航空发动机作为航空航天领域的核心装备,正面临日益严苛的高温、热腐蚀及复杂载荷等极端服役环境,其研发和制造水平直接关系着国防安全以及国家竞争力[1-2],其中航空发动机转子叶片等热端部件在服役过程中需要长时间承受高温气体、冷热疲劳、磨损和冲击等影响[3]。镍基高温合金因其优异的耐高温、耐腐蚀以及抗氧化能力被广泛应用于航空发动机转子叶片等关键部位[4],与传统铸造多晶叶片相比,定向凝固成形的镍基高温合金由于消除垂直于[001]生长方向的横向晶界,其高温热稳定性和热疲劳性能得到了显著提高,在很大程度上提高叶片的使用寿命。然而,航空发动机叶片在长期服役的过程中不可避免地会受到磨损与烧蚀,致使大量叶片报废[5]。受限于航空发动机叶片的复杂结构和高精度,传统的焊接或激光熔覆修复方式使得被修复部位堆积大量的修复材料,加工精度较低且缺乏可靠性,迫切需要一种能够快速制造复杂结构和高性能的叶片修复技术。
金属增材制造技术通过高能束逐层熔化离散粉末并堆积形成“近净成形”构件,具有能量密度高、成形精度高、设计和制造自由度大等优点,是一种公认解决精密复杂构件整体成形难题的有效技术手段。与常用于叶片修复的激光金属沉积增材制造技术相比[
6],激光粉末床熔融(laser powder bed fusion,LPBF)技术具有良好的光束质量和更加细微的聚焦光斑,有利于获得高致密度、高尺寸精度和优异力学性能的成型件[
7-
8],是修复具有高精密复杂结构航空发动机叶片的理想技术。
影响定向镍基高温合金LPBF修复过程的因素众多,一旦选择不当的工艺参数,极易在熔池内部、道与道之间、层与层之间等局部区域产生孔洞和熔合不良等内部冶金缺陷,且很难通过后处理方式彻底消除。而LPBF修复过程中的能量传递涉及多尺度多物理场耦合,仅靠传统实验手段难以高效准确地揭示这一动态过程的演变规律。近年来,国内外研究人员结合数值模拟方法,有效地阐明增材制造过程中熔池热力学、动力学及凝固演变过程。Verhaeghe等[
9]将球形粉末简化为同等大小的球体模型进行LPBF过程的模拟,模拟结果证明蒸汽反冲压是调控熔池凝固形貌的重要因素。Lee等[
10]基于捕捉激光束与单个粉末颗粒之间的相互作用为增材制造构建一个粉末尺度的熔池模型,并通过温度场计算的凝固参数评估凝固形态和晶粒尺寸。Fang等[
11]采用多尺度元胞自动机(cellular automaton,CA)-欧拉多相模型预测Inconel 718激光直接能量沉积过程中的树枝状和晶粒结构。Lian等[
12]利用离散元素法和有限体积法分别实现粉末床铺展和粉末床的扫描过程,在增材制造模拟的基础上扩展CA法用于凝固过程中的晶粒结构演变模拟。这些研究为探索复杂且难以实验观测的LPBF修复过程提供全新途径,但现有报道关于LPBF修复定向镍基高温合金打印参数的筛选仍多采用试错法,其非平衡凝固过程中冶金缺陷与微观组织的演变规律及调控机制也尚不清晰。
本工作利用有限体积法和元胞自动机,构建定向DZ125镍基高温合金LPBF修复过程中粉末尺度温度场、凝固轨迹和微观组织的数值模型,分析不同打印参数对凝固轨迹形貌、冶金缺陷和微观组织的影响规律,研究LPBF修复过程中冶金缺陷的形成机制和晶粒形貌的外延生长机制,进而指导高致密定向镍基高温合金打印参数的高效准确设计,为定向镍基高温合金叶片的LPBF修复技术提供理论基础。通过实验观察验证数值模拟方法的准确性,确保模拟结果的可靠性,实现修复试样力学性能的提高,对于实际工程应用具有参考价值。
1 实验材料与数值模拟
1.1 实验材料
采用课题组前期开发修复用合金成分,粉体采用气雾化法制备,粒径为15~53 μm,粉末实测成分见
表1。采用的LPBF设备为西安铂力特增材技术有限公司生产的BLT-A300。LPBF实验是在DZ125基板上进行的,试样缺陷使用Axio Imager金相显微镜进行观察。本研究的电子背散射衍射(electron backscattered diffraction,EBSD)结果主要由配备取向测量系统的JSM-7900F场发射扫描电镜获得。
