进行了分析。从图8可以看出,使用后的砖厚度明显减少。而在顶部其他区域选取的砖,残余厚度较大。从本次炉次使用的大多数砖的锯切表面上发现了裂纹,且裂纹大致平行于热面。
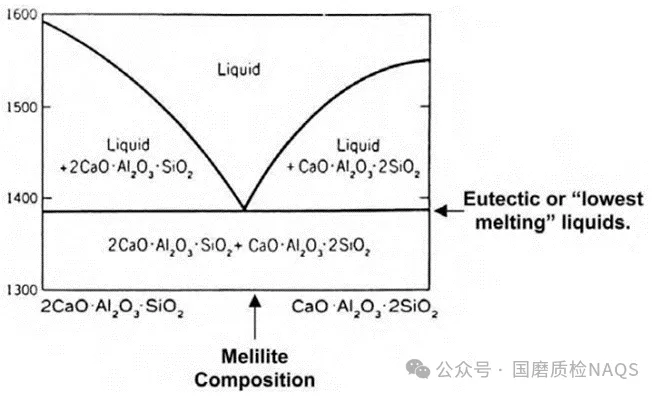
将砖切片并制作抛光切片,在光学显微镜下进行反射光观察。在最靠近热面的区域,即渣-砖界面处有大量的腐蚀反应迹象(图9)。认识到砖中的“本征”相是铝土矿、粘土(碎料)和莫来石,可以看出在最靠近热面的区域没有莫来石。图9中热面处的相包括铁铝尖晶石或FeAl2O4(标记为“S”)、六铝酸钙或CaO·6Al2O3(浅灰色针状晶体)、从冷却过程中析出的条形刚玉晶体、残留铝土矿颗粒中的刚玉晶体(右下角区域)和深灰色背景的钙铝硅酸盐玻璃。
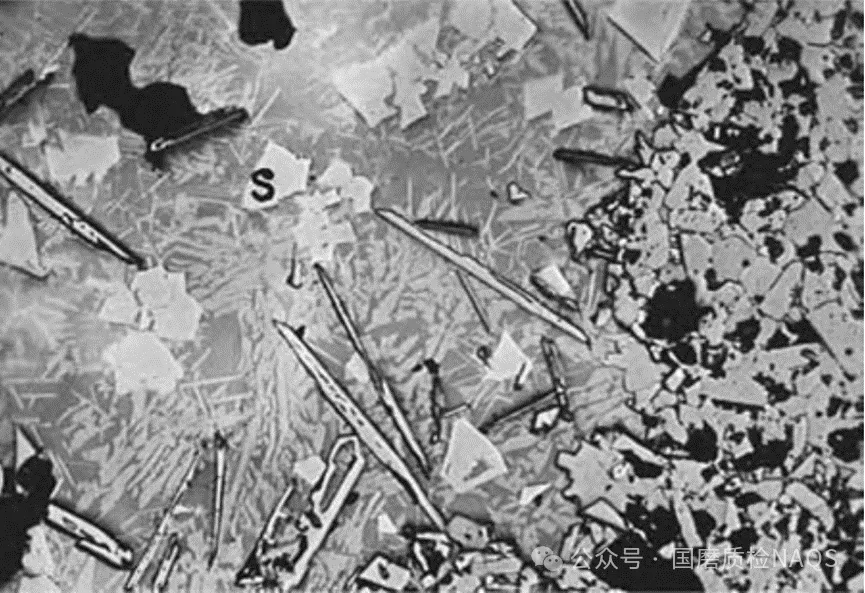
在距离热面约2~4 mm的位置,渣通过砖的孔隙结构渗透,并且由于其极端的晶体生长,很容易发现莫来石晶体出现的位置(图10)。莫来石晶体呈现为大型、浅灰色条形晶体,在被残留铝土矿颗粒包围的孔隙壁处。小型六铝酸钙晶体位于莫来石晶体之间的玻璃相中。
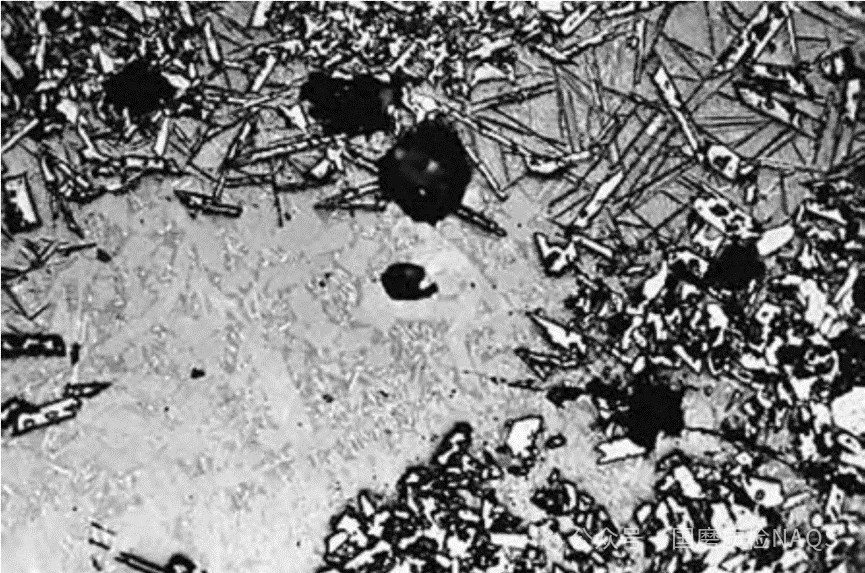
莫来石的出现表明渗透相中钙氧化物含量低于约20%。这是由于渣对砖的腐蚀和远离热面时渣量减少导致的“稀释”效应。在距离热面约10 mm处,渣渗透停止。在靠近冷面的区域,用焙烧铝土矿和粘土混合制成的70%氧化铝耐火材料具有正常的显微结构。通过这项分析得出结论:发生了正常预期的腐蚀反应,并且加速损耗可能是由于较差的抗震性能导致增强剥落,最终缩短了电弧炉顶部使用寿命。(1) 渣覆盖在耐火材料表面,并且当表面温度超过约1265~1380 ℃时,腐蚀开始。反应可以表达为:钙(铁)铝硅酸盐渣与70%氧化铝耐火材料反应,形成阳起石-海泡石玻璃,并将莫来石和铝土矿溶解到渣中。
