概述 根据工业发达国家统计,每年因钢材腐蚀造成的经济损失约为GDP的2%~4%。目前,全球钢材腐蚀造成的经济损失高达万亿美元。近年来,我国因钢结构腐蚀造成的不安全事故约占桥梁安全事故的25%~30%。因此,学者们在钢结构的腐蚀、检测和防腐技术等方面开展了广泛研究。 桥梁钢结构腐蚀与 腐蚀疲劳损伤机理 钢材的腐蚀类型多种多样,包括均匀腐蚀、点腐蚀、缝隙腐蚀、晶间腐蚀和应力腐蚀等。均匀腐蚀是指钢材表面全面均匀发生的腐蚀现象,导致材料整体逐渐变薄。点腐蚀则在局部区域发生,形成小面积的快速腐蚀,通常在应力集中或保护层缺陷处出现。缝隙腐蚀多发生在金属连接处,如焊缝或紧固件接缝处,由于缝隙中电解质的渗透而形成。晶间腐蚀和应力腐蚀则分别由材料的晶粒边界和外部应力作用引起,它们都可能导致材料的突然断裂。 2.1 桥梁钢构件腐蚀疲劳损伤 图1 Q690D腐蚀样本的S-N曲线:C0无腐蚀,C1,C2,C3腐蚀 Jiang等研究腐蚀效应对正交异型钢桥面板疲劳性能的影响和疲劳裂纹扩展的规律,利用元胞自动机腐蚀模型获取了在不同质量损失率(w)下典型正交异型钢桥面板构件的三维腐蚀形态,并建立了具有毫米级腐蚀坑和裂纹的长跨度桥梁的多尺度有限元模型。结果显示,与通过均匀厚度减小来表征腐蚀效应的方法相比,元胞自动机腐蚀模型获得的极限承载能力更符合实验结果。与未考虑腐蚀效应时相比,当U肋的w分别为6%、8%和10%时,U肋焊脚的裂纹起始处的峰值应力强度因子增加了32%、49%和86%,U肋-隔板的疲劳裂缝寿命分别降低了6.5%、18.9%和50%。根据U肋焊脚处裂纹起始的应变能释放率,裂纹是以张开型裂纹为主,滑开型裂纹和撕开型裂纹为辅的复合裂纹。 罗霞飞等采用自主设计的海水间歇供水循环系统模拟干湿比为1:1的海水干湿交替环境,研究了空气环境、全浸环境、干湿交替环境和应力比0.1、0.3和0.5对高强度钢EH690钢疲劳裂纹扩展的影响。基于试验获得的a-N曲线(a裂纹长度,N为疲劳周期)和da/dN-ΔK曲线(da/dN为裂纹扩展速率,裂纹尖端应力强度因子幅值),发现在裂纹扩展前期,EH690钢在干湿交替环境与全浸环境中的裂纹扩展速率为空气中的三倍左右,呈现出显著的疲劳裂纹扩展加速现象。对于给定的应力强度因子,疲劳裂纹扩展速率随着应力比的增大而增大。研究还拟合得到了不同环境和应力比下标准紧凑拉伸试件的Pairs常数,并通过扫描电镜从微观角度分析EH690高强钢的腐蚀疲劳裂纹扩展机理,为实际海洋平台的腐蚀疲劳寿命评估提供了可靠的试验数据参考。 胡春建等基于潍莱铁路线一座全焊接免涂装耐候钢桥,开展了列车动力作用下的关键构件和焊接节点疲劳损伤分析,并进行考虑腐蚀劣化影响下的疲劳寿命评估。基于列车-轨道-桥梁耦合系统模型,研究了在高速列车动力荷载下桥梁主桁关键构件动力响应,并得到结构中最不利构件位置,分析了关键构件在列车通行振动效应下的疲劳损伤度。结合考虑局部节点板精细化的多尺度耦合有限元模型,考虑轨道不平顺和列车运行速度的影响,得到桥梁节点板在不同速度下的疲劳损伤度;考虑环境腐蚀对桥梁疲劳寿命的影响,结合桥梁列车年运营量进行腐蚀环境下桥梁关键杆件和节点的疲劳使用寿命评估。研究结果表明,铁路钢桁梁桥在列车动力作用下,不同构件的疲劳损伤不同,刚度较小以及应力响应影响线较短的构件疲劳损伤度更大,其中疲劳损伤度由大到小依次为节点横梁、腹杆、下弦杆、上弦杆。