旋流器是航空发动机中关键的零部件之一,其可在火焰筒头部形成回流区,降低气体流速,使火焰筒头部产生稳定火源,起到稳定燃烧室的重要作用[1-2]。随着航空工业的快速发展,对飞机机动性、稳定性的要求不断提高,这也对航空发动机性能提出了更高要求[3-4]。在众多高温结构材料中,TiAl合金因具有低密度、高熔点、高比强度、优异的高温强度及抗氧化等优点,成为一类介于镍基、钴基高温合金和先进陶瓷材料之间理想的新型轻质高温结构材料,展现出替代传统高温合金的巨大潜力,因此成为航空发动机实现轻量化、提高推重比的重要材料[5-7],尤其适用于轻质高性能旋流器的制造。经过多年发展,TiAl合金在国外已经开始工程化应用,如美国GE公司研发的铸造Ti-48Al-2Cr-2Nb合金已于2007年应用于波音787飞机的第6,7级低压涡轮叶片[8]。目前,TiAl合金的制备工艺主要为精密铸造[9-10],但由于合金化程度较高,铸造TiAl合金往往存在严重的成分偏析和组织不均匀等问题[11],同时铸造过程中易产生夹杂、疏松、晶粒粗大等缺陷,导致材料成品率低,力学性能较差。加之多层壁结构旋流器的结构较为复杂,而TiAl合金本身室温塑性差[12],加工成形困难,制造成本高,严重限制其工程化应用水平。与铸造工艺相比,粉末注射成形(powder injection molding,PIM)将传统粉末冶金与现代塑料注塑技术相结合,能够极大程度地克服精密铸造过程中产生的冶金缺陷,并可直接制备三维复杂形状零部件,避免或减少了机加工过程,材料利用率接近100%,易于实现批量化生产,是一种节约资源、能源的低成本制造技术,有望为复杂形状TiAl合金的近终形批量化制备提供新的解决途径[13-14]。
黏结剂的选用与脱除是粉末注射成形的核心环节[15],黏结剂作为临时载体,承担着使原料粉末以流体状态顺利填充型腔并维持生坯形状至预烧结阶段的重要作用。目前,以石蜡为主组元的蜡基黏结剂已被广泛研究[16],但因其脱脂时间长、制件尺寸精度低等问题,逐渐在实际生产中被取代。聚甲醛(POM)基黏结剂所制备生坯强度高,催化脱脂时主组元聚甲醛可实现直接由固态到气态的转变而除去,避免了黏结剂成分因沸腾引起的膨胀、裂纹等缺陷,脱脂时间短、脱脂效率与尺寸精度高,能有效减少TiAl合金注射成形过程中杂质的引入,成为当前研究的重点[17-18]。此外,PIM烧结致密化行为主要受元素扩散控制,但由于Ti,Al元素间的互扩散系数差异大,导致粉末TiAl合金常压烧结致密化困难[19-20]。为提高粉末烧结致密化程度,通常采用靠近TiAl合金液相线温度进行烧结,然而高温烧结条件下晶界迁移速度快,往往会造成晶粒组织异常长大,导致制件力学性能受限[21]。常压两步烧结方法基于晶界迁移激活能在不同温度区间的差异来调控烧结致密化和晶粒长大进程[22-23],有望通过调节烧结工艺实现TiAl合金高致密化的同时晶粒不发生明显长大,从而改善合金室温脆性,并平衡和提高其综合力学性能。
旋流器截面尺寸差异较大,环形轮廓上分布着上下贯通的细薄叶片,且在环形一侧还存在“倒T形”特征结构。对于粉末注射成形零部件而言,较大的厚度差异以及环状凸形结构特征易造成生坯脱模困难,致使在脱模过程中坯体产生变形、裂纹等缺陷,严重影响产品质量及尺寸精度,制备难度较大。为此,本工作采用水溶性芯模的模具设计方法以解决旋流器特征结构限制开模问题,并以Ti-48Al-2Cr-2Nb预合金粉末为原料,设计和制备出高粉末装载量的催化脱脂型TiAl合金喂料,研究其流变行为及脱脂规律,对比分析不同烧结工艺下合金的显微组织及孔隙特征,结合优化的两步烧结工艺制备出接近全致密的TiAl合金旋流器样件,并对其特征位置的尺寸精度及表面粗糙度等性能进行验证评估。本研究旨在为复杂形状TiAl合金的低成本、高精度、高性能制备提供一种可行方法,并为拓展TiAl合金在航空航天领域的应用提供技术支撑。
