硝基苯是重要的有机化工原料,广泛应用于农药、染料、医药、橡胶等领域,但同时也被世界卫生组织国际癌症研究机构列入致癌物清单,属于优先控制的环境污染物[1-6]。现有的硝基苯生产工艺在生产过程不可避免会产生含有硝基苯的废水[7],而硝基苯废水具有微生物抑制性高、氨氮含量高、色度高等特点,是工业污水处理难题之一[8-12],因此硝基苯废水处理长期处于高投入、低效益的困局。
近年来,随着国家环保要求的日益严格及煤气化装置运行水平的提升,利用水煤浆技术协同处理废水,即将化工废水代替常规工业用水制备水煤浆,逐渐成为越来越多煤化工企业在环保政策下的新选择[13-16]。该技术既节约了工业用水又解决了废水处理问题,是一种普适性较强、经济性较好、操作流程简便的高效技术手段。但由于化工废水的物性不同及来源不稳定,煤浆制备系统稳定运行的不确定性因素增加,设备管道的腐蚀控制成为影响装置长周期运行的关键因数。某企业自从将硝基苯废水引入煤浆制备系统后,棒磨机腐蚀、跑浆漏浆问题频发,非计划停工次数增加,给整个气化装置的安稳运行带来较大挑战。因此,针对煤浆制备系统的腐蚀问题开展全面深入的研究,对于保障煤气化装置的“安稳长满优”运行及推进化工废水资源利用具有十分重要的意义。
1. 现场腐蚀调研
1.1 腐蚀情况
某企业煤化工部共有五台湿式溢流型棒磨机设备投入生产运行。其中,合成氨单元有两台,分别是H3101A、H3101B;制氢单元有三台,分别是X5201A、X5201B、X5201C(备用)。煤浆制备系统的工艺流程见图1。原料煤经给料机称量后送入棒磨机,同时按比例加入添加剂、工艺水,经钢棒的研磨后制成合格的水煤浆;水煤浆经低压、高压煤浆泵送至气化炉。自2011年开始,用硝基苯废水代替清江水后,棒磨机设备开始出现腐蚀问题,筒体跑浆、漏浆现象频繁发生。从停工检维修期间的腐蚀照片可以看出,腐蚀整体表现为衬板及筒体的减薄,漏浆发生位置较为集中,在螺栓头与衬板、衬板与衬板的连接处,如图2~3所示。而作为备用设备的X5201C长期工艺用水较为稳定(主要是灰水),腐蚀并不突出,如图4所示。
1.2 工艺用水腐蚀性分析
根据现场腐蚀调研,棒磨机腐蚀问题出现在制浆工艺用水变化后,因此,分别对涉及的煤浆工艺用水即清江水、灰水、硝基苯废水及煤浆进行了取样分析,分析结果见表1。结果表明,与清江水、灰水相比,硝基苯废水具有盐含量高、电导率高的特征。其中,硝基苯废水中硫酸根离子、硝酸根离子含量增大明显,且出现了亚硝酸根离子,而其他工艺用水中都无亚硝酸根离子。煤浆水中硝酸根和亚硝酸根存在化学转化。也就是说,工艺用水调整为硝基苯废水后,电导率的升高、亚硝酸的出现都有可能导致棒磨机腐蚀加剧。
项目 | 清江水 | 灰水 | 硝基苯废水 | 煤浆 | |
---|---|---|---|---|---|
pH | 7.67 | 8.09 | 10.83 | 7.83 | |
电导率(50 ℃)/(mS·cm-1) | 0.36 | 4.64 | 30.40 | 21.20 | |
阴离子质量分数/( μg·g-1) | F- | 0 | 6.21 | 0 | 0 |
HCOO- | 0 | 1 371 | 0 | 0 | |
Cl- | 18.9 | 72.9 | 9.4 | 191.4 | |
![]() |
0 | 0 | 356 | 0 | |
![]() |
38 | 243 | 960 | 1 074 | |
![]() |
45 | 101 | 17 973 | 13 221 | |
![]() |
9 | 0 | 2 078 | 0 | |
![]() |
0 | 0 | 0 | 0 |
2. 模拟腐蚀试验
为了明确硝基苯废水加剧腐蚀的原因,基于现场腐蚀情况及物料性质分析结果,在模拟现场工况的不同工艺用水(清江水、灰水、硝基苯废水、煤浆及现场模拟溶液)中进行了全面腐蚀试验和缝隙腐蚀试验。试验材料为65Mn钢,其化学成分(质量分数)为0.66% C、0.24% Si、0.98% Mn、0.021% P、0.02% S、0.11% Cr、0.02% Ni、余量为Fe。将65Mn钢制成尺寸为40 mm×13 mm×2 mm的挂片。挂片经丙酮除油、无水乙醇脱水后称量。
