1 前言
流体作用下的金属材料容易发生冲刷腐蚀。这种腐蚀在海洋环境及石油管道运输中十分常见,其在工业磨损中所占比重大于5%[1]。冲刷腐蚀是金属表面与腐蚀性流体之间由于高速相对运动而产生的金属损坏现象,是冲刷磨损和电化学腐蚀交互作用的结果[2]。冲刷与腐蚀协同作用造成的金属材料失重远大于冲刷和腐蚀单独作用之和[3-8]。一般来说,机械磨损在金属的冲刷腐蚀中占主要作用[9-12];而电化学腐蚀在整个冲刷腐蚀中发挥着重要作用[12-14]。
冲刷腐蚀是一个十分复杂的过程,影响腐蚀速率的因素有很多,主要包括:液体流速[5,15-17]、流体含沙量[3,5,15,16]、沙粒大小[15,16]、冲刷角[6,9,14,18]、流体pH值[18]、溶液温度[16,17,19]、材料的组成[3,14]、材料的微观结构[4,20,21]和热处理制度[22]等。
2 国内外研究状况
目前,国内外学者对冲刷腐蚀进行了较深入的研究,主要采用电化学测试手段及失重方法研究了不同流体力学条件、环境因素、材料性质对金属冲刷腐蚀的影响作用。丁一刚等[23]对国内外液/固两相流的冲刷腐蚀研究进行了综述,重点论述了冲刷腐蚀的影响规律及其危害性。近几年来,有研究者[24,25]开始使用计算机建模的方法模拟冲刷腐蚀实验,以期揭示流体力学因素对冲刷腐蚀的影响规律,从而找到减少流体中金属冲刷腐蚀的方法。随着金属材料的研究开发,对金属进行表面改性处理以增强其抗冲刷腐蚀的性能成为冲刷腐蚀研究的趋势[20,26,27]。
本论文主要对冲刷腐蚀机理、影响冲刷腐蚀的因素等进行概括,并从元素含量、热处理制度及金属基复合材料发展等几个方面综述提高金属材料防冲刷腐蚀性能的几种方法,重点介绍冲刷腐蚀的国内外最新研究进展,为金属冲刷腐蚀的研究与防护提供依据和帮助。
3 冲刷腐蚀的机理
3.1 冲刷腐蚀的组成
由机械磨损和电化学腐蚀的相互作用引起的金属材料的腐蚀速率大于两者单独作用时的腐蚀速率之和[6,10]。研究[11,18]表明,冲刷腐蚀速率KEC可表示为:
其中,KC0和KE0分别为单独的电化学腐蚀速率和冲刷磨损腐蚀速率,ΔKC和ΔKE分别为冲刷磨损对电化学腐蚀的加强及电化学腐蚀对冲刷磨损的增强部分。KC0可通过测定静止溶液中金属材料的腐蚀速率得到,KE0可通过测定电极施加阴极保护后的冲刷磨损速率得到[28,29];KC可通过极化曲线或者电化学阻抗谱 (EIS) 计算得到,最后求得ΔKE。式 (1) 可用于分析不同环境因素和材料性质对冲刷腐蚀速率及机理的影响。郑玉贵等[30,31]探讨了冲刷磨损与电化学腐蚀交互作用规律、影响因素及冲刷引起的“腐蚀增量”和腐蚀引起的“冲刷增量”的产生机制。结果表明,冲刷磨损对电化学腐蚀的影响主要在于影响O2、腐蚀产物等的传质过程,同时使材料钝化膜减薄、破裂,使材料发生变形,并形成冲蚀坑,从而加速电化学腐蚀。电化学腐蚀对冲刷磨损的作用主要表现在粗化电极表面,弱化材料的晶界、相界,使材料中耐磨的硬化相暴露,突出基体表面,从而促进冲刷磨损。
3.2 冲刷腐蚀中的冲刷磨损部分
一般来说,机械磨损在金属的冲刷腐蚀中占主要作用[9-12]。机械强度性质是影响金属材料冲刷磨损失重的最主要因素[11,12]。
Jana等[18]认为冲刷磨损速率KE可表示为:
其中,c为沙含量,Ui为流体流速,EM为无因次侵蚀率。根据Finnie第一和第二模型[32]及沙粒的反弹效应,EM与以理想行为撞击电极的沙粒百分含量、回弹系数、金属材料的密度、硬度及冲刷角有关。
从式 (2) 可以看出,机械磨损主要受流体流速和溶液含沙量影响,并与冲刷角、沙粒及金属的性质有关系。然而,Meng等[10]和Hu等[33]发现,流体速率较高时或者溶液中沙含量达到临界值后,冲刷腐蚀速率并不随流体流速及沙含量的增大而加剧。因此推测,式 (2) 仅在流速较低、沙含量较小的条件下成立。
3.3 冲刷腐蚀中的电化学腐蚀部分
Neville等[13-15]使用电化学手段对液/固流体中合金的腐蚀和机械冲刷进行了较深入的研究,结果表明电化学腐蚀在整个冲刷腐蚀中发挥着重要作用。电化学腐蚀一般包括金属的溶解、钝化、过钝化及点蚀4个部分。本体溶液中,金属的电化学腐蚀主要与溶液中腐蚀离子的种类及浓度、氧含量、温度、pH值及金属本身的性质有关。流体中,除了以上因素影响金属的电化学腐蚀外,由于流体对金属表面基体及钝化膜造成破坏,金属的电化学腐蚀与流体流速、溶液中沙含量、沙粒大小、冲刷角等有关系。