(2) 渣渗透到耐火材料中,填充孔隙并溶解粘结相(莫来石),直到渣中的钙氧化物含量降低到约20%以下。在这个区域后面,莫来石重新出现,并且随着距离热面的增加,晶体生长程度逐渐降低,直到达到渣在砖中的冻结面。
-
在另一个涉及不同铸造厂的案例研究中,对一块90%Al2O3砖进行了检查,以确定其在黑色铸造炉炉底/下侧壁应用中使用后的腐蚀情况。过早失效的是炉底处支撑下侧壁的一块“斜背”砖。图11是一块使用后的砖的照片。由于该砖磨损严重,怀疑是腐蚀导致了故障。
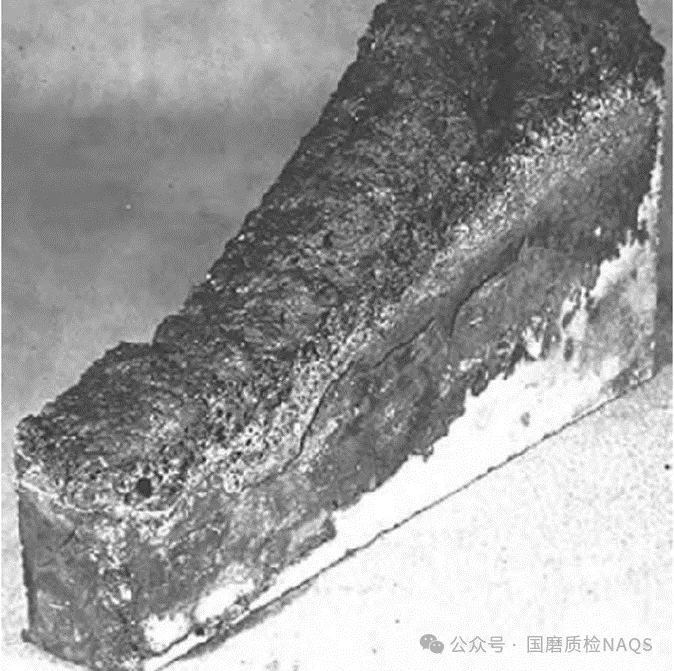
图11 铁铸造后的90%Al2O3砖
90%Al2O3砖是用熔融氧化铝骨料和莫来石、玻璃基质制成的。钙铁铝硅酸盐渣溶解了耐火材料表面的所有莫来石,并显示出熔融氧化铝骨料颗粒溶解的迹象(图12)。除刚玉(来自标有“A”的熔融氧化铝)以外的相包括铁铝尖晶石(标有“H”)、六铝酸钙(浅灰色针状晶体)和条形刚玉晶体(从冷却过程中析出)。熔融氧化铝骨料似乎溶解在渣中,并在骨料外围形成铁铝尖晶石(铁铝尖晶石)。深灰色背景是钙铝硅酸盐玻璃。
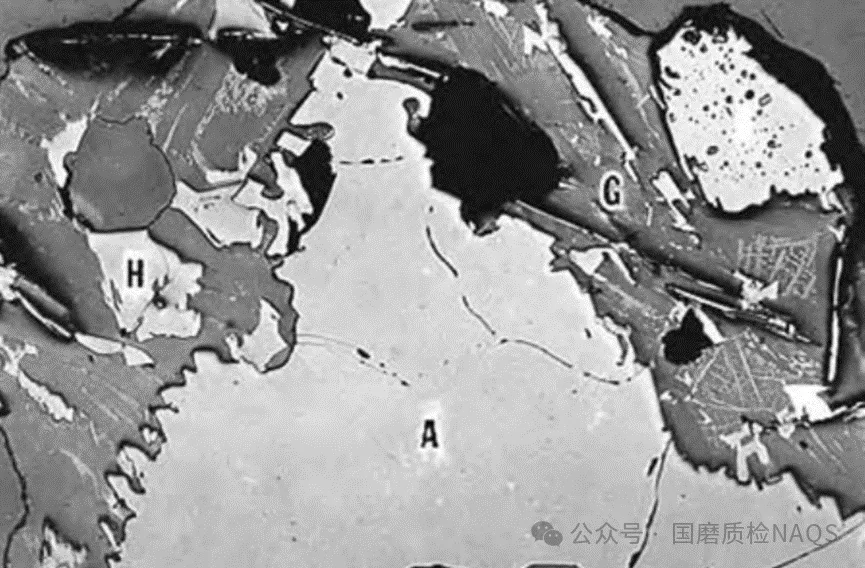
渣液体渗入耐火材料的深度为表面后10~20 mm。在表面后约8~10 mm处,显微结构中出现了莫来石,表明渗入渣中的CaO含量降至约8%以下(图13)。在该显微镜图像的上部区域,玻璃或渣(标有“G”)渗透到熔融氧化铝骨料颗粒(标有“A”)之间。六铝酸钙针状晶体分散在玻璃相中。在下部区域,莫来石(标有“M”)呈现为分散在玻璃相中的单个晶体团,由于渣的渗透,玻璃相的化学性质发生了一些改变。
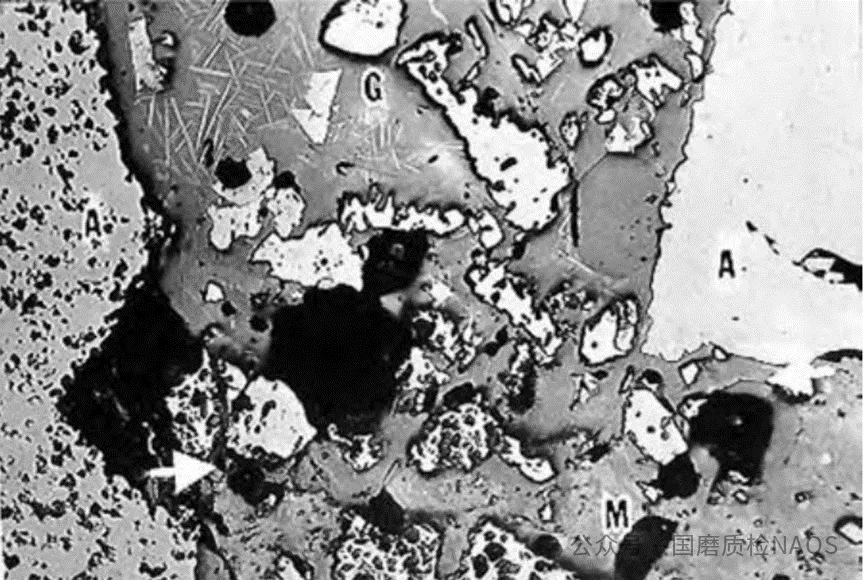
