不同电子束流EB-PVD制备YSZ热障涂层的组织结构演变、热循环寿命与失效行为分析
航空发动机作为现代大飞机的动力系统,其技术进步对国家工业实力具有显著的指示作用[1-2]。在航空发动机领域,推重比和工作效率是衡量其性能的关键指标。为了提升这些性能指标,提高涡轮前进口温度成为当前技术发展的主要方向。然而,随着温度的提高,涡轮叶片的承温能力面临严峻挑战。因此,热障涂层(thermal barrier coatings,TBCs)技术作为提升涡轮叶片耐高温性能的关键技术,其研究与应用显得尤为重要[3-6]。
热障涂层技术通过在航空发动机和燃气轮机的涡轮叶片上施加一层具有优异隔热性能、抗氧化性能和抗高温腐蚀性能的涂层,从而有效提高部件的承温能力[7-10]。目前,热障涂层主要由金属黏结层和陶瓷面层两部分组成,金属黏结层提供优异的抗氧化性能并起到基体和陶瓷面层间的黏结作用,而陶瓷面层通常为低热导率陶瓷材料,提供优异的隔热效果,增加耐温能力。氧化钇稳定氧化锆(yttria-stabilized zirconia,YSZ)陶瓷材料由于具备低热导、高熔点、化学稳定性好等优势,成为热障涂层陶瓷层的首选材料之一,被广泛应用于热障涂层中[11-13]。
目前,制备YSZ热障涂层的主要技术包括大气等离子喷涂(air plasma spraying,APS)和电子束物理气相沉积(electron beam-physical vapor deposition,EB-PVD)两种技术,其中APS制备的层片状YSZ热障涂层热导率低,具有优异的隔热性能,主要应用于燃烧室隔热瓦、导向静子叶片表面[14-16]。而发动机涡轮转子叶片在高温高压下转动时产生的巨大离心力使叶片产生伸长应变,APS制备热障涂层的应变容限无法匹配叶片变型而出现失效剥落,EB-PVD技术利用高能电子束将材料加热至蒸发,然后在加热基体上沉积形成涂层,EB-PVD制备的热障涂层具有独特的柱状晶结构,其柱状晶的垂直排列可极大地提高热障涂层应变容限,从而提高热障涂层的热循环寿命和抗剥落性能,满足涡轮转子叶片的服役要求[17-19]。此外,等离子喷涂物理气相沉积(plasma spray-physical vapor deposition,PS-PVD)技术也在不断发展,可兼具高效率制备和类柱状晶结构的特点,因此,该种工艺的柱状晶组织结构的调控也尤为重要[20]。李国浩等[21]研究了EB-PVD工艺所制备YSZ热障涂层的抗热震性能,表明热障涂层致密程度的变化可影响热震过程中的应力缓解和释放,从而影响涂层寿命。Wang等[22]研究了EB-PVD工艺转速对(Gd0.8Yb0.2)2Zr2O7/YSZ双陶瓷层热障涂层微观组织结构的影响,发现不同转速下热障涂层的柱状晶粒发生显著变化,微观组织对涂层热循环行为产生影响。Liu等[23-24]研究了金属黏结层与陶瓷层间组织结构及粗糙度的变化对热障涂层热循环寿命的影响及微观结构演变,并阐述了随界面微观结构变化的失效作用机制。Zhen等[25]对EB-PVD热障涂层热循环下的内应力进行分析,发现陶瓷层和热生长氧化(thermally grown oxide, TGO)层热氧化内应力由基本一致到TGO层超过陶瓷层内应力的演变趋势。然而,在服役过程中,柱状晶结构与热流方向平行,使得EB-PVD制备的热障涂层隔热效果不及APS制备的层片状热障涂层,并且EB-PVD技术中对柱状晶结构的有效调控与制备鲜见报道,EB-PVD电子束流对涂层的影响有待进一步研究。
针对上述问题,本工作采用EB-PVD工艺,在不同蒸发电子束流下制备了YSZ热障涂层,探究了热障涂层相结构与微观组织结构演变,测定了不同工艺制备YSZ热障涂层的热导率变化,并对不同电子束流所制备YSZ热障涂层进行1150 ℃热循环寿命测试,研究其微观组织结构变化对涂层热循环寿命的影响,进一步分析了YSZ热障涂层失效行为。