Yu等[34]研究了Q235碳钢在长江水、黄河水和塔里木河水3种水体中的冲刷腐蚀行为。其中,塔里木河水由于Cl-,SO42-和HCO3-等腐蚀性离子含量远高于其它两种水体,在其它条件不变的情况下,Q235钢在塔里木河水溶液中的冲刷腐蚀总速率接近其在长江水中冲刷腐蚀失重的两倍。
流体力学因素对类似于不锈钢的钝化金属的极化曲线影响较大,这与不锈钢表面快速形成的附着力较强的钝化膜有关。当电极表面无钝化膜形成时,机械磨损对金属材料的自腐蚀电位和电化学腐蚀速率影响较小。而对于能够形成钝化膜的金属材料,在一定的腐蚀环境中发生机械磨损时,钝化膜因溶液中粒子高频率的冲击而受损;当钝化膜的破坏/再钝化交替发生时,电极表面的电化学反应速率迅速增加,从而加速了不锈钢的腐蚀速率[12,35]。Jiang等[36]研究不锈钢在20%H2SO4溶液中的冲刷腐蚀时发现,机械磨损使得其腐蚀电势负移约400 mV,阳极电流密度增大约两个数量级。这一结果与Li等[37]研究不锈钢在10%H2SO4溶液中钝化电流密度随溶液流速增加迅速升高的研究结论相吻合。与不锈钢相比,低合金钢的腐蚀速率则不易受流体冲刷的影响,主要因为低含量合金难以形成致密的氧化膜[12]。
3.4 冲刷磨损与电化学腐蚀的相互作用
Stack等[38]分别研究了X52钢在水溶液、80%油水混合液、油溶液中的冲刷腐蚀行为后,根据冲刷磨损与电化学腐蚀在整个冲刷腐蚀中的贡献程度,将冲刷腐蚀机制分为以下4类:(1) KC/KE<0.1时为冲刷磨损控制,(2) 0.1≤KC/KE<1时为冲刷磨损-电化学混合控制,(3) 1≤KC/KE<10时为电化学-冲刷磨损混合控制,(4) KC/KE≥10时为电化学控制。
Stack等[38]的研究发现,一定条件下,水溶液中冲刷腐蚀主要由电化学-冲刷磨损控制,在油水混合液中腐蚀主要由冲刷磨损-电化学控制,而在纯原油溶液中则由冲刷磨损控制。这是由于Fe2+和Fe3+在油中的溶解度较小,油的比重增大时,钢的溶解受阻,电化学腐蚀过程受到抑制[16]。
流体冲刷加剧金属电化学腐蚀主要包括两方面[28]:(1) 增强了O2的传质过程,加速了钝化金属的钝化或者再钝化过程及非钝化金属的电化学腐蚀过程,促使金属表面形成的腐蚀产物脱落,从而加速腐蚀;(2) 机械力作用于金属电极表面,削薄或者破坏表面钝化膜。此外,冲刷造成材料表面出现凸凹不平的冲蚀坑,增加了材料的比表面积,从而导致腐蚀加剧[31]。与静态相比,动态条件下X60钢在10%H2SO4溶液中的阴极极化曲线多了一个斜率较小的“平台段”,向溶液中充入N2除氧,该“平台段”下移,流速增大平台段上移[39]。动态条件下,氧去极化成为一个主要的阴极过程。
腐蚀对冲刷的影响主要在于粗化材料表面,造成微湍流的形成,同时溶解掉材料表面的加工硬化层,降低其疲劳强度,从而促进冲刷[31]。
4 冲刷腐蚀的研究装置
实验室研究冲刷腐蚀的装置主要有3类:旋转圆盘 (柱) 电极 (RDE/RCE)[16,17,19,40-45],管路装置[46,47]和喷射式装置[6,9,13,35,38,48]。
一般来说,使用RDE和RCE研究水动力流体条件对金属冲刷腐蚀影响时,旋转圆盘或圆柱很难使得底部的沙粒全部均匀悬浮在溶液中,因此,实验中改变沙粒含量时,腐蚀速率随沙含量的变化不显著;喷射式装置则可以用于研究流体中固体粒子的机械撞击对腐蚀的影响。RDE和RCE分别用于产生层流与湍流,当旋转速度够高时,RDE也可以产生过渡或者相对的湍流[16]。除了这3种装置外,泥浆罐[49]、旋转笼[50]以及Coriolis测试仪也可用于研究冲刷腐蚀。
郑玉贵等[30,31]对研究冲刷腐蚀装置的各类实验方法及设备的优缺点进行了总结,认为在实验室条件下,RDE装置由于设备简单、价格低廉、测试用液量小 (一般可小于4 L)、实验周期短等优点使用最为广泛。此外,喷射式装置由于可以精确控制冲击液流的流速、冲刷角并可获得很高的流速,使用也较为常见。管流装置由于整套系统占据空间大,实验所需溶液量大,泵需要持续运转,实验周期长,对阀门、管件以及密封的可靠性要求高,整套装置的费用和实验费用均较高,较少使用。
5 冲刷腐蚀的研究方法
目前,国内外研究冲刷腐蚀的方法主要分为两大类:实验测试和数值模拟。
5.1 实验测试