在这种情况下,可以确定腐蚀反应是黑色铸造厂通常会发生的反应,即耐火材料结合相发生化学溶解,并向表面后方渗透。在使用过的耐火材料中发现了大量凝固金属“脉络”,这表明在使用过程中出现了机械损伤,随后出现了金属渗透。
在生产碳钢的碱性氧气炉中,对一块90%氧化镁级烧成的沥青浸渍砖进行了短期试验。炉渣成分可以看作是含有大量氧化铁的高CaO/SiO2比液体。由于砖中的主要成分是氧化镁,因此可以使用CaO-MgO-SiO2三元系来近似地观察腐蚀过程(图14)。
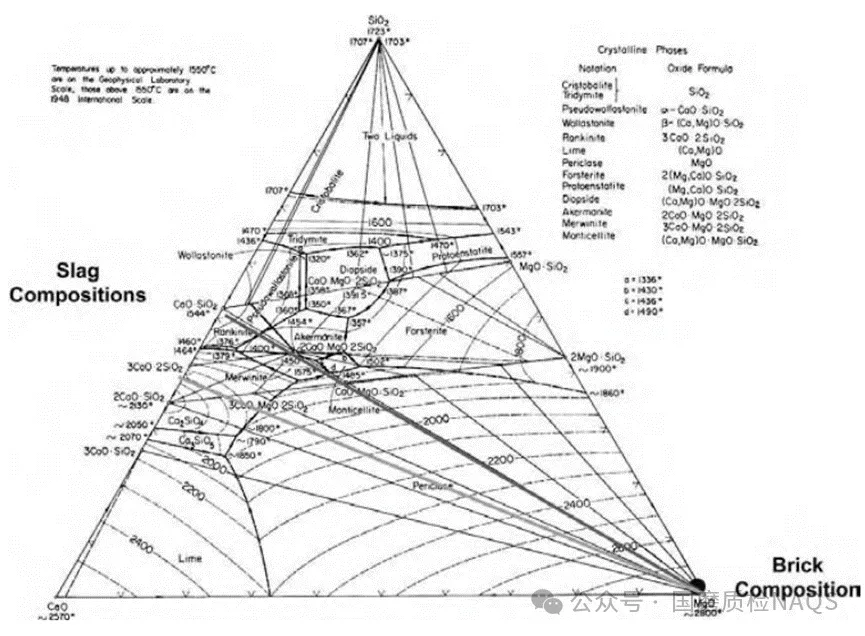
图14 CaO-MgO-SiO2相图以及砖(MgO)和熔渣(CaO-SiO2连接处)的界面分析在90%氧化镁级耐火砖中,氧化镁含量为95.5%,氧化钙含量为2.7%,二氧化硅含量为1.4%。这意味着耐火砖中的“本征”硅酸盐是硅酸二钙(2CaO·SiO2)——一种非常耐火的第二相,在以直接烧结键合为主的产品中,它提供了部分粘结力。在使用过程中,当硅在金属浴中被氧化时,存在一个暂时阶段,耐火材料表面暴露于较低碱度的硅酸盐。这也是氧化铁与耐火材料接触强度增加的阶段。由于耐火材料的成分可以用相图(图14)上的“MgO”顶点来表示,因此可以画出不同的CaO/SiO2比率连接线来说明腐蚀过程:(1) 当CaO/SiO2比率为1.0时,耐火材料将与熔渣发生反应,形成钙镁硅酸盐(CaO·MgO·SiO2),其熔点为1485 ℃。一种含铁的钙镁硅酸盐(FeO·MgO·SiO2)的熔点为1230 ℃。因此,当液相在1230 ℃以上形成时,腐蚀就开始了。熔渣的渗入会导致耐火材料表面的粘结相被溶解,并向表面后方渗透。在紧邻表面区域,粘结硅酸盐相的效果降低。(2) 当CaO/SiO2比率为1.5时,在表面形成的反应产物是梅花石(3CaO·MgO·2SiO2)。梅花石在1575 ℃时“不协调地”熔化。有趣的是,随着炉渣碱度的增加(即随着CaO/SiO2比率的增加),腐蚀反应开始的温度越高。