条件编号 | 温度/℃ | CO2分压/MPa | 搅拌线速率/(m·s-1) |
---|---|---|---|
1 | 50 | 0.30 | 1.5 |
2 | 100 | 0.63 | 1.5 |
3 | 114 | 0.73 | 1.5 |
CO2腐蚀易引发井下管柱失效,降低油气井的使用寿命,给油气工业带来巨大经济损失[1-2]。深入研究油套管钢的腐蚀行为对井筒优化选材和安全生产至关重要。低铬钢(Cr质量分数1%~5%)的成本仅为普通碳钢的1.5倍,但耐蚀性比普通碳钢提升3~40倍[3-5],因此受到了众多科研学者的广泛关注。尽管低铬合金钢在这一领域的研究取得了一些进展,但仍存在一些热点问题尚待澄清。
首先,关于低铬钢的最佳Cr含量仍存在争议。不少研究人员认为增加0.5%~1.0%(质量分数,下同)的Cr可防止严重的台地状腐蚀[3,6-8]。GUO等[9]提出当钢中Cr质量分数达到2%时,连续且具有韧性的无定形层会覆盖整个试样表面,可以消除局部腐蚀。另有学者[10-14]发现,在3Cr钢中,Cr会导致含铬化合物与FeCO3在钢中竞争沉积,形成结构致密且富铬的FeCO3腐蚀产物膜。陈长风等[15-17]认为含4%Cr的N80钢的腐蚀产物膜由非晶态的Cr7C3、Cr2O3和FeCO3组成。UEDA等[18]发现,含4%~5%Cr的钢经24 h浸泡后,其腐蚀产物膜中的铬含量可达到钢基体中的10倍,且试样呈均匀腐蚀形态,无点蚀发生。
其次,对于低铬钢的最佳适用临界条件仍未明确。GUO等[9,13,19]研究了低铬合金钢在CO2环境中的腐蚀行为,结果发现:1Cr钢发生轻微点蚀,2Cr钢表面的条状晶皮可能引起局部腐蚀,3Cr、5Cr钢均呈现均匀腐蚀形态。任永峰等[20]发现在常温常压的CO2环境中,3Cr钢的耐腐蚀性能大大优于碳钢。陈长风等[8,16,21-26]研究发现:在含CO2井筒环境中,N80钢发生严重点蚀,含1%Cr钢的腐蚀速率较N80钢低,但仍存在点蚀行为;而含4%~5%Cr钢呈现均匀腐蚀。孙建波等[27-28]研究发现,在CO2环境中X65钢发生了严重的台地状腐蚀和局部孔蚀,1Cr钢存在尺寸均匀的蚀坑,3Cr钢表面未见孔或蚀坑,5Cr钢表面光滑平整。
目前,普遍认为低铬油管钢在各类腐蚀环境中的耐蚀性优于普通碳钢。但也有学者认为,添加Cr元素并未改善钢材的耐蚀性[10,28-29]。因此,作者基于陆上某油田区块的井筒腐蚀环境与防腐蚀选材问题,在含CO2井筒环境中对低铬钢1Cr和碳钢N80的腐蚀行为进行了研究。
1. 试验
1.1 材料与试样
试验选用低铬钢1Cr作为目标材料,对比材料为普通碳钢N80。N80钢密度为7.856 g/cm3,1Cr钢密度为7.757 g/cm3。试样尺寸为25 mm×10 mm×3 mm,一端带有直径为6 mm的圆孔。试样经过金相磨抛机逐级打磨,清洗后通过冷风干燥处理,分别用游标卡尺和分析天平测量试样的尺寸和质量。然后,将试样装载至聚四氟乙烯挂架,并置于高温高压动态反应釜中进行试验。每种材料制备3个平行试样。
1.2 动态腐蚀试验
某油田区块垂深井筒温度分为中温、中高温及高温。根据陆上某油田区块垂深井筒温度,在反应釜中模拟地层水(4 000 mg/L Cl-)腐蚀环境对1Cr钢和N80钢试样进行动态腐蚀试验,试验时间为72、168、336 h,具体条件见表1。模拟地层水由NaCl和去离子水配制。