表1 粉末成分(质量分数/%)
Table 1 Powder composition(mass fraction/% )
|
1.2 粉末床熔池温度场模拟
LPBF扫描过程中随着热源的移动,合金材料面临的快速熔化和冷却凝固过程中激光与粉末之间热传递行为如
图1所示,温度场在短时间内发生急剧变化,而材料的热物性参数同样随温度发生变化[
13]。
图1 LPBF过程中激光与粉末之间热传递行为示意图[13]
Fig.1 Schematic diagram of heat transfer behavior between laser and powder in LPBF process[13]
|
对LPBF过程温度场的求解是一个三维非线性瞬态热传导的问题[
14],如
式(1):
(1)
式中:

为材料密度;

为材料比热容;

为坐标

随时间

的温度分布;

为梯度算子;

为材料的热导率;

为热流梯度;Q为单位体积内的热生成速率。
激光热源选取高斯面热源[
15-
16],热源方程如
式(2):
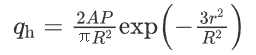
(2)
1.3 微观组织模拟
元胞自动机是增材制造过程中微观组织模拟的常见手段,该方法最早由Rappaz和Gandin基于晶粒成核和晶体生长理论提出[
19]。CA方法从给定的离散域中选取潜在的大块形核位点,对于每个选定的单元确定形核条件,超过临界过冷度后则会发生形核。在晶粒生长过程中,CA采用欧拉角表示新生晶核的取向并基于晶体生长理论求解晶核生长速度和外部轮廓的变化过程。固液界面外延形核基于对Kurz-Giovanola-Trivedi模型[
20]的拟合确定,对于立方晶系,CA方法假设晶核外部整体包络为正八面体。晶体〈001〉方向对应八面体对角线,为晶粒最优的生长方向。在计算过程中,随着时间的推移,包络体不断增长,最终吞噬相邻包络面来生长晶粒。当一个液态单元中心被吞噬时,一个新的规则八面包络体被分配给该单元,它继承捕获包络体的晶粒方向,最终实现晶粒的不断生长。采用单元过冷度的函数来拟合外延形核的生长速度v,如
式(5) [
12]:
1.4 LPBF扫描策略
基于前期研究工作[
21],在改变激光功率和扫描速度的同时,选择5组工艺参数进行模拟仿真,如
表2所示。LPBF修复过程采用FLOW-3D软件进行粉末尺度温度场模拟,模型尺寸为0.80 mm × 0.40 mm × 0.20 mm。
表2 LPBF打印参数
Table 2 LPBF printing parameters
|
Number |
Laser power (P)/W |
Scanning speed (V)/(mm∙s-1) |
Hatch spacing (H)/μm |
Layer thickness/μm |
Energy density/(J∙mm-3) |
1 |
150 |
800 |
65 |
35 |
82.40 |
2 |
200 |
600 |
65 |
35 |
146.50 |
3 |
200 |
800 |
65 |
35 |
109.90 |
4 |
200 |
1000 |
65 |
35 |
87.90 |
5 |
250 |
800 |
65 |
35 |
137.40 |
2 结果与分析
2.1 热物性参数计算
热物性参数决定材料热传递行为,LPBF模拟的不同阶段材料的热物性参数是动态变化的。为保证数值模拟的准确性,本工作通过JMatPro软件计算修复用合金粉末的热物性参数,LPBF粉末的热物性在成形过程中随着温度以及状态的改变而发生非线性变化。热导率和比热容用于计算热量在材料内部的分布和流动,其决定热量在熔池和周围材料中的传播速度并影响熔池的温度分布和尺寸,热导率和比热容随温度的变化情况如
图2(a)所示。动态黏度和表面张力决定熔池内熔体的流动特性和受力情况,其在熔池的稳定性、液滴飞溅和缺陷的数值模拟中具有重要影响,动态黏度和表面张力随温度的变化情况如