轨道不平顺和列车运行速度对桥梁节点板应力响应最大值影响并不显著,列车运行速度为120 km/h时与所分析桥梁共振更明显。环境腐蚀会降低铁路桥梁疲劳寿命,且对桥梁不同构件寿命影响程度不同。 2.2 高强钢丝、缆索的 腐蚀/腐蚀疲劳损伤 王鑫等研究了含裂纹高强钢丝在不同腐蚀周期后的力学性能变化及腐蚀机理。通过对1770MPa高强镀锌钢丝进行人工加工刻痕模拟微裂纹状态,在中性盐雾环境下进行了不同时间(120,240,360,480,720小时)的腐蚀试验。拉伸试验结果显示,随着腐蚀时间的增加,钢丝的极限强度、断后伸长率逐渐降低,但弹性模量基本不变。有限元分析表明,蚀坑刚形成时裂纹底部会发生应力集中,更易在此处断裂。断口分析显示,腐蚀会促进裂纹扩展,但不改变钢丝微观结构;随腐蚀时间增加,断口由韧窝转为脆性断裂。 Li等研究了腐蚀时间、应力水平、应力范围对钢丝失效模式、疲劳寿命和S-N曲线的影响。通过SEM扫描电镜扫描分析了不同腐蚀程度钢丝疲劳断裂和裂缝增长速率,揭示了腐蚀钢丝的裂纹萌生和扩展机制。图3展示了不同腐蚀程度下钢丝断裂形态。研究表明,钢丝疲劳寿命随腐蚀程度的增加而减少。这个腐蚀程度对钢丝疲劳寿命的影响是从敏感到不敏感。随着腐蚀程度的增加,晶体间距和裂纹增加速率也会增加,裂纹萌生比例和裂纹扩展区从缆索直径的45%减少到直径的28%。腐蚀深度越大、表面越锐利,越容易成为疲劳裂纹源。 图3 不同腐蚀程度下钢丝断裂形态图试件 (F20-d90-ε2000-1/2/3/4中F20代表第20个疲劳试件,d90代表腐蚀龄期为90天,ε2000表示应变水平为2000 με,1/2/3/4代表4个不同的应力范围) Xu等基于腐蚀寿命逆等阶假设,考虑斜拉索的腐蚀及其变化,建立了平行钢丝斜拉索中钢丝连续失效过程的等效循环次数递推公式。通过分别对钢丝的腐蚀程度和疲劳寿命进行两次阶次统计,估算了斜拉索疲劳寿命累积分布函数(CDF)的界限,但没考虑未断丝的荷载重分布。基于Bai的腐蚀程度从0.18%到18.67%的腐蚀钢丝的腐蚀应力寿命模型,通过蒙特卡罗模拟获得了腐蚀及其变化对斜拉索疲劳寿命的影响。结果显示,斜拉索的疲劳寿命受腐蚀程度较大的钢丝影响,一旦考虑了腐蚀及其变异性,斜拉索应在5%的钢丝断裂时视为失效。此外,随着腐蚀程度和及其变异性的增加,斜拉索的疲劳寿命会急剧下降,而钢丝和斜拉索的疲劳寿命的变异性也会增加。 Yan等基于钢丝实验数据,确立了钢丝的均匀腐蚀深度的均值和标准偏差之间的关系,获得了拉索中钢丝的质量损失率的分布。随后基于Miner线性累积损伤准则和平行系统理论去计算考虑钢丝腐蚀变化的疲劳寿命。 Yu研究了腐蚀和活载共同作用下钢丝耐久性。通过钢丝断面形态和不同样本腐蚀特征去分析钢丝的每种类型的失效模式。研究发现,在低应力幅下,钢丝的疲劳寿命主要受环境的影响。但随着应力幅的增加,疲劳寿命由应力幅决定。钢丝断裂形态分为单源断裂和多源断裂(图4)。腐蚀程度低的钢丝裂纹起源于单个疲劳源,随着疲劳程度增加,腐蚀坑的深度增加,裂纹从不同的疲劳源扩展。随着钢丝严重腐蚀,扩展区减少,断裂区域增加。 图6 钢丝裂纹失效模式 刘佳伟等为了评估在役满20年后拱桥吊杆钢丝的剩余疲劳寿命,基于某服役满20年拱桥更换下来的吊杆,以吊杆内部高强度钢丝为研究对象,对钢丝进行不同时间的加速腐蚀,获得不同腐蚀程度的钢丝试件。