这也是炼钢厂希望在精炼循环中尽早溶解石灰石炉渣以延缓炉渣腐蚀的原因之一。(3) 当CaO/SiO2比率为2.0时,最低共晶温度约为1790 ℃。如果不考虑渣中氧化铁和其他成分的影响,这意味着渣和砖之间的反应产物高于大多数炼钢温度。然而,氧化铁起着重要的作用,它大大降低了反应产物的温度。
氧化铁是炼钢渣中的主要成分之一,它会降低炼钢渣的熔化温度,增加炼钢渣的流动性和侵蚀性。表1列出了碱性制冷剂和炼钢渣之间可能发生的一些反应。
表1 炼钢渣与碱性耐火材料的反应产物,熔点为完全熔化或部分熔化(包晶反应)
从表1可以看出,含铁相在1200~1350 ℃范围内就会熔化,而含硅相则需要1485 ℃以上才能熔化。此外,由于多组分共晶和杂质的存在,实际上炼钢渣的熔化温度会比三组分图所示的更低。
钙铁硅酸盐炼钢渣和含镁耐火材料之间的腐蚀过程取决于炼钢渣的流动性和浓度。
图15是炼钢炉上部壁位置的一块耐火材料中炼钢渣与耐火材料界面区域的显微结构。这里的反应产物是混合尖晶石相(MgO,FeO)·(Al2O3,Fe2O3)、硅酸二钙(2CaO·SiO2)和铁氧体二钙(2CaO·Fe2O3)。由于炉气中氧化铁粉尘浓度较高,且缺乏持续的炼钢渣侵蚀(或流动),混合尖晶石相在耐火材料表面形成了一种“屏障层”。
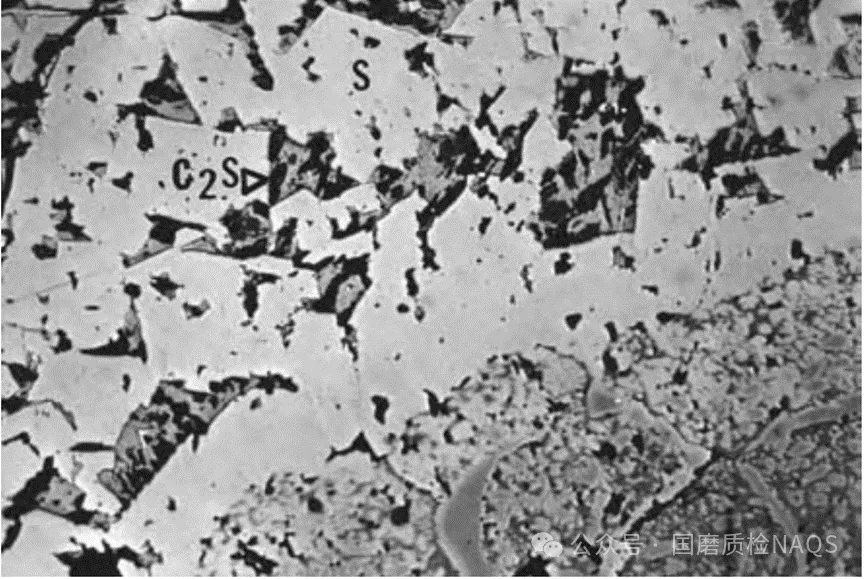
相比之下,渣线位置的耐火材料则表现出不同的腐蚀过程(图16)。在这里,腐蚀产物似乎是铁氧体二钙(2CaO·Fe2O3)渗透到单个氧化镁晶体(圆形灰色晶体)周围,而在炼钢渣层中存在孤立的黑色硅酸二钙(2CaO·SiO2)。氧化镁晶体似乎是在极高的温度和炼钢渣接触强度下从耐火材料表面被侵蚀出来的。
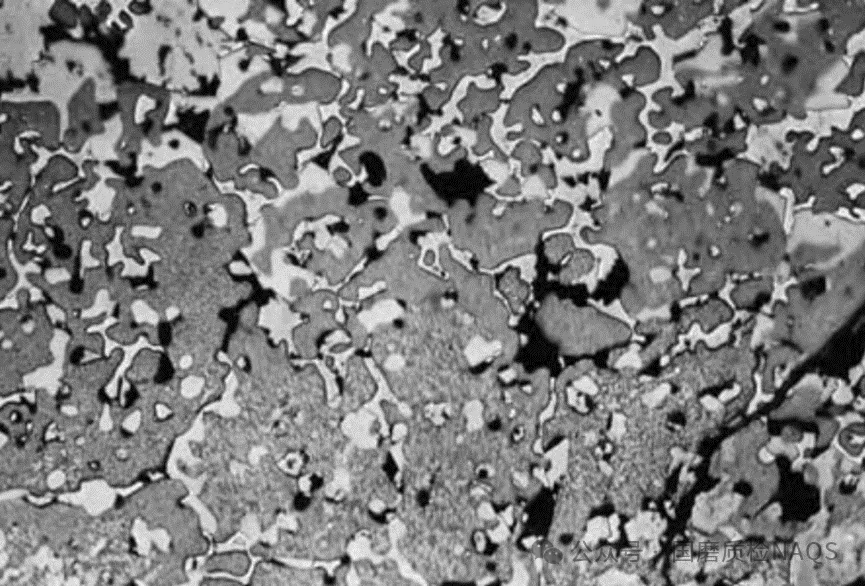