图2(b)所示。修复用合金粉末的凝固温度区间为1488~1650 K,基板预热温度为473 K,弹性模量、泊松比和线膨胀系数是计算熔化凝固过程中材料体积变化的关键力学性能参数,其随温度的变化情况如
图2(c)所示,相关热物性参数将用于后续数值模型的构建。
图2 合金热物性参数随温度的变化(a)热导率和比热容;(b)动态黏度和表面张力;(c)弹性模量、泊松比和线膨胀系数
Fig.2 Variation of thermal parameters of alloys with temperature(a)thermal conductivity and heat capacity;(b)dynamics viscosity and surface tension;(c)modulus of elasticity,Poisson’s ratio and coefficient of linear expansion
|
2.2 LPBF过程熔池形貌模拟
图3为不同打印参数下垂直于扫描方向的熔池截面形貌。当能量密度为82.4 J/mm3(P=150 W, V=800 mm/s)时,熔池形貌表面波动较大,有不连续倾向,并且存在明显孔洞与熔合不良等缺陷,如
图3(a)所示。随着能量密度增加至87.9 J/mm3(P=200 W, V=1000 mm/s),熔池内部的熔合不良缺陷减少。这是因为更高的能量输入使得未熔化的粉末颗粒减少,熔池区域液态金属的分布更加均匀,如
图3(d)所示。当能量密度达到109.9 J/mm3(P=200 W, V=800 mm/s)时,溶池内部无缺陷,但凝固表面出现波动,如
图3(c)所示。当能量密度达到137.4 J/mm3(P=250 W, V=800 mm/s)时,激光功率过高导致熔池内部的气体不能顺利逸出,使得孔洞再次出现,如
图3(e)所示。当能量密度达到146.5 J/mm3(P=200 W, V=600 mm/s)时,熔池波动加剧,熔池内部存在孔洞且凝固表面具有明显地起伏,如
图3(b)所示。固定激光功率为200 W时,溶池凝固后无孔洞等熔合不良缺陷,随着扫描速度的增加,凝固表面平整度也逐渐增加,如
图3(b)~(d)所示。这是因为在相同的激光功率下,扫描速度低导致能量输入高,熔池内的速度场同时会随着扫描速度发生周期性变化,熔池宽度形成不一致,进而导致熔池形貌出现波动。
图3 不同打印参数下Y-Z截面熔池形貌(a)P=150 W,V=800 mm/s;(b)P=200 W,V=600 mm/s;(c)P=200 W,V=800 mm/s;(d)P=200 W,V=1000 mm/s;(e)P=250 W,V=800 mm/s
(a)P=150 W,V=800 mm/s;(b)P=200 W,V=600 mm/s;(c)P=200 W,V=800 mm/s;(d)P=200 W,V=1000 mm/s;(e)P=250 W,V=800 mm/s
Fig.3 Melt pool morphology of Y-Z cross-section under different printing parameters
|
图4为不同打印参数下的打印结果。正如模拟结果所示,在能量密度为82.4 J/mm3(P=150 W,V=800 mm/s)时,由于能量输入不足,粉末吸收的能量不足以使其完全熔化。当粉末未能完全熔化时,熔池中会形成孔隙,低能量密度下熔体流动性差也会导致孔隙未能在熔池凝固前被填充从而形成熔合不良缺陷如
图4(a)所示。当能量密度增加至87.9 J/mm3(P=200 W,V=1000 mm/s)和109.9 J/mm3(P=200 W, V=800 mm/s),粉末可吸收能量增加,熔合不良缺陷减少,如
图4(c),(d)所示。能量密度高于137.4 J/mm3(P=250 W,V=800 mm/s)后,熔池内流体流动速度加快,这可能导致气体被卷入熔池并在熔池内不均匀分布进而形成孔洞,如
