近年来,相变诱导塑性(transformation induced plasticity, TRIP)中锰钢因具有优异的综合力学性能[1]和相对低廉的生产成本,被认为是第三代汽车用钢的潜在材料。然而,高强塑积中锰钢变形过程存在塑性失稳,导致结构稳定性恶化,特定情况下诱发过早失效,已成为限制其商业化的关键问题[2]。早期研究表明,铝基合金、镁基合金及钢等在特定范围应变速率或温度下表现出局部区域内非均匀变形[3],大致可分为吕德斯(Lüders)带和PLC(Portevin-Le Chatelier)带两类[4],在工程应力-应变曲线上分别显现为屈服平台(Lüders带传播过程)[5-6]或连续起伏的密集型锯齿(PLC带)[7]。PLC带通常分为A型、B型和C型三种类型[8],A型PLC带在特定位置形成,沿拉伸轴向连续传播;B型PLC带沿拉伸轴向跳跃式传播;C型PLC带为静止带,即为空间不相关性。
中锰钢具有多相组织和TRIP效应,并表现出不同类型和程度的塑性失稳行为,机理解释不尽相同。通常认为,PLC带由动态应变时效(dynamic strain aging,DSA)引起,与可动位错累积和溶质原子扩散之间的相互作用有关[9];Lee等[10]认为在Fe-C-Mn系孪晶诱导塑性(twinning induced plasticity,TWIP)钢中DSA效应是C-Mn原子对、堆垛层错能以及位错共同作用的结果。近年来,数字图像相关(digital image correlation,DIC)和红外热像(infrared thermography,IRT)技术被大量采用表征分析拉伸过程中的力学行为、应变场和温度场分布。随着研究的不断深入,发现TRIP中锰钢的塑性失稳行为与应变诱导马氏体相变(strain-induced martensite transformation,SIMT)具有一定的相关性。Yang等[11]研究发现冷轧退火态0.3C-7Mn-2Al(质量分数/%,下同)钢中PLC带内低稳定性残余奥氏体转变为马氏体且PLC带类型随着马氏体含量增加由A+B型转变为A型;Wang等[12]结合DIC和IRT技术对Fe-7Mn-0.14C-0.23Si冷轧退火态中锰钢在拉伸过程中的热源变化进行了详细分析,证明了Lüders带集中发生了SIMT,PLC带内马氏体转变量很有限;Sun等[13]结合DIC和离位X射线衍射(X-ray diffraction,XRD)研究了临界退火态Fe-0.26C-11.6Mn-2.7Al热轧钢拉伸过程中SIMT与应变不稳定性之间的相关性,认为PLC带内局部马氏体间歇成核并连续传播,导致非连续SIMT,塑性失稳和SIMT效应只发生在一定范围内稳定的奥氏体中。Hwang等[14]结合DIC和原位高能X射线衍射系统地研究了冷轧退火态Fe-22Mn-0.6C钢拉伸过程中的塑性失稳,确认锯齿状应力起伏对应着PLC带形成、传播和消失,PLC带形成会导致位错密度的突增,传播过程减轻了弹性应力,导致晶格(弹性)应变下降。
目前,塑性失稳相关研究主要集中于Lüders 带和冷轧中锰钢,高强塑积热轧中锰钢的PLC带相关研究相对较少。虽然可以确定PLC带的形成与传播伴随着应变诱导马氏体相变,但奥氏体稳定性和位错增殖对PLC带的影响机理需要进一步研究。本工作结合DIC和IRT等技术,对临界退火态热轧含铝中锰钢单轴拉伸过程中的宏观力学行为、局部应变场和温度场进行原位观察与研究,分析塑性失稳的具体特征和演变规律。
1 实验材料与方法
