热障涂层(thermal barrier coatings,TBCs)系统由陶瓷层(top coating,TC)、黏结层(bond coating,BC)和基体组成,是迄今为止最先进的热端部件涂层防护体系[1-3]。在服役过程中,黏结层表面形成以Al2O3为主的热生长氧化物(thermally grown oxide,TGO)层[4],而TGO生长到一定厚度后涂层会剥落,严重降低涡轮叶片的使用寿命,对发动机的使用可靠性构成很大威胁[5-7]。研究表明,在陶瓷层沉积之前对黏结层进行热处理(扩散处理)可以显著提高TBCs性能[8-9],经扩散处理后的TBCs系统既有较强的抗氧化能力,又可从一定程度上避免涂层剥落[10-12]。目前,对已应用TBCs系统的发动机叶片进行扩散处理是提高其使用寿命的一种有效工艺。扩散处理可以提高黏结层的黏结强度,降低孔隙率,增加黏结层与基体界面的冶金结合比例[13-16]。另外,扩散处理可使黏结层表面形成一层较薄的TGO,服役期间TGO可有效抑制氧气扩散,进而提高其服役寿命[17-20]。目前,工业生产中常采用800~1100 ℃的扩散温度,而关于更高扩散温度对涂层影响的研究报道较少[8]。本工作采用真空电弧镀技术在DD6合金基体上制备NiCoCrAlYHf涂层(HY5涂层),经不同扩散温度(900,1050,1080 ℃和1100 ℃)处理后,采用电子束物理气相沉积技术沉积陶瓷涂层,通过分析不同扩散温度下黏结层的相组成和微观组织形貌,进而对不同扩散温度下热障涂层的循环氧化性能进行探究。
1 实验材料与方法
1.1 实验材料
基体材料选用镍基单晶高温合金DD6棒材,采用线切割从DD6高温合金棒上加工出尺寸为30 mm×10 mm×1.5 mm的片状试样。首先对试样进行吹砂处理,工作压力为0.2 MPa,吹砂后清洗、吹干,然后采用真空电弧镀(arc ion plating,AIP)工艺制备HY5涂层,沉积时间为100 min,涂层厚度为20~40 μm。DD6和HY5涂层的化学成分见表1。
HY5涂层制备完成后,在真空度小于1.0×10-2 Pa的真空炉中进行扩散,扩散温度分别为900,1050,1080 ℃和1100 ℃,达到设置温度后保温3 h,随后炉冷,最后采用电子束物理气相沉积(EB-PVD)方法沉积厚度为80~120 μm的陶瓷涂层。
1.2 循环氧化实验
依据HB 5258《钢及高温合金的抗氧化性测定试验方法》进行热冲击实验。将涂覆热障涂层的30 mm×10 mm×1.5 mm试样放入1150 ℃高温循环氧化炉(DC-B/14)中,保温55 min,出炉后冷却5 min,在规定的周期数称量试样,试样质量变化ΔG≤0时,停止实验。
1.3 表征方法
采用X射线衍射仪(XRD,Bruker D8 Advance),分析黏结层表面的相结构,扫描范围为10°~90°。采用扫描电子显微镜(SEM,ZEISS Sigma300)和能谱仪(EDS)对黏结层试样表面的微观结构和元素分布进行表征。
2 结果与分析
2.1 扩散温度对黏结层相组成的影响
采用XRD对不同扩散温度处理后的黏结层表面相结构进行表征,通过MDI jade6软件与标准相衍射峰进行比对,确定黏结层表面的相结构,如图1所示。可以看出,不同扩散温度处理3 h后,黏结层表面主要为β-NiAl相和γ′-Ni3Al相。经过不同扩散温度处理后,黏结层试样表面均出现β-NiAl衍射峰。通常沉积态涂层主要由γ′-Ni3Al相组成。可知扩散后黏结层中的β-NiAl是从沉积态涂层的γ′-Ni3Al基体相中析出的。并且,扩散温度越高,黏结层试样表面的β-NiAl衍射峰越高,表明随着扩散温度的升高,β-NiAl在黏结层中的含量随之增加。原因可能是,扩散过程中受高温的影响,黏结层中Al元素扩散,导致β-NiAl相从黏结层中的γ-Ni3Al相中析出[21]。综上所述,真空环境下扩散处理后的黏结层试样由沉积态的单相结构转变为扩散处理后的双相结构。与沉积态γ/γ′相相比,具有体心立方结构的β-NiAl相作为Al的富集相,有利于形成连续致密的α-Al2O3氧化层,其抗氧化性能更优[22]。