图4(b),(e)所示。
图4 不同打印参数下修复区金相显微镜照片(a)P=150 W,V=800 mm/s;(b)P=200 W,V=600 mm/s;(c)P=200 W,V=800 mm/s;(d)P=200 W,V=1000 mm/s;(e)P=250 W,V=800 mm/s
(a)P=150 W,V=800 mm/s;(b)P=200 W,V=600 mm/s;(c)P=200 W,V=800 mm/s;(d)P=200 W,V=1000 mm/s;(e)P=250 W,V=800 mm/s
Fig.4 Microscopic photographs of repair area under different printing parameters
|
图5为不同打印参数下平行于扫描方向的凝固轨迹截面形貌。随着能量密度的增加,熔池形貌的波动呈现先减少后增加的趋势。能量密度直接影响熔池凝固表面的平滑程度,当P=200 W,V=1000 mm/s,能量密度为87.9 J/mm3时,熔池凝固表面具有最佳成形效果如
图5(d)所示。当P=200 W,V=600 mm/s时,能量密度达到146.5 J/mm3,熔池凝固形貌波动最大如
图5(b)所示。此外,激光功率达到250 W时,凝固轨迹前端凹陷最为明显,熔池前端的凹陷会形成一个深而窄的孔洞。如果这个孔洞在熔池凝固过程中未能完全闭合则会改变熔池的几何形状和热流分布,导致熔池的凝固过程不均匀并使成形表面粗糙或形成凹坑。后续打印过程中层与层之间的过渡区域则难以适当地被熔化材料填充,极易导致层间结合不良。
图5 不同打印参数下X-Z截面熔池形貌(a)P=150 W,V=800 mm/s;(b)P=200 W,V=600 mm/s;(c)P=200 W,V=800 mm/s;(d)P=200 W,V=1000 mm/s;(e)P=250 W,V=800 mm/s
(a)P=150 W,V=800 mm/s;(b)P=200 W,V=600 mm/s;(c)P=200 W,V=800 mm/s;(d)P=200 W,V=1000 mm/s;(e)P=250 W,V=800 mm/s
Fig.5 Melt pool morphology of X-Z cross-section under different printing parameters
|
图6为不同参数下平行扫描方向截面熔池流速模拟结果。随着能量密度的增加,平行于扫描方向的液态金属流速逐渐增大。这是由于蒸汽反冲压力增加造成的激光正下方熔池液态金属触及到熔池底部后反弹,随后沿着扫描的反方向移动。
图7(a)显示扫描路径后壁处的熔体受到蒸汽反冲压力、马兰戈尼力和重力,三种力的动态平衡避免熔池内的熔体在光斑处富集。在能量密度为82.4 J/mm3(P=150 W, V=800 mm/s)时,如
图7(b)所示,较小的能量密度使得熔池窄而浅,此时熔池形貌主要受熔池熔合不良影响。而能量密度的增加使得熔池的长度和深度增加,这为液态金属的流动提供更大的空间。同时,能量输入的增加也使得蒸汽反冲压平行于扫描方向的分力增加,为熔池内部的扰动提供驱动力。以能量密度146.5 J/mm3(P=200 W, V=600 mm/s)为例,高能量密度引发熔池失稳并造成熔滴飞溅,飞溅熔滴重新被吸入熔池后同时也破坏熔池中的稳定区域,最终降低熔池凝固后的表面形貌的成形质量。
图6 不同参数下X-Z截面熔池流速(a)P=150 W,V=800 mm/s;(b)P=200 W,V=600 mm/s;(c)P=200 W,V=800 mm/s;
(d)P=200 W,V=1000 mm/s;(e)P=250 W,V=800 mm/s
(a)P=150 W,V=800 mm/s;(b)P=200 W,V=600 mm/s;(c)P=200 W,V=800 mm/s;