实验钢的名义和实测化学成分分别为5Mn-3.2Al-0.35C和5.11Mn-3.25Al-0.35C。利用Thermo-Calc软件和TFCE6.0数据库计算得到奥氏体开始转变温度(A c1)和奥氏体转变结束温度(A c3)分别为675 ℃和966 ℃。采用ZG-25型中频真空感应炉熔炼配制合金原料,在氩气保护下浇注获得柱状铸坯,加工除去氧化皮。铸坯在1250 ℃均匀化退火2 h,而后锻为100 mm(宽)×30 mm(厚)的钢坯,空冷至室温;将钢坯随炉加热至1200 ℃后保温2 h,在 880 ℃开轧经7道次获得7 mm厚钢板,总压下率约为77%,空冷至室温。将热轧淬火钢板置于SG2-5-12型箱式电阻炉内,升温至750 ℃后保温1 h,空冷至室温。具体制备工艺流程如图1所示。为便于表述,将临界淬火态实验钢用IA750标示。
图2(a)为DIC和IRT测量系统示意图,使用 MT-858型拉伸试验机进行单轴拉伸测试,采用AMAMIS 5M非接触式三维应变测量系统获得局部应变,图片采集频率为4帧/秒,采用FLIRA655SC红外热像仪对拉伸过程中温度场进行实时监测;沿着轧制方向使用电火花线切割取样,按图2(b)所示尺寸加工得到标准板状拉伸试样,板厚和标距长度分别为1.5 mm和40 mm,标距段两面分别均匀喷涂散斑漆和石墨,沿拉伸方向标距段依次取7个观测区域,使用ARAMIS GON软件分析处理数据,获得不同宏观应变量下的微区应变,并对拉伸过程中标距段表面温度场进行同步测试。
采用标准流程制取金相样品,经打磨、手动抛光和电解抛光。利用FEI Quanta 650型场发射扫描电镜获得EBSD图像,测试参数如下:工作距离15 mm、扫描步长45 nm、加速电压15 kV和探针电流10 nA,通过专业分析软件Channel 5获得晶界、相组成和晶粒取向等晶体学信息。采用PANalytical Empyrean型X射线衍射仪进行物相分析,实验参数:Cu靶Kα1谱线,扫描角度20°~100°,扫描速度2 (°)/min。采用五峰法[15]计算残余奥氏体含量(volume fraction of retained austenite,V RA)。沿标距段等距离使用HVS-1000Z型自动转塔数显显微硬度计获得不同应变量下(ε=0%,10%,15%,20%,30%,40%和50%)的显微硬度分布,共26个点,每个点测量3次求平均值,加载力为49 N,保荷时间10 s。显微硬度的试样尺寸如图2(c)所示。
2 结果与分析
2.1 单轴拉伸力学行为
图3为IA750实验钢的工程应力-应变曲线及其局部放大图与真应力-真应变和加工硬化率曲线图。如图3(a)所示,IA750实验钢在单轴拉伸过程中从工程应变17.8%开始存在密集型、锯齿状应力起伏,一直持续至颈缩阶段。IA750实验钢的抗拉强度,总伸长率和强塑积分别为948.3 MPa,63.7%和60.4 GPa·%,表现出优异的综合力学性能;如图3(b)所示,真应变达到15.3%时,加工硬化率开始出现较大起伏,约在-20000~43000 MPa之间波动,这与位错的增殖和运动受阻具有密切关系,真应变在0.48~0.5之间,试样开始颈缩直至断裂,加工硬化率出现异常(远低于-20000 MPa),这与截面尺寸陡变和裂纹快速扩展有关,加工硬化率曲线与应力-应变曲线上观察到的锯齿状应力起伏相对应。但较低的屈服强度 (615.5 MPa)和塑性失稳可能对实验钢成形和服役产生不利影响。
2.2 局部应变场和温度场演变
