离子 | Mg2+ | Ca2+ | Na+ | ![]() |
![]() |
![]() |
Cl- |
---|---|---|---|---|---|---|---|
质量浓度/(mg·L-1) | 93.3 | 33.1 | 15 243.61 | 102.37 | 287.26 | 3 293.73 | 19 048.40 |
随着中国经济的发展,对石油的需求日益增长。石油一般储存在储罐中。储罐寿命一般为20 a。在含蜡原油或高黏度、低凝点原油的储存过程中,用储罐内加热盘管加热或保温[1-2]可使原油保持流动,防止其凝固。但近年来,储罐加热盘管腐蚀泄漏导致的储罐大修停产现象频发,这严重影响了储罐的安全稳定、长期运行,给环境安全和经济生产带来了不利影响[3]。
储罐内加热盘管具有结构简单,操作便捷,管内可以承受较高压力等优点,一般安装在储罐底部,分别与导热油(蒸汽)管线和控制阀门连接。导热油(蒸汽)作为热源通过加热盘管管线回路对储罐内原油进行加热,再从出口处排出,从而形成一条完整的加热回路。储罐内加热盘管一般按结构形式的不同可分为分段式和蛇管式两种类型[4]。另外,根据容器的形状,加热盘管可制作成不同形状,也可采用多组相互独立的加热盘管,利用不同的热源进行加热。但是,加热盘管的通过能力有限,长时间使用后,流体中的杂质会堆积在加热盘管内,且加热盘管极易发生腐蚀失效现象[4-5]。
针对原油储罐加热盘管腐蚀泄漏频发现象,分析了储罐底部加热盘管腐蚀失效的原因。另外,通过盐雾腐蚀试验模拟储罐内加热盘管的服役工况,研究了盐雾腐蚀老化后环氧树脂、无机富锌和聚氨酯三种加热盘管防腐蚀涂层的形貌、表面粗糙度及腐蚀速率,为加热盘管外部防腐蚀涂料的选择提供参考。
1. 加热盘管内外部腐蚀
1.1 加热盘管内部腐蚀
水中的和
受热分解,生成CO2,随蒸汽一起进入加热盘管内部,由于储罐内原油温度较低,蒸汽发生冷凝,CO2溶解于冷凝水中形成酸性溶液,腐蚀加热盘管内部[6]。在电解质环境中,同一金属结构内部出现很多阳极区和阴极区,产生原电池,阳极区表现为点蚀。当蒸汽停止供应后,管道内的冷凝水作为电解质为电化学腐蚀提供了环境条件,加速了加热盘管的腐蚀[6-7]。此外,锅炉水中仍存在氧元素,当系统加热时,氧元素随蒸汽进入管道,使加热盘管内壁发生氧腐蚀。
为防止加热盘管内部腐蚀,建议合理利用油水分离技术和污水处理技术降低原油中的含水量,并通过除氧设备和使用除氧水等方法缓解氧腐蚀,进一步降低腐蚀速率。
1.2 加热盘管外部腐蚀
在开采过程中,原油中混入了大量的水,因此储罐中的原油也含有大量的水,含水原油会对加热盘管的外壁造成一定程度的腐蚀[8-9]。储罐中存在一定的沉淀物和含有氯化盐的油水混合物,同时水中溶解了大量的腐蚀介质,如O2,CO2,,H2S,硫酸盐还原菌(SRB)等,这些因素都会导致加热盘管外壁不间断发生腐蚀。H2S在水中发生电离形成H+、HS-,在H2S-H2O体系中H+、HS-和H2S发生氢去极化作用,并且在加热条件下与罐底附近大量的CaCl2、MgCl2反应生成HCl和H2S,加剧腐蚀[7]。此外,加热盘管处于储罐底部污水层,高矿度污水的配伍性差,也会形成垢下腐蚀[10]。
为防止加热盘管的外部腐蚀,建议对预制加热盘管进行喷砂处理,再喷刷性能优异的防腐蚀涂料,阻止油品中水分和腐蚀介质对外壁的侵蚀。
2. 试验
2.1 涂层制备
从储罐内加热盘管上切割尺寸为2 cm×3 cm的试样,用砂纸打磨试样表面,然后用10%(体积分数)稀硝酸清洗去除表面污垢。在处理过的加热盘管试样表面分别涂刷环氧树脂、无机富锌和聚氨酯防腐蚀涂层(涂层厚度约为200 μm),再将涂刷不同防腐蚀涂层的加热盘管试样置于70 ℃电热恒温鼓风干燥箱中恒温保持1~2 h,使涂层固化。
2.2 试样方法
2.2.1 加热盘管腐蚀因素测试
使用PE NexION 300X型电感耦合等离子体发射质谱仪(ICP-MS)测定储罐内沉积水样中的阴阳离子含量,证实加热盘管的确切腐蚀因素。