(d)P=200 W,V=1000 mm/s;(e)P=250 W,V=800 mm/s
Fig.6 Melt pool velocity of X-Z cross-section under different parameters
|
图7 熔体受力情况与不同能量密度下的熔体形貌(a)熔池后部熔体的受力情况;(b)低能量密度熔体形貌;(c)高能量密度熔体形貌
Fig.7 Melt force condition and melt morphology under different energy densities(a)force diagram of melt at back of melt pool;(b)melt morphology with low energy density;(c)melt morphology with high energy density
|
2.3 熔池特点与缺陷形貌分析
在LPBF过程中,在高能量密度过程下,金属熔池中的高温会导致显著的热梯度使得熔池内部的液态金属由高温区向低温区流动,即马兰戈尼效应。
图8为P=250 W,V=800 mm/s时垂直扫描方向截面熔池流速演变结果。结合温度场的模拟结果,可以更深入地分析熔池内部液态金属的流动规律。马兰戈尼力。如
式(6)所示[
22]:
图8 垂直扫描方向截面熔池流速演变(a)第一阶段;(b)第二阶段;(c)第三阶段;(d)第四阶段
Fig.8 Evolution of molten pool velocity in vertical scanning section(a)the first period;(b)the second period;(c)the third period;(b)the fourth period
|
(6)
式中:γ是表面张力;∇s T是表面温度梯度。熔池流动随扫描过程的演变可分为几个阶段:首先,激光开始扫描时,表面温度上升,液体表面张力由于温度的非均匀分布而形成梯度,特别是在熔池边缘和中心之间,表面张力梯度产生足够的驱动力,使得熔池中心的液态金属在激光的作用下直接流向底部;然后,扫描过程中,部分液态金属到达熔池底部后反弹回熔池内部,流体仍然沿熔池边缘从表面流向底部,形成马兰戈尼对流;随后,随着激光移动,熔池中心受到的动量冲击减小,流体开始沿反重力方向从中心向表面流动;最后,这种流动模式也驱动沿熔池表面流动的流体在马兰戈尼对流作用下向表面汇聚。温度差异是驱动马兰戈尼流动的主要因素,调控合适的能量密度有助于熔池内材料的混合和均匀性。
当激光功率过小或者扫描速度过大时,由于热输入较小会产生扫描层间的熔合不良缺陷,
图9为P=150 W,V=800 mm/s时,不同时间扫描过程的多层多道次温度场模拟结果。当t=0时,由于先前道次凝固轨迹的表面波动较大,当前的粉末层很可能存在较大的间隙,如
图9(a)所示;当t=5 μs时,激光作用在粉末与间隙上,但其中气体难以完全排出如
图9(b)所示;当t=45 μs时,不能排出的气体被吸入熔池,熔池中的气体不能顺利逸出,最终形成熔合不良缺陷如
图9(c)所示;当t=60 μs时,部分间隙虽然没有形成熔合不良缺陷,但使凝固轨迹表面高度明显下降,造成表面波动从而影响下一层粉末如
图9(d)所示。
图9 不同时间扫描过程多层多道次温度场(a)t=0;(b)t=5 μs;(c)t=45 μs;(d)t=60 μs
(a)t=0;(b)t=5 μs;(c)t=45 μs;(d)t=60 μs
Fig.9 Multi-layer and multi-pass temperature field during scanning at different time
|
当前道次扫描结束后,由于蒸发现象停止,反冲压力的影响会消失。此时,扫描路径的熔体在重力作用下下降,填充空腔。低能量密度(P=150 W, V=800 mm/s)模型中熔体流动方向始终保持由熔池表面流向熔池内部,熔体流动过程受扰动程度较小,扫描末端凹陷程度低,如