1 实验材料与方法
1.1 涂层制备
选用DD6镍基单晶高温合金作为基体材料,其名义化学成分列于表1中,采用精密线切割加工得到尺寸为30 mm×10 mm×1.5 mm试样,使用金相砂纸打磨试样表面,并经吹砂(120目Al2O3砂粒)处理,保证表面粗糙度R a达到(1.0±0.3) μm。随后,试样依次经过自来水冲洗、去离子水浸泡、酒精脱水处理,并最终烘干,确保试样表面清洁无污染,完成试样制备。
采用真空电弧离子镀(vacuum arc ion plating)工艺在试样表面沉积镍钴铬铝钇铪(NiCoCrAlYHf)作为金属黏结层,涂层名义化学成分见表1,沉积前将真空室抽至10-3 Pa并通入氩气,对试样及炉内进行20 min溅射清洗,活化试样表面状态,随后进行涂层沉积,沉积工艺参数如表2所示。涂层沉积后,将试样置于真空热处理炉中,在(1173±50) K下进行3 h的保温处理,确保涂层与基体材料之间的界面结合强度,同时维持炉内真空度在2×10-3 Pa以上,以避免氧化等不利影响。
之后,采用EB-PVD工艺进行氧化钇部分稳定的氧化锆(8%(质量分数)Y2O3·ZrO2,YSZ)涂层制备,并通过改变工艺过程中的电子束流,实现不同电子束流下YSZ涂层的沉积,其沉积工艺参数如表3所示,电子束流1.2,1.8,2.4 A对应制备的涂层试样编号为S1,S2,S3。
1.2 测试与表征
采用D8 Advance型Cu元素Kα特征X射线衍射仪对试样进行相结构测试,扫描速度为5 (°)/min。采用FEI-Quanta 600型环境扫描电子显微镜(scanning electron microscopy, SEM)对试样表面和截面显微结构进行分析,利用扫描电镜所配带的Oxford INCAx-sight 6427型能量散射(EDS)系统对试样进行能谱分析,分析元素含量与分布。采用Image J图像分析软件测定所制备热障涂层柱状晶直径尺寸,每个试样选取3张代表性截面显微形貌照片进行厚度测试,每张照片测试统计不少于10个尺寸数据,计算柱状晶直径尺寸平均值和标准差。采用Netzsch LFA 427型激光闪射分析仪(laser flash analysis, LFA)对3种不同参数制备的涂层热导率进行测试,测试温度范围为25~1200 ℃。采用高温热循环测试设备测试涂层的热循环寿命,测试温度为1150 ℃,热循环模式为炉内保温55 min,空气自然冷却5 min,当表面涂层脱落超过10%时停止测试,平均每种工艺涂层测试5个试样热循环寿命,并计算5个试样的热循环寿命平均值和标准差作为最终测试结果。
2 结果与分析
2.1 热物理性能
图1为不同电子束流下制备的YSZ热障涂层XRD谱图,根据谱图可知,YSZ热障涂层衍射峰分别为30.16°,35.20°,50.40°,59.88°,73.56°和74.30°,对应T相(JCPDS No.48-0224)中的(101),(110),(112)+(200),(103)+(211),(004)和(220)晶面,由于T相的(112)和(200)以及(103)和(211)衍射峰非常相近,所以在YSZ涂层的 XRD谱图仅在50.40°以及59.88°各显示单一较宽峰的存在。由此表明,YSZ涂层中不存在明显的单斜相和立方相结构,证明Y原子稳定固溶至ZrO2内部,在室温形成亚稳态四方相(T′)。此外,随着电子束流的逐步增加,四方相(101)晶面衍射峰逐步增强,表明该晶面为YSZ涂层生长的择优取向,且YSZ晶粒随电子束流增加该晶面取向尺寸发生变化,结合涂层显微组织结构图(图2)分析,电子束流的增加使得YSZ涂层柱状晶尺寸增大,类金字塔形尖端更加明显。因此,电子束流的增加不会改变Y原子在ZrO2内部的稳定固溶,可以形成良好的亚稳态四方相,但随着电子束流的不断增加,YSZ柱状晶组织在其择优取向上尺寸增大。