实验测试研究主要包括:采用极化曲线[16,38,51]、循环极化曲线[52]、恒电位阶跃 (Potentiostatic measurements)[33,53]、EIS[16,22,27,42,54]和电化学噪声 (EN)[55]等电化学技术准确测取金属冲刷腐蚀过程中的腐蚀速率,使用扫描电镜 (SEM)[8,54]、光学显微镜[8]、共焦激光扫描显微镜 (CLSM)[56]、透射电镜 (TEM)[27,56,57]、X射线衍射 (XRD)[58]和X射线光电子能谱 (XPS)[56]等测试技术观察腐蚀前后电极表面微观结构和成份变化;综合上述方法的测试结果可判断冲刷腐蚀的类型。此外,失重法[38,59]也广泛地被用于定量地计算金属的冲刷腐蚀总速率。这些方法可用于研究不同环境因素如流体条件、材料性质等对低碳钢、不锈钢等材料冲刷腐蚀的影响。于福洲等[60]通过采用划伤电极法来测定金属的再钝化动力学参数,从而发展了一种用于快速评价合金耐冲刷腐蚀性能的新方法。
5.2 数值模拟
在目前的冲刷腐蚀研究中,采用计算流体动力学 (CFD) 软件进行数值模拟,是使用最为广泛的数值模拟方式。
通过模拟金属材料在冲刷条件下的腐蚀进行腐蚀机理研究,对流态进行数值仿真模拟计算,可以减少实验和设计工作的盲目性和工作量,降低消耗并增加可靠度。Stack等[24,25,61,62]在此方面进行了较深入的系统研究,将CFD软件模拟技术和有限元技术用于模拟材料的失重从而评估不同参数对冲刷腐蚀过程的影响,绘制出Fe弯管上冲刷磨损控制的部位与电化学腐蚀占主导地位的部位图[61]。
除采用CFD软件外,部分研究者自主设计软件,用来模拟冲刷腐蚀。林玉珍和雍兴跃[63-68]等较早地采用数值计算与实验研究相结合的方法,通过确定不同流动体系中不同流态的流体力学模型,在分析流动腐蚀过程不同的动力学主控因素及其在协同效应中的相对影响程度的基础上,建立流动腐蚀动力学模型,结合冲刷腐蚀实验,研究了双相不锈钢、碳钢在不同流动体系下的冲刷腐蚀机理,结果发现模拟计算得到的腐蚀速率与实测值基本一致。此外,Zhang等[69]在冲刷腐蚀建模方面也做了一些工作。
6 影响金属冲刷腐蚀的主要因素
6.1 流体环境对冲刷腐蚀的影响
流体环境中,金属基体在静态溶液中形成的表面氧化膜难以持续存在,腐蚀加剧[9,35]。流体对金属冲刷腐蚀的影响主要表现为正应力和剪切应力的竞争效应。机械磨损、电化学腐蚀、以及两者的协同作用主要决定于电解液、金属本身的性质和摩擦学条件[12]。
Meng等[10]研究了液体流速、沙含量及温度对不锈钢冲刷腐蚀行为的影响。实验发现,水流速率和沙介质对腐蚀速率的影响较大,温度影响最小。Hussain等[70]认为金属表面的去钝化及再钝化过程与单位时间内沙粒撞击电极表面的动力学总能量EK有关。
式中,N为沙粒单位时间内撞击电极表面的次数,mav为沙粒的平均质量,V为沙粒的运动速率。
6.1.1 流速对冲刷腐蚀的影响 在冲刷腐蚀过程中,流体流速发挥着重要的作用,其影响着传质过程尤其是腐蚀粒子Cl-的传递[10]。
流速对冲刷腐蚀的影响可分为3种情况[71]:(1) 流速较低且没有诱发对流的情况下,传质主要由自然对流引起,金属表面钝化膜保护金属免于严重的电化学腐蚀,金属钝化占主导地位,冲刷磨损相对较弱;电化学腐蚀在整个冲刷腐蚀过程中占主导地位,冲刷腐蚀主要受电化学腐蚀机制控制[54]。(2) 在中等流速时,诱发的对流导致传质的增加,液体流动引起的剪切力使得电极表面的钝化膜不再稳定,腐蚀速率迅速增大,此时,冲刷磨损开始占据主导作用。(3) 在更高的冲刷速率下,金属表面难以形成有效的保护膜,腐蚀速率达到较高值,且不再发生变化,此时会产生机械流体效应,并且材料的损伤机制变得格外复杂。杨帆等[52]采用循环极化曲线检测BFe30-1-1铜镍合金在不同流速人工海水中电极表面钝化膜的完整性时发现,在低流速 (低于2 m/s) 或静止条件下,材料表面存在较完整的保护膜,而高流速 (3 m/s) 下保护膜破裂。对于UNS S32654和UNS S31603两种不锈钢,临界速度都在4~7 m/s之间[53]。低于临界流速时,电化学腐蚀在整个冲刷腐蚀过程中占主导地位,冲刷腐蚀主要受电化学腐蚀机制控制[54];高于临界流速时,金属的冲刷腐蚀受电化学腐蚀与冲刷磨损机制控制。当溶液流速增至7 m/s时,电极表面会发生弹性变形并出现划痕[53]。不同冲刷条件下,金属的流速临界值不同。高流速下沙粒撞击的动力学能量的增大及撞击次数的增加,将产生较大的瞬态腐蚀电流。