将模拟地层水加入反应釜并浸没腐蚀试样,关闭反应釜。先向反应釜中通入超纯氮气(10 h),然后通入CO2(2 h)。随后,升温至预设温度,并加压至试验设定条件开始试验。
试验完成后,将试样彻底干燥,分析产物膜成分,再进行清洗、称量。清洗过程按照ASTM G1-2003《腐蚀试样的制备、清洁处理和评定用标准实施规范》进行。根据失重法计算腐蚀速率,如式(1)所示。
|
(1) |
式中:vcorr为试样的腐蚀速率,mm/a;Δm为试样腐蚀前后的质量差,g;ρ为试样的密度,g/cm3;A为试样暴露面积,cm2;t为浸泡时间,h。
1.3 微观表征
采用TM-3030型台式扫描电镜、QUANTAX-70型能谱仪(EDS)分析了腐蚀产物膜的形貌和元素组成。采用激光扫描共聚焦显微镜(CLSM)观察清洗后试样表面的点蚀形貌。
2. 结果与讨论
2.1 腐蚀速率
图1为三种腐蚀条件下N80钢和1Cr钢的平均腐蚀速率。由图1可见,随着时间的延长,两种材料的腐蚀速率均呈现明显的递减趋势。在50 ℃、0.30 MPa CO2分压下(条件1),N80钢的腐蚀速率高于1Cr钢,这说明添加Cr元素可显著降低了钢的腐蚀速率。
2.2 腐蚀产物膜
图2为三种腐蚀条件下腐蚀336 h后N80钢和1Cr钢腐蚀产物膜的SEM图,表2为腐蚀产物膜的能谱分析结果。
材料 | 温度/℃ | ![]() |
质量分数/% | |||
---|---|---|---|---|---|---|
Fe | O | C | Cr | |||
N80 | 50 | 0.30 | 46.5 | 42.7 | 10.3 | - |
1Cr | 50 | 0.30 | 44.1 | 43.9 | 10.2 | 1.8 |
N80 | 100 | 0.63 | 48.6 | 40.2 | 10.6 | - |
1Cr | 100 | 0.63 | 50.2 | 37.6 | 9.1 | 2.4 |
N80 | 114 | 0.73 | 46.2 | 38.7 | 12.3 | - |
1Cr | 114 | 0.73 | 45.9 | 36.1 | 13.7 | 2.1 |
在50 ℃、0.30 MPa CO2分压下(条件1),N80钢表面形成了少量的晶体状堆垛,见图2(a),这些堆垛镶嵌或覆盖于内层膜之上。能谱分析结果表明,腐蚀产物膜的组成元素主要是Fe、C和O,且O元素的含量约为Fe元素的3倍,腐蚀产物膜的成分为非晶态的FeCO3。1Cr钢表面除了形成少量的FeCO3晶体状堆垛外,暴露的产物膜呈现开裂的特征,见图2(b)。腐蚀产物膜的组成元素为Fe、O、Cr和C,其铬含量远高于钢基材,表明在CO2腐蚀环境中,低铬钢的腐蚀产物膜呈现出FeCO3和Cr(OH)3两相混合结构。部分FeCO3在弱酸性环境中发生溶解,反应如式(2)所示,导致腐蚀产物膜中Cr(OH)3的含量占比逐渐增加,从而使腐蚀膜的韧性、完整性和致密性增强,并呈现一定程度的富铬特征。
|
(2) |