2.2 显微结构和成分
图2为不同电子束流下制备的YSZ热障涂层表面显微形貌及其EDS元素分析,由于PVD工艺中的气相原子自阴影效应,YSZ涂层表面无法形成平面状显微组织形貌,生长末期会出现类金字塔状尖端[25]。由图2可知,不同电子束流下制备的YSZ热障涂层表面显微形貌及尖端结构存在较大差异。在1.2 A电子束流下制备的热障涂层表面呈现三角状尖端(图2(a)),尺寸较为细小,且表面存在较多孔隙,组织结构疏松;当电子束流增加至1.8 A时,典型的柱状晶金字塔状尖端结构出现,表面致密度显著提高(图2(b));当电子束流为2.4 A时,YSZ涂层呈现山脊状尖端,即金字塔尖端进一步粗化(图2(c))。结合XRD峰强度变化,其柱状晶直径随电子束流增加明显粗化,结构致密度增加。此外,对3种不同显微形貌的涂层表面均进行了EDS成分分析,其主要成分均为Zr,Y,O 3种元素,且Y元素的质量分数基本一致,表明显微形貌并未引起涂层的成分偏析。因此,电子束流的变化可显著改变涂层表面形貌,尖端结构随着电子束流的增加不断生长粗化,由细小三角状转变为金字塔状和山脊状,表面致密度增加,单个柱状晶直径不断增大,但不会引起涂层成分的偏析。
图3为不同电子束流下制备的YSZ热障涂层截面显微形貌,由图3可知,在不同电子束流下制备的YSZ热障涂层均呈现柱状晶组织结构,但其柱状晶尺寸存在明显差异,1.2 A低电子束流下,YSZ涂层柱状晶组织结构较为纤细,且枝晶较多,各纤细柱状晶生长相互干涉,形成纤细柱状晶、多枝晶交叉的结构(图3(a));随着电子束流的提高,柱状晶尺寸明显增加,1.8 A电子束流制备的柱状晶尺寸较1.2 A下增加了1倍以上,结构致密度明显提高,且柱状晶的枝晶结构基本消失,而单根柱状晶内部出现了排列有序的纳米孔结构,推测为柱状晶枝晶结构的进一步生长闭合形成纳米闭气孔,单根柱状晶尺寸也进一步增大,但柱状晶间相互增长仍然产生干涉,形成柱状晶相互交叉排列的结构(图3(b));2.4 A电子束流下,柱状晶组织结构更为明显,且柱状晶结构致密度进一步提高,单根柱状晶的纳米孔消失,形成羽毛状结构,此外,由于柱状晶尺寸的增加与致密度的提高,柱状晶间排列有序、间隙明显,没有明显的干涉(图3(c))。
图4为不同电子束流下制备YSZ热障涂层的柱状晶直径尺寸,由测量数据可知,随着电子束流的升高,柱状晶直径不断增加,这与图3中涂层截面显微形貌结果相对应。1.2 A低电子束流下,YSZ涂层柱状晶直径在0.8 μm左右,且多为枝晶交叉;1.8 A电子束流下,柱状晶平均直径尺寸增加至约2.6 μm,并且尺寸波动幅度增大,表明柱状晶间生长干涉影响了尺寸增长;2.4 A电子束流下,柱状晶直径进一步增加,达到5.4 μm左右,且排列有序,柱状晶结构完整。此外,对不同电子束流制备YSZ热障涂层的热导率进行了测试,同为YSZ材料的涂层热导率变化差异不大,在室温至1200 ℃范围内,均在1.4~2.0 W·m-1·K-1之间,室温至1000 ℃范围内,由于晶格结构对声子散射作用的影响,声子散射平均自由程随温度升高而降低,热导率也随之逐渐降低,1000~1200 ℃范围内,除声子热传导的传热机制,光子辐射传热机制的比例增加,导致热导率随温度提高出现增大的现象。3种不同柱状晶结构的热导率出现微小差异,其中1.8 A电子束流下制备的热障涂层热导率较其他两种降低约0.1 W·m-1·K-1,由图3可知,1.8 A电子束流下制备的柱状晶结构除柱状晶排列紧密外,同时存在较多的纳米闭气孔,这可能会进一步增加声子散射平均自由程,降低涂层热导率,而1.2 A电子束流下的纤细疏松柱状晶结构也会对热导率降低产生积极作用,2.4 A电子束流下制备的粗大致密度高的柱状晶结构产生的孔隙较少,且柱状晶排列的间隙大多与热流方向平行,对热导率的影响不明显。综上所述,EB-PVD热障涂层热导率除本征材料影响外,在一定程度上受柱状晶结构的影响,柱状晶尺寸的增加对热导率的降低产生不利影响,内部纳米孔、枝晶结构等缺陷也会降低热导率。
