随着我国航空工业领域的快速发展,对高性能、长寿命发动机部件的需求日益增加。单晶高温合金凭借优异的高温强度与疲劳性能、抗蠕变性、耐蚀性和抗氧化性等特点,已成为制造航空发动机热端部件的重要结构材料[1]。涡轮转子叶片作为航空发动机的核心热端部件之一,其主要功能是将高温高压燃气的热能转化为机械能,驱动涡轮轴旋转,进而带动压气机和其他附件工作,是决定航空发动机推力和性能的关键环节。
由于航空发动机单晶高温合金涡轮转子叶片长期服役于离心载荷、热应力和高温腐蚀等极端恶劣的工况环境,不可避免地产生各种局部损伤,如裂纹、烧蚀、磨损等,严重影响其服役性能,需要进行更换或修复[2]。然而,单晶高温合金涡轮转子叶片的制备工艺极其繁杂,且制造周期长、成品率低,更换新的叶片将造成材料的极大浪费,并大幅增加成本[3-4]。因此,单晶高温合金涡轮转子叶片修复技术已成为航空发动机维修领域的研究热点。
受涡轮转子叶片的复杂型面设计、特殊的微观组织特征以及苛刻的运行载荷条件等因素限制,对其服役损伤的修复,不仅要考虑恢复叶片几何形状、保持单晶的完整性,同时要避免修复区及其与基体的结合区产生冶金缺陷,从而使其满足严苛的服役要求[5]。单晶高温合金修复存在的最主要问题在于热裂纹和杂晶缺陷的形成,热裂纹的产生将引起修复失败[6],而杂晶的引入会大幅降低单晶高温合金的抗高温蠕变和疲劳性能[7]。针对上述问题,国内外学术界和工程界开展了大量研究工作,在单晶高温合金涡轮转子叶片修复区枝晶凝固理论、热裂纹形成机理和组织性能控制方法等方面均取得了一系列研究成果。
本文系统梳理了航空发动机单晶高温合金涡轮转子叶片的修复工艺方法及其应用进展,针对单晶合金增材修复中易产生的热裂纹缺陷问题,从热裂纹形成机理、关键影响因素和控制措施等角度进行了归纳,总结了单晶高温合金增材修复组织及性能的研究进展。在此基础上,展望了单晶高温合金涡轮转子叶片的未来研究方向和发展趋势。
1 单晶高温合金涡轮转子叶片修复方法研究及应用进展
针对航空发动机单晶高温合金涡轮转子叶片的修复,一般采用电弧熔丝直接能量沉积(wire arc directed energy deposition, WA-DED)、激光定向能量沉积(laser directed energy deposition, DED-L)、激光粉末床熔融(laser powder bed fusion,LPBF)和钎焊等修复方法。
1.1 WA-DED增材修复技术
WA-DED增材修复技术是利用非熔化极(钨极)与工件之间产生的高温电弧为热源,将被修复零件表面局部熔化形成熔池,同时将手动或送丝机自动输送至熔池前沿的焊丝(填充材料)熔化。熔化的焊丝通过熔池前壁流入熔池,随着电弧向前移动,熔池逐渐冷却凝固,形成新的金属层,从而实现材料的逐层堆积和修复[8-9]。此过程中,氩气等惰性保护气通过焊枪喷嘴连续不断地喷出,覆盖在电弧、熔池及热影响区,形成局部气体保护层,有效地隔绝空气,防止修复区域被氧化和污染[10]。WA-DED增材修复技术具有修复质量高、操作灵活、适应全位置修复等特点,是广泛应用于单晶高温合金修复的技术之一。
蔡祖鹏[11]采用WA-DED工艺对DD407单晶合金进行焊接熔凝,研究了工艺参数对凝固组织特征、杂晶和裂纹缺陷的影响,指出电弧热输入是影响熔凝区微观组织结构的主要因素,采用较小电流和较大运动速度可以有效降低熔凝区的杂晶含量,保证单晶完整性。此外,熔凝区裂纹类型主要为弧坑裂纹和晶间裂纹,裂纹多聚集于杂晶区域。
针对修复合金材料对WA-DED增材修复单晶合金转子叶片的影响,Churchman等[12]分别采用IN625,FM-92和IN738三种填充材料对Rene N5单晶合金进行增材修复,发现焊缝形状是影响开裂发生率的一个重要因素,WA-DED沉积层即使存在杂散晶粒,也不易出现裂纹,三种填充材料均未导致开裂问题。曲伸等[13]根据DZ125定向合金涡轮叶片叶尖的磨损与裂纹损伤,采用WA-DED工艺探究了传统钴基焊材(Co-Cr-W,Co-Cr-Mo,GH605)和自研MGS-1镍基焊材的适用性,发现采用钴基焊材进行修复时,热影响区易形成热裂纹,且修复区硬度显著下降;当采用MGS-1镍基焊材,能够显著减少甚至消除热影响区的裂纹问题,在1000 ℃温度下的抗拉强度达到了母材强度的90%,展现出优异的修复质量和性能恢复效果。