在较高温(100、114 ℃)和较高CO2分压(0.63、0.73 MPa)下(条件2和3),两种材料的表面均形成了一定程度的FeCO3晶体状堆垛。N80钢最外层的FeCO3膜层覆盖完整、堆砌致密、无明显的孔隙;1Cr钢的外层膜晶体堆垛间隙较大,部分次外层的产物膜未被完全覆盖。由于腐蚀产物膜强度不够,被流体流动产生的剪切力剥离了基体表面,或是非晶态Cr(OH)3产物膜对阳离子选择性透过阻碍了由金属基体阳极溶解生成的Fe2+向外迁移,在部分表面腐蚀产物未来得及沉积形成致密的膜层。
在50 ℃、0.30 MPa CO2分压下(条件1),碳钢表面的晶态产物膜并非抑制腐蚀的主要因素,其内层致密的非晶态FeCO3膜层才是降低腐蚀速率的关键。低铬钢的腐蚀速率很大程度上受FeCO3和Cr(OH)3共同沉积形成的胶泥状混合产物膜控制,致密的混合产物膜对金属基体起到了很好的保护作用。在高温和较高CO2分压下,N80钢的表面可形成致密的晶态FeCO3产物膜,有效阻碍了金属基体与腐蚀介质之间的传质过程,抑制了腐蚀的进一步加剧。然而,1Cr钢在该环境中也不能免受腐蚀,其腐蚀产物不致密,与基体的附着力较弱,在流体剪切应力作用下产物膜从基体表面剥离,造成了材料表面的产物膜不完整,降低了1Cr钢的耐蚀性。
图3是不同腐蚀条件下N80钢和1Cr钢表面腐蚀产物的XRD谱。由图3可见,N80钢表面腐蚀产物主要成分是FeCO3,物相匹配结果对应其特征峰24.7°、32.0°、52.6°和69.3°,与图2的分析结果相吻合。在1Cr钢表面腐蚀产物中除了检测到FeCO3外,还检测到一定量的Cr7C3,物相匹配结果对应其特征峰39.1°和61.3°。50 ℃下Fe的特征峰较强,分别对应44.6°和65.0°;其他峰较弱,还含有少量的FeCO3腐蚀产物,这说明此时试样的腐蚀较轻。
2.3 点蚀形貌
图4是三种腐蚀条件下N80钢和1Cr钢的宏观腐蚀形貌。由图4可见,在50 ℃、0.30 MPa CO2分压下,N80钢和1Cr钢均呈现明显的点蚀形貌。对两种材料表面的点蚀形貌进行评价,结果见图5和图6。
N80钢表面出现较多的大尺寸半球状点蚀坑,见图5(a)。其中最大点蚀坑(除边缘部分)的开口深度和宽度分别达到712.51 μm和329.04 μm,见图6(a)。相比之下,1Cr钢表面的点蚀程度相对较轻微,见图5(b),最大点蚀坑深度和宽度分别为506.88 μm和131.87 μm,见图6(b)。通过点蚀特征分析可知,1Cr钢的点蚀密度、点蚀尺寸和点蚀敏感性均较N80钢有显著降低,耐蚀性较好。
在较高温(100、114 ℃)和较高CO2分压(0.63、0.73 MPa)下(条件2和3),N80钢表面整体呈现均匀腐蚀特征,平整度较好,见图4(b,c),但仍存在极少量较深的点蚀坑,见图7(a,c)。这些点蚀坑的形成原因如下:腐蚀产物未能有效地抑制腐蚀作用,蚀坑内的金属溶解产生过剩的金属阳离子(Fe2+),使蚀坑周围的Cl-向内迁移以保持电平衡;Cl-的积聚引发了酸化自催化反应,进一步加剧了点蚀发展。对于1Cr钢的腐蚀形貌分析显示,相较于试样打孔位置,金属基体表面被腐蚀掉较厚一层,呈现明显的台阶状。这是由于均匀腐蚀速率远大于点蚀速率。结合微观点蚀分析结果可知,1Cr钢的耐点蚀性能比N80钢有一定程度的提升。台地状腐蚀可归因于最初形成的点蚀坑。由于点蚀坑内富集了腐蚀产物Cr(OH)3,点蚀坑内的电位升高,比蚀坑周围区域电位更正,形成大阳极、小阴极的腐蚀环境,促进了周围区域发生阳极溶解,最终演化发展为台地状腐蚀。
2.4 讨论