1 实验材料与方法
1.1 实验材料
实验所用粉末原料为气雾化法制备的球形Ti-48Al-2Cr-2Nb预合金粉末(中航迈特粉冶科技有限公司),中位径D 50=14.8 μm,粉末形貌及粒度分布如图1所示;选用市售分析纯聚苯乙烯(PS)为水溶性模芯材料、分析纯三氯乙烯作为溶剂以溶解去除PS;选用市售分析纯聚甲醛、高密度聚乙烯(HDPE)、乙烯-醋酸乙烯共聚物(EVA)和硬脂酸(SA)为黏结剂组元,制备成三种不同成分的催化脱脂型注射喂料(F1,F2,F3),三种喂料的黏结剂配比如表1所示。
注射喂料制备及成形:将粉末与黏结剂在高纯氩气保护的Universal型手套箱中进行预混合,封装后在CF-1L型气氛保护密炼机中制备喂料,混炼温度为190 ℃,混炼时间为1.5 h;冷却后取出在CF-2HP破碎机中制成粒状喂料,然后在ZE600Ⅲ型注射机上注射成形出水溶性模芯和旋流器零件生坯,旋流器生坯的注射温度为180 ℃,注射速度为40 mm/s,保压压力为110 MPa,保压时间为3 s,模具温度为110 ℃,旋流器模型示意图如图2所示。
脱脂及烧结:在自制溶剂脱脂装置中脱除PS模芯,脱脂温度为50 ℃,脱除时间为4 h;随后在DZF-6022型真空干燥箱中进行烘干处理;之后在STZ-C200型草酸催化脱脂炉中进行催化脱脂处理,脱脂温度分别为125,135 ℃和145 ℃,草酸通入速率分别为1.8,2.0 g/min和2.2 g/min;最后在VS-50MDI型真空脱脂烧结炉中进行热脱脂和烧结处理,热脱脂工艺根据喂料的热分析曲线确定,烧结方法采用两步烧结工艺,具体工艺如下:首先从室温升高至1450 ℃或1430 ℃,保温1 h,然后再以5 ℃/min降温至1250 ℃,保温5 h后炉冷,获得旋流器烧结体,烧结工艺分别记为工艺1和工艺2。
热等静压(hot isostatic pressing,HIP)处理:将上述所制备的烧结体在QIH-9型热等静压炉中进行后处理以闭合孔隙,烧结温度为1250 ℃,烧结压力为180 MPa,保温时间为4 h,升温速率为5 ℃/min。
1.2 实验方法
采用Ultra PYC 1200e型真密度测量仪对不同黏结剂含量的喂料进行全自动密度测试;采用MLW-400A型毛细流变分析仪对所制喂料进行不同温度、不同剪切速率下的黏度测试,分析喂料的流变特性,料筒直径为12 mm,毛细管长径比为10∶1;利用Archimedes排水法测量TiAl合金样品的致密度;采用Kroll试剂对TiAl合金进行侵蚀处理,试剂成分为HF∶HNO3∶H2O=1∶2∶17(体积比);采用FEI 450型扫描电镜(SEM)观察粉末形貌、合金显微组织及拉伸断口形貌;采用游标卡尺对旋流器不同特征部位进行尺寸测量,相同尺寸部位重复测量3次并取平均值作为最终测试结果;采用NewView9000型3D白光干涉仪对旋流器样件非加工表面进行粗糙度测试,为提高测试准确率和可重复性,选取3个区域进行测量,并以3次测量结果的平均值作为最终测试结果;采用INSTRON万能材料试验机进行室温拉伸测试,应变速率为1×10-3 s-1,拉伸试样与旋流器同批同炉,形状为“狗骨形”,标距直径为5 mm,长度为40 mm,以3次测量结果的平均值作为最终测试结果。
2 结果与分析
2.1 模具设计
2.1.1 水溶性模芯