在WA-DED增材修复应用方面,加拿大Liburdi集团公司采用自动送丝WA-DED增材修复设备进行叶片修理,已实现了RB211发动机高、中、低压涡轮转子叶片修理[14]。中国航发北京航空材料研究院在单晶合金涡轮转子叶片WA-DED增材修复研究处于国内领先水平,采用精密弧焊方法增材修复了某型燃气轮机Rene N5单晶涡轮转子叶片叶尖损伤,恢复尺寸后的叶尖修复区组织呈现为定向柱晶(图1),修复的叶片已装机应用。
1.2 DED-L增材修复技术
DED-L增材修复技术是采用高能量密度的激光束加热并熔化基体和同轴送达基体表面的填充材料,快速形成局部熔池,随着激光热源的移动,熔池凝固并实现填充材料的沉积。DED-L技术的独特优势在于其高度灵活的工艺调控能力,不仅能够根据需求定制金属结构的生长方向,如制备柱状晶体结构与单晶结构,还具备快速修复损伤部件的能力,极大地提高了生产效率与材料利用率。同时,DED-L技术还能够通过混合不同性质的金属粉末,灵活调控修复区的合金成分,为修复结构的组织调控和性能提升提供了新的设计思路与实现途径[15-16]。
DED-L增材修复单晶合金过程中高的温度梯度和凝固速率可减小初级枝晶臂间距并细化γ′相,细化后的γ′相能够更有效地阻碍位错运动,提高材料的高温强度和抗蠕变性能,从而对单晶材料或部件的力学性能产生积极影响[17]。Gäumann等[18]利用DED-L技术对CMSX-4单晶涡轮转子叶片的裂纹损伤进行了增材修复,如图2所示,验证了该技术在单晶高温合金涡轮转子叶片修复中的可行性。
Vurgun等[19]通过DED-L技术,采用同母材的高温合金粉末修复了PWA1484单晶合金涡轮转子叶片,通过调整工艺参数,其最大修复高度达到2.3 mm,修复成功率高达94.85%。Cardoso等[20]采用DED-L技术在René N5单晶合金表面沉积René N4合金,发现沉积层继承了单晶基体的晶体结构和取向,形成了织构明显的柱状枝晶凝固组织,这表明在单晶高温合金基体上采用异质填充材料进行DEL-L修复也具有可行性。
Wang等[21]以DD407单晶高温合金为对象,对比研究了DED-L和电弧增材修复在显微组织和力学性能上随深度变化的差异。结果表明,两种修复区均能保持单晶外延生长,无明显裂纹,且具有相似的细晶析出物,在DED-L过程中,修复区顶部出现了柱状晶向等轴晶过渡现象。Kaierle等[22]结合DED-L和激光重熔两种工艺,成功实现了在CMSX-4和PWA 1426单晶合金涡轮转子叶片叶尖表面沉积和重熔形成完整的单晶结构,为单晶高温合金的修复提供了一种新方法。
美国霍尼韦尔公司已成功将DED-L增材修复技术应用于Avro RJ支线喷气系列飞机LF507发动机的涡轮转子叶片修理。德国弗朗霍夫创新中心开发了可用于转子叶片叶尖损伤修复的DED-L增材修复技术,如图3所示[5],形成了增材修复、机械加工、精密抛光和无损检测修理规范。国内方面,沈阳发动机设计研究所联合沈阳黎明航空发动机公司,开展了某型发动机涡轮转子叶片叶尖裂纹的DED-L增材修复技术研究,其修复的转子叶片通过了300 h近服役环境的热冲击实验考核,符合大修叶片故检标准[23]。中国航发北京航空材料研究院针对服役后叶尖磨损和裂纹的DD6和DD32单晶合金涡轮转子叶片开展了DED-L增材修复技术研究,修复出了无裂纹和未熔合缺陷的单晶合金叶片,且修复区获得了近单晶的定向组织,见图4。
1.3 LPBF增材修复技术
LPBF增材修复技术是利用激光器的能量输出,通过扫描振镜精确调控光束轨迹,直接作用于铺设在粉末床上的金属粉末颗粒,实现完全熔化并逐层构建三维实体。LPBF技术通过采用更细小的粉末粒度与优化的激光束光斑尺寸,显著提升了修复件的表面光洁度与尺寸精度。受限于打印室的尺寸与操作环境,其适用范围主要为小型化、结构复杂且对精度要求极高的部件修复[24]。