图2为不同扩散温度下黏结层的表面形貌。可知,扩散处理后涂层表面均匀、致密,但有团簇状凸起并伴有缺口存在。通过对比分析发现,随着扩散温度的提高,涂层孔隙率降低。涂层上的缺口位置(凹陷处)形成了Al2O3,涂层表面的凹陷处被Al2O3填充,使得黏结层表面变得平坦。这是由于随着扩散温度的升高,涂层表面的颗粒氧含量逐渐增加[23]。
图3为不同扩散温度下黏结层的截面形貌。可以看出,由于涂层和基体元素的扩散,界面上出现扩散区。沉积态涂层一般为单相结构(γ-Ni和γ'-Ni3Al相),其成分与原靶材相似。对截面形貌进行分析,在扩散处理后的涂层中观察到灰白色相和黑色相,这证明扩散处理可以改变黏结层的相结构,这与XRD的结论相一致。结合XRD结果可知,扩散处理后HY5涂层由单相结构转变为双相结构,其中黑色相为β-NiAl,灰白色相为γ-Ni和γ'-Ni3Al。
2.3 扩散温度对热障涂层性能的影响
对经过不同温度扩散处理的热障涂层试样进行1150 ℃的循环氧化实验,图4为对应的循环氧化增重曲线。循环氧化增重曲线可分为3个阶段;第1阶段,快速氧化增重;第2阶段,缓慢氧化增重;第3阶段,逐渐减重。与其他温度扩散的涂层相比,900 ℃扩散的涂层循环氧化寿命最长,超过400 h,1100 ℃扩散处理的涂层循环氧化寿命最短,不到300 h。这是由于,扩散温度较低时,涂层的孔隙率较大,表面未形成致密的Al2O3;当扩散温度过高时,涂层已经非常致密。但是在扩散过程中,氧化速率过高,导致球形Al2O3与混合氧化物的形成,破坏了TGO的完整性。
为了进一步阐明扩散温度对黏结层氧化行为的影响,研究不同扩散温度下黏结层试样的TGO厚度随循环氧化时间的变化,如图5所示。可以看出,TGO增厚可分为两个阶段:(1)TGO增厚速率较高;(2)TGO增厚速率较低。氧化过程中TGO增厚与质量变化相似。其中,扩散温度为900 ℃时,黏结层的氧化速率和TGO增厚速率最低。
由于氧在陶瓷层中具有较高的扩散速率,陶瓷层起不到阻碍氧传输的作用。氧先进入陶瓷层,再通过陶瓷层扩散到达黏结层[24]。氧进入陶瓷层分为两步:第一步,氧分子在陶瓷层的表面吸附,并分解成氧原子,
;第二步,吸附在表面的氧原子的离化,Oa⇒O2-+2P+。

图6为TGO生长的示意图。TGO的生长包括:(1)向外生长,黏结层中的Al离子通过TGO向外扩散,在TGO/TBC界面与O反应生成Al2O3;(2)向内生长,O向内扩散,通过TGO在TGO/BC界面与黏结层表面的Al反应生成Al2O3 [24]。TGO的厚度h包括向外生长的厚度h 0和向内生长的厚度h i(即h=h 0+h i)。当TGO增长到一定厚度时,导致应力增加,最终引起陶瓷层的脱落[25-26]。所以,从抗氧化性能的角度考虑,相组成中并非β-NiAl相的含量越多越好,而是存在阈值,在阈值以内提高β-NiAl相含量才能获得更好的服役性能。
3 结论
(1)扩散处理后涂层表面均匀、致密,黏结层由γ′相单相结构转变为γ′相和β相双相结构,随着扩散温度升高,β相含量增加。
(2)900 ℃扩散处理的涂层循环氧化寿命最长,超过400 h;1100 ℃扩散处理的涂层循环氧化寿命最短,不到300 h。扩散温度为900 ℃时,黏结层的氧化速率和TGO增厚速率最低。
(3)相组成中并非β-NiAl相含量越多越好,而是存在阈值,在阈值以内提高β-NiAl相含量才能获得更好的服役性能。
免责声明:本网站所转载的文字、图片与视频资料版权归原创作者所有,如果涉及侵权,请第一时间联系本网删除。
相关文章
无相关信息
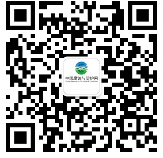
官方微信
《腐蚀与防护网电子期刊》征订启事
- 投稿联系:编辑部
- 电话:010-62316606
- 邮箱:fsfhzy666@163.com
- 腐蚀与防护网官方QQ群:140808414
点击排行
PPT新闻
“海洋金属”——钛合金在舰船的
点击数:10028
腐蚀与“海上丝绸之路”
点击数:7814