图10(a)所示。随着能量密度增加至87.9 J/mm3(P=200 W,V=1000 mm/s),扫描路径的熔体连接并共同形成液体通道,该液体通道导致结合的熔液在后端熔体推动下向上流动从而实现快速填充末端凹陷,如
图10(d)所示。能量密度达到109.9 J/mm3(P=200 W, V=800 mm/s)时,熔体在末端前壁的阻挡下,由熔池表面和内部两个方向向后流动,凹陷处还未完全填充时就发生凝固,如
图10(c)所示。在能量密度超过137.4 J/mm3后,较大的温度梯度和较长的冷却时间会促进前壁的熔体凝固。此时凹陷尖端下方的熔体向前的流动被抑制,向上流动的液体通道无法形成,但熔体顺时针方向的流动增强。熔池内自上而下的顺时针流动无法快速填充末端凹陷,最终在凝固后留下凹陷,如
图10(b),(e)所示。
图10 不同参数下熔池末端凹陷形貌(a)P=150 W,V=800 mm/s;(b)P=200 W,V=600 mm/s;(c)P=200 W,V=800 mm/s;(d)P=200 W,V=1000 mm/s;(e)P=250 W,V=800 mm/s
(a)P=150 W,V=800 mm/s;(b)P=200 W,V=600 mm/s;(c)P=200 W,V=800 mm/s;(d)P=200 W,V=1000 mm/s;(e)P=250 W,V=800 mm/s
Fig.10 Depression at the end of molten pool under different parameters
|
2.4 微观组织模拟与实验验证
LPBF过程中复杂的传热与熔池形貌变化对微观组织形貌具有很大影响,因此在进行CA微观组织模拟的过程中不能单纯地只考虑成形部件微区的温度变化。本研究将温度场模拟过程中的材料形貌变化转移至CA模型,从而获得更精确的模拟结果。将粉末尺度温度场热流与网格数据逐层导入CA模型中,并选择温度高于环境温度的网格点与之取交集,便可以实现内部不同取向晶粒粉末床的导入。在多层多道次温度场最中间选取尺寸为80 μm×80 μm×92 μm的区域用于耦合CA模型,
图11为不同打印参数下微观组织模拟结果,其中晶粒颜色越靠近红色代表晶粒沿生长方向,即[001]方向的生长情况越好。图中模拟结果底部深红色区域代表基体,首先在CA模型中随机生成各种取向的晶粒组织。
图11 不同打印参数下CA模拟结果(a)P=150 W,V=800 mm/s;(b)P=200 W,V=600 mm/s;(c)P=200 W,V=800 mm/s;(d)P=200 W,V=1000 mm/s;(e)P=250 W,V=800 mm/s
(a)P=150 W,V=800 mm/s;(b)P=200 W,V=600 mm/s;(c)P=200 W,V=800 mm/s;(d)P=200 W,V=1000 mm/s;(e)P=250 W,V=800 mm/s
Fig.11 CA simulation results under different printing parameters
|
当能量密度为82.4 J/mm3(P=150 W,V=800 mm/s)时,熔池冷却速率低,并且熔池凝固过程受热流影响较小,晶粒沿主要热流方向生长,与基体的取向差小于10°。但部分未熔化粉末存在于熔池内部,并作为异质核心形核生长,导致后续扫描层出现杂晶,如
图11(a)所示。当能量密度增加至87.9 J/mm3(P=200 W, V=1000 mm/s)时,由
图6可以看出能量密度的增加会导致凝固过程中平行于扫描方向的热流分量增大,熔池流速在一定程度上可以反映熔池内的温度梯度。温度梯度高意味着熔池内部温度变化剧烈,这会导致熔体从温度较低区域向温度较高区域的流动更加剧烈,从而提高熔池流速。晶体受到水平方向热流干扰带来的剪切力的影响产生与基体更大的取向差,如
图11(d)所示。进一步增加能量密度至109.9 J/mm3(P=200 W, V=800 mm/s)时,随机取向的细小柱状晶晶粒数量增多,如