2.1 全面腐蚀试验
参照NACE TM0169-2012 Standard Guide for Laboratory Immersion Corrosion Testing of Metals标准采用浸泡法对挂片进行全面腐蚀试验。将处理后的挂片安装在旋转挂片支架上,倒入适量介质溶液,保证试片全浸于液相,控制搅拌速率为0.67 m/s,升温至50 ℃,试验周期为96 h。待试验结束后,用清洗液去除挂片表面的腐蚀产物,再称量。采用失重法计算腐蚀速率,并利用体视显微镜和扫描电镜观察其腐蚀形貌。
2.2 缝隙腐蚀试验
缝隙腐蚀试验分别采用了浸泡法和电化学法并参照ASTM G78-2015 Standard Guide for Crevice Corrosion Testing of Iron-Base and Nickel-Base Stainless Alloys in Seawater and Other Chloride-Containing Aqueous Environments和T/CSTM 0046.10-2018《低合金结构钢腐蚀试验第10部分:缝隙腐蚀试验方法》标准进行。
浸泡法:用“*”形凸台四氟隔离环将处理后的挂片固定在支架上,再放入旋转挂片试验装置的烧杯内,倒入适量介质溶液,升温至50 ℃,试验周期为30 d。待试验结束后,用清洗液去除试片表面的腐蚀产物,并进行称量。然后,采用失重法计算腐蚀速率,并利用体视显微镜观察腐蚀形貌。
电化学法:将处理后的挂片固定在支架上,预制缝隙通过“O”形四氟密封圈压制实现;然后利用Zennium Pro电化学工作站分别在50 ℃、通氧的不同工艺用水中进行开路电位和极化曲线的测试。待测试结束后,通过挂片腐蚀形貌或极化曲线的变化趋势进行缝隙腐蚀的判定。试验过程中,介质溶液p H调节使用的是硫酸和氢氧化钠溶液。
3. 结果与讨论
3.1 硝基苯废水对全面腐蚀的影响
图5和图6分别为在不同工艺用水中全面腐蚀后65Mn钢的宏观形貌和微观形貌。结果表明,65Mn钢在灰水中全面腐蚀后仍保持金属光泽,肉眼观察未见明显腐蚀,而在清江水、硝基苯废水、煤浆水中腐蚀后65Mn钢表面出现明显的局部腐蚀。
由图7可以看出,65Mn钢在硝基苯废水与清江水中的腐蚀速率较大,而在灰水与煤浆水的腐蚀速率较小。硝基苯废水的腐蚀性与清江水的腐蚀性有差别,但没有本质差别。因此,制浆工艺用水由硝基苯废水换成清江水后,腐蚀速率会有所增大,但这并不是导致腐蚀加剧的主要原因。
3.2 硝基苯废水对缝隙腐蚀的影响
由图8可以看出,65Mn钢在清江水、灰水、煤浆水中缝隙腐蚀后仍保持金属光泽,而在硝基苯废水中缝隙腐蚀后则存在明显的局部腐蚀。
由图9可以看出,65Mn钢在硝基苯废水缝隙腐蚀过程中的腐蚀速率明显大于在其他工艺用水中的腐蚀速率。虽然,ASTM G78-2015标准指出腐蚀速率不宜作为缝隙腐蚀结果的评价指标,但该腐蚀速率在一定程度上也反映出工艺用水更换为硝基苯废水后,物料腐蚀性明显增加,长期使用势必会增强煤浆制备系统的腐蚀风险。模拟工况试验结果表明,棒磨机的腐蚀加剧是因为其在硝基苯废水中发生了缝隙腐蚀。
3.3 不同因素对缝隙腐蚀的影响
在工艺用水更换为硝基苯废水后,缝隙腐蚀明显加剧,故采用电化学测试考察了工艺用水水源、p H、阴离子等因素对缝隙腐蚀的影响。
3.3.1 工艺用水水源
由图10可以看出,在硝基苯废水中经电化学测试后65Mn钢表面存在明显的缝隙腐蚀痕迹,而在清江水、灰水以及煤浆水中65Mn钢发生过钝化,无缝隙腐蚀痕迹。
由图11可以看出,电化学测试时,65Mn钢在硝基苯废水中的反向扫描电流大于正向扫描电流,故其极化曲线存在滞后环,而在清江水、灰水以及煤浆中反向扫描电流基本上原路返回,极化曲线无滞后环。这同样证实了65Mn钢在硝基苯废水条件下发生了缝隙腐蚀。
3.3.2 工艺用水p H