2.3 热循环寿命和失效行为
为探究YSZ热障涂层的服役寿命,对不同电子束流制备的YSZ热障涂层开展了1150 ℃热循环寿命测试,即在1150 ℃高温下加热55 min,然后空气冷却5 min为1个测试循环周期。图5为不同电子束流下制备的YSZ热障涂层热循环寿命,实验数据表明,不同电子束流下制备的YSZ热障涂层热循环寿命存在差异,1.2 A的低电子束流下制备的YSZ涂层热循环寿命为436周次,1.8 A电子束流下制备的YSZ热障涂层热循环寿命达到895周次,2.4 A下制备的YSZ涂层热循环寿命为675周次。初步表明,不同电子束流下制备的YSZ热障涂层热循环寿命存在明显差异,1.8 A下制备的YSZ热障涂层具有最优异的热循环寿命,约为1.2 A下制备YSZ涂层热循环寿命的2倍,2.4 A下制备的YSZ涂层热循环寿命的1.3倍。
为进一步探究YSZ热障涂层的失效行为,对热循环后不同电子束流下制备的YSZ热障涂层进行截面组织结构分析,如图6所示。首先观察YSZ陶瓷层柱状晶结构变化,热循环后1.2 A下制备的YSZ陶瓷层柱状晶组织结构相互扩散连接,产生了明显的烧结,在陶瓷层内部出现纵向和横向裂纹并发生扩展(图6(a-2)),这是由于柱状晶间的烧结降低了涂层的应变容限,热循环时即会产生裂纹而释放循环应力,因此,该YSZ陶瓷层存在由于烧结而引起的陶瓷层失效;而1.8 A和2.4 A下制备的YSZ陶瓷层在热循环后,柱状晶组织结构存在少量烧结,但仍为完整的柱状晶结构,2.4 A下制备的陶瓷层(S3)柱状晶形貌更加明显,而热循环时间更长的1.8 A陶瓷层(S2)存在部分柱状晶粘连,烧结程度更高,因此,随着柱状晶组织的生长粗化,陶瓷层的抗高温烧结性能也不断提高。观察热障涂层的TGO层显微形貌变化,由图6(a-2)可知,1.2 A下涂层的TGO层生长较薄,符合较低热循环次数的结果,且没有明显的TGO裂纹出现,即较薄的TGO层累积的界面应力较低,表明1.2 A下热障涂层无TGO层生长产生的层间失效;而2.4 A下涂层TGO层界面处存在明显的裂纹,表明其TGO层处应力累积超出应力极限,存在TGO层生长失效,而高电子束流的粗大柱状晶组织排列结构决定了热障涂层界面具有较低的应变容限,易于在热循环过程中由于应力累积而产生界面裂纹;1.8 A下制备的热障涂层则表现出了不同的失效行为,由于其热循环时间最长,TGO层生长最厚,产生了较大的界面应力累积,界面出现部分裂纹;此外,其YSZ陶瓷层内部也出现了一定程度的烧结,并存在内部横向和纵向裂纹(图6(b-2)),同样是由其热循环时间长所致,因此,涂层主要失效为TGO层生长失效,同时存在由于长时间高温烧结产生的陶瓷层裂纹。
根据前人研究,高温服役过程中热障涂层存在多种失效机制,其中一种典型的失效行为是陶瓷层应力分层失效,主要原因是高温服役过程中陶瓷层不断地进行原子扩散,柱状晶相连成块体陶瓷,产生烧结,而在冷热循环过程中,块体陶瓷内部产生应力累积,烧结处萌生应力裂纹并不断扩展,造成陶瓷层剥落失效[26-27];另一种典型的失效行为是TGO层生长失效,在高温环境下,由于选择性氧化作用在陶瓷层和金属黏结层之间生长产生TGO层,其主要成分为Al2O3,而TGO层的不断增厚会造成Al2O3内部的应力累积,并且随着Al元素的氧化消耗而出现氧化镍、氧化铬等形成的尖晶石脆性相,当TGO层达到临界增厚状态,应力累积超过陶瓷层和金属黏结层间的应变容限时,TGO层内部在应力累积作用下造成裂纹的萌生和不断扩展,最终导致涂层剥落失效[28-29]。