在这些情况下,尽管耐火材料在同一炉中,但反应界面的微观结构却极为不同。在上部壁位置,氧化铁和含石灰粉尘的反应促进了耐火材料腐蚀过程。相比之下,在渣线位置,与流动熔渣的持续接触导致了耐火材料腐蚀和侵蚀过程的发生。
90%氧化镁烧成浸渍砖在碱性
氧气炼钢炉中的使用情况
图17是碱性氧气炼钢炉中使用过的一块底塞砖。底塞砖是用来控制向熔融金属浴中注入氧气的装置,氧气和金属之间的放热反应会产生局部高温。可以看到,这块砖的热面有一层明显的剥落。
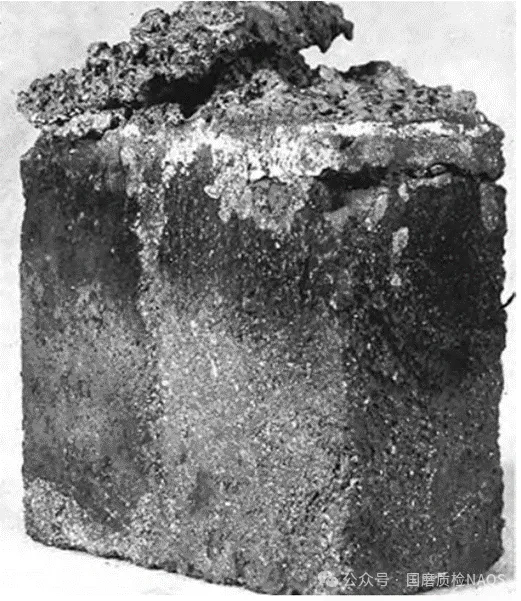
图17 90%氧化镁烧成的浸渍砖在BOF底塞中使用后的效果
图18是这块砖的热面区域的显微结构。显微照片的上部区域是炉渣与耐火材料的直接界面。渗透到单个氧化镁晶体中的渣相是铁素体钙,它在耐火材料的外部区域形成了一层致密层。在致密层后面,有一个黑色区域,这是耐火材料中浸渍碳相被氧化去除后形成的孔隙区。在图18中,可以看到一个大的空隙位于耐火材料的左下方。这个空隙是由于耐火材料配方缺陷造成的。如图17所示,在长期受热的情况下,这个缺陷导致了表面剥落。图19显示了耐火材料腐蚀过程的细节。在这里,铁素体钙(亮相)和硅酸钙钙渗透到聚集颗粒中单个氧化镁晶体周围。几个较小的圆形氧化镁晶体处于溶解的最后阶段。尽管硅酸二钙是与氧化镁相容的相,但它仍会溶解氧化镁–这一点从显微照片中可以看出。
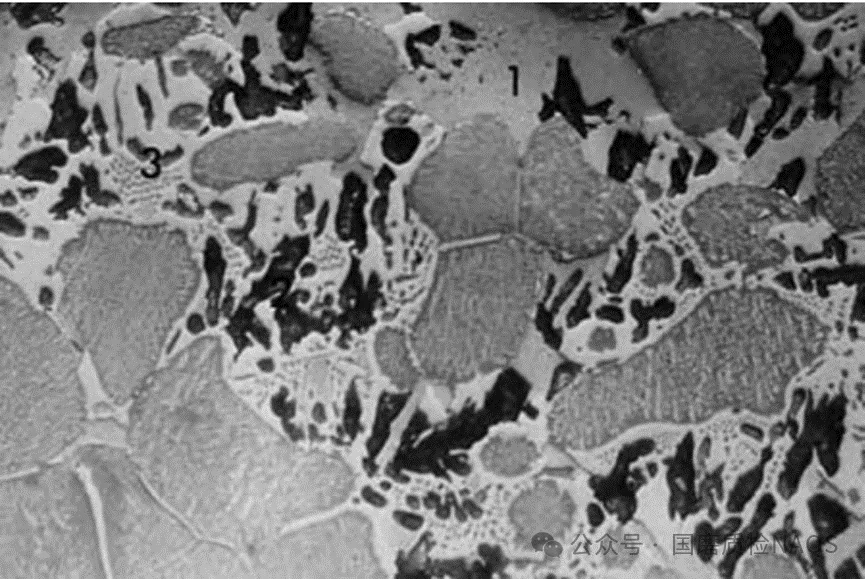
因此,腐蚀过程可以用以下反应表示:MgO+2CaO·SiO2→3CaO·MgO·2SiO2。
在耐火材料表面后面,可以看到一个由细粒(和碳)组成的基质从骨料颗粒中收缩的区域(图20)。这就在耐火材料中形成了空隙,这些空隙最终连成一片,形成了图19中较大的空隙。这些空隙导致耐火材料层在使用过程中剥落(薄层剥落),造成过度磨损。当面对这些证据时,耐火材料的开发人员对这种分离现象感到惊讶,因为他们在实验室的焦化箱实验中从未见过这种现象。最终,人们认为1000 ℃的焦化箱温度与耐火材料的使用温度(1600 ℃)相差甚远。