2.2.2 盐雾腐蚀试验
参考GB/T 10125-2012《人造气氛腐蚀试验盐雾试验》标准,对带涂层试样和无涂层试样进行盐雾腐蚀试验。盐雾腐蚀试验模拟了储罐内加热盘管的服役工况及不同防腐蚀涂层在中性环境下的老化作用。盐雾为5%(质量分数)NaCl溶液,喷雾压力为0.1 MPa,试验温度为35 ℃,试验周期为10 d。
试验结束后,对试样进行干燥、打磨,使用GeminiSEM 300型扫描电子显微镜(SEM)对试样表面形貌进行观察,对比不同防腐蚀涂层在加热盘管上的涂覆及腐蚀情况,分析防腐蚀涂层的防腐蚀效果。采用Bruker Scan-Dimension-Icon型原子力显微镜(AFM)观察盐雾腐蚀试验后试样的三维形貌,并进行表面粗糙度测试。采用ContourGT-X型表面轮廓仪对盐雾腐蚀试验后试样进行腐蚀深度测试,进而得出腐蚀速率。
3. 结果与讨论
3.1 加热盘管腐蚀因素
提取原油储罐中的沉积水,其组成成分如表1所示。结果表明:测试水样中存在Ca2+,Mg2+,,
,Cl-等,这进一步证实影响加热盘管腐蚀的相关因素。用SRB计数瓶对水样中细菌数量进行计算,结果显示,水样中SRB含量约为3.3×103个/mL。
3.2 腐蚀形貌
目测结果表明,盐雾腐蚀后无涂层试样表面附着了一定厚度的腐蚀产物,而涂刷了聚氨酯涂层、无机富锌涂层、环氧树脂涂层试样的腐蚀程度较轻,如图1所示。扫描电子显微镜观测结果表明,涂环氧树脂涂层试样表面相对更光滑,如图2所示。
3.3 表面粗糙度
图3为盐雾腐蚀试验后各试样表面AFM形貌,表2为AFM测得的试样表面粗糙度。结果表明,在三种带涂层试样中,涂环氧树脂涂层试样的表面粗糙度最低,仅为5.9 nm。
试样 | 表面粗糙度/nm | 试样 | 表面粗糙度/nm |
---|---|---|---|
无涂层 | 11.6 | 涂聚氨酯涂层 | 7.2 |
涂无机富锌涂层 | 8.4 | 涂环氧树脂涂层 | 5.9 |
3.4 腐蚀速率
图4为盐雾腐蚀试验后试样表面轮廓仪测试图,表3为根据单位时间内金属腐蚀的深度计算得到的腐蚀速率。结果表明,涂环氧树脂涂层试样的腐蚀速率最低,为9 μm/a,远低于涂聚氨酯涂层试样(27 μm/a)和涂无机富锌涂层试样(30 μm/a),而无涂层试样的腐蚀速率最高,达到了42 μm/a。
试样 | 腐蚀速率/( μm·a-1) | 试样 | 腐蚀速率/( μm·a-1) |
---|---|---|---|
无涂层 | 42 | 涂聚氨酯涂层 | 30 |
涂无机富锌涂层 | 27 | 涂环氧树脂涂层 | 9 |
4. 结论与建议
(1)储罐加热盘管的外部腐蚀主要是由罐内油品中水分和Ca2+,Mg2+,,
,
,SRB等腐蚀介质造成。建议在对预制加热盘管喷砂处理后,喷刷性能优异的防腐蚀涂料,阻止油品中水分和腐蚀介质对外壁的侵蚀。
(2)储罐加热盘管内部腐蚀的主要因素为整个加热系统的CO2腐蚀和氧腐蚀。建议合理利用油水分离技术和污水处理技术降低原油中的含水量,并通过除氧设备和使用除氧水等方法缓解氧腐蚀,进一步降低管内腐蚀速率。
(3)通过盐雾试验模拟储罐内加热盘管的服役工况,研究了盐雾腐蚀后环氧树脂、无机富锌和聚氨酯三种防腐蚀涂层的表观形貌、表面粗糙度及腐蚀速率。结果表明,相对于聚氨酯涂层、无机富锌涂层,环氧树脂涂层表面更光滑,表面粗糙度和腐蚀速率数据更低,分别为5.9 nm和9 μm/a,故环氧树脂涂层更适合作为加热盘管防腐蚀涂层,可延长加热盘管的使用寿命,保障储罐的安全高效运营。
免责声明:本网站所转载的文字、图片与视频资料版权归原创作者所有,如果涉及侵权,请第一时间联系本网删除。
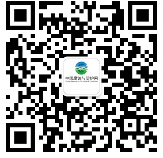
官方微信
《腐蚀与防护网电子期刊》征订启事
- 投稿联系:编辑部
- 电话:010-62316606
- 邮箱:fsfhzy666@163.com
- 腐蚀与防护网官方QQ群:140808414