图11(c)所示。当能量密度达到137.4 J/mm3时,外延生长的晶粒类型发生变化,由柱状晶转变为大量随机取向的杂晶,如
图11(e)所示。当能量密度达到146.5 J/mm3时,晶粒外延生长方向与基体取向差继续增大至60°以上,杂晶未见增多,如
图11(b)所示。在定向修复过程中,一个较高的温度梯度通常有助于促进沿特定方向的晶粒生长,晶体外延生长会沿着温度梯度最大的方向进行,以最小化系统自由能。较大温度梯度带来的快速冷却通常导致晶粒尺寸减小,因为晶体生长的时间缩短,从而可能促进形成细小的随机取向晶粒。CA模拟结果表明杂晶容易在温度梯度较大的边缘处存在,并且熔池内流体流速随着能量密度的增加同时增大,这导致外延生长晶粒与基体取向差逐渐增大。因此,通过调整工艺参数以保证温度梯度和熔池内熔体流速在合理范围内来实现修复定向DZ125合金。
模拟结果表明,随着激光功率的增加,熔池内部发生柱状晶-等轴晶转变(columnar to equiaxed transition,CET)。激光功率的增加使得熔池深度增加,但柱状晶区增加速度小于等轴晶区的增加速度。Hunt模型是描述CET的一个经典模型,其中临界温度梯度
如
式(7)所示[
23]:
(7)
式中:φ为熔池中等轴晶核的体积分数;a和n都是与材料相关的常数;R为凝固速率。随着激光功率的增加,熔池内部吸收的能量升高,温度梯度减小,低于临界温度梯度后会形成更多的过冷液体区域,从而促进新晶核的形成,进而得到更细小的晶粒。当激光功率增加至250 W后,熔池内部不同晶向区域发生CET转变。
为了验证外延生长模拟结果的准确性,在不同参数下进行打印实验,
图12为不同打印参数下的EBSD结果中试样修复界面的IPF(inverse pole figure)图,其中黑色虚线代表修复界面。当能量密度为82.4 J/mm3(P=150 W, V=800 mm/s)时,晶粒与柱状晶基体的取向差较小,但由于能量密度较低,部分未熔化的颗粒可能作为异质核心形核生长,导致后续打印层中出现与基体取向差较大的柱状晶晶粒,如
图12(a)所示。当能量密度为87.9 J/mm3(P=200 W,V=1000 mm/s)时,外延生长情况较好,柱状晶晶粒更加粗大并且与基体取向差较小,如
图12(d)所示。当能量密度为109.9 J/mm3(P=200 W, V=800 mm/s)时,少量随机取向的细小柱状晶晶粒出现,如
图12(c)所示。当能量密度达到137.4 J/mm3(P=250 W,V=800 mm/s)时,杂晶取代柱状晶作为外延生长主要晶粒类型存在,如
图12(e)所示。在能量密度为146.5 J/mm3(P=200 W, V=600 mm/s)时,外延生长柱状晶粒主要表现为两种取向,如
图12(b)所示。激光功率的增加使得熔池深处方向具有更大的温度梯度,在相同的激光功率下,扫描速度影响冷却速率,当打印参数为P=200 W,V=1000 mm/s时,温度梯度与冷却速率相匹配使得外延生长情况最佳。通过相同参数下模型CA模拟结果与打印件实验结果的对比,较好地验证了多层多道次模型微观组织模拟的准确性。
图12 不同打印参数下修复界面IPF图(a)P=150 W,V=800 mm/s;(b)P=200 W,V=600 mm/s;(c)P=200 W,V=800 mm/s;(d)P=200 W,V=1000 mm/s;(e)P=250 W,V=800 mm/s
(a)P=150 W,V=800 mm/s;(b)P=200 W,V=600 mm/s;(c)P=200 W,V=800 mm/s;(d)P=200 W,V=1000 mm/s;(e)P=250 W,V=800 mm/s
Fig.12 IPF results of repair interface under different parameters
|
2.5 修复试样力学性能
