半导体材料的发展经历了三个主要阶段。第一代半导体材料,如硅(Si)和锗(Ge),通过取代体积庞大的电子管,推动了晶体管和集成电路的发展,广泛应用于低电压、低频率和中等功率的器件中。第二代半导体材料,如砷化镓(GaAs)和磷化铟(InP),虽然具有更高的电子迁移率和更宽的带隙,但由于原材料的毒性和资源短缺,其发展受限,主要用于微波、毫米波和通信领域。第三代半导体材料,如碳化硅(SiC)、氮化镓(GaN)和氮化铝(AlN),凭借其出色的电子迁移率、耐辐射性、高击穿电压和优异的热导率,广泛应用于轨道交通、电网等高温、高频、高压和大功率的电子器件领域。
近年来,美国特斯拉率先大量采用碳化硅芯片,展现了这种材料在电动汽车领域的巨大潜力。
硅作为最常见的半导体材料,广泛应用于电子科学和光伏领域,特别是晶体硅在太阳能电池中的应用,其高光电转换率使其成为光伏领域的核心组件。单晶硅的制备主要采用直拉法(Czochralski法),这一方法以其高生产效率、可控的生长过程以及掺杂控制的优势,广泛应用于国内外的单晶硅生产。
第三代半导体材料因其独特的物理特性,在高温、腐蚀环境中具备良好的耐腐蚀性,但其制备过程中仍面临着严重的腐蚀挑战。例如,在硅单晶制备中,石墨组件暴露于硅蒸气中易被腐蚀,影响单晶质量和设备寿命。 为解决这些问题,研究者们开发了碳材料表面的耐腐蚀涂层,如热解碳(PyC)、碳化硅(SiC)和碳化钽(TaC)涂层,以提高碳材料在高温腐蚀环境中的使用寿命。这些涂层在半导体制造过程中表现出优异的防护效果,成为碳材料保护的关键手段。 硅化腐蚀 01 热解碳涂层的硅化腐蚀
Cao等研究了用于单晶硅炉中的碳材料(G330石墨和AC200 C/C复合材料)的硅化腐蚀。结果表明,从石墨内部延伸至表面的开口孔隙为熔融硅的侵蚀和扩散提供了通道,这加速了碳材料的硅化过程,硅化腐蚀深度超过1.5毫米,如图2a和2b所示。因此,有效地封闭这些开口孔隙对于抑制熔融硅的扩散至关重要。图2c和2d显示了硅化腐蚀对C/C复合材料中纤维取向的影响。沿纤维方向的硅扩散速度比垂直纤维方向的扩散速度更快。
图2 G330石墨和AC200 C/C复合材料硅化腐蚀后的形貌
02 碳化硅涂层的硅化腐蚀
Jiang等提出了一种用于Czochralski单晶硅的石墨导管基体增强和表面涂层的制备方法。该方法包括在石墨导管表面均匀涂覆一层碳化硅浆料,然后在高温炉中进行原位反应,最终形成厚度为3050微米的碳化硅涂层。反应温度为1850~2300 ℃,保温时间为26小时。之后,使用CVD方法进行沉积,沉积时间为1020小时。经过处理的碳化硅涂层导管可以在1500 ℃的单晶环境中使用1500小时,而不会出现表面裂纹或粉化现象。
03 碳化钽涂层的硅化腐蚀
Nakamura等使用湿法粉末工艺,在石墨表面制备了厚度约为100微米的碳化钽(TaC)涂层,并在CVD工艺中对SiC晶体进行测试。测试结果表明,经过腐蚀处理后,TaC涂层表现出良好的抗腐蚀性能,没有发生涂层剥落或裂纹现象,表明TaC涂层石墨基材能够在高纯度且厚的CVD SiC晶体外延生长过程中有效应用。
Nakamura等还计算了基材与TaC涂层的热膨胀系数,并选择了与TaC涂层热膨胀系数匹配的石墨材料,使用湿法粉末烧结成型技术制备了大尺寸的TaC涂层坩埚。在晶体硅炉中经过3次评估后,发现坩埚表面未出现明显的损坏,表明TaC涂层能够有效延长设备的使用寿命。
氨腐蚀 01 热解碳涂层的氨腐蚀
Chollon等在纯氨气(NH3)环境中处理了石墨上的热解碳涂层,氨气流速为400 sccm,压力为10 kPa,最高温度为1095 ℃。在涂层破损并暴露石墨基材之前,没有观察到显著的质量损失,这时石墨基材才开始与氨气发生反应。当多晶石墨基材暴露并在相同条件下处理时,900 ℃以上温度下发生了明显的持续质量损失,这与相关研究一致。