对试件钢丝进行表观检测、称重、疲劳实验和断口形貌分析,得到了不同腐蚀程度下钢丝的表面粗糙度、质量损失率、断裂机理和疲劳寿命。通过Weibull模型对疲劳寿命数据分析,得到了不同失效概率下吊杆钢丝的剩余疲劳寿命公式。研究结果表明,随着腐蚀程度的增加,吊杆钢丝表面粗糙度和质量损失率的数值不断增加,疲劳寿命降低且疲劳断口均为脆性破坏。打磨后的钢丝疲劳寿命有所提升;相同失效概率下,吊杆钢丝剩余疲劳寿命将随着应力比的增加或腐蚀程度的增加而减少。通过实验得到了在役满20年后拱桥吊杆钢丝的Pf-S-N曲线,为吊杆钢丝的服役状态和疲劳寿命预测提供了参考。 2.3 钢桥连接腐蚀/腐蚀疲劳损伤 Jiang等研究了腐蚀对钢塔角焊缝的疲劳寿命的影响,并提出了一种基于断裂力学方法的非承载角焊缝疲劳寿命预测方法。研究考虑了初始裂纹处的点蚀、初始裂纹附近的点蚀和腐蚀疲劳裂纹扩展三种腐蚀效应,并定义了不同腐蚀环境下的轻度、中度和重度三种腐蚀等级。结果表明,当点蚀发生在角焊缝初始裂纹处时,疲劳寿命会随着腐蚀深度增加而降低。在中等和严重腐蚀水平下,疲劳性能不满足Eurocode 3(图8);当点蚀发生在初始裂缝附近时,由于点蚀降低了焊趾附近裂缝前端的拉应力,角焊缝的疲劳性能会有所提升。 (a) CFCB-1 (b) CFCB-2 (c) CFCB-3 Kuang等研究了腐蚀栓钉的疲劳性能,并根据疲劳裂纹扩展理论和腐蚀栓钉疲劳失效机理,提出了腐蚀栓钉疲劳寿命预测模型。研究发现,随着栓钉腐蚀率的增加,疲劳寿命迅速降低。当栓钉的腐蚀率从5%增加到50%时,栓钉的疲劳寿命分别从20%下降到90%(图10)。 Guo等研究了轴向受力的高强度螺栓在腐蚀后的疲劳性能,对螺栓进行长达300天的中性盐雾试验,以模拟长期腐蚀。基于螺栓的宏观形态和微观形态,揭示了螺栓螺纹及锈蚀成分的演化规律,并建立了腐蚀时间对腐蚀坑的期望和方差影响的量化公式,获得了螺栓剪坏和断裂的失效模式。此外,失效模式转变时的临界腐蚀时间为150天,平均质量损失率为7.12%。如果腐蚀时间短于临界时间时,螺栓断裂变得更加明显;否则,螺栓螺纹剪切会变得更明显(图11)。分别针对螺栓断裂和螺栓螺纹剪切失效模式建立了疲劳寿命和腐蚀周期之间的指数和线性关系。同时,在中性盐性喷雾环境下的S-N曲线被提出,为腐蚀螺栓的疲劳寿命预测奠定了基础。 图11 高强度螺栓疲劳寿命与腐蚀时间的关系 芦燕等对G20Mn5QT/Q355异种钢对接焊接接头在模拟海水环境下的腐蚀疲劳性能进行了研究,开展了其在NaCl溶液中腐蚀疲劳试验(图13),并对腐蚀疲劳断口进行了扫描电子显微镜试验,分析了其腐蚀疲劳失效机理。研究揭示了在较大应力水平(>220 MPa)下,母材缺陷及焊接缺陷是导致裂纹成核的主要原因;而在较小应力水平(≤220 MPa)下,表面蚀坑是导致裂纹成核的主要原因。对腐蚀疲劳试验数据分别采用Stromeyer公式与基于三参数威布尔分布模型建立了对接焊接接头的腐蚀疲劳寿命预测方法,结果表明采用三参数威布尔分布的腐蚀疲劳S-N曲线拟合精度更高。 马燕等为了给解决耐候钢桥在应用和发展中所面临的腐蚀问题提供理论方法与对策,针对耐候钢在大气环境中的腐蚀损伤演化特性,通过编制MATLAB程序,建立了基于三维元胞自动机技术的耐候钢焊接节点大气腐蚀经时演化模型。