如前所述,不同电子束流的EB-PVD工艺会制备出不同显微组织结构的YSZ陶瓷层,如图7所示。较低电子束流EB-PVD工艺中,在基体表面形成纤细柱状晶结构YSZ层,枝晶多且致密度低;较高电子束流EB-PVD工艺中,在基体表面形成粗大柱状晶结构YSZ层,柱状晶排列规则且结构致密。经过1150 ℃热循环测试,发现纤细柱状晶结构及疏松排布下,YSZ柱状晶间更容易发生原子扩散,引起涂层烧结,并导致烧结裂纹的萌生扩展,但纤细柱状晶更多的间隙排布使得陶瓷层与黏结层间的应变容限大幅提高,TGO层临界增厚值增大,造成该结构热障涂层在TGO层未增厚至临界状态时即发生陶瓷层的剥落失效,烧结应力失效成为其主要失效行为;而在粗大柱状晶及致密排布下,YSZ柱状晶间不易发生原子扩散,抗烧结性能大幅提高,但较为粗大的柱状晶排列更加致密,陶瓷层和金属黏结层间应变容限低于纤细柱状晶结构的应变容限,TGO层更易达到临界增厚状态,在其冷热循环过程中,TGO层处的应力裂纹较早出现并且发生扩展,造成涂层剥落失效,TGO层生长成为其主要失效行为。
综上所述,1.2 A的较低电子束流EB-PVD工艺制备的YSZ热障涂层在热循环过程中更易于产生烧结应力失效,2.4 A的较高电子束流EB-PVD工艺制备的YSZ热障涂层在热循环过程中更易于产生TGO层生长失效,而1.8 A电子束流EB-PVD工艺制备的YSZ热障涂层柱状晶结构适中,一方面可起到一定的抗柱状晶烧结性能,另一方面适中的柱状晶尺寸排列可大幅提高层间应变容限,在冷热循环过程中,有效平衡烧结应力失效和TGO层生长失效,通过形貌观察,其主要失效行为仍为TGO层生长失效,并伴有陶瓷层产生的烧结裂纹,表明其TGO层生长和陶瓷层烧结基本同时达到热循环寿命极限,并且达到TGO和陶瓷烧结两种失效模式的平衡状态,因此,1.8 A电子束流下可获得更为优异的热循环寿命。此外,不同电子束流未造成涂层的成分偏析行为,因此不存在成分差异引起的相变体积膨胀等涂层失效行为。
3 结论
(1)不同电子束流下EB-PVD制备的YSZ热障涂层均为亚稳四方相结构,随着电子束流的增加,柱状晶尺寸逐渐增大,1.8 A下制备涂层中的纳米孔柱状晶结构使得热导率略微降低。
(2)1.2,1.8,2.4 A电子束流下制备的YSZ涂层分别具有三角状、金字塔状、山脊状的柱状晶尖端结构,且随着电子束流的增加,单根柱状晶由纤细结构转变为粗大结构且枝晶逐渐减少,柱状晶排列结构由相互干涉逐渐转变为有序排列。
(3)1.8 A下制备的YSZ热障涂层热循环寿命可达895周次,为1.2 A下制备的YSZ热障涂层热循环寿命的2倍,2.4 A下制备的YSZ热障涂层热循环寿命的1.3倍。
(4)热循环过程中,低电子束流制备的纤细柱状晶结构YSZ涂层优先出现的失效行为是烧结引起的陶瓷层内应力失效,高电子束流制备的粗大柱状晶结构YSZ涂层优先出现的失效行为是TGO层生长引起的应力失效,1.8 A下制备的YSZ热障涂层可平衡两种失效行为,有效延长热循环寿命。
免责声明:本网站所转载的文字、图片与视频资料版权归原创作者所有,如果涉及侵权,请第一时间联系本网删除。
相关文章
无相关信息
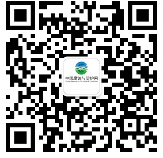
官方微信
《腐蚀与防护网电子期刊》征订启事
- 投稿联系:编辑部
- 电话:010-62316606
- 邮箱:fsfhzy666@163.com
- 腐蚀与防护网官方QQ群:140808414
点击排行
PPT新闻
“海洋金属”——钛合金在舰船的
点击数:10028
腐蚀与“海上丝绸之路”
点击数:7814