对于PIM技术而言,制件在注射成形过程顺利脱模是保证最终产品尺寸精度的基础。旋流器局部存在的“倒T形”结构特征在注射成形过程中严重限制开模,导致注射生坯难以顺利从模具中脱出。为此,采用水溶性芯模的模具设计方法,在制备旋流器之前,成形出契合“倒T形”结构的水溶模芯,利用水溶性PS聚合物填充难开模区域,制备出带有模芯的旋流器生坯,再以三氯乙烯为脱脂溶剂,通过溶剂脱脂过程去除多余模芯,从而避免“倒T形”结构给脱模过程带来的不利影响,“倒T形”结构如图3(a)所示,模芯结构及注射过程中其与旋流器型腔的装配方式如图3(b)所示。
2.1.2 最佳浇口位置
为获得合理浇口位置,采用工业应用较为成熟的Moldflow模流分析软件对旋流器最佳浇口位置进行数值模拟,通过评价浇口匹配性和流动阻力指示器指标指导浇口位置的设计[24]。由于旋流器样件尺寸较大,故采用3D网格进行有限元网格划分,网格类型为四面体网格,共有854177个网格单元,平均纵横比为6.44。浇口位置分析结果如图4所示,其中图4(a)所示为旋流器的浇口匹配性云图,蓝色区域表示浇口匹配性较好的区域范围,红色区域表示浇口匹配性较差的区域,中间为过渡区域。可以看出,在临近旋流器中心的环形位置处具有较佳的浇口匹配性,而靠近外侧及叶片部位的浇口匹配性较差。图4(b)为旋流器内部的流动阻力分析结果云图,红色区域为流体在旋流器内部流动所受阻力较大的区域,蓝色区域则为流动较容易的区域。对比可知,图4(b)中显示流动阻力最小的区域与图4(a)中显示为最佳浇口位置的区域基本一致。对于旋流器制件,由于在开模时需要利用水溶性模芯材料填充临近环形的“倒T形”区域,在注射充型过程中热喂料会与冷模芯相接触而产生温度梯度。因此,可以将最佳浇口位置设置在环形位置的中心部位,最大程度地促使接触部位温度实现均匀分布,避免因模芯变形而引起旋流器坯体发生欠注、开裂、变形等缺陷,以获得质量良好的注射坯体,浇口位置设置如图4(c)所示。
2.2 注射喂料性能表征
2.2.1 粉末装载量
图5为三种不同喂料密度随粉末体积分数(粉末装载量)的变化曲线。可以看出,粉末装载量较低时,三种喂料密度变化趋势较为一致。当粉末装载量升高至一定程度后,喂料密度突然转折呈现下降趋势,这个转折点即为喂料临界粉末装载量。三种喂料的临界装载量分别为60%(体积分数,下同)(F1),63%(F2)和65%(F3)。由此可以判断,通过适当调整主组元POM含量可以提高喂料的临界粉末装载量,有助于成形坯体保形性的提高。在实际操作中,由于模具设计不同,一般认为最佳固体粉末装载量比临界粉末装载量低2%~5%[25-26],因此,三种黏结剂装载量分别选择57%(F1),60%(F2)和62%(F3)进行后续实验。
2.2.2 喂料流变行为
对于粉末注射成形来说,喂料呈现假塑性流体特征,喂料剪切速率与黏度的关系可以用式(1) 进行描述:
式中:η为喂料黏度,Pa·s;γ为剪切速率,s-1;K为材料常数;n为流动行为指数。图6为不同温度下三种喂料黏度随剪切速率的变化曲线,表2为三种喂料对应的流动行为指数。从图6可以看出,所设计制备的三种喂料均表现出假塑性流体的剪切稀化特性,黏度随剪切速率的升高而降低,表明其可满足注射成形的要求。n值越大,表明喂料黏度随剪切速率的变化越缓慢,喂料流动充型的稳定性越好,这对旋流器这种形状复杂精密零部件的注射成形尤其重要。但是n值太大则没有剪切稀化效果,喂料流动性变差,将导致喂料无法顺利填充型腔。为了确保顺利完成注射成形过程,在100~10000 s-1之间的剪切速率范围内,喂料黏度应低于1000 Pa·s[27]。从图6还可以看出,在相同温度下,喂料F1, F2和F3的黏度差异较小,而随着温度升高,在相同剪切速率下,三种喂料的黏度都有所下降。值得说明的是,三种喂料的黏度均满足PIM要求。此外,三种喂料的n值均在0.2~1之间,但喂料F3的流动行为指数较低(表2),即使在500 s-1的剪切速率下,黏度也低于1000 Pa·s(180 ℃),表明喂料F3更适合注射成形工艺。