该模型根据耐候钢在大气腐蚀过程中发生的化学反应,将大气腐蚀系统中的关键元素抽象成4种元胞类型,并离散成元胞网格。对母材和焊缝分别定义了不同的元胞邻居类型,模拟了耐候钢焊接节点代表性体元在介观尺度上的腐蚀演化过程,并通过大气暴露试验验证了所提出方法的可行性和有效性,揭示了耐候钢焊接节点腐蚀动力学及蚀坑演化规律,分析了溶解氧浓度和溶解概率对腐蚀损伤的影响。在此基础上提出了耐候钢大气腐蚀经时演化预测方法。 腐蚀检测与评估 3.1 桥梁钢构件腐蚀监测技术 目前全球范围内桥梁“老龄化”问题凸显,受腐蚀损害严重,桥梁的服役性能劣化及桥梁倒塌等灾祸在全球范围内出现了逐年上升的趋势。因此,加大桥梁养护和检测势在必行。目前检测桥梁腐蚀状况的检测技术主要是基于计算机视觉和机器学习的损伤识别方法和基于传感器检测技术的无损检测方法。 3.2 基于计算机视觉和机器学习 的损伤识别方法 冯东明等为了实现悬索桥主缆的自动化、智能化检查,开展了基于无人机的主缆巡检路径规划和小样本数据下的主缆病害识别研究(图14)。首先,利用无人机倾斜摄影测量技术快速建立悬索桥的三维模型,提出主缆无人机自动巡检路径的规划方法;然后,采用Faster RCNN网络模型识别主缆图像中的表观病害;最后,采用基于图像融合的数据增强方法,提高小样本数据集下目标检测的准确率。在Faster RCNN网络模型训练过程中,随着训练轮次的增加,测试集中裂纹、锈蚀和划痕三类病害的平均精确率得到提升,并在第15个训练轮次后逐渐稳定,经过100个训练轮次后,测试集中所有类别的平均精确率为0.723。以小龙湾桥为研究对象,进行了主缆的现场检查试验。研究结果表明,基于悬索桥三维模型进行主缆无人机自动巡检路径规划具有实际可行性;基于Faster RCNN网络模型能较准确地识别主缆的裂纹、锈蚀和划痕病害;利用图像融合方法生成病害数据能有效克服数据样本少的问题,并提高识别的准确性。 图15表明,所提出的自适应光照预处理方法有效改善了实桥腐蚀图像的光照不均和低光照问题,修复和增强了细节和纹理特征信息,颜色保真度较高;所提出的数据标注方法能够精准标注腐蚀区域,减少边缘描绘工作;与原始图像相比,该方法预处理后的图像训练的模型在准确率、精确率、召回率、F1-score、交并比IoU和AUC上分别提高了5.2%、2.7%、22.5%、19.4%、25.4%和10.5%;对于光照良好的均匀腐蚀图像,预处理对分割精度提高有限,对于点蚀图像,分割精度有较大的提高,对于低光照或光照均匀性较差的图像,分割精度得到了大幅提高。 Gao等采用了基于视觉图像特征的准确检测方法。无人机技术用于收集钢桥的腐蚀图像。考虑到图像的复杂性,利用深度神经网络对图像进行卷积运算。根据锈迹图像的明显特征构建了一个深度神经网络模型。监督学习的深度神经网络与无监督学习的稀疏自编码相结合,通过无监督学习的稀疏自编码对深度神经网络进行自编码来减少重构偏差。在此基础上,实现了对锈蚀状态的准确检测。 3.3 基于传感器检测技术的 无损检测方法