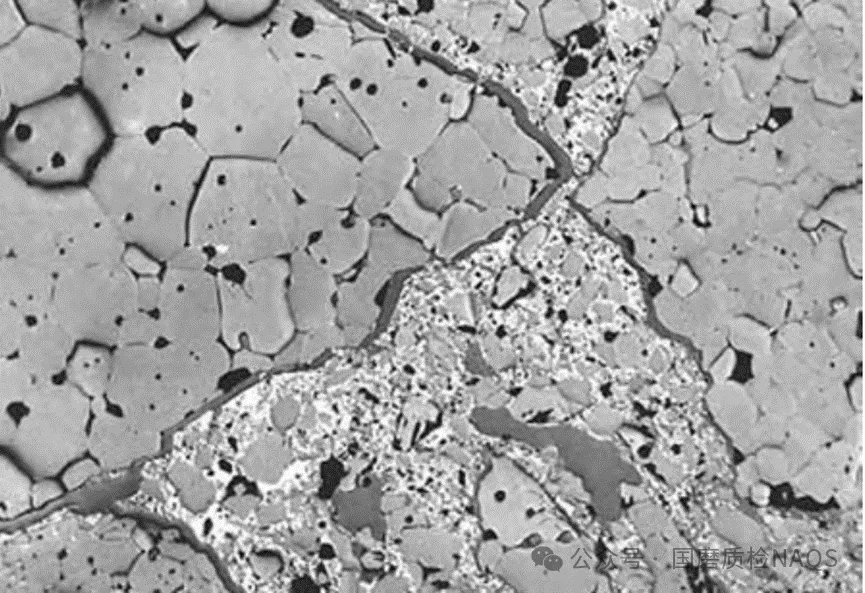
在其他案例研究中,对镁铬耐火材料和白云石耐火材料在氩氧脱碳反应器(AOD)中生产不锈钢后的使用情况进行了检测。在这种情况下,在典型的精炼周期内收集炉渣试样,并在使用活动结束后对耐火材料进行检查。AOD精炼周期略高于一小时,其中包括一个初始阶段(脱碳周期),硅在金属中被氧化,产生非常粘稠或块状的炉渣。这种早期炉渣的显微照片显示,尖晶石相或(MgO,FeO)·(Cr2O3·Al2O3·Fe2O3)团和明亮的金属液滴相互分散在硅酸钙玻璃中(图21)。
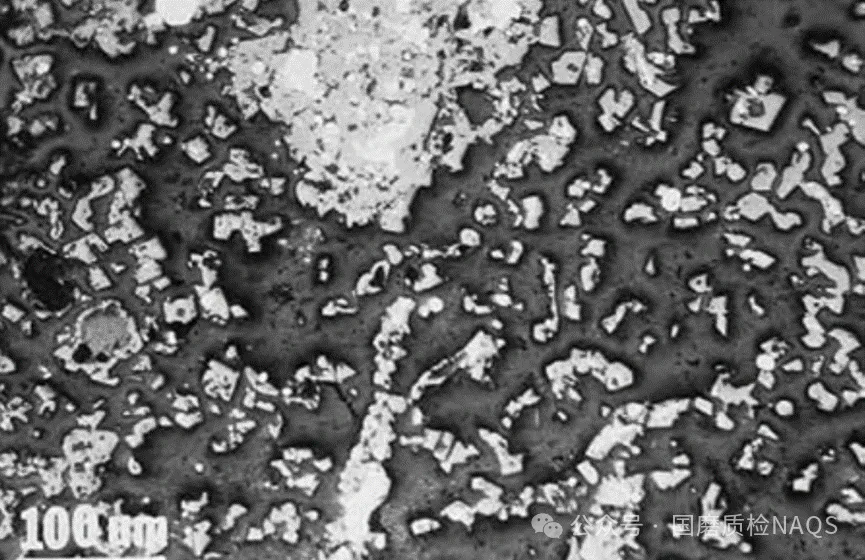
图22显示了高放大倍率下的角状尖晶石晶体和金属液滴。炉渣的块状性质是由于高浓度尖晶石晶体造成的高粘度所致。
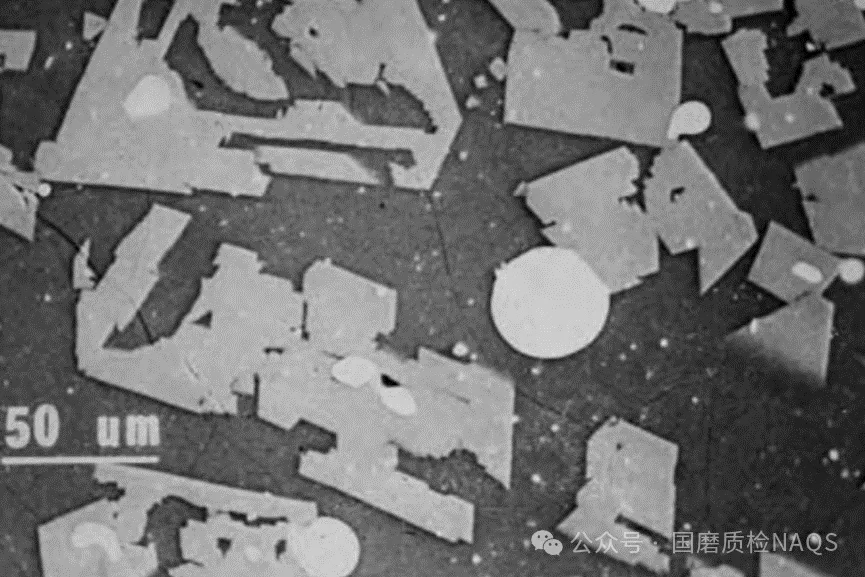
早期的AOD熔渣还含有氧化镁晶体的侵蚀块。在图21的左下方区域和使用扫描电子显微镜拍摄的照片(图23)中可以看到这样的碎片。在后一张照片中,硅酸钙玻璃连续体中的尖晶石晶体围绕着照片中心的深灰色氧化镁块。
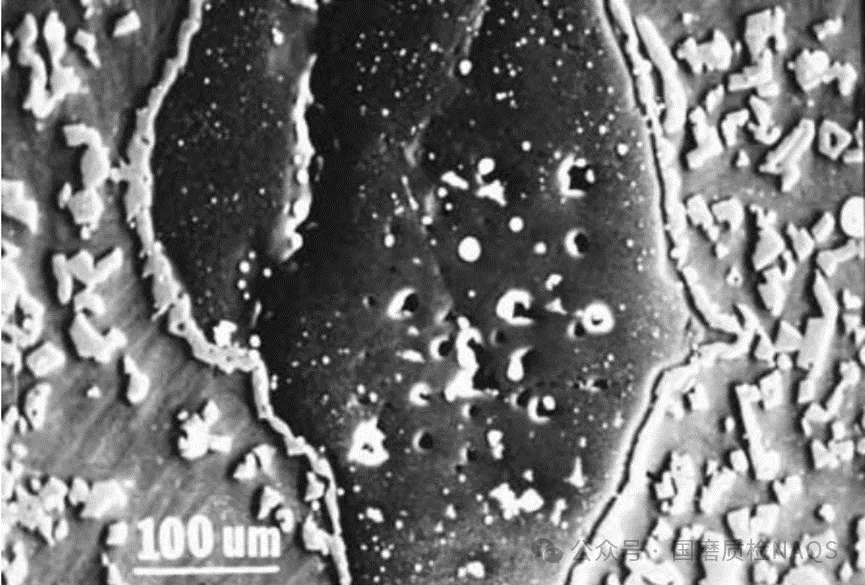
AOD精炼周期还包括一个短暂的还原期,在这段时间内向金属中注入氩气以从熔渣中回收铬。实际上,尖晶石相被大幅减少。此循环还采用增加渣中CaO/SiO2的比例来促进铬的回收。还原渣的显微照片如图24所示。只有少量尖晶石晶体从玻璃中突出,表明还原效率很高。在抛光过程中,炉渣显示出水蚀痕迹,这与镁硅钙石和/或钙铝黄长石的溶解度一致(见表1)。
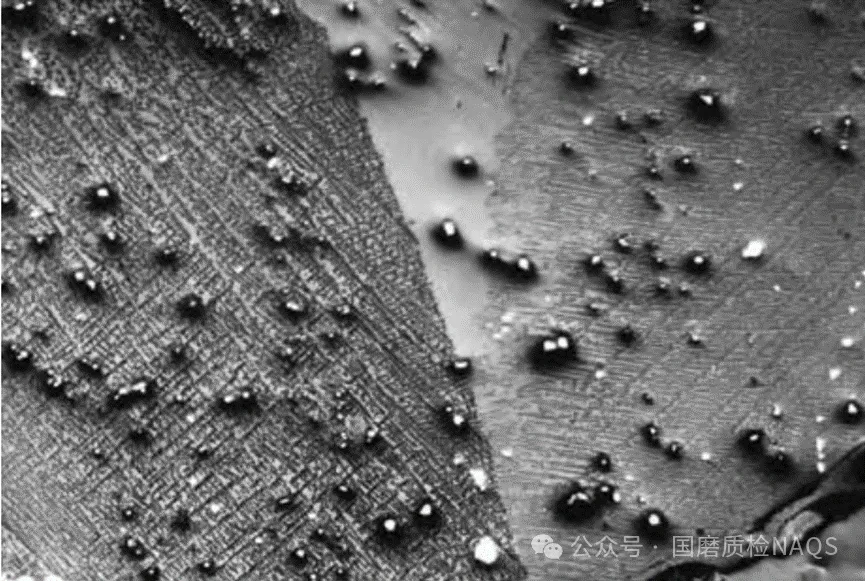