图4(a)为标距段S3区域局部应变(εyy,黑线)、局部应变速率( L,蓝线)及局部温度(T L,红线)随时间变化曲线图。按照局部温度(T L)变化情况,单轴拉伸变形可分为3个阶段:第Ⅰ阶段(t≤20 s,ε≤0.1%),T L小幅下降(0.8 ℃),由热弹性效应所致[16];第Ⅱ阶段(20 s<t<270 s,0.1%<ε<17.8%),T L平稳升高,可能与持续应变诱导马氏体相变及位错增殖等相关;第Ⅲ阶段(t≥270 s,ε≥17.8%),T L呈“波浪形”交替变化,可能与位错增殖以及位错之间交互作用密切相关。另外,随着实验时长和工程应变的增加,εyy 先线性增加而后呈台阶状逐步增加,对应出现 L峰值。εyy 和T L同时发生周期性大幅波动,表明S3区域内存在具有明显热效应和应变增量的PLC带[14]。图4(b)为S3区域不同应变台阶或温度起伏阶段的局部应变差(Δε L,黑色菱形)、应变速率峰值( L ,蓝色圆形)和局部温度起伏差值(ΔT L,红色矩形)的趋势变化。随着局部应变的增长,相邻应变台阶的局部应变差值(Δε L)由0.022(stage 1)逐渐升高至0.052(stage 8),最后陡增至0.105(stage 9);第一处温度起伏(ΔT L)较小为1.5 ℃,其余均高于3.2 ℃,局部温度起伏差与应变速率峰值的变化高度相关。综上所述,实验钢单轴拉伸过程表现出持续的集中塑性应变特征(即塑性失稳)明显热效应。
图5为IA750实验钢不同塑性失稳阶段相对应的工程应力-应变曲线、标距段全域应变速率( )和温度场云图。变形前期(Ⅰ阶段,ε=17.80%~20.77%)首条PLC带( max)形成于标距顶端(ε=17.80%),而后逐渐下移,直至湮灭(ε=20.77%)于标距底端,工程应力陡降(图5(a-1))并趋于平缓,第二条PLC带形成于标距顶端,而后逐步下移。温度场呈现类似变化趋势,温峰区域(T max,用红色三角形标示)从标距顶端逐渐移至底部(ε=19.94%),对应着首条PLC带传播,当应变达到20.34%时,标距上端(黑色框区域)温度逐渐升高,表明新的PLC带再次形成;当ε超过20.77%时,标距顶端再次出现温峰。上述结果表明,变形初期(Ⅰ阶段,ε=17.80%~20.77%)PLC带具有典型沿拉伸轴向单向传播的A型特征。
图5(b-1),(b-2),(b-3)分别为IA750实验钢在变形中期(Ⅱ阶段,ε=26.15%~29.48%)塑性失稳阶段的σ-ε曲线以及标距段全域应变速率云图和全域温度场云图。如图5(b-2)所示,前一个PLC带在标距上方消失,新的PLC带在标距下方产生,对应σ-ε曲线陡然下降,在传播过程中新的跳跃型PLC带产生,之后在标距中部生成新的PLC带并往下传播,其间新的跳跃型PLC带产生,并伴随着工程应力的陡然下降,PLC带与加载方向(loading direction,LD)大致成60°夹角。T max与 max紧密关联,但两者存在区域未能完全同步对应,可能与热量传递滞后效应有关。变形中期的PLC带具有跳跃(B型)特征,无规律且多点爆发式形成、扩展和湮灭。变形后期(Ⅲ阶段,ε=45.07%~56.10%),加工硬化现象更趋显著, max和T max变化相互对应。PLC带表现为A型特征,在标距中部形成,向顶端或者底端移动直至湮灭,对比变形前期与中期,后期PLC带传播需要更大的外应力和更长的时间。颈缩断裂发生前(ε=56.10%),PLC带内 可达0.75~1.18 s-1,显著高于其他区域对应值(0~0.4 s-1)。
2.3 PLC带形成机理