Atabay等[25]采用LPBF技术制备了高密度无裂纹的Rene 77单晶高温合金,扫描电子显微分析表明,制样的微观结构由主要沿〈100〉方向排列的柱状晶粒、细小的γ′沉淀相和球形晶界碳化物组成。张宇等[26]采用LPBF技术在CM247LC单晶基体上外延生长一种具有中等体积分数γ′相的合金粉末,发现修复界面的熔池宽深比大于4时,沉积区与基体能形成良好的结合界面以及较小的晶粒取向差。通过增大扫描速率和降低激光功率可以有效减小沉积区裂纹密度,沉积组织以沿沉积方向生长的柱状枝晶为主,沉积层越高,冷却速率越小,枝晶间距和晶粒取向差越大。通过打印参数优化,最终得到了裂纹密度低、晶粒取向单一且与单晶基板结合优异的镍基单晶高温合金沉积层,其抗拉强度可达1094 MPa,伸长率达到21%。
Wang等[27]采用CM247LC填充材料对受损的SRR99单晶合金涡轮转子叶片进行增材修复(图5),发现在CM247LC/SRR99界面上实现了无裂纹的冶金结合,CM247LC修复区域有效消除了铸态SRR99区域的缩孔。与SRR99基体相比,修复区硬度提高了8.62%,修复后试样的抗拉强度为791 MPa,断裂发生在SRR99基体,表明在CM247LC/SRR99界面处具有优良的冶金结合强度。
1.4 钎焊增材修复技术
钎焊增材修复技术是将高温合金与低熔点钎料加热到钎料熔点温度以上,通过毛细作用使液态钎料填充待修复区域,实现单晶高温合金的修复。目前,较为常见的单晶高温合金修复钎料多使用硼(B)作为降熔点元素[28]。然而,由于B元素在镍基高温合金中的固溶度较小,在非等温凝固过程中易形成大量低熔点脆性硼化物,引发裂纹的萌生和扩展,降低单晶高温合金的力学性能[29-30]。
Lang等[31]研制了一种Ni-40Cr-10Ta (原子分数/%)合金作为单晶高温合金的填充材料,实现了DD5单晶合金的高性能钎焊,相比于传统的含B和Si元素的钎料,避免了含B和富Si的化合物和低熔点共晶物的形成,有效提高了修复区的性能,其接头处的抗拉强度达到654 MPa,为单晶基体的88.5%,具有良好的修复效果。
高熵合金因其独特的组成和可调特性而受到广泛关注,在降低钎焊接头中的脆性金属间化合物方面具有巨大的潜力[32]。Ren等[33]开发了一种Ni-Co-Cr-Al-Nb-Ti钎料,其熔点为1155 ℃,在1200 ℃钎焊条件下实现了DD6单晶高温合金的修复。经过时效处理,其合金元素分布较为均匀,枝晶间第二相的尺寸得到细化,且修复区域的γ+γ′相与DD6单晶基体具有相同的取向,在980 ℃时的抗拉强度可达到559 MPa。
2 单晶高温合金涡轮转子叶片修复热裂纹研究进展
由于单晶高温合金在液相和固相之间的冷却过程中收缩率相对较低,常表现出对热裂纹和一系列收缩缺陷的高敏感性。另外,由于增材修复过程中快速的加热和冷却,导致热裂纹形成趋势进一步增加,严重影响单晶合金修复件的力学性能。目前,研究较为广泛的多种单晶高温合金,如CM247LC,CMSX-10,DD432,DD6等在增材修复过程中均极易出现热裂纹缺陷[34-38]。
2.1 单晶合金增材修复的热裂纹形成机理研究
单晶高温合金增材修复过程中产生的裂纹缺陷主要包括凝固裂纹和液化裂纹,其典型特征如图6示[39-40]。凝固裂纹主要发生在凝固末期液相和固相共存的糊状区内,在凝固过程中,枝晶组织的形成抑制了枝晶间残余液体的流动。同时,在凝固收缩引起的热应变/应力作用下,树枝晶间液膜被撕裂,形成凝固裂纹[41]。此外,由于液体中的合金元素分布不均匀,导致在新生晶粒周围形成低熔点液膜,这些低熔点的液相薄膜会降低固液界面能,通过广泛润湿固体枝晶来促进裂纹的产生。由于脆性晶界不能传递残余的拉伸应力或由于冷却熔体引起的收缩,相邻的两个晶粒会发生分离,形成凝固裂纹[42]。Han等[43]的研究表明,凝固裂纹一般在晶粒之间萌生,并沿大角度晶界(HAGBs>15°)扩展。
液化裂纹一般发生在与基体金属熔合区相邻的部分熔化区,在加热过程中,由于该区域的温度较高,某些低熔点相被重新熔化成液相薄膜,涉及γ-γ'共晶的软化与液化、粗大γ'相的不稳定分解、MC型碳化物的热诱导液化、析出相溶解等[44]。在残余应力作用下,这些液相薄膜易形成裂纹。Zhao等[45]观察到DED-L增材修复的Rene88DT合金裂纹区域内存在明显的液化现象,呈现典型的脆性晶间断裂模式。在裂纹内再凝固产物中含有大量的Ti,Al,Cr,Co和Ni,即γ+γ′共晶物。Li等[46]在DED-L形成的K465合金中验证了液相薄膜的存在和液化裂纹的扩展行为,发现具有一定宽度的裂纹始于热影响区,并沿着晶界或枝晶生长方向延伸到修复区。与凝固裂纹类似,液化裂纹也容易沿着HAGBs扩展。