Fe和Cr元素均属于较活泼的金属,且Cr元素的活性比Fe元素高,因此N80钢和1Cr钢的阳极反应主要如式(3,4)所示。随着腐蚀反应的进行和离子的迁移,在金属基体附近的滞流层中发生的反应如式(5,6)所示,当FeCO3和Cr(OH)3的离子积K大于溶度积常数Ksp时,它们便在试样表面沉淀成膜。
|
(3) |
|
(4) |
|
(5) |
|
(6) |
在水溶液中,FeCO3的溶度积常数为3.2×10-11,Cr(OH)3的溶度积常数为6.3×10-31[30],因此1Cr钢的腐蚀产物Cr(OH)3具有更好的稳定性。这也是在中温较低分压下,1Cr钢耐蚀性优于N80钢的一个主要原因。另一方面,低铬钢在CO2环境中的腐蚀产物膜是由晶态的FeCO3外层和连续的、具有韧性的胶泥质不定形态Cr(OH)3内层构成[8,21,22,27,31],Cr(OH)3腐蚀产物膜具有阳离子选择透过性,抑制了式(3)所示阳极反应。综合以上原因,所以低铬钢1Cr在中温环境中表现出出色的耐蚀性。
在较高温度和较高分压条件下,两种材料耐蚀性能发生逆转可以从两个方面解释。首先,较高温度时,式(4)所示反应的活化能降低,这降低了N80钢形成产物膜的势垒,使腐蚀减缓[20,29]。同时,高温有助于改善产物膜的致密性和稳定性,减少局部腐蚀的风险,提高金属基体的表面平整度,从而降低均匀腐蚀速率,与本试验结果相符。其次,在高温高压的CO2环境中,温度影响了电化学反应过程和产物膜结构,使得腐蚀产物膜的稳定性和结合强度降低[20,29],腐蚀产物膜结构疏松,在流体剪切应力的作用下被剥离,暴露出新鲜的金属基体。此时在大阴极、小阳极的电偶效应催化作用下,形成最初的点蚀缺陷,并随着点蚀发展,形成台地状腐蚀特征。此外,高温容易使低铬钢从半钝化状态转为活化状态,且活化状态下含Cr低合金钢的腐蚀程度较碳钢更为严重[32,33]。因此,综合以上原因,低铬钢1Cr的腐蚀速率会高于碳钢N80。由此可见,1Cr钢的耐CO2腐蚀适用范围需进一步明确。
3. 结论
(1)在高温和高CO2分压条件下,N80钢表现出比1Cr钢更强的耐蚀性。N80钢能迅速形成致密和完整的腐蚀产物膜,提高其耐局部腐蚀性,减小表面粗糙度,从而扩大碳钢的应用范围。然而,在实际应用中,可能需要适当增加壁厚,以平衡强度和经济性的考量。
(2)在高温高压环境中,尽管1Cr钢形成了富铬的无定形产物膜,但由于最外层FeCO3层不完整,其耐蚀性受到限制,导致其耐蚀性能不如N80钢。
(3)在低温和低CO2分压条件下,由于产物膜中的Cr(OH)3更稳定,且低温减缓了FeCO3的形成速率,1Cr钢相对于N80钢表现出更好的耐蚀性。
(4)腐蚀产物膜的组成和特性是控制材料耐腐蚀性的主要因素。研究特定腐蚀条件下的成膜机理,有助于选择合适的防腐蚀材料。1Cr钢在井筒浅部的环境中具有优越性能;然而,在井筒深部不推荐使用该钢材,需要谨慎选择适当的材料。
免责声明:本网站所转载的文字、图片与视频资料版权归原创作者所有,如果涉及侵权,请第一时间联系本网删除。
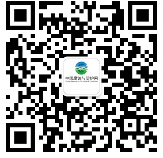
官方微信
《腐蚀与防护网电子期刊》征订启事
- 投稿联系:编辑部
- 电话:010-62316606
- 邮箱:fsfhzy666@163.com
- 腐蚀与防护网官方QQ群:140808414