除了剪切速率外,温度也对喂料黏度有重要影响。随温度升高,喂料黏度随之降低,温度的升高导致黏结剂分子发生平直化,使得黏结剂分子之间的排斥力增加。温度对黏度的影响关系到热激活过程,其关系可用Arrhenius方程描述[28]:
式中:η为喂料黏度,Pa·s; 为特定剪切速率下的参考黏度,Pa·s;E为黏流活化能,kJ·mol-1;R为气体摩尔常数;T为绝对温度,K。图7为不同剪切速率下三种喂料黏度与温度的变化曲线图。黏流活化能E的大小体现了喂料对温度的敏感程度。对式(2) 两边取自然对数,作
曲线可求得E值。图7对比分析了在三种不同测试温度下,剪切速率由500 s-1到8000 s-1剪切速率范围内的黏度变化,通过线性拟合可得不同喂料在不同测试条件下的E值。由图7可知,三种喂料在相同或相近剪切速率下,E/R值基本处于同一水平。如在接近注射条件下(剪切速率约为2000 s-1),三种喂料的黏流活化能分别为21.32,23.78,22.95 kJ/mol,表明温度对三种喂料的黏度敏感性差异较小。通常对于结构复杂的零部件而言,喂料的E值越小,则温度变化对喂料黏度值影响就越小,喂料的注射温度范围变宽,且喂料进入型腔后黏度变化小,可避免试样因应力集中导致的内部开裂、变形等缺陷,有利于提升注射生坯质量,获得高性能PIM制件。

综合流变学因子α STV可以用来综合评价粉末注射成形喂料的流变性能,包括喂料黏度、黏度对温度的敏感性以及黏度对剪切速率的敏感性等流变学主要参数,可用式(3) 表示:
在TiAl合金粉末注射成形工艺中,对喂料要求黏度小,流动行为指数小,黏流活化能小。显然,α STV值越大,设计制备的TiAl合金注射喂料的综合流变学性能越好[29]。在180 ℃,2000 s-1测试条件下不同黏结剂配方所制喂料F1,F2,F3流变性能的综合流变学因子α STV值分别为8.78,7.48,9.59。而喂料F3的综合流变学因子高于其他两种喂料,表明所制喂料的综合流变性能最佳。因此,本研究优选F3黏结剂所制喂料进行TiAl合金旋流器的制备。
2.3 黏结剂脱除行为
2.3.1 脱脂温度与草酸通入速率对催化脱脂率的影响
为研究脱脂温度、脱脂时间与草酸通入速率对生坯脱脂率的影响,测量了不同脱脂温度和草酸通入速率下注射生坯的催化脱脂率,如图8所示。结果表明,在不同脱脂温度下,脱脂率均随脱脂温度的升高和脱脂时间的延长而增加。当草酸通入速率为1.8 g/min、脱脂温度为125 ℃时,脱脂率增长较慢,脱脂时间延长至14 h仍难以完全脱除POM,如图8(a)所示;草酸通入速率保持不变、脱脂温度升高至135 ℃时,经12 h脱脂后脱脂率达到98.4%(图8(b));进一步升高至145 ℃后,经12 h脱脂后脱脂率提升至99.1%,但仍然难以完全脱除POM(图8(c))。当草酸通入速率为2.0 g/min、脱脂温度为125 ℃时,经14 h脱脂后脱脂率可超过99%,且温度升高至145 ℃时,经8 h脱脂后即可完全脱除POM。同样的,当草酸通入速率提高至2.2 g/min时,在135 ℃和145 ℃脱脂温度下POM均可实现完全脱除,但在125 ℃脱脂温度下经14 h也难以完全除去POM。