试验材料 | 质量分数/% | |||||
---|---|---|---|---|---|---|
WS2 | Al | Ni | Fe | Mn | Cu | |
C13W | 13 | 5 | 5 | - | - | 余量 |
AlCu | - | 9.8 | - | 2.9 | 1.5 | 余量 |
海洋装备是实现海洋强国战略的重要基础和支撑,在“十四五”规划和2035年远景目标中被列为重点发展领域。随着海洋资源的开发和利用,海洋装备面临着比陆地环境更为苛刻的服役条件,海洋装备中的一些关键摩擦副零部件如轴承、衬套、阀、齿轮和螺旋桨,必须直接在海水中工作[1]。在海水中,摩擦运动对材料腐蚀具有不可忽视的加速作用,而腐蚀的加剧又会增加材料磨损,最终形成磨损与腐蚀交互作用,这是海洋装备运动部件面临的一个重大的难题[2-4]。海洋装备的使用寿命和安全性很大程度上取决于体系各部件在海水环境中的腐蚀磨损情况,因此,研究海水环境中材料的摩擦行为具有重要意义。
腐蚀磨损一般是指发生在腐蚀介质中的磨损现象,是力学因素、化学因素、电化学因素以及它们交互作用的结果,腐蚀的存在使得摩擦学的研究变得复杂。海水中的Cl-会腐蚀材料并加剧其磨损[5]。国内外学者对腐蚀介质中金属材料的摩擦行为进行了大量的研究[6-9]。但是,关于自润滑材料在腐蚀介质中腐蚀磨损的研究较少。为此,作者采用放电等离子烧结技术制备了铜基自润滑复合材料(以下称C13W),研究了海水浸润条件下该自润滑材料的摩擦磨损性能,并与AlCu合金(以下称AlCu)进行了对比,期望为此材料在海洋环境中的应用提供理论基础。
1. 试验
1.1 试验材料
将铜粉(48 μm、纯度≥99%),WS2粉(0.58 μm、纯度≥99%),镍粉(48 μm、纯度≥99%)和铝粉(48 μm、纯度≥99.5%)按表1所示C13W的配比称量后,放入行星球磨机进行混合,球磨机转速为300 r/min,混料时间为8 h。将混合好的粉末装入HPD-250-C型系统石墨模具中进行烧结。烧结条件如下:系统真空度为10 Pa,烧结压力为30 MPa,升温速率为50 ℃/min,烧结温度为900 ℃,保温时间为20 min。随炉冷却至150 ℃得到直径40 mm、高度30 mm的圆柱状C13W试样。通过质量分数计算得到C13W的理论密度为7.863 g/cm3,而通过阿基米德方法测试得到其实际密度为7.744 g/cm3,C13W试样的致密性可达到约98.5%。AlCu为市购商用铸造合金,其化学成分见表1。
1.2 摩擦磨损试验
采用HSR-2M型高速往复摩擦试验机在空气(干摩擦)和海水(浸润)中进行摩擦磨损试验。用人工海水模拟海水环境,其化学成分为25 g/L NaCl、11 g/L MgCl2·6H2O、8 g/L MgSO4·7H2O、1.2 g/L CaCl2,pH为7~8,呈弱碱性。通过注射滴管滴加方式添加海水,滴加速率为50滴/min。将C13W和AlCu制成20 mm×15 mm×3 mm的测试试样,用SiC砂纸逐级(至1200号)打磨并抛光试样表面。摩擦副为ϕ6 mm的SiN球。摩擦磨损试验前,对摩擦副和试验件进行超声波清洗。试验条件如下:载荷10 N,往复速率300次/min,划痕长度5 mm,试验时间20 min。试验所得摩擦因数、磨损量为三次重复试验的平均值。
1.3 表征
利用X射线衍射仪(XRD)对制备的C13W进行物相分析,扫描速率为0.5(°)/s。利用场发射扫描电镜(SEM)观察C13W和AlCu在海水浸润前后的微观形貌,明确金属基体和固体润滑相的结合情况和反应情况;同时采用扫描电镜观察试样摩擦磨损后表面形貌,测量磨痕宽度,计算磨损速率。
2. 结果与讨论
2.1 物相结构
图1为C13W的XRD谱。从图1中可以看出,C13W中主相是Cu,同时检测到W、Cu2S、WS2和NiAl的衍射峰,这说明在烧结过程中Cu和WS2发生了界面反应,反应方程式如(1)所示。
|
(1) |
2.2 表面形貌
由图2可以看出,在海水浸润前后,C13W表面形貌变化不大,均为网状结构。结合XRD分析结果可确定,亮色区域为W/WS2,灰色区域为Cu,黑色部分为Cu2S。这说明在C13W烧结过程中,WS2发生了分解反应,生成了单质W和Cu2S,Cu2S和未分解的WS2都具有润滑作用,可以提高润滑效果,缓解材料磨损。Cu2S的形成能在一定程度上减少样品烧结过程中孔洞的形成,而且能够提高样品的硬度和强度[10-11]。而AlCu表面经过海水浸润后变化较大,原始表面灰色区域为Cu,黑色区域为富Al相;经过海水浸润后富Al相发生了腐蚀,表面出现不规则片状结构,表面变得粗糙,无明显小孔。