在DZ125基体上进行LPBF成形实验,对激光功率为200 W、扫描速度为1000 mm/s打印参数下修复的样品进行力学性能检测。修复试样的拉伸曲线和拉伸后的断裂试样如
图13(a)所示,修复后的样品屈服强度为895 MPa、抗拉强度为1081 MPa、断后伸长率为6.1%,均超过了定向凝固DZ125合金室温下屈服强度为840 MPa、抗拉强度为980 MPa、断后伸长率为5.0%的力学性能需求[
24],试样的界面结合性较好,且试样的断裂部位处于基体端,达到修复要求。采用KAM(Kernel average misorientation)图进一步研究修复试样力学性能的强化机制,
图13(b)为激光功率为200 W,扫描速度为1000 mm/s打印参数下修复试样的KAM图,对于某一点(Pi )的KAM计算如
式(8)所示[
25]。
(8)
式中:N为周围点数量;∆θij 为中心点i与周围点j的取向差。KAM值越大表示该区域的晶格畸变越大,位错密度越高。修复界面上方部分为修复区,下方部分为基体,修复区的KAM值明显高于基体,这表明样品修复区中位错密度较大,有较好的位错增强效果。
图13 修复试样应力-应变曲线(a)与KAM图(b)
Fig.13 Stress-strain curve(a) and KAM diagram(b) of repair sample
|
为进一步揭示修复样品的断裂行为,采用扫描电子显微镜(scanning electron microscope,SEM)对试样基体、修复区和断裂界面的微观组织进行观察和分析,如
图14所示。实验结果表明,基体中存在的白色组织和较大析出相分别为碳化物和γ+γ'共晶区[
26],如
图14(b)所示。而在修复区中未见明显碳化物和γ+γ'共晶区,如
图14(a)所示。在塑性变形过程中,大块碳化物的大尺寸和不规则形状导致其与周围的基体材料之间可能因变形能力不匹配而产生不均匀变形,这种不均匀变形会在材料中产生应力集中点,进而导致材料在较低的应变下更易引发裂纹的萌生和扩展。此外,碳化物本身较脆,这使得材料更倾向于沿碳化物断裂,如
图14(c)所示。
图14(d)显示较大的γ+γ'共晶区会造成微观组织的不均匀,这种不均匀性同样会在塑性变形过程中引起局部应力集中并促进断裂的扩展。
图14 断后拉伸试样不同区域SEM图(a)修复区;(b)基体;(c)断裂界面处碳化物;(d)断裂界面处γ+γ'共晶
Fig.14 SEM images of different regions of tensile sample after fracture(a)repair area;(b)substrate;(c)carbide at fracture interface;(d)γ+γ' eutectic at fracture interface
|
3 结论
(1)结合多层多道次熔池形貌模拟,能量密度小于87.9 J/mm3时,由于粉末颗粒熔化不完全导致熔合不良等缺陷的形成,能量密度大于137.4 J/mm3时,气体逸出受阻和熔池内部流动加剧导致熔池凝固表面出现明显起伏,影响成形质量。
(2)能量密度增加导致扫描热流水平分量的增大会干扰晶粒的外延生长过程,晶体受到剪切力的影响进而导致与基体更大的取向差。能量密度为82.4 J/mm3时晶粒与基体的取向差小于10°,能量密度达到146.5 J/mm3时晶粒与基体的取向差大于60°。
(3)激光功率的增加导致熔池内温度梯度减小,较低的温度梯度促使更多的过冷液体区域的生成进而促进新晶核的形成。激光功率从150 W增加到250 W时,熔池内部不同晶向区域发生CET转变,外延生长由柱状晶转变为大量杂晶。
(4)基于无缺陷熔池形貌与定向外延生长模拟结果,结合实验验证,分析获得修复用合金增材制造的合理工艺参数为:P=200 W,V=1000 mm/s,H=65 μm。该参数打印合金的力学性能:屈服强度为895 MPa、抗拉强度为1081 MPa、断后伸长率为6.1%,均超过了定向凝固DZ125合金的力学性能需求。