图6(a)与图6(b)分别为不同拉伸应变量下IA750实验钢的XRD谱图和残余奥氏体(retained austenite, RA)含量。如图6(b)所示,临界淬火态实验钢由奥氏体(γ)和临界铁素体(α)相组成,V RA约为30.9%(体积分数,下同);随着ε增加,V RA快速降至12.8%(ε=10%)和6.2%(ε=60%,拉伸断裂态)。低应变下(ε=3%~10%)出现密排六方(hexagonal close packed,HCP)结构ε-马氏体衍射峰(图6),该相常被认为是奥氏体转变为体心立方(body center cubic,BCC)结构马氏体相的过渡中间相[17],而拉伸断裂态(ε=60%)试样XRD谱图中未见ε-马氏体相衍射峰。奥氏体转变量(ΔV RA)呈先快后缓的趋势,10%工程应变下ΔV RA仅为6.6%。
图7为IA750实验钢在不同预应变后(ε=0%,3%,10%和20%)相分布图和反极图(inverse pole figure,IPF),红色和绿色分别对应面心立方(face center cubic,FCC)相和体心立方相,FCC相为残余奥氏体,形态主要为块状和条状,包含少量等轴状;BCC相为临界铁素体(αIA)或马氏体(α′)。IPF图反映了FCC相或BCC相晶粒之间的晶面取向差异,如图7(a-2)中白框区域所示,相邻RA取向相同,可能均由同一取向热轧淬火态板条马氏体逆转变而来。根据EBSD统计分析获得残余奥氏体含量分别为28.05%(ε=0%),26.88%(ε=3%),17.16%(ε=10%)和6.19 %(ε=20%),与XRD计算结果大致相符。随着预应变量增大,块状奥氏体数量逐渐减少;因塑性变形引入的位错、间隙原子等晶体缺陷破坏母相和新相的共格关系,并造成奥氏体加工硬化,使马氏体转变时原子运动更为困难。当ε为20%时,仅存在稳定性较高的条状和等轴状奥氏体,从IPF图(图7(d-2))可得奥氏体晶粒取向存在明显差异,说明稳定性较高的等轴状残余奥氏体细晶沿特定结晶方向旋转,通过改变滑移面和滑移方向来适应外加应变增加。综上所述,IA750实验钢在拉伸过程中力学稳定性较低的块状奥氏体优先产生SIMT,可能与塑性失稳具有一定关联性。
图8为IA750实验钢不同变形量(ε=0%,10%,15%,20%,30%,40%和50%)标距段显微硬度分布。如图8所示,变形前(ε=0%)标距段显微硬度为(260±1)HV5。当ε增至10%时,显微硬度显著提升至(283±3)HV5,且无较大起伏;当ε超过10%时,显微硬度分布在拉伸轴向存在明显差异,平均值偏差在11~12HV5之间浮动,峰值区域由左移至右侧;当ε为50%时,22~25 mm处显微硬度均值偏差达21HV5。结合EBSD结果推断,随着应变量的增加,加工硬化现象是马氏体相变和位错增殖共同作用的结果,体现出一定的时序性和传播性。
以往研究结果表明,锰钢内PLC带的形成与传播由DSA效应引起,但TWIP钢和TRIP钢中DSA效应的产生机理不尽相同。高锰TWIP钢中C和Mn相互吸引[18],DSA效应来自C-Mn配合物中C原子的重新取向。普遍研究[9,19-20]认为高锰TWIP钢在拉伸过程中优先形成的位错会将C原子从八面体间隙转移到四面体间隙,后续位错形成之前C原子会从四面体间隙再次转移到八面体间隙,故八面体间隙中C原子增加了后续位错滑动的剪切应力,致使DSA效应的产生。TRIP钢中DSA效应的形成机理并无统一说法,Nam等[21]研究冷轧退火态Fe-5.15Mn-0.15C-0.37Si 钢在拉伸过程中的塑性失稳现象后认为:由于Mn含量相对较低,C原子扩散系数增大即C原子扩散活化能减小,在拉伸过程中C原子与位错发生相互作用,致使DSA效应产生;Field等[22]研究冷轧退火态Fe-11.9Mn-0.17C-1.2Si-0.042N钢发现DSA效应的终止活化能与Mn原子奥氏体晶格扩散能相接近,而ε-马氏体被认为是由部分位错限定的系列固有堆垛层错,在拉伸过程中Mn原子位于堆垛层错相邻的两层原子面时降低了堆垛层错能,而DSA效应与Mn原子和马氏体、奥氏体界面相互作用有关。