耐腐蚀材料 陈继林采用腐蚀失重法、宏观形貌观察、扫描扫描电子显微镜、X射线衍射及电化学测试,对耐候冷镦钢在模拟海洋大气环境中的腐蚀行为进行了研究。图18显示,在模拟海洋大气腐蚀环境下,耐候钢表面锈层随腐蚀时间由浅黄色依次向棕黄色、红棕色转变;锈层截面形貌从薄而疏松、不连续演变为厚而致密、均匀分布;锈层微观形貌显示,表面锈层存在相对平滑、不规则圆形花状结构、闭环的环形巢结构、毛绒状结构等4个演变状态,但致密的毛绒状结构锈层对基体的保护能力明显提高;腐蚀产物主要由Fe3O4、γ-FeOOH、α-FeOOH组成,腐蚀初期主要是致密的Fe3O4,腐蚀中期开始形成γ-FeOOH,腐蚀后期γ-FeOOH逐渐溶解并还原形成稳定的α-FeOOH,对基体提供良好的保护作用;电化学分析显示,腐蚀24~72 h,耐候钢的阴极电流密度呈线性增大,且趋于稳定。耐候钢的腐蚀深度损失与腐蚀时间呈幂函数关系;受腐蚀过程不同腐蚀产物的影响,腐蚀速率呈现先增长后下降的变化规律。 张宇等考虑免涂装耐候钢桥面临着腐蚀环境的巨大挑战,基于ISO规范对环境腐蚀的分类,回顾和讨论金属材料和耐候钢腐蚀评价方法。依据我国《桥梁用结构钢》和《耐候结构钢》的规定,采用指数线性模型得到《桥梁用结构钢》规定耐候钢腐蚀上限模型。对比结果表明,我国耐候钢具有较好的抗腐蚀性能,并且在各环境腐蚀等级中,抗腐蚀性能与欧洲耐候钢基本相当。通过耐候钢腐蚀试验数据验证了腐蚀模型的准确性,表明基于耐候钢腐蚀上限模型可作为免涂装耐候钢桥梁的设计依据。结合《铁路桥梁钢结构设计规范》与《公路钢结构桥梁设计规范》,提出基于腐蚀量模型的免涂装耐候钢桥梁强度和稳定设计方法,为我国免涂装耐候钢桥梁设计提供理论依据。为简化设计,还提出容许腐蚀厚度设计方法用于超低,低和中度腐蚀环境,其中,超低和低腐蚀环境容许腐蚀厚度取500 μm,中度腐蚀环境容许腐蚀厚度取1000 μm。 朱桂琴以Q500Qenh钢为基材,利用二氧化碳气体保护焊方法,制作了两种含不同耐候元素的焊接接头试样(图19)。利用干湿交替加速腐蚀试验考察了两种试样的耐蚀性及其元素富集情况。结果表明,相比于2号焊接接头试样,耐候元素含量较多的1号焊接接头试样经腐蚀后,锈层更加致密、稳定,且耐候元素出现明显富集,腐蚀率与腐蚀深度均较低。 李伟伟等采用中性盐雾加速腐蚀试验,使试件处于较高浓度的氯离子环境中,模拟钢材在海洋大气环境中的长期腐蚀行为,对Q355NH,Q355钢的腐蚀形貌,以及腐蚀后的力学性能进行了研究分析。得出了Q355NH钢和Q355钢的均匀腐蚀厚度、蚀坑深度与质量损失率的幂函数定量关系。相比Q355钢,Q355NH钢在腐蚀早期的腐蚀速率更大,但在长期腐蚀作用下,Q355NH钢的耐腐蚀性更好。 图21 未稳定化处理和稳定化处理的Q420NH钢的锈层截面元素分布图
防腐技术 桥梁中钢结构的防腐技术涉及多个层面,包括使用专门的防腐涂料来隔绝腐蚀介质、采用阴极保护等电化学方法来减缓腐蚀、依据环境特点设计合理的涂层体系、进行严格的表面处理以增强涂层附着力、执行定期的检查和必要的维护工作、控制腐蚀环境的温湿度、应用耐候钢以提高耐大气腐蚀性能、遵循防腐涂装养护技术指南和标准,以及在设计和施工阶段就综合考虑防腐措施。这些技术的综合应用有助于延长桥梁钢结构的使用寿命,确保桥梁的安全性和耐久性。 任玉苓等采用平板、切口、划线、杯突、折弯等不同制样方式,对不同种类锌铝镁镀层彩涂钢板在连续盐雾试验中的涂层起泡等级、切口和划线扩蚀宽度、不同试样部位的红锈出现时间等进行检测,获得了不同锌铝镁镀层种类、不同镀层质量、不同涂层种类、不同加工方式彩涂钢板的耐盐雾性能。