吴成红等[72]认为增大流速也有其有益的一面,如增大流速可以减少腐蚀性物质在金属表面的累积,从而避免点蚀和缝隙腐蚀的发生。另外,增大流速可以改善钝化剂或抑制剂通过流动边界层到达金属表面的能力,从而促进金属的钝化,起到抑制腐蚀,保护金属基体的作用。
此外,Ruff等[73]总结了影响金属机械磨损的因素,其中最主要的是含沙流体的流速;机械磨损随流体的流速增大,以沙粒速率的平方或立方的速率加速磨损。在Bitter的模型[74]中,机械磨损正比于沙粒速率的平方。
6.1.2 沙含量的影响 流体中的沙粒加速了金属的腐蚀。沙粒对电极表面氧化膜的冲击破坏使得金属裸露在流体中,或者沙粒冲击电极表面使得氧化膜难以形成,导致电化学腐蚀及其与冲刷磨损的协同效应部分对整个电极失重贡献很大[15]。有研究[17,19,53]发现,在不加沙的条件下,Al合金和不锈钢的电化学腐蚀主要由O2的扩散步骤控制,增大电极转速,O2扩散速率加快,电极表面形成氧化膜;在加沙条件下,电极转速增大时,合金的电化学腐蚀加剧。
冲刷腐蚀速率随着溶液中沙含量的增加而上升[27]。Zhang等[9]在研究了乙二醇/水溶液体系中3003铝合金的冲刷腐蚀后指出,随着沙含量的增加,冲刷腐蚀总速率增大,其中机械磨损部分的失重增加较多,而电化学腐蚀部分基本不变。这一研究结果得到了Stack等[24]的证实。其采用CFD模型来模拟室温下粒子浓度对90°弯管的冲刷腐蚀的影响,结果表明,随着沙浓度的升高,电化学腐蚀在整个冲刷腐蚀的比重下降。
冲刷腐蚀程度并不随着含沙量的升高而一直加剧。Meng等[10]和Hu等[33]研究了不锈钢从钝化态到伪钝态的腐蚀转换行为,并证明了沙含量临界值的存在。在腐蚀体系由流体引发的电化学腐蚀到冲刷腐蚀的转变中,沙含量及流体流速存在临界值,表明电极表面在低含沙量和低流速下形成的钝化膜消失[53]。Zheng等[75]认为,溶液中沙含量在临界值以下时,冲刷腐蚀速率随沙含量增大而加剧,当沙含量高于临界值时,冲刷腐蚀速率达到稳定,不再随沙含量增大而增加。在Hu等[53]的研究中,临界含沙量为60~100 mg/L;高于临界值时,两种不锈钢电流明显增大,并且波动频率变大,这主要源于冲刷腐蚀由流体引发的电化学腐蚀机制转换为冲刷腐蚀机制。含沙量低于60 mg/L时,电流的上升主要源于电化学反应 (如点蚀的产生)。在含沙量为60~200 mg/L时,沙粒对电极表面的撞击有效地破坏了表面的氧化膜,导致电流上升。然而,Neville等[15]发现沙含量更高 (15%和20%,质量分数) 时,合金由于冲刷腐蚀导致的失重下降,可能由于碰撞沙粒和反弹沙粒之间的相互干扰所致[72]。
6.1.3 沙粒大小对冲刷腐蚀的影响 冲刷腐蚀速率随着溶液中沙含量及沙粒尺寸的增加而增大[11,16]。沙含量一定时,沙粒尺寸的改变引起沙浓度的相应变化[45]。沙粒粒径较小 (<50 μm) 时,电化学腐蚀占主导地位,冲刷腐蚀速率与沙粒的大小无关;沙粒粒径超过100 μm时,这种无关性减弱[71],且金属电化学行为表现为钝化[45]。
Zheng等[75]研究了2.4%NaCl溶液中加入尺寸约6.6 μm的海泥对碳钢冲刷腐蚀行为的影响。研究发现,与尺寸38 μm的沙粒加剧冲刷腐蚀相比,溶液中海泥含量越高,金属冲刷腐蚀失重反而越少,作者认为由于海泥颗粒较小,粘附在电极表面起到了隔绝金属与溶液的屏障作用。Luo等[76]研究沙粒尺寸对表面涂有涂料的合金在含沙的1%NaCl的自来水中的冲刷腐蚀行为的影响,发现了两个临界沙粒尺寸。沙粒尺寸低于第一个临界直径 (FCD,80 μm) 时,材料的冲刷腐蚀失重随沙粒尺寸增加变化不大。当沙粒尺寸大于FCD小于第二个临界直径 (SCD,410 μm) 时,冲刷腐蚀引起的失重随沙粒尺寸增大呈指数增加。沙粒直径大于FCD时,冲刷腐蚀速率随沙粒尺寸增大基本保持不变。作者认为,沙粒的撞击力与惯性力及粘滞阻力有关,惯性力大小正比于沙粒直径的立方,而粘滞阻力正比于沙粒直径的平方,惯性力使得沙粒以原来的方向前进,粘滞阻力则阻碍沙粒前进。因此,单个沙粒的有效撞击力随直径增大而增加。能使金属材料产生裂缝或者使填料脱离涂料的沙粒最小撞击能对应FCD。小沙粒则仅仅影响流体的密度和液体介质的流动状态。
当沙粒尺寸达到临界值后,电极表面的冲刷磨损速率不会随沙粒尺寸的增大而增大;可能的一种解释为颗粒大的沙粒易发生碎裂,导致实际的撞击能小于实验条件下理论的撞击能[77]。沙粒浓度恒定时,随着沙粒尺寸减小,相邻两次撞击的时间随之变小,导致金属的再氧化大大减小。而相邻两次撞击之间的时间决定再钝化速率,从而最终决定去钝化速率[21]。