谢敬佩等[23]通过研究中锰奥氏体钢透射电镜原位拉伸过程发现中锰奥氏体钢在拉伸过程中极易形成堆垛层错,层错反应形成固定位错,随着应变量增大,位错增殖并产生交互作用,从而使钢表面强化,同时应变诱导马氏体在高密度位错区形核,随应变量增大而长大。
综合DIC,IRT,EBSD和显微硬度分布等结果分析,IA750实验钢在单轴拉伸过程中存在塑性失稳并伴随热量的变化,奥氏体转变为马氏体主要集中于变形前期,而PLC带的形成与传播一直持续到试样颈缩。因此,可以确定拉伸过程中PLC带形成和传播的主要原因并非应变诱导马氏体转变机制,而更可能是增殖位错与间隙溶质原子的相互作用,即DSA效应。图9为IA750实验钢拉伸过程PLC带形成机理示意图。如图9(a)所示,未变形的IA750实验钢组织主要由奥氏体和铁素体组成;变形前期(图9(b)),拉伸过程中基体应力的增加以及位错的形成有利于马氏体的形核长大,因此,力学稳定性差的奥氏体(软相)最终转变为α′-马氏体(硬相),而力学稳定性高的奥氏体晶粒通过旋转抵抗外加应力的增大,位错运动将受到晶界等阻碍,当位错滞留在障碍物前的等待时间内,扩散过来的溶质间隙原子与其发生交互作用而受到钉扎,需要更大外应力使得位错挣脱溶质间隙原子气团的钉扎,位错会优先向低密度位错区域运动即沿轴向单向传播,PLC带呈现A型特征并持续向底端移动。
变形中期(图9(c)),此时实验钢具有残余奥氏体+铁素体+应变诱导马氏体(α')的复相组织,更高的局部应变驱动少量较高力学稳定性的残余奥氏体持续转变,同时位错源和位错密度不断增加,致使位错之间产生交互作用,使得DSA效应具有不稳定性,故PLC带呈现出跳跃(B型)特征;变形后期(图9(d)),未转变残余奥氏体具有最高的力学稳定性,分布相对均匀,随着位错密度的增加以及交互作用的增强,位错障碍大量生成,加剧了位错增殖以及与新生位错的相互作用,最终致使位错的运动越来越困难,所以后期PLC带传播需要更大的外应力和更长的时间,具有A型特征,并向两端连续扩展。必须指出的是,高强塑积含铝中锰钢的组织演变过程和塑性失稳机理十分复杂,有待进一步深入分析和验证。
3 结论
(1)塑性失稳表现为锯齿状应力起伏,宏观塑性变形大部分来自局部应变集中(即PLC带),经历从连续(A型)至跳跃(B型)再到连续(A型)的演变,具有显著热效应。
(2)实验钢单轴拉伸过程中,残余奥氏体转变为马氏体主要集中在变形前期,PLC带形成与传播受控于间隙溶质原子与位错的相互作用,变形前期,位错会优先向低密度位错区域运动即沿轴向单向传播形成A型PLC带,中期位错增殖和开始交互作用的影响致使形成跳跃性(B型)PLC带,后期位错密度的增大和交互作用的增强,使得A型PLC带形成。
免责声明:本网站所转载的文字、图片与视频资料版权归原创作者所有,如果涉及侵权,请第一时间联系本网删除。
相关文章
无相关信息
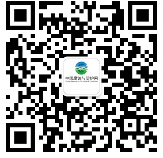
官方微信
《腐蚀与防护网电子期刊》征订启事
- 投稿联系:编辑部
- 电话:010-62316606
- 邮箱:fsfhzy666@163.com
- 腐蚀与防护网官方QQ群:140808414
点击排行
PPT新闻
“海洋金属”——钛合金在舰船的
点击数:10028
腐蚀与“海上丝绸之路”
点击数:7814