Lu等[47]研究CMSX-10和DD432单晶高温合金DED-L成形热裂纹形成机制时,得出单晶合金沉积区内热裂纹形成取决于液相薄膜的稳定性、应力集中及晶界析出相的共同作用。液相薄膜的稳定性取决于枝晶凝固过冷度,当形成稳定液相薄膜的晶界角处枝晶凝固过冷度大于晶粒内部枝晶间液相薄膜的过冷度时,将为沿晶裂纹源形成提供稳定的液相薄膜;同时,沉积区内部的高水平应力集中驱动了热裂纹的萌生与扩展;富Re型析出相通过“钉扎作用”抑制液相补缩及弱化与基体之间结合强度等作用进一步促进了热裂纹形成。
2.2 单晶合金增材修复的热裂纹抑制方法研究
工艺参数直接影响单晶合金增材修复的凝固条件和应力状态,因此工艺优化是抑制热裂纹的一个重要途径。Gäumann等[18]和Lu等[47]研究指出,由于单晶材料的晶界面积远小于多晶材料,采用单晶材料对热裂纹的敏感性更低,而杂晶的引入将显著加剧热裂纹的敏感性。因此,实现外延生长可以抑制单晶合金增材修复的热裂纹缺陷。荣鹏等[48]通过DED-L进行多道多层沉积修复实验,探索了单晶合金开裂敏感性与晶粒尺寸的关系,发现晶粒尺寸是影响凝固裂纹形成的重要因素,较大的晶界角将引起热裂纹,而较小的晶粒尺寸可以提高临界晶粒边界角。随着激光扫描速度增快,晶粒尺寸减小、凝固裂纹倾向减弱。在激光功率为250 W、扫描速度为2.5 mm/s、单层提升高度为100 μm、叠加率为4.1%时,可以完全消除凝固裂纹,实现对损伤单晶叶片的无缺陷修复。
Chen等[49]采用风冷和水冷两种不同的冷却方式进行了DD407单晶合金DED-L实验,发现在空气冷却条件下形成的外延微结构几乎没有裂纹,而水冷却条件下则会因热应力积累而增加沉积层的热裂纹敏感性。在水冷情况下,几乎所有裂纹都出现在重叠区,只有少数裂纹出现在其他区域。元素分布分析和晶界角分析显示,显微偏析和大角度晶界导致了典型的凝固热裂纹。上述研究结果表明,通过改变单晶修复过程中的冷却状态,降低热应力累积,能够有效抑制热裂纹的产生。
卢楠楠等[47,50]提出一种动态沉积策略,通过逐层降低激光功率(热输入量),即激光功率从首层的1000 W逐层降低至末层的550 W,实现缓解沉积区应力集中并减少晶界形成,获得了无裂纹缺陷的单晶合金沉积样件。
3 单晶高温合金涡轮转子叶片修复组织及性能研究进展
3.1 单晶合金增材修复的组织研究
3.1.1 单晶合金增材修复的组织特征
单晶合金增材修复的典型组织特征如图7所示,自下而上可分为底部冶金结合区(即基体与沉积层的结合界面)、中部与基体同取向的连续外延生长柱状晶区和顶部等轴晶区[51]。在增材修复过程中,等轴晶粒的形成阻碍了[001]枝晶的外延生长,并破坏了单晶生长的完整性。高能量密度的热源为基体柱状晶的接续及其连续外延生长提供了高温度梯度条件,而随着熔池底部到顶部的温度梯度减小和凝固速率增加,在熔池顶部可观察到柱状向等轴状的转变,形成杂晶。
Lei等[52]研究发现,在单晶高温合金的修复中,杂晶基本上会存在于三个典型的位置:沉积区的外表面处、沉积区的上部及沉积区的底部,如图8(a)~(d)所示。沉积区的外表面处的杂晶主要是由于沉积过程中,未完全熔化的单晶粉末黏结到还未形成固相的熔池外表面上。这类未完全熔化的单晶粉末相当于柱状晶凝固前沿液相的形核质点,最终在侧壁表面形成等轴晶,这类等轴晶形态上具有典型的放射状的枝晶形态,其核心部位为未熔的固相。上部的杂晶主要是由于随着沉积高度的升高和温度梯度的下降而形成的等轴晶组织。对于熔合区底部杂晶,在沉积过程中,在激光的辐照下固相基体要发生熔化。当熔化的界面处分布具有大量低熔点元素的析出相及共晶相时,该位置便会形成下塌的现象,如图8(e),(f)所示。在熔合界面塌陷处的温度梯度的方向就会偏离原来的温度梯度的方向。在胞状晶的生长过程中,胞晶沿着固液界面处散热的相反方向生长,也即胞状晶沿着垂直于固液界面的方向生长。因此,在大尺寸析出相及共晶相导致的熔合界面塌陷处,胞晶的生长方向会发生偏转,进而形成熔合界面处的杂晶,如图8(g)~(j)所示。