另外,沙粒本身的性质也会影响金属冲刷腐蚀速率。随着电极材料硬度与沙粒硬度比值的增大,机械磨损速率迅速降低,而电化学腐蚀速率则与该硬度比值无关[12]。根据相关的磨损实验结果,要使得材料的耐磨性有较大的提高,材料硬度与磨料硬度的比值应达到0.8以上[78]。
6.1.4 温度的影响 流体温度升高,一方面使得O2扩散速率增大,金属表面易于生成钝化膜;另一方面,流体粘度降低,撞击能增大,电极表面的损坏程度加剧,导致电荷转移速率增大[53,79]。当温度从18 ℃升至50 ℃时,海水的粘度从1.09×10-2 cm2/ s降低至0.451×10-2 cm2/s[53]。表明温度较高时,沙粒的运动受液体流动的影响较小,导致更多的沙粒撞击金属表面。此外,温度上升,热力学驱动力增大,金属的反应活性升高[10,53]。采用SEM观察发现,随着溶液温度上升,电极表面腐蚀区域范围扩大,裂缝和腐蚀点数目增多[35]。Tian等[16]研究石油运输过程中温度对X65钢腐蚀的影响发现,X65钢的自腐蚀电位随温度的上升而负移,且阳极极化电流密度随温度增高而迅速增大,表明阳极反应速率明显增大。
Ping等[80]研究了不同高温环境对17-4PH不锈钢在H2SO4介质中冲刷腐蚀行为的影响。结果表明,随着温度的升高,17-4PH不锈钢微观结构也随之改变,460 ℃时17-4PH不锈钢微观结构主要为马氏体, 610 ℃则包括马氏体和奥氏体。在温度由400 ℃上升到610 ℃过程中,材料硬度先随温度升高而增大,460 ℃时达到最大值,此时具有最佳的抗冲刷腐蚀能力。此后,材料硬度随温度上升而降低。
6.1.5 冲刷角 (攻角) 的影响 含沙流体中,流体冲刷作用对冲刷磨损影响较大[81]。流体冲刷角对冲刷腐蚀的影响主要表现为剪切应力和正应力。剪切应力通过削薄甚至移除钢表面的氧化膜而增强冲刷腐蚀过程。正应力则是通过撞击或损伤电极表面而产生孔洞。冲刷角小于45°时,剪切应力占主导地位;大于45°时,正应力占主导地位[11]。
Tang等[11]发现,冲刷角从30°增至45°时,腐蚀速率随冲刷角增大而增大,45°增至90°的过程中,冲刷腐蚀速率先随冲刷角增大而降低,然后随其增大而增大。邢建东等[78]研究了18-8不锈钢和T8高碳钢在含沙的低浓度H2SO4溶液流体中的冲刷腐蚀行为。结果表明,两种钢的冲刷腐蚀速率均在冲刷角为45°时达到最大。Sasaki等[82]研究发现,冲刷角较小 (50°) 时,易产生较粗糙的电极表面,与光滑的金属表面相比,表面点蚀坑更深且直径更小,因此粗糙表面更容易产生可以发展到正常生长阶段的点蚀坑,从而降低点蚀电势;冲刷角较大 (90°) 时,更容易发生点蚀。
邢建东等[78]认为金属材料在攻角约为45°时冲刷腐蚀速率达到最大,其主要原因是材料在此角度下的机械磨损达到最大值,从而使腐蚀与磨损的交互作用也达到最大值。因此,对于在这一角度下使用的材料,应注重提高其耐磨性。Heitz[83]研究发现,在液/固双相流冲刷腐蚀条件下,脆性材料冲刷腐蚀速率随颗粒冲刷角度的增大而增加,最大冲蚀率发生在90°,这一研究结果得到了Zheng等[56]的证实;延性材料则最大冲蚀率发生在攻角为15°~40°之间。
6.1.6 pH值、含氧量对冲刷腐蚀的影响 溶液的pH值不同,金属的冲刷腐蚀速率也不同。这是由于表面生成膜的成分及其性质不同所致。例如,在一定流速下当溶液pH值降低到3.6,在铜镍合金表面不能形成保护膜,耐冲刷能力降低。
有钝化特性的金属只有当介质中加入了足够的氧化剂,才能产生钝态。而不具有钝化特性的金属,O2的存在 (特别是在中性条件下) 将加速阳极金属的溶解。对铜合金而言,在脱氧的海水和淡水中,其腐蚀速率大为降低[72]。因此,在一定条件下O2的卷入会促进腐蚀,而在另一些条件下则有可能促进材料钝化,减缓腐蚀[16]。
6.1.7 环境因子的协同作用 条件参数之间的相互作用关系是十分重要的[33,53]。Meng等[10]采用正交实验和方差分析方法定量研究了不同环境参数及其相互作用对材料总失重的影响,采用的三因素水平分别为实验温度为20 和50 ℃,液体流速为7和20 m/s,沙含量为5×10-6和5×10-5 (质量分数)。