镁铬耐火材料曾经用于早期的AOD衬里。尽管最近的趋势是在这些反应器中使用镁碳耐火材料,但对镁铬耐火材料的检查说明了腐蚀过程的几个原则。图25是50吨AOD反应器中桶位置的一块耐火材料。
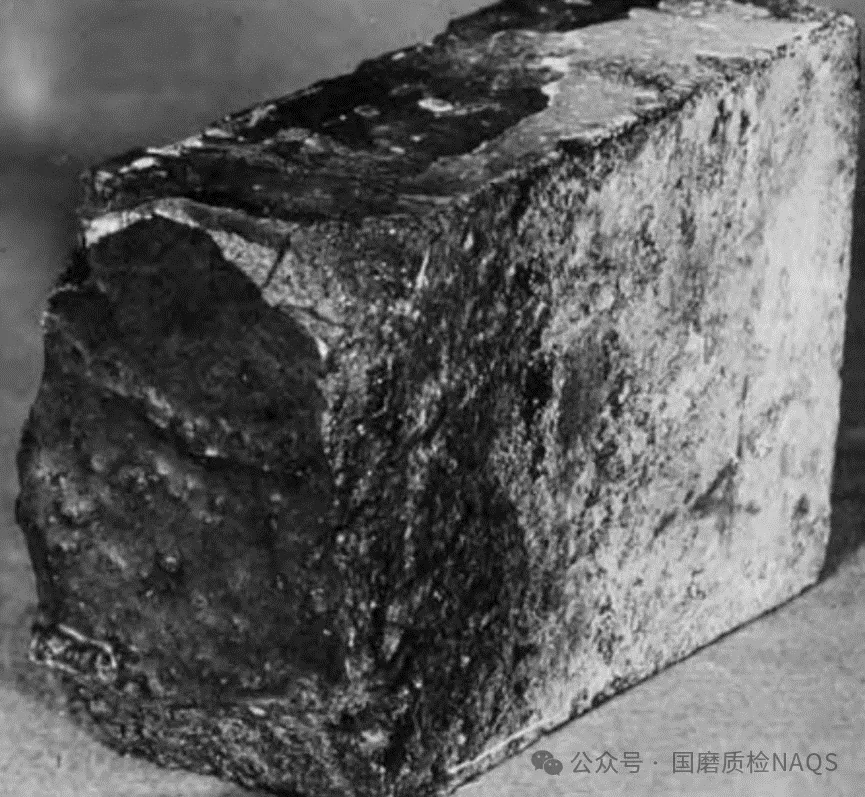
图26显示了镁铬耐火材料的热面区域。铬铁矿颗粒(标有 “Cr”)位于显微照片图的中心,粗菱镁矿骨料颗粒位于该区域的左侧。渣层位于显微照片的顶部。从耐火材料表面的锯齿形可以明显看出,腐蚀过程优先清除了耐火材料的基质,使粗颗粒突出到渣层中。在这种低倍放大镜下,还可以看到铬铁矿颗粒外围似乎被腐蚀了。
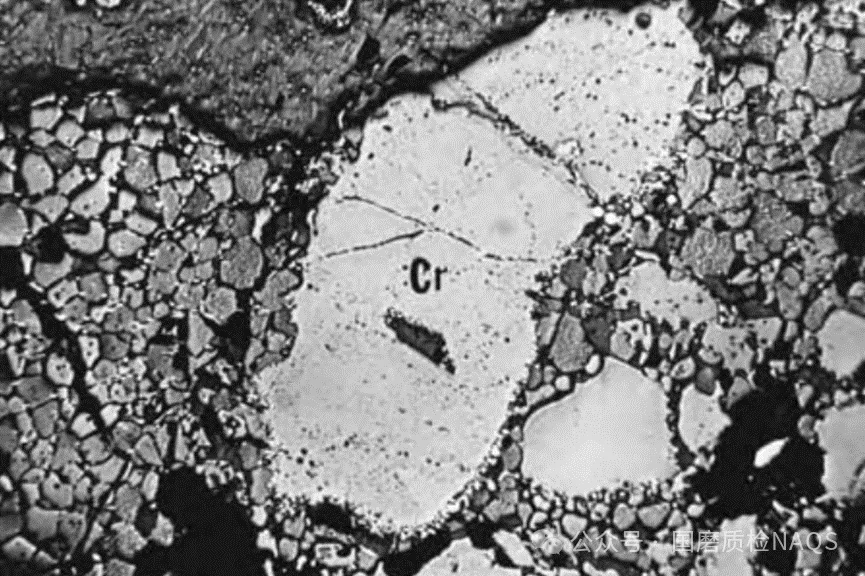
图27显示了耐火材料热面区域的详细视图(渣层位于视场顶部)。在这里,梅花石或3CaO·MgO·2SiO2(标有 “m”)和钙镁橄榄石或CaO·MgO·SiO2是炉渣硅酸盐。在CaO/SiO2范围为1.0~1.5的炉渣中,这两种硅酸盐与含MgO的耐火材料接触时预计会形成相容相(见图14)。铬铁矿晶粒的腐蚀边缘是次生晶粒,在耐火材料的使用温度下并不存在。这一过程是铬矿石成分(Al2O3、Cr2O3和Fe2O3)在熔渣中溶解,然后在耐火材料最后一次冷却时在铬铁矿晶粒周围优先析出。这些尖晶石并没有在紧邻渣耐火材料界面的铬铁矿晶粒顶部形成,因为在最后一次炼钢加热后进行了快速淬火。图27中还可以看到金属液滴。这些液滴的形成可能部分是由于铬铁矿中的氧化物还原成金属状态。

腐蚀过程可归纳如下:
(1) 熔渣中的氧化镁溶解,熔渣渗入耐火材料内,破坏耐火材料表面后面的直接结合。(2) 铬铁矿在渣相中溶解,氧化物部分化学还原成金属态。