由此可见,草酸通入速率需要高于1.8 g/min、脱脂温度需要高于125 ℃。需要说明的是,当脱脂温度相同时,随草酸通入速率增加,脱脂气氛中草酸浓度增大,会加快POM分解进程。但是过高的草酸通入速率会导致炉腔内的草酸不能及时与聚甲醛发生催化反应,不仅浪费资源,而且会使草酸在炉门、炉腔甚至进酸管道内发生结晶现象,损害脱脂设备,因此,草酸通入速率控制在2.0 g/min。此外,虽然在145 ℃脱脂温度下经8 h便可基本脱除POM,但是高的脱脂速率意味着高的甲醛气体产生速率,若甲醛气体来不及排除则会使炉内气压异常增加,容易导致样品产生内部裂纹、表面气孔等脱脂缺陷。通过上述分析可知,最佳的草酸脱脂工艺参数为脱脂温度135 ℃,草酸通入速率2.0 g/min,脱脂时间10 h。
图9为TiAl合金旋流器注射生坯及催化脱脂坯的微观形貌图。从图9(a)可以看出,注射生坯中黏结剂均匀包裹在粉末颗粒表面,使粉末颗粒之间具有良好的润湿性,可以保证注射过程中顺利充满整个旋流器型腔。经催化脱脂后,TiAl合金粉末表面粗糙度降低(图9(b)),这主要是由POM的去除引起的。此外,从图9(a)还可以看出,催化脱脂后粉末颗粒之间形成了许多贯通孔隙,这些孔隙可以充当快速脱脂通道以便后续热脱脂去除剩余黏结剂组元。催化脱脂后剩余的少量黏结剂组元可从图9(b)中清晰观察到,其成分主要为高熔点HDPE骨架剂和低熔点EVA,SA相容剂组元。
2.3.2 热脱脂工艺及脱脂效果分析
为制定高效热脱脂工艺,对喂料进行了DSC-TGA测试以分析不同组元的热分解行为。图10(a)所示为喂料F3的DSC-TGA曲线,可以看出,黏结剂的热分解大致分为三个阶段,第一阶段为255~330 ℃,失重峰值为303 ℃,表示低分子量的SA发生热解及EVA的部分链段发生裂解,该阶段失重率为2.48%;第二阶段为330~420 ℃,失重峰值为364 ℃,对应主组元POM的分解,此外,在这个温度区间内部分HDPE也开始发生热解,该阶段失重率为13.51%;第三阶段为420~497 ℃,失重峰值为451 ℃,对应剩余EVA链段和HDPE的全部分解,该阶段失重率为1.26%,表示剩余HDPE完全热解脱除。经计算总的失重率为17.25%,黏结剂脱脂率已达到99.71%,表明黏结剂已几乎完全脱除。在脱脂过程中,黏结剂热解时残留的气态产物可以通过脱脂形成的开孔逸出。图10(b)为根据喂料DSC-TGA曲线制定的TiAl合金热脱脂工艺路线图,热脱脂阶段设置四个保温脱脂阶段,分别为300,360,450,600 ℃。采用较低的升温速率和较长的保温时间是为了保证低分子量黏结剂组元缓慢、完全脱除,从而形成连通孔隙通道为进一步热脱脂做好准备。图10(c)为TiAl合金旋流器生坯热脱脂后的微观形貌图。可以看出,经热脱脂后粉末颗粒间基本形成了点接触以维持脱脂坯不变形,且粉末表面洁净,无明显黏结剂残留,表明所制定的热脱脂工艺合理可行。
表3所示为TiAl合金原料粉末、热脱脂坯与烧结体中的杂质含量。可以看出,热脱脂坯中的C,O,N含量均高于原料粉末,这主要是因为高活性的TiAl合金粉末与黏结剂中POM,HDPE等组元的热解产物发生反应以及存在微量黏结剂残留。随着烧结过程的进行,坯体中残留的黏结剂完全分解并从脱脂通道中去除,因此烧结体中的C,O,N含量较之脱脂坯有所下降。相较于原料粉末,烧结体的氧增量较小,约为0.032%(质量分数)。较低的氧增量水平主要得益于PIM过程中的控氧方式,如在高纯氩气保护的手套箱和密炼机中进行预混合与混炼,真空干燥箱中进行干燥处理,真空条件下进行热脱脂和烧结处理等。