在同时考虑温度、流体速度和沙含量3个环境因素对材料冲刷腐蚀速率 (失重) 的影响时,得到各环境因素对腐蚀速率的贡献比重。例如,流速的贡献比重如下:
其中,V(%) 表示流速的贡献比重,SSV表示流速的影响,SSS为沙含量的影响,SST为温度的影响,SSVS为液体流速与沙含量的协同影响,SSVT为水流速率与温度的协同影响,SSTS为温度和沙含量的协同影响,SSTVS为三者的协同影响。
其中,
WHV和WLV分别为8次实验高、低流速时的材料失重平均值,WG为8种实验条件下材料失重的平均值。同样可以计算出其它6个环境因素的影响值。
运用该模型计算得到对UNS S31603不锈钢影响最大的环境因素为溶液流速,这与Luo等[76]的研究结果一致;然后是沙含量及其与溶液流速协同作用的影响;在高流速和高沙粒含量时,沙含量与溶液流速协同作用较强。上述协同作用并不仅仅受某个因素影响,当没有足够的撞击动力学能量时,脆性粗糙面不能移动,所以推测两者协同作用的迅速增加主要受临界撞击动力学能量的影响。
7 冲刷腐蚀的防护
7.1 金属元素含量及合金种类
7.1.1 元素含量 金属中特定元素的存在及其含量会对金属抗冲刷腐蚀能力产生很大的影响[53,84,85]。Meng等[10]研究发现,UNS S32654钢的耐冲刷腐蚀能力比UNS S31603钢强。这主要由于两种合金的元素含量不同 (表1),尤其是Cr,Mo和N的含量差异使得两种合金抗电化学腐蚀能力不同,从而使得耐冲刷腐蚀能力存在差异。Hu等[53]认为金属中C,Mo和N的添加可减慢电极表面去钝化时的溶解速率,因而表现出良好的再钝化性能。在静态海水溶液中,合金中Mo,N和Cr含量的升高对减小局部腐蚀有重要的作用。
表1 UNS S32654钢和UNS S31603钢中的元素组成[10]
研究[10,53,20,85-87]表明,合金中Mo,Ni和Cr等元素的含量对合金的抗冲刷腐蚀性能有较大的影响。
Wu等[88]研究含Mo不锈钢在H2SO4中的冲刷腐蚀机理时发现,Mo含量的增加能增强其抗电化学腐蚀及冲刷腐蚀能力。一方面,Mo与Cr具有相似的电子结构,金属活性较低,难以与介质形成复合物,同时阻碍了Fe与溶液中阴离子形成稳定的化合物;另一方面,不锈钢中Mo可消除电极表面的活性位点,形成含MoO42-或者Mo10O4110-的钝化膜或吸收腐蚀产物的膜,从而抑制点蚀的发生;此外,Mo含量的升高使得不锈钢由单相奥氏体向奥氏体与富Mo铁素体中间相转变,显微硬度增大,因而使得不锈钢抗冲刷腐蚀性能增强。合金中Mo和Ni的存在可加强电极表面钝化能力[53,85]。Ilevbare等[86]研究了不锈钢合金中Mo对合金性能的影响,认为Mo可能以钼酸盐的形式融入金属的氧化膜中,改变了氧化膜的离子选择性,使得Cl-难以通过;同时,Mo的存在可以增加电极表面钝化膜的厚度。
在金属基体中加入Cr后,由于形成更好的保护钝化膜、碳化物和硬沉淀,合金的抗冲刷腐蚀能力增强[20]。Barker等[87]研究了不同Cr含量钢的抗冲刷腐蚀能力,Cr含量8%以上的钢普遍具有马氏体、双相和亚稳奥氏体的混合结构,具有高加工硬化的潜力,有较强的抗冲刷腐蚀的能力。
Ni可以稳定不锈钢的奥氏体相进而增强电极表面的钝化能力[86]。王国华[89]通过对经过950 ℃,60 min时效处理的S31803和S32750钢的金相组织进行观察,发现含有22%Cr和3%Mo的S3180钢组织为α+γ,未发现σ相的析出;含有25%Cr和4%Mo的S32750钢组织除了α+γ,还有σ相。导致这样的结果是因为在双相不锈钢中提高Cr和Mo等铁素体形成元素的含量,既缩短了相形成的孕育期,同时提高了σ相稳定存在的上限温度。
7.1.2 合金种类 吴成红等[72]将金属的耐冲刷腐蚀性分为3类:(1) 金属如钛合金、镍合金在整个实验流速范围内表面能形成致密的保护膜,有很好的抗冲刷能力;(2) 不锈钢、镍铬合金在高速和中速范围内表面形成保护膜,有很好的抗冲刷能力,但在低速下不形成保护膜,抗冲刷能力较差;(3) 铜合金在低速下有很好的抗冲刷性,但在高速和中速下,其保护膜易被冲刷破坏。因此,针对不同的环境,选择不同的金属材料,可以减缓冲刷腐蚀。
7.2 热处理制度 (微观结构)