同时与锌铝镁镀层盐雾试验数据进行对比,找到了涂镀层钢板耐盐雾性能的规律,为评估不同镀层彩涂产品耐蚀性能奠定基础。 张泽灵等采用基于硫氰酸铵溶液的试验和电化学方法,研究了强度等级和表面质量对热镀钢丝应力腐蚀敏感性的影响,并分析了应力腐蚀断口形貌。图22表明,1860 MPa级和2060 MPa级桥梁缆索用热镀钢丝的应力腐蚀断裂时间相当,但2060 MPa级钢丝的应力腐蚀时间更加离散;钢丝表面越粗糙,应力腐蚀敏感性越强;2060 MPa级钢丝表面采用800目砂纸打磨后,应力腐蚀断裂时间明显缩短。应力腐蚀断口形貌分为裂纹源区、裂纹扩展区和瞬断区,裂纹主要起源于表面。 图22 桥梁缆索用热镀钢丝的应力腐蚀开裂断口形貌 卢道胜等使用3种钝化工艺对9Cr1Mo钢进行表面钝化处理,通过电化学测试、FeCl3腐蚀试验、盐雾腐蚀试验、高温高压腐蚀试验测试3钝化工艺对9Cr1Mo合金耐腐蚀性能的提升。结果表明,通过钝化处理,在9Cr1Mo钢表面形成保护性好的钝化膜,可有效降低钢基体的腐蚀速率使得耐电化学腐蚀性能和耐盐雾腐蚀性能显著提升。在高温高压腐蚀试验中未钝化和钝化后的9Cr1Mo钢的腐蚀过程由CO2和H2S腐蚀共同控制,钝化处理有利于钢基体发生更为均匀的腐蚀,对9Cr1Mo钢表面腐蚀膜的形成过程产生一定影响,但不会改变其腐蚀机理。 徐攀等采用电镀锌和热镀锌铝对Ф4.3 mm SWRS82B钢丝进行表面处理,对电镀锌和热镀锌铝钢丝在0.1 mol/L HCl溶液中进行耐腐蚀性能研究,对腐蚀后的形貌进行观察并分析腐蚀机理。结果表明,电镀锌后钢丝表面粗糙度Ra=1.024 μm,热镀锌铝后钢丝表面粗糙度Ra=0.637 μm,热镀锌铝试样表面粗糙度明显小于电镀锌试样;电镀锌的锌层厚度约为15 μm,扩散层为35 μm,热镀锌铝合金的镀锌层约为24 μm,扩散层为50 μm,热镀锌铝试样的耐腐蚀性能明显优于电镀锌试样。 王海洋等为提高大桥主缆防腐效果,开发研制了S形精密热镀锌钢丝。选用可加工性强的低碳钢盘条,对酸洗、开坯、连续冷轧、热镀、精整等工序进行优化,完成产品尺寸精度和表面质量的控制(图23)。试验结果满足预期的性能指标要求:S形热镀锌钢丝抗拉强度650~700 Mpa,扭转20次以上,弯曲8~12次,锌层面质量300~330 g/m2,缠绕试验8圈不断,钢丝表面锌镀层平整光滑,缠丝应用良好。 图24 温州东欧大桥吊杆防水套包覆防腐方案效果 图25 舟山官山大桥吊杆防水套包覆防腐方案效果 姚迪等依托某海港LNG码头工程,从分析海水腐蚀环境出发,结合码头结构耐久性要求,介绍了钢管桩牺牲阳极阴极保护系统(图28)的设计过程、牺牲阳极材料及类型的选取、各参数的计算方法、施工工艺流程、焊接施工质量检验及系统保护效果检测。阐述了通过减小牺牲阳极与被保护钢结构之间的距离、适当增加小规格牺牲阳极重量的设计优化方式,达到满足设计年限要求、节省工程投资、方便安全施工的目的。 图29 不同干湿态时间比下牺牲阳极的活化溶解形貌