在不同p H的硝基苯废水和煤浆水中对65Mn钢进行电化学测试,测试后65Mn钢的腐蚀形貌如图12和图13所示。由图12可以看出,当硝基苯废水p H为7.0~10.0时,65Mn钢均存在缝隙腐蚀敏感性。由图13可以看出,当煤浆水p H为7.85~10.00时,65Mn钢发生过钝化,基本没有缝隙腐蚀痕迹,说明该条件下65Mn钢的缝隙腐蚀敏性能较低。因此,在工艺范围内,工艺用水p H的调整对缝隙腐蚀基本没有影响,或者说缝隙腐蚀基本不受工艺范围内p H的影响,p H的调整不能控制或减缓缝隙腐蚀。
3.3.3 工艺用水中阴离子
硝基苯废水中含、
、
等阴离子,为了考察阴离子
、
、
对缝隙腐蚀的影响,用蒸馏水配制含不同阴离子的溶液,并用氢氧化钠将溶液p H调至10左右,对65Mn钢进行电化学测试。结果表明,
、
及
+
组合容易造成65Mn钢过钝化,而
及其与
、
的组合则使65 Mn钢表现出缝隙腐蚀敏感性。由此可见,导致65Mn钢发生缝隙腐蚀的主要原因是溶液中存在
。此外,模拟液中少量氯离子的存在对腐蚀情况影响不大。
为了确定对缝隙腐蚀的影响程度,在
含量不同的模拟溶液中对65Mn钢进行电化学测试。图14为65Mn钢经电化学测试后的腐蚀形貌。可以看出,随着
含量的减少,缝隙腐蚀逐渐减轻。当
质量分数小于30 μg/g时,65Mn钢在溶液中基本没有发生缝隙腐蚀,缝隙腐蚀敏感性消失。
4. 腐蚀过程分析
通常,棒磨机中的金属磨损来自三个方面,即磨料磨损、化学腐蚀磨损和高能量冲击磨损,三者相互作用。与干磨物料不同,当湿磨物料与大型磨机作用时,大型磨机在承受磨料磨损的同时,还要经受腐蚀和高能量冲击磨损,三者的相互促进、相互叠加作用将更突出[17-19]。
从上述模拟工况腐蚀试验结果可以看出:65Mn钢在清江水和硝基苯废水中腐蚀严重,腐蚀速率分别为1.837 1、3.648 9 mm/a;与其他制浆工艺用水不同,65Mn钢在硝基苯废水中表现出了明显的缝隙腐蚀敏感性。当工艺用水改为硝基苯废水后,65Mn钢衬板在制备煤浆过程中腐蚀速率增大、磨损加速,其原因主要有以下两方面。一方面,当筒体高速转动时,衬板与衬板之间、衬板与螺栓之间及筒体与螺栓之间更易松动,有利于缝隙腐蚀环境的形成;另一方面,棒磨机内部形成的局部腐蚀会因65Mn钢衬板在硝基苯废水中存在缝隙腐蚀敏感性而加速。作为一种常见的局部腐蚀形式,缝隙腐蚀[20-25]一般比较隐蔽,孕育期较长且没有明显的预兆。缝隙腐蚀一旦开始,其腐蚀速率会迅速增加并给材料带来严重的破坏,导致筒体螺栓处漏浆严重,设备日常维护工作激增,难以保证装置长周期运行。这与现场衬板表现出的缝隙腐蚀形貌也十分吻合。
进一步结合缝隙腐蚀影响因素的研究结果可以看到:65Mn钢只有在硝基苯废水中表现出缝隙腐蚀敏感性,而在煤浆水中却无明显缝隙腐蚀敏感性。这两种介质最大区别是后者无和
。在无
的溶液中,65Mn钢无缝隙腐蚀敏感性,这表明
是导致缝隙腐蚀的原因;当
质量分数小于30 μg/g时,65Mn钢无明显的缝隙腐蚀敏感性。在棒磨机内部混合过程中,棒绝大多数亚硝酸根被消耗,在棒磨机出口处物料已形成了稳定煤浆,基本避免了由
带来的腐蚀加剧问题,故棒磨机之后设备的缝隙腐蚀敏感性均明显降低。总之,
的存在是导致煤浆制备系统内腐蚀较为集中的根本原因。
5. 结论
硝基苯废水的资源化利用不仅能够节约水资源,而且也是生产企业节本降耗、贯彻绿色发展理念关注的重点领域之一,但硝基苯废水对制浆设备的腐蚀成为制约其资源化利用推进的技术难题,通过针对性的腐蚀成因分析及腐蚀规律研究,得到以下结论:
(1)更换制浆水源(硝酸苯废水)后,因其中含有,棒磨机国发生了严重的缝隙腐蚀而频繁失效。
(2)以硝基苯废水作为制浆水源后,在运行工况条件下,65Mn钢衬板具有极高的腐蚀风险,当质量分数小于30 μg/g时,棒磨机衬板才没有明显的缝隙腐蚀风险。
(3)由于棒磨机内部混合过程中发生化学反应而消失,因此棒磨机之后的管道设备缝隙腐蚀风险变小。
免责声明:本网站所转载的文字、图片与视频资料版权归原创作者所有,如果涉及侵权,请第一时间联系本网删除。
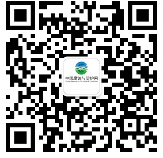
官方微信
《腐蚀与防护网电子期刊》征订启事
- 投稿联系:编辑部
- 电话:010-62316606
- 邮箱:fsfhzy666@163.com
- 腐蚀与防护网官方QQ群:140808414