2.4 烧结致密化及性能分析
2.4.1 烧结温度对合金显微组织的影响
图11为不同烧结工艺下PIM TiAl合金的显微组织。从图11(a)可知,工艺1所得烧结体主要由γ/α2片层团组成,且晶粒较为粗大,存在较多的大尺寸圆形孔隙,孔隙主要分布于γ/α2片层间,经Archimedes排水法测量可知其致密度为93.2%。如图11(b)所示,当保持低温温度1250 ℃不变,而将高温温度降低至1430 ℃时,烧结体中出现少量分布于γ/α2片层团间的等轴γ晶粒,γ/α2片层团尺寸明显减小,约为100 μm,且片层间距变小。此外,该工艺下烧结体的孔隙尺寸和数量明显减少,孔隙分布位置并未发生明显改变,致密度提升至96.3%。这是因为烧结温度较高时(1450 ℃),晶界迁移能力迅速激增,晶粒长大速率提高,存在于片层团处的孔隙难以发挥对晶界的钉扎作用,晶粒的快速长大使得孔隙来不及消除就被保留在晶粒内部,并导致烧结组织粗化;而当烧结温度降低时(1430 ℃),虽然晶界迁移在此阶段仍占据主导地位,但由于能量输入减少,晶界迁移速率相对较低,界面处存在的孔隙能够对晶界起到有效钉扎作用而使晶粒不粗化,经较低温度下长时间烧结后,晶界扩散作用使高温残留孔隙被大幅消除,从而使烧结体兼具高致密化和细晶特征。为进一步消除孔隙,提升合金致密度及力学性能,对工艺2所制烧结体进行了热等静压处理,其显微组织如图11(c)所示。对比图11(b),(c)可知,经热等静压处理后片层间残留的孔隙消失,显微组织形态及片层团尺寸并未发生明显改变,表明热等静压工艺较为合理。此外,由上述不同烧结工艺下的组织形态可知,TiAl合金的显微组织形态对高温烧结温度较为敏感,因此,在制备过程中尤其需要保证烧结温度的精确控制,有助于获得性能稳定的PIM TiAl合金制件。图12为旋流器注射生坯及烧结体(热等静压处理后)正、反两面的宏观形貌。可以看出,旋流器注射生坯中含有水溶性模芯材料PS,填充的PS成功避免了“倒T形”结构对开模过程的不利影响,所制备的旋流器生坯质量良好(图12(a))。经脱脂、烧结及热等静压处理后,所制备TiAl合金旋流器整体收缩均匀,未见明显裂纹等缺陷,且表面具有明显的金属光泽,表面质量较为良好(图12)。
2.4.2 旋流器尺寸精度分析
图13为旋流器模型中各部位的特征尺寸,其中位置1为样件的横向最大尺寸位置,位置2为样件的高度最大尺寸位置,位置3为样件上表面中心圆形位置,位置4为样件中心叶片的外侧圆位置,经测量原始模型4个位置处的尺寸分别为79,15,24 mm和64 mm。利用游标卡尺对热等静压处理后制备的旋流器样件对应位置尺寸进行了测量,统计结果如表4所示。经测量可知,旋流器样件4个特征位置处的实际尺寸分别为78.96,15.01,24.04 mm和63.91mm。与相应的理论尺寸对比可知,4个特征位置处的尺寸偏差分别为-0.04,+0.01,+0.04 mm和-0.09 mm,尺寸偏差在±0.1 mm范围内,表明PIM技术制备的TiAl合金旋流器制件具有较高的尺寸精度。
2.4.3 旋流器表面质量分析
式中:R a为平均表面粗糙度;N为采样点总数;Zi 为第i个采样点的高度;Z avg为高度的平均值。经计算可得,所选位置A,B和C的表面粗糙度分别为1.062,0.848 μm和1.229 μm,3次测量的平均值为1.046 μm,优于常规激光选区熔化(R a≈10 μm)及精密铸造技术水平(R a≈6.3 μm)[30-31]。
2.4.4 室温力学性能