图3是两种材料在空气和海水环境中摩擦磨损后的表面形貌。由图3可见,在空气中摩擦磨损后,C13W和AlCu表面遭受了严重的挤压,发生了明显的塑性变形,表面分布着许多擦伤痕迹和犁沟。这表明二者在空气中干摩擦的情况下主要发生黏着磨损和磨粒磨损。但AlCu表面的磨痕宽度大于C13W表面,且存在擦伤撕裂的痕迹。在海水中摩擦磨损后,C13W和AlCu表面磨痕较为光滑,出现了不同大小的犁沟,这表明二者在海水浸润条件下的磨损机理主要为磨粒磨损。其中,C13W磨痕内部表面较为平整,AlCu磨痕内部表面犁沟清晰,与C13W相比,AlCu表面犁沟的深度和宽度都有所增加。富铝区域存在腐蚀产物膜,使硬质磨屑颗粒的尺寸增大,从而导致AlCu表面犁沟加深、变宽。
2.3 摩擦磨损性能
图4显示了两种材料的摩擦磨损性能。由图4(a)可见,在空气中干摩擦条件下,两种材料起始的摩擦因数相当,均为0.35左右;随着时间的延长,AlCu的摩擦因数逐渐升高,平均摩擦因数为0.458,而C13W的摩擦曲线较为平缓,平均摩擦因数为0.404。由图4(b)可见,在海水浸润条件下,两种材料的摩擦因数差异较大。二者在起始阶段的摩擦因数均小于干摩擦条件下的摩擦因素,但随着时间的延长,AlCu的摩擦因数迅速增大,最终稳定在0.472左右,大于其在干摩擦条件下的摩擦因素,而C13W的摩擦因数随时间的变化较小,一直稳定在0.220左右。在海水浸润条件下,摩擦副之间会形成一层润滑水膜,使得C13W的摩擦因数由干摩擦条件下的0.404减小到海水浸润条件下的0.220。由于AlCu表面存在海水,富铝区域发生腐蚀,表面粗糙度大幅增大,海水的润滑作用急剧下降,因此与干摩擦条件相比其摩擦因数反而增大。
表2为C13W和AlCu在空气和海水中的磨痕宽度,根据磨痕宽度计算[12]得到磨损率,计算公式见式(2),结果见图5。
|
(2) |
式中:W为磨损率;d为对磨副球直径,6 mm;t为摩擦时间,20 min;h和L分别为磨痕的长度(划痕长度5 mm)和宽度;F为载荷,10 N;v为往复速度,300次/min。
材料 | 磨痕宽度/mm | |
---|---|---|
空气 | 海水 | |
C13W | 0.411 | 0.333 |
AlCu | 1.014 | 0.495 |
从图5中可以看出,两种材料在海水浸润条件下的磨损率比在干摩擦条件下的磨损率均大幅度降低,C13W的磨损率由干摩擦条件下的3.22×10-5 mm3/(N·m)降到海水浸润条件下的1.71×10-5 mm3/(N·m),AlCu的磨损率由干摩擦条件下的29.63×10-5 mm3/(N·m)降到海水浸润条件下的5.70×10-5 mm3/(N·m)。这归因于具有一定黏度的海水,海水作为一种天然的润滑剂,在磨损过程中起到一定润滑作用[13],减小了摩擦副间的剪切作用,避免了黏着磨损的发生;同时摩擦过程中产生的热量被海水带走,使材料冷却,抑制了材料表面黏着磨损的发生,从而缓和了材料的磨损。从两种材料表面的摩擦磨损形貌也可看出,在海水浸润条件下,试样表面均无磨粒存在,并且磨损表面的犁沟数量和深度均有所减小,材料磨损率减小。
3. 结论
(1)经过海水腐蚀,铜基复合材料C13W表面形貌变化不大,AlCu表面富铝区域发生腐蚀,表面变粗糙。
(2)与干摩擦条件比,在海水浸润条件下C13W的摩擦因数明显下降,由0.404下降至0.220,而AlCu的摩擦因数在两种条件下的变化不明显,由0.458升高到0.472。
(3)在海水浸润条件下,两种材料的磨损率比在干摩擦条件下均大幅度降低,C13W的磨损率由干摩擦条件下的3.22×10-5 mm3/(N·m)降到海水浸润条件下的1.71×10-5 mm3/(N·m),AlCu的磨损率由干摩擦条件下的29.63×10-5 mm3/(N·m)降到海水浸润条件下的5.70×10-5 mm3/(N·m)。
免责声明:本网站所转载的文字、图片与视频资料版权归原创作者所有,如果涉及侵权,请第一时间联系本网删除。
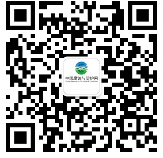
官方微信
《腐蚀与防护网电子期刊》征订启事
- 投稿联系:编辑部
- 电话:010-62316606
- 邮箱:fsfhzy666@163.com
- 腐蚀与防护网官方QQ群:140808414