3.1.2 单晶合金增材修复组织的理论研究
在凝固过程中伴随着相变潜热的释放,依据潜热传递路径的不同,可以将凝固方式分为两种类别:一类是沿着特定方向进行的定向生长,另一类是不受方向限制的自由生长,这两种晶体生长方式对应的晶粒形态分别为柱状晶和等轴晶。在单晶合金外延生长过程中,若凝固条件发生改变,引起晶粒形态由柱状晶向等轴晶转变(columnar to equiaxed transition,CET),将在修复区内形成取向各异且偏离基材晶向的杂晶。究其本质,杂晶的形成就是晶粒形态的CET[53]。
自20世纪80年代起,国内外众多学者针对凝固过程的CET现象,开展了一系列理论和实验研究。研究表明,成分过冷枝晶凝固理论是晶粒形态由柱状晶向等轴晶转变的一种主要机制。在柱状晶生长方式下,热流方向与枝晶的生长方向呈现逆向,而等温线的运动速率是固-液界面迁移速度的关键因素。对于合金材料,若溶质分配系数低于1,固-液界面前沿将形成一层溶质富集带,溶质浓度的变化引起局部平衡温度的改变。若实际温度低于平衡温度时,该区域会出现成分过冷,为等轴晶形成创造条件。
1984年,Hunt[54]基于稳态凝固条件,结合柱状晶生长和等轴晶形核及生长模型,率先建立了CET解析模型,创建了凝固参数、材料参数等轴晶体积分数和晶粒形态之间的定量判据。基于该模型,可根据不同的临界体积分数判定凝固组织的晶粒形态,当柱状晶前沿的等轴晶体积分数为0.66%时,完全避免CET的条件如式(1) 所示。
式中:G为固液界面前沿液态金属的温度梯度;N 0为单位体积内的非均质形核质点数; T N为非均质形核的临界过冷度; T C为柱状晶生长前沿的过冷度。
Kurz等[55]指出修复单晶高温合金的核心问题为控制凝固过程中柱状晶向等轴晶的转变,在综合考虑温度扩散、速度分配和相变等效应后,建立了枝晶快速凝固理论(KGT)。Vitek[56]在Kurz的研究基础上,进一步通过数值计算方法建立了工艺参数与晶体生长之间的关系。该研究将熔池形貌与3D Rosenthal模型结合,获得了熔池内部各位置的温度梯度与凝固速率,揭示了熔池形貌对晶体生长方向的影响。相比于Kurz采用的平均温度梯度评估熔池内部的CET,Vitek等采用了局部温度梯度,可以更加精确地判断熔池内局部位置的CET是否发生。
2001年,Gäumann等结合KGT理论,将Hunt的CET模型适用范围从稳态凝固扩展至快速凝固条件,并结合热力学数据库,把此模型应用于CMSX-4单晶高温合金的DED-L过程。由于DED-L过程的温度梯度和凝固速率较高,可忽略形核过冷度的作用,得到温度梯度、非均质形核质点密度、凝固速率和等轴晶体积分数(φ)之间的解析模型:
若φ<0.66%,可获得完全避免CET的条件为:
式中:K CET,a和n为材料特性的相关参数,对于CMSX-4单晶合金,K CET=2.7×1024 (K3.4/m4.4s),a=1.25×106 K3.4/ms,n = 3.4。
根据上述Gäumann模型,在选定单晶合金材料条件下,其凝固组织取决于修复过程中的固液界面前沿温度梯度(G)和凝固速率(V),通过调节G和V,可实现对凝固组织的调控,该理论已被广泛应用于对单晶高温合金增材修复过程中柱状晶连续外延生长和杂晶控制。
3.1.3 工艺参数对单晶合金增材修复组织的影响研究
单晶高温合金损伤修复区的微观组织结构对修复件高温力学性能具有决定作用,通过增材修复工艺获得与单晶基体接续且取向一致的完整外延生长柱状晶,是修复件成功实现再服役的基础。在增材修复过程中控制柱状晶连续外延生长,同时避免在杂晶形成,是单晶高温合金修复的关键[57]。针对单晶合金杂晶抑制问题,众多学者从工艺参数优化角度,开展了大量研究工作[58]。