结论与展望 随着桥梁钢结构在各种环境条件下的广泛应用,其面临的腐蚀问题日益突出,对桥梁的安全运营和耐久性构成了严重威胁。腐蚀环境显著影响桥梁钢结构的疲劳寿命,而腐蚀与疲劳的耦合作用会进一步加速结构损伤的进程。为了应对这些挑战,研究人员已经开展了多方面的研究工作,包括腐蚀疲劳损伤机理的深入分析、腐蚀监测技术的创新、以及耐候钢和其他耐腐蚀材料的开发与应用等。此外,智能监测技术的应用、基于数据驱动的维护策略的提出,以及综合防腐措施的实施,都表明了桥梁钢结构防腐技术正朝着更加智能化、系统化和环保化的方向发展。对2023年桥梁钢结构腐蚀进展总结与展望如下: (1)研究发现腐蚀环境对钢桥的疲劳寿命和性能有显著影响,腐蚀疲劳耦合作用下,结构的损伤发展速率加快,疲劳寿命降低。研究者们通过建立模型、进行实验和理论分析,提出了不同的预测和评估方法,以提高钢桥的耐腐蚀性能和延长其使用寿命。未来的研究可进一步探索和完善腐蚀疲劳损伤的预测模型,以更准确地预测钢桥在不同环境和载荷条件下的使用寿命。此外考虑到实际应用中腐蚀环境的复杂性,未来的研究还应包括多因素耦合作用下的腐蚀疲劳行为,如温度、湿度、盐分等环境因素与多载荷的交互影响。 (2)桥梁的腐蚀监测技术主要是采用基于计算机视觉和机器学习的损伤识别方法,以及基于传感器的无损检测技术。利用无人机技术结合三维模型自动规划巡检路径,并通过深度学习模型来识别桥梁主缆的病害。此外,尤其是在光照条件不佳的情况下,可以通过自适应光照预处理结合深度学习的方法可以改善腐蚀区域检测的难题。结合无人机采集的高清图像和深度学习网络,能够有效地建立钢桥病害图像库,实现病害的自动识别。在无损检测方面,MsS超声导波检测系统能够快速检测桥梁缆索的内部损伤,具有较高的检测灵敏度和效率。在未来应该继续优化深度学习和机器学习算法,以提高病害识别的准确性;结合物联网(IoT)技术,实现桥梁状态的实时监测和数据收集,为桥梁管理和维护提供更准确的信息;在数据分析方面,开发更复杂的数据处理和模式识别算法,以便从大量监测数据中提取有用信息,预测桥梁的腐蚀趋势和潜在风险。 (3)耐候钢的研究集中在理解其腐蚀行为、锈层结构与性能、表面处理技术、焊接技术、腐蚀疲劳性能,以及在设计方法与规范、免涂装桥梁设计、全寿命周期评估、新材料开发和智能监测等方面的应用。未来应该给予更多关注在耐候钢性能提升和在复杂环境下耐候钢的开发。并进一步对钢材中添加金属元素含量的改良,逐步提高耐候钢的防腐性能指标。 (4)桥梁钢结构的主要防腐方法包括使用防腐涂料隔绝腐蚀介质、阴极保护等电化学方法减缓腐蚀、设计合理的涂层体系、进行表面处理以增强涂层附着力、执行定期检查和维护、控制腐蚀环境的温湿度、遵循防腐涂装养护技术指南和标准,以及在设计和施工阶段综合考虑防腐措施。在未来应该深入探索和开发先进的防腐材料与技术,以实现更高效和持久的腐蚀防护效果;其次,开发和优化新型环保防腐涂料和合金材料,以提高桥梁钢构件的耐久性;此外,研究应更多地考虑耐久性设计,通过标准化施工工艺和高质量的表面处理技术来增强涂层的附着力和防腐性能;最后,探索不同环境条件下的防腐技术,并开发适应这些环境的高性能防腐系统。
免责声明:本网站所转载的文字、图片与视频资料版权归原创作者所有,如果涉及侵权,请第一时间联系本网删除。
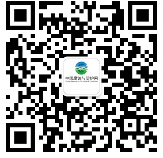
官方微信
《腐蚀与防护网电子期刊》征订启事
- 投稿联系:编辑部
- 电话:010-62316606
- 邮箱:fsfhzy666@163.com
- 腐蚀与防护网官方QQ群:140808414