7.2.1 σ相 钢中γ相具有韧性好、形变强化能力高等特点,α相硬度也较低,σ相却具有较脆、硬度较高的特点。金属的耐磨性与硬度有很大的相关性[56]。双相不锈钢的温度和热处理时间会对钢中σ相的析出产生重要的影响[89]。研究人员通过对经850 ℃不同热处理时间的S31803双相不锈钢试样进行金相分析,发现时效初期5 min内没有σ相析出,随着时效时间的延长,σ相的体积分数升高,但析出速率逐渐减小。脆性σ相的析出,降低了双相不锈钢的塑性、韧性以及耐蚀性。
然而,耐蚀性和耐磨性很多情况下都是矛盾的[90]。Zheng等[91,92]的研究发现,由于σ相硬度较高,且与金属基体电化学性质接近,可以增强不锈钢的抗冲刷腐蚀性能。两种σ相增强的S1和S2不锈钢 (热处理温度和时间分别为850 ℃,5 h和950 ℃,8 h) 在10%H2SO4 (质量分数) 和15%含沙量及不同流速条件下冲刷72 h后发现,与316不锈钢相比,含较少量及较小尺寸σ相的S1钢仅在低流速时有较强的抗冲刷磨损性能,而σ相含量较高且尺寸较大的S2钢在所有流速下皆表现出较强的抗冲刷磨损性能。在冲刷磨损占主导地位的情况下,较小的冲刷磨损在很大程度上决定了材料具有较低的冲刷腐蚀总速率。
此外,材料的凝固速率能在很大程度上影响钢的主要组成元素在γ相与σ相之间的分布,进而影响其抗冲刷腐蚀性能[28]。
7.2.2 非晶态合金 电化学腐蚀弱化材料的晶界、相界,使材料中耐磨的硬化相暴露、突出基体表面,使之易折断甚至脱落,促进冲刷[31]。金属的非晶态不存在明显的晶界,有较高的硬度,金属表面喷涂无定型态金属能增强其在一定条件下的耐冲刷腐蚀性能[56,57]。急冷处理产生的骤冷合金相,因未能充分进行有序向无序转化,会冻结在按组成比形成置换式统计原子的无序状态,而形成非晶态合金。
Zheng等[56]采用高速氧燃热喷涂技术在304不锈钢表面喷涂Fe54.2Cr18.3Mo13.7Mn2.0W6.0B3.3C1.1Si1.4非晶态合金 (AMC),并对比了该涂层与304不锈钢在含沙的3.5%NaCl溶液中的冲刷腐蚀行为。研究表明,AMC在高流速冲刷条件下形成的钝化膜保护性能比304不锈钢更好。虽然304不锈钢的耐均匀腐蚀性能优于AMC,但是AMC抗点蚀能力远高于304不锈钢,其抗冲刷腐蚀性能更强,适合用于含Cl-较高的海水泵的冲刷腐蚀防护中。并认为,由于304不锈钢为晶体结构,晶界和相界首先发生腐蚀,引起表面颗粒和相的凸出,沙粒撞击电极表面将导致颗粒和相脱落。
7.3 硬质颗粒掺杂
陶瓷具有较高的硬度、耐磨、耐蚀、耐热和抗高温氧化性能,因此,合金中掺杂陶瓷粒子可以大大改善其耐磨损性能。硬质颗粒WC及TiC 作为硬质相掺入合金中使用较多,TiN 也有一些研究[93]。不同的硬质相在合金中表现出不同的性质。WC颗粒具有高强度、高润湿性能和低热膨胀系数[94],与铁基金属的润湿角为零,且与其它金属陶瓷颗粒(如TiC 等)相比易于获得,是目前广泛掺杂的粒子之一[95]。金属基体表面涂覆掺杂WC的合金涂层可大大改善金属基体耐冲刷腐蚀的能力[20]。WC颗粒可通过铸造、烧结等方法获得[95]。基体一般选择相对较软的金属材料,能保证较高的耐蚀性、良好的冲击韧性和断裂韧性[30]。
7.3.1 硬质颗粒掺杂对合金抗冲刷腐蚀能力的影响 Xu等[27]使用表面处理技术将纳米粒子SiO2和SiC掺杂在镍合金中,通过SEM观察掺杂的两种粒子对镍合金微观结构的影响,发现呈球状的SiO2均匀地分布在镍合金的奥氏体基体中,未与基体发生界面反应,处于化学惰性状态。而SiC则呈稍大的球状及较小的条状颗粒分布在晶界以及Ni的合金点阵中。在流速为3.45 m/s的3.5%NaCl溶液中冲刷一段时间后,发现316不锈钢失重质量是掺杂SiO2的镍合金的7倍;掺杂SiO2合金表面仅有少量的点蚀坑,无裂缝或孔洞,其抗冲刷腐蚀能力最强。合金中纳米粒子SiO2和SiC的掺杂可填补合金微观结构中的裂缝、沟及孔洞,同时由于纳米粒子能作为隔离缺陷、腐蚀萌生及扩大的物理屏障,掺杂后能增强合金的抗冲刷腐蚀能力。在流体中,纳米粒子SiO2由于与镍合金点阵键能较大,从而可以抵抗沙粒撞击时的“微观切断效应 (micro-cutting)”。