Zeng等[7]对DED-L增材修复DD6单晶合金的研究结果显示,较快送粉速率和较高激光功率对柱状枝晶的外延生长和杂散晶粒的消除具有积极影响,而扫描速度对杂晶的作用效果并不明显。其指出复杂的热循环引起的残余应力并不是诱导杂晶形成的直接原因,位错的快速移动导致熔合线附近许多细晶粒的生长形态各异,位错移动到柱状晶粒的边界并逐渐形成亚晶粒边界。此外,形成碳化物和相邻γ/γ′共晶的元素在树枝状晶核和树枝状晶间区之间的含量差异导致二者的取向错位,在介观尺度上表现为杂晶。卢楠楠[50]和Xu等[51]分别通过工艺实验探究了激光功率、扫描速度对DED-L修复CSU-B2和CMSX-10单晶高温合金微观组织的影响,以连续生长的柱状晶长度和沉积区整体高度的比值来定量表征外延生长率,即r=h/H,指出激光功率和扫描速度会共同影响DED-L单晶合金的微观结构,高激光功率和低扫描速度有助于提升外延生长高度而降低外延生长率,在扫描速度为8~14 mm/s范围内,当激光功率大于600 W时,外延生长率高于92%。
Liang等[59]理论计算了涉及送粉情况的微观组织结构,指出适度的送粉速率可以有效地抑制杂晶的形成。卢楠楠[50]发现随着送粉速率增加,外延生长高度先升高后降低,外延生长率显著降低。Chen等[60]研究了送粉状态对单晶修复质量的影响,结果表明,不稳定的给粉会改变熔池中杂散颗粒的分布,金属粉末的熔化和流动影响了局部凝固条件。通过模拟实验结果表明,注入粉末使熔体局部冷却,从而促进了杂晶的形成。同时,Liu等[61]的研究结果显示,通过改变激光离焦量和倾斜激光入射角度,可以调节局部凝固条件并抑制杂晶的形成。
关于扫描路径对单晶合金内部杂晶的影响,已报道的研究结果存在不同的观点。Xu等[51]通过对CSU-B2单晶合金进行DED-L增材修复,指出与单向扫描法相比,双向扫描法制备的单晶合金外延生长率较高,可达97.4%。相反地,Chen等[60]以DD5单晶合金为研究对象,发现双向激光扫描模式阻碍了柱状枝晶的连续外延生长。在多层激光熔覆过程中,由于激光扫描方向的改变,导致局部凝固条件如热量积累和热流方向的改变,会导致外延枝晶沿激光扫描方向偏转或沿外延生长方向旋转。Wei等[62]同样发现,单向激光束扫描时形成纤维织构,当激光扫描方向旋转180°时,织构生长方向旋转90°。
Wang等[57]的研究结果表明,在DED-L过程中,足够高的激光功率以确保前一沉积层表面杂晶区域完全熔化,这是消除杂晶的前提。王慧君等[63]研究了DD6单晶合金在不同功率下重熔区内部杂晶分布,发现激光功率升高导致温度梯度降低,进而诱导柱状晶向等轴晶转变,枝晶交汇处杂晶的产生是由枝晶交汇处的温度梯度比其他地方小以及温度梯度方向改变引起的。Liu等[64]建立了一个自洽的三维数学模型,用于预测单晶合金多层多道激光粉末沉积过程中的晶体生长和微观结构形成,发现激光扫描路径重叠率是影响修复区外延柱状枝晶生长连续性和一致性的关键参数,重叠比过小和过大都会导致之前沉积层残留杂晶。
3.1.4 基体取向对单晶合金增材修复组织的影响研究
在增材修复单晶高温合金过程中,熔池内的柱状枝晶沿着熔池边界外延生长时,其方向并不严格平行于温度梯度,而是选择与基体一致的择优方向生长,因此基体取向是控制柱状晶外延生长和抑制杂晶形成的一个关键因素。
王雷等[65]对(001)和非(001)取向的DD6单晶合金增材修复过程中的杂晶形成能力进行了对比分析,通过数值计算获得了控制微观组织的局部凝固变量,并将杂晶的体积分数作为量化单晶完整性指数。结果表明,与(001)晶面相比,多数非(001)晶面可以促进柱状晶的外延生长,进而获得更好的单晶完整性。Guo等[66]通过在三个传统的晶体平面(001),(011)和(111)上改变激光扫描方向,对比分析了基体取向对DD6单晶合金杂晶形成敏感性的影响,指出在(011)和(111)晶面上,激光扫描方向对杂晶形成影响显著,而在(001)晶面上其影响较小。三个晶面显示出不同的CET敏感性,杂晶形成的倾向按照(111)>(001)>(011)的顺序变小,并指出在(011)晶面上沿
方向进行DED-L增材修复,可以有效抑制杂晶的形成。

Wang等[57]通过将基体取向引入到Gäumann模型,建立了一个结合基底取向和单晶外延生长过程中等轴晶形成敏感性的数值模型,以预测熔池中杂晶的形成趋势,提出可以通过选择优化的单晶基体晶格取向来控制杂晶。结合不同基体取向下激光表面重熔和单层沉积实验以及局部温度梯度和凝固速率的有限元模拟结果,指出(001)/[110]和(01