(3) 在镁铬耐火材料和其他粘结耐火材料中,熔渣可渗透到耐火材料表面后75 mm或更深处。虽然严重的化学腐蚀通常仅限于耐火材料表面后25 mm以下的深度,但熔渣的存在会因耐火材料的收缩和其他过程而改变耐火材料的物理性质。如果渗入区的热膨胀系数与冷面区的热膨胀系数不同,则渗入区与未渗入区或冷面区之间的界面附近会出现剥落。使用过的耐火材料可能会在该区域出现裂缝,甚至在裂缝明显连接的地方出现更大的空隙。这种现象被称为致密化剥落,可导致厚度约为75 mm的部分剥落损失。
为了评估炉渣对耐火材料的腐蚀性能,已经开发了多种实验室熔渣试验方法。这些方法可以分为静态试验和动态试验,静态试验是指炉渣与耐火材料接触后保持不动,动态试验是指炉渣在耐火材料表面移动。下面列举了一些常用的试验方法。
这是一种用来评价炉渣对耐火材料腐蚀性能的试验方法。通常是在耐火材料上钻一个直径为50 mm的孔,孔内填充炉渣,并加热到指定的试验温度,保持一定的时间。这种试验只能反映炉渣与耐火材料之间的等温反应和渗透能力。
用来评价炉渣对耐火材料腐蚀性能的试验方法。通常是在耐火材料上滴落炉渣,并测量腐蚀在表面造成的“缺口”深度。该试验在ASTM C768中进行了描述。该试验反映了炉渣和耐火材料之间的等温反应能力。可以使用实际生产中的炉渣或“新鲜”炉渣进行试验。
用来评价炉渣对耐火材料腐蚀性能的试验方法。通常是将25×25×200 mm的耐火棒或棒状试样部分浸入装有熔渣的坩埚中,并在保持试样旋转的同时加热到指定的试验温度。该试验反映了流动熔渣的等温反应能力,但没有考虑“新鲜”熔渣的持续供应。可以使用实际生产中的熔渣或“新鲜”熔渣进行试验。
用来评价炉渣对耐火材料腐蚀性能的试验方法。通常是将斜面耐火材料(通过锯切形成)或整体材料作为小型回转炉的内衬,回转炉不断地向炉内注入炉渣。试验后,对试样进行腐蚀损失和熔渣渗透检查。该试验在ASTM C768中进行了描述。该试验反映了在温度梯度和“新鲜”熔渣的持续供应下的腐蚀情况。可以使用实际生产中的熔渣或“新鲜”熔渣进行试验。