Neville等[15]研究发现溶液中沙粒粒径较大时,金属基复合材料抗冲刷腐蚀能力不一定优于不锈钢。含WC颗粒的镍合金与UNS S31603不锈钢的失重比在沙粒粒径比较大时约为2.8,而在沙粒粒径比较小时为0.6。观察两种沙粒的微观结构发现,粗沙比细沙形状更接近球形。细沙既可以划伤单独的WC颗粒,也可能撞击基体 (掺杂颗粒的粘合剂)。细沙颗粒划伤基体粘合剂相,WC颗粒抑制划痕的扩展,起到保护作用。粗沙在材料表面留下的划痕较细沙大,并且可以同时伤害金属基复合材料 (MMCs) 表面的两相 (WC颗粒和基体相),WC颗粒起不到抑制划痕发展的作用。与MMCs不同的是,UNS S31603不锈钢不含硬质相,微观结构主要为奥氏体,依靠晶界给材料提供保护力。当不锈钢在粗沙流体中冲刷腐蚀时,晶界为颗粒提供支撑,从而使材料强度提高,不会发生过于严重的腐蚀。此外,不锈钢在粗沙撞击时表现出较好的抗冲刷腐蚀的另一个原因是,粗沙粒撞击下不锈钢表面附近显微硬度变大,而在使用细沙撞击时并无此发现。Levin等[96]研究发现,冲刷撞击后,冲刷磨损表面下的材料会经历弹性变形,距表面一定距离地方的显微硬度会增强。
此外,温度较高时,因为电化学腐蚀作用,基体相的相对较快腐蚀导致WC颗粒不受保护,使金属腐蚀加剧[20]。
然而,Zheng等[91]指出,硬质颗粒掺杂并非适合于所有合金。碳化物与基体较大的电化学性质差异将导致较严重的相界晶间腐蚀,因而不适合用于强腐蚀性的介质中。
7.3.2 影响金属基复合材料抗冲刷磨损的因素 金属基复合材料抗冲刷磨损能力主要取决于材料的点阵韧性和材料中增强粒子的硬度,并与硬质相 (增强粒子) 的体积分数、尺寸和分布有关[26,94]。陶瓷粒子的独特性能使得金属基复合材料成为冲刷腐蚀环境下的良好选择[26,97]。设计金属基陶瓷颗粒掺杂材料的一个重要步骤是确定陶瓷颗粒之间的最佳平均自由程[26]。Cooper等[98]认为平均自由程较大时,材料强度变小;因为随着基体层变厚,陶瓷颗粒之间失去接触,强度取决于基体本身的微观结构。就抗沙粒磨损性能而言,硬质颗粒对粘结金属的“阴影保护效应”理论认为,金属陶瓷的抗磨粒磨损性能决定于复合层的硬质陶瓷颗粒间的距离。距离越小,则陶瓷相对粘结相的保护效应就越强,复合层越耐磨。然而,陶瓷相含量并非越高越好。因为过高的陶瓷相含量将降低陶瓷相颗粒与基体的结合强度,易于造成陶瓷相的剥落而失效。因此,针对各种技术工艺和使用情况,陶瓷相有其最佳含量[95]。
陶瓷颗粒尺寸对材料耐磨性也会产生重要影响。对掺杂WC硬质颗粒的合金而言,一般认为,在松散硬质磨料中,WC硬质合金的耐磨性随WC颗粒尺寸的减小而增加;而对于承受冲击载荷、对抗压强度要求高的各类工具,则一般选用韧性较好的粗颗粒[95]。此外,为了增强涂层的耐磨性能,可采用大小颗粒搭配使用的方法来减少硬质相的间距,加强大颗粒WC之间 (粘结金属) 的耐磨性,避免沙粒将基体磨损后又将硬质相撞出。在WC硬质合金的制备过程中,若WC颗粒烧损程度较低,则可尽量保持WC颗粒原始形貌,从而有效提高材料的耐磨性能,Xu等[27]的研究结果证实了这一点。
8 展望
(1) CFD软件建模。通过实验数据,建立系统的数据库,用统计的方法进行数据分析,可为未来冲刷腐蚀模型的建立提供指导方向,可以更加清楚地理解流速、沙含量以及温度等因素对合金腐蚀性能的影响。
(2) 新的测试方法的使用。传统冲刷腐蚀主要采用失重、极化曲线和EIS等方法研究环境因素对冲刷腐蚀的影响。有研究表明,声发射可测取材料局部腐蚀产生的超声弹性波,是研究高低温下腐蚀现象的强有力工具[71],预计能给出沙粒撞击频率和能量分布。根据声发射活动的强弱可以判断腐蚀的快慢。此外,可以使用先进的显微技术来研究冲刷腐蚀过程中材料力学性能的变化,构建不同变量之间的函数关系[38]。
(3) 耐冲刷腐蚀材料的发展。通过类似等离子喷焊 (PTA)、热喷涂、激光堆焊等耐磨堆焊技术,激光熔覆,铸渗等手段向合金掺杂纳米陶瓷颗粒,对材料表面进行改性处理,提高基体的抗冲刷腐蚀能力[20,27,95]。此外,金属表面喷涂添加了强化填充物的涂料,也可用于金属冲刷腐蚀的防护[76,99]。其中,涂料对材料冲刷腐蚀防护性能的影响与加工处理的温度及处理时间有关[99]。在实际冲刷腐蚀防护中,应根据腐蚀环境、介质性质、溶液流速等,综合考虑材料的耐蚀性和耐磨性,做出合适的选择。
参考文献
免责声明:本网站所转载的文字、图片与视频资料版权归原创作者所有,如果涉及侵权,请第一时间联系本网删除。
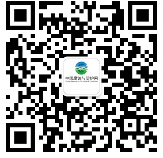
官方微信
《腐蚀与防护网电子期刊》征订启事
- 投稿联系:编辑部
- 电话:010-62316606
- 邮箱:fsfhzy666@163.com
- 腐蚀与防护网官方QQ群:140808414