此外,研究还对高度取向热解石墨(HOPG)进行了相同条件下的测试,直到1095 ℃之前未检测到化学反应。这表明氨气的腐蚀行为与碳晶体的取向密切相关。在各向同性的石墨材料中,氨腐蚀行为明显,而在各向异性的石墨材料中,氨气腐蚀的影响显著降低。然而,晶粒取向对抗氨气腐蚀的具体影响尚未被充分研究。
02 碳化硅涂层的氨腐蚀
图6 SiC涂层在NH3腐蚀后的表面形貌
03 碳化钽涂层的氨腐蚀
Nakamura等在石墨表面制备了一层厚度为100微米的碳化钽涂层,并使用该涂层作为MOCVD氮化镓(GaN)晶体外延生长的石墨基材,基材尺寸为φ58 mm×19.5 mm。氨气和氢气等腐蚀性气体在1030 ℃和40 kPa的压力下被引入反应腔体,腐蚀时间为60分钟。图7a和7b显示,除在边缘区域沉积了一层外,碳化钽涂层在GaN晶体外延生长过程中并未受到明显的腐蚀损伤。
氯气腐蚀 01 氯气对热解碳涂层的腐蚀
02 氯气对碳化硅涂层的腐蚀
Wang等在直径220毫米的石墨环表面制备了碳化硅涂层,并在900 ℃下使用特制的氯气炉对涂层进行了两组40小时的腐蚀测试,氯气的流量分别为30 mL/min和60 mL/min。氯气会严重腐蚀碳化硅涂层,反应式为:SiC+2Cl₂=SiCl₄↑+C。
03 氯气对碳化钽涂层的腐蚀
Daisuke等提出了一种在石墨基材上制备超厚(50~200微米)碳化钽(TaC)保护涂层的生产技术,该技术包括碳化钽浆料涂覆及随后的烧结过程。经过烧结后,TaC涂层表现出致密的颗粒结构,没有裂纹或孔洞。
图9 TaC涂层在AlN外延生长过程中的耐腐蚀性能
其他环境 01 氯气和空气混合物对碳化硅涂层的腐蚀
Vogel等使用了一种新的方法,利用纳米傅里叶变换红外光谱(nano-FTIR)技术来分析各种碳化硅保护层的腐蚀耐受性。研究表明,碳含量高的碳化硅涂层和硅含量高的碳化硅涂层在1000 ℃下分别暴露于50%氯气和空气的混合气体中12小时后,氮含量高的碳化硅涂层表现出更好的抗腐蚀性能。氮化硅氧 (SixNyO)保护层的形成可能降低了氯气向碳化硅涂层扩散的速率,从而赋予了更高的耐腐蚀性。
02 氯三氟化物对碳化硅颗粒的腐蚀
目前,使用氯三氟化物(ClF3)清洁反应器的技术已应用于碳化硅的化学气相沉积(CVD)方法中。然而,常见的用于半导体的防腐蚀涂层,如碳化钽(TaC)和碳化硅(SiC),在高温和高浓度的氯三氟化物中无法有效抵抗腐蚀。研究表明,纯化的热解碳膜可以将耐腐蚀极限温度从480 ℃提高到570 ℃。
在实验中,研究人员使用了纯化的热解碳涂层来保护反应器基体,并随后对碳化硅颗粒进行CVD沉积,最后进行氯三氟化物清洁实验。实验结果表明,残留的碳化硅颗粒被有效清除,而热解碳涂层在清洁后仍保持完好。
结论与展望 本文评估了热解碳(PyC)、碳化硅(SiC)和碳化钽(TaC)涂层在硅蒸气、氨气、氯气等环境中的耐腐蚀性能。 研究表明,气固反应在涂层的耐腐蚀过程中起关键作用,CVD制备的高纯度致密材料表现出良好的耐腐蚀性能,但不同微观结构与腐蚀性能的关系研究仍不充分,CVD涂层中的残余应力对耐腐蚀性能的影响也有待进一步研究。 目前,防腐蚀涂层的研究仍处于初期阶段,未来需关注降低成本、增强防护效果、延长设备使用寿命,以及探索涂层的修复技术。继续推进这些研究将有助于满足半导体行业不断发展的需求。
免责声明:本网站所转载的文字、图片与视频资料版权归原创作者所有,如果涉及侵权,请第一时间联系本网删除。
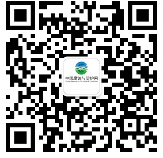
官方微信
《腐蚀与防护网电子期刊》征订启事
- 投稿联系:编辑部
- 电话:010-62316606
- 邮箱:fsfhzy666@163.com
- 腐蚀与防护网官方QQ群:140808414