为全面评估TiAl合金旋流器质量,采用旋流器制件的同批同炉拉伸试样进行了室温拉伸性能测试,测试结果及相关研究报道数据汇总列于表5 [32-35]。真空烧结态TiAl合金的抗拉强度为388 MPa,几乎没有塑性;经热等静压处理后,合金的极限抗拉强度(ultimate tensile strength,UTS),屈服强度(yield strength,YS),断后伸长率(elongation at break,EL)分别达到577,466 MPa,0.96%,较之烧结态均有较大程度的提升。烧结态TiAl合金中存在较多孔隙,样品在拉伸过程中这些孔隙极易成为裂纹源,从而导致合金过早断裂失效。热等静压处理后,基本消除了合金中存在的孔隙,大幅提升了烧结态TiAl合金的致密度,样品接近全致密,几乎消除了样品本身孔隙缺陷在拉伸时的不利影响,使得样品可以承受更大的载荷。此外,对比文献报道数据可知,本研究制备的TiAl合金具有较为良好的室温拉伸性能,且伸长率处于目前报道较高水平。伸长率的提升主要得益于PIM过程中的严格控氧以及最终烧结制件中较低的孔隙率。
图15为烧结态及热等静压处理后TiAl合金拉伸测试后的断口形貌。从两种试样的拉伸断口可以发现,TiAl合金的断裂方式并无明显本质区别,均呈现出室温解理断裂特征,层间断裂、穿晶断裂及河流花样形态如图15所示。此外,烧结态TiAl合金断口(图15(a))中存在较多孔隙,且局部裂纹从孔隙处产生并向外扩展,导致合金塑性较差。TiAl合金中α2与γ两相之间强度差异较大,在拉伸过程中微裂纹倾向在两相片层界面处形核。当片层与裂纹扩展路径形成角度较小时,微裂纹沿着层片间这一路径扩展;否则,微裂纹将沿着晶间或者阶梯状路径扩展。
3 结论
(1)采用水溶性芯模模具设计方法有效解决了旋流器“倒T形”结构限制开模问题,并结合Moldflow模流分析中的浇口匹配性和流动阻力指示器两项评价指标,确定了旋流器环形中心位置为最佳浇口位置。
(2)喂料粉末装载量受主组元POM含量的变化而产生波动,成分为82%POM-5%HDPE-5%EVA-8%SA的黏结剂具有较高的粉末装载量和较佳的充模性能,其流动行为指数n为0.56,黏流活化能E为22.95 kJ/mol,综合流变学因子α STV为9.59;坯体催化脱脂效率随脱脂温度和草酸通入速率的增加而提高,最佳的催化脱脂工艺为脱脂温度135 ℃,草酸通入速率2.0 g/min,脱脂时间10 h。
(3)采用常压两步烧结方法实现了高致密度和细晶的协同控制,在1430 ℃/1 h+1250 ℃/5 h烧结工艺下,PIM所制备TiAl合金的致密度达到96.3%,且晶粒未发生明显长大,片层团尺寸约为100 μm,结合热等静压处理实现了TiAl合金的近全致密化。所制备TiAl合金旋流器具有较高的表面质量,特征部位尺寸偏差控制在±0.1 mm范围内,非加工表面粗糙度R a为1.046 μm,优于常规激光选区熔化及精密铸造技术水平;热等静压处理后TiAl合金室温抗拉强度、屈服强度、伸长率分别达到577,466 MPa,0.96%。
免责声明:本网站所转载的文字、图片与视频资料版权归原创作者所有,如果涉及侵权,请第一时间联系本网删除。
相关文章
无相关信息
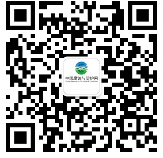
官方微信
《腐蚀与防护网电子期刊》征订启事
- 投稿联系:编辑部
- 电话:010-62316606
- 邮箱:fsfhzy666@163.com
- 腐蚀与防护网官方QQ群:140808414
点击排行
PPT新闻
“海洋金属”——钛合金在舰船的
点击数:10028
腐蚀与“海上丝绸之路”
点击数:7814