)/[100]基体取向,能够有效抑制杂晶的形成。

Liu等[67]针对DZ125定向合金DED-L过程,建立了一个晶体生长三维模型,结合工艺实验,深入研究了不同基体晶体取向下沉积层的微观结构和晶体生长行为。结果显示,在熔池纵向截面上,基体晶体取向的变化主要影响柱状晶向等轴晶转变的位置,而在横向截面上,其主要影响柱状晶择优生长方向。在纵向截面上,当基体取向的倾斜角从-30°变为+30°时,柱状晶外延生长率近似呈线性增长,从9%增加至94%。在横向截面上,当基体取向的倾斜角从0°变为+45°时,柱状晶择优外延生长方向的过渡线从熔池边缘移向中心轴。同时,Liu等[68]针对DD6单晶合金的倾斜侧壁和扭转侧壁等特殊非垂直结构,研究了倾斜角对单晶薄壁结构DED-L的微观组织和晶体生长行为的影响,指出斜向薄壁结构的成形性限制在一个较窄的范围内(≤30°),过大的倾斜角度(≥40°)不能维持熔池的平衡,形成质量差、不成形的熔池。通过超细柱状枝晶的连续外延生长,薄壁结构接续了单晶基体的[001]/[100]晶向。
Wang等[69]通过将DD3单晶基体绕x轴、y轴和z轴(分别对应[100],[010]和[001]晶向)旋转,探究了不同旋转角度的基体取向对单晶合金DED-L过程中凝固组织的影响。结果表明,基底取向会同时影响枝晶生长方向的温度梯度G和生长速率V,且G对基体取向变化的敏感性高于V,因此基体取向对枝晶外延生长和杂晶形成的作用主要取决于G的改变。从[100]/(001)初始状态开始,当围绕y轴旋转时,CET随基底方向的变化而强烈变化,而当围绕x轴或z轴旋转时,CET几乎没有变化。造成这种差异的原因是,当围绕y轴旋转45°时,熔池中不存在不同取向的枝晶交汇点,而围绕x轴或z轴旋转时,至少会出现一个交汇点。G在枝晶交汇处最低,因此枝晶交汇点的数量和位置共同影响着整个CET的趋势,减少交汇点或将它们转移至温度梯度高的位置,有利于避免CET并抑制杂晶形成。
此外,单晶合金损伤的几何形状可能改变增材修复时的散热条件,Chen等[70]针对复杂几何形状的单晶合金修复问题,通过制备并旋转圆柱体试样模拟了柱状晶生长方向与热流方向的角度β([001]晶向与激光轴向夹角),如图9(a)所示,系统探究了热流角β对杂散晶粒形成的影响。结果显示,柱状树枝晶趋向沿着靠近热流的晶向外延生长,在外延柱状枝晶区域,当β超过临界值30°时杂晶产生(图9(b)),并提出了通过几何形状设计确保β不大于30°的修复原则。
3.2 单晶合金增材修复的性能研究
针对单晶合金增材修复的性能评价,Ci等[71]成功地从基板上制备了无裂纹的DD32单晶合金,并进行了中温拉伸实验。结果表明,中温拉伸断口呈现为解理断裂,断裂区域为基板;而高温拉伸实验中的断裂模式为微孔聚集断裂,断裂区域为沉积层。断裂模式不同的原因是裂纹起源不同。如图10所示,在中温拉伸实验中,粗大的MC碳化物碎片产生了裂纹源,并在基板中进一步扩展裂纹。由于熔点较低,γ+γ'共晶在高温拉伸实验中容易开裂并扩展断裂。
秦仁耀等[72-73]实验探究了DED-L增材修复DD6单晶高温合金的显微硬度分布,发现增材修复区的显微硬度可达450~470HV,显著高于DD6单晶基体(402~413HV),这得益于修复材料含有更高的C,Cr,Co,Hf,Re等合金化元素,其形成的晶间MC碳化物具有显著的弥散强化作用,同时较高的Cr,Co和Re含量在γ基体相中也有强烈的固溶强化作用。
Ren等[1]研究了SRR99单晶合金修复件的磨损行为,并与其铸态合金进行对比,发现采用DED-L制备的单晶高温合金γ′析出相尺寸低一个数量级,其磨损率和摩擦因数分别比铸态合金低75%和20%,磨损性能的改善是由于其更高的位错密度、更细的γ′相沉积和梯度组织的形成。Yang等[74]和Lei等[75]研究了DED-L镍基单晶高温合金在燃料气体环境中的热腐蚀行为,并将其与基体的腐蚀行为进行了比较,指出沉积的单晶层由γ(Ni)基体和丰富的球形γ′(Ni3Al)纳米粒子相组成,沉积部分的耐热腐蚀性能优于基底部分,这是由于γ′相更细、γ′相的体积分数更高以及沉积区的腐蚀产物更紧密的协同效应。
4 结束语
综上所述,增材制造为单晶高温合金涡轮转子叶片提供了一种先进的高效、高质量修复方法,迄今为止针对单晶高温合金及其转子叶片增材修复的研究主要集中在修复热裂纹形成机理、再结晶与晶粒外延生长影响机制和有限基础性能分析方面。在此基础上,国内外采用WA-DED,DED-L方法均成功实现了单晶高温合金涡轮转子叶片叶尖损伤的修复和应用[5,14]。目前各增材制造方法在修复单晶高温合金及其涡轮转子叶片时有着各自的优势,但均仍存在一些技术瓶颈:(1)单晶高温合金增材制造的可成形差特性以及涡轮叶片的薄壁特点和损伤部位结构拘束,使得WA-DED,DED-L和LPBF方法用同母材填充材料修复单晶合金涡轮叶片过程中极易发生热裂纹;(2)涡轮叶片的薄壁特点和损伤部位结构拘束,导致单晶合金涡轮叶片的增材修复部位不可避免存在较大的残余应力,致使在后续型面精加工或热处理过程中易发生再结晶和开裂。因此,采用增材制造技术如何实现单晶高温合金涡轮转子叶片的高效、高质量修复,获得理想的外延生长修复组织和优异的接头性能,并有效提高修复合格率,仍需开展更深入的研究。为实现增材修复技术在航空发动机单晶高温合金涡轮转子叶片深度修理领域的广泛应用,以下3个方向将是未来的研究重点。
(1)基于工艺特性的单晶合金增材修复专用合金材料成分设计
在现有的单晶合金涡轮转子叶片增材修复研究和应用中,所采用的填充材料普遍是与基体相同成分或与其相似成分的商用单晶合金材料,此类材料的组分及其配比是基于传统铸造或锻造技术设计开发的,未充分考虑增材修复过程中,高能量密度热源作用下的微区冶金、非平衡凝固和反复热循环等特性,而这些因素与修复区和基体结合区的应力状态、修复过程中的凝固参数和固态相变等密切相关,直接影响单晶合金修复件的冶金质量、凝固组织和服役性能。因此,针对增材修复工艺特征,综合考虑热裂纹敏感性、单晶完整性和强化机制等因素,结合材料热力学数据库,设计并制备单晶合金专用修复合金材料将是单晶合金涡轮转子叶片增材修复领域的一个重要研究方向。
(2)基于单晶合金材料特性的增材修复新工艺开发
目前,关于单晶高温合金DED-L增材修复所采用的热源模式主要集中在高斯光束能量分布,即热源能量呈中心高、边缘低的分布特性,此热源特性下熔池过热度高、凝固枝晶组织粗大,易引起单晶合金修复区热应力增大和高温力学性能降低等问题。随着光束整形技术的快速发展,各类具有特殊能量分布特征的激光热源类型被设计和开发,如环形光束、椭球光束、逆高斯光束等,上述热源类型已在金属增材制造领域获得初步应用,并验证了其在控形、控形方面的有益效果。鉴于DED-L修复与增材制造的冶金过程具有相似性,因此,开展DED-L新工艺开发研究,探索不同热源模式对单晶合金及其涡轮叶片修复冶金缺陷、晶体生长和残余应力的作用机制,基于单晶合金材料特性,设计激光热源能量分布形式,是单晶合金修复领域的一个重要研究方向。
(3)基于深度学习的单晶合金涡轮转子叶片增材修复多目标协同优化
目前,针对单晶合金增材修复中的工艺优化问题,多采用单一优化目标(热裂纹、杂晶、柱状晶外延生长控制等),且实验设计往往遵循单一变量原则,一方面,针对单一目标的工艺优化,未考虑其他目标性能的协同变化因素,可能出现对其他性能指标的削弱;另一方面,由于单晶合金增材修复的过程参数众多,包括热源功率、扫描速度、送粉速率、基体取向、熔池形状等,采用单一变量实验设计的工作量大,且缺乏对参数间交互作用的考虑,影响单晶合金修复件的综合性能。因此,采用深度学习方法,全面考虑工艺参数间的交互作用进行实验设计,建立单晶合金涡轮转子叶片多目标协同优化预测模型,实现对修复件综合性能的控制,是单晶合金修复领域的另一个重要研究方向。
免责声明:本网站所转载的文字、图片与视频资料版权归原创作者所有,如果涉及侵权,请第一时间联系本网删除。
相关文章
无相关信息
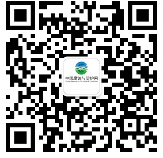
官方微信
《腐蚀与防护网电子期刊》征订启事
- 投稿联系:编辑部
- 电话:010-62316606
- 邮箱:fsfhzy666@163.com
- 腐蚀与防护网官方QQ群:140808414
点击排行
PPT新闻
“海洋金属”——钛合金在舰船的
点击数:10028
腐蚀与